Compósitos impressos em 3D com 60% de fibra, menos de 1% de vazios
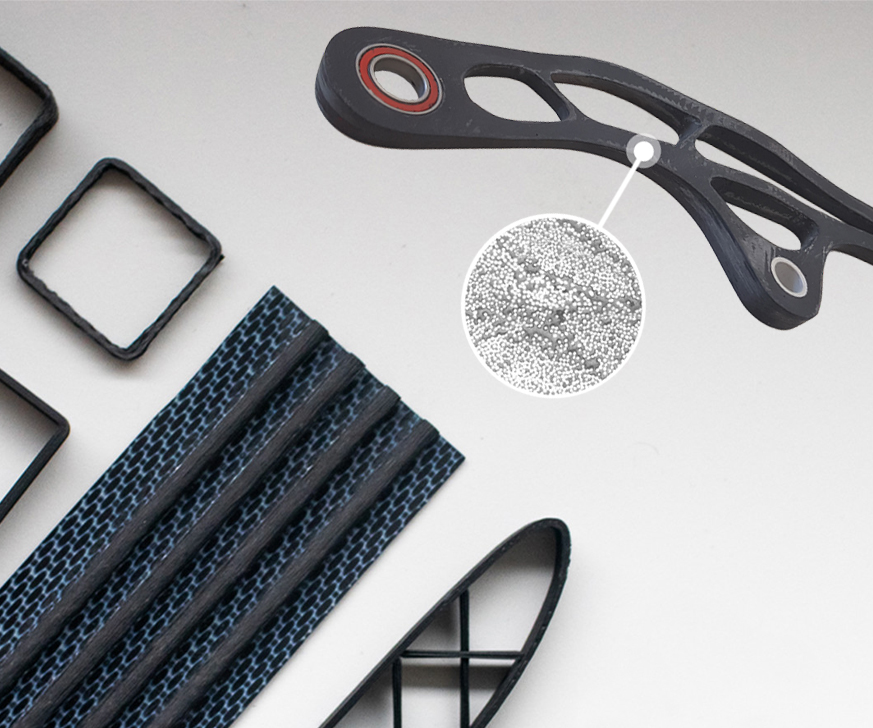
“Nosso principal objetivo é produzir compostos de fibra contínua estruturais para a indústria”, afirma o cofundador da 9T Labs (Zurique, Suíça), Giovanni Cavolina. “Se você conversar com pessoas que fabricam peças de CFRP (polímero reforçado com fibra de carbono), a maioria não acredita que seja possível obter um conteúdo de vazio super baixo ou uma boa resistência ao cisalhamento interlaminar (ILSS) entre as camadas com impressão 3D de fibra contínua.” 9T Labs, no entanto, desenvolveu um pós-processo patenteado que elimina espaços vazios. “Agora podemos imprimir compostos de fibra contínua em 3D com grande adesão entre as camadas e conteúdo vazio abaixo de 1 por cento, o que compete com os compostos fabricados convencionalmente.”
Começando na ETH Zurique
O 9T Labs começou com um projeto de pesquisa no Laboratório de Materiais Compósitos e Estruturas Adaptativas (CMAS) do Instituto Federal Suíço de Tecnologia de Zurique (ETH Zurique). Cavolina e cofundadores da 9T Labs, Martin Eichenhofer e Chester Houwink desenvolveu uma cabeça de impressão de compósitos, “que montamos em um braço robótico e fizemos núcleos treliçados para estruturas sanduíche ultraleves, voltadas para aplicações aeroespaciais”, explica Cavolina.
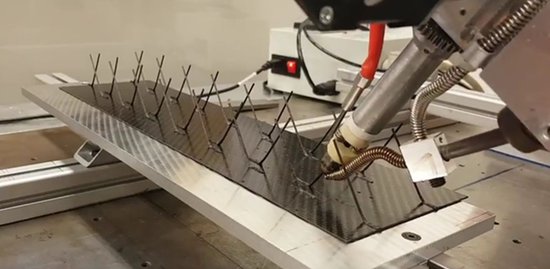
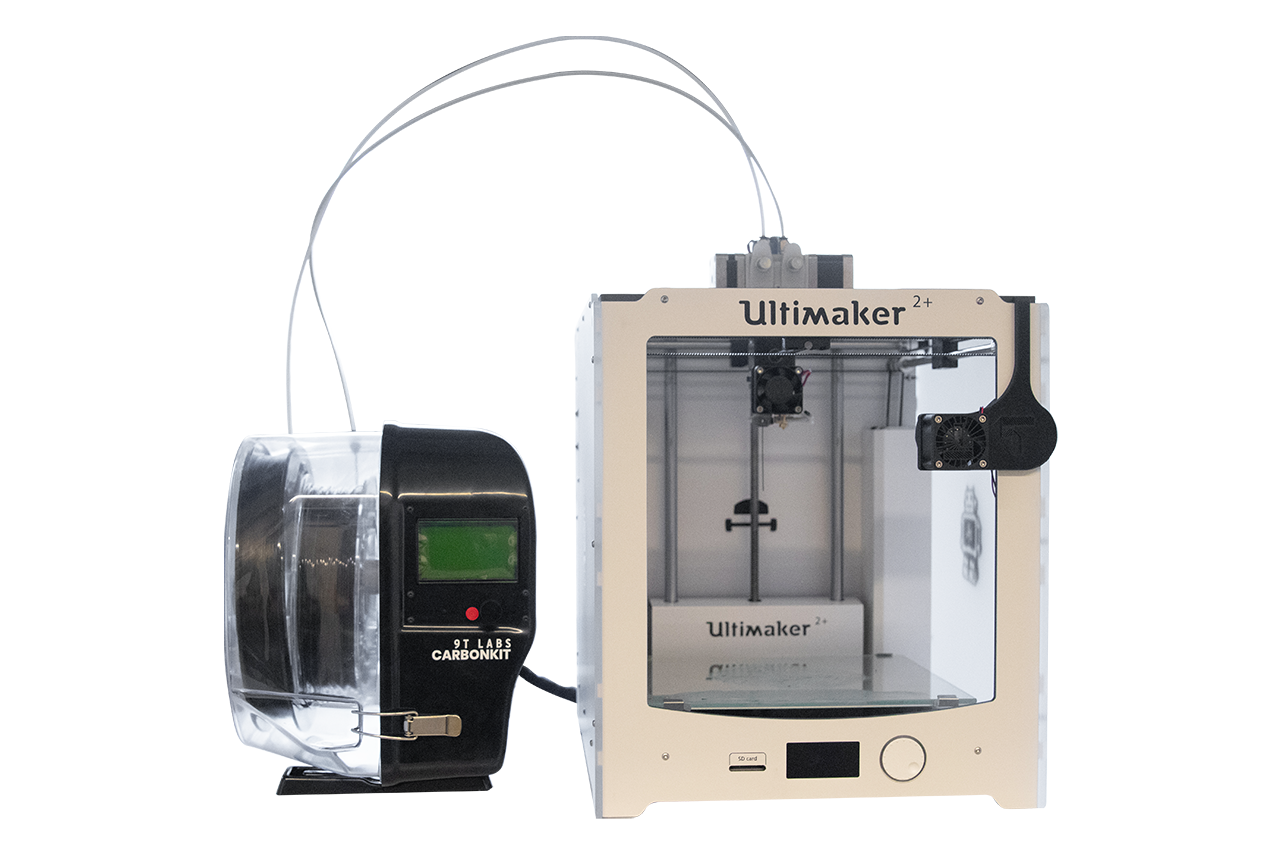
CarbonKit era um produto de liberação limitada que permitia que as impressoras FDM prontas para usar usassem fibra de carbono contínua, mas ainda não era a solução certa para a produção de peças estruturais CFRP de custo competitivo. FONTE | 9T Labs.
CarbonKit
Assim, o 9T Labs foi estabelecido no início de 2018 para provar o conceito de laminados CFRP monolíticos de impressão 3D que poderiam atender aos requisitos do cliente em potencial. “Nosso próximo passo foi o CarbonKit”, diz Cavolina. Este é o produto que é apresentado em CW Artigo de março de 2019 “Movendo a impressão 3D de fibra contínua para a produção”. O CarbonKit transforma as impressoras Ultimaker ou Prusa 3D em um sistema capaz de imprimir com fibra de carbono contínua. “Ele permite que você use suas impressoras existentes em combinação com nossa cabeça de impressão, filamentos e software para colocar fibras contínuas, de acordo com o caso de carga, com conteúdo de volume de fibra de carbono de 50 por cento - não 30 por cento, que tem sido a norma em impressão 3D CFRP ," ele adiciona.
Cavolina explica que embora o interesse por este produto fosse bastante grande, “atendíamos apenas 25 clientes. Mantivemos este produto limitado porque percebemos que com apenas um processo de FDM [modelagem de deposição fundida] de uma etapa, não é possível obter peças estruturais de uso final para aplicações aeroespaciais industriais que também sejam competitivas em termos de custo com as tecnologias atuais. ”
No entanto, por meio do CarbonKit, a 9T Labs estabeleceu relacionamentos valiosos com os clientes. “Pudemos aprender o que as empresas esperavam e precisavam, embora essas peças não fossem realmente possíveis de produzir com o CarbonKit”, explica ele. “A consolidação in situ é realmente possível com FDM, mas exigiria máquinas muito mais complexas e com custo proibitivo. Portanto, produzimos um processo de 2 etapas com uma consolidação pós-impressão. ”
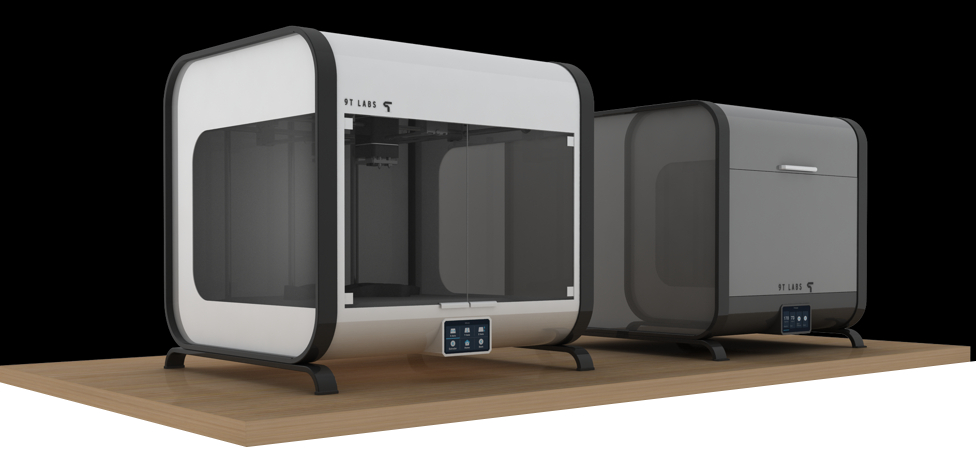
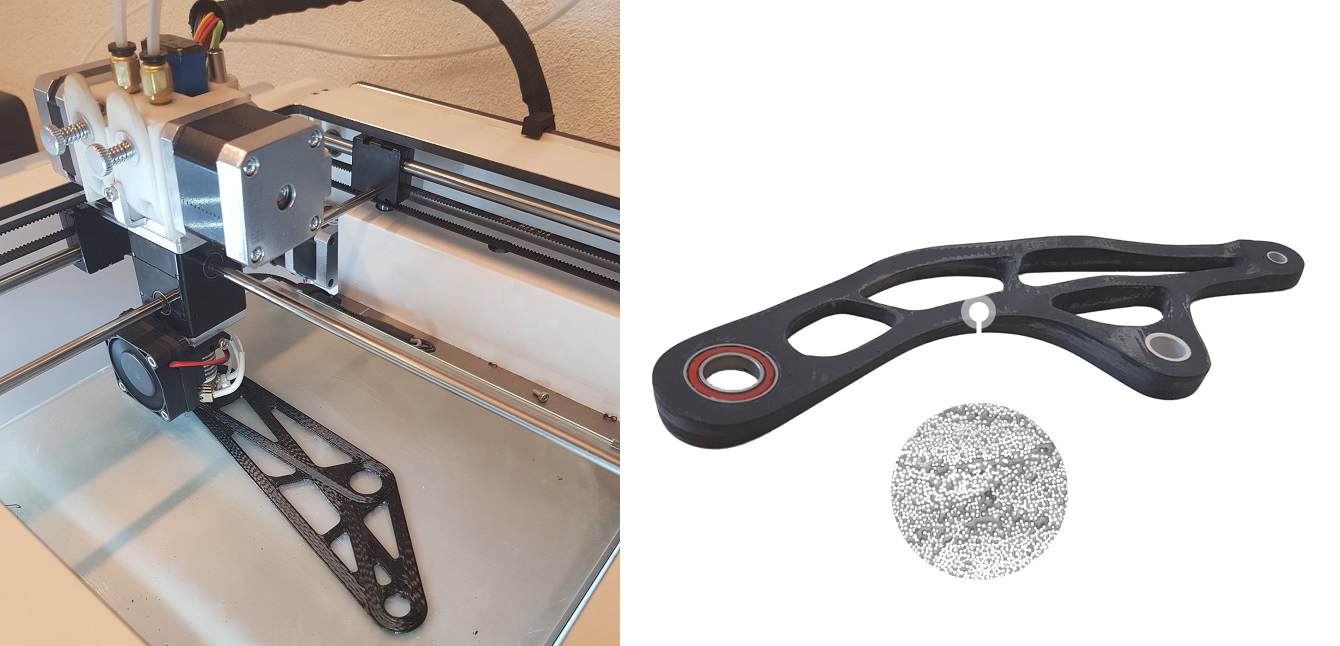
Com a Red Series, a 9T Labs obteve estruturas CFRP impressas em 3D com> 50% do volume de fibra e <1% de vazios a um custo acessível em comparação aos métodos de produção de compósitos atuais. FONTE | 9T Labs.
Série Vermelha, processo de 2 etapas
Isso nos leva aonde a 9T Labs está hoje. “Estamos comercializando a Série Vermelha, que compreende duas unidades:uma unidade de impressão FDM clássica com uma cabeça de impressão patenteada e uma Unidade de fusão adjacente para pós-processamento”, explica Cavolina. “Não alcançamos a consolidação in-situ completa durante a impressão, mas, em vez disso, imprimimos e consolidamos em um segundo processo. Em essência, estamos imprimindo uma pré-forma que é colocada na Unidade de Fusão para pós-consolidação usando alta temperatura e pressão para atingir mais de 50% do volume de fibra com menos de 1% de vazios. Este processo de 2 etapas atinge qualidade aeroespacial a um custo acessível. ”
A Série Vermelha usa materiais termoplásticos, por enquanto. “Imprimimos fibra de carbono com PEI, PEKK, PA (náilon) e também temos experiência com PP”, diz Cavolina. A Série Vermelha é um sistema de materiais abertos? “A única maneira de ser competitivo em termos de custos é usar os materiais existentes em um novo processo de fabricação”, explica ele. “Se você criar seu próprio material do zero, estará excluindo a possibilidade de entrar na fabricação em série. Por motivos de segurança e confiabilidade da cadeia de suprimentos, os fabricantes de séries não dependerão de uma pequena empresa para seus materiais. Portanto, permitimos que nossos clientes usem seu suprimento de materiais existente, garantindo que os materiais funcionem em nosso sistema. ” Ele explica que o 9T Labs testa os materiais para garantir que a matéria-prima atenda a certos requisitos e determine os melhores parâmetros para impressão.
E quanto ao software aberto? “Nosso software de impressão é combinado com um software de simulação estrutural”, diz Cavolina. “É ótimo para um engenheiro colocar fibras onde necessário, mas como você pode ter certeza de que é realmente onde elas devem ser colocadas? Nosso software dá a liberdade de projetar e, em seguida, fazer a verificação cruzada com uma simulação estrutural. A outra direção é definir um layup orientado a fibra em uma simulação estrutural e, em seguida, convertê-lo em um caminho de impressão em nosso software. Usamos um parceiro já existente, testado e conhecido para a FEA que é executado em segundo plano. Você também pode projetar uma peça em CAD diretamente e, em seguida, carregar esse arquivo em nosso programa. Lá, você decide onde quer a fibra de carbono e onde o polímero puro é suficiente. ”
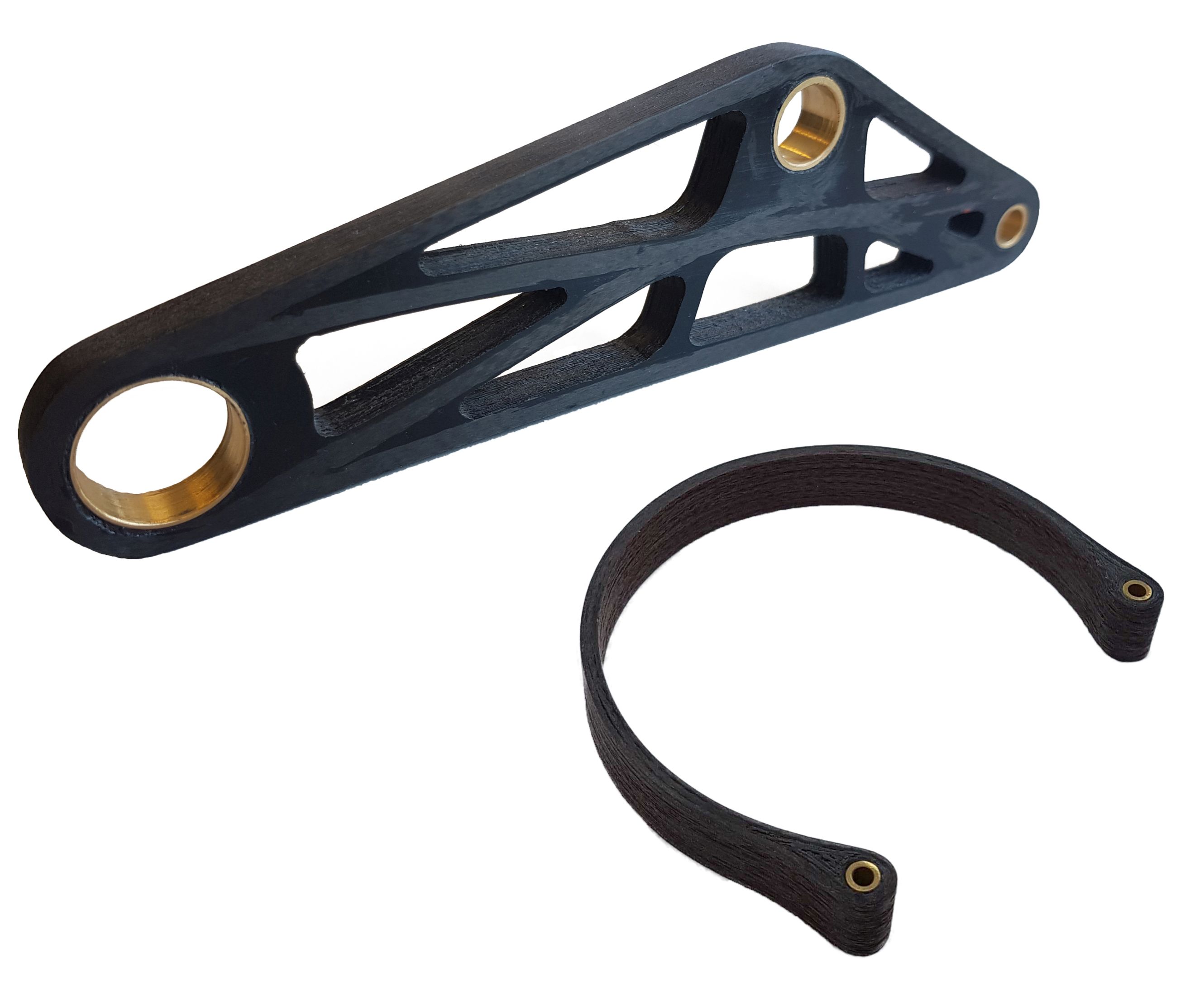
Este suporte de CFRP e balancim para aplicações não aeroespaciais realmente atendem aos requisitos de laminado aeroespacial e apresentam mais de 40 camadas - cada camada com uma orientação de fibra diferente para explorar a anisotropia e otimizar peças estruturais que não eram possíveis anteriormente. FONTE | 9T Labs.
Aplicativos
9T Labs está buscando aeroespacial (interiores, por enquanto), automação biomédica e industrial (por exemplo, máquinas de embalagem), bem como lazer / luxo (por exemplo, esportes motorizados, calçados esportivos, óculos). Este último mercado, diz Cavolina, “é onde você precisa ter compostos estruturais, mas os requisitos não são tão rígidos quanto no aeroespacial”. Ele cita o braço oscilante mostrado acima. “Este é um suporte para uma estrutura não aeroespacial que representa uma aplicação estrutural que você pode produzir de forma otimizada usando nossa tecnologia”, explica ele. “Ele vem de uma peça de alumínio com topologia otimizada para economizar peso orientando as fibras de carbono de acordo com o caso de carga. Você pode economizar custos porque pode reduzir a quantidade de fibra de carbono usada em comparação com outros processos de compósitos. Você não pode fazer isso por outros meios, porque não é possível com outros métodos orientar cada fibra conforme necessário em alta resolução. ”
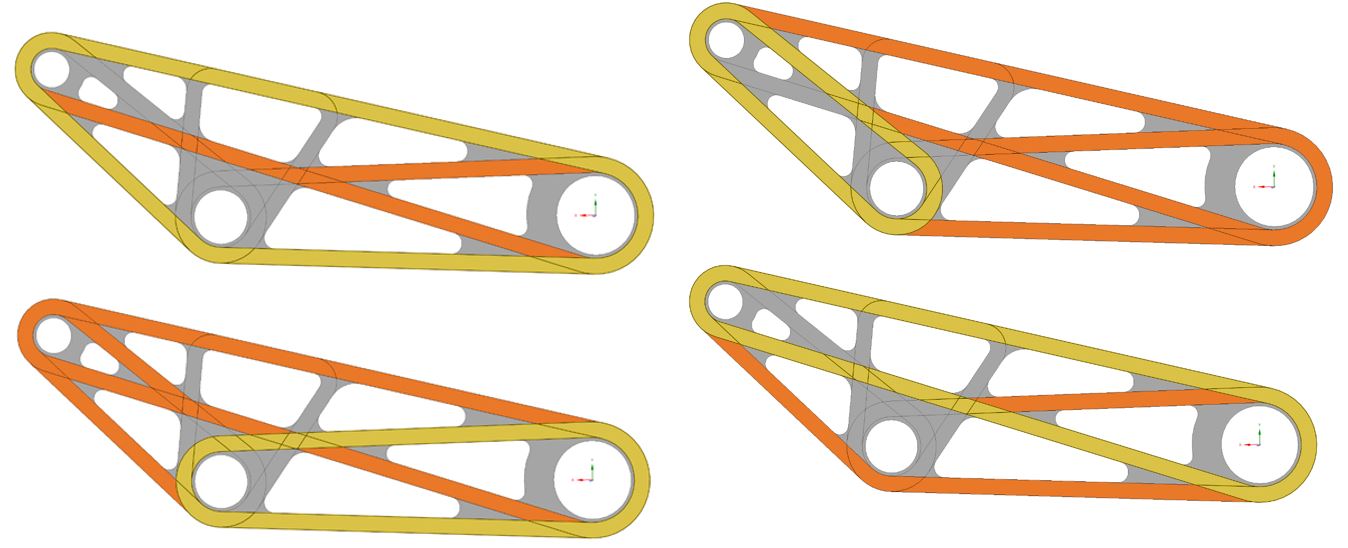
Quatro layups de fibra de carbono contínuos diferentes são alternados em toda a espessura do suporte CFRP impresso com 9T Labs Red Series. FONTE | 9T Labs.
Cavolina observa que este balancim compreende mais de 40 camadas de fibra e polímero, “e podemos ter orientações de fibra diferentes em cada camada. Tentamos quatro layups diferentes, não restritos a quase isotrópicos. Essa liberdade nos permite explorar a anisotropia dos compostos para otimizar ainda mais a estrutura de uso final. Não seria possível fazer isso com outros métodos de fabricação atuais. ”
Ele também destaca que a impressão 3D CFRP é um processo automatizado em comparação com a configuração manual. “Nossa tecnologia reduz drasticamente o trabalho manual por meio de layup automatizado”, diz Cavolina. “Com a nossa tecnologia, basta imprimir, consolidar e pronto.”
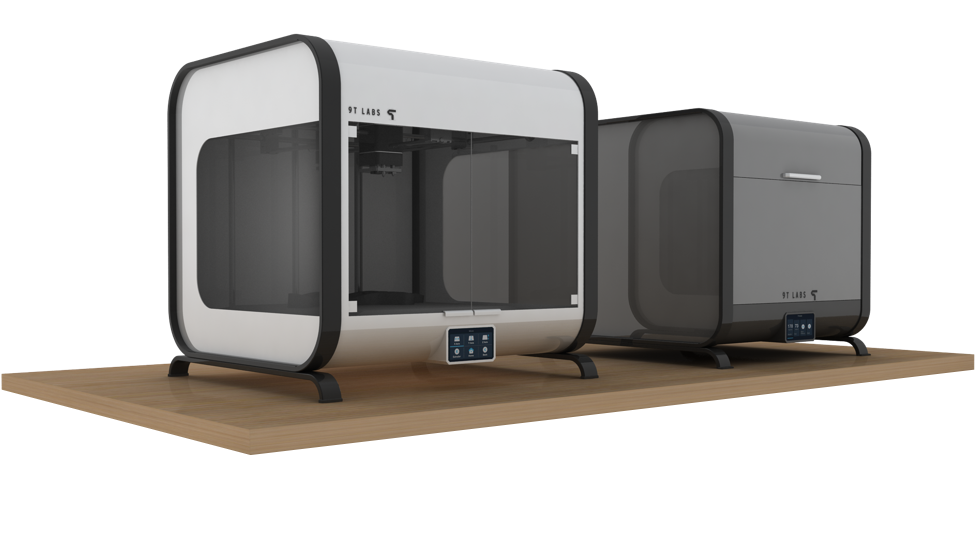
A Red Series imprime pré-formas menores, complexas e monolíticas de CFRP que são consolidadas em uma segunda etapa para produção em série industrial escalonável. FONTE | 9T Labs.
Tamanho de impressão da Red Series, velocidade e lançamento completo
A Red Series é destinada a peças menores e monolíticas para fabricação em série em uma área de impressão de 350 por 300 milímetros. “Aqui vemos no momento o maior valor agregado para nossos clientes”, explica Cavolina.
E quanto à velocidade de impressão? “Estamos falando de uma forma muito concreta sobre a produção nos próximos 1-2 anos de 4.000 a 8.000 peças por ano para clientes diferentes, alcançada com as unidades gêmeas da Série Vermelha”, diz Cavolina. “Como separamos a produção de pré-formas complexas e detalhadas da consolidação, agora é possível aumentar o volume de produção rapidamente.”
“Passamos muito tempo analisando a estrutura de custos do nosso processo, incluindo equipamentos, mão de obra e custos de material”, ele responde. “Temos uma estrutura de custo de equipamentos acessível e automatizamos o processo de pré-formação. Usamos materiais que são mais baratos e eficientes e, em seguida, reduzimos a quantidade de material necessária orientando as fibras de acordo com o caso de carga e usando a otimização estrutural. Trabalhamos em estreita colaboração com nossos parceiros em simulação estrutural e de processo e vemos que isso continuará a crescer como uma grande parte do objetivo de produção de usar a tecnologia dupla digital para permitir plug and play com células e linhas de produção 4.0. ”
A Série Vermelha será lançada em 2020. “Agora, estamos avaliando isso por meio de nossos programas de colaboração com parceiros de produção. Certificamos as peças e processos com eles, portanto, eles reservaram os primeiros slots para as máquinas da Série Vermelha e os usarão para fabricar seus produtos de uso final. ”
Resina
- Reforçando as peças impressas em 3D com roteamento de fibra eficiente:Parte 1
- Parte da semana - Tripé impresso em 3D com pernas contínuas reforçadas com fibra de carbono
- Reciclagem:Compósitos termoplásticos reforçados com fibra contínua com policarbonato reciclado
- Compostos curtos de fibra de carbono expandem o alcance dos compostos termoplásticos
- TxV Aero Composites está em conformidade com os padrões AS9100
- Hexcel faz parceria com Lavoisier Composites, Arkema
- Reciclagem de compósitos - chega de desculpas
- Covestro lança termoplásticos de fibra contínua Maezio
- Fabricação contínua de fibra (CFM) com compostos moi
- Compósitos para impressão 3D com fibra contínua