Pré-formação automatizada, Parte 7:Preencher Gesellschaft
Esta é a parte final de uma série de sete partes sobre pré-formação. Para obter mais informações sobre esta série, clique nos links abaixo:
FONTE:Preencher Gesellschaft
Histórias de casos de automação
As primeiras máquinas de Fill foram desenvolvidas para automatizar a produção de esquis para Fischer. Hoje, são necessários 25% dos trabalhadores para produzir 80% do volume de produção anual original. Observe também que os esquis têm um design híbrido, compreendendo camadas de vidro e / ou composto de fibra de carbono, núcleos de madeira, bordas de aço e vários tipos de plástico.
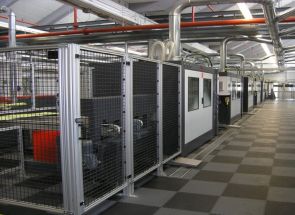
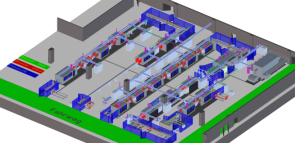
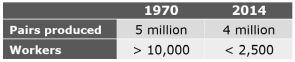
Preenchimento fornecido várias gerações de equipamentos automatizados para a produção de esquis compostos.
FONTE:Preencha a apresentação Gesellschaft 2017 CAMX.
BMW
Enquanto a BMW desenvolvia os modelos i3, i8 e os novos 7 Series - todos usando compostos de plástico reforçado com fibra de carbono (CFRP) - Fill forneceu uma gama de soluções de automação.
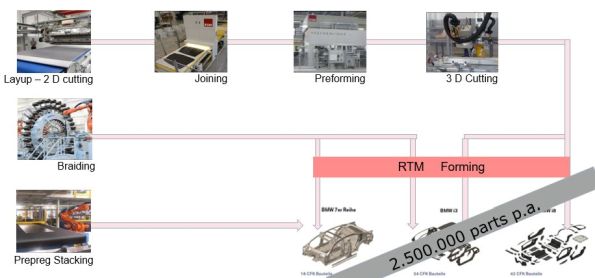
FONTE:Preencher Apresentação Gesellschaft 2017 CAMX
Monocoques compostos
Fill também desenvolveu uma linha de produção exclusiva para a Mubea CarboTech, capaz de produzir monocoques CFRP para dois modelos de automóveis diferentes:o Volkswagen VW XL1 e o Porsche 918 Spyder. Essa linha automatizada incluía ferramentas de moldagem atuada por várias peças, moldagem por transferência de resina de alta pressão (HP-RTM), recursos de pós-cura e usinagem.
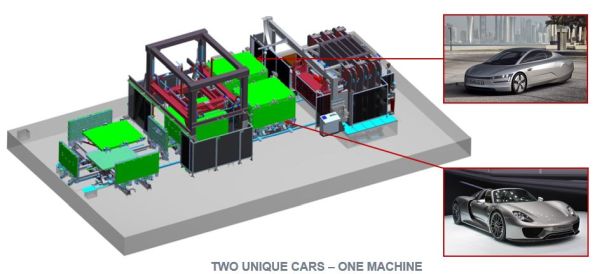
Preencha fornecido um linha de produção de monocoque composto para Mubea CarboTech.
FONTE:Preencher a apresentação Gesellschaft 2017 CAMX
Automatizando Layup
Para layup automatizado, Fill desenvolveu sistemas para uma variedade de materiais diferentes, incluindo tecido seco de até 3 m de largura (para produção de alto volume na BMW). O sistema automático de colocação de capas de longarina SpeedLayer 800 para pás de turbina eólica aplica prepreg de fibra de carbono unidirecional de até 800 mm de largura a uma taxa relatada de 1,5 m / se precisão de ± 1,5 mm. Ele pode lidar com rolos pré-impregnados de 600 kg e integra funções de validação de processo e garantia de qualidade.
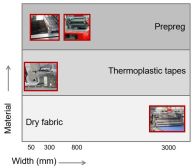
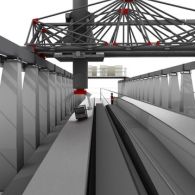
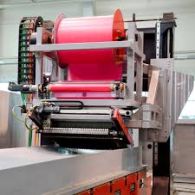
Preenchimento desenvolvido uma gama de sistemas de layup automatizados (esquerda) incluindo SpeedLayer 800 para longarinas de pás de vento usando pré-impregnado de carbono UD de até 800 mm de largura (direita).
FONTE:Preencher a apresentação Gesellschaft 2017 CAMX
O projeto de Processo Composto Flexível de Baixo Custo (LOWFLIP) foi uma iniciativa financiada pela UE de 3 anos (outubro 2013-outubro 2016) que incluiu Fill e nove outros parceiros, com o objetivo de automatizar o layup prepreg para transporte curado fora da autoclave (OOA) estruturas. É composto por três manifestantes:
- 2,5 × 2,9 m de parede frontal para um reboque de caminhão
- Travessa transversal automotiva com 1,2 m de comprimento
- Painel do cone de cauda de aeronave com pele endurecida de 1,0 × 1,2 m
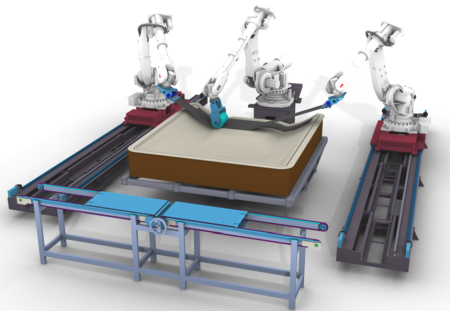
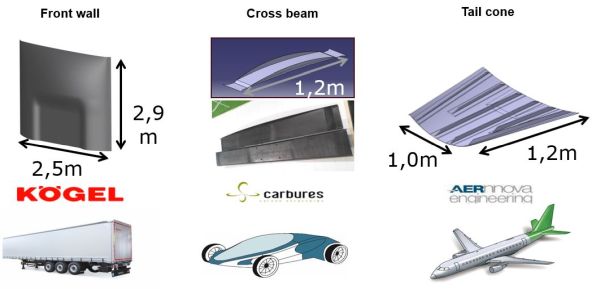
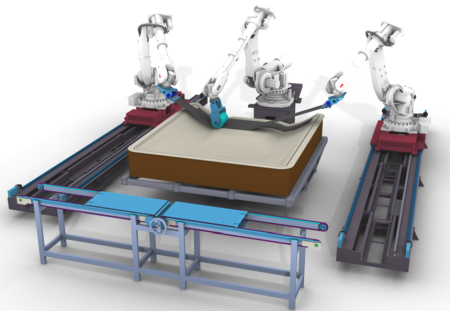
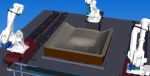
Animação
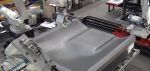
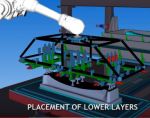
Fill trabalhou com nove parceiros no LOWFLIP para desenvolver uma célula de layup automatizada para a produção de grandes estruturas de transporte compostas sem autoclave.
FONTE:Preencher a apresentação Gesellschaft 2017 CAMX
“Usamos aquecimento por resistência elétrica para aquecer o molde até 120 ° C”, lembra Wilhelm Rupertsberger, chefe do Centro de Competência da Fill para Compósitos e Plásticos. “O material estava sempre sob tensão durante o layup automatizado”, acrescenta, “e conseguimos um revestimento sem rugas diretamente no molde. Construímos um processo humano, mas usando robôs para melhorar a repetibilidade. ”
Você pode ver a parede do trailer do caminhão à esquerda, bem como a viga transversal do carro e os demonstradores do painel do cone da cauda da aeronave na foto da equipe LOWFLIP acima .
FONTE:Preencher a apresentação Gesellschaft 2017 CAMX
Sistema Multi-Layup para Multicamadas
O sistema Multi-Layup da Fill foi desenvolvido para a produção de peças automotivas body-in-white (BIW), como paredes traseiras e reforços de pára-choques inferiores usando fitas termoplásticas. Foi previsto que essas peças incluiriam nervuras sobremoldadas e outros recursos, portanto, o ciclo de layup para a pré-forma precisaria corresponder ao ciclo de moldagem por injeção subsequente.
Minha postagem no blog pós-show do JEC 2017 incluía um vídeo do Sistema Multi-Layup, que alimentava fitas de vários rolos, colocando todas as fitas necessárias por camada simultaneamente, em vez de em série, uma de cada vez. Desta forma, atingiu um tempo de ciclo de 10-15 segundos por camada.
Fill agora modificou ainda mais o sistema e o renomeou como Multicamadas. Ele alimenta, corta e coloca até 16 fitas em larguras de até 50 mm (cada 0,01-0,04 mm de espessura) em uma mesa rotativa. O leito de colocação de fita pode produzir peças de até 1,6 x 1,6 m. As fitas são aplicadas a uma velocidade de ≈500 m 2 / h - a cada 12-15 segundos, uma camada de peça de tamanho real é aplicada por aproximadamente um tempo de ciclo de 1 minuto por pré-forma acabada. As camadas não são totalmente consolidadas, mas unidas por ligação térmica. À medida que cada bobina fica sem fita, ela é trocada automaticamente sem parar a máquina.
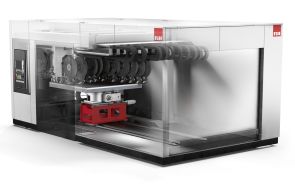
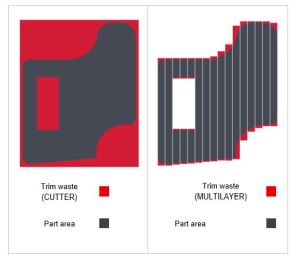
Fill's Multilayer automatizado O sistema de pré-formação permite uma redução significativa no desperdício de aparagem, colocando fitas somente onde necessário e orientando-as conforme necessário para obter laminados personalizados.
FONTE:Preencher a apresentação Gesellschaft 2017 CAMX
As pré-formas acabadas são então consolidadas em uma prensa. “Integramos o Multilayer com uma prensa de consolidação automatizada e célula de moldagem por injeção Engel, que funcionam em conjunto para fornecer um tempo de ciclo de 1 minuto”, diz Rupertsberger. A Fill recebeu um pedido para o primeiro sistema multicamadas da Swinburne University of Technology (Melbourne, Austrália) no início deste ano e irá demonstrar o equipamento ao vivo pela primeira vez no JEC World 2019 (12 a 14 de março, Paris, França).
Prensas RTM e injeção adaptativa
A Fill forneceu várias impressoras RTM, incluindo impressoras HP-RTM para SGL Composites.
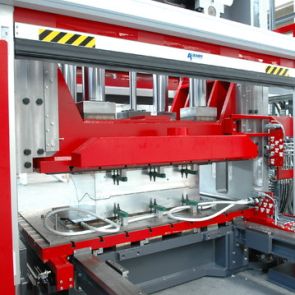
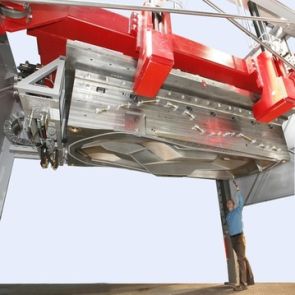
Preenchimento fornecido uma ampla variedade de impressoras para produção de compósitos, incluindo impressoras HP-RTM até SGL Composites (à direita).
FONTE:Preencher Gesellschaft
Com a Airbus Operations (Stade, Alemanha) e o Institute of Plastics Processing (IKV) da RWTH Aachen University, Fill desenvolveu uma unidade de injeção adaptativa inovadora para RTM, inicialmente para estruturas de aerocomposto. Antes que as peças feitas com RTM possam voar em uma aeronave, elas devem passar por um processo de garantia de qualidade (QA) demorado e caro. Para encurtar esse processo, as ferramentas de modelagem RTM foram equipadas com sensores, permitindo que o QA seja implantado em linha durante a produção. IKV, Airbus e Fill integraram agora esses sensores no sistema de injeção, eliminando a necessidade de equipar todas as ferramentas de modelagem. Usando cartuchos descartáveis da mesma forma que os sistemas de injeção de pistão são usados em sistemas RTM típicos, a unidade de injeção adaptativa é equipada com uma caixa de sensor que permite que os seguintes dados sejam medidos e registrados in situ:
- Temperatura
- Pressão
- Viscosidade da resina
- Densidade de reticulação do sistema de resina
- Temperatura de transição vítrea (Tg).
Além de garantir a qualidade das peças moldadas, esses dados também podem ser usados para gerenciar e controlar o processo de injeção. Este sistema de injeção adaptativa Industry 4.0 está sendo desenvolvido para aerocompósitos e também estendido para outras indústrias, como automotiva.
Formação de cortina a quente
Nos artigos recentes da turnê, Sara Black e eu escrevemos sobre compósitos de alto desempenho em Israel, notamos que a maioria das empresas estava usando moldagem por cortinas a quente. Na verdade, no Elbit Cyclone, nosso guia turístico Jonathan Hulaty declarou:"Não sei como você faz esse tipo de produção de peças pré-impregnadas de alta taxa sem a formação de drapeado a quente", referindo-se a vigas e pilares para montagens do Boeing 787. Os formadores de cortinas a quente (HDF) também são considerados indispensáveis pela FBM e pelas Indústrias Aeroespaciais de Israel. A Fill fornece sistemas HDF há anos, incluindo várias unidades em produção na FACC. Eles são basicamente sistemas de formação de vácuo, equipados com infravermelho ou outros tipos de elementos de aquecimento e uma membrana de borracha de silicone reutilizável para aquecer e comprimir - desbastar - layups pré-impregnados em suas ferramentas antes da cura. HDF se torna uma peça chave na linha completa de produção de aerocompósitos mostrada abaixo.
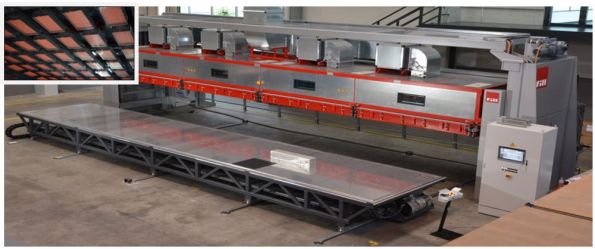
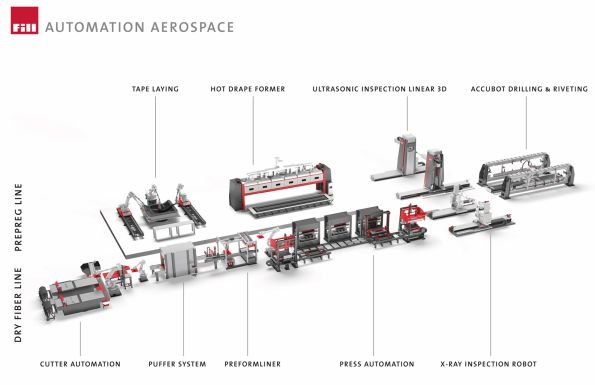
Formação de cortinas a quente tornou-se um facilitador importante para a produção de alto volume de aeroestruturas compostas pré-impregnadas e é automatizado pela Fill como parte de suas soluções de cadeia de processo completa. FONTE: Preencher Gesellschaft
Células de produção da indústria 4.0 para CFRP
No final de 2013, a Fill começou a desenvolver um sistema de produção para a fabricação de longarinas CFRP, usadas para endurecer as cápsulas dos flaps de pouso do Airbus A320, em colaboração com o fornecedor Tier. Após a instalação, esse sistema reduziu com sucesso o número de estações, melhorando o fluxo de produção e também facilitando o uso. Inclui:
- Armazenamento automático de ferramentas de modelagem
- estação HDF
- Estação de elevação prensa-viradeira onde os laminados são processados em longarinas.
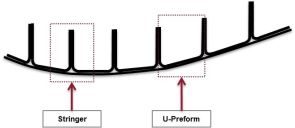
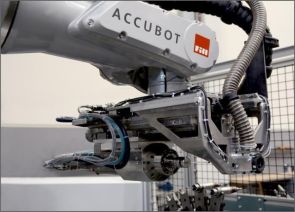
Preenchimento desenvolvido três gerações de células de produção automatizadas (direita) para longarinas de flap de trem de pouso feitas de prepreg (esquerda).
FONTE: Preencher Gesellschaft
Um sistema de segunda geração para produzir o mesmo tipo de peças foi comissionado em 2017. Onde o primeiro sistema se concentrava na otimização de estações individuais, este último sistema teve como objetivo minimizar as tarefas manuais e integrar toda a logística da ferramenta. Três áreas principais de desenvolvimento permitem que este sistema de segunda geração alcance alta reprodutibilidade e aumento significativo da produtividade:
- A recuperação manual e o armazenamento das ferramentas de conformação são substituídos por um retorno de ferramenta totalmente automático, reduzindo os tempos do processo logístico. Isso também reduziu a necessidade de espaço em mais de 50 por cento.
- A automação adicional de subprocessos reduziu o tempo improdutivo.
- Digitalização da indústria 4.0 de todos os registros e relatórios. O software desenvolvido pela Fill permite a visualização do processo em todos os momentos e o registro do histórico de cada componente ao longo da cadeia do processo. Os sensores detectam a disponibilidade de ferramentas e materiais para evitar gargalos e melhorar o reordenamento.
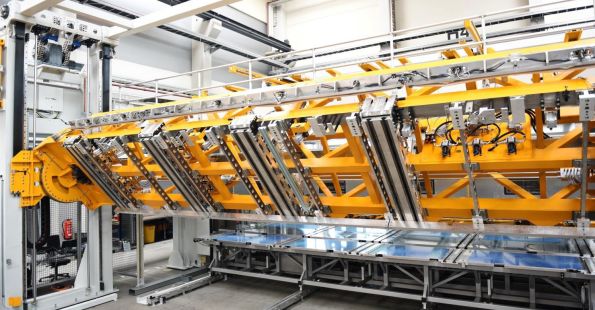
Press-turn - estação de levantamento usada em células de produção automatizadas para longarinas de trem de pouso A320 e A350.
FONTE: Preencher Gesellschaft
Fill agora está trabalhando em um sistema de produção de terceira geração para cápsulas de flap de pouso destinadas ao Airbus A350-900. Ele também compreende armazenamento de ferramentas, estação de formação de membrana (HDF), estação de levantamento de prensa e retorno automático de ferramenta, mas foi aprimorado com um sistema de transporte para ferramentas de autoclave, substituindo caminhões de transporte manual anteriores e tratores elétricos por veículos guiados automatizados (AGVs ) Fill já está trabalhando em sistemas futuros, procurando como melhorar ainda mais a colaboração entre homem e máquina.
Accubot
Mesmo antes de a indústria de compósitos começar a verbalizar sua necessidade futura de uma célula de trabalho multi-operação, a Fill já estava desenvolvendo os primeiros protótipos, o que chama de Accubot. A ideia era desenvolver um robô preciso usando um rastreador a laser para compensação espacial e também sistemas de medição externa direta. Este robô seria capaz de alternar funções com efetores finais, tornando-se não apenas uma célula de teste não destrutivo (NDT), mas também uma célula de usinagem. Os aplicativos Accubot incluem:
- Perfuração
- Rebitagem
- NDT - Ultrassom com um squirter
- NDT - Raio-X
- NDT - Tomografia computadorizada
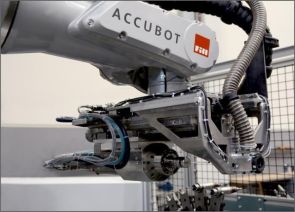
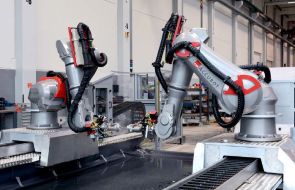
Accubot para perfuração (esquerda) e NDT usando varredura ultrassônica de alta velocidade (direita).
FONTE:Preencha Gesellschaft.
FlexHyJoin
Fill é membro do projeto Flexible Production Cell for Hybrid Joining (FlexHyJoin), financiado pela UE. Este programa de 3 anos visa desenvolver um processo piloto totalmente automatizado para a união de suportes / acessórios metálicos com compósitos termoplásticos em aplicações automotivas, combinando tecnologias de união a laser e união por indução. A Fill projetou e construiu a célula automatizada, incluindo software e integração de várias tecnologias.
A pesquisa e o desenvolvimento de Fill continuam. Ela entende que sistemas de produção inovadores e inteligentes são necessários para tornar a fabricação de peças compostas mais econômica e receptiva a volumes maiores. E tem o compromisso de desenvolver esses sistemas de acordo com a escala e as necessidades específicas de seus clientes.
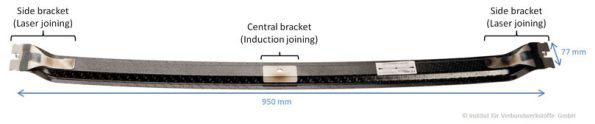
FONTE:FlexHyJoin.
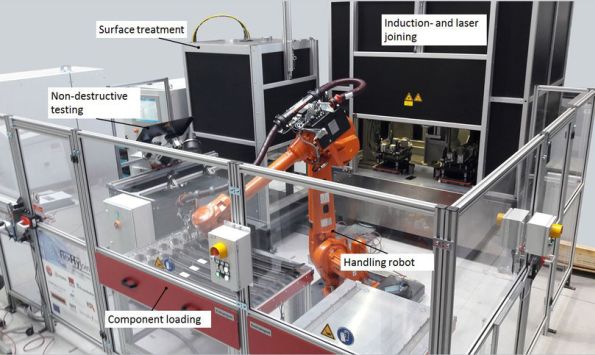
Resina
- Preencher Barragem
- Diretivas de pré-processador C#
- Python strftime()
- Python strptime()
- Suas peças mais fortes com impressão 3D de fibra de carbono - Preenchimento isotrópico Parte 1
- Introdução aos harmônicos:parte 1
- Sustentabilidade na fabricação - Parte 3
- O giro é opcional
- Inspeção automática de dados de tomografia computadorizada em linha de conectores eletrônicos
- Cilindricidade em GD&T