Fabricação contínua de fibra (CFM) com compostos moi
A impressão e deposição contínua em 3D de fibra está ganhando impulso. Conforme o número de empresas que a usam e a fazem crescer, essa tecnologia sem dúvida moldará a indústria de compósitos.
Em primeiro lugar, oferece fabricação sem moldes ou ferramentas. Em segundo lugar, oferece estruturas multifuncionais (por exemplo, condutividade elétrica, mudança de forma, detecção). Terceiro, ele abre a porta para um mundo de manufatura hibridizada - por exemplo, laminação em cima de impressão 3D e fresagem durante a impressão - bem como uma paisagem quase infinita de desenvolvimento de materiais, de fibras de liga de Nitinol com memória de forma (SMA) a soluções de nanocompósitos condutivos para modelagem de deposição líquida (LDM). Este último é um mundo inteiro ao qual voltarei em um futuro blog.
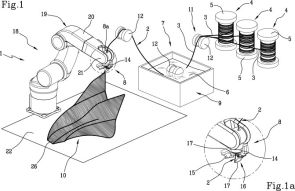
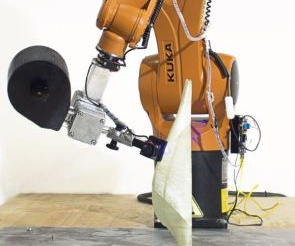
Patente WO2017085649A1 e sistema de impressão Atropos. FONTE:compósitos moi.
A Moi composites foi criada em fevereiro de 2018 pela engenheira de materiais e professora Marinella Levi, a engenheira de design Gabriele Natale e a arquiteta Michele Tonizzo. Em 2013, o professor Levi começou a trabalhar com impressão 3D no Politecnico di Milano (Milão, Itália). Em 2014, ela formou o + LAB no Departamento de Química, Materiais e Engenharia Química da universidade "Giulio Natta". Sua visão era fundir P&D, ensino e inovação de materiais reunindo engenheiros, designers, pesquisadores e fabricantes em um centro de impressão 3D colaborativo e multidisciplinar.
2014 Primeira ferramenta para impressão 3D de compósitos termofixos de fibra contínua 2015 Patente WO2017085649A1 2016 Parcerias com Owens Corning e KUKA Robotics,
Atropos projeto e sistema de impressão 2017 Prêmio JEC de Inovação, parceria com Autodesk,
Vice-campeão do prêmio James Dyson,
Parceria com automação COMAU
(Linha do tempo completa)
“Começamos a moi composites porque queríamos produzir peças comerciais e nos envolver em projetos internacionais”, explica Michele Tonizzo. “Descobrimos que há muito mercado. Estamos fabricando componentes biomédicos, bem como peças para aplicações marítimas, de petróleo e gás e aeroespaciais, principalmente usando fibra de vidro. A tecnologia CFM é capaz de fabricar soluções exclusivas que seriam impossíveis com os métodos tradicionais. "
Lâmina da hélice impressa em 3D com treliça estrutural interna usando fibra de vidro contínua (topo). Este projeto também demonstrou a colocação de fibra ao longo de curvas não lineares (canto inferior esquerdo) e laminado de fibra contínua com orientações de fibra tradicionais (por exemplo, 0 °, + 45 °, -45 °, 90 °, canto inferior direito). FONTE:compósitos moi
Gama de resinas e fibras
Atropos demonstrou a capacidade de imprimir polímeros termofixos reforçados com fibras descontínuas e contínuas, não apenas camada por camada, mas também ao longo de curvas não lineares. Ele usou luz ultravioleta (UV) para curar os polímeros no local. “Atualmente, podemos imprimir com cura UV em epóxi, acrílico e vinilester”, diz Tonizzo. Ele observa que o acrílico funciona bem para peças arquitetônicas porque é transparente e não requer temperatura para cura / pós-cura. Vinylester é usado para peças marítimas e epóxi para óleo e gás e peças aeroespaciais.
“Para algumas aplicações, a cura por UV é apenas o estágio inicial e depois fazemos a pós-cura com aquecimento convencional”, observa Tonizzo. “Não estamos presos à cura por UV. Imprimimos com polímeros de cura não UV e entendemos que, para aplicações de propriedades mais altas, precisaremos de diferentes opções de matriz. ” Para referência, a temperatura de transição vítrea (Tg) para a resina mais comumente usada, um viniléster, é de cerca de 140 ° C.
“Também estamos trabalhando com fibra de carbono, mas não com resinas de cura UV”, diz Tonizzo. Ele ressalta que tanto a transparência da fibra quanto a cor afeta a cura por UV. “O problema com o carbono é que ele é opaco e Preto. Esta é a pior combinação. Queremos desenvolver a melhor solução para a fibra de carbono como material, não apenas a tecnologia mais fácil que funciona. Existem muitas outras opções de materiais de cura que podemos usar, por isso estamos investigando isso. ”
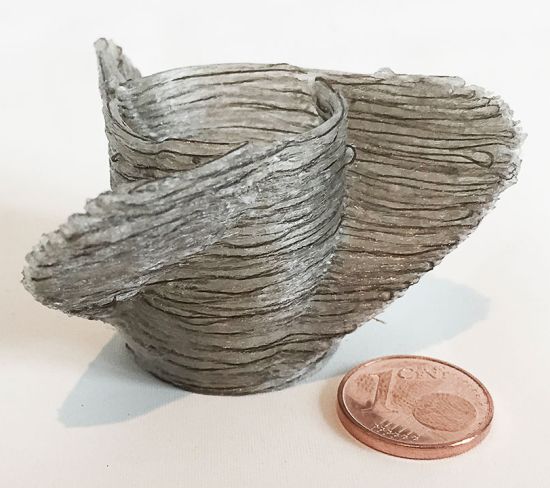
Compostos Moi podem imprima fibras condutivas contínuas para funcionalidade elétrica / térmica, detecção, mudança de forma, etc. FONTE:compostos de moi.
A Moi composites imprimiu fibra de vidro contínua de até 2.400 tex (207 jd / lb com um diâmetro máximo de 24 μm de acordo com uma folha de dados da Owens Corning) e está testando fibras naturais. Também imprimiu com fibra de basalto. “Podemos imprimir muito bem com cura UV e fibra de basalto porque, na verdade, é um pouco transparente e mais marrom do que preto”, explica Tonizzo.
As fibras que conduzem corrente elétrica também podem ser utilizadas na tecnologia CFM. Eles podem ser colocados conforme necessário na estrutura que está sendo impressa. Um dos projetos listados no site + LAB mostra a fibra de Nitinol, que é uma liga com formato de memória. “Assim, você poderia fazer estruturas que mudam de forma”, diz Tonizzo. “Por exemplo, você poderia usá-lo para liberar tensão em outras fibras, como em concreto protendido.”
impressão 3D como parte da fabricação de híbridos
Atropos usa um braço robótico Kuka com um envelope de impressão de 0,5 x 0,5 x 0,5 m de altura. “Agora estamos imprimindo em um robô Comau com um envelope de 1,0 x 0,5 x 0,8 m de altura, que é o sistema de segunda geração”, diz Tonizzo. “Também usamos robôs maiores com mesas rotativas e volumes de construção de 1,5 x 1,5 x 1 m de altura e demonstramos que nossa tecnologia é facilmente escalonável.”
A Moi também está desenvolvendo uma cabeça de impressão all-in-one de terceira geração com um sistema para aplicar pressão às fibras, sensores, mecanismos de corte e ferramenta de fresagem. Tonizzo diz que isso fechará a lacuna entre a impressão 3D e a colocação automática de fibras (AFP ) “A impressão 3D não atinge o desempenho do AFP, mas o CFM oferece mais flexibilidade. Já conseguimos imprimir com fibras de 0,25mm de espessura e temos a capacidade de criar curvas e colocar fibras contínuas na posição ideal ”, acrescenta.
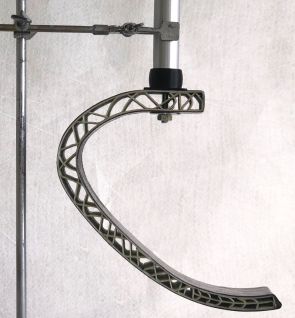
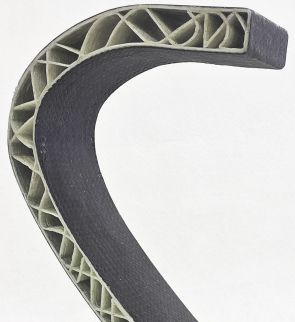
SuPeRIOR é um Prótese de membro inferior otimizada para o mínimo de peso, deflexão e custo.
O núcleo estrutural impresso em 3D foi então laminado com fibra de carbono e resina epóxi seguido pela cura VBO. FONTE:compósitos moi.
“A impressão 3D deve ser usada para o que faz de melhor”, diz Tonizzo, “o que inclui a otimização do fluxo de trabalho. Por exemplo, você pode imprimir em 3D um núcleo interno com recortes e direções de fibra inteligente. Você então usa laminação manual comum no topo e cura em autoclave ou apenas com saco a vácuo. ” Ele descreve uma peça que era impossível fazer convencionalmente com um molde. “Imprimimos o núcleo interno e depois o envolvemos em laminado e o curamos em autoclave a 110 ° C e 2 bar de pressão por várias horas. A parte ficou ótima. ” Esta parte é coberta por um acordo de sigilo, portanto, não há mais detalhes disponíveis, mas a moi produziu a prótese SuPeRIOR de maneira semelhante, curada não em autoclave, mas apenas com bolsa a vácuo (VBO). “Todos os internos estão usando uma fibra de vidro contínua”, explica ele, “mas o laminado externo é um tecido de fibra de carbono de layup manual e resina epóxi”. Todo o design reduz a deflexão e aumenta a personalização, ao mesmo tempo que reduz significativamente os custos e o tempo de produção.
Software de otimização baseado em Voxel
Tonizzo explica que o processo de projeto da peça combina o algoritmo baseado em voxel da Autodesk com os algoritmos de moi para otimização de tensão e caminho. Isso é o que produz o caminho otimizado da fibra para a estrutura. O software também trabalha para escolher o caminho mais possível para a fabricação. “Este é um processo iterativo”, diz Tonizzo. “O design não é totalmente automatizado como o design generativo. Ainda precisa de engenheiros para fazer escolhas. Mas acho que é assim que deve ser - o designer e o software combinados, não apenas a IA sozinha. ”
Futuro multimaterial, forte potencial de mercado
Em uma das imagens da pá da hélice impressa em Atropos, há um close up mostrando um padrão quase tecido. “Isso não é tecido, mas será possível em breve”, diz Tonizzo. Ele me direciona para o projeto de onda senoidal no site + LAB. “Os demonstradores mostrados são impressos em 3D em plástico com fibras curtas e o processo LDM [modelagem de deposição líquida] enquanto eram pesquisadores do + LAB. Os algoritmos que usamos são os mesmos que estamos avançando agora com fibra contínua ”.
+ LAB’s Sine Wave demonstra padrões de preenchimento de polímero impresso em 3D com uma resposta elástica ajustável. FONTE:+ LAB.
É óbvio, pelo site + LAB, que as inovações e possibilidades de materiais para este tipo de impressão são quase infinitas. A questão é saber o que oferecerá a maior oportunidade e potencial para soluções de alta demanda. Enquanto isso, os fornecedores de materiais estão apoiando o desenvolvimento contínuo. Por exemplo, a Owens Corning está interessada em demonstrar fibra de vidro com mais matrizes, como cerâmica e concreto. Obviamente, isso é muito interessante para aplicações de construção e pode ter um potencial significativo à luz das tendências atuais para fabricação digital e construção com eficiência energética, módulos pré-fabricados externos e sustentabilidade aprimorada por meio de materiais naturais e reciclados, todos os quais são leves. “O Departamento de Giulio Natta no Politécnico de Milano está em um projeto da UE para imprimir geopolímeros que se comportam como concreto”, acrescenta Tonizzo. “Elas curam sozinhas com o tempo, mas ficam com a consistência de argila durante a impressão para um melhor escoamento. Com certeza continuaremos trabalhando nesta área, bem como com novos polímeros e fibras. ”
Compostos Moi é também imprimindo com geopolímeros, que se comportam como concreto.
FONTE:+ LAB.
Você venderá máquinas? “Sim, mas no futuro”, diz Tonizzo. “Por enquanto, estamos produzindo peças e trazendo a tecnologia para as instalações do cliente, usando nosso know-how, cabeça de impressão e software para realizar soluções de peças sob demanda.” Ele acrescenta que, tendo trabalhado no ano passado para melhorar a tecnologia com os primeiros a adotar CFM, e demonstrar o caso de negócios para muitas peças diferentes em diferentes mercados, a moi composites está agora buscando investidores para dimensionar ainda mais máquinas e processos CFM para oportunidades de mercado comercial.
Resina
- Acessórios de montagem de impressão 3D com compósitos Markforged
- Fabricação de aditivos com compostos na indústria aeroespacial e defesa
- Avaliando uma cadeia de suprimentos de compósitos em fluxo
- Comercialização de termofixos curáveis por UV para impressão 3D de fibra contínua
- Reciclagem de compósitos - chega de desculpas
- Fabricação contínua de fibra confunde a linha entre a impressão 3D e AFP
- Covestro lança termoplásticos de fibra contínua Maezio
- Compósitos para impressão 3D com fibra contínua
- A Severstal investe em robótica para automatizar a fabricação de compostos avançados com Airborne
- GE Digital:Insights operacionais com dados e análises