A manufatura aditiva adiciona versatilidade a grandes estruturas marítimas
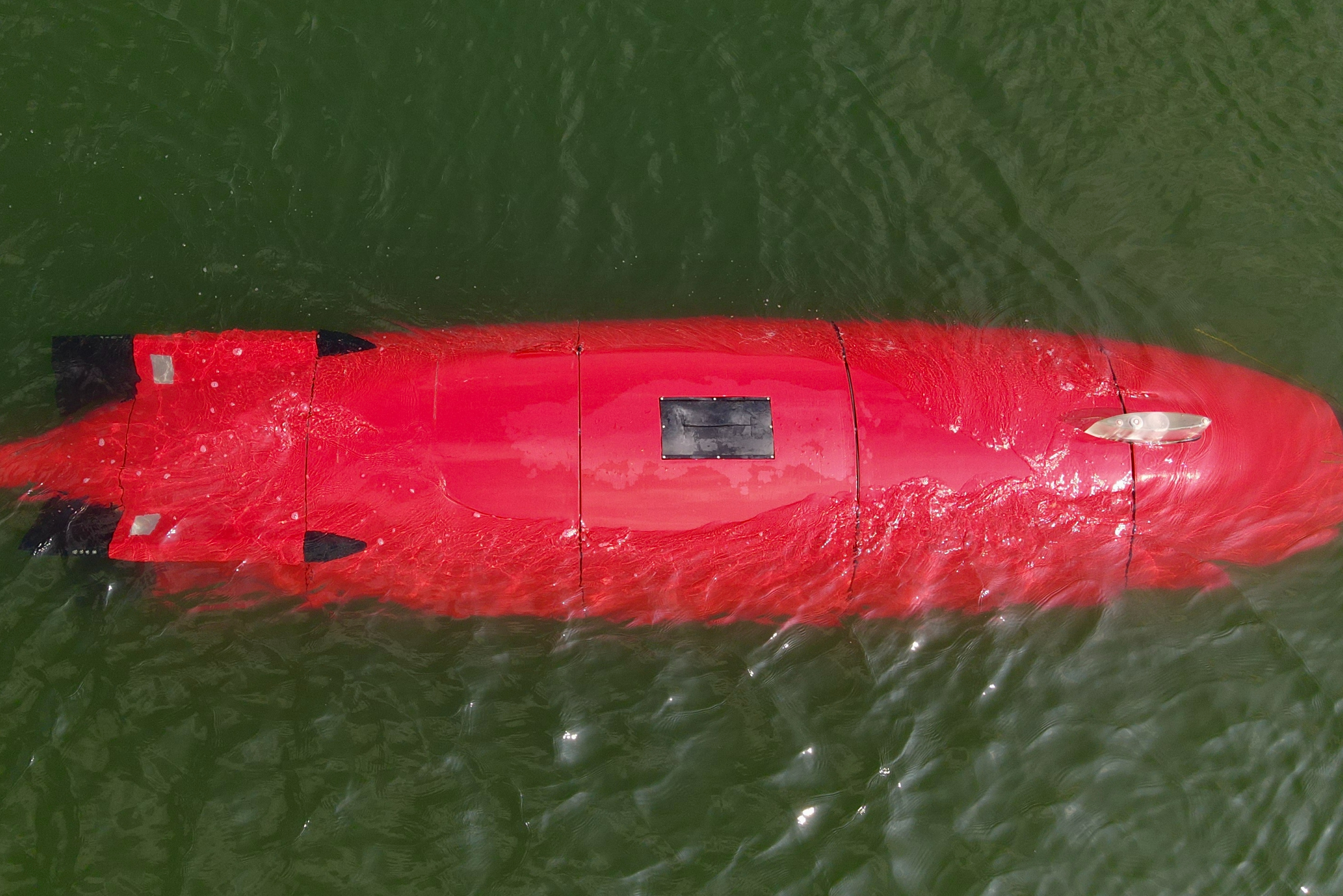
A capacidade de construir rapidamente diferentes iterações de peças - sem ter que desenvolver ou comprar ferramentas dedicadas caras - é a razão pela qual a manufatura aditiva (AM) é tão freqüentemente usada na prototipagem de peças. No entanto, à medida que os materiais e as tecnologias de impressão continuam a melhorar, mais empresas podem estender a velocidade e versatilidade da AM também às peças de uso final, especialmente para aplicações de pequenas tiragens ou únicas, onde a capacidade de produzir novos designs rapidamente é um ativo .
Recentemente, duas empresas demonstraram que as tecnologias de AM compostas podem permitir soluções para a personalização de grandes estruturas marítimas, como veículos subaquáticos autônomos (AUV) e lanchas.
Impressão 3D de grande formato para produção de AUV personalizável
Os veículos subaquáticos autônomos são um tipo de veículo robótico não tripulado capaz de viajar debaixo d'água sem conexão física a um barco ou controle remoto de um operador humano, e muitas vezes são equipados com câmeras ou sensores para vários casos de uso em defesa, pesquisa oceânica ou aplicações de levantamento offshore. Normalmente, os cascos externos dos AUVs compreendem um grande vaso de pressão de metal ou são construídos de plástico termoformado ou compostos. Ambas as opções, no entanto, requerem o desenvolvimento e a compra de ferramentas dedicadas, o que pode ser caro e limita a quantidade de customização que pode ser acomodada para clientes AUV. O fabricante de AUV Dive Technologies (Quincy, Mass., EUA) descobriu que a impressão 3D composta resolve muitas das limitações da fabricação tradicional.
Em 2018, os co-fundadores da Dive Technologies Bill Lebo, Jerry Sgobbo e Sam Russo decidiram formar sua própria empresa para projetar e lançar um novo AUV mais capaz que atenda às demandas dos clientes por longa durabilidade e grande capacidade de carga útil.
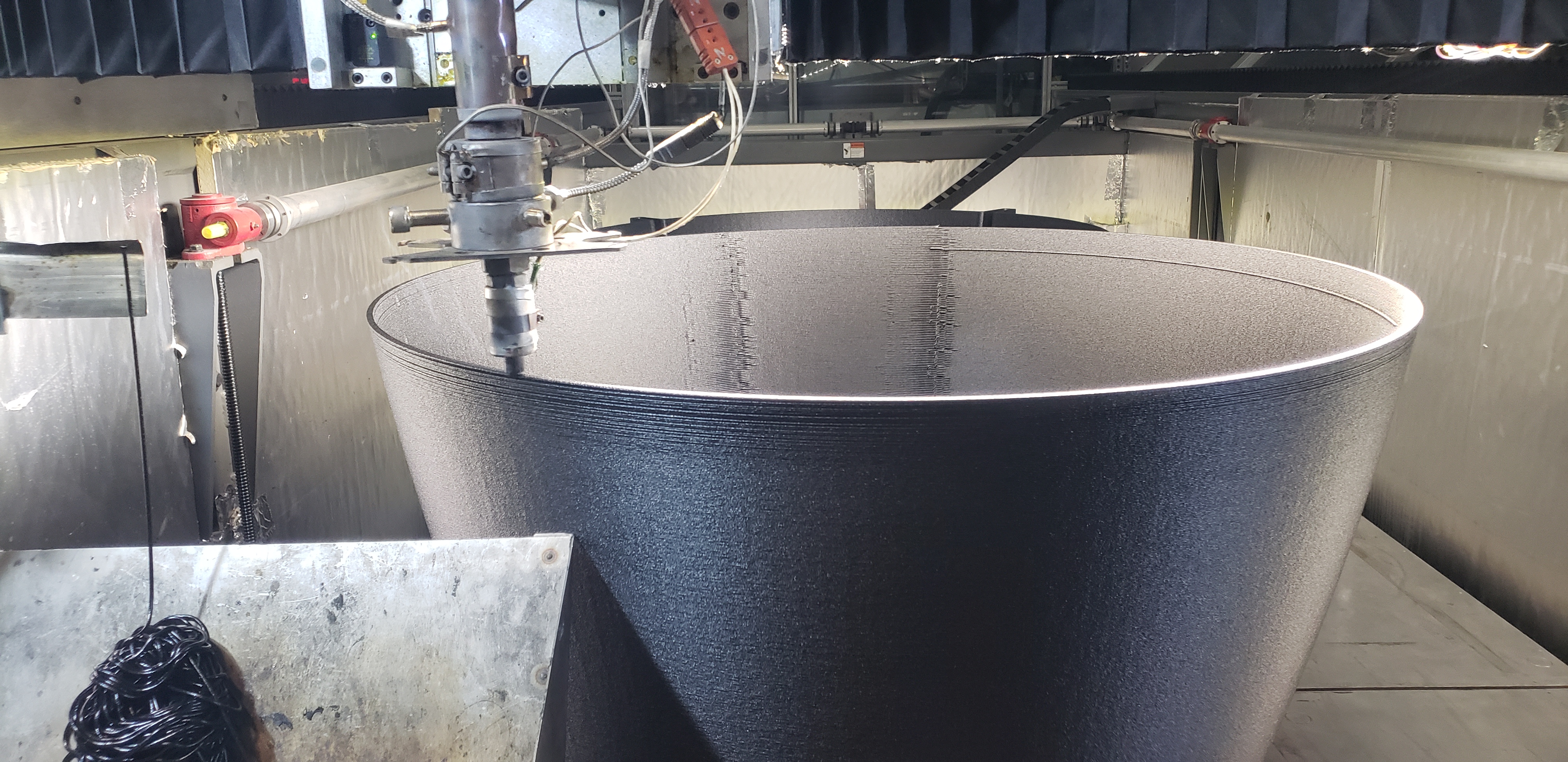
O que eles e sua equipe desenvolveram é o DIVE-LD, um AUV comercial de 19 pés de comprimento e 4 pés de diâmetro, capaz de mergulhar a 6.000 metros e viajar até 500 milhas, carregando uma carga útil de até 1 metro cúbico. Originalmente, a equipe presumiu que a estrutura final de seu veículo usaria plásticos termoformados para o casco externo. Para explorar e testar o design, a Dive Technologies conversou com o Oak Ridge National Laboratory (ORNL, Oak Ridge, Tenn., EUA) sobre o uso de impressão 3D para prototipagem rápida. Por meio do ORNL, a equipe de mergulho foi apresentada às soluções de engenharia aditiva especializadas em fabricação aditiva de grande formato (LFAM) (AES, Akron, Ohio, EUA) e começou a trabalhar com a equipe da AES em um processo de fabricação para suas formas de casco AUV.
Ao longo do trabalho nos protótipos impressos em 3D, no entanto, a Dive Technologies percebeu o potencial da LFAM para produzir rapidamente acabados componentes, não apenas protótipos. Não apenas os componentes do protótipo impressos em 3D atendem aos requisitos de peças melhor do que o esperado, mas a adoção de AM para veículos de produção também economiza custos de ferramentas, permite que a Dive produza produtos finais mais rapidamente do que usar métodos tradicionais e permite um nível novo e mais alto de personalização rápida para clientes.
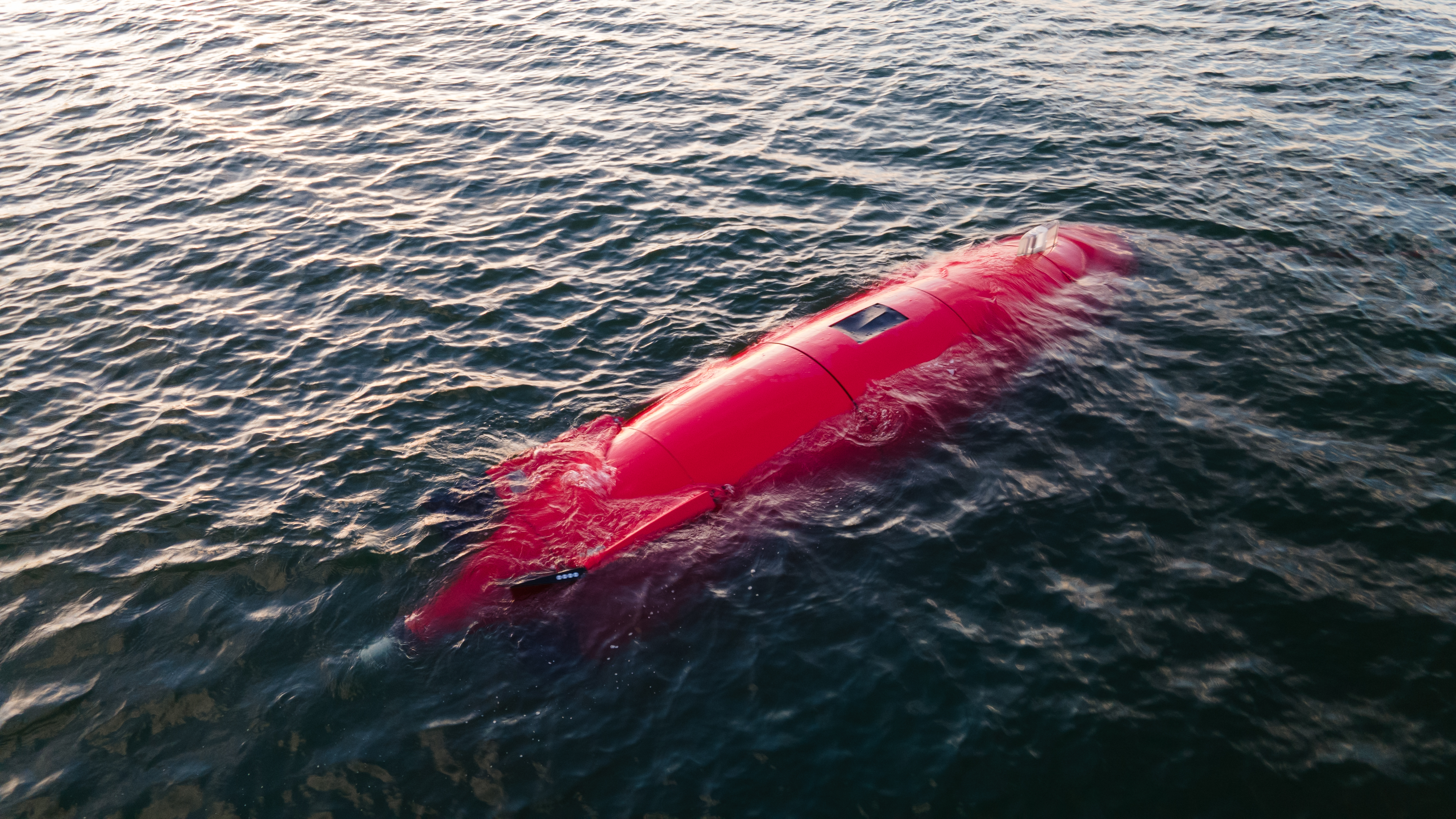
O casco externo do DIVE-LD compreende nove carenagens em forma de tubo impressas usando uma das quatro impressoras 3D da Cincinnati Inc. (Cincinnati, Ohio, EUA) Big Area Additive Manufacturing (BAAM) da AES. Essas carenagens são impressas em ABS preenchido com fibra picada fornecido pela Sabic (Riyadh, Arábia Saudita). De acordo com o cofundador e vice-presidente da AES, Andrew Bader, a AES pode imprimir todas as peças de um casco completo em menos de dois dias. Depois de entregues à Dive, as carenagens impressas em 3D são fixadas mecanicamente com quatro fixadores por carenagem e revestidas para produzir uma superfície externa hidrodinâmica e lisa. Após os testes iniciais bem-sucedidos em 2020, a Dive está construindo os primeiros veículos do cliente nesta primavera e entregará o primeiro pedido em junho de 2021.
De acordo com Russo, AM se tornou uma parte central da proposta de valor da Dive Technologies para futuros veículos e produtos. A parceria com a Dive é um grande passo para AES e também para a impressão 3D composta. Bader acrescenta:“Normalmente, quando as pessoas pensam em impressão 3D, elas pensam em protótipos, acessórios e ferramentas, então isso mostra do que mais a impressão 3D é capaz.”
Para ler mais sobre tecnologias de mergulho e AES, leia “A impressão 3D de grande formato permite uma produção rápida e sem ferramentas para AUVs”.
Fibra contínua AM e automação para projetos versáteis de lanchas
Desde que patenteou seu processo de manufatura contínua de fibra (CFM) em 2015, a Moi Composites (Milão, Itália) explorou uma gama de aplicações para sua tecnologia CFM de impressão 3D de fibra contínua baseada em deposição. As marcas registradas do CFM incluem o software de design personalizado da Moi Composites, o uso de braços robóticos, cura UV e fabricação "híbrida" - laminação composta mais tradicional sobre um núcleo estrutural impresso em 3D. Recentemente, a empresa demonstrou sua tecnologia CFM como solução para projetos de estruturas marítimas mais econômicas, rápidas e inovadoras, por meio de uma lancha demonstradora chamada MAMBO.
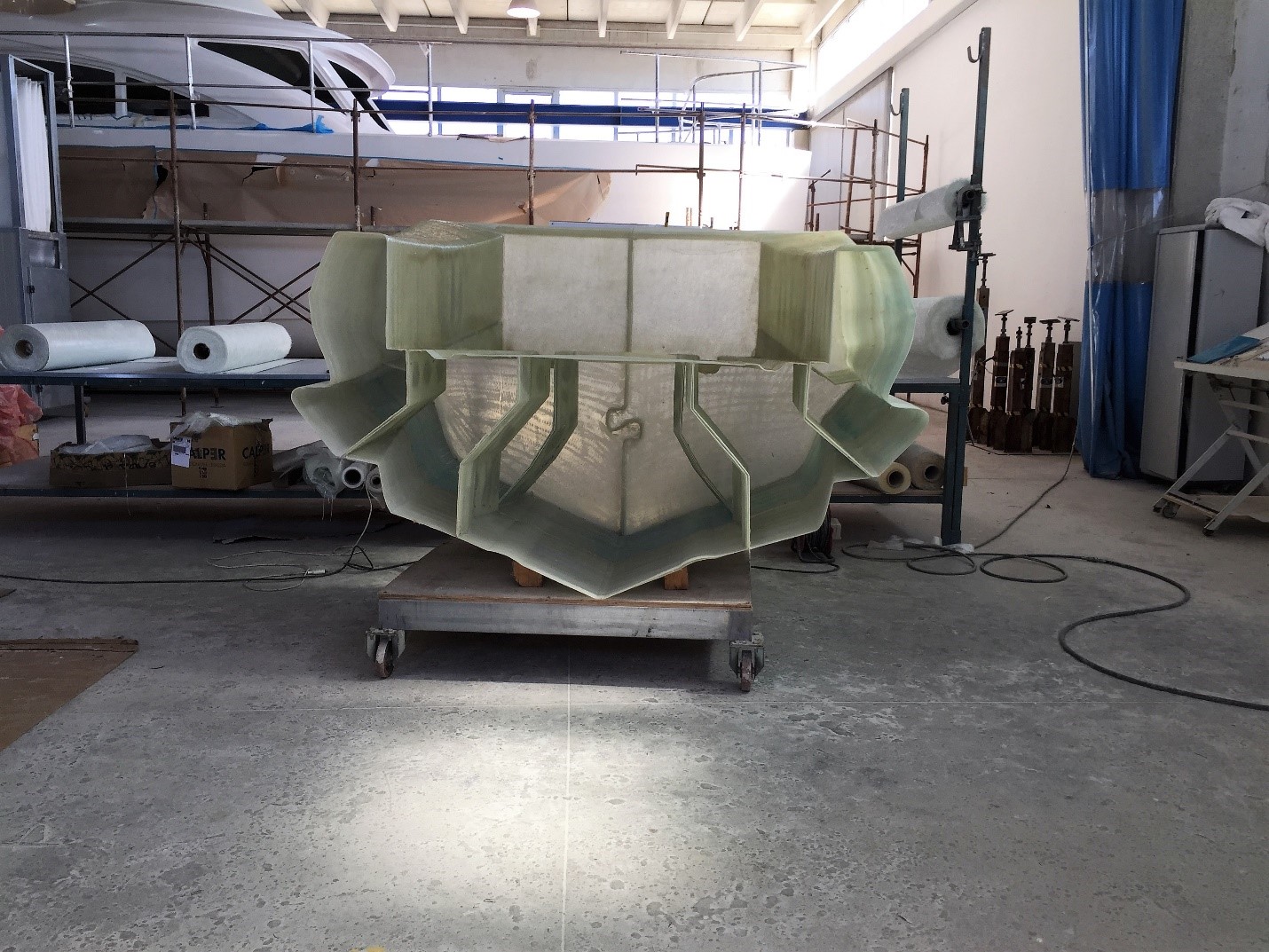
De acordo com Gabriele Natale, cofundadora da Moi Composites, ele e sua colega cofundadora Michele Tonizzo compareceram ao Genoa Boat Show em 2017 e perceberam que os custos de ferramentas e os processos tradicionais de infusão de fibra de vidro usados para muitos cascos de barco limitam a capacidade dos projetistas de explorar novos e designs mais complexos. Reconhecendo que sua tecnologia de impressão 3D de fibra contínua e sem molde pode ser uma solução capacitadora, Natale diz:“A partir daí, começamos a desenvolver um plano e começamos a nos reunir com parceiros da indústria naval”.
O barco MAMBO resultante tem 6,5 metros de comprimento x 2,5 metros de largura, com um peso seco de cerca de 800 quilos, equipado com sistema de navegação, piso de cortiça, bancos em couro branco e motor de 115 cavalos. A Moi Composites trabalhou com o estúdio de engenharia de design marinho MICAD (Lecce, Itália) no conceito de design estrutural do barco, que combina formas orgânicas em seus elementos estruturais inspirados no famoso catamarã Arcidiavolo de Sonny Levi. Os softwares de manufatura aditiva Autodesk (San Rafael, Califórnia, EUA) Fusion 360 CAD e NETFABB foram usados no projeto e na análise dinâmica de fluidos dos componentes.
O casco e o convés do barco, impressos em vidro E unidirecional fornecido pela Owens Corning (Toledo, Ohio, EUA) e resina de éster de vinil, foram projetados para serem fabricados em 50 seções individuais de tamanhos variados. Metade das seções foram impressas nas instalações da Moi Composites em Milão, e a outra metade nas instalações de fabricação avançada (ACF) da parceira Autodesk em Birmingham, a tecnologia de impressão 3D CFM da Moi Composites no Reino Unido e robôs Kuka (Augsburg, Alemanha) duplos foram usados em ambos instalações. De acordo com Dominique Müller, gerente de pesquisa da equipe de manufatura aditiva da Autodesk, o sistema CFM do centro de tecnologia da Autodesk permitiu que o barco fosse impresso rapidamente e também permitiu que a Autodesk conhecesse melhor a tecnologia que Moi dirigia remotamente usando o software Autodesk . O tempo total de impressão de todos os componentes foi de aproximadamente dois meses.
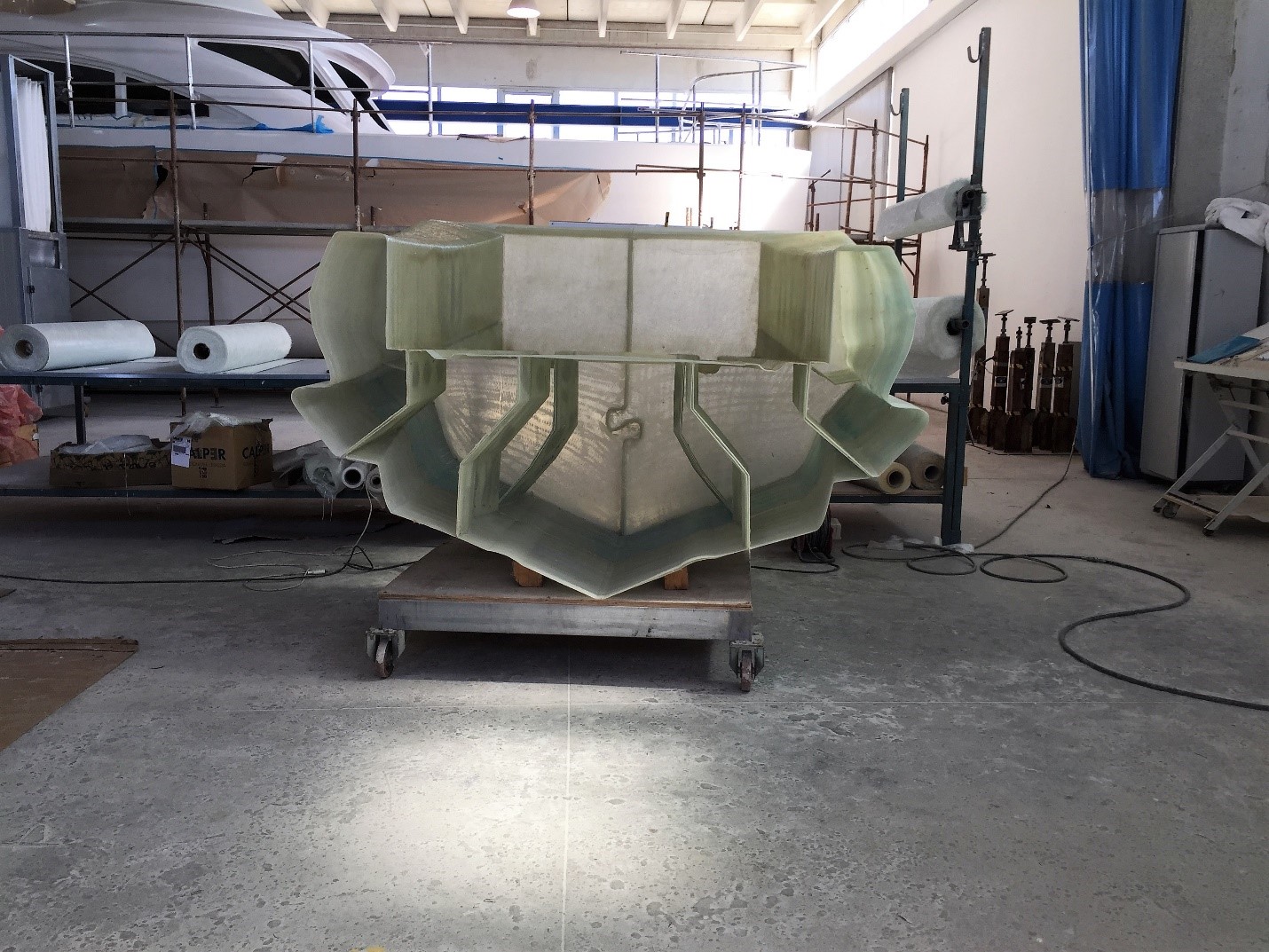
As peças impressas foram enviadas para o estaleiro Catmarine em Miggiano, Itália, onde foram montadas e coladas com adesivo. Em um processo de fabricação híbrido semelhante ao que Moi tem usado com próteses e outras peças, todo o casco foi então laminado via layup manual com uma camada adicional de fibra de vidro / poliéster com núcleo de espuma de PVC, que, segundo Natale, varia em espessura ao longo da estrutura. Depois que o casco e o convés foram totalmente montados, lixados e revestidos com gel, os parceiros da Moi Composites equiparam o barco com sistemas de propulsão, navegação e outros para completar o barco.
Os testes de mar iniciais e os testes de estabilidade foram realizados no outono de 2020, com o MAMBO atingindo até 26 nós; A Moi Composites planeja continuar os testes de mar no verão de 2021, trabalhando para a certificação do barco.

“A fabricação aditiva, a digitalização e a automação podem acelerar a criação de novos conceitos e projetos futuristas, porque para cada barco que você deseja projetar, é necessário criar um novo molde. Usando essa tecnologia, você pode modificar facilmente seu modelo 3D e imprimi-lo novamente. Isso é perfeito especialmente para barcos de curta duração ou únicos ”, diz Natale.
Para mais informações sobre MAMBO, leia “MAMBO testa as águas para impressão 3D de grandes estruturas marinhas.”
Resina
- 5 Processos de Fabricação de Aditivos Comuns
- Manufatura Aditiva vs Manufatura Subtrativa
- Vantagens da fabricação de aditivos
- Uma pesquisa sobre fluxos de trabalho de manufatura aditiva
- Henkel oferece plataforma de materiais para fabricação de aditivos
- NCAMP lança o primeiro programa de qualificação de manufatura aditiva
- Termoplásticos sustentáveis e formas de aliança de manufatura aditiva no Colorado
- 5 tecnologias que interrompem a fabricação
- Manufatura Aditiva em Eletrônicos
- Manufatura Aditiva na Aeroespacial