Projeto para fabricação automatizada de compósitos de aeroestruturas de baixo volume
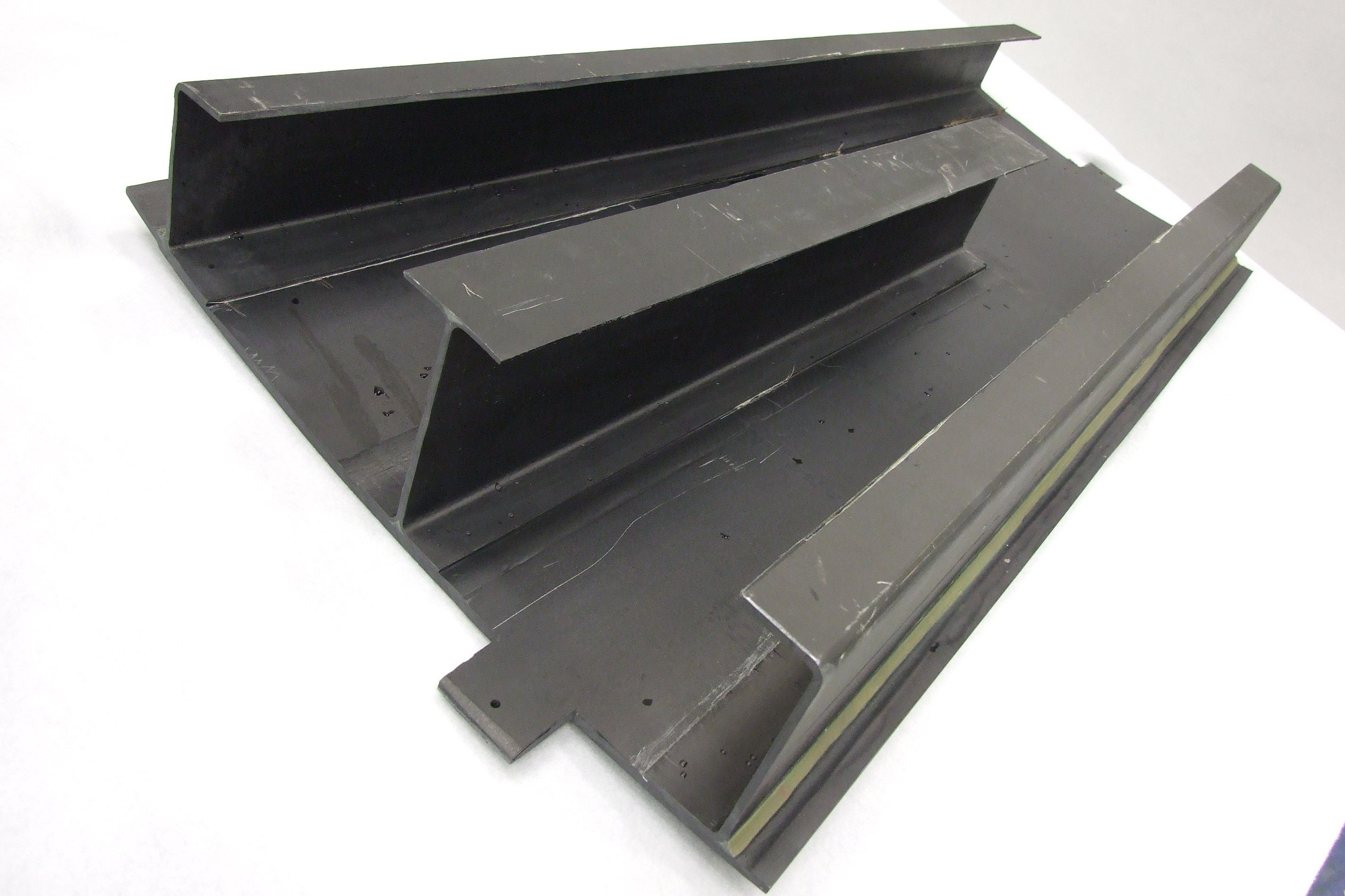
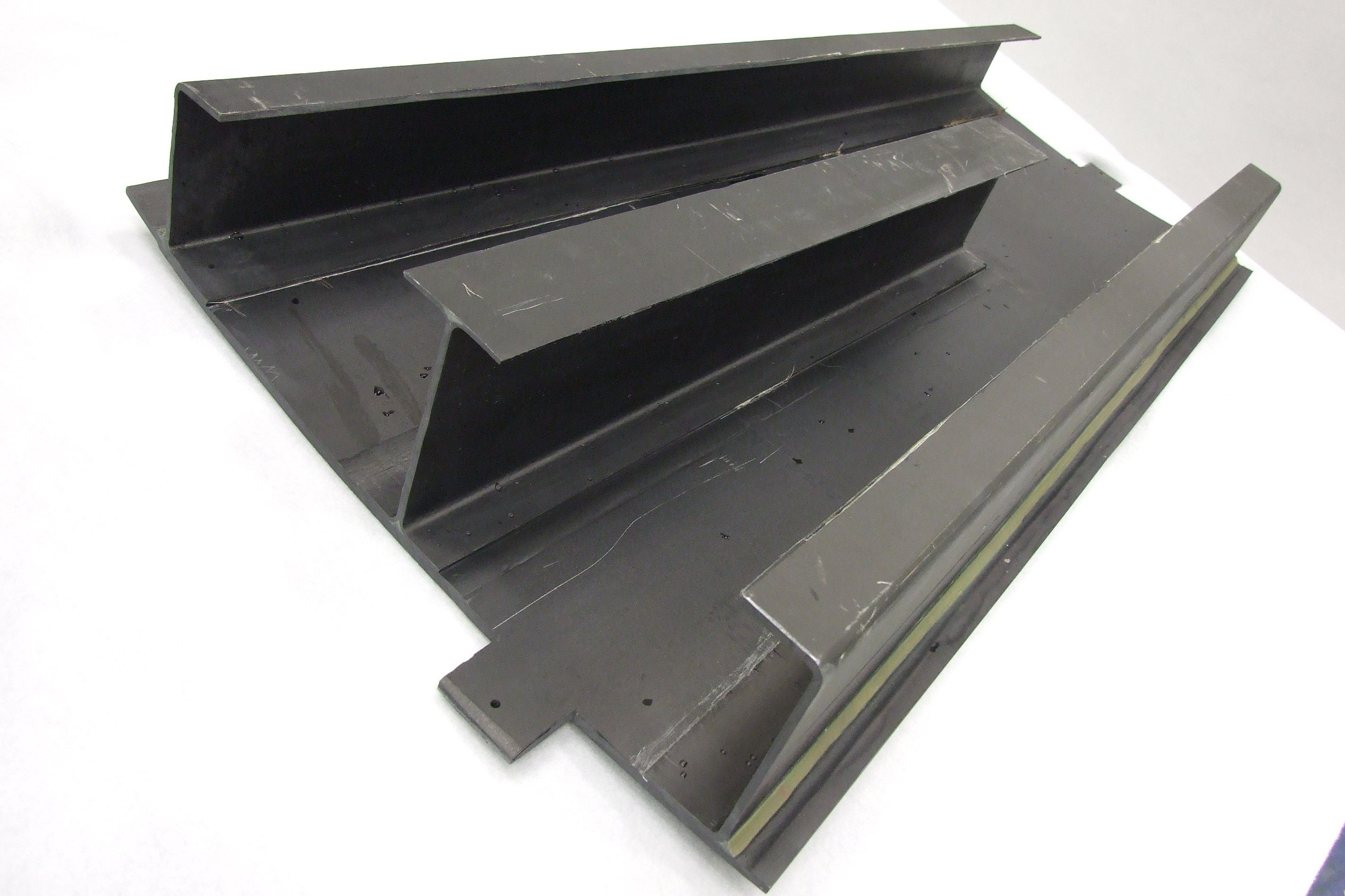
A fabricação de aeroestruturas compostas para aeronaves comerciais se estende por mais de 50 anos e progrediu constantemente de peças menores para estruturas primárias muito grandes - fuselagem, asas, empenagem, motores - desenvolvidas no início de 2000 para o Boeing 787 e o Airbus A350. A grande maioria dessa evolução dependeu do uso de pré-impregnados de fibra de carbono / epóxi curados em autoclave, inicialmente colocados à mão e, posteriormente, por meio de colocação automática de fibra (AFP), assentamento automatizado de fita (ATL) e outros processos baseados em máquina.
Essas tecnologias de material e processo (M&P) eram adequadas para o 787 e o A350 de grande porte que, antes da pandemia, apresentavam taxas de aumento de 10-15 por mês. Como a Boeing e a Airbus olham para o futuro, no entanto, e consideram a aplicação de materiais compostos em estruturas primárias de aeronaves de corredor único que devem ter taxas de construção de 60-100 por mês, o projeto e M&P irão favorecer taxas altas, fora de -autoclave (OOA), processos altamente automatizados. Esses processos incluem, entre outros, moldagem por transferência de resina (RTM), moldagem por compressão e infusão de resina líquida.
Mas mesmo que a fabricação de alta taxa domine o setor aeroespacial comercial, a fabricação de estruturas aeroespaciais compostas para baixa taxa aeronaves - incluindo aeronaves regionais e programas de jatos executivos - não apenas persistirão, mas podem e devem se beneficiar de algumas das mesmas inovações de custo, design e M&P que serão implantadas em programas de alta taxa.
Foi com tudo isto em mente que lançou o programa European Clean Sky 2 OPTICOMS - Opti mized Com posite S Estruturas para Aeronaves de Pequeno Porte. OPTICOMS é um consórcio liderado pelo fabricante aeroespacial Israel Aerospace Industries (IAI, Lod, Israel) com parceiros que fornecem tecnologias de automação de inovação, materiais, software, ferramentas e maquinários. O objetivo do OPTICOMS é avaliar um projeto de caixa de asa de produção de baixa taxa que apresenta fabricação automatizada, estruturas integradas, cura OOA, grande ligação estrutural, fabricação inovadora e ferramentas de montagem, monitoramento de integridade estrutural de linhas de união e testes virtuais.
Arnold Nathan, diretor de P&D do grupo de aviação da IAI e gerente da OPTICOMS, diz:"Sempre que tentamos colocar a automação em uma [discussão] sobre a fabricação de compósitos, muitas vezes ouvimos nossos clientes dizerem:'Automação é boa, mas apenas quando você tem um grande volume de produção. 'OPTICOMS foi configurado para descobrir se você pode justificar a automação quando você não têm produção de grande volume. A automação da fabricação de compósitos pode ser competitiva e econômica para baixos volumes? ”
Design da asa
A OPTICOMS nasceu de um pedido da Clean Sky 2 emitido pelo fabricante italiano de aeronaves executivas Piaggio Aerospace (Gênova) para o desenvolvimento de uma asa alternativa totalmente composta para seu P180 Avanti turboélice gêmeo para nove passageiros. A caixa da asa mede 6,8 metros de comprimento, 0,71 metros de largura na raiz e 0,28 metros de largura na ponta. A Piaggio, diz Nathan, estava ansiosa para avaliar uma alternativa à caixa da asa legada toda em metal - uma alternativa com as mesmas dimensões, mas com peso reduzido (20%). Além disso, o custo deve ser reduzido em 20-30% em comparação com a fabricação de caixa de asa composta convencional. O IAI e seus parceiros ganharam o contrato e começaram a trabalhar com a Piaggio em 2016.
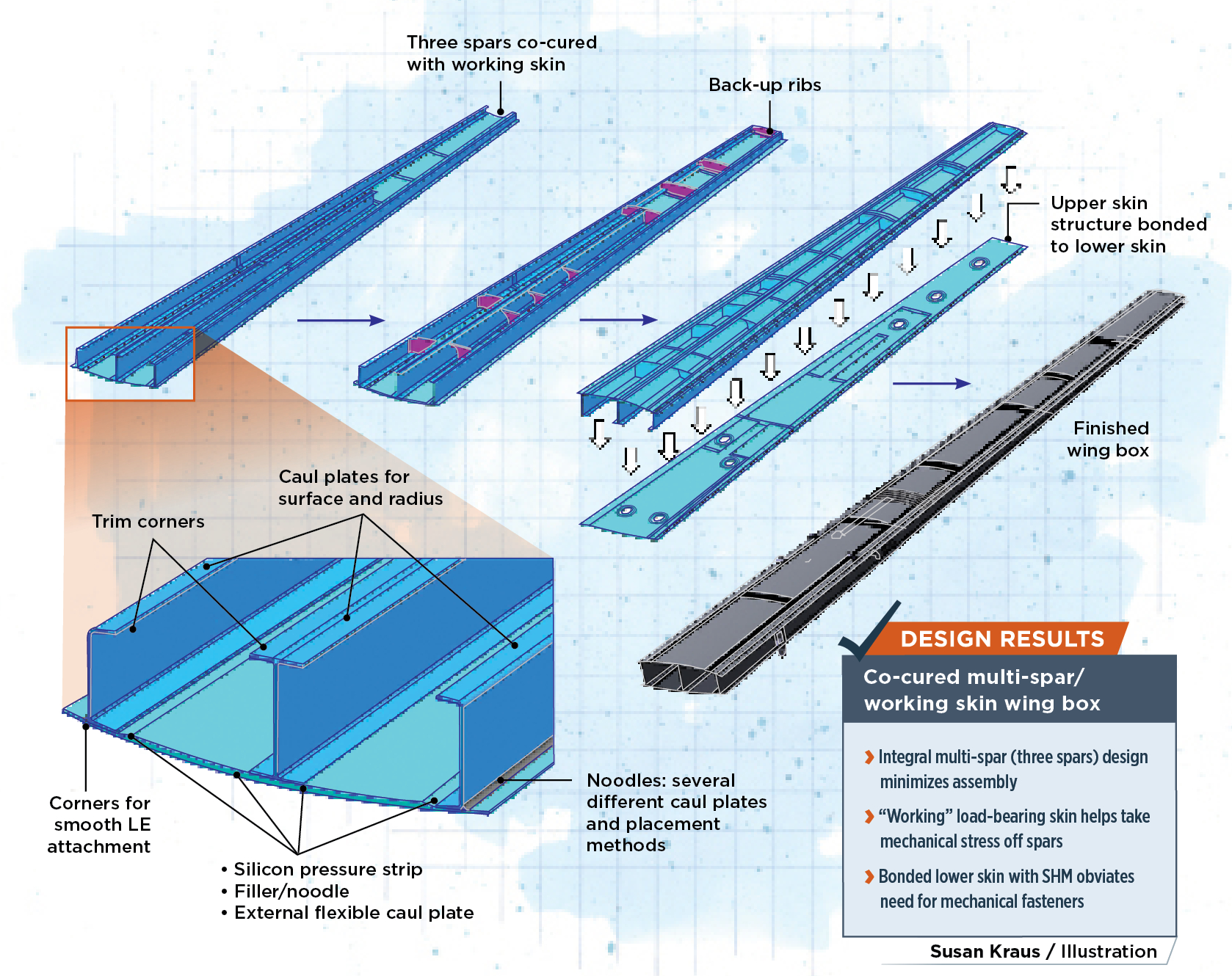
OPTICOMS é um programa de várias partes projetado para realizar uma série de estudos comerciais altamente detalhados e meticulosamente conduzidos para avaliar e determinar o projeto de asa ideal, combinação de materiais e processo de fabricação OOA para a fabricação automatizada de uma caixa de asa totalmente composta de baixo volume.
IAI e OPTICOMS, diz Nathan, decidiram desde o início que se concentraria em avaliar o uso de três processos de fabricação fornecidos por três parceiros:Seleção e colocação automatizada de tecidos secos e pré-impregnados, fornecidos pela Techni-Modul Engineering (TME, Coudes, França); colocação automática de fibras (AFP) de reboques secos e pré-impregnados, fornecidos por Coriolis Composites (Queven, França); e tecnologia de colocação automatizada de material seco (ADMP), fornecida pela Danobat (Elgoibar, Espanha). A seleção dessas tecnologias e parceiros seria crítica para orientar o IAI em seus estudos comerciais de múltiplas variantes.
Resultados do design
- O design integral de várias longarinas (três longarinas) minimiza a montagem
- A pele de suporte de carga "funcional" ajuda a aliviar o estresse mecânico das longarinas
- Pele inferior colada com SHM elimina a necessidade de fixadores mecânicos
A primeira etapa neste estudo comercial foi a avaliação do projeto. Esse esforço foi liderado no IAI por Adam Sawday, engenheiro de projeto estrutural para tecnologias avançadas. Sawday diz que ele e IAI adotaram uma abordagem simples para o projeto da asa, estudando mais de 18 conceitos em uma variedade de arquiteturas. Os designs rapidamente caíram em uma das duas categorias. O primeiro emprega um revestimento “funcional” no qual o revestimento da caixa da asa torna-se uma estrutura de suporte de carga. O segundo emprega revestimentos não funcionais com longarinas carregadas. Dentro dessas categorias, os projetos incluem um conceito tradicional com nervuras, longarinas e duas longarinas ou, alternativamente, o uso de três longarinas - chamadas multi-longarinas - sem costelas ou longarinas. Vários conceitos também consideraram o uso de uma construção de painel sanduíche que produz uma pele semi-funcional.
“Nosso mantra era reduzir o esforço de fabricação e reduzir o esforço de montagem”, diz Sawday. “E acreditamos que se você puder desenvolver uma estrutura mais eficiente e mais integral, então você obterá uma estrutura mais barata e mais leve.”
Sawday diz que os projetos foram medidos em relação a uma série de métricas para avaliar sua capacidade de atender às metas de custo e peso do programa. Essas métricas incluem:custos de material, complexidade de projeto, custos de fabricação de componentes, custos de montagem, custos de testes não destrutivos (NDT), custos de ferramentas e jigging, peso, resistência, nível de preparação de tecnologia (TRL), considerações ecológicas, perfil de risco, robustez e confiabilidade. Destes, os critérios com maior peso foram peso, custos de fabricação e montagem, complexidade do projeto, TRL e perfil de risco.
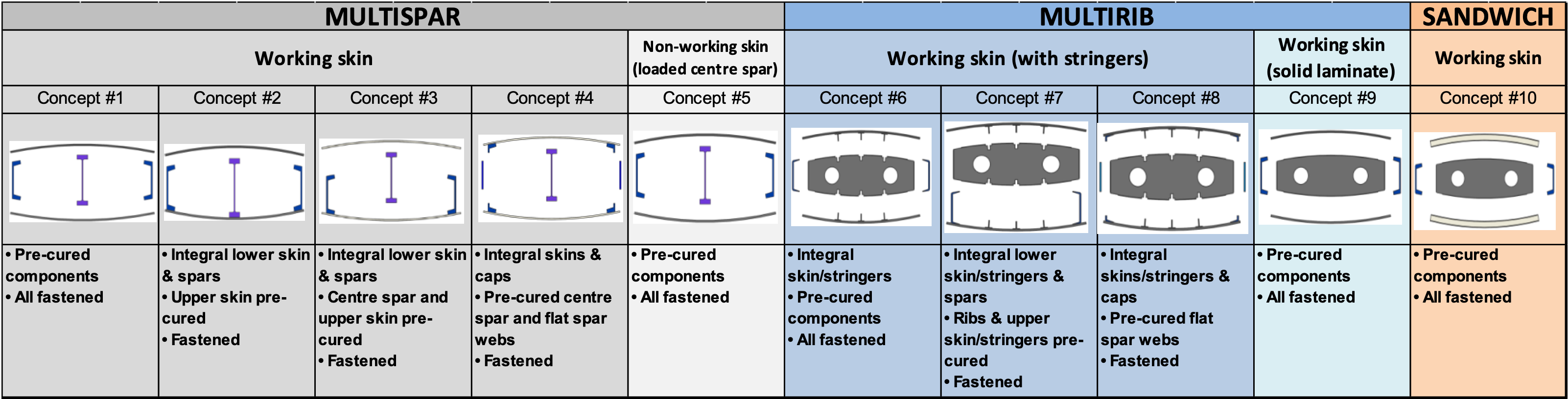
Seleção inferior para o design final
Os dados dessa avaliação ajudaram o IAI a selecionar os conceitos de design para 10 finalistas. Quatro eram multi-longarinas / pele de trabalho, uma era multi-longarinas / pele sem trabalho com longarinas carregadas, quatro eram multi-costelas / pele de trabalho com longarinas, uma era multi-costelas / pele de trabalho sem longarinas e uma era sanduíche estrutura / pele de trabalho sem longarinas. Cada projeto oferece várias combinações de pré-cura, co-cura, colagem ou fixação mecânica.
Chegar ao projeto final envolveu outra rodada de estudos comerciais usando muitos dos mesmos critérios do primeiro estudo. Cada projeto recebeu um valor comercial, com base em quão bem ele atendeu aos critérios. “Tínhamos essa grande mesa de troca e cada opção de design tinha um valor, e isso nos ajudou a ver a opção mais forte”, diz Sawday.
Houve um projeto, desde o início, que teve um desempenho consistentemente bom nos estudos de comércio e parecia que provavelmente sairia por cima, observa Sawday. E assim foi. Denominado internamente como multi-spar / working skin # 2, apresenta um revestimento superior altamente integrado e co-curado e três longarinas. Estes são então colados a uma película inferior que possui painéis de acesso. Localizada seletivamente entre as longarinas está uma série de nervuras de “apoio”, projetadas para apoiar a pele, que suporta a maior parte das cargas de flexão.
“As estruturas mais favoráveis que desenvolvemos”, diz Sawday, “foram aquelas com vigas múltiplas, onde a pele se torna mais resistente. As longarinas, então, tornam-se estruturas mais simples e finas, e não tão pesadas quanto nos designs de asas compostas tradicionais. Pensamos que se pudéssemos apenas tornar essas longarinas muito simples, com uma seção transversal constante, isso pouparia muita dor de cabeça e muito refugo. ”
Sawday diz que o projeto de multi-longarina / pele de trabalho integral colado mostrou uma promessa particular por seus custos de montagem reduzidos, baixo peso, facilidade de automação e baixa contagem geral de peças. A questão permaneceu, no entanto:quais materiais e quais processos de fabricação seriam mais adequados para dar vida a esse projeto?
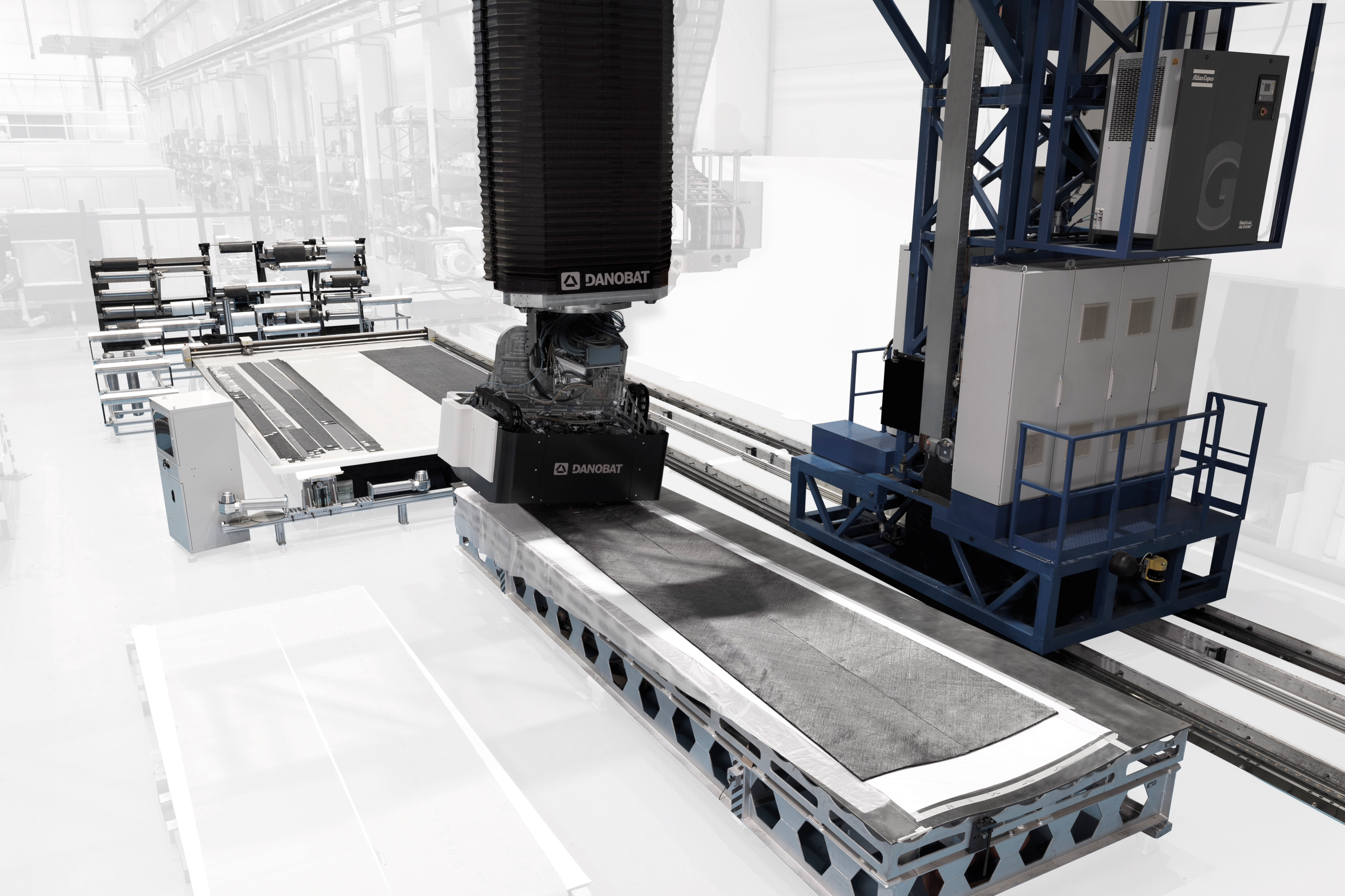
Estudos comerciais de M&P
Em primeiro lugar, foram os estudos de comércio de materiais. Eles foram executados no IAI por Yaniv Yurovitch, engenheiro de materiais compostos. Ele diz que a OPTICOMS começou a avaliar pré-impregnados de fibra de carbono OOA, fibras secas de carbono (fitas e tecidos) e resinas com base nas recomendações da Piaggio, IAI e parceiros de tecnologia. O resultado foi uma lista de 35 materiais qualificados e novos.
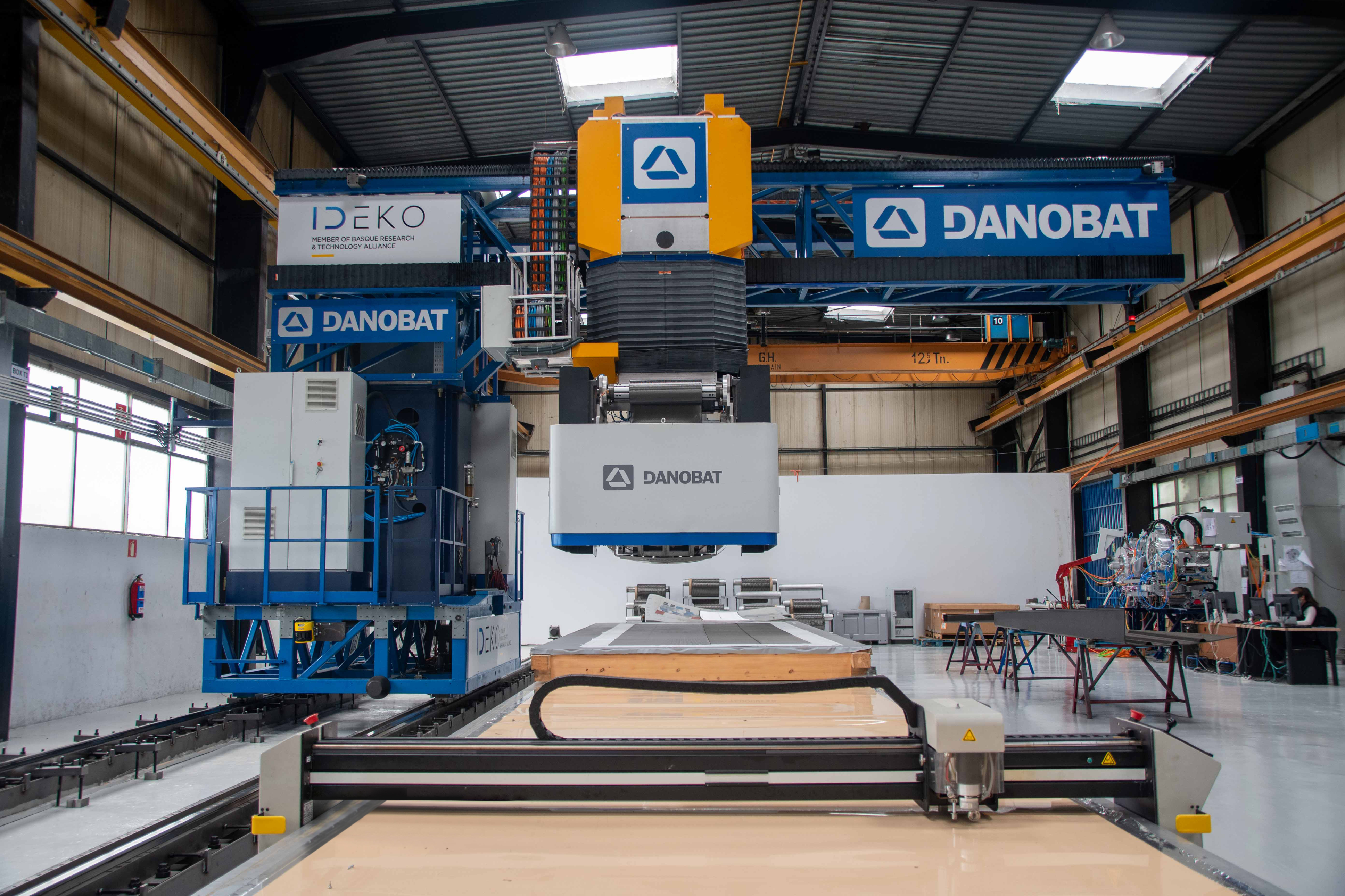
Este primeiro grupo de materiais foi então selecionado com base nos parâmetros mais cruciais para o projeto OPTICOMS:Custo, temperatura de transição vítrea (T g ), viscosidade (para infusão ou injeção) e adequação para tecnologias automatizadas de layup. Essa avaliação reduziu a lista de materiais de 35 para 20 pré-impregnados, fibras secas e resinas.
Amostras de cada um desses 20 materiais foram encomendadas; Yurovitch então fez cupons e executou testes mecânicos como parte da próxima seleção para baixo. “Foi um pacote de trabalho realmente grande”, diz Yurovitch. “Isso nos permitiu tomar mais decisões e selecionar os três materiais finais.” Essas combinações de fibra / resina são:
- Toray Composites Materials America’s (Tacoma, Wash., U.S.) 2510 fibra de carbono / epóxi prepreg.
- Fitas UD de fibra de carbono HiTape da Hexcel (Stamford, Conn., EUA), para serem usadas com a resina epóxi HexFlow RTM6 da Hexcel.
- Tecido não crimpado de fibra de carbono (NCF) fornecido pela SAERTEX (Saerbeck, Alemanha), para ser combinado por meio de infusão com Solvay Composite Materials ’(Alpharetta, Ga., EUA) PRISM EP2400 epoxi endurecido.
Essa lista obviamente favorece o uso de fibras secas, o que por sua vez favorece a infusão como processo de fabricação. Nathan diz que isso é motivado em parte pelo desafio de gerenciar a vida útil do pré-impregnado em um ambiente de baixo volume. “Quando você está falando de produção de baixo volume, você realmente não quer carregar muito pré-impregnado e se preocupar com o gerenciamento da vida útil”, diz ele. “A fibra seca não tem esse problema.”
Esses três materiais também foram combinados com um ou mais dos processos de fabricação selecionados para OPTICOMS:Toray prepreg combina com pick-and-place e AFP, HiTape / RTM6 da Hexcel combina com AFP, bem como pick and place, e SAERTEX NCF combina com pick-and-place ou ADMP.
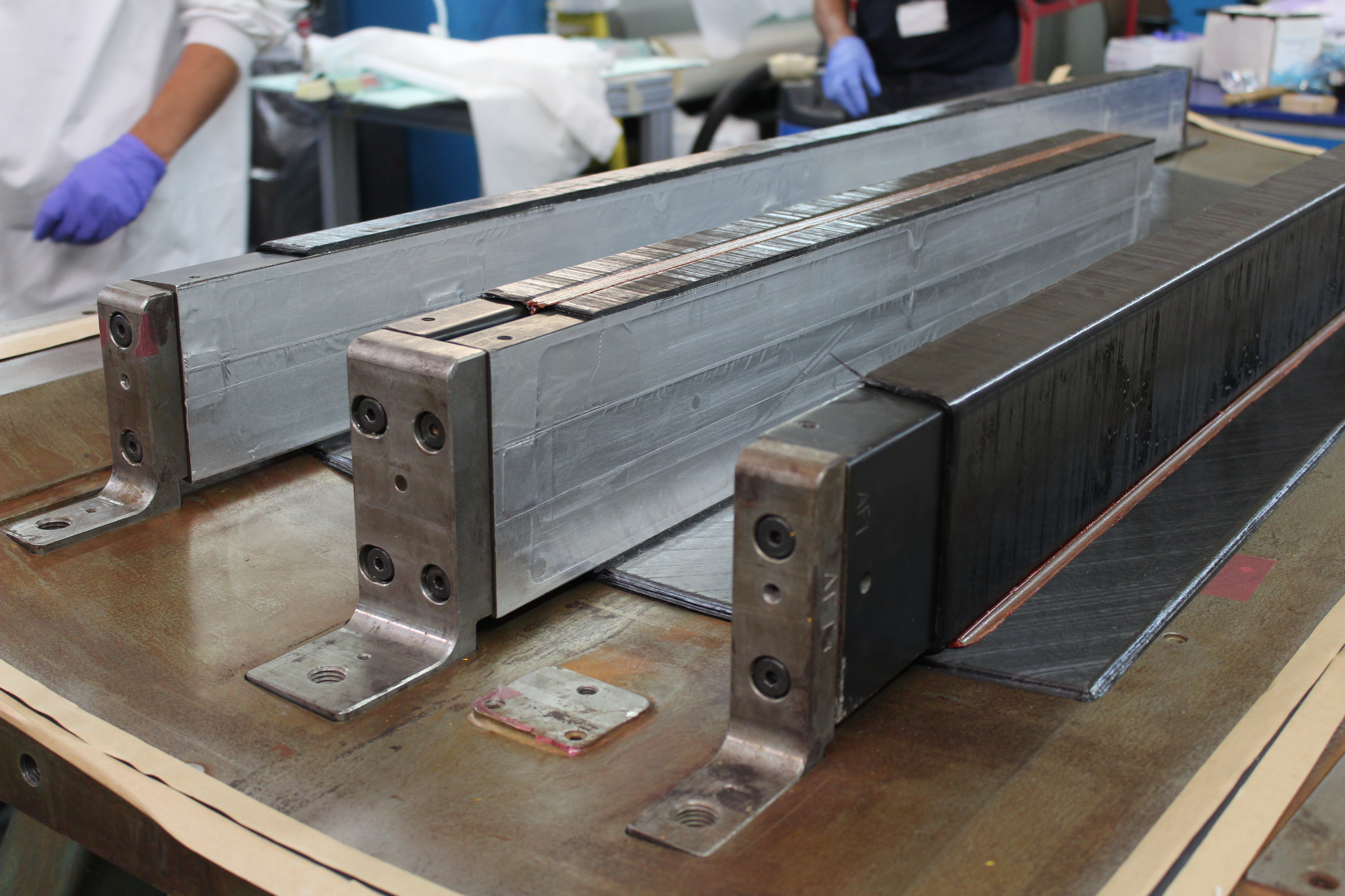
As negociações em torno dos processos de manufatura automatizados - que são mais adequados para cada tipo de peça - ainda estão sendo realizadas pela IAI e pela OPTICOMS. No entanto, os resultados preliminares, diz Nathan, estão definitivamente apontando as tecnologias em certas direções. Por exemplo, a tecnologia ADMP da Danobat, originalmente desenvolvida para a colocação rápida de tecidos largos na fabricação de pás de turbinas eólicas, provou ser igualmente eficiente em ÓPTICOS. A tecnologia amadureceu durante o OPTICOMS e sua robustez e confiabilidade foram aprimoradas, mas ainda é uma tecnologia de layup aeroespacial menos madura em comparação com o AFP.
Por outro lado, AFP com o sistema Coriolis, com sua extensa experiência aeroespacial, é uma tecnologia madura e precisa, mas tem tempos de layup mais longos em comparação com ADMP e requer inspeção relativamente frequente para verificar se há anomalias. Coriolis fez um progresso notável em todo o projeto OPTICOMS com o desenvolvimento de inspeção em linha e em tempo real do layup para lidar com este desafio, disse Nathan. Finalmente, a tecnologia pick-and-place da TME, projetada para automatizar a transferência de tecidos cortados da mesa de corte para o molde, parece ser mais eficaz para peças menores e discretas, como as nervuras de back-up no multi-spar / working design de pele.
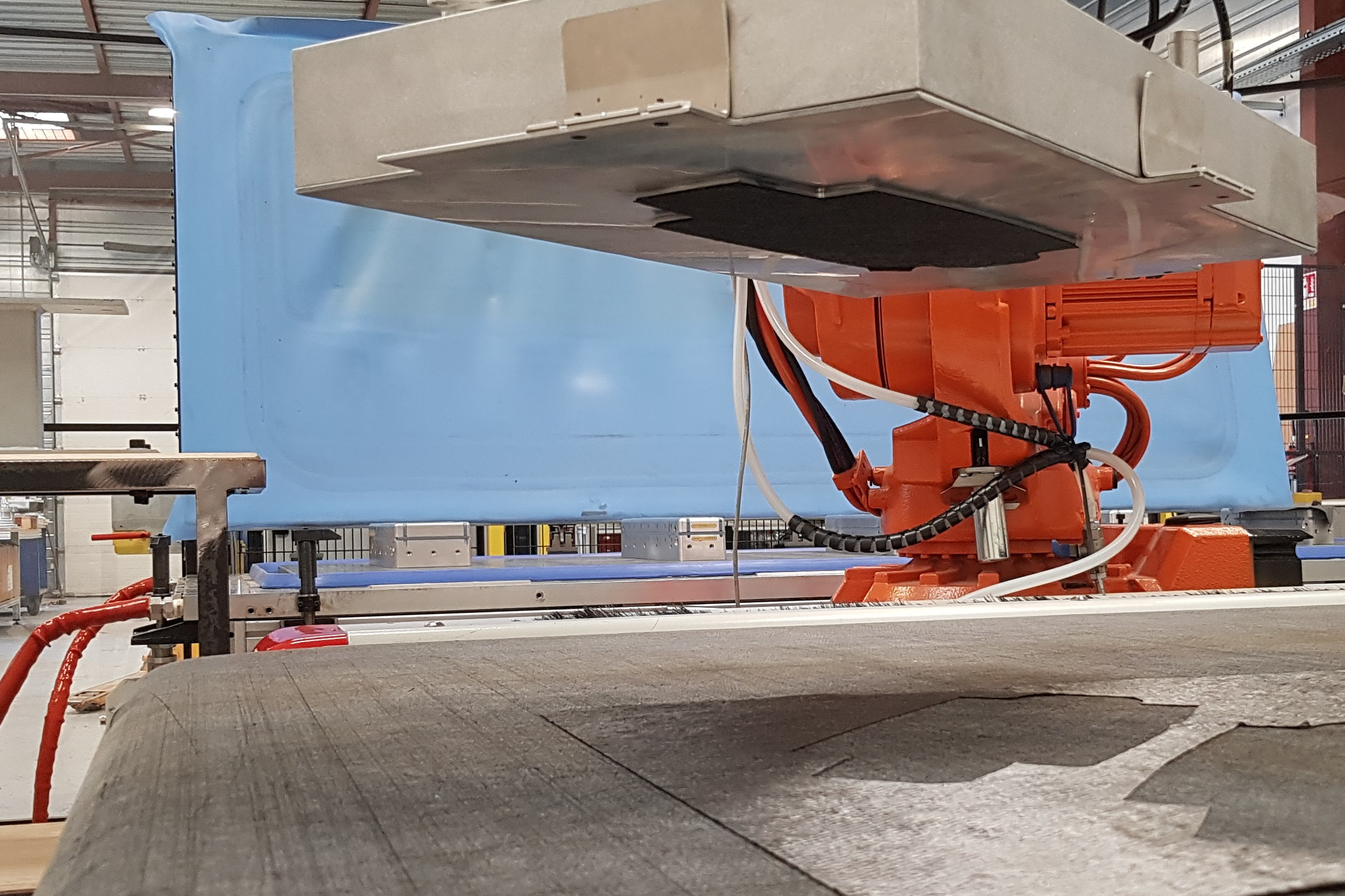
Próximas etapas
A OPTICOMS está no caminho certo para cumprir as metas de automação, redução de custos e peso estabelecidas pelo programa, diz Nathan, embora ainda haja vários meses de trabalho a ser feito para avaliar os processos de fabricação, bem como as soluções de montagem.
“Este é um ponto importante sobre o OPTICOMS”, explica ele. “Tivemos uma seleção robusta do design. Fizemos uma seleção inferior do material. Fizemos uma seleção inferior dos processos. Tudo isso leva tempo e esforço. Este é um dos aspectos únicos do projeto. ”
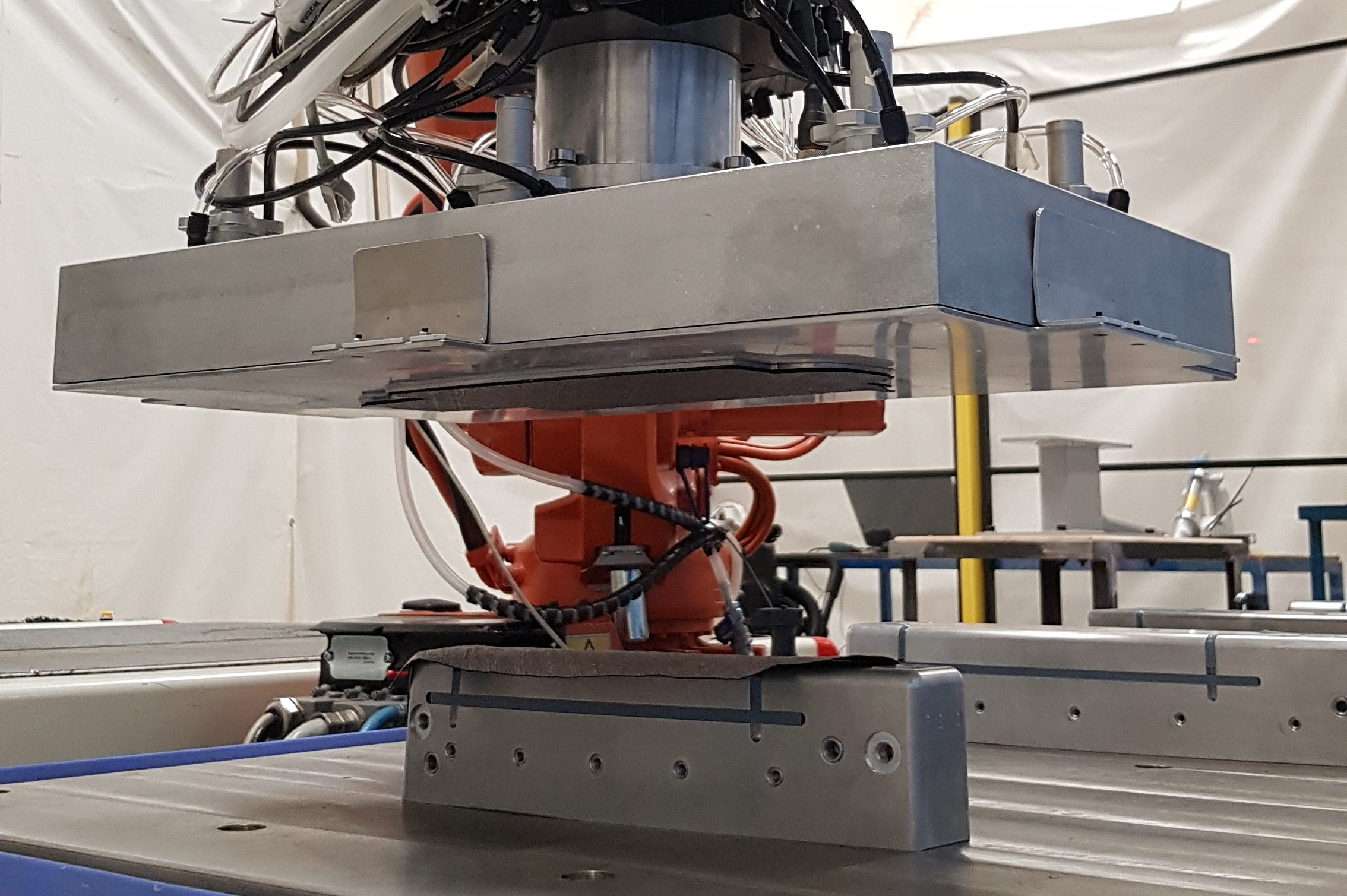
A OPTICOMS iniciou três chamadas de propostas (CFP) para tecnologias e hardware para apoiar, garantir e aprimorar os objetivos do projeto. As propostas bem-sucedidas tornaram-se projetos Clean Sky 2, associados e complementares ao Parceiro Core “mãe” da OPTICOMS - todos trabalhando juntos em um objetivo comum.
O primeiro esforço neste desenvolvimento é FITCoW, que visa desenvolver um novo sistema de ferramentas de fibra de carbono integral para a co-cura da pele de trabalho e três longarinas. A lista de metas da FITCoW é ambiciosa:redução de 50% no custo das peças fabricadas, redução de 30% no custo das ferramentas (em comparação com a alternativa metálica), redução de 20% no tempo de fabricação em comparação com as alternativas de autoclave e OOA, redução de 40% no descasamento CTE em comparação com as ferramentas Invar , Redução de 20% no tempo de aquecimento e resfriamento e redução de 40% no tempo de inspeção graças aos melhores recursos de controle dimensional.
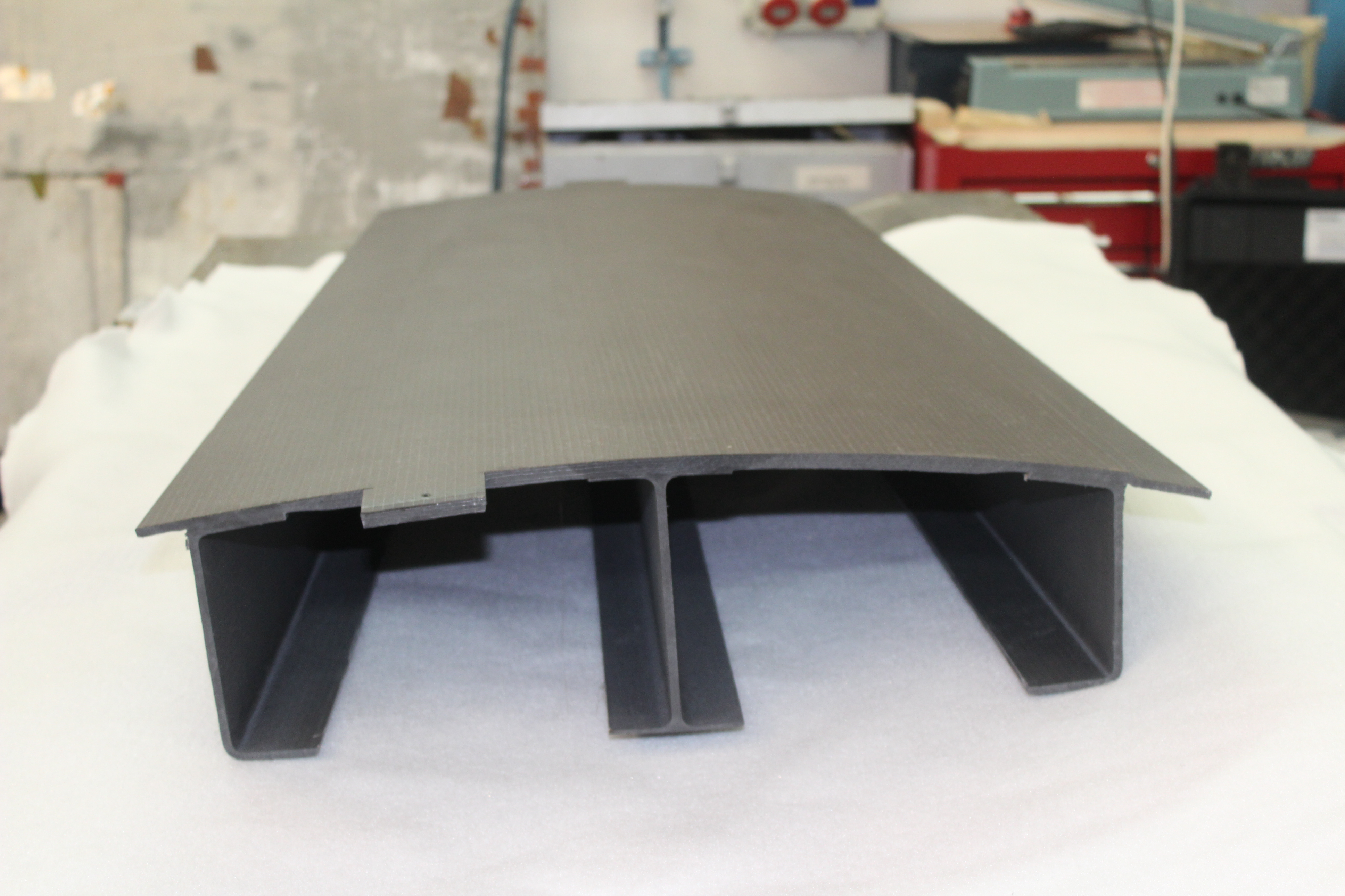
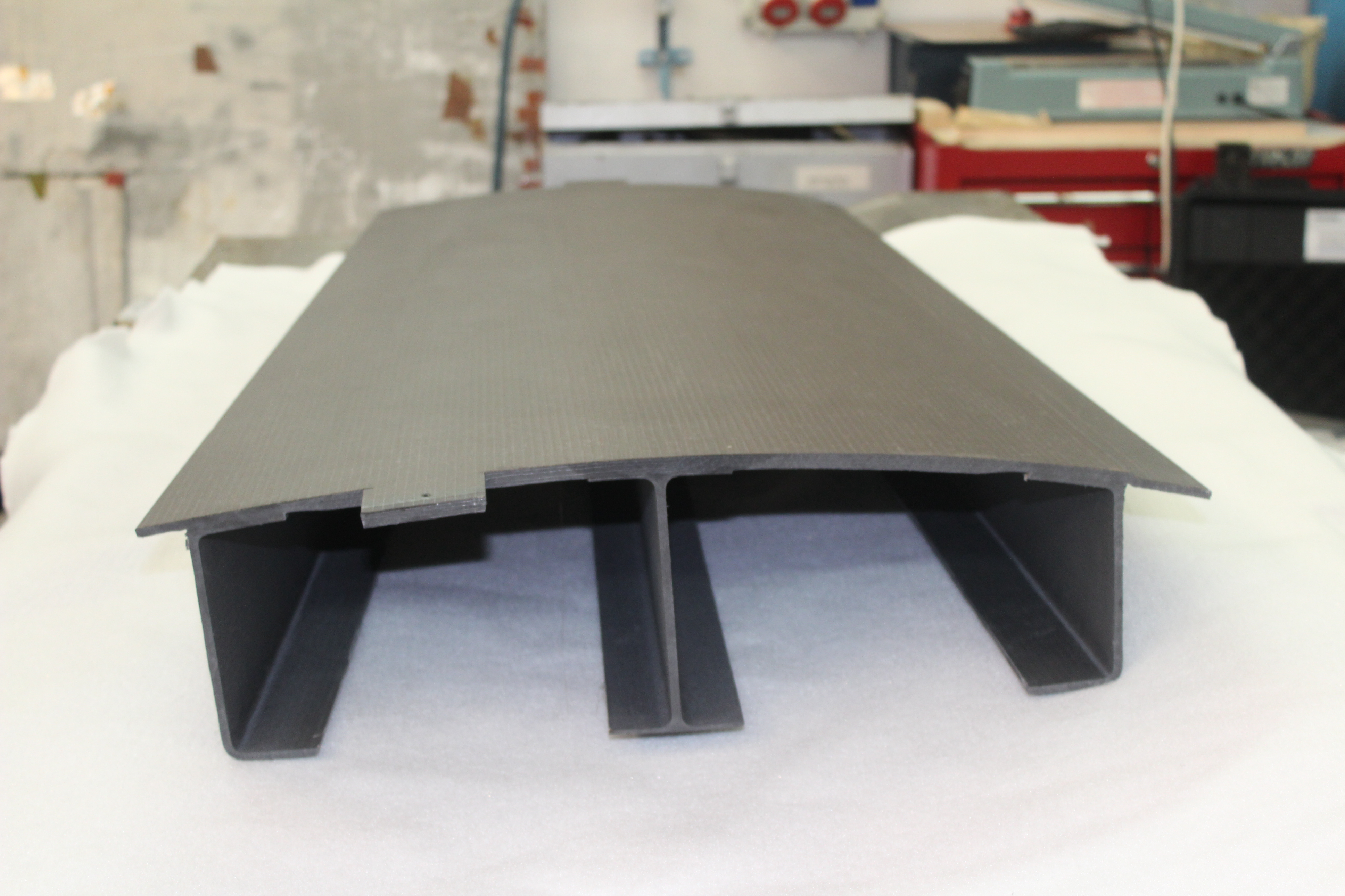
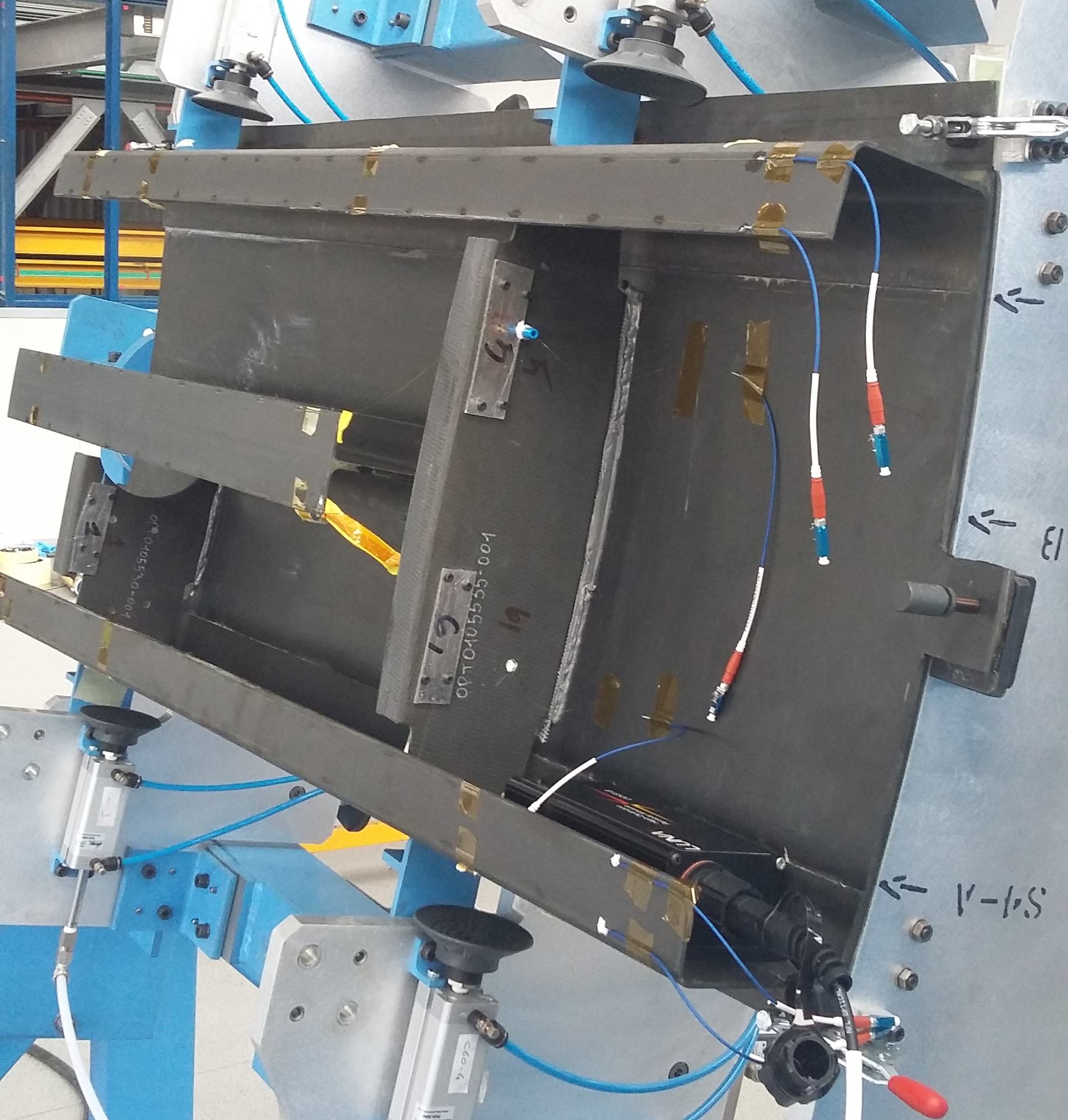
Para unir a estrutura da longarina / pele à pele inferior, o segundo CFP resultou em outro projeto OPTICOMS denominado WIBOND, para desenvolver uma ferramenta de montagem de colagem que coloca o adesivo, aplica a pressão adequada e incorpora sensores de fibra óptica na linha de colagem para a saúde estrutural monitoramento do vínculo; CW relatará sobre esta e outras tecnologias de montagem em um artigo separado a ser publicado em 2022.
O terceiro CFP foi iniciado para lidar com o desafio crucial de tensões residuais que causam um “salto” da estrutura da longarina / pele. Essas deformações podem ter efeitos deletérios no processo de montagem de colagem. O projeto ELADINE juntou-se ao esforço da OPTICOMS para desenvolver software que modela e prediz anisotropia térmica, contração de polimerização, interação de peças de ferramenta, fluxo de resina e compactação e gradientes de temperatura em toda a estrutura.
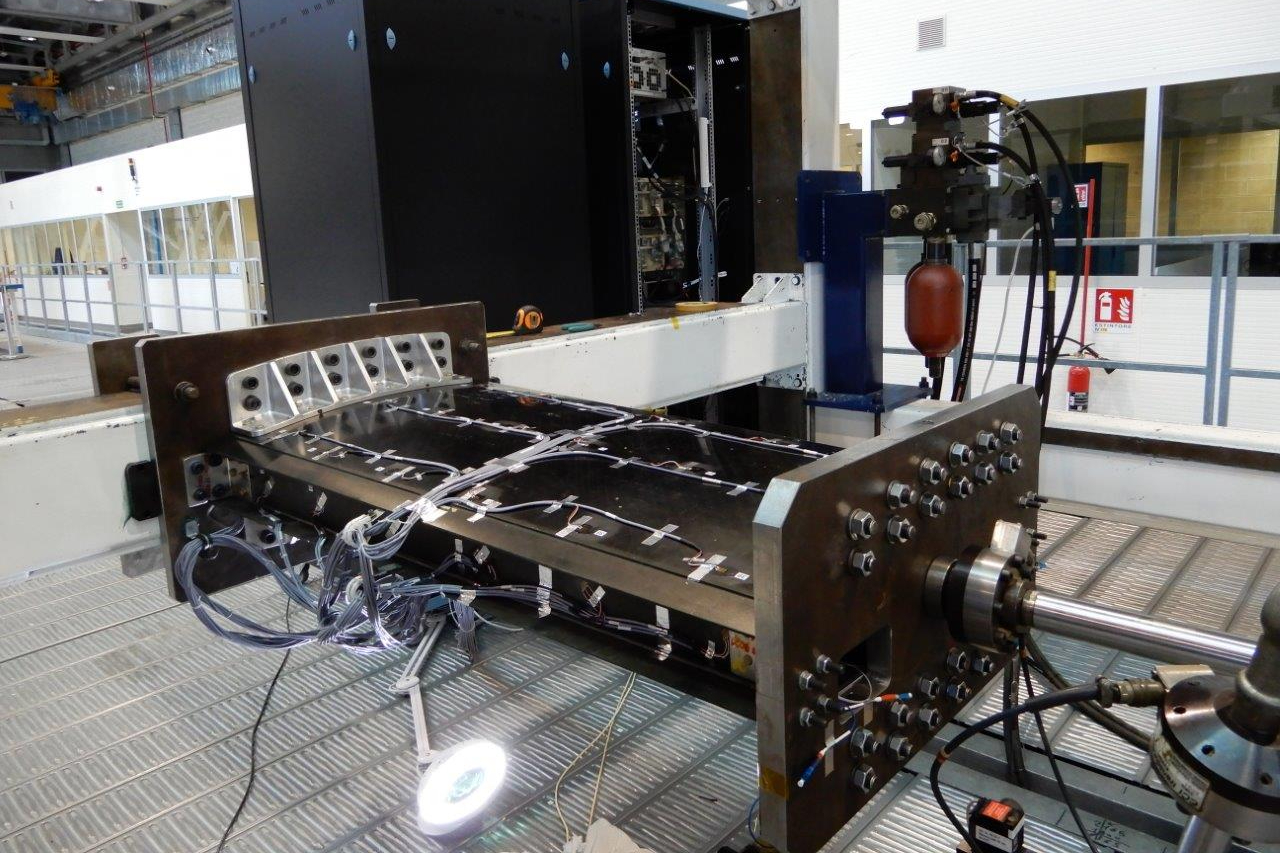
O foco principal da IAI e da OPTICOMS agora é entregar até o segundo trimestre de 2022 uma asa demonstradora completa de 6,8 metros para a Piaggio para testes estáticos e de fadiga. Isso será seguido por uma análise do desempenho geral da asa e a capacidade do design, materiais e processos para atender aos critérios do projeto. Em seguida, virá uma recomendação da Piaggio sobre os possíveis próximos passos para a comercialização.
Além da Piaggio, no entanto, o IAI espera que a caixa da asa OPTICOMS possa encontrar aplicação em outras aeronaves. “Embora este projeto seja baseado em uma aeronave específica”, diz Sawday, “tentamos tornar o projeto escalonável para diferentes espessuras e diferentes tamanhos. Nunca perdemos de vista o fato de que essa tecnologia pode e deve ser altamente adaptável. ”
Resina
- Compósitos TPE ultraleves para calçados
- Nexam Chemical, a NCC desenvolve solução para a fabricação de compósitos de alta temperatura
- Compostos Solvay selecionados para catamarã de corrida
- Community college adiciona flexibilidade para alunos de manufatura de compósitos avançados
- 4 erros comuns a serem evitados ao projetar para fabricação
- Fabricação de PCB para 5G
- Atendendo à grande necessidade de automação de compósitos
- Metais para fabricação de alta mistura e baixo volume
- O que é fabricação automatizada?
- Evite estes 4 erros comuns ao projetar para fabricação