Entrevista com um especialista:Spencer Wright de pencerw.com e nTopology

Quase todos os envolvidos no mundo da manufatura já terão acessado o blog de Spencer Wright ou o boletim informativo de manufatura em algum momento. Spencer é um especialista de longa data em fluxos de trabalho para fabricação de aditivos de metal e chefe de pesquisas e parcerias na nTopology. Spencer teve a gentileza de se sentar com a RP Platform para discutir sua experiência em AM e manufatura convencional, seu trabalho atual projetando fluxos de trabalho otimizados e como ele vê o campo evoluindo em um futuro próximo.
Como você começou a se interessar pela impressão 3D?
Fiquei interessado em impressão de metal só porque parecia legal!
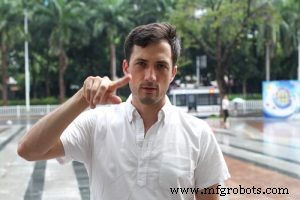
Minha formação é em manufatura tradicional. Eu sou um gerente de projeto, gerente de produto, um designer mecânico bastante decente ... Eu construí quadros de bicicletas personalizados por vários anos. Depois disso, trabalhei em uma oficina de prototipagem onde desenvolvíamos montagens eletromecânicas, então ganhei alguma experiência em projetos de sistemas embarcados.
Eu me mudei para Nova York em 2012 e estava dando um passo para trás e pensando no que eu queria me concentrar, enquanto continuava a trabalhar em coisas manufaturadas convencionalmente. Mas eu estava procurando por algo um pouco diferente. Na época, Makerbot e Shapeways eram realmente grandes no cenário de hardware de Nova York. Ambas são empresas realmente interessantes, mas tendo experiência em coisas mecânicas - coisas estruturais, funcionais - fiquei curioso e ouvi falar de algumas tecnologias diferentes de impressão de metal. Isso foi mais ou menos na mesma época em que a GE adquiriu a Morris, o que fez um grande sucesso aqui nos Estados Unidos. Fiz amizade com um monte de gente que trabalhava em uma empresa de estratégia chamada Undercurrent, que estava trabalhando muito com a GE na época, e acabei me juntando a eles em tempo integral.
Foi por meio desse trabalho que tomei conhecimento da fusão do leito de pó metálico. Havia muito marketing por aí sobre como a impressão 3D mudaria X, Y e Z, mas pensei "Vamos contextualizar aqui". Temos processos de fabricação extremamente estáveis. Temos extrusão, temos fundição, temos forja, temos usinagem ... São indústrias multibilionárias. Como a impressão em metal se compara a eles?
Comecei a pesquisar e descobri que essas impressoras custavam cerca de US $ 1 milhão, o que parecia muito dinheiro em comparação com uma usina CNC. Portanto, a pergunta era:“O que eles podem imprimir?” As plataformas de construção eram quase do tamanho de uma caixa de pão, então o que é uma peça de alto valor que cabe em uma caixa de pão e pode se beneficiar por ser leve ou ter alguns elementos de design interessantes?
A maior parte da indústria de impressão em metal hoje é composta de peças para aeroespacial, ou implantes médicos, ou óleo e gás, mas a resposta que eu encontrei foram as peças de bicicleta. Na verdade, é uma grande indústria, pois as pessoas pagarão muito dinheiro por algo que é um pouco mais leve ou se encaixa um pouco melhor. Se você pode imprimir uma parte que parece realmente única, isso é claramente futurista, as pessoas gostam disso.
Eu não sabia nada sobre tecnologia, mas sabia como projetar peças, sabia como adquirir peças e sabia como fazer perguntas. Usei essas três habilidades (e o fato de ter um blog e um boletim informativo, o que era um grande buraco no mercado) e continuei trabalhando nisso. Eu estava projetando e imprimindo peças, depois escrevendo sobre isso, e isso simplesmente se tornou uma coisa. Enquanto estava trabalhando nisso, comecei a receber cada vez mais ligações inesperadas de pessoas em empresas como a Siemens e a Philips, que são muito melhores nessas coisas do que eu. Isso espalhou minha voz e me deu acesso às pessoas dessas empresas, para que eu pudesse fazer perguntas e descobrir o que elas estavam passando.
Naquela época, acabei procurando algo um pouco diferente na minha carreira. Decidi focar em tempo integral em fluxos de trabalho de fabricação e design, então agora trabalho na nTopology, que faz software de design para impressão 3D industrial. A maior parte do que faço é descobrir como nosso software se encaixa no resto da cadeia de ferramentas. Como rastreamos os fluxos de trabalho de nossos clientes ao longo de todo o ciclo e tornamos essa experiência melhor?
Parece que sua experiência na fabricação tradicional significa que você está abordando a impressão 3D de uma forma muito mais orgânica do que muitas pessoas:começando com um problema e identificando a impressão 3D como a ferramenta certa para corrigi-lo. Você concorda com isso?
Sim, definitivamente. Observarei que, ao mesmo tempo, meu interesse é usar a tecnologia certa para o trabalho. Estou constantemente mexendo em projetos de design. Eu imprimo alguns deles, mas eu CNC alguns deles também. Todas as semanas recebo pessoas que me enviam e-mails dizendo que têm uma ideia de negócio e que querem imprimi-la em 3D. Minha pergunta é sempre “Por que você quer imprimir?”
Esta é realmente uma coisa única sobre a impressão hoje, e acho que a imprensa de tecnologia talvez não tenha feito um ótimo trabalho em estabelecer por que alguém iria querer uma peça impressa. Existem muitas histórias por aí dizendo "Vamos imprimir o X e será incrível", mas acho que a imprensa não tem sido boa em questionar como isso seria benéfico para alguém. Quando estou procurando algo, não me importo se foi impresso. Os consumidores não se importam se as coisas são impressas e as empresas certamente não se importam. O que os preocupa é se este produto tem um desempenho melhor, custa menos ou está mais disponível.
O resultado final é que, para a grande maioria das peças, imprimir não é uma boa solução. Para algo que precisa ser mais leve, sim, pois é possível incorporar passagens internas e simplificar a montagem. Esses são benefícios reais. Para mim, tem sido descobrir essas aplicações e as heurísticas que podemos usar para olhar para uma indústria e descobrir se ela será uma boa aposta para impressão.
Meu conselho para as pessoas é:não tente forçar sua aplicação na impressão. Existem coisas realmente boas para imprimir e devemos nos concentrar nelas.
Quais seriam alguns bons exemplos disso recentemente?
Trabalhamos em algumas indústrias primárias. Em todas essas diferentes indústrias, estamos projetando estruturas treliçadas [leves] que têm as propriedades mecânicas exatas que nossos clientes desejam.
O maior deles é aeroespacial - foguetes e espaçonaves - onde o ambiente regulatório é muito complicado. Existem questões significativas sobre como você inspeciona as peças e garante que elas ainda estão boas após um número X de horas de vôo, por exemplo. A indústria aeroespacial tem os requisitos mais rigorosos, portanto, se você puder atendê-los, normalmente poderá atender às necessidades de outras indústrias!
Também temos uma grande presença em implantes médicos, onde as necessidades de design são muito diferentes, mas ainda muito regulamentadas. Também trabalhamos com muitas empresas de tecnologia de consumo, que estão fabricando peças que absorvem energia de uma maneira específica. As empresas de calçados são muito públicas sobre isso, mas há outras empresas de roupas esportivas que procuram imprimir itens como estofamento. Quando o corpo de uma pessoa colide com algo, você deseja absorver essa energia para que ela não seja transferida para os ossos. A espuma é boa nisso, mas você pode usar estruturas diferentes para dissipar a energia para fora, em vez de através da almofada.
Você acha que existe uma grande curva de aprendizado em termos de fluxos de trabalho das empresas, especialmente quando várias plataformas de software estão envolvidas?
Isso é muito complicado. Há momentos em que me vejo executando $ 50.000 em software de engenharia no meu computador ao mesmo tempo! A boa notícia é que não importa no que você esteja trabalhando, sejam peças de foguete ou sapatas, o calibre do software que vemos é normalmente muito semelhante. Há meia dúzia de programas CAD que nossos clientes normalmente usam, depois há um punhado de pacotes de análise e plataformas de software de manufatura diferentes.
Embora existam diferenças, os requisitos gerais são muito semelhantes. Essas são empresas de engenharia sérias com necessidades sérias, então você tem que manter a rastreabilidade, atender ao ambiente regulatório, ter documentação e ser capaz de rastrear os resultados da análise, o que pode ser complicado.
A realidade é que, embora o mundo do software de engenharia seja relativamente maduro, o software de manufatura não é. Os pacotes que as empresas usam (principalmente Autodesk Netfabb e Materialize Magics) não existem há muito tempo, no grande esquema das coisas. Todos os anos, eles são atualizados com diferenças bastante significativas. Além disso, você tem formatos de arquivo que mudam constantemente, então pode ficar complicado.
O que você vê como a resposta em termos de simplificar tudo isso?
No momento, nosso foco é tornar esse processo o mais suave possível. Em última análise, a área em que podemos afetar isso mais é em nosso software, o Element. Podemos tornar essa experiência ótima. Dentro desta indústria, isso é difícil. Quais são os formatos de arquivo que você usará para ir do CAD ao Element e ao processador de construção? Agora é STL, que é uma bagunça de formato de arquivo.
Estruturas reticuladas podem ter milhões de vigas. Quando você usa STL, está descrevendo a superfície dessa estrutura com triângulos. Para cada viga, você terá um mínimo de talvez dez triângulos, embora na maioria dos casos consideremos melhor usar pelo menos 50 triângulos. Com um milhão de feixes, isso significa tamanhos de arquivo que são simplesmente insanos.
Não é prático descrever a geometria dessa forma e, portanto, dentro do Element, não usamos geometria tesselada de forma alguma. Usamos uma estrutura de grafo, então cada viga vai de um nó para outro. Cada nó tem uma localização X, Y e Z e um raio atribuído a ele. Os feixes então conectam esses nós. Com uma quantidade relativamente pequena de informações, podemos mostrar projetos que possuem muitos, muitos feixes. Criamos designs dentro de nosso software dessa forma e, em seguida, usamos uma especificação de arquivo de código aberto que permite exportá-los e usar seus próprios divisores e ferramentas de orientação.
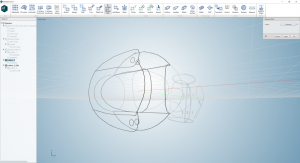
Estamos trabalhando para integrar isso ao padrão de arquivo 3MF. O objetivo é ter uma apresentação de arquivos muito mais simples para comunicar reticulados. No mínimo, isso significa que se você tiver que enviar um arquivo por e-mail, não deverá esperar 20 minutos para que ele seja carregado. A transferência de arquivos é mais fácil e a renderização é muito mais fácil, pois a geometria simplificada significa que sua CPU não está trabalhando tão duro. Podemos cortar essa representação muito bem também. Também podemos importar isso diretamente para o seu software FEA, para que possamos executar a análise do feixe - que é muito mais fácil do que usar elementos sólidos.
Como você vê a aceitação desse novo formato de arquivo?
Honestamente, não estou preocupado com isso. Já vimos ajustes e inícios em formatos de arquivo antes, mas para nós, há uma vantagem tão clara nesse formato que suspeito que ele mudará muito rapidamente. A maioria dos formatos de arquivo de impressão ainda usa triângulos, o que significa que a representação geométrica existe dentro do mesmo paradigma. 3MF também tem geometria triangulada (é um formato melhor por uma série de outros motivos), mas estamos adicionando uma representação completamente diferente em cima disso, para que possamos representar a mesma parte com um arquivo muito menor. Eu suspeito que os benefícios disso superarão em muito qualquer dificuldade.
Você vê a personalização para as necessidades específicas dos clientes como um fator-chave no software de sucesso para AM?
Sim e não. Somos uma empresa de produtos. Vendemos um produto que construímos para os usuários mais exigentes e procuramos fazer a melhor versão possível disso. Ter uma abordagem consistente dos problemas torna a experiência consideravelmente melhor. Para as aplicações CAD mais marginais, o que geralmente acontece é um cliente dizer “Amamos os recursos, mas realmente gostaríamos que houvesse menus de contexto em todos os lugares”. A empresa de CAD realmente quer a venda, então eles fornecem os menus de contexto. Em alguns meses, você obtém menus de contexto em todos os lugares, eles funcionam bem e obtêm uma grande venda.
Em um ano, alguém chega e diz "Nós amamos o seu software, mas realmente queremos um sistema de pasta de comando melhor, já que os menus de contexto não funcionam realmente para nossos engenheiros". A empresa de CAD gasta seis meses nisso, e então você tem duas maneiras de fazer exatamente a mesma coisa. O que você acaba com é um software esquizofrênico.
Temos a tendência de preferir uma única interação. Qualquer novo recurso que apresentarmos será tratado da mesma maneira e será consistente em todo o fluxo de trabalho. Ouvimos o que nossos clientes realmente precisam e criamos algo que se encaixa em nossa estrutura de gerenciamento de interações, mas também se ajusta a essas necessidades.
Mas, além disso, a necessidade de flexibilidade nos fluxos de trabalho é definitivamente um ponto. Com o novo formato de arquivo, nós o escrevemos de uma forma que seja muito fácil para qualquer pessoa pegá-lo, manipulá-lo e entender o que está acontecendo.
Que tal otimizar os fluxos de trabalho de AM? Que maneiras você encontrou de tornar os processos gerais mais rígidos e reduzir qualquer desconexão?
Isso é difícil. Em última análise, quando você olha para nossos usuários aeroespaciais, você está constantemente oscilando entre coisas diferentes. Mesmo com uma peça relativamente simples, você acaba com um número de peça, depois a versão 2, a versão 3 etc. e meio que explode. Uma coisa que fizemos foi permitir várias versões do mesmo design em um único arquivo. Você pode distribuir em direções diferentes, mas manter tudo dentro do mesmo arquivo real, o que ajuda um pouco.
Em última análise, no entanto, a interoperabilidade é muito mais importante do que a simplificação. Pensamos muito em fazer uma versão mais simples do Element como um plug-in para outro software CAD, mas então estamos trabalhando com o kernel de geometria e interface do usuário de outra pessoa. Ajustar essas coisas é mais difícil do que fazer em seu próprio software. Além disso, você escolhe o software CAD mais popular e constrói para ele? Você escolhe aquele que seus clientes usam?
Portanto, por enquanto, optamos por manter nossa flexibilidade. Você importa para o nosso software, mas vamos tornar esse processo o mais fácil possível. Sabemos que se mantivermos a maior parte do trabalho em nosso software, podemos garantir uma boa experiência do usuário.
Em termos gerais, como você vê tudo isso evoluindo?
Estou animado para a impressão de metal se tornar mais madura. Os humanos têm um século de corte de metal sob seus cintos. Temos feito muito isso e somos bons nisso. É repetível e confiável, então não preciso saber em que máquina uma peça é feita. Com a impressão em metal, isso é completamente diferente. Não é tão repetível, então se eu for a vários fabricantes diferentes com o mesmo arquivo, eles o construirão de maneiras diferentes e obteremos um resultado diferente. Ouço gente falando que precisamos de mais materiais ou velocidade, e essas coisas são importantes, mas o que eu quero mesmo é maturidade. É por isso que estou realmente animado.
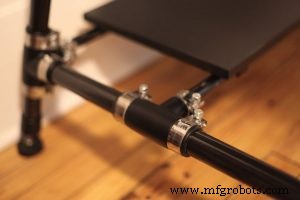
Temos esse grande esforço para criar restrições de design em nosso software. Se você projeta algo no Photoshop, ele possui uma paleta de cores que pode ser aplicada ao seu projeto. Eles não permitem que você escolha cores como ultravioleta, porque você não pode vê-los, então não há por que projetar algo assim! Com o software CAD, é fácil projetar coisas que não podem ser fabricadas. Nosso foco principal é ajudar nossos usuários a entender o que é e o que não é fabricável e construir essa inteligência no software, para que eles recebam feedback em tempo real sobre como seu design será impresso.
É muito difícil para nós fazer isso em um mundo onde não apenas as máquinas imprimem peças de maneira diferente, mas os fabricantes não publicam especificações sobre o que pode ser impresso. O que eu realmente quero é que os fabricantes de máquinas publiquem APIs que forneçam feedback sobre a capacidade de impressão e apontem onde estão as áreas problemáticas.
Para encerrar, o que você vê como a ‘próxima grande coisa’ nos próximos cinco anos?
Não é uma resposta sexy, mas estou procurando um processo mais confiável, mais repetível e mais estável. Ou, pelo menos, quero um fluxo onde as pessoas possam fazer coisas malucas, mas que ofereça tempos de construção confiáveis para fornecer uma base sólida para isso.
Acho que é bom ver mais fabricantes de máquinas desenvolvendo mais integração com fabricantes de peças e abrindo seus próprios escritórios de serviço. Eles aprenderão mais sobre a impressão de peças e, com sorte, alimentarão essa inteligência em suas máquinas. Ao mesmo tempo, estamos vendo os fabricantes de máquinas ficarem mais intimamente ligados ao software.
Existe uma coisa chamada Lei de Conway que diz que as empresas tendem a construir sistemas que são uma cópia de sua própria estrutura organizacional. Por exemplo, se você tem uma peça com uma placa de circuito impresso conectada à moldagem por injeção e a equipe de engenharia mecânica está em um prédio diferente da equipe de engenharia de sistemas embarcados, então o PCB vai cair da peça moldada por injeção .
O corolário razoável é que, se você deseja um fluxo de trabalho de ponta a ponta que seja contínuo, é necessário integrar essas equipes mais estreitamente. Faça-os trabalhar no mesmo prédio e esbarrar uns nos outros no bebedouro! Ter mais empresas reunindo essas funções diferentes é algo que estou muito interessado em ver.
www.pencerw.com
impressao 3D
- Entrevista com um especialista:Professor Neil Hopkinson, Diretor de Impressão 3D da Xaar
- Entrevista com um especialista:Philip Cotton, fundador do 3Dfilemarket.com
- Entrevista com um especialista:Dr. Alvaro Goyanes da FabRx
- Entrevista com um especialista:Dr. Bastian Rapp da NeptunLab
- Entrevista com um especialista:Ibraheem Khadar de Markforged
- Gabaritos e acessórios:6 maneiras de melhorar a eficiência da produção com impressão 3D
- Entrevista com especialista:Duncan McCallum, CEO da Digital Alloys, sobre a impressão Joule e o futuro da impressão 3D em metal
- Entrevista com especialista:Nanoe CEO Guillaume de Calan sobre o futuro da impressão 3D em cerâmica
- Entrevista com especialista:Ultimaker Presidente John Kawola sobre o futuro da impressão 3D
- Motorsports, Performance Racing e impressão 3D:uma entrevista com Revannth Murugesan da Carbon Performance