Avanço da caixa de asa infundida OOA
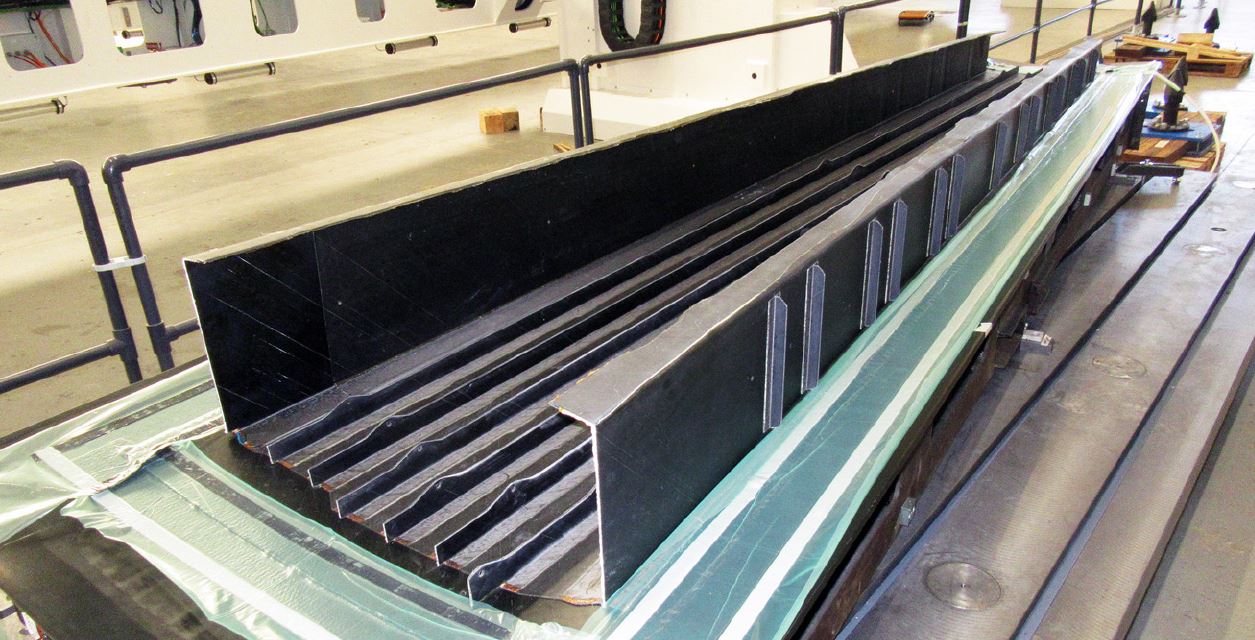
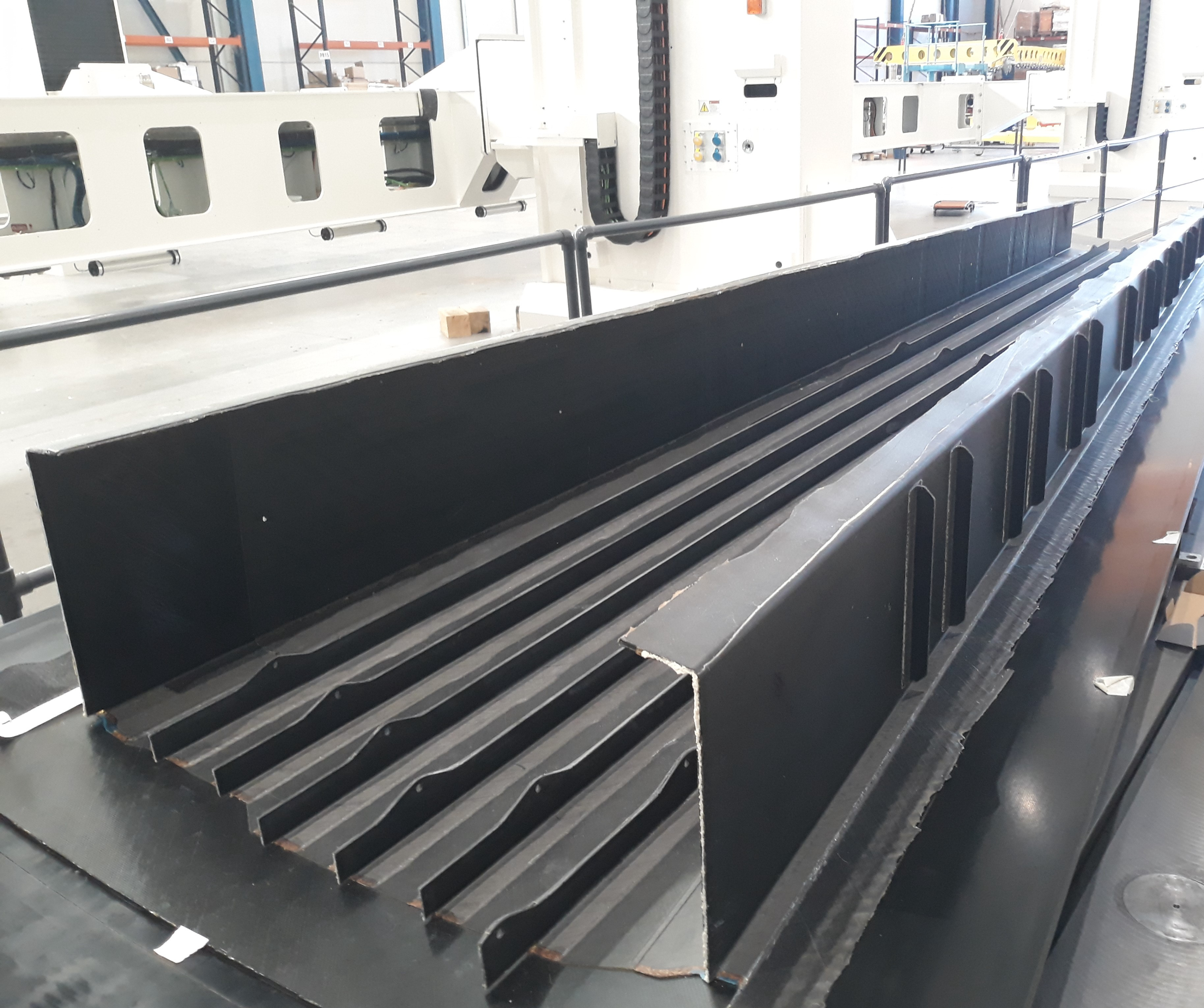
Como a indústria aeroespacial antecipa sua recuperação da pandemia COVID-19, o impulso anterior para a produção de alta taxa girou para um impulso urgente para reduzir as ameaças ambientais ao planeta e às pessoas. Esse esforço inclui limites de emissões de gases de efeito estufa (GEE), uso de energia e água e geração de resíduos que não podem ser reciclados. Embora essas iniciativas estivessem em andamento antes do COVID, sua ênfase agora é aumentada, assim como a necessidade de custos muito mais baixos para produzir estruturas compostas. O programa de aviação pan-europeu Clean Sky 2 financiou pesquisa e desenvolvimento em todas essas áreas e avançou significativamente em uma variedade de tecnologias de compósitos reforçados com fibras.
Incluído na sétima chamada de propostas da Clean Sky 2 (CFP07, outubro de 2017) está o pedido da Airbus Defence and Space (Airbus DS, Cadiz, Espanha) para uma planta piloto inovadora e flexível para produzir um demonstrador voador de caixa de asa altamente integrado usando fibra automatizada colocação (AFP) e infusão de resina líquida.
Houve outros demonstradores de caixa de asa com infusão de resina e / ou fora de autoclave (OOA), incluindo uma caixa de asa “combinada” OOA revelada pela GKN Aerospace (Redditch, Reino Unido) em 2013; a asa do Airbus A220 produzida pela Spirit AeroSystems Belfast na Irlanda do Norte usando infusão de transferência de resina em uma autoclave; e a asa OOA produzida pela AeroComposit (Moscou, Rússia) para o MS-21 jato. No entanto, todos eles montaram revestimentos e longarinas reforçadas com vigas compostas discretas com fixadores mecânicos (consulte “O caminho para asas OOA com fixadores mínimos”).
A caixa da asa solicitada pelo Airbus DS no Clean Sky 2 deveria dar um passo à frente, integrando a pele inferior endurecida com longarinas reforçadas dianteiras e traseiras, permitindo um módulo mais completo sem prendedores a serem encaminhados para montagem com os componentes restantes da asa.
Esta caixa tipo asa também usaria fitas de fibra de carbono secas estreitas (0,25 ou 0,5 polegada de largura) e de alta temperatura (180 ° C T g ) resinas de cura, mas com economia de energia, sistemas de aquecimento de baixo custo e controle digital baseado em sensor e simulação para prever e gerenciar o processamento, encurtar os loops de tentativa e erro durante o desenvolvimento e permitir o treinamento rápido do pessoal de manufatura. Esta digitalização iria evoluir para incluir um aplicativo móvel de realidade aumentada (app) que também fornece manuais de usuário e manutenção, definição de sequência de processo, processo sem papel e rastreamento de peças e projeção de modelos CATIA na peça para auxiliar na colocação precisa de pré-formas de reforço, inserções de ferramentas e placas de vedação de polímero reforçado com fibra de carbono (CFRP).
Talvez o mais exigente, este projeto exigia que todas as ferramentas e equipamentos de manufatura fossem portáteis e flexíveis, fáceis de implantar em qualquer local de manufatura e adaptáveis para outros projetos de peças e atualizações conforme tecnologias mais avançadas de ferramentas, aquecimento e controle de processo de compósitos 4.0 se tornassem disponíveis.
Conforme explicado pelo gerente de tópico Luis Rubio, chefe de engenharia de desenvolvimento de compósitos - tecnologia e processo da Airbus DS, “O objetivo final do projeto é demonstrar que uma tecnologia alternativa (para pré-impregnação e autoclave) com custos mais baixos, prazos de entrega reduzidos e a pegada ambiental pode atingir tolerâncias de design e níveis de qualidade semelhantes. ”
MTorres (Torres de Elorz, Espanha) respondeu, candidatando-se sem parceiros. “Tínhamos todos os recursos internos:AFP, infusão, materiais de fita seca e automação”, explica Sebastian Diaz, gerente sênior de tecnologias aplicadas de compósitos na MTorres. A empresa foi premiada com o projeto Innovative Infusion Airframe Manufacturing System (IIAMS), financiado por meio do programa Horizon 2020 da União Europeia sob o acordo de subvenção nº 820845, e começou a trabalhar em outubro de 2018.
Demonstrador de caixa da asa externa
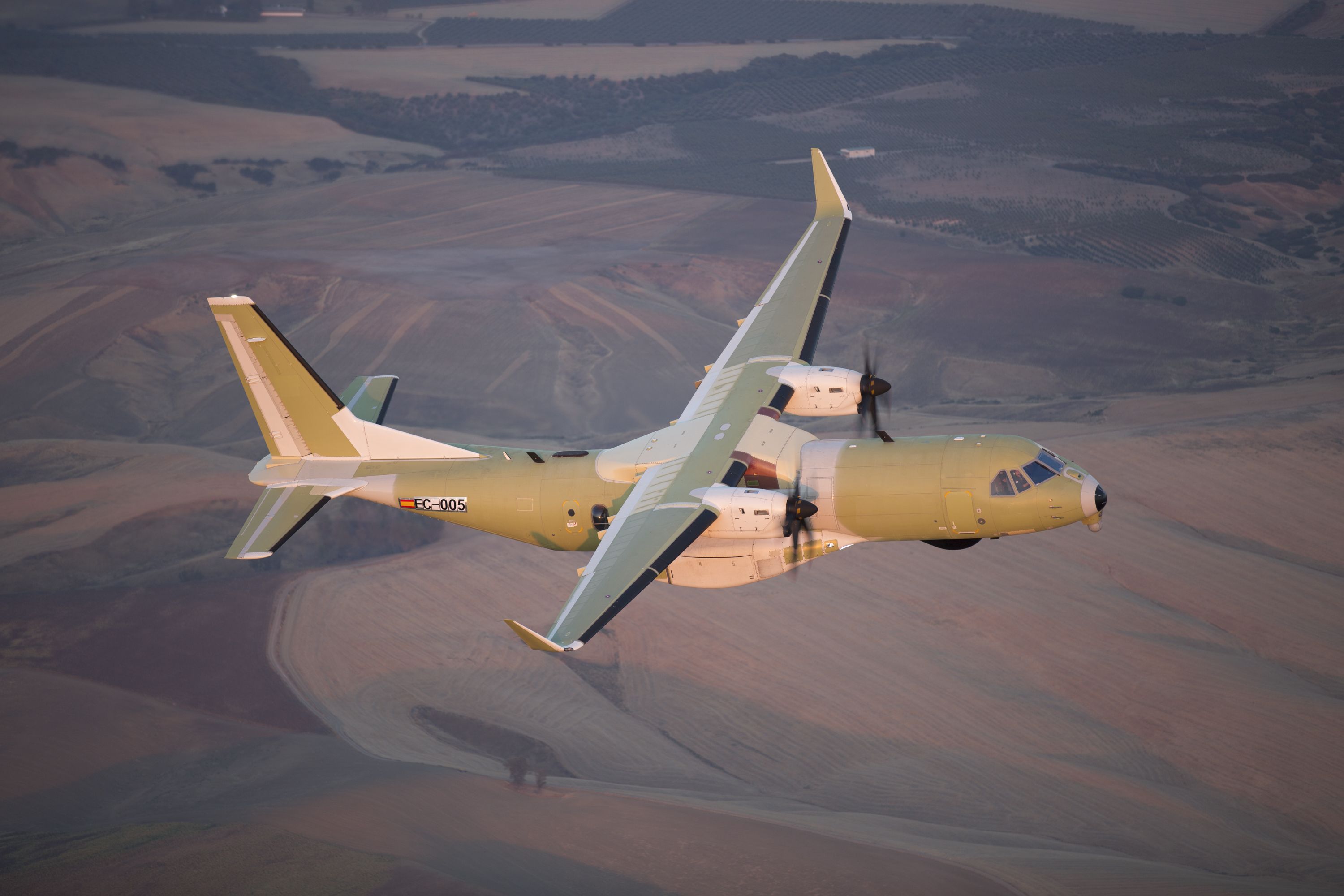
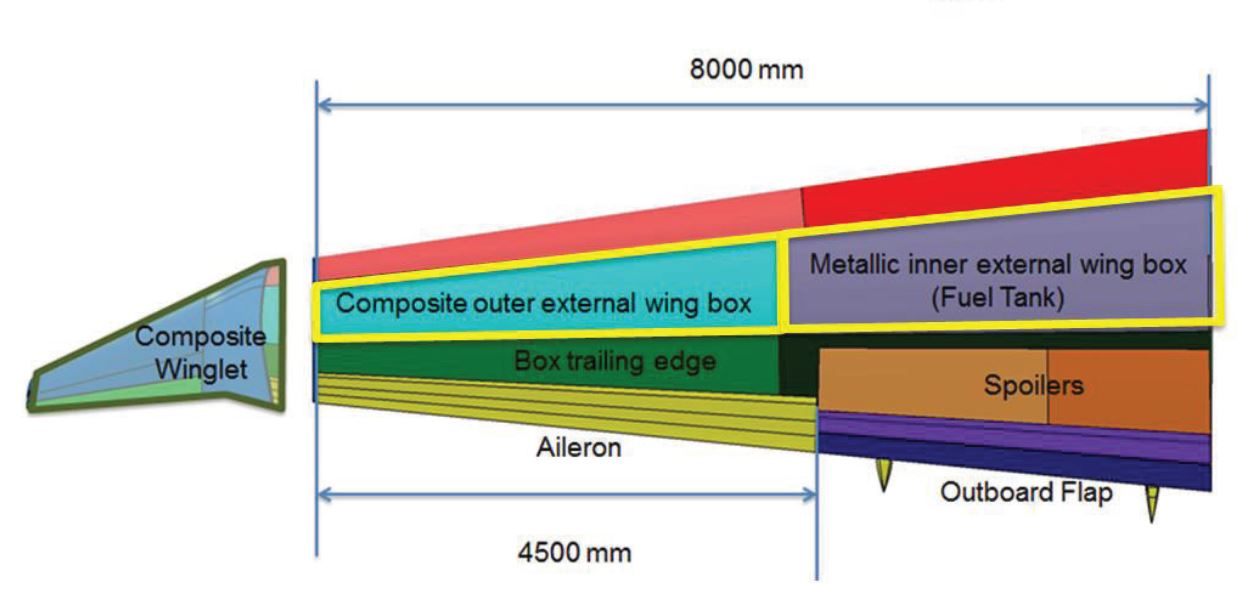
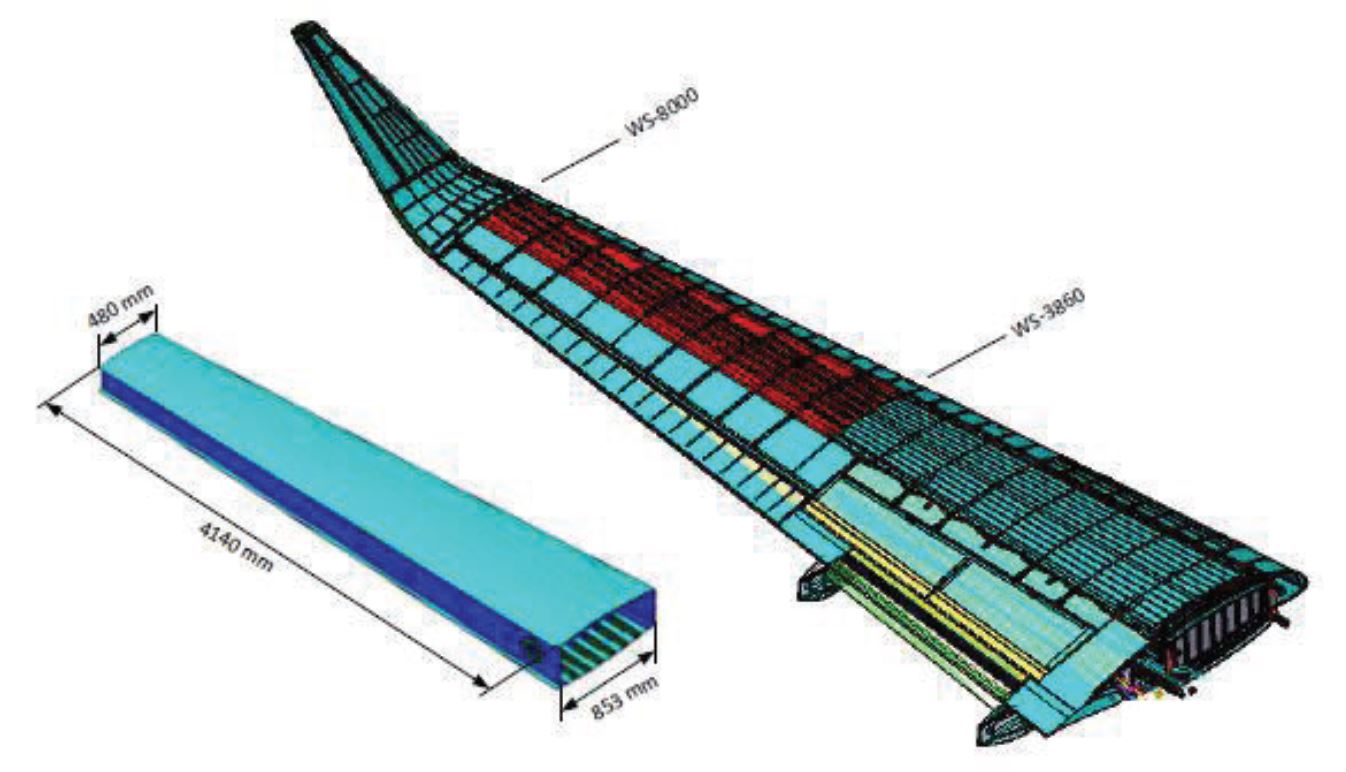
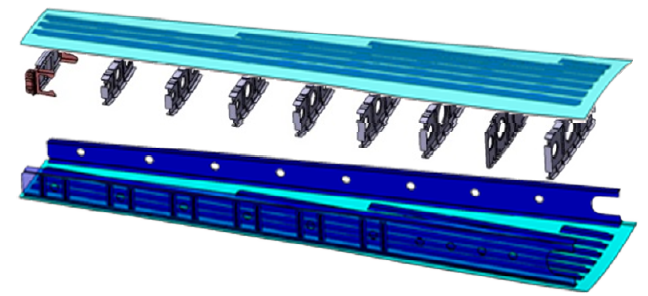
O demonstrador que a Airbus DS escolheu foi uma caixa de asa externa baseada em seu transporte militar turboélice duplo C-295 (Fig. 1), produzido em San Pablo, Sevilha, Espanha. Esta caixa de torque externa composta de 4,14 metros de comprimento combina com um metal interno caixa de torção. A caixa de asa composta também se conecta a um winglet, borda de ataque e borda de fuga.
“Deveríamos fabricar dois demonstradores de 4 metros de comprimento, as asas direita e esquerda, que serão instalados para testes em vôo”, diz Diaz. “A fabricação deveria ser um processo único, sem ligação secundária. Fizemos apenas o “U”, compreendendo a pele inferior com seis longarinas integradas e as longarinas de cada lado. A pele, longarinas e longarinas variam em espessura. A forma em J das longarinas e a integração de seus reforços eram bastante difíceis de fabricar. Também enfrentamos o desafio de como manter tolerâncias estreitas e geometria precisa com esse processo de fabricação. Essa precisão é crítica, especialmente na raiz para montagem na caixa da asa interna e também no winglet. ”
O design da manufatura industrial inovadora foi desenvolvido na MTorres, enquanto a Airbus DS forneceu as especificações do design da peça. “Trabalhamos com facilidade juntos para projetar o melhor processo de fabricação, verificando se esse projeto poderia ser produzido pelo nosso processo e vice-versa”, diz Diaz.
Centro automatizado de infusão térmica (ACTI)
De acordo com as especificações do Airbus DS, todas as ferramentas e equipamentos de fabricação usados para produzir a caixa da asa devem ser portáteis, capazes de ser transportados para outras instalações com veículos padrão e montados rapidamente sem medidas especiais. Isso levou ao desenvolvimento do centro automatizado de infusão térmica (ACTI), que realiza a formação de cortinas a quente das longarinas e longarinas; infusão das longarinas, longarinas e pele; e ciclos de cura. Formação de cortina a quente (HDF) - desenvolvida como redução de volume aquecido em aeroestruturas e como pré-formação aquecida fora do aeroespaço - remove vazios em layups e converte espaços em 2D para as longarinas e longarinas em pré-formas moldadas (consulte “Formação de cortina a quente”).
O ACTI tem uma área interna útil de aproximadamente 5,5 x 2,2 metros e se parece com um sistema HDF tradicional, com estrutura de aço e uma metade superior que é elevada e abaixada eletronicamente, completa com travamento e outros dispositivos de segurança. A ferramenta de cura e várias ferramentas de moldagem por cobertura a quente são posicionadas dentro do ACTI. “Nenhuma pressão é aplicada, apenas vácuo”, observa Diaz. “O ACTI usa ar aquecido com fluxo de ar que foi definido para fornecer rápida transferência de calor tanto na formação da cortina quente quanto nos processos de infusão”.
Ele também observa que o sistema é autonivelante. “A rigidez da estrutura ACTI (e da ferramenta de cura) foi projetada para atender às tolerâncias sob cargas operacionais em uma condição simplesmente apoiada em apenas duas seções de suporte”, explica Diaz. “Isso significa que a precisão dimensional é mantida ao repousar no chão, sem necessidade de nivelamento ou outro ajuste geométrico. O ACTI também apresenta baixo consumo de energia e baixos custos de fabricação. ”
Este último se deve, em grande parte, à substituição da montagem de múltiplas peças curadas pela montagem de múltiplas pré-formas, que são então infundidas e curadas em uma única estrutura integrada. “A ferramenta de cura também é a ferramenta de montagem”, diz Diaz. “Todos os elementos são pré-formas secas montadas na ferramenta de cura e, em seguida, co-infundidas em um processo de injeção única.” Nenhum gabarito de montagem é necessário e tolerâncias estritas são alcançadas por meio de elementos inovadores nas ferramentas.
Outro aspecto importante dessa abordagem é remover os testes destrutivos e não destrutivos (NDT), em vez de confiar nos dados do processo coletados durante as várias etapas de fabricação para verificar a qualidade do processo e sinalizar os parâmetros fora das especificações. Os sensores usados com o ACTI coletam temperatura, vácuo, fluxo de resina e estado de cura. “Tanto a temperatura do ar quanto as temperaturas das peças são monitoradas”, diz Diaz. “O ferramental tem termopares integrados que rastreiam a temperatura para os moldes e as superfícies das peças.” Todos os dados são registrados, analisados e usados para imprimir gráficos e ajudar a orientar as decisões de fabricação.
“Tanto no IIAMS quanto em projetos futuros, os dados ajudam a melhorar a configuração do processo nos estágios iniciais”, explica Diaz. O fluxo da resina e o estado de cura são monitorados usando sensores dielétricos Netzsch (Selb, Alemanha), instalados diretamente nas ferramentas de cura CFRP. “Precisávamos de sensores sem contato para a pele porque não há contato direto entre a resina e o molde”, diz Diaz. “Os sensores monitoram a mudança do campo dielétrico conforme a resina chega e então se torna sólida durante a cura. Usamos esses dados para encurtar o ciclo de cura. ”
Posteriormente no projeto, os sensores e o ACTI foram combinados com uma interface homem-máquina (HMI) desenvolvida pela MTorres, que permite o verdadeiro controle do processo a partir de um computador, incluindo vácuo e temperatura, bem como o fluxo de resina via válvula de alimentação. O objetivo, de acordo com a Airbus DS, é avançar a produção em massa de estruturas primárias compostas integradas, tornando o processo mais simplificado e inteligente.
Ferramentas leves e portabilidade
A MTorres produziu dois conjuntos de moldes - um para a asa direita e outro para a asa esquerda. “As peças com geometria idêntica, como reforços, tinham apenas um conjunto”, observa Diaz. “Outras ferramentas foram compartilhadas, quando possível.”
Uma única ferramenta de cura de uma peça foi usada para formar a forma 3D da pele, na qual todas as outras pré-formas foram localizadas. Medindo cerca de 4,5 metros de comprimento, as versões direita e esquerda desta ferramenta foram feitas em CFRP, diz Diaz. “Isso facilita a manutenção das tolerâncias porque projetamos o ferramental com o mesmo layup e processamento das peças, de forma que o CTE fica muito próximo ao da peça final. Essas ferramentas de cura CFRP também são leves, com cerca de 200 kg e, portanto, móveis com uma pequena empilhadeira elétrica. Isso seria impossível se usássemos metal para uma ferramenta de 4,5 metros de comprimento ”.
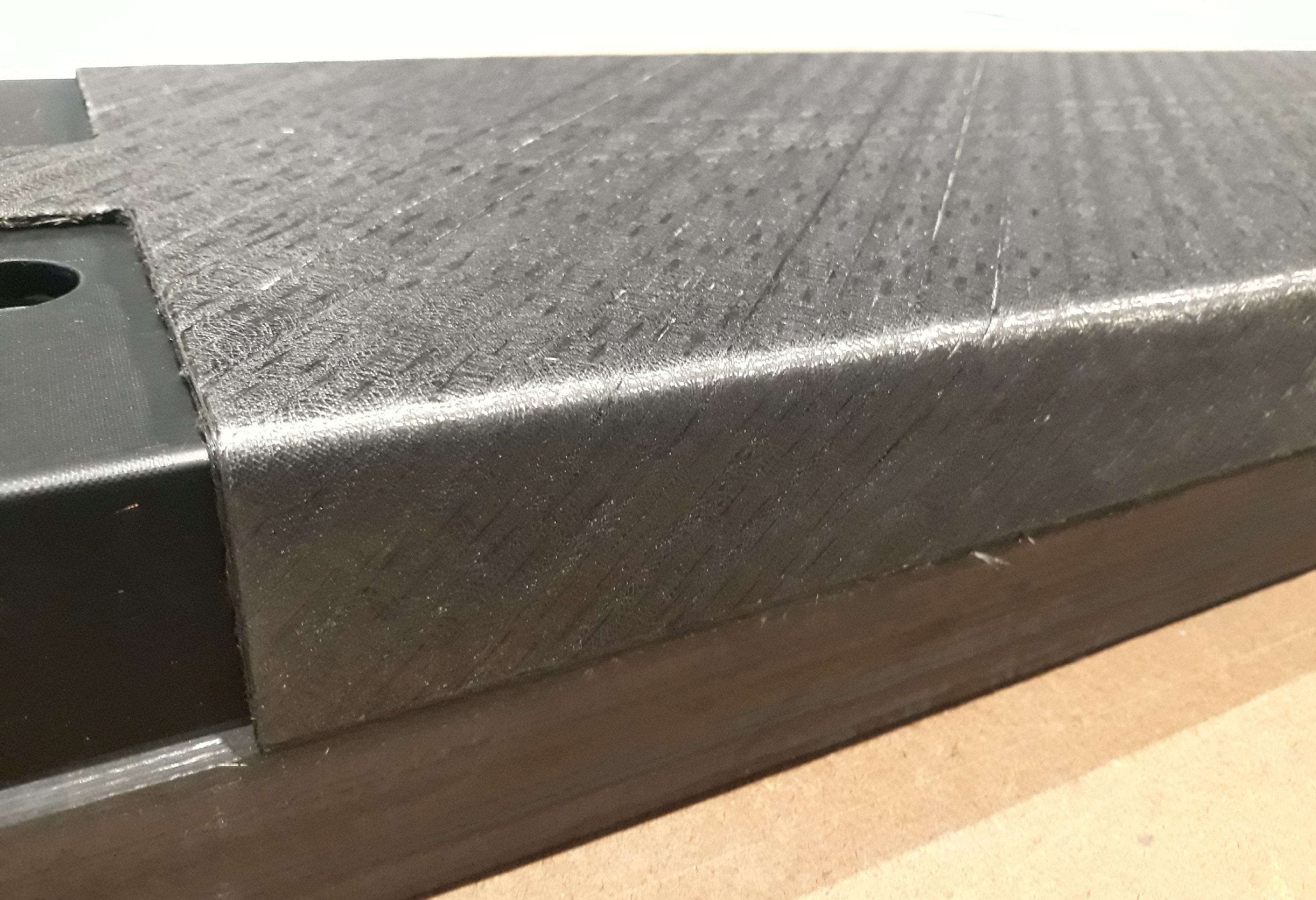
O resto das ferramentas - cauls, posicionadores e ferramentas HDF - eram facilmente gerenciadas à mão. A HDF das longarinas, longarinas e pré-formas de reforço das longarinas usava ferramentas masculinas (IML), também feitas de CFRP. Durante o uso, eles foram montados em uma mesa de alumínio e colocados dentro do ACTI.
AFP usando nova fita de fibra seca
Todos os elementos estruturais da caixa da asa - pele, longarinas, longarinas, reforços das longarinas - foram produzidos usando a tecnologia MTorres AFP para fitas de fibra seca. “A chamada de proposta dizia para usar materiais rápidos e baratos”, diz Diaz. “Mas as fitas de fibra seca disponíveis comercialmente, especialmente de fornecedores maiores, não eram tão fáceis de comprar e tínhamos a experiência para fazer nosso próprio material (consulte“ Nova fita seca para compósitos moldados líquidos ”). Portanto, usamos nossa fita de fibra de carbono seca de 0,5 polegada de largura e 300 gramas por metro quadrado (g / m²) feita de fibra Mitsubishi Rayon (Tóquio, Japão) 50K de alta resistência (HS). Nossa fita foi projetada para facilitar e funcionar bem durante a infusão, mas também durante o layup usando nossos cabeçotes AFP. Conhecemos todos os parâmetros para layup AFP, formação de cortina a quente e infusão de resina e, se precisássemos fazer pequenas alterações, poderíamos porque tínhamos a linha de fabricação de fita disponível. ”
A MTorres também testou seu processo de fabricação de caixa de asa com fita de 200 g / m² da Hexcel (Les Avenières, França) feita de sua fibra de módulo intermediário (IM). “Embora nosso processo possa funcionar bem com os dois tipos de fitas”, diz Diaz, “durante a fase de desenvolvimento, foi mais fácil e barato colocar nosso material em comparação com o material disponível comercialmente - a largura e a rigidez foram projetadas para que seu comportamento de os carretéis para a mesa foram suaves e rápidos. Também estava disponível. ”

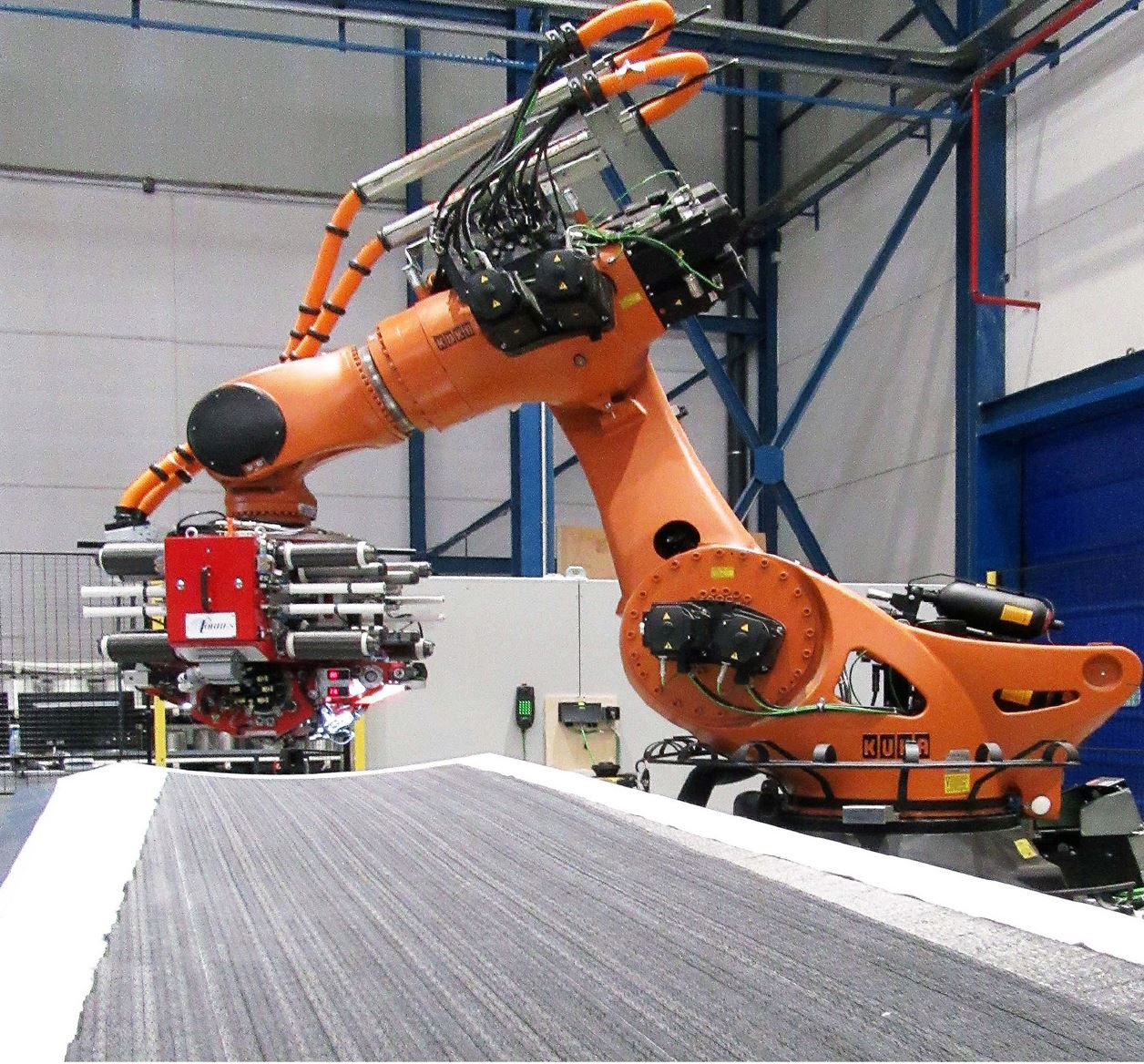
Etapa 1. AFP foi usado para colocar o revestimento da caixa da asa (mostrado aqui), bem como espaços em branco 2D para longarinas, longarinas e reforçadores de longarina. Crédito da foto, todas as etapas: Projeto IIAMS, Airbus Defense and Space, MTorres.
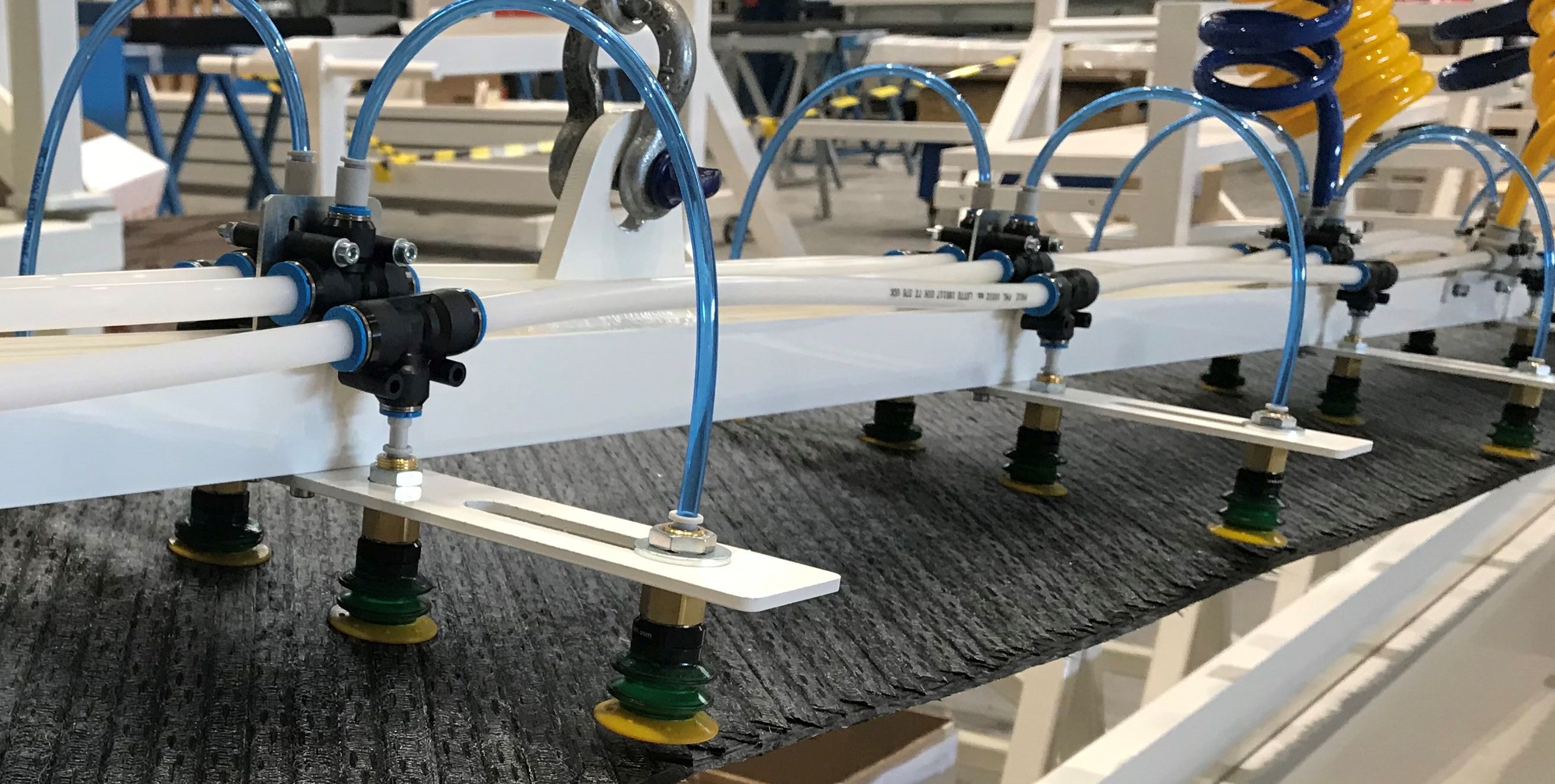
Etapa 2. Os espaços em branco de fita plana foram transportados da mesa layup para as ferramentas de formação de cortinas quentes.
Ele observa que duas estratégias foram seguidas para AFP:uma para a parte inferior da pele e outra para as longarinas, longarinas e reforços da longarina. A pele (3-6 milímetros de espessura) foi colocada na forma 3D final na parte superior da ferramenta de cura (Etapa 1), usando uma membrana semipermeável - patenteada pela Airbus em sua infusão de processo assistido por vácuo (VAP). As longarinas, longarinas e reforçadores das longarinas foram colocadas como peças planas (2D) em uma mesa a vácuo e, em seguida, movidas para as ferramentas HDF para atingir sua forma 3D final (Etapa 2).
Pré-formação aquecida
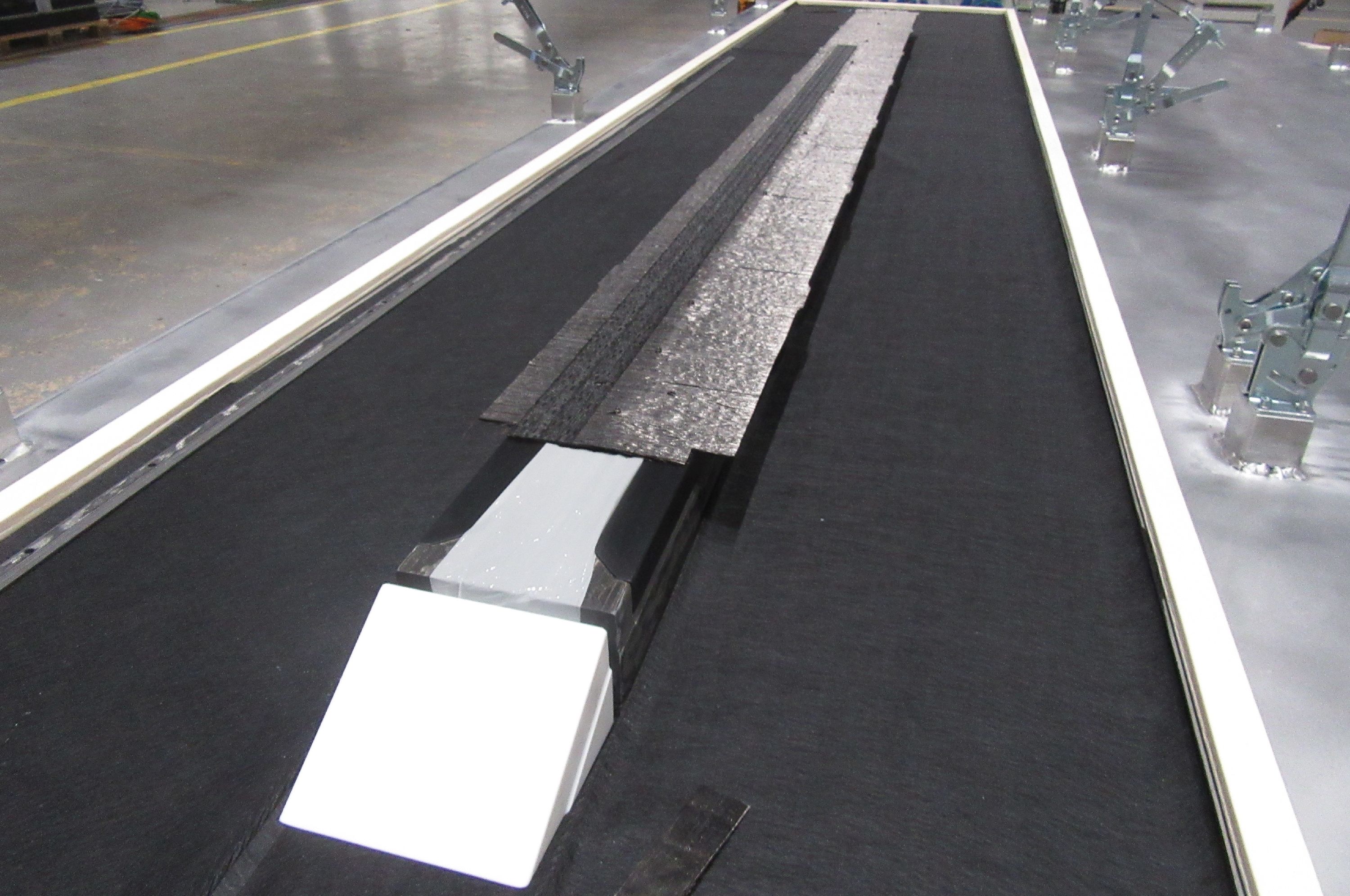
Etapa 3. O espaço em branco da longarina é colocado em cima da ferramenta HDF masculina.
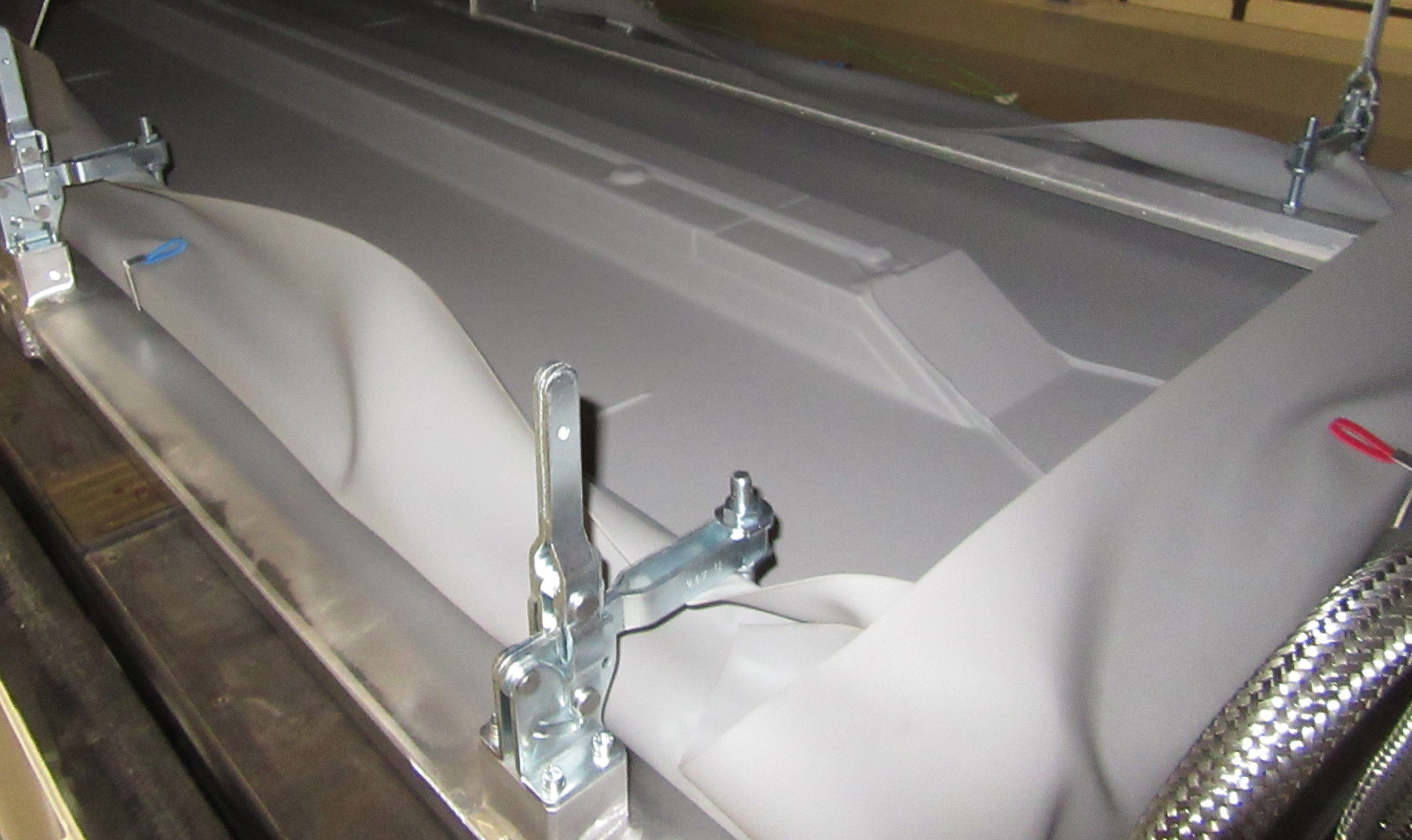
“Nós movemos os blocos planos para as longarinas, longarinas e reforçadores de longarina da mesa layup para a estação de conformação a quente usando um pórtico com pinças a vácuo”, explica Diaz. “O sistema automatizado pode mover os espaços em branco e colocá-los nas ferramentas de conformação macho [Etapa 3] sem criar rugas.” As ferramentas de conformação foram instaladas em uma mesa de conformação de alumínio, que foi colocada no ACTI. Um saco de silicone a vácuo reutilizável (Mosites Rubber Co., Fort Worth, Texas, U.S.) foi colocado no topo dos espaços em branco, que foram então aquecidos no ACTI a 130 ° C e moldados usando pressão de vácuo (Etapa 4). “O vácuo foi aplicado suavemente seguindo uma rampa predefinida por meio de uma válvula de controle quando o ponto de ajuste da temperatura foi atingido”, diz Diaz.
Ele observa que as fitas secas são mais fáceis de pré-moldar / moldar a quente, “porque a ligação entre as camadas é mais macia do que nos pré-impregnados. Apesar de ser um material seco, é um HDF / redução de volume aquecido em que a pré-forma resultante mantém a forma graças aos aglutinantes incluídos nas fitas. ”
Para as longarinas e reforçadores de longarina, os espaços em branco foram formados em dois Ls, que foram então colocados costas com costas na ferramenta de cura para formar longarinas / reforçadores. Cada uma das seis longarinas de pele é diferente e requer espaços em branco de diferentes formatos para criar as pré-formas. Cada um dos 24 reforçadores da longarina também tem um comprimento diferente.
As longarinas J dianteiras e traseiras compreendem uma estrutura formada em C, voltada para o interior da caixa da asa, e outra estrutura formada em Z voltada para fora - as duas são colocadas costas com costas. As longarinas também têm pés em forma sinusoidal do lado de fora da caixa da asa (seta na etapa 7). “Cortamos a forma dos pés da longarina na mesa de layup plana antes de mover a peça bruta para a estação de formação”, diz Diaz. “Nada poderia ser aparado ou fresado posteriormente nesta área. Os espaços em branco foram colocados diretamente na ferramenta de conformação macho com os pés da longarina no lado esquerdo da ferramenta e o flange superior no lado direito. ”
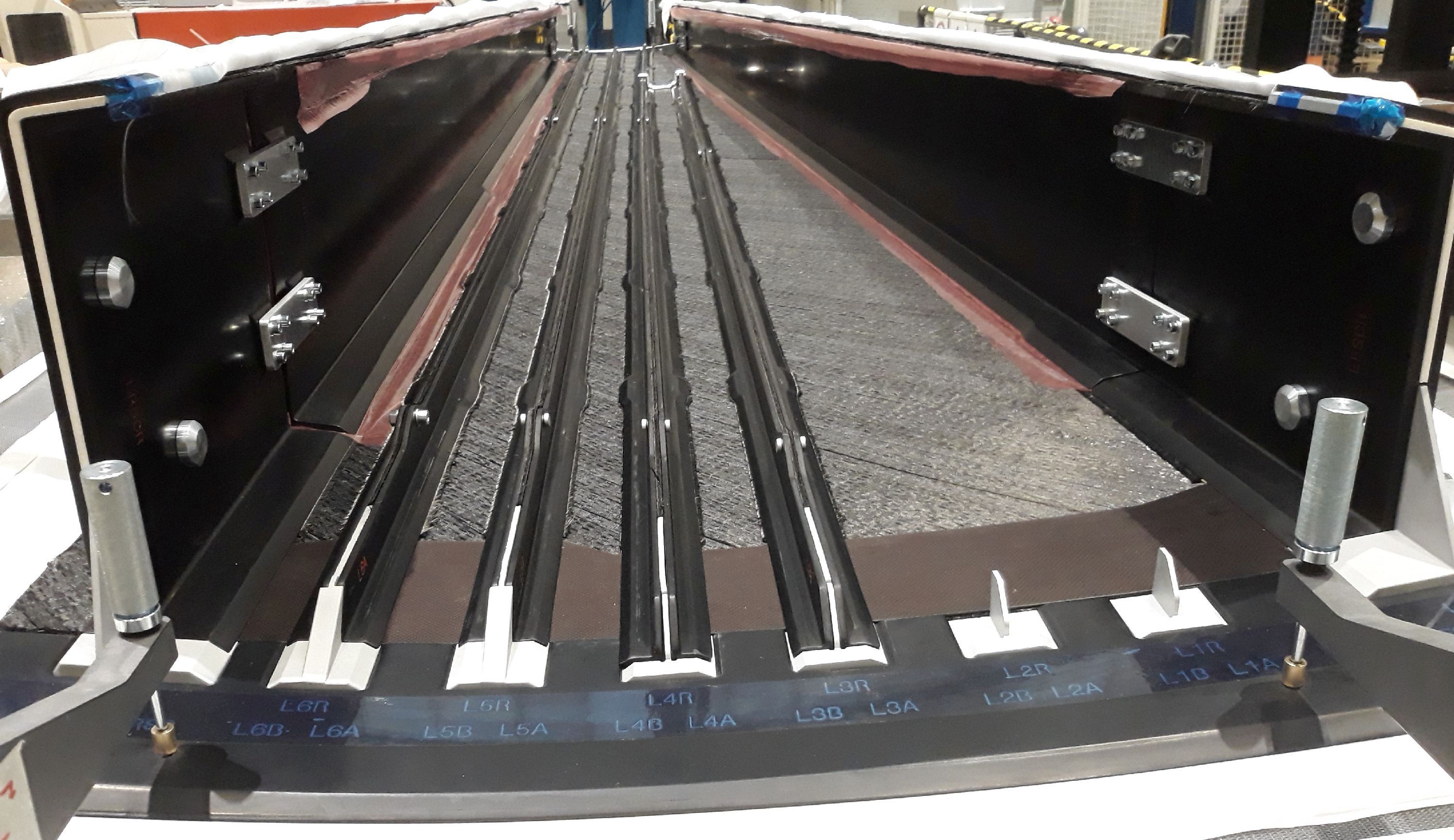
Fig. 3. Colocação precisa da pré-forma. Pré-formas para longarinas e longarinas foram posicionadas usando cilindros metálicos gêmeos (vistos à esquerda e direita), posicionadores brancos e uma vedação CFRP com recortes para longarinas / posicionadores. Crédito da foto: Projeto IIAMS, Airbus Defense and Space, MTorres.
Infusão única
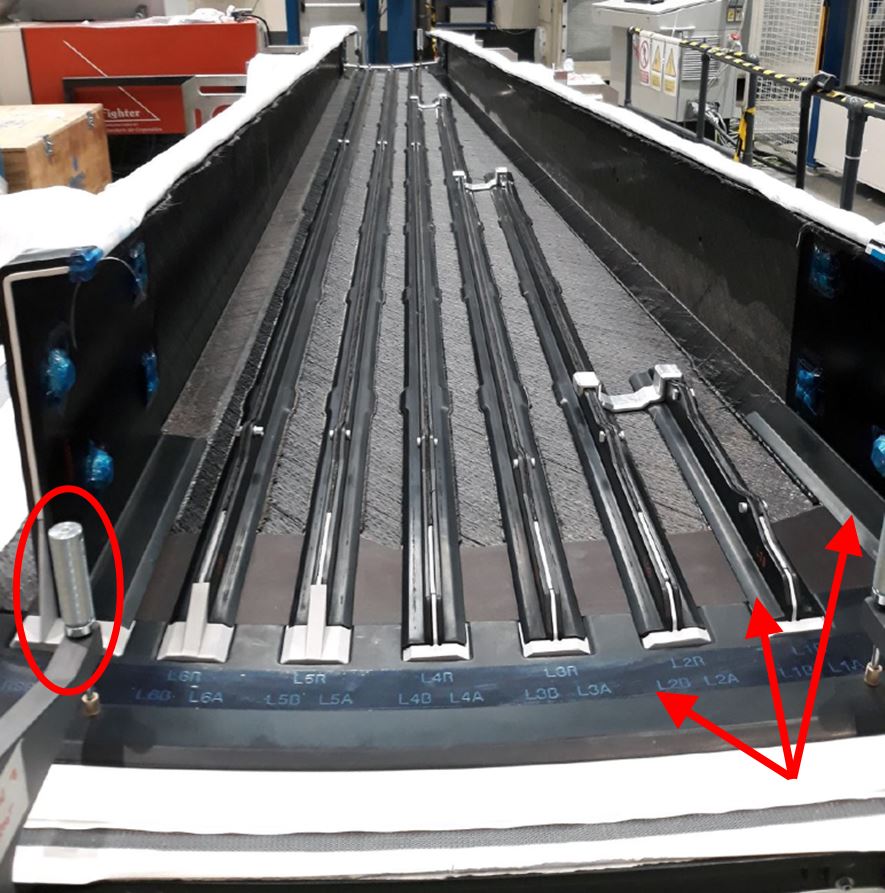
Etapa 5. Pré-formas de longarina e longarina foram colocadas na pele inferior, auxiliadas por cilindros ( circulados ) e elementos de posicionamento brancos. Cauls CFRP preto ( setas ) também foram usados para ajudar a posicionar longarinas e colocado em cima de longarinas e longarinas.
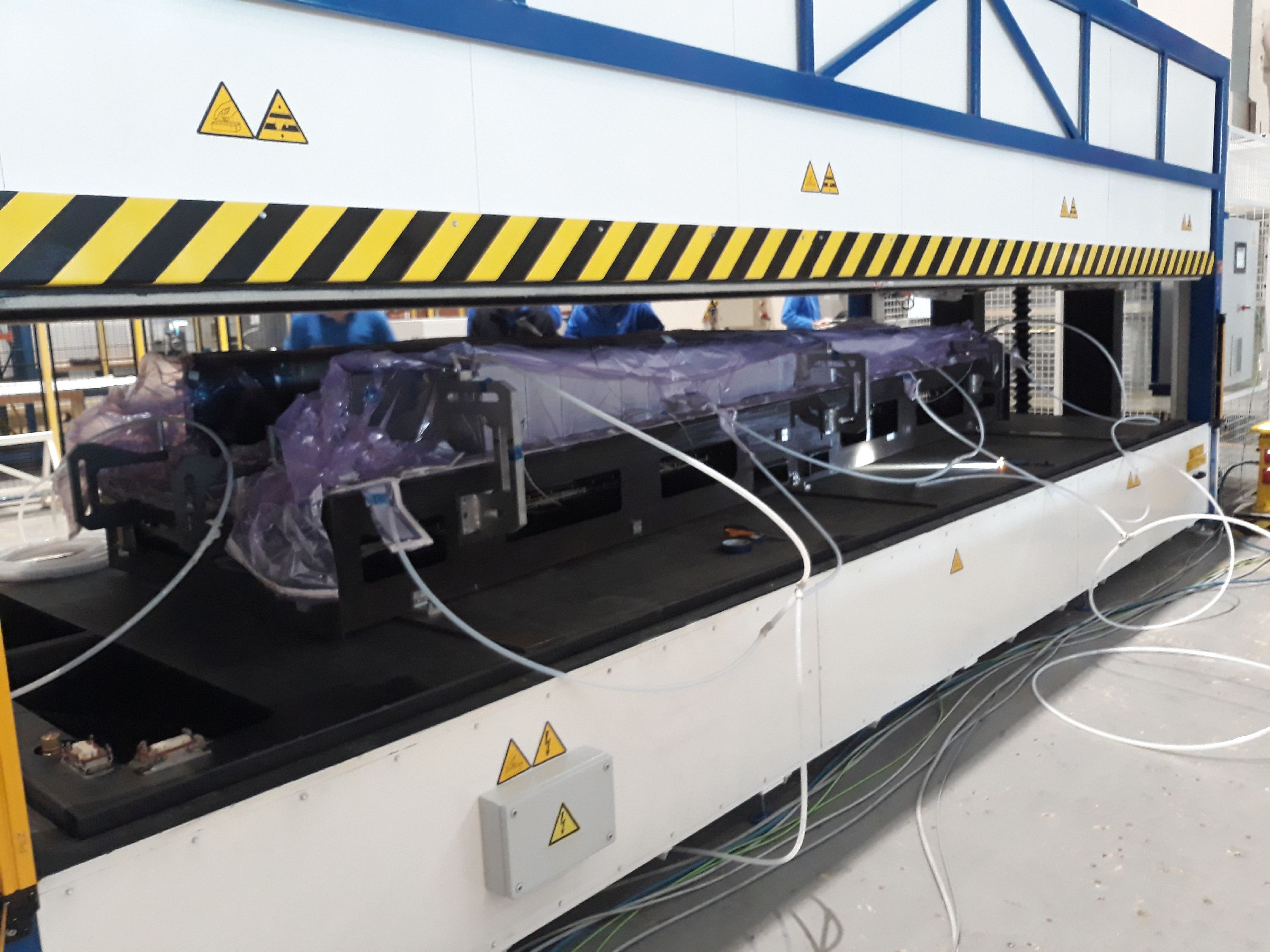
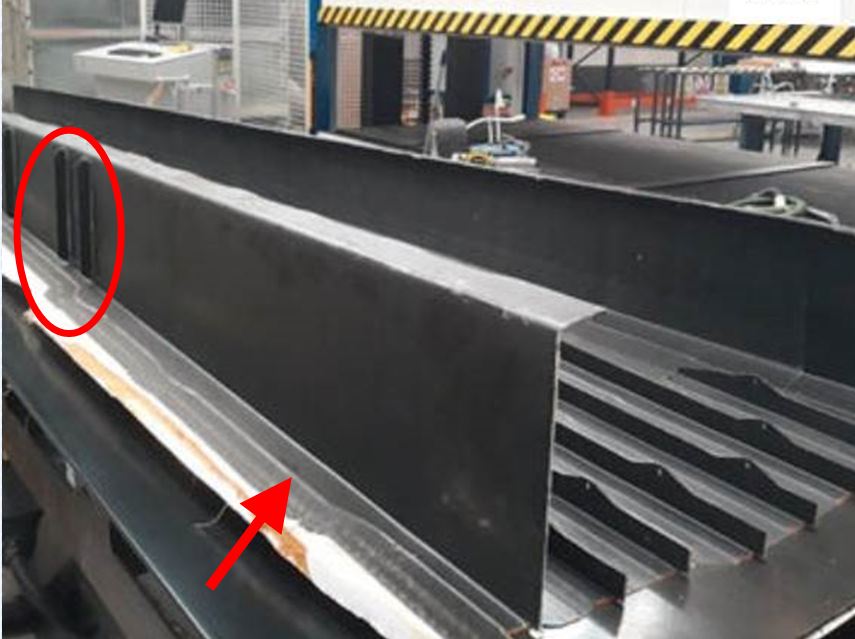
Etapa 7. O demonstrador inicial concluído em MTorres mostra o J-spar com dois reforçadores de costela ( circulado ) e seus pés sinusoidais ( seta )
A próxima etapa foi colocar as pré-formas da longarina, da longarina e do reforçador da longarina na pele inferior da asa já colocada (Etapa 5). “Estávamos indexando cada pré-forma à medida que a colocávamos na pele e na ferramenta de cura”, diz Diaz. Cilindros que atuam como elementos de localização podem ser vistos no final da longarina à esquerda da Etapa 5 e no final de ambas as longarinas na Fig. 3. Essas imagens também mostram dispositivos de posicionamento branco para longarinas e J-longarinas. Havia 13 desses posicionadores na montagem final da pré-forma e cada um era diferente.
As placas Caul também foram uma parte importante do sistema de localização e colocação da pré-forma. Eles serviam ao propósito tradicional de manter pressão e temperatura uniformes em regiões de layups complexos e / ou geometria, mas também seriam essenciais para a infusão, conforme discutido abaixo. Uma placa de vedação de CFRP preta com recortes para as pré-formas das longarinas pode ser vista no final das longarinas e longarinas na Etapa 5 e na Fig. 3.
“A localização das pré-formas das longarinas depende da localização dessa vedação”, explica Diaz. “A tecnologia digital que desenvolvemos para monitorar e controlar o processo de fabricação incluía um aplicativo de realidade aumentada que projetava os modelos CATIA no layup. Isso foi usado para ajudar a orientar a colocação das placas de calafetagem, elementos de posicionamento e, em seguida, pré-formas. Também mostrava as próximas etapas a serem executadas. O aplicativo permite o autossuporte em tablets para que todos os funcionários tenham acesso fácil a todas as informações ”.
Um conjunto final de placas de caul CFRP pretas foi então colocado no topo das pré-formas L para as longarinas e também ao longo da parte interna e externa de cada longarina em J, estendendo-se para cima no flange e para baixo no pé do lado de fora do caixa de asa, conforme mostrado na Etapa 5 e na Fig. 3. “As peças também utilizam uma espécie de placa de calafetagem no lado interno nas extremidades, a fim de obter maior precisão nas áreas de junta”, diz Diaz. “Todas essas placas de vedação foram usadas durante o processo de HDF e permaneceram presas às pré-formas durante o layup.”
A montagem completa da pré-forma seca com placas de vedação foi então coberta com peel ply e um filme de saco a vácuo. The entire assembly of skin, stringers and spars was then placed into the ACTI and the tooling was heated to 120°C. Hexcel RTM6 epoxy resin was heated to 70°C and degassed before infusion through a single resin feed location. “The ACTI was prepared to feed resin from four locations,” notes Diaz, “but after extensive simulation and tests, we decided it was easier and cheaper to have a single resin inlet.”
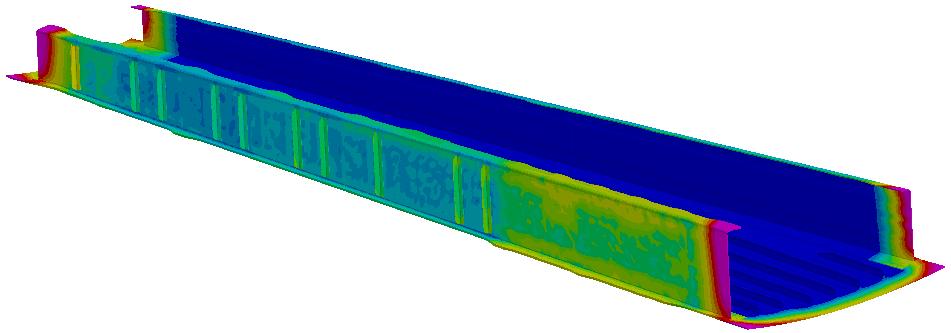
Even with a single inlet, the infusion process was very complex, comprising three different modes. “We first performed flow simulation, using PAM-RTM software [ESI Group, Paris, France],” says Diaz. “There was such a complex mix of flow fronts and parameters needed for complete wetout. For example, resin flow was faster in the center of the wing box, but it was a challenge to wet out all of the stiffeners.”
VAP, with a semi-permeable membrane, worked well for the lower skin, but this was exchanged for high-temperature flow mesh along the stringers and on the inside of the spars. “The corners were the most challenging areas to wet out,” notes Diaz, “but they were also the most critical for holding tolerances for assembly, as well as along the edges.” This can be seen in the red areas of the flow simulation in Fig. 4. “In these areas, a customized approach was developed to achieve the precise dimensions required,” he explains. We also used vacuum ports along the perimeter and on top of the spars.”
The infusion was relatively quick, as predicted by simulations, followed by a two-hour cure at 180°C, using only hot air, and not heated tooling. After being demolded, each wing box demonstrator was then inspected using ultrasonic testing (UT). This was done as part of the IIAMS project deliverables, to analyze the quality of the demonstrators. Industrial application of this process, however, will reduce traditional NDT in favor of digital sensors and faster inline inspection tools such as vision systems.
According to Diaz, although the infusion cure cycle was similar to that for an autoclave-cured prepreg wing box, the overall cycle time should be lower. “We have eliminated most of the assembly afterward and we also don’t have to shim anything like with prepreg, yet our quality is the same. For example, the bonding between the last layer of the skin and the first layer of a stringer needs no adhesive film in the middle to improve mechanical properties and account for tolerances.” This is obviously more efficient, but he notes that part production rate was not initially the driving factor. “This method is not competing with manufacturing of individual parts but with a completed wing box assembly.”
Complete demonstrators, path to certification
“We had only 18 months to complete this project, which included designing the process and tooling and manufacturing the tooling and demonstrators,” says Diaz. “By month 14, we had the first demonstrator ready for display at JEC in late February 2020 [Step 3], but then JEC was canceled due to the pandemic. Although the project finished in late September 2020, if you subtract the months we could not work due to COVID-19, we actually finished in month 16. We were able to keep this very tight schedule due to our in-house design capability and ability to manufacture the tooling prototypes using our AFP and CNC milling machines.”
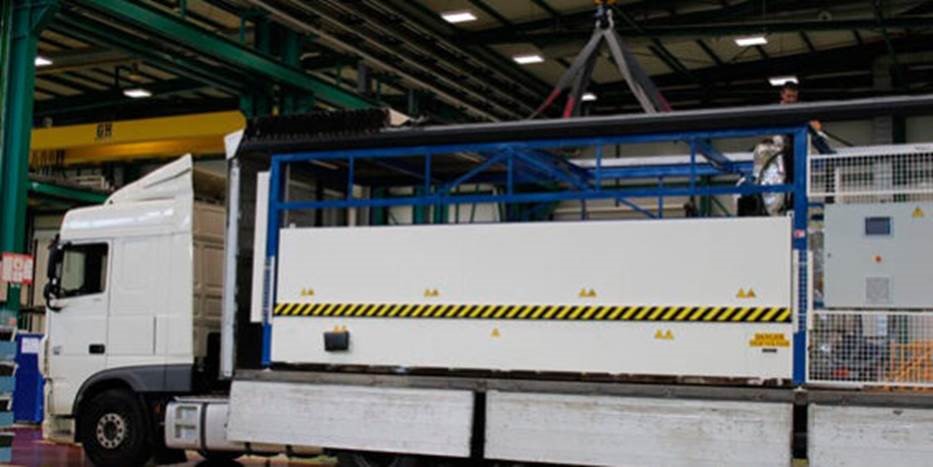
Step 8. ACTI forming/curing equipment and wing box tooling were lifted onto a standard moving truck and relocated to Airbus DS in Cadiz, Spain.
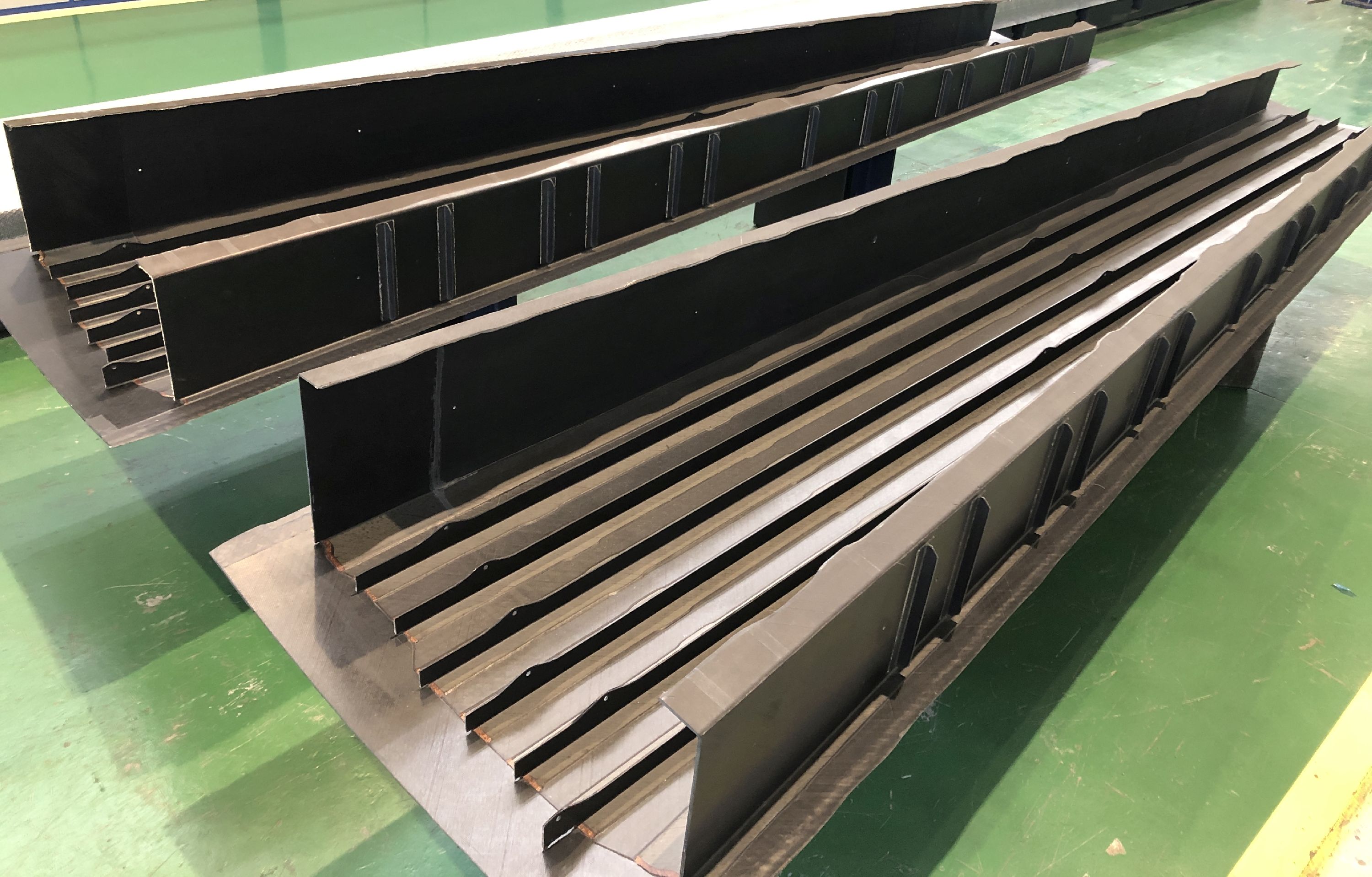
A simplified, 1-meter-long demonstrator was made at MTorres to check all of the process parameters. Then, the first full-size demonstrator was produced. Tooling and manufacturing equipment were then relocated to Airbus DS in Cadiz (Step 8), where the final demonstrator was produced. This was also part of the project’s deliverables, proving that the equipment could be easily transported and installed at multiple locations.
As explained in the sidebar, “IIAMS wing box road map to certification,” Airbus DS has played a key role in the Clean Sky program, progressing from co-leader of the Green Regional Aircraft (GRA) integrated technology demonstrator (ITD) in Clean Sky, to co-leader of the AIRFRAME ITD, as well as leader for the flight testbed 2 (FTB#2) in the REGIONAL integrated aircraft demonstrator platform (IADP) within Clean Sky 2. The FTB#2 will include other composites and airframe developments, including in the cockpit and other wing components.
All of the projects to prepare the FTB#2 are, in fact, part of a broader, long-range strategy at Airbus. The goal is to develop a future turboprop airframe that is lighter and more efficient, and production processes that are cheaper and use less energy, manufacturing liquids and ancillary materials, yet also generate less scrap and offer increased recyclability.
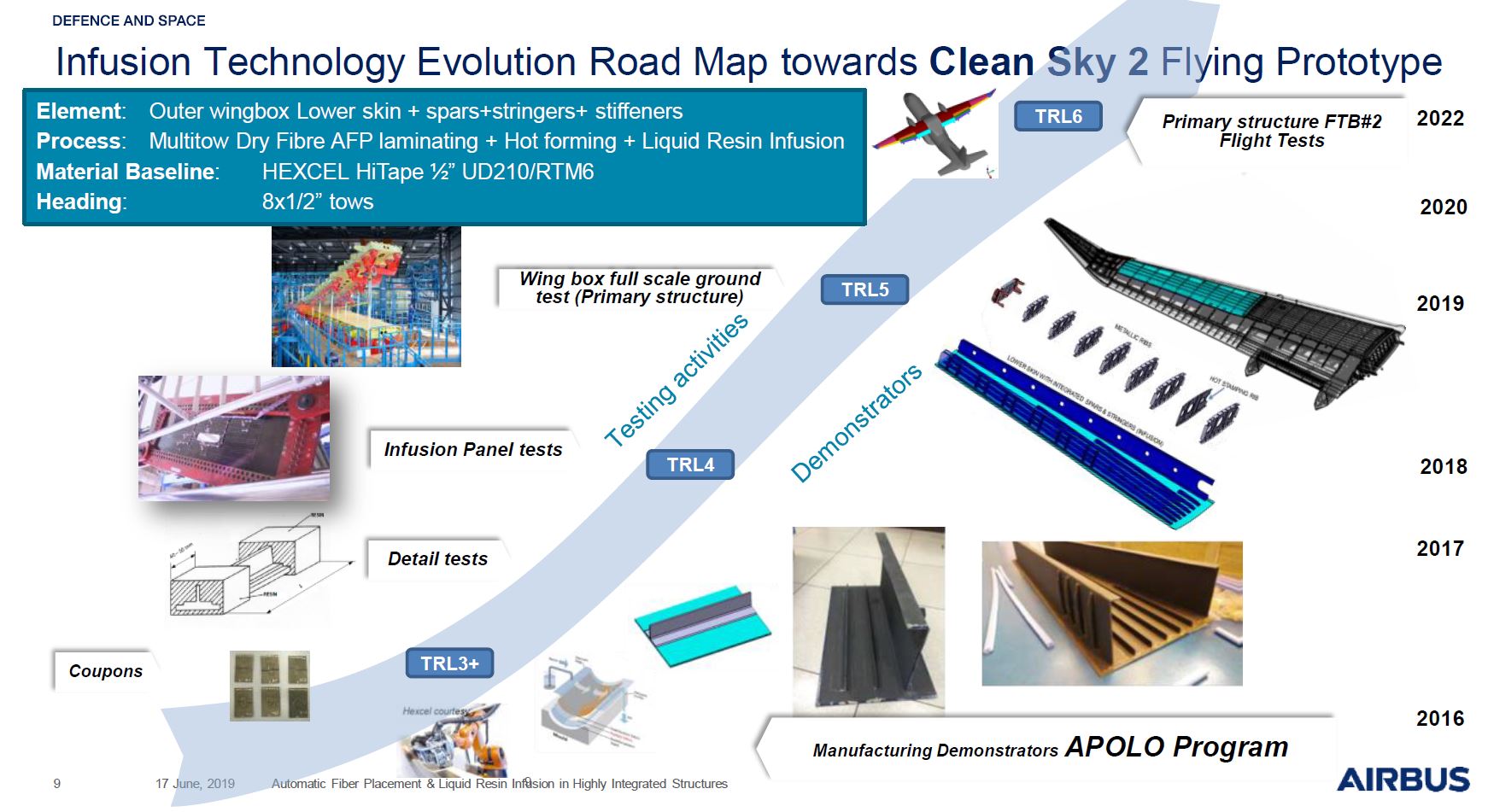
“Step by step we [Airbus DS] are going through the entire airframe structures test pyramid from coupons to the full-scale structural tests of the outer wing,” explains A.E. Jiménez Gahete in a September 2020 Materiales Compuestos article titled, “Airbus Defence and Space highly integrated wing box section manufactured by dry fiber placement and liquid resin infusion.” Materials characterization testing, a design details test matrix and subcomponent tests for design allowables have all been completed with positive results. MTorres aided in this testing, including manufacturing test coupons and parts, as well as demonstrators to validate the wing box manufacturing process and design details. Only the final outer wing full-scale static and functional tests remain, says Gahete, to obtain the FTB#2 qualification for flight.
“One-shot infusion reduces joints, decreases weight and increases robustness,” says Diaz. “The novel dry tape MTorres has developed produced excellent results, both in the processing — AFP, hot drape forming and infusion — and in the part’s structural properties.” He notes that, historically, there has been doubt that resin-infused composites could match the same structural performance and tolerances as autoclave-cured prepreg.
“To get the same tolerances in a single-shot process with soft [non-metallic] tooling was our greatest challenge,” he concedes. “But we have proven this technology works and that it can produce the large primary structures needed for future aircraft. Our next step is to keep advancing the digital technologies and portability of the production system.”
Resina
- Pigmentos em pó infundiram brilho para a indústria de plásticos
- BLB Industries A CAIXA PEQUENA
- Airbus apresenta a fábrica do futuro
- Participando da Conferência Edge Supply Chain? Veja como o gerenciamento da cadeia de suprimentos está avançando
- O Desenvolvimento de Plásticos Modernos
- História do Parafuso
- Vespel®:O Material Aeroespacial
- O que é a economia circular?
- Avançando a tecnologia no novo cenário de trabalho
- A melhor escolha:Torno CNC Box Way