Fabricação da metade superior do Demonstrador de Fuselagem Multifuncional (MFFD)
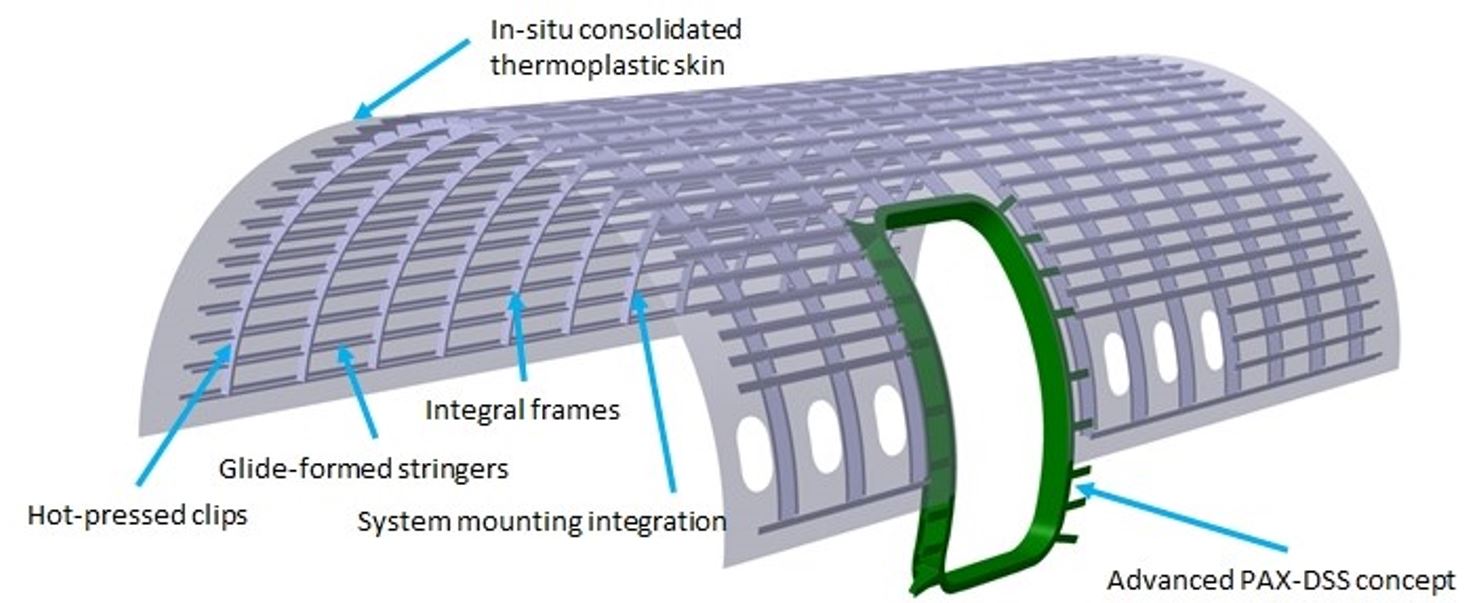
Este blog é uma continuação de uma apresentação feita pelo Centro Aeroespacial Alemão (DLR, Stuttgart e Augsburg) no simpósio TU Munich no outono passado e CW O resumo publicado durante o mesmo período, "Avançando no Demonstrador de Fuselagem Multifuncional (MFFD)". O projeto também foi descrito em uma apresentação dada por Lars Larsen às 9:35 no Dia 3 do ITHEC 2020:“Avanço baseado em dados de processo de soldagem ultrassônica contínua baseada em robô para a Montagem Livre de Poeira de Estruturas de Fuselagem do Futuro”.
Conforme explicado por Larsen, “O principal desafio é mostrar que os custos de produção podem ser reduzidos significativamente com o uso da automação”. Para a metade superior do MFFD, isso inclui consolidação in-situ por meio de colocação de fita / colocação de fibra automatizada (ATL / AFP) para evitar a autoclave e soldagem sem poeira / sem poeira para a montagem. “Isso deve possibilitar a mudança da sequência de componentes e linhas de montagem final no futuro”, diz Larsen, “permitindo que os sistemas sejam integrados antes conjunto." Isso ocorre porque, ao contrário da usinagem para orifícios de fixação, a soldagem não produz lascas ou detritos que possam danificar os sistemas pré-instalados, como energia elétrica distribuída, acessórios internos, etc.
Este blog é baseado na minha entrevista com Sebastian Nowotny, chefe de design de componentes e tecnologias de manufatura no Instituto DLR de Estruturas e Design (BT, Stuttgart) e Frederic Fischer, líder técnico para produção de compósitos termoplásticos no Centro DLR para Tecnologia de Produção Leve ( ZLP, Augsburg). Fischer também é gerente de projeto da metade superior do MFFD na DLR.
NOTA:Na imagem acima, longarinas formadas por deslizamento referem-se a um processo desenvolvido no Clean Sky 2 por Applus + Labaoratories (Barcelona, Espanha), consulte meu blog de 2017 sobre formação por deslizamento e clipes prensados a quente referem-se a estamparia, consulte:
- Acelerando os compósitos termoplásticos na indústria aeroespacial
- Compósitos termoplásticos “prendem” o tempo, trabalho em peças pequenas, mas cruciais
- Dentro de um viveiro de compósitos termoplásticos
Combinando estrutura, cabine e sistemas
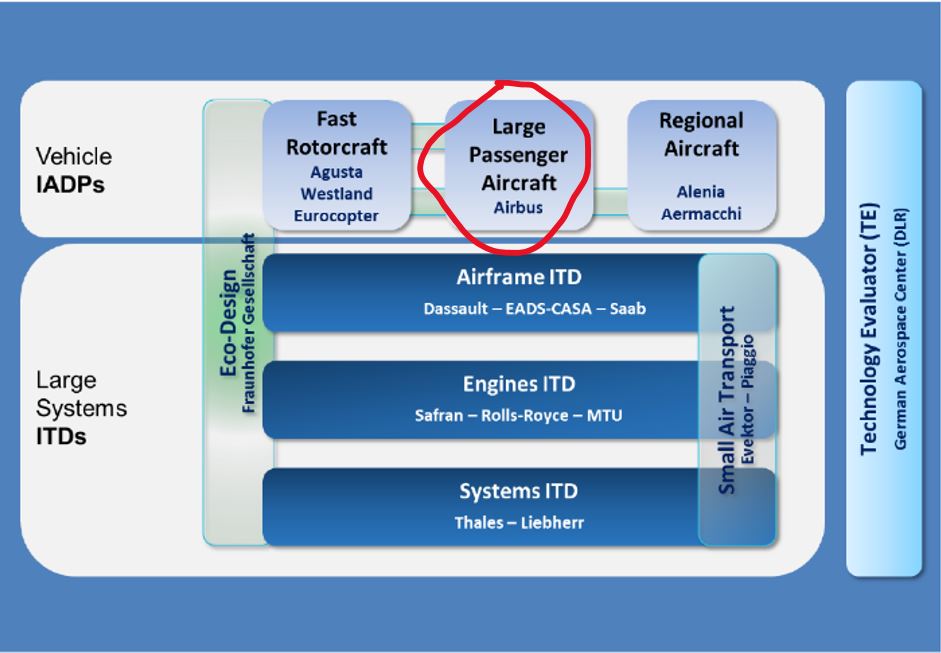
Perguntei a Nowotny sobre a história da metade superior do MFFD. “Quando o Clean Sky 2 começou, foi lançada a primeira chamada de propostas”, ele responde. “Acho que começamos em 2015 e vencemos a licitação do projeto ICASUS, que era um projeto de co-parceria para o programa de aeronaves de passageiros de grande porte (LPA). O foco principal estava no projeto de uma fuselagem multifuncional. Naquela época, não era composto termoplástico. O objetivo principal era combinar a fuselagem, a cabine, os sistemas e a estrutura em um processo de design. Então, basicamente, o trabalho que foi feito lá é o que agora se tornou o demonstrador multifuncional da fuselagem (MFFD) e é o suporte de tecnologia para o nosso trabalho no projeto da parte superior. ”
ICASUS
O projeto ICASUS visa desenvolver soluções multifuncionais e altamente integradas para a fuselagem multifuncional de próxima geração da fuselagem, cabine e sistemas integrados. Hoje, o processo de fabricação e montagem de aeronaves de corredor único é conduzido por etapas sequenciais caras e demoradas. Especialmente a montagem de componentes principais (MCA) e a linha de montagem final (FAL) são gargalos que impedem processos mais rápidos e acelerados. Por este motivo, o ICASUS desenvolverá um novo conceito para fabricação e montagem de alvos para futuras aeronaves de corredor único:
- Alta produção de 60 aeronaves / mês;
- Redução de custo recorrente de fuselagem de € 1 milhão em comparação com a referência A321 ACF (“Advanced Cabin Flex”);
- Redução do peso da fuselagem de 1 tonelada métrica em comparação com o A321 ACF.
A abordagem será combinar as disciplinas originalmente autárquicas de cabine / carga, sistemas e estrutura para terminar com a combinação e integração mais promissora das respectivas funções e requisitos. Isso deve ser alcançado usando materiais avançados e aplicando princípios de design inovadores em combinação com a arquitetura de sistema mais avançada em combinação com a cabine de próxima geração.
O principal objetivo é reduzir significativamente o consumo de combustível aplicando sistemas de baixo peso e arquitetura / integração do sistema. Isso requer um procedimento de otimização geral multidisciplinar, bem como o desenvolvimento e a aplicação de uma abordagem holística da Indústria 4.0. O projeto para fabricação automatizada, automação, sensorização, análise de dados e troca segura de dados deve ser utilizado. Os principais objetivos da fabricação do MFFD incluem a verificação da produção econômica e em alto volume de estruturas compostas multifuncionais e contribuir para os conceitos de certificação para juntas termoplásticas CFRP (por exemplo, soldagem).
Como você combina a cabine, os sistemas e a estrutura da fuselagem em um só? “Você ainda teria essas disciplinas com seus respectivos requisitos, mas acho que o objetivo principal é a abordagem para colaborar já em um estágio inicial”, explica Nowotny. “Existem regras rígidas para o processo de projeto da fuselagem da aeronave que criaram restrições e impediram um projeto de aeronave totalmente otimizado. A ideia inicial de combinar estrutura, cabine e sistemas era ter um processo de design que reúna esses três aspectos e, em seguida, tente encontrar o ótimo global, não apenas um primeiro para a cabine e depois um para a estrutura e depois um para os sistemas . Mas, claro, existem muitas regras e este não é um processo fácil porque também envolve certificação. ”
“É um processo contínuo, no sentido de que uma plataforma digital foi estabelecida e todos os parceiros europeus fornecem contribuições para esse design digital único”, diz Fischer. “Avançar com esse design integrado para o MFFD é o que vem acontecendo nos últimos dois anos. Nossa equipe entregará a metade superior com provisões para cabine e sistema de fixação. A visão é revolucionar a montagem final, entregando componentes principais totalmente equipados. ”
Embora o DLR já fizesse parte do projeto de design do MFFD, ele não recebeu a aprovação final para o projeto de fabricação até 2019. O consórcio para construir a metade superior compreende a Airbus como líder geral do projeto MFFD, Premium Aerotec (Augsburg, Alemanha ) como líder do projeto industrial e estrutural e fornecedor das armações, Aernnova (Vitoria-Gasteiz, Espanha) para produzir as longarinas e DLR como líder para o layup de pele e desenvolvimento de tecnologia de soldagem. No ano passado, diz Fischer, “refinamos o design da metade superior para garantir que possa ser fabricado com as tecnologias selecionadas”.
Consolidação in-situ
Enquanto a metade inferior do MFFD está sendo produzida usando ATL e AFP seguido por consolidação em autoclave, a metade superior usará consolidação in-situ durante ATL / AFP. Por quê? “Para obter a produção máxima do projeto de pesquisa, optamos por desafiar a linha de base”, diz Fischer, “e aproveitar a oportunidade de usar uma tecnologia em complemento à metade inferior”. Nowotny acrescenta:“Mostramos que é um método de fabricação muito promissor que se concentra na produção enxuta, reduzindo as etapas de fabricação. Mas acho que está claro que não existe um único método de fabricação que atenda a todos os propósitos. Você ainda precisa decidir, caso a caso, qual é o processo de fabricação ideal para cada peça. ”
Dois tipos de soldagem
Outra opção feita para a metade superior foi o uso de duas tecnologias de soldagem diferentes. “Usamos soldagem ultrassônica contínua baseada em robô para as longarinas, porque, em nossa opinião, essa é a tecnologia mais adequada para juntas realmente longas e especialmente para a configuração da longarina”, explica Fischer. A soldagem por resistência foi escolhida para a integração das armações da fuselagem. “Essas escolhas são resultado de análises intensivas que fizemos no início do projeto, em conjunto com a Premium Aerotec. Observamos os diferentes cenários de soldagem, o que precisava ser unido e onde. ”
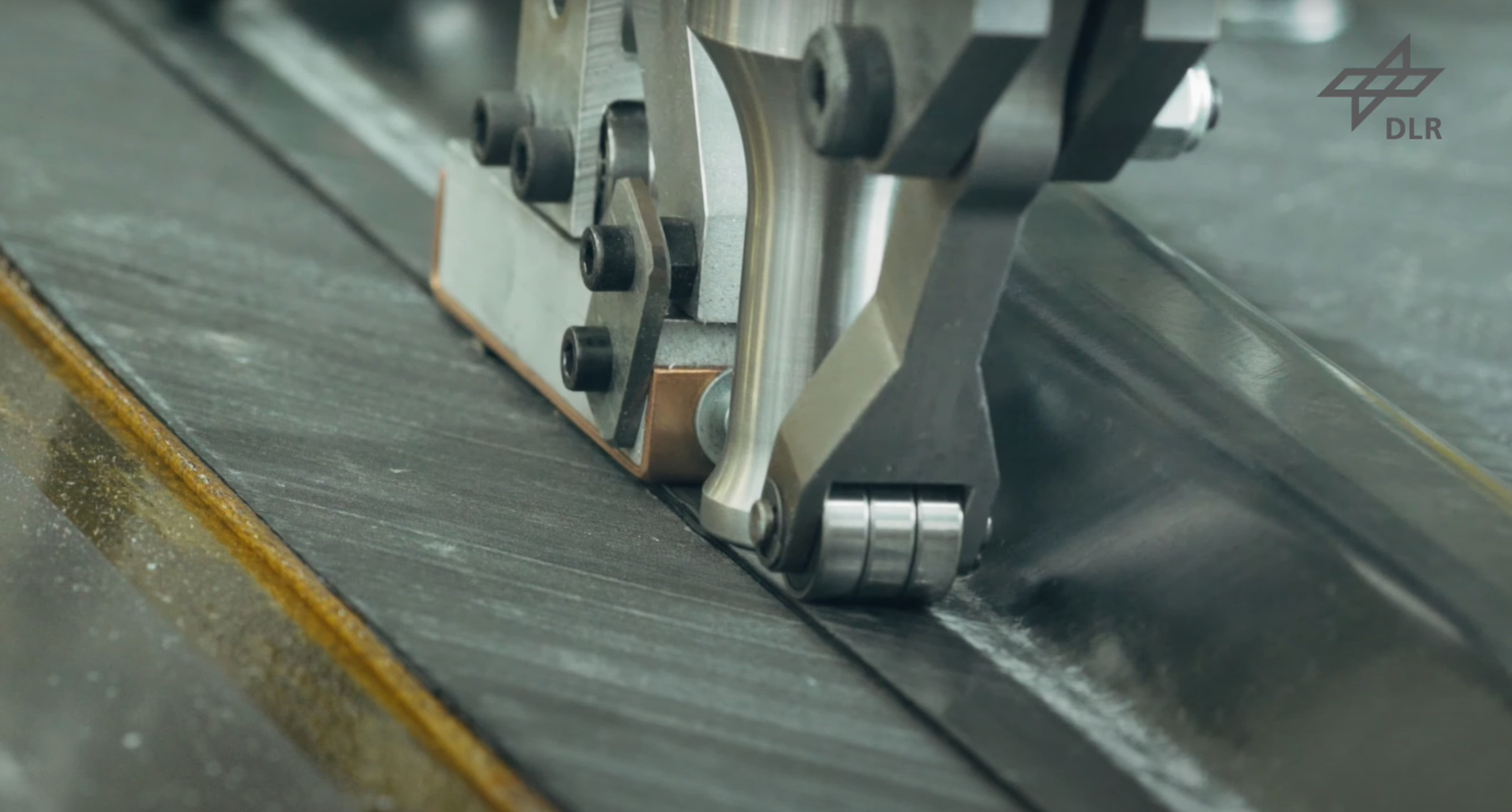
A soldagem ultrassônica contínua desenvolvida pela DLR usa um robô industrial padrão. O efetor de final de soldagem compreende um rolo de pré-execução, um sonotrodo de 25 milímetros de diâmetro e uma unidade de compactação seguinte. O efetor final é equipado com vários sensores, o que permite o monitoramento do processo em linha. Usando o robô como um manipulador, conforme mostrado no vídeo abaixo, uma variedade de geometrias podem ser soldadas, como uma antepara de pressão traseira curva ou longarinas ômega em uma pele.
“Portanto, temos dois processos com uma grande distinção”, observa Fischer. “Um é contínuo processo e o outro é um descontínuo processo. Para as juntas de 8 metros de comprimento das longarinas Z, optamos pela soldagem ultrassônica contínua. E para o caso de uso altamente complexo - em termos de gerenciamento de acessibilidade e tolerância - para soldar os flanges das armações à pele, escolhemos a soldagem por resistência. Vamos encaixar e pré-equipar o elemento de soldagem por resistência à geometria da estrutura e ter uma ferramenta de soldagem tipo grampo que se fecha pneumaticamente, entra em contato com os elementos de soldagem e, em seguida, aciona o processo de soldagem. ”
Nowotny observa que a soldagem por resistência tem a maior maturidade e maior resistência, o que combina bem com a maior carga observada nas juntas entre os quadros e as travas. Ele ressalta que este processo está soldando a estrutura à pele e soldar a presilha tanto no quadro quanto na longarina.
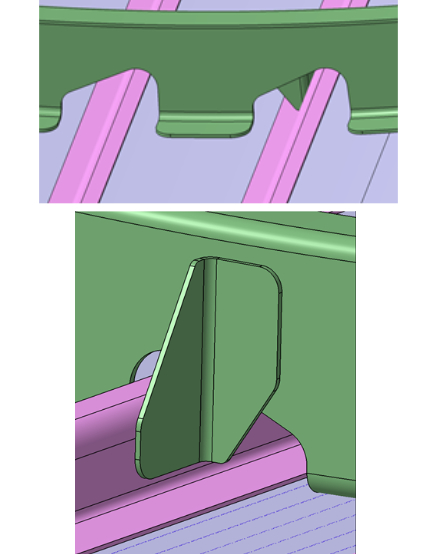
“Mostramos a integração do clipe em peças genéricas na JEC 2017”, diz Fischer. Nowotny acrescenta:“E realmente tínhamos o projeto HISYS com o departamento de alta elevação da Airbus Bremen em 2005-2008 para soldagem por resistência com termoplástico PEEK (polieteretercetona). Trouxemos todo o processo de soldagem das costelas na pele até o TRL 5. Assim, os fundamentos do processo são bastante bem compreendidos e agora podemos nos concentrar principalmente na adaptação, automação e robustez do processo. ”
“ Um dos principais capacitadores para diferentes tecnologias de soldagem - embora já existam por muito tempo - é mostrar que estão prontas para aplicação comercial na indústria ”, destaca Fischer,“ incluindo a necessária automação, programação e garantia de qualidade . Um dos principais problemas que estamos examinando é como saber se a solda está boa. Queremos ter certeza de que temos os dados do processo para mostrar que sabemos que a solda terá um desempenho de longo prazo e que não estamos pedindo uma verificação NDT subsequente com ultrassom ou outra inspeção geral na montagem concluída. Portanto, um dos nossos principais objetivos neste projeto é desenvolver a garantia da qualidade industrial. ”
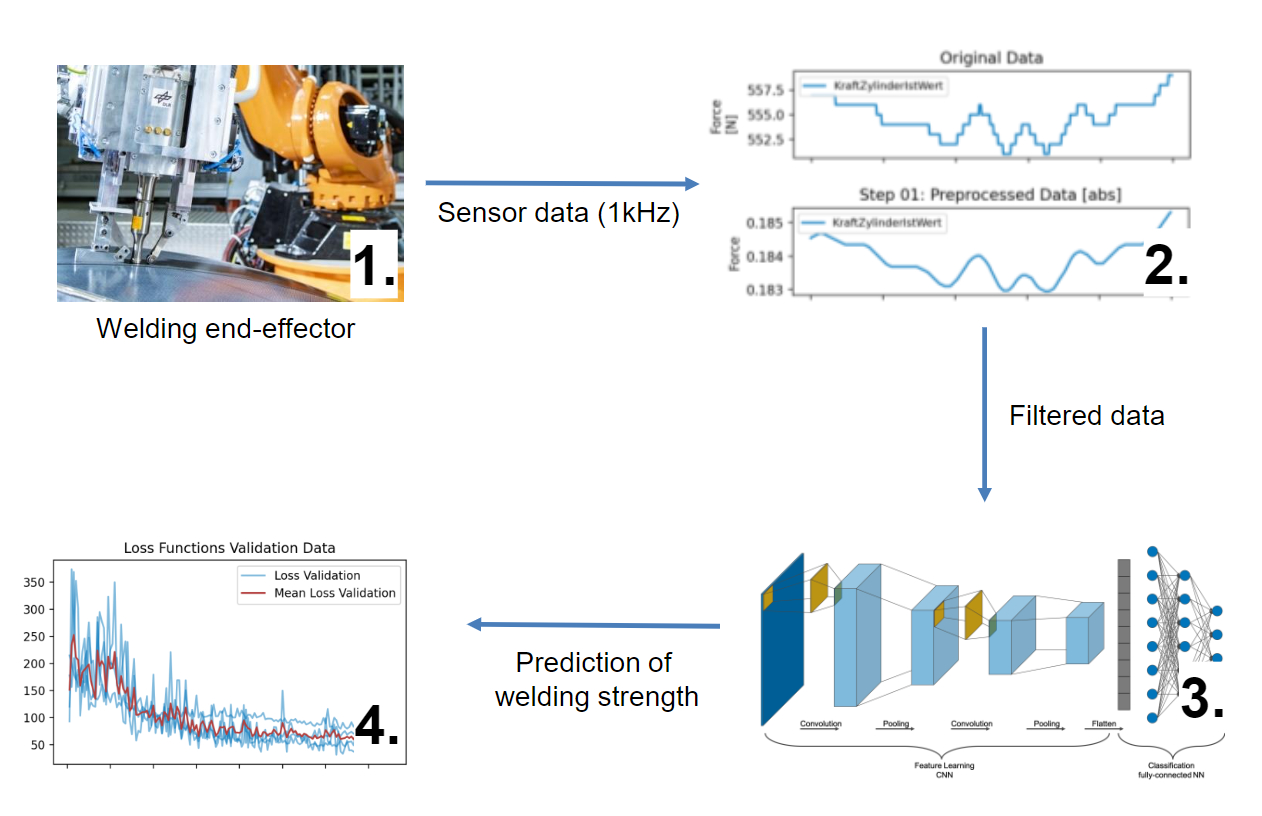
Dinamizando para LM PAEK
Conforme explicado no meu blog, "Provando a soldagem LM PAEK para Demonstrador de Fuselagem Multifuncional", embora o MFFD tenha começado com fibra de carbono / PEKK (polietercetonecetona), na 10ª chamada de propostas (CFP10) em março de 2019, o material de base foi mudou para fibra de carbono / PAEK (poliariletercetona). PAEK é a família geral de polímeros dentro da qual residem PEEK, PEKK e LM PAEK. Quanta experiência a equipe da metade superior tem com LM PAEK? “Já o usamos para uma série de testes de fabricação”, diz Fischer. “O desempenho do material é bastante promissor tanto para soldagem ultrassônica quanto para soldagem por resistência. Ainda assim, o material está em desenvolvimento e um processo de troca comum em termos de lições aprendidas e desenvolvimento de diretrizes de processamento foi estabelecido entre todos os parceiros europeus e o fornecedor do material. ”
“ No entanto, ”acrescenta Nowotny,“ acho que é uma coisa boa termos essas opções de materiais agora, porque muitos anos atrás, havia apenas Cytec APC-2 e nada mais. Especialmente na Europa, às vezes você poderia obter o material e às vezes você obteria, 'não, desculpe'. Agora, temos vários fornecedores de materiais que trabalham ativamente nos materiais e também nos diferentes processos. Por exemplo, a Victrex, como vimos apresentado no simpósio 2020 TU Munich, agora está procurando a otimização para a manufatura aditiva. Também há algum trabalho em andamento com a otimização para consolidação AFP in-situ e alguns para consolidação secundária usando uma autoclave, bem como vários processos de fabricação fora de autoclave (OOA). Então, há muito mais acontecendo agora, e isso aumenta as chances de conseguir um bom material para cada processo. ”
Cronograma e próximas etapas
“Basicamente, concluímos o processo de fabricação do projeto para um demonstrador intermediário - diâmetro A320 com dois compartimentos de estrutura e largura de 950 milímetros - e construiremos essa meia-carcaça menor no início do próximo ano (2021)”, diz Fischer . “Além disso, começamos a aquisição do ferramental para a metade superior em escala real e estamos aprimorando nossas tecnologias para garantir que seremos capazes de produzir a metade superior em tamanho real dentro do prazo em 2022 . ”
O que isso acarreta? Um problema são as tolerâncias de montagem. “As juntas longitudinais ao longo dos lados esquerdo e direito das metades superior e inferior da fuselagem foram projetadas há algum tempo”, explica Fischer. “A partir disso, temos certos requisitos e precisamos garantir que nossas tolerâncias de produção atendam a esses requisitos.”
“A história básica do que estamos tentando fazer com a casca superior é demonstrar as rotas mais eficientes para a produção de compósitos termoplásticos e abrir um caminho que pode competir com o alumínio para futuras aeronaves”, diz Fischer. Ele observa que a DLR já demonstrou isso em seu trabalho com a Premium Aerotec para desenvolver uma antepara de pressão traseira termoplástica soldada, mostrada em 2018 e 2019 (veja também “Novos horizontes na soldagem de compósitos termoplásticos”). A soldagem e a produção enxuta são os principais facilitadores dos termoplásticos. E agora devemos tirar essas tecnologias do laboratório e colocá-las na indústria. E para que as indústrias acreditem que podem realmente usar essas tecnologias de soldagem, devemos mostrar que elas podem ser automatizadas, previsíveis e controladas para confiabilidade em tarefas reais de produção. E é isso que estamos fazendo ”.
Resina
- Os benefícios da fabricação de curto prazo
- Os materiais orgânicos são o futuro da fabricação de plásticos?
- Como escolher o melhor fornecedor de manufatura de plástico
- Robôs de montagem 101:O quê, onde e como os robôs de montagem na manufatura
- As últimas novidades em manufatura de remanejamento
- O papel do blockchain na fabricação
- Os 8 desperdícios do Lean Manufacturing
- O que está no processo de fabricação?
- O futuro da impressão 3D na fabricação
- A impressão 3D é o futuro da manufatura?