Ferramentas aditivas híbridas de grande formato:moldes mais leves, rápidos e menos caros para peças grandes
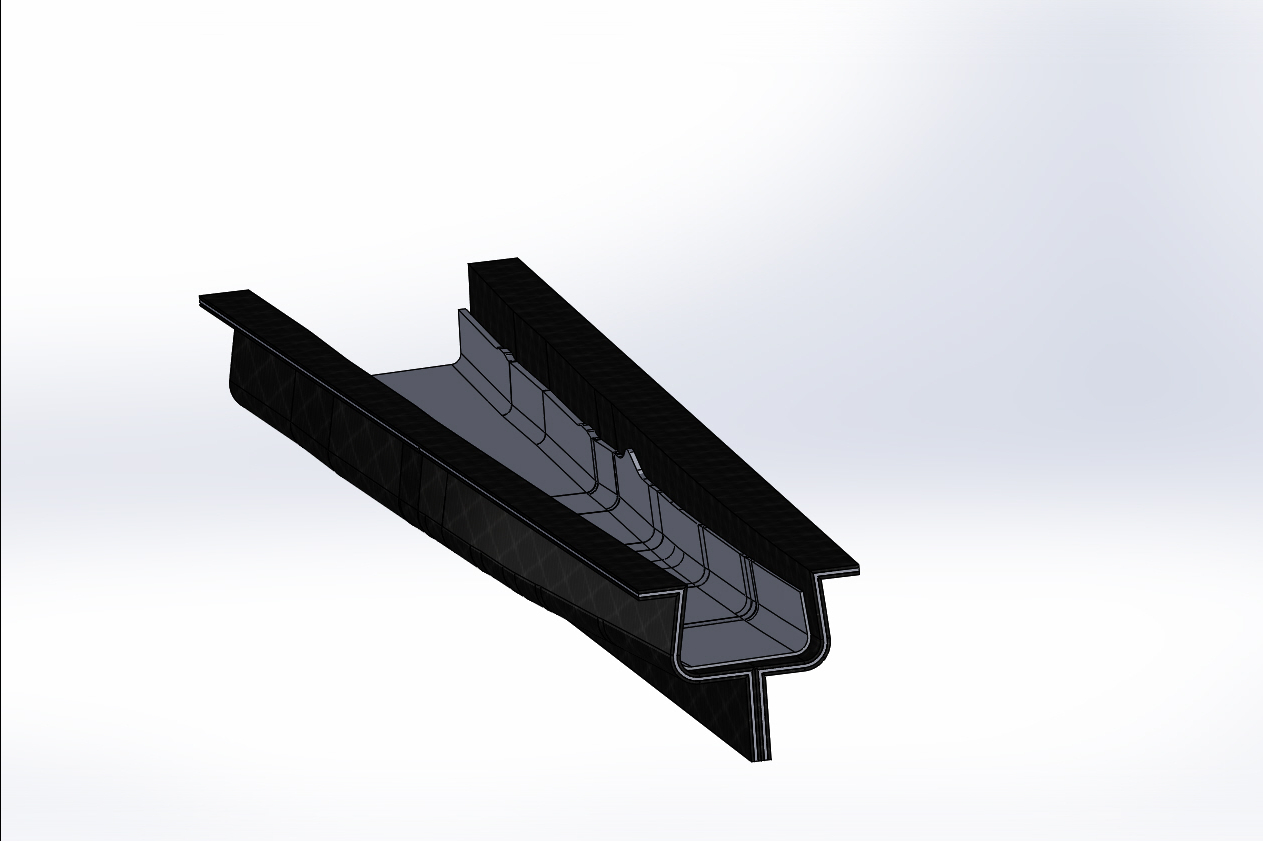
Por mais de três décadas, a aviação comercial adotou cada vez mais os materiais compostos. Na verdade, mais da metade dos componentes estruturais críticos em vários modelos das principais aeronaves comerciais atualmente são compostos. Como o uso desses materiais cresceu em termos de volume e tamanho das peças, tornou-se cada vez mais difícil construir ferramentas - ferramentas particularmente acessíveis - para prototipar e fabricar mais rapidamente essas peças. Por exemplo, as asas do A350 XWB da Airbus SE (Leiden, Holanda) têm, cada uma, 32 metros de comprimento por 6 metros de largura e representam algumas das maiores estruturas compostas de aviação já produzidas.
“Existem agora tecnologias de fabricação tão inovadoras no mercado que podemos esperar grandes passos na evolução das ferramentas, ajudando-nos a enfrentar os desafios que enfrentamos no desenvolvimento de componentes de aeronaves compostas”, observa M. Pilar Muñoz Lopez, engenheira de fabricação de compostas da Fábrica da Airbus em Illescas, Espanha. “É crucial para nós investigarmos essas tecnologias, capacidades e limitações para que possamos estar preparados para o futuro.”
Dado que o ferramental representa uma proporção significativa dos custos totais do programa para peças aeroestruturais, e dado o tamanho crescente dessas peças, são necessárias novas opções de ferramental com custos e prazos de entrega mais baixos. Um estudo interessante sobre ferramentas híbridas, de grande formato e manufaturadas aditivamente (LFAM) para peças de aeroestrutura de protótipo e produção de baixo volume foi recentemente concluído pela Airbus, Northrop Grumman Aeronautics Systems - Unidade de Negócios de Estruturas Aeroespaciais (Clearfield, Utah, EUA) e a Universidade do Dayton Research Institute (UDRI, Dayton, Ohio, EUA) com resultados encorajadores.
Controlando os problemas de expansão térmica
A maioria das aeroestruturas de plástico reforçado com fibra de carbono (CFRP) são produzidas a partir de pré-impregnado com matriz de epóxi. Para moldar essas peças, o ferramental deve sobreviver a temperaturas de cura em forno ou autoclave de até 180 ° C / 356 ° F. Além disso, dado o coeficiente muito baixo de CFRP de expansão térmica (linear) (CLTE ou CTE), é fundamental combinar - o mais próximo possível - ferramentas e materiais de moldagem CLTEs em temperaturas ambiente e elevadas. Isso garante que os moldes mantenham as dimensões para que as peças resultantes também atendam aos requisitos dimensionais. Para evitar distorções ou tensões nas estruturas finais, também é importante evitar o uso de um material de ferramenta que esfria mais rápido do que o material da peça. Como consequência, as ferramentas mais comuns usadas para moldar grandes aeroestruturas de CFRP são feitas do próprio CFRP ou do Invar, uma liga ferrosa de níquel e ferro conhecida por seu baixo CLTE. Ambos são caros e podem ter prazos de entrega significativos. Além disso, o Invar é difícil e demorado para usinar e pesado para transportar. Enquanto as ferramentas de aço ou alumínio podem reduzir custos, seus valores CLTE relativamente mais altos limitam o uso em muitas aplicações - particularmente ao moldar peças grandes ou longas.
Muitos estudos dos setores público e privado avaliaram ferramentas manufaturadas aditivamente impressas em materiais termoplásticos e concluíram que elas potencialmente oferecem benefícios, incluindo custos mais baixos e prazos mais curtos para produzir compostos laminados termofixos. Infelizmente, o ferramental LFAM baseado em polímero tem problemas como a porosidade da ferramenta, o que pode levar a uma perda significativa de vácuo em temperaturas / pressões de cura. Resolver isso requer retrabalho de preenchimento de ferramenta adicional e revestimentos de superfície. Um desafio ainda maior são os valores CLTE altamente anisotrópicos, devido ao alinhamento do enchimento de matéria-prima no plano durante a extrusão / impressão, o que pode levar a diferenças de expansão / contração de 5 a 10 vezes maiores no eixo Z do que nos eixos de impressão X e Y. Isso torna um desafio obter peças dimensionalmente precisas de forma repetitiva e reproduzível - especialmente quando as peças são grandes, têm uma relação de aspecto elevada e / ou apresentam superfícies complexas.
“Todos os interessados em ferramentas aditivas estão enfrentando os mesmos problemas de porosidade e expansão térmica descontrolada, com poucas maneiras eficazes de resolver esses problemas”, explica Scott Huelskamp, líder da equipe UDRI, desenvolvimento de processo de fabricação avançado, Divisão de Materiais Estruturais. “Há muitas pessoas que querem usar as ferramentas AM, mas estão esperando que alguém resolva esses problemas.”
Dado o potencial da AM para reduzir custos de ferramentas e prazos de entrega, a indústria concentrou esforços consideráveis em abordar questões de expansão, explorando novos materiais imprimíveis, modificações de hardware de impressora e abordagens de modelagem inovadoras. Por exemplo, alguns grupos desenvolveram um “valor de compensação” para projetar ferramentas AM para lidar com os diferenciais CLTE. No entanto, Huelskamp observa que determinar qual o valor de compensação a ser usado é difícil e sujeito a erros. Além disso, tais abordagens têm sido ineficazes para ferramentas de cavidade fêmea e ferramentas com recursos de retenção em seu comprimento que criam condições de travamento de matriz capazes de danificar peças durante o ciclo térmico na ferramenta.
“Não há nenhum fator de compensação que vai resolver esse tipo de problema”, acrescenta. “Até o momento, nenhum estudo de ferramentas AM abordou totalmente a necessidade de valores CTE isotrópicos baixos em temperatura elevada. Sem esta característica, os tamanhos e geometrias das ferramentas sempre serão limitados e as ferramentas maiores sofrerão erros dimensionais mais elevados em temperaturas de cura. ”
Em um esforço para tentar novas abordagens para resolver os desafios de ferramentas LFAM, um projeto de 18 meses foi realizado por várias empresas membros sob os auspícios do Instituto de Inovação de Fabricação de Compostos Avançados (IACMI, Knoxville, Tenn., EUA) e apoiado pelos EUA Departamento de Energia e EmpregosOhio (Columbus, Ohio). A equipe foi liderada pela UDRI e incluiu Airbus e Northrop Grumman. Essas organizações já haviam colaborado em outras pesquisas, tanto dentro quanto fora do IACMI e, portanto, estavam familiarizadas com as capacidades umas das outras.
Abordagem de “força bruta”
A UDRI já tinha uma experiência considerável de trabalho em estudos de ferramentas AM e é um membro ativo da America Makes (Youngstown, Ohio, EUA), o consórcio AM dos EUA. Além disso, o instituto fez pesquisas para a Força Aérea dos EUA envolvendo estruturas AM com suportes metálicos e trabalhou com a Cincinnati Inc. (Harrison, Ohio, EUA), produtora de impressoras de Big Area Additive Manufacturing (BAAM), em ferramentas AM puras.
“Também trabalhamos com compostos personalizados em novas matérias-primas para impressoras 3D, mas nada do que estávamos fazendo parecia estar avançando muito, e não sabíamos se ninguém mais estava tendo mais sucesso do que nós”, lembra Huelskamp. “Foi então que tivemos a ideia de abordar o problema de forma diferente. Se não pudéssemos mudar a forma como os materiais da AM se comportam ou prever esse comportamento diretamente , então talvez pudéssemos forçá-los a se comportar da maneira que desejamos indiretamente . ” Tomando o que Huelskamp chama de abordagem de "força bruta", a UDRI propôs um estudo LFAM híbrido que produziria ferramentas de aeroestrutura aplicando convencional Revestimentos faciais de CFRP em compósito termoplástico Núcleos AM.
Os objetivos do projeto eram simples:encontrar um método mais rápido e mais barato para fazer grandes ferramentas para aeroestruturas. A equipe buscou uma opção que reduziu os custos em 50% e produziu pelo menos 10 protótipos aceitáveis ou peças de produção de baixo volume para testes subsequentes
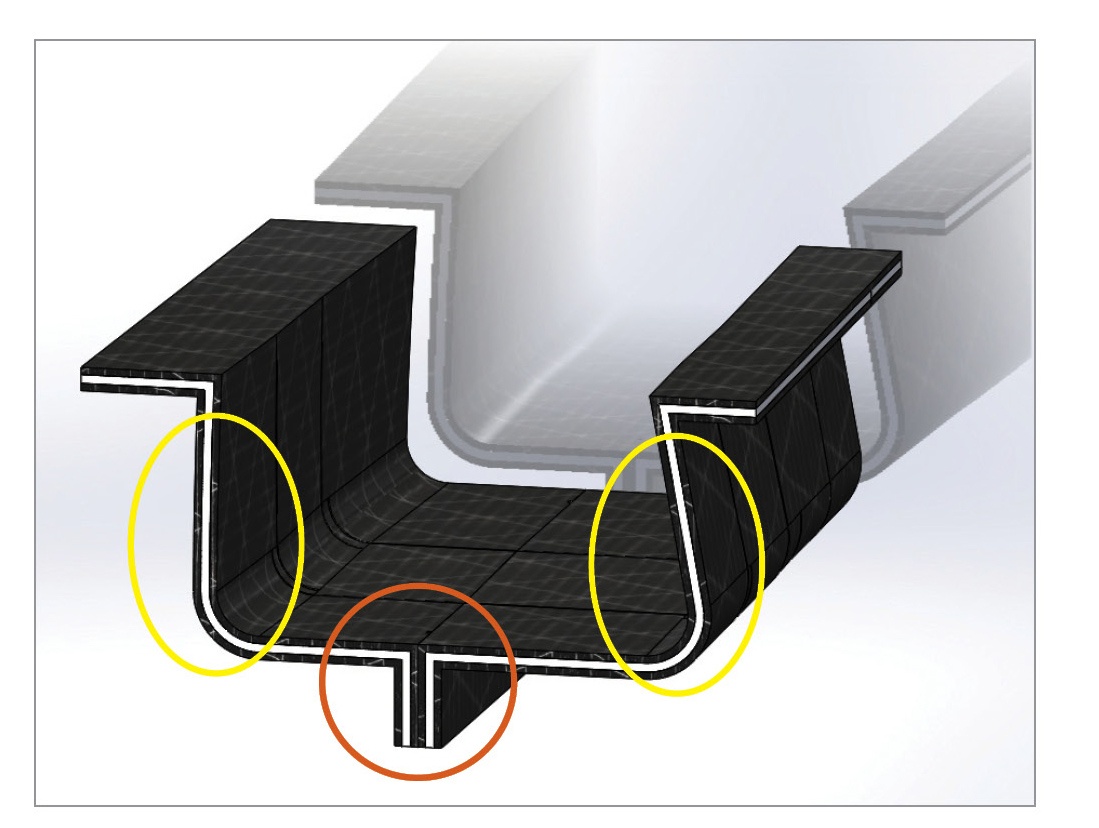
A equipe decidiu usar uma estrutura de sanduíche para produzir ferramentas unilaterais para uma seção de uma longarina genérica usando dados de ferramentas da Airbus. Além de produzir ferramentas para moldar apenas uma seção do C-spar em escala real - devido às limitações de espaço nas instalações da UDRI - nenhuma grande mudança no projeto foi feita.
Uma ferramenta fêmea foi projetada para garantir que a geometria crítica da peça fosse formada usando superfícies usinadas. Esta ferramenta spar cap tinha um leve ângulo interno que criava inclinação negativa e uma condição de trava de molde, sendo uma ferramenta de peça única. Isso levou os pesquisadores a modificar o projeto para uma ferramenta de divisão que foi selada com gaxeta / cordão. Para mitigar o risco, a equipe começou com uma ferramenta de subescala de 0,6 metro / 2,0 pés para provar o conceito. Depois que o processo de desenvolvimento da ferramenta e as peças do protótipo produzidas nessa ferramenta foram testados e funcionaram, a equipe construiu uma ferramenta maior de 3,3 metros / 11 pés de comprimento para moldar uma seção maior da longarina para o teste do protótipo.
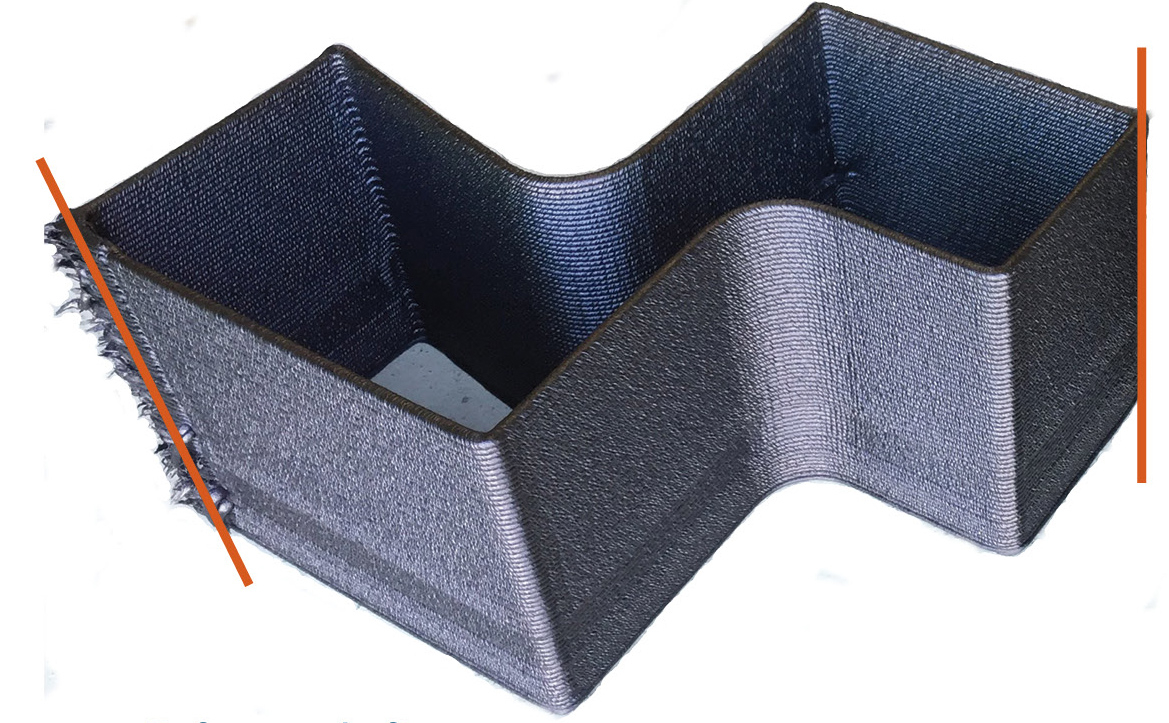
Como o ferramental CFRP tem um valor CLTE tão baixo, é mais leve que o Invar e a ferramenta era para peças de produção de protótipo / baixo volume, a equipe decidiu usar capas de rosto CFRP para restringir o núcleo AM. As películas foram feitas com prepreg de ferramentas epóxi Hextool M81 da Hexcel (Corp., Stamford, Conn., U.S.).
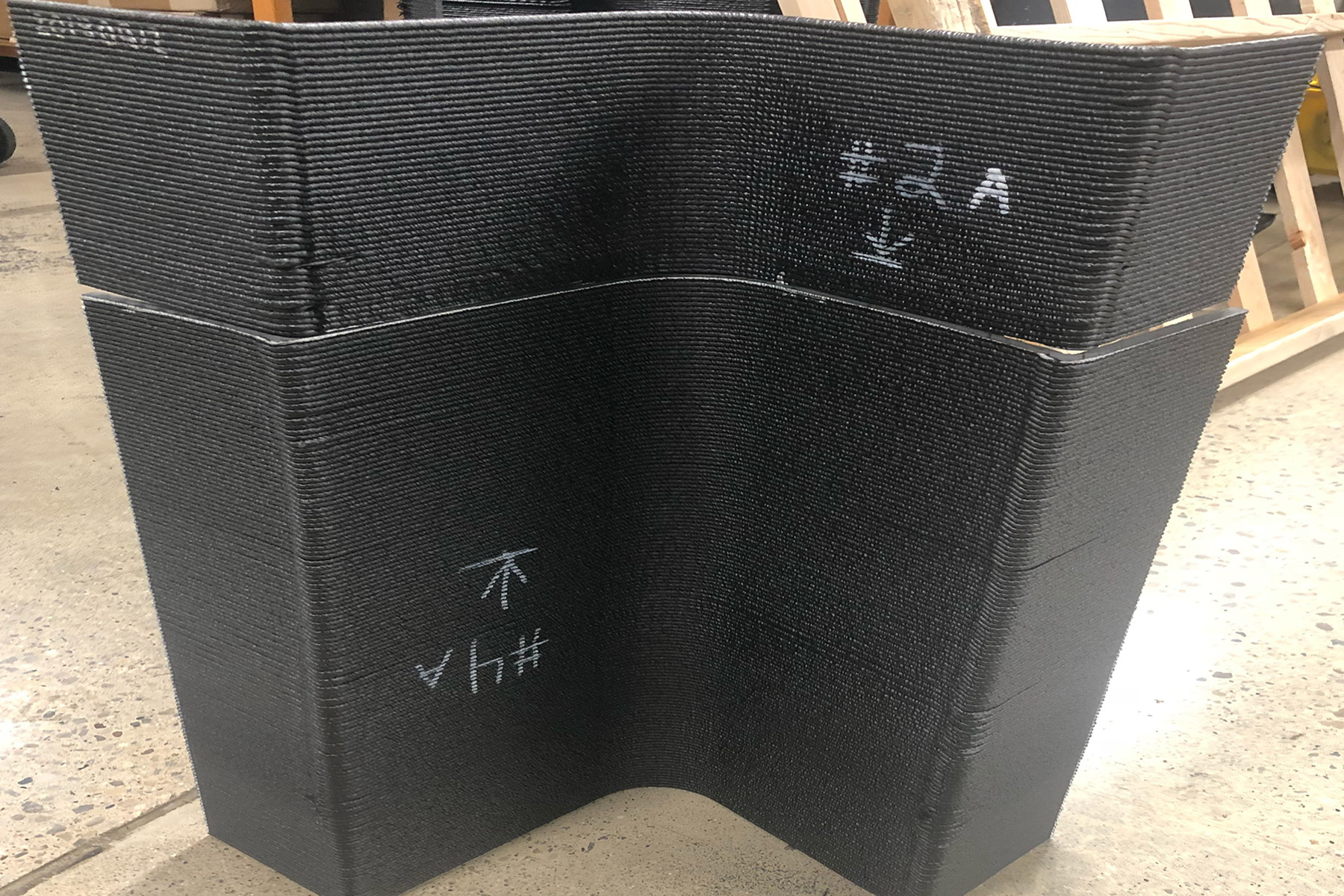
A imagem superior mostra uma seção da metade direita da subescala, ferramenta impressa com BAAM, com linhas vermelhas indicando linhas de corte após a impressão. A imagem inferior mostra a ferramenta da metade direita depois que as seções foram unidas. Crédito da foto:University of Dayton Research Institute.
O formato do material era uma esteira de fibra de carbono picada de 2.000 gramas por metro quadrado / 59 onças por jarda quadrada impregnada com epóxi endurecido 8552 da Hexcel. Este material é frequentemente usado para ferramentas compostas devido às suas propriedades quase isotrópicas, que permitem a usinagem pós-molde sem movimento da ferramenta que poderia ser causado por relaxamento de tensão residual.
Dado que o núcleo seria impresso em uma impressora Cincinnati Inc. BAAM 1000 na Additive Engineering Solutions (Akron, Ohio, EUA), e dado que UDRI e Cincinnati tinham experiência significativa de trabalho com a polieterimida termoplástica de alta temperatura (PEI), eles selecionaram PEI reforçado com 20% de fibra de carbono curto (Thermocomp EX004EXAR1 Ultem) da SABIC, (Riade, Arábia Saudita) para imprimir um núcleo com formato quase final. (A presença de fibras de carbono estabiliza o polímero durante a impressão e evita que ele desmorone; na estrutura acabada, as fibras reduzem o CLTE na direção da impressão.) Para manter os custos baixos, o núcleo funcionou como o mestre de ferramentas e as películas faciais foram laminadas diretamente ao núcleo sem adesivo, mas com algumas modificações na superfície do núcleo que é coberta pela propriedade intelectual (PI) desenvolvida durante o projeto. Essa abordagem foi eficaz, sem delaminação, mesmo após vários ciclos térmicos.
Fabricação condensada
Na fabricação convencional de ferramentas de CFRP de aeroestrutura, um master de baixo custo é criado primeiro. Isso geralmente envolve a união de blocos de placa de ferramentas em um forno ou autoclave e, em seguida, a usinagem da estrutura monolítica na geometria da peça desejada. O material da ferramenta é então armazenado, ensacado e curado no master em uma autoclave. Após a desmoldagem e limpeza, uma estrutura de suporte é colada à ferramenta e a superfície da ferramenta é usinada novamente para garantir uma boa tolerância geométrica e acabamento superficial.
Com ferramentas AM híbridas, a equipe desenvolveu um processo de manufatura condensado para reduzir o lead time e os custos. Primeiro, um núcleo de formato quase líquido (mestre da ferramenta) foi impresso em 3D (em fibra de carbono curto / PEI). Em seguida, o pré-impregnado de ferramentas CFRP foi laminado diretamente em ambos os lados do núcleo (com debulks a quente entre as camadas um, quatro e sete de acordo com as recomendações do fornecedor). Toda a estrutura foi então ensacada a vácuo e curada em autoclave.
Processo de fabricação condensado para ferramenta C-spar de subescala.
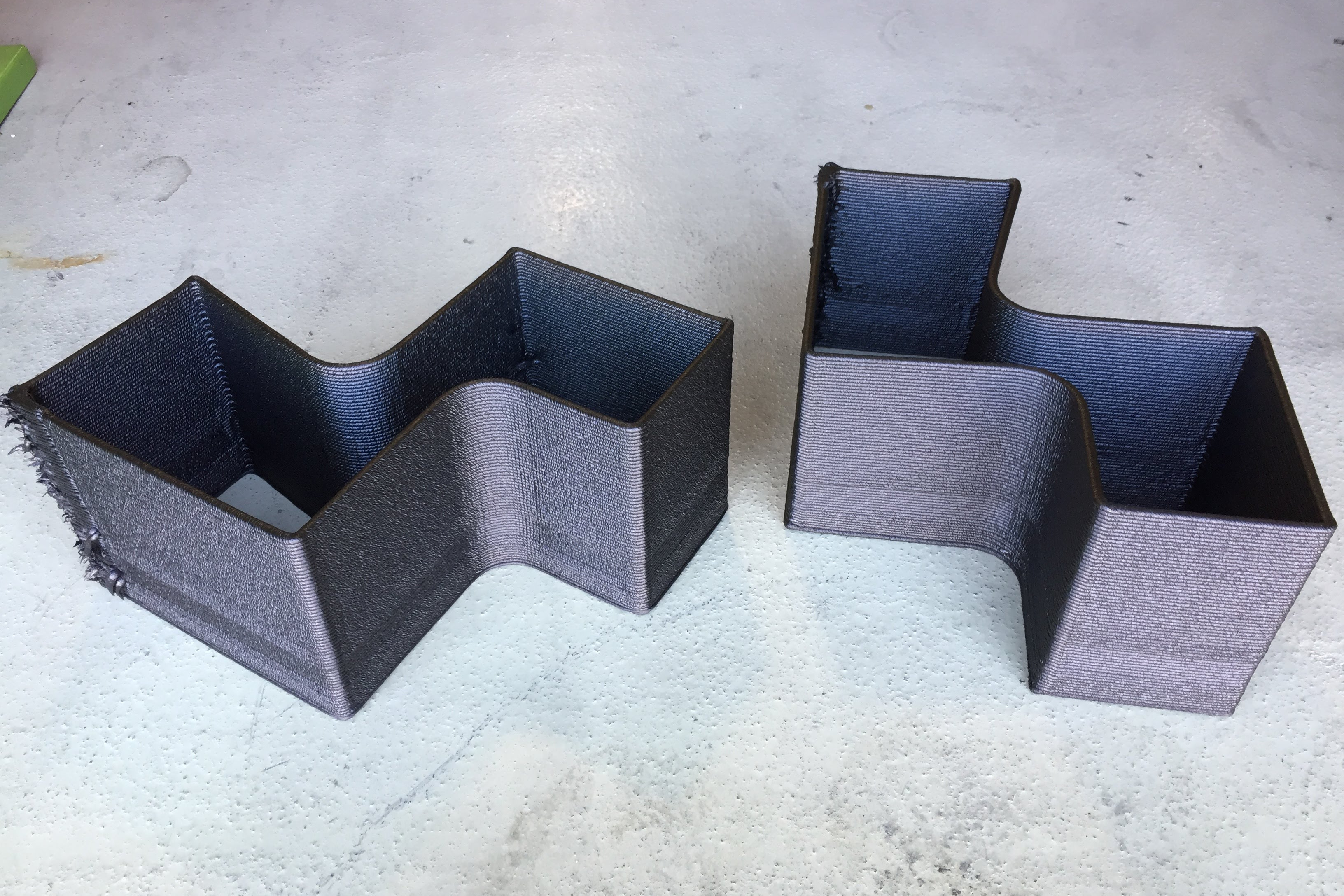
Etapa 2:corte a impressão BAAM ao meio e nas metades esquerda e direita.
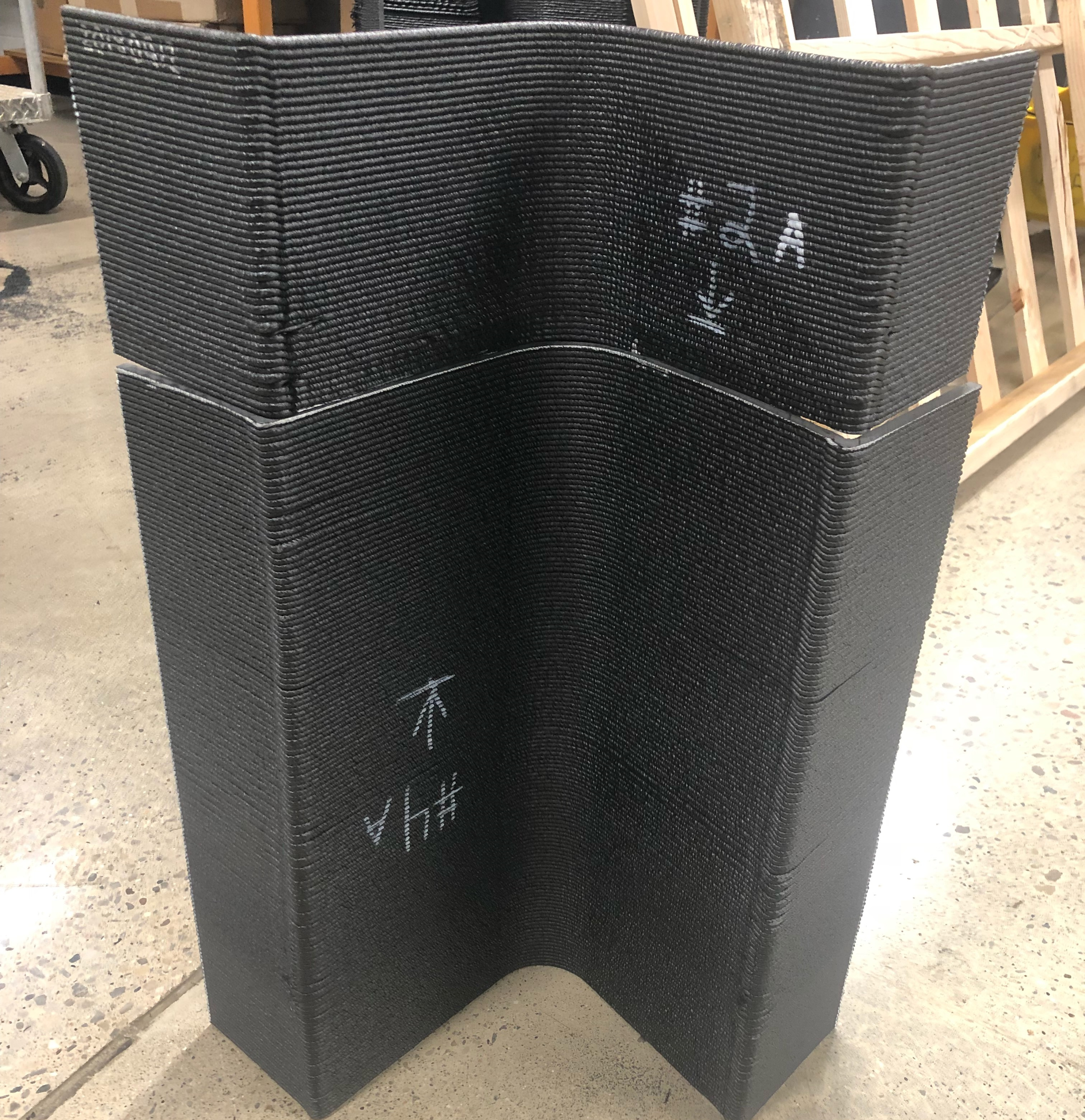
Etapa 3:Faça a colagem da impressão BAAM para obter o comprimento necessário e deixe curar.
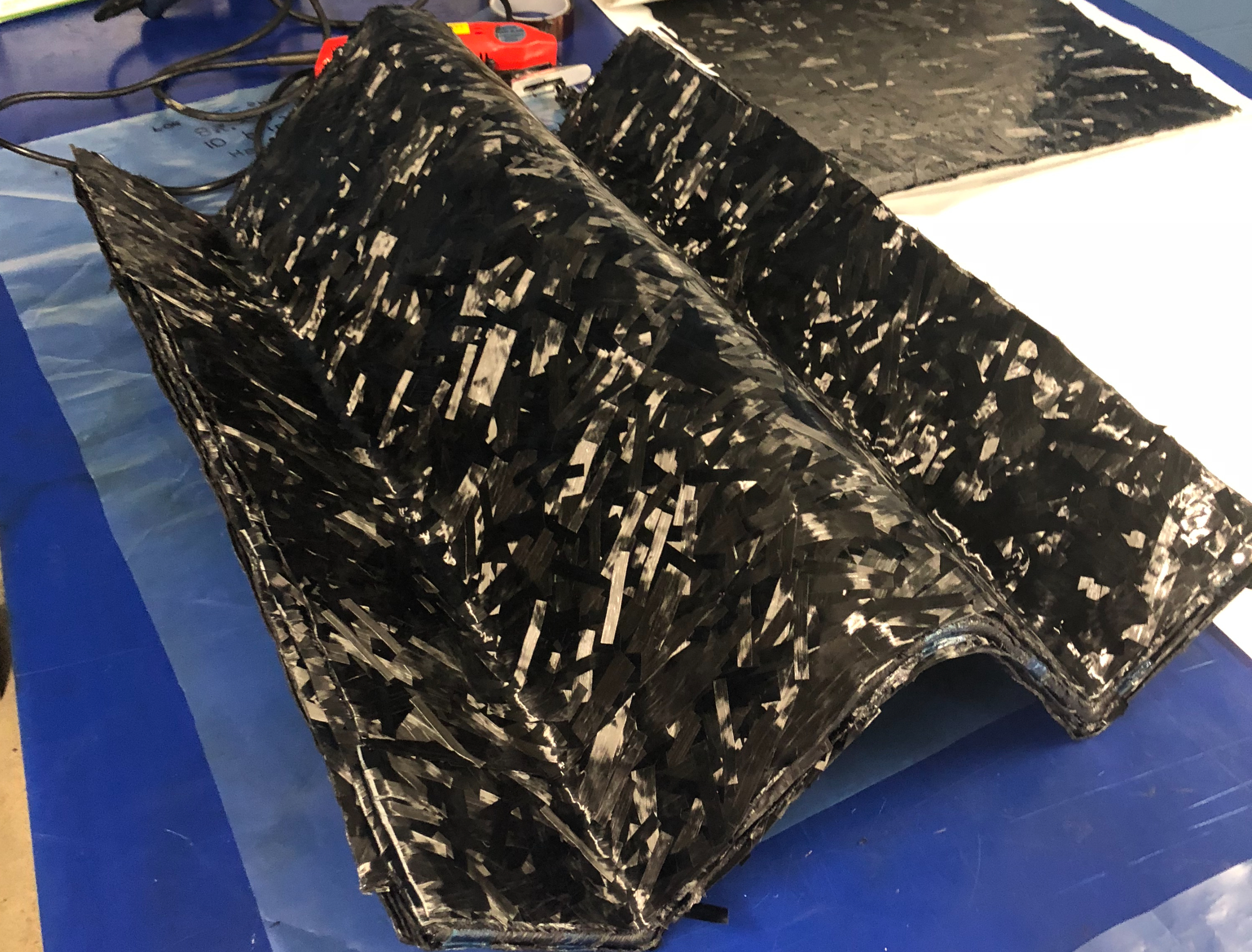
Etapa 4:Pré-impregnado de ferramentas laminadas em ambos os lados do núcleo com despressurização a quente de acordo com as instruções do fabricante.
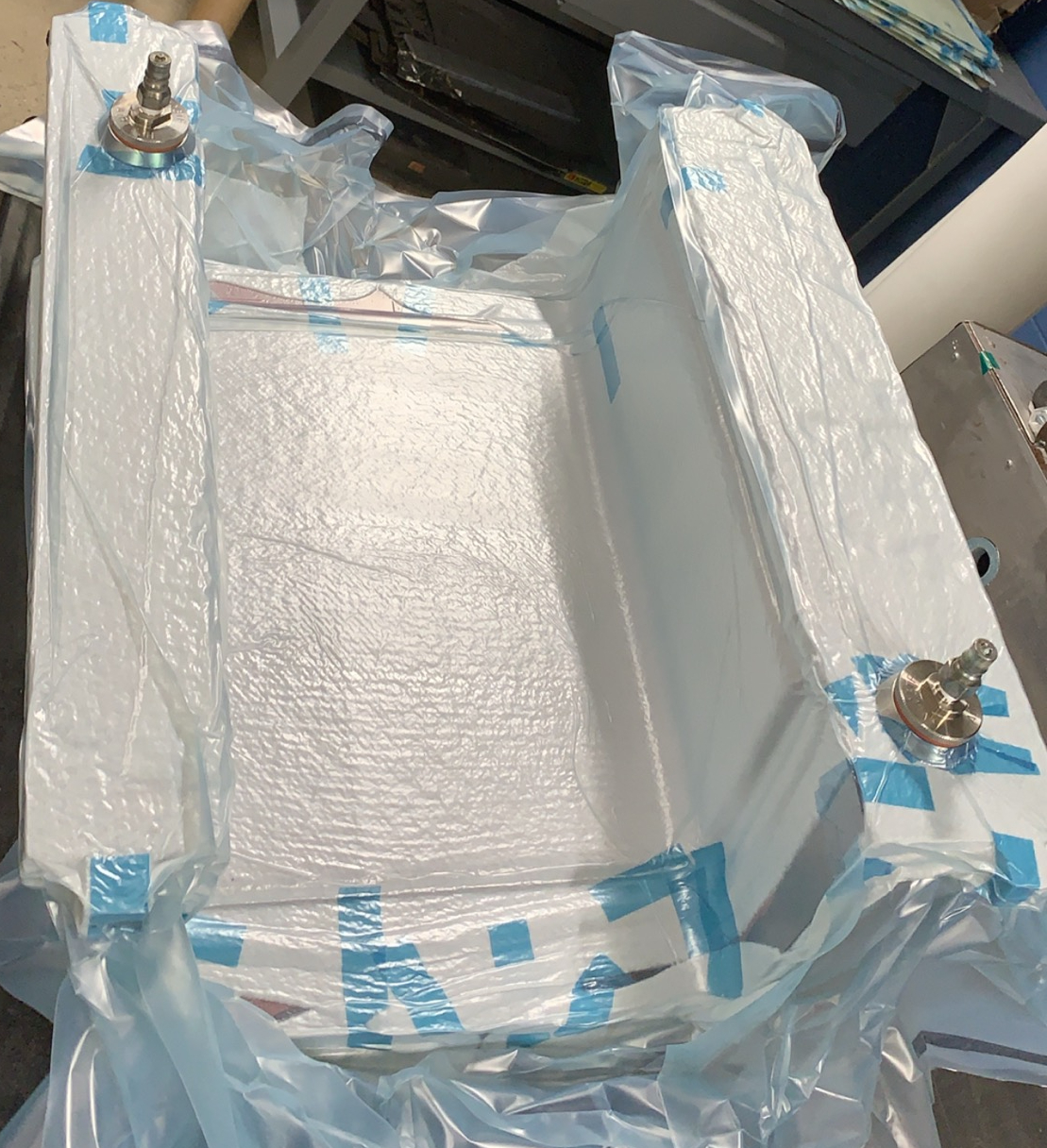
Passo 5:Saco a vácuo e catalise em autoclave.
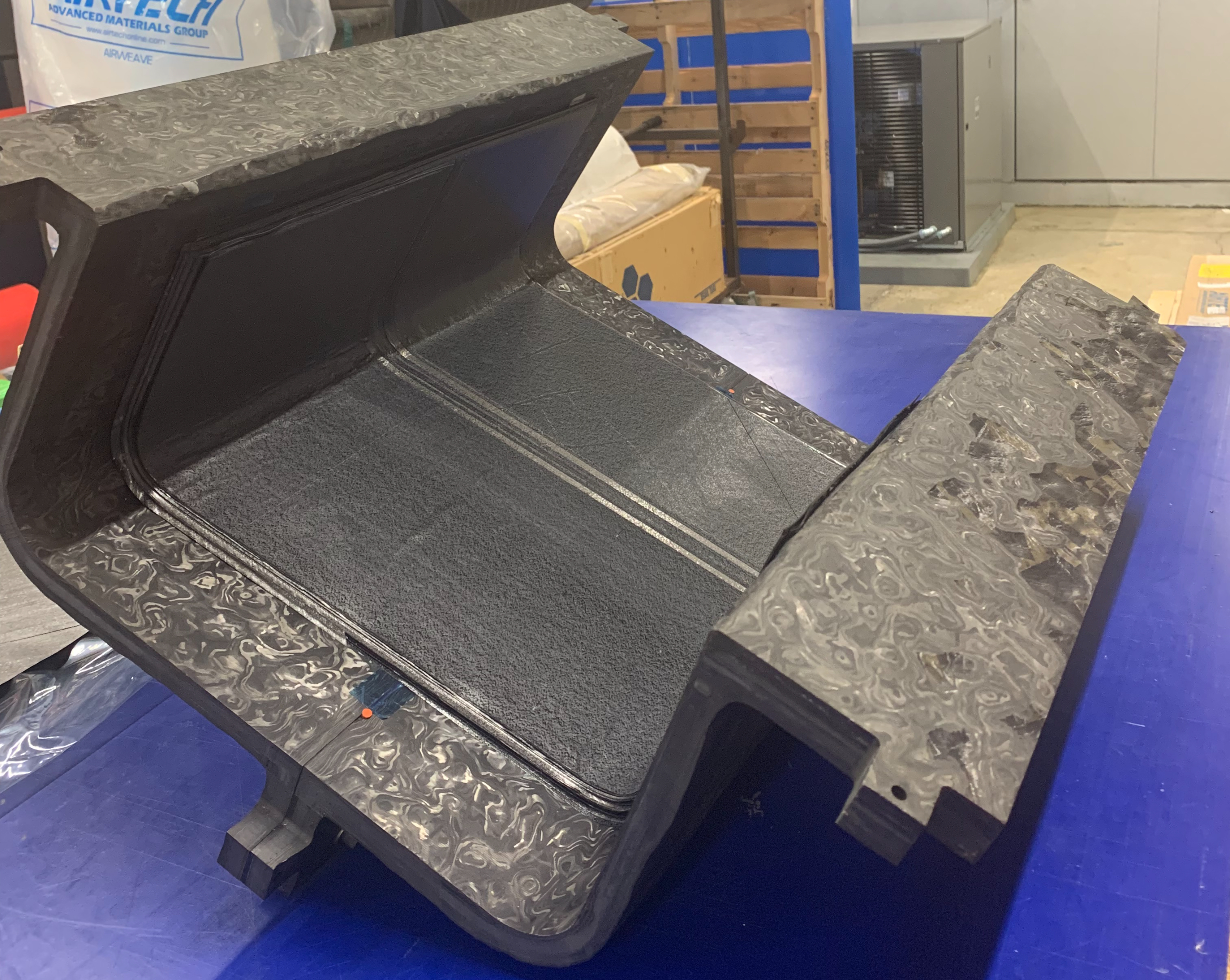
Etapa 6:ferramenta de cura à máquina para obter as dimensões finais e o acabamento superficial.
Anterior Próximo
Boa adesão foi alcançada entre o núcleo PEI e as películas de epóxi durante a cura do laminado, portanto, o adesivo não foi necessário. As películas de CFRP não são apenas não porosas e mais duráveis do que o núcleo AM, mas também restringem fisicamente o movimento do núcleo durante as excursões de temperatura devido aos seus valores CLTE muito mais baixos. Apenas uma cura única e uma única operação de usinagem - ambas as principais despesas durante o tradicional produção de ferramentas - eram necessárias para atingir as dimensões finais e o acabamento superficial. Além disso, nenhum suporte foi necessário, devido à estrutura em sanduíche e formato da ferramenta, que incluía flanges de retorno no topo do molde para rigidez lateral e uma junta aparafusada no centro do molde para rigidez vertical - eliminando uma operação de colagem.
Desafios iniciais
Os pesquisadores enfrentaram vários desafios gerenciáveis com o novo processo.
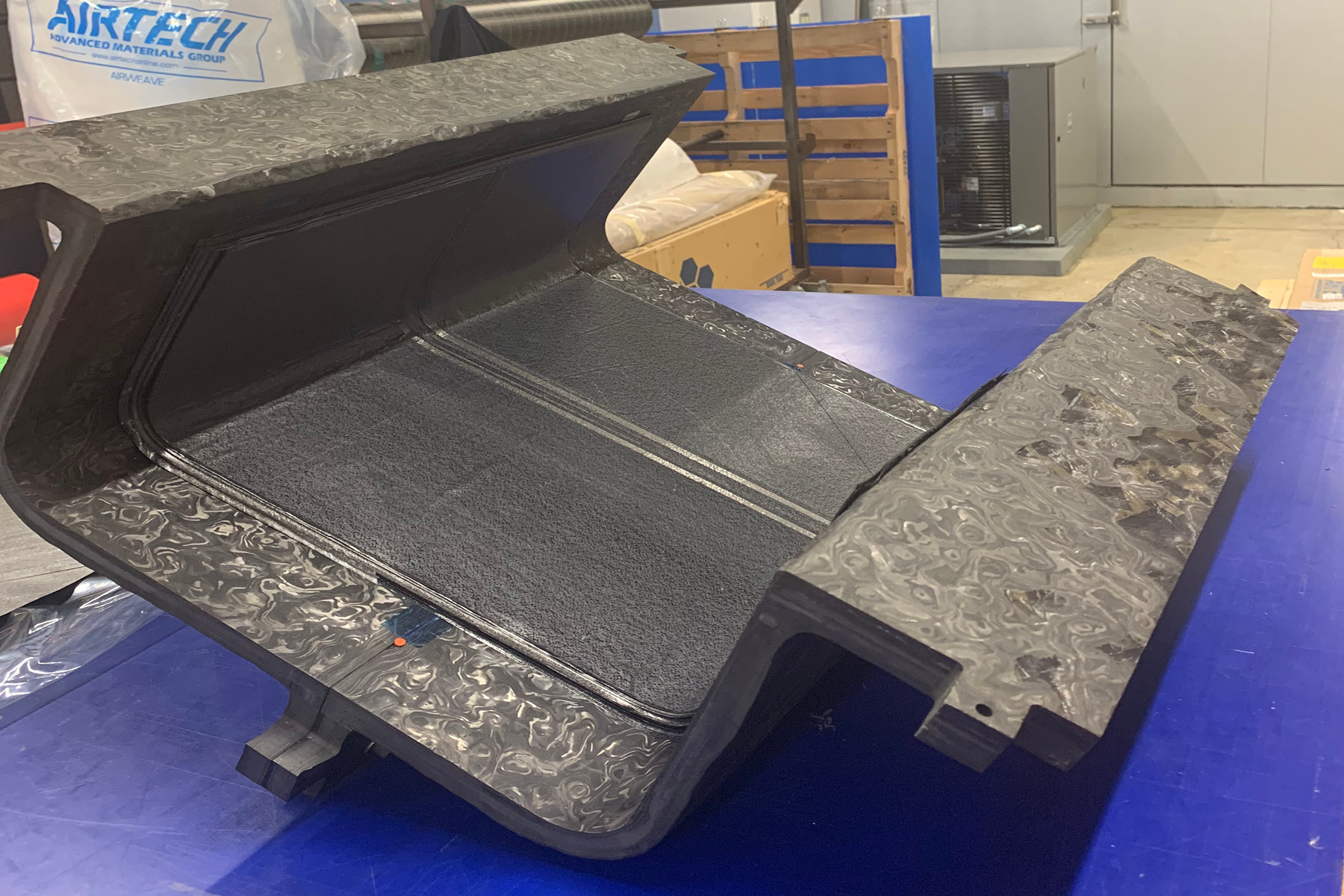
Para facilitar a fabricação no BAAM, a direção de fabricação preferida para o núcleo foi imprimir a seção transversal como uma construção vertical. Isso não foi um problema para a ferramenta de 0,6 metros; no entanto, para a ferramenta maior, 3,3 metros era mais alto do que o BAAM 1000 poderia imprimir verticalmente. Devido às limitações de espaço de impressão do eixo Z da impressora, os pesquisadores optaram por reduzir pela metade as duas ferramentas de subescala em seu comprimento e, em seguida, dividi-las novamente nas seções esquerda e direita (para resolver os problemas de rebaixo da tampa da longarina e facilitar a desmoldagem).
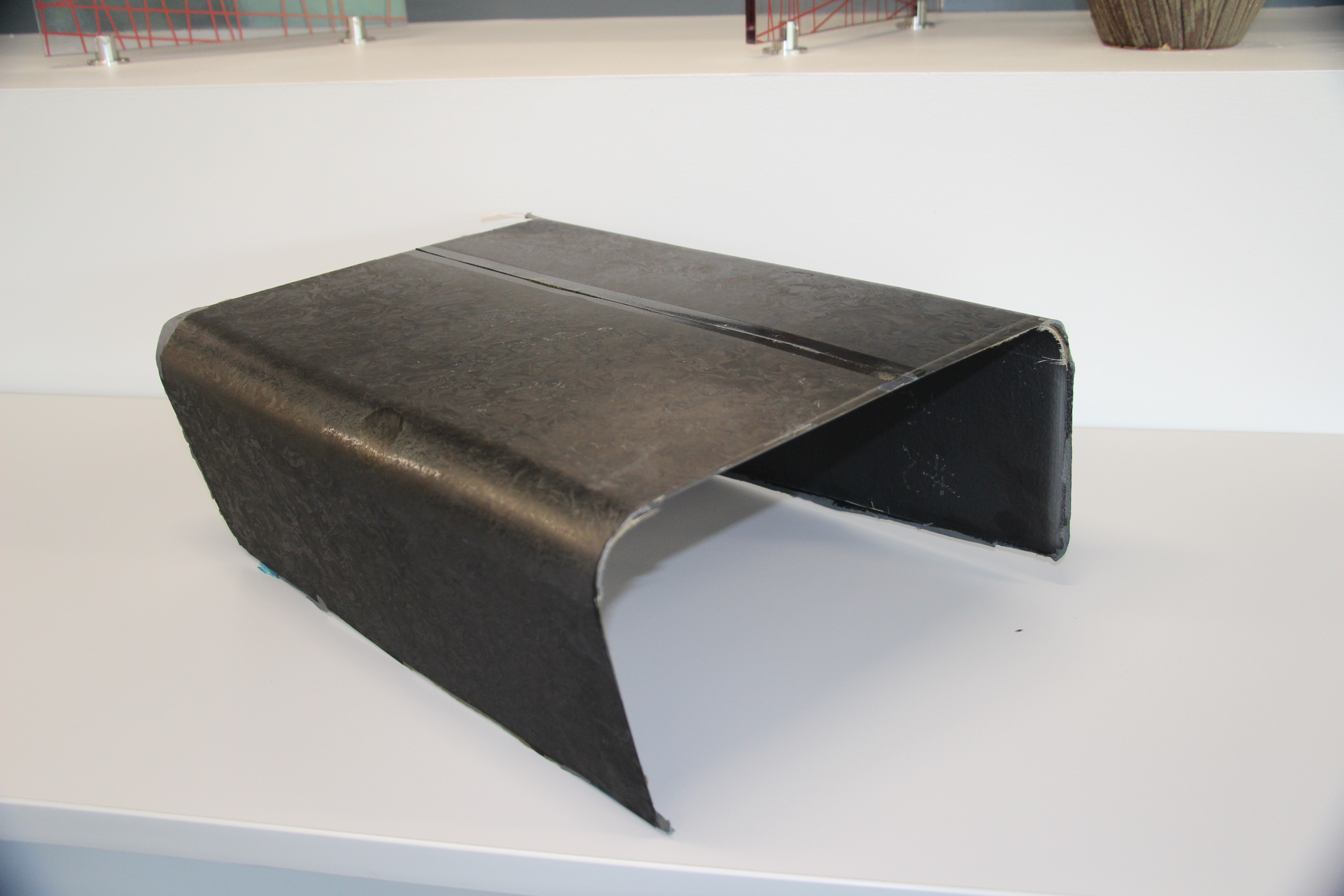
Para aumentar a eficiência da impressão, as seções da ferramenta foram impressas uma após a outra e depois cortadas em peças à direita e à esquerda. Para atingir o comprimento de 3,3 metros, as duas seções do lado direito foram unidas seguidas pelas duas seções do lado esquerdo usando o adesivo epóxi Loctite EA9394 da Henkel Corp. (Rocky Hill, Conn., EUA). A equipe deixou o núcleo AM sem usinar, sentindo que isso era fundamental para obter baixos custos de ferramentas e prazos de entrega curtos, bem como para criar um intertravamento mecânico entre o núcleo AM e as películas CFRP de cada lado. A parte posterior de cada metade da ferramenta foi laminada com cinco camadas de prepreg, enquanto a parte frontal foi laminada com nove camadas para fornecer material extra que poderia ser removido durante a usinagem pós-cura.
Resultados preliminares
Além de controlar o CLTE do núcleo AM, o pré-impregnado forneceu uma superfície sem corrosão que manteve a integridade do vácuo sem a necessidade de selante / revestimento. Essa abordagem foi tão bem-sucedida que permitiu o uso de um projeto de ferramenta de várias peças vedado com uma gaxeta, o que os pesquisadores acreditam não ter sido demonstrado anteriormente em ferramentas AM usadas em altas temperaturas. Além disso, a massa da ferramenta foi reduzida significativamente; a ferramenta de subescala tinha um terço do peso calculado para um design Invar comparável. As ferramentas CFRP mais leves não apenas são mais fáceis de manusear e armazenar em racks, mas também requerem ciclos mais curtos de aquecimento / resfriamento em autoclave. Em uma ferramenta para moldar o C-spar em escala real, essa vantagem de peso pode fazer a diferença entre estar abaixo ou exceder os limites de peso do pórtico / guindaste em alguns espaços de fabricação.
É importante ressaltar que o custo da ferramenta híbrida de 0,6 metros foi calculado durante a fabricação, usando taxas de mão de obra padrão da indústria, em $ 24.136 USD com uma divisão de aproximadamente 50/50 entre os custos de usinagem e os custos de impressão / laminação. Em contraste, uma ferramenta idêntica da Invar foi cotada a $ 46.775 USD - uma economia de quase 50%. Os custos da ferramenta de 3,3 metros não estão completos, mas devem gerar uma economia de cerca de 30% com base no custo / comprimento da unidade, pois os custos de material / impressão aumentam linearmente, mas os custos de usinagem desfrutam de uma economia de escala que reduz seu impacto. A abordagem híbrida produziu ferramentas que atendiam aos requisitos de desempenho operacional do Airbus e Northrop Grumman e é considerada uma alternativa viável ao Invar para protótipos rápidos ou ferramentas de baixo uso. A investigação da vida útil da ferramenta não fez parte deste estudo, mas provavelmente se estenderia consideravelmente além dos 12 ciclos que foram demonstrados.
O programa foi estendido de 18 para 30 meses, mas ainda há áreas onde mais estudos são necessários, como entender como a geometria final do núcleo impresso difere daquela prevista nos modelos CAE. A equipe também deseja melhorar a precisão preditiva para que camadas suficientes sejam adicionadas em áreas críticas para garantir que não haja punção durante a usinagem. Ainda assim, a equipe considerou este um projeto de sucesso com oportunidades consideráveis para ferramentas LFAM futuras.
“A Northrop Grumman está ansiosa para construir uma peça de demonstração da longarina de 3 metros usando a ferramenta híbrida de 3,3 metros construída pela UDRI e nosso próprio processo automatizado de conformação de reforço (ASF) para avaliar a durabilidade e estabilidade dimensional da ferramenta”, acrescenta Vern Benson, pesquisador técnico da Northrop Grumman.
Resina
- Evonik, Evolve Additive Solutions para desenvolver materiais de impressão 3D para o processo STEP
- Henkel oferece plataforma de materiais para fabricação de aditivos
- Essentium e Lehvoss fazem parceria para desenvolver materiais para fabricação de aditivos
- Novo Náilon 6 Estabilizado por Calor para Trem de Força Híbrido e Elétrico
- Trelleborg anuncia novo distribuidor de materiais de ferramentas
- UAMMI, Objetos impossíveis constroem peças compostas para a Força Aérea dos EUA
- Victrex e parceiro Bond para impressão 3D de peças PAEK
- AeroLas explora nova tecnologia de fiação para fio híbrido termoplástico
- Dicas para moldes de impressão 3D
- Minimizando tempos de retorno para peças grandes