Impressão 3D em metal:um guia definitivo (2021)
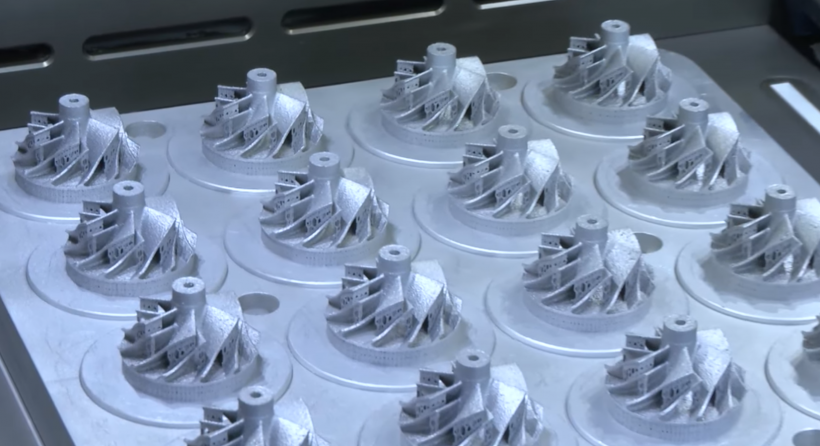
A impressão 3D em metal está avançando rapidamente em todas as frentes :a tecnologia está cada vez mais avançada, as velocidades de impressão aumentam e existe uma gama maior de materiais industriais do que nunca. Esses avanços estão abrindo novas aplicações interessantes para a tecnologia.
No entanto, familiarizar-se com as tecnologias disponíveis e integrá-las aos fluxos de trabalho existentes pode ser um desafio para muitas empresas.
Este guia tem como objetivo ajudá-lo a compreender melhor a impressão 3D em metal, desde as tecnologias que estão atualmente disponíveis até os benefícios, limitações e principais aplicações da tecnologia.
Impressão 3D em metal:as tecnologias
Existem várias tecnologias de impressão 3D em metal disponíveis atualmente no mercado. Embora cada um tenha seus benefícios e limitações, todos são unidos pelo princípio fundamental de impressão 3D de criar peças de metal camada por camada.
As tecnologias de impressão 3D de metal comumente usadas incluem:
- Fusão de Cama de Pó
- Deposição de energia direta
- Jateamento de aglutinante de metal
- Laminação de folha ultrassônica
Tecnologias de fusão em cama de pó

De todas as tecnologias de impressão 3D de metal, o metal Powder Bed Fusion é talvez o mais estabelecido.
Com as tecnologias de fusão de leito de pó, camadas de metal em pó são uniformemente distribuídas na plataforma de construção de uma máquina e seletivamente fundidas por uma fonte de energia - um laser ou um feixe de elétrons.
Existem dois processos principais de impressão 3D de metal que se enquadram na categoria Powder Bed Fusion:
- Fusão seletiva a laser (SLM) / Sinterização direta a laser de metal (DMLS)
- Derretimento por feixe de elétrons (EBM)
Derretimento seletivo a laser e sinterização direta a laser de metal
SLM e DMLS são as tecnologias de impressão 3D de metal mais dominantes, com DMLS tendo a maior base instalada em todo o mundo, de acordo com um relatório da IDTechEx Research.
Com SLM e DMLS, um poderoso laser de ajuste fino é aplicado seletivamente a uma camada de pó metálico. Desta forma, as partículas de metal são fundidas para criar uma peça.
Um requisito importante para ambas as tecnologias é uma câmara de construção fechada cheia de gás inerte, como o argônio. Isso evita a contaminação do pó metálico com oxigênio e ajuda a manter a temperatura correta durante o processo de impressão.
Derretimento do feixe de elétrons
Outro processo de impressão 3D na família Powder Bed Fusion é o Electron Beam Melting (EBM). EBM opera de forma semelhante ao SLM em que os pós de metal também são fundidos para criar uma peça de metal totalmente densa.
Para evitar a contaminação e oxidação do pó, o processo EBM ocorre em um ambiente de vácuo.
A principal diferença entre as tecnologias SLM / DMLS e EBM é a fonte de energia:em vez de um laser, os sistemas EBM usam um feixe de elétrons de alta potência como fonte de calor para derreter camadas de pó metálico.
EBM também tende a produzir peças de metal com um nível inferior de precisão quando comparado a SLM e DMLS. Isso ocorre porque a espessura da camada no processo SLM é normalmente mais fina (entre 20 e 100 mícrons) do que no EBM (entre 50 e 200 mícrons), resultando em impressões mais precisas.
Uma vez que um feixe de elétrons é normalmente mais poderoso do que um laser, EBM é frequentemente usado com superligas de metal de alta temperatura para criar peças para aplicações altamente exigentes, como motores a jato e turbinas a gás. As peças de metal produzidas são altamente densas e, portanto, ideais para a indústria aeroespacial.
O alto custo dos sistemas EBM é algo a se considerar para empresas que buscam investir nessa tecnologia. Além disso, como a tecnologia depende de cargas elétricas, o EBM só pode ser usado com metais condutores, como titânio e ligas de cromo-cobalto.
Seja SLM / DMLS ou EBM, todas as peças de metal produzidas com tecnologias de fusão de leito de pó exigirão alguma forma de pós-processamento. O pós-processamento é necessário, não apenas para melhorar a estética da peça, mas também para melhorar suas propriedades mecânicas e atender aos parâmetros de projeto exatos, especialmente para aplicações exigentes.
Deposição de energia direta
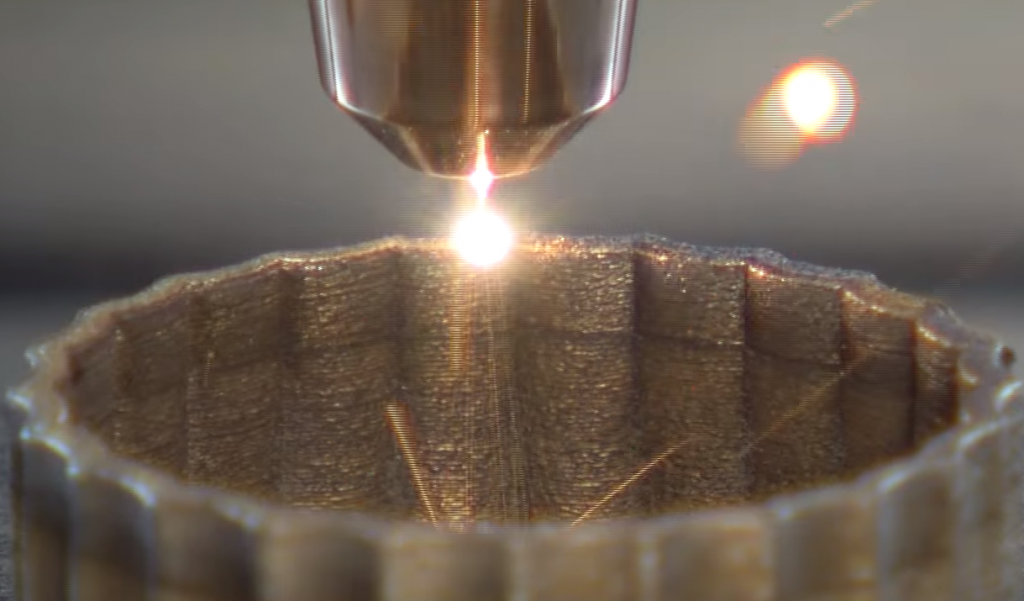
[ Imagem cortesia de Hybrid Manufacturing Technologies ]
A Deposição de Energia Direta (DED) funciona derretendo o material metálico com um laser ou feixe de elétrons à medida que é depositado por meio de um bico na plataforma de construção. Normalmente, as máquinas DED têm altas taxas de deposição de material e podem trabalhar com materiais metálicos na forma de pó ou arame, criando peças altamente densas com formatos próximos da rede.
Em contraste com os processos de fusão de leito de pó, que normalmente produzem componentes menores, mas altamente precisos, alguns métodos DED proprietários podem produzir peças de metal maiores.
Um exemplo é a tecnologia proprietária de Electron Beam Additive Manufacturing (EBAM) da empresa norte-americana Sciaky, que se diz ser capaz de produzir peças com mais de 6 metros de comprimento.
A tecnologia DED é adequada para reparar peças danificadas, como lâminas de turbinas e inserções de ferramentas de moldagem por injeção, que seriam difíceis ou impossíveis de reparar usando métodos de fabricação tradicionais.
Jateamento de ligantes metálicos
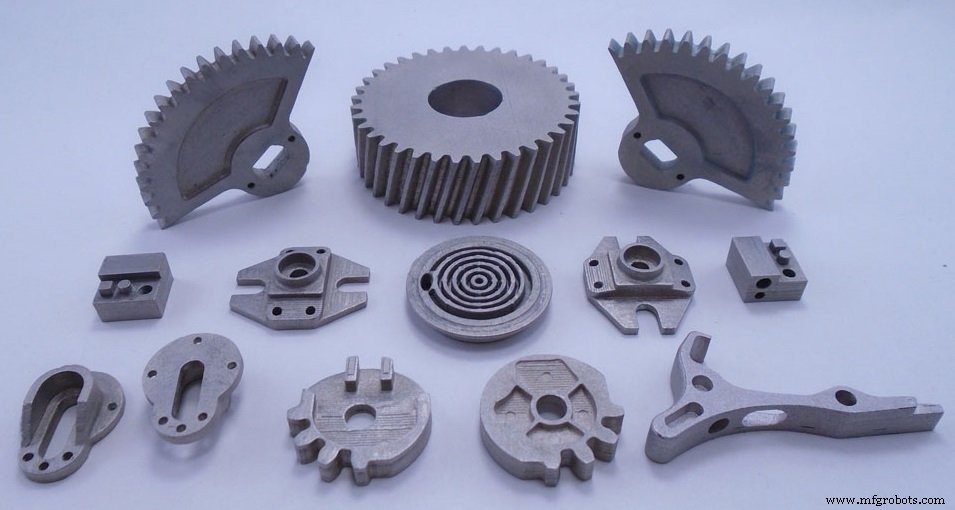
O jato de metal ligante é uma das tecnologias de impressão 3D de metal mais econômicas disponíveis no mercado.
Semelhante à impressão de tinta em papel, o jato de metal aglutinante envolve o uso de uma cabeça de impressão. Esta cabeça de impressão move-se sobre a plataforma de construção, depositando gotículas de um agente de ligação em camadas de pó metálico. Por meio desse processo, as partículas de metal são fundidas para criar uma peça.
Várias cabeças de impressão podem ser usadas para acelerar o processo de impressão.
As máquinas de injeção de encadernação de metal oferecem velocidades de impressão mais rápidas e um grande volume de impressão. Eles também tendem a ser significativamente mais baratos do que os sistemas de leito de pó.
No entanto, devido à natureza do processo de impressão, as peças produzidas com jato de metal aglutinante têm propriedades mecânicas limitadas:são altamente porosas devido à queima do aglutinante durante o processo de impressão.
Como resultado, as peças exigirão um pós-processamento significativo antes do uso final. Essas etapas incluem cura, para endurecer a peça, sinterização e infiltração de bronze para reduzir a porosidade e aumentar a resistência.
Laminação de folha ultrassônica
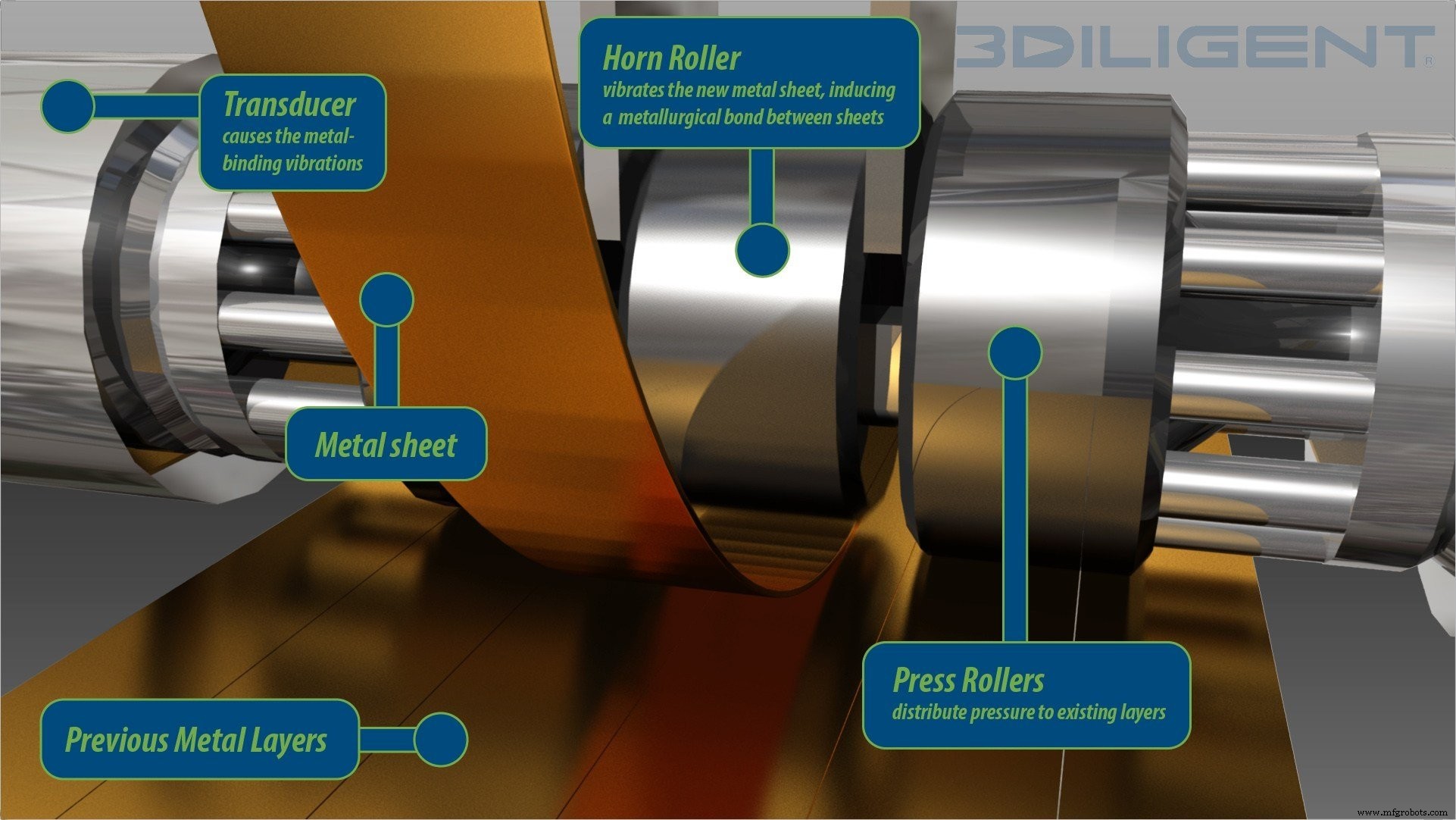
Ultrasonic Sheet Lamination é um processo de fabricação de aditivos de metal híbrido de baixa temperatura.
A tecnologia funciona soldando folhas de metal finas com vibrações ultrassônicas sob pressão. Assim que o processo de impressão for concluído, a fresagem CNC é aplicada para remover o excesso de material e finalizar a peça.
Por ser um processo de baixa temperatura, a laminação por ultra-som não derrete o material metálico. O processo também é capaz de fundir tipos de metais diferentes.
As principais vantagens dessa técnica são seu baixo custo, alta velocidade de impressão e a capacidade de criar peças com componentes eletrônicos integrados e sensores de uma variedade de metais.
Novos processos de impressão 3D de metal
Com a rápida evolução da impressão 3D em metal, os fabricantes de hardware procuram continuamente desenvolver novos processos. Abaixo, descrevemos algumas tecnologias de impressão 3D de metal recentemente desenvolvidas que têm o potencial de revolucionar a impressão 3D de metal, tanto em termos de velocidade quanto de custo.
Impressão 3D de metal baseada em extrusão
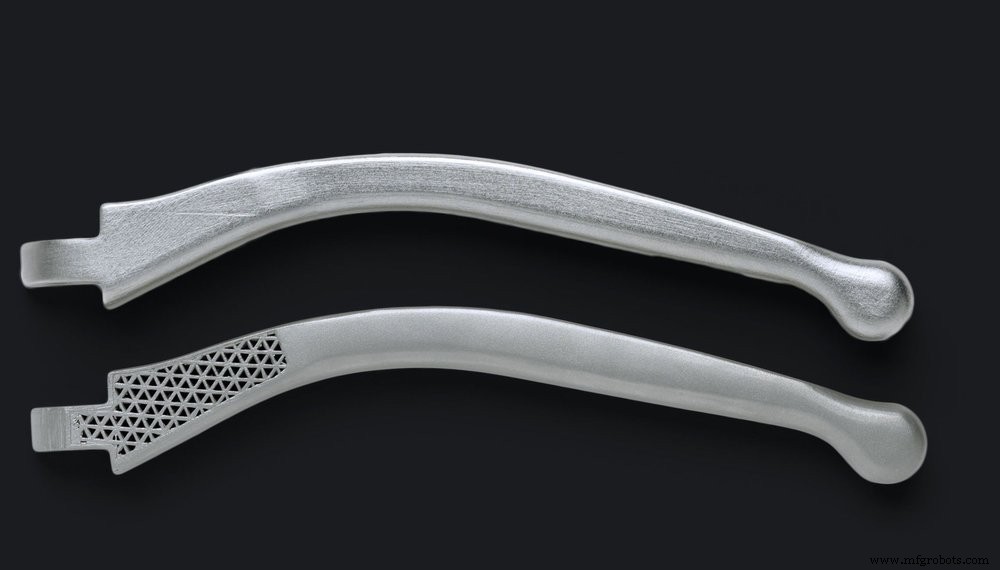
Produzir peças aditivamente por meio da extrusão de filamentos de metal é uma abordagem relativamente nova.
As duas empresas mais proeminentes que trabalham nesta área são Markforged e Desktop Metal. Ambas as empresas apresentaram pela primeira vez seus sistemas de impressão 3D de metal (Metal X da Markforged e Desktop Metal’s Studio System) em 2017.
A impressão 3D de metal baseada em extrusão funciona de maneira semelhante ao Fused Deposition Modeling (FDM), em que um filamento é aquecido e extrudado através de um bico, criando uma peça camada por camada.
No entanto, ao contrário dos filamentos de plástico usados em FDM, a extrusão de metal usa filamentos feitos de pós de metal ou pellets envoltos em aglutinantes de plástico.
Uma vez que uma peça foi impressa, ela permanece em um "estado verde" e precisará passar por etapas adicionais de pós-processamento:descolagem para queimar o plástico restante e sinterização para fundir as partículas de metal.
A impressão 3D de metal baseada em extrusão é um dos processos de fabricação de aditivos de metal mais acessíveis. Isso ocorre em parte porque ele usa materiais de moldagem por injeção de metal (MIM), que são significativamente mais baratos do que os pós de metal usados em processos de leito de pó.
Jateamento de material
Material Jetting é um processo de impressão a jato de tinta no qual as cabeças de impressão são usadas para depositar material fotorreativo na forma líquida em uma plataforma de construção, camada por camada.
Material Jetting tem sido normalmente usado como uma tecnologia de prototipagem para criar modelos de plástico totalmente coloridos de alta precisão.
No entanto, uma empresa reconheceu o potencial da tecnologia para impressão 3D em metal:a empresa israelense XJet desenvolveu uma nova técnica de jato de tinta para metais que pode atingir um alto nível de detalhe e acabamento.
A tecnologia NanoParticle Jetting ™ (NPJ) da XJet usa cabeças de impressão para depositar tintas metálicas suspensas em uma formulação líquida. O processo ocorre em uma câmara aquecida.
À medida que as tintas metálicas são depositadas, elas são depositadas em uma bandeja de construção quente, evaporando a formulação líquida para deixar apenas as partículas de metal. As partículas possuem um pequeno revestimento de agente de ligação, permitindo que elas se liguem umas às outras em todos os três eixos.
Depois de concluída a impressão, a peça é levada para um forno, onde passa por um processo de sinterização. Essa tecnologia pode ser usada tanto para prototipagem funcional quanto para fabricação sob demanda de componentes de metal de pequeno e médio porte.
Jato de metal (HP)
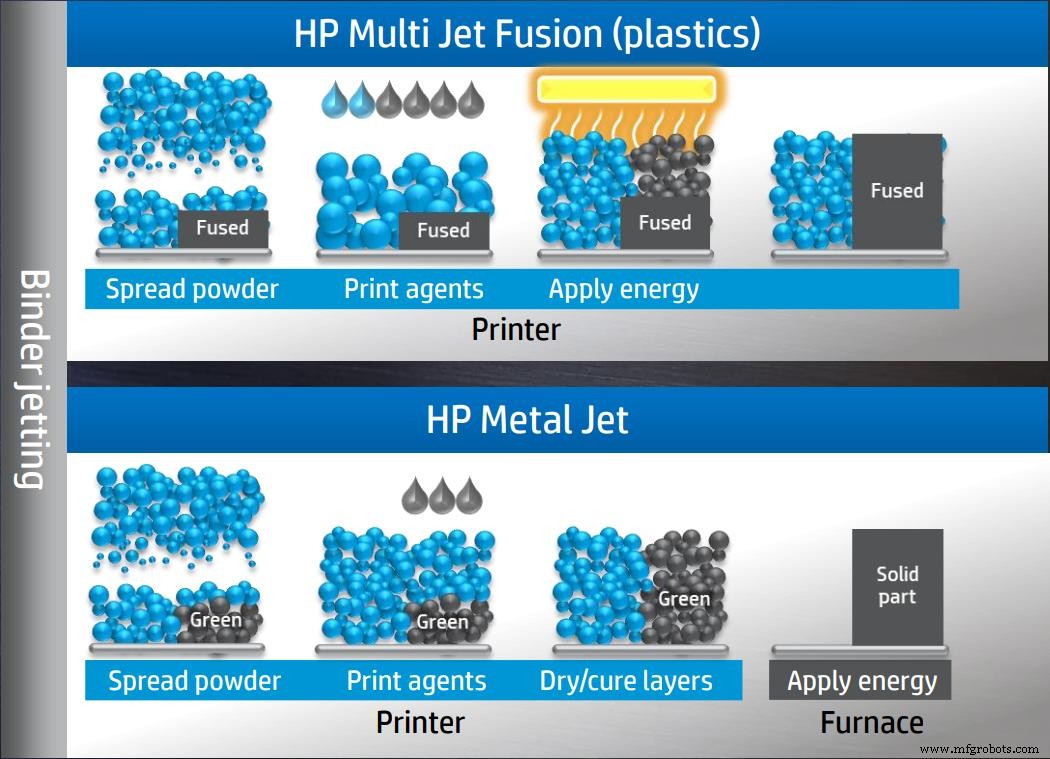
A HP causou sensação ao entrar no mercado de impressão 3D em 2016, com o lançamento de seu sistema de polímero Multi Jet Fusion. Em 2018, a empresa deu um passo adiante em sua tecnologia de binder jetting, anunciando seu novo sistema de impressão 3D de metal:Metal Jet.
O sistema Metal Jet é baseado no processo de binder jetting da HP, que foi aprimorado para permitir uma impressão mais rápida e barata.
Embora funcione de forma semelhante a outras máquinas de jato de aglutinante, o sistema usa um aglutinante proprietário desenvolvido com a ajuda da tecnologia de tinta látex da HP. Diz-se que essa nova formulação de aglutinante torna a sinterização de uma peça mais rápida, econômica e muito mais simples.
Além disso, a Metal Jet usa pós de moldagem por injeção de metal (MIM) e é capaz de produzir peças isotrópicas que atendem aos padrões ASTM.
Uma das principais características da tecnologia é o aumento da quantidade de cabeçotes de impressão, o que torna o Metal Jet até 50 vezes mais produtivo do que as máquinas de sinterização a laser e aglutinantes comparáveis do mercado hoje.
Impressão Joule (ligas digitais)

Embora seu lançamento comercial não seja até 2020, a tecnologia de impressão Joule patenteada da Digital Alloys é outro processo de impressão 3D de metal que vale a pena mencionar aqui.
A impressão Joule é uma tecnologia de alta velocidade que usa fio de metal em vez de pó.
O fio de metal é alimentado em um sistema de movimento de precisão com uma alimentação de fio de precisão. Uma vez que o fio é posicionado, a corrente é passada através do fio e, subsequentemente, na plataforma de impressão e na própria peça. O fio de metal é derretido pela corrente conforme a cabeça de impressão se move, com as gotas de metal fundidas para formar a parte final.
Diz-se que a tecnologia de impressão Joule permite a produção de peças de formato quase final e pode ser usada para ferramentas e outras aplicações nas indústrias automotiva, aeroespacial e de bens de consumo.
MELD (Fabricação MELD)
A MELD Manufacturing Corporation desenvolveu um novo processo de impressão 3D de metal em estado sólido para fabricar peças de metal. O fato de ser de estado sólido significa que o processo não requer a fusão do material metálico durante o processo de impressão.
Em vez disso, o processo envolve a passagem do material metálico por uma ferramenta rotativa oca, onde a extrema pressão e fricção atuam para deformar o material que está sendo adicionado, bem como o material que já foi depositado.
O processo garante que as peças produzidas tenham alta resistência e propriedades mecânicas, como resistência à corrosão.
As peças impressas com a tecnologia MELD são totalmente densas e não requerem tratamento térmico subsequente. Além disso, a tecnologia não é apenas adequada para criar peças, mas também para revestir e reparar componentes existentes.
Fazendo o caso de negócios para impressão 3D em metal
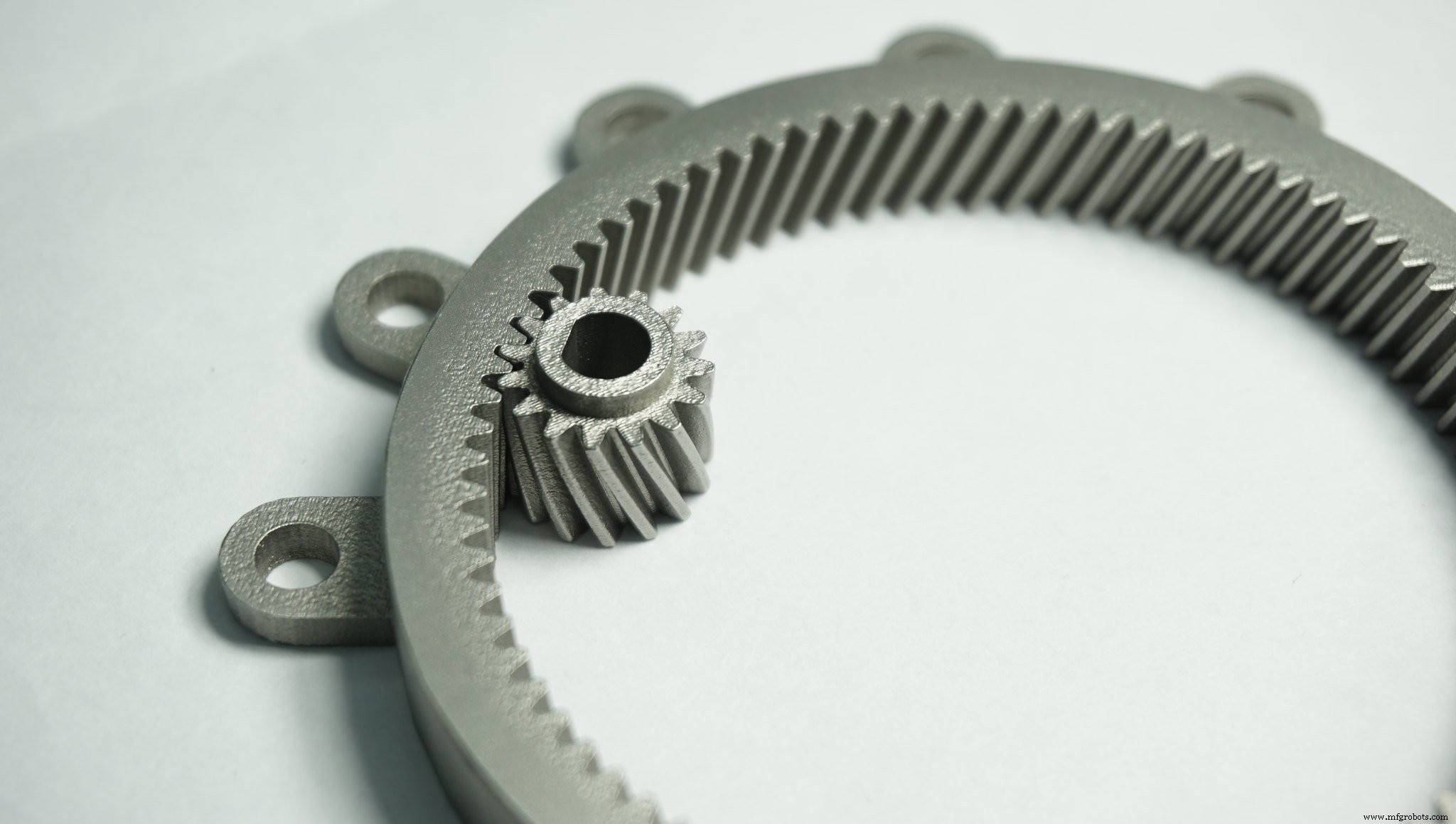
A impressão 3D em metal tem o potencial de transformar a maneira como as peças são fabricadas, fornecendo um nível de complexidade e personalização que não é possível com os processos de manufatura tradicionais.
Ao decidir se deseja investir em impressão 3D de metal, é importante avaliar se sua empresa pode se beneficiar com a tecnologia. Abaixo, descrevemos alguns dos principais benefícios da impressão 3D de metal.
Economize tempo e reduza custos
Em primeiro lugar, a impressão 3D elimina a necessidade de ferramentas e moldes caros, permitindo que os fabricantes eliminem custos de configuração caros e demorados. Em segundo lugar, a capacidade de ir do design à produção pode reduzir significativamente os prazos de entrega de semanas ou meses para dias.
Finalmente, a capacidade de consolidar montagens de peças com impressão 3D pode ajudar a economizar tempo e custo de mão de obra significativamente.
Desperdício de menos material
Os métodos tradicionais de manufatura subtrativa envolvem grande desperdício de material, com um estudo mostrando que o uso de fresadoras CNC para cortar material de blocos de metal pode levar a desperdícios de material de até 95%.
Em comparação, os processos de impressão 3D de metal geram muito menos resíduos, pois o material é sinterizado ou derretido apenas quando necessário. Em alguns casos, pós metálicos não sinterizados podem até ser reutilizados.
Como resultado, o uso de material com impressão 3D é altamente eficiente, com taxas de refugo de material geralmente abaixo de 5 por cento.
Alcance maior inovação em design
A impressão 3D em metal pode ser usada para produzir geometrias complexas, ultrapassando os limites do que é possível com a manufatura. Esses projetos complexos podem ser produzidos de forma mais econômica do que com os processos tradicionais.
Juntamente com ferramentas de design como otimização de topologia e design generativo, a impressão 3D pode ser usada para criar peças de metal leves com funcionalidade aprimorada e propriedades mecânicas.
Essas ferramentas de design de software podem, portanto, ajudar a desbloquear uma infinidade de possibilidades de design novas e inovadoras. Por exemplo, estruturas de rede podem ser fatoradas em um projeto para reduzir o peso de uma peça de metal e, portanto, melhorar o desempenho de um veículo ou aeronave.
Produção econômica de baixo volume
Com a impressão 3D, a produção de baixo volume torna-se economicamente viável.
Devido aos altos custos de ferramentas, os métodos de fabricação tradicionais podem ser extremamente caros de implementar para a produção de peças em baixos volumes.
Em contraste, a impressão 3D não requer ferramentas e, portanto, é uma opção mais econômica para produção de baixo volume. Um exemplo importante disso é o caso de peças personalizadas, em que os produtos podem precisar ser produzidos individualmente ou como parte de um pequeno lote.
A impressão 3D também pode ser usada para criar peças sob demanda. Por exemplo, as empresas podem ferramentas de impressão 3D e peças sobressalentes internamente conforme necessário - o que reduz a necessidade de estocar peças em um inventário físico e simplifica a logística e a cadeia de suprimentos geral.
Desafios da impressão 3D em metal
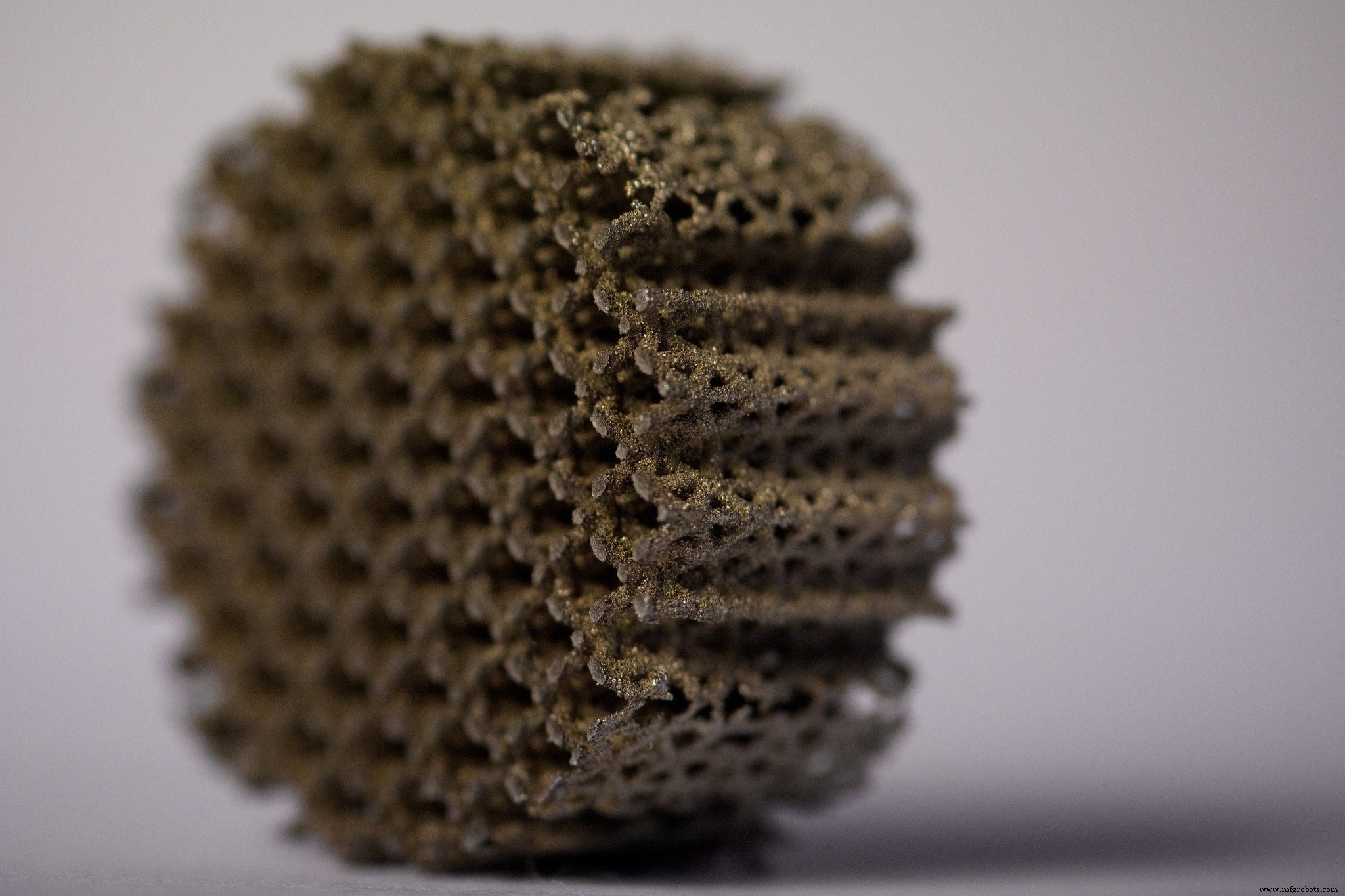
Embora os benefícios da impressão 3D em metal sejam claros, existem desafios para a implementação bem-sucedida da tecnologia. A seguir, cobrimos alguns dos principais desafios que o mercado de impressão 3D de metal enfrenta atualmente.
Custos elevados
Embora o preço das impressoras 3D tenha caído significativamente na última década, o custo dos sistemas AM de metal ainda continua sendo um dos principais desafios para as empresas que buscam investir em tecnologia.
Atualmente, uma impressora 3D de metal pode facilmente custar centenas de milhares de dólares e até mais de $ 1 milhão.
Ao mesmo tempo, os atuais materiais metálicos disponíveis no mercado são geralmente bastante limitados, com custos significativamente mais elevados do que os dos metais usados na fabricação de metais tradicional.
Dito isso, nos próximos anos, esperamos que os avanços na ciência dos materiais metálicos expandam as opções de metais imprimíveis em 3D e reduzam os custos.
Maior complexidade
Múltiplas variáveis envolvidas na impressão 3D de metal a tornam um processo muito mais complexo do que a impressão 3D de polímero. Atualmente, muitas empresas não possuem o conhecimento necessário para operar com sucesso impressoras 3D de metal internamente.
Uma maneira possível de começar a usar a tecnologia é por meio da colaboração com fornecedores de serviços de impressão 3D de metal. Os bureaus de serviço podem oferecer sua experiência na escolha da tecnologia e dos materiais AM de metal corretos.
Para empresas que buscam trazer a tecnologia AM internamente, desenvolver e implementar uma estratégia de AM será o primeiro passo fundamental nessa jornada.
Garantindo a qualidade das peças
A qualidade da peça e a repetibilidade do processo são as principais preocupações dos fabricantes. Quando se trata de impressão 3D de metal, há uma ampla gama de variáveis que podem afetar a qualidade de uma peça. Essas variáveis abrangem todo o fluxo de trabalho do AM, do design à preparação e pós-processamento da construção.
No entanto, o controle dessas variáveis para permitir peças de metal de alta qualidade que podem ser repetidas continua sendo um desafio.
Os materiais
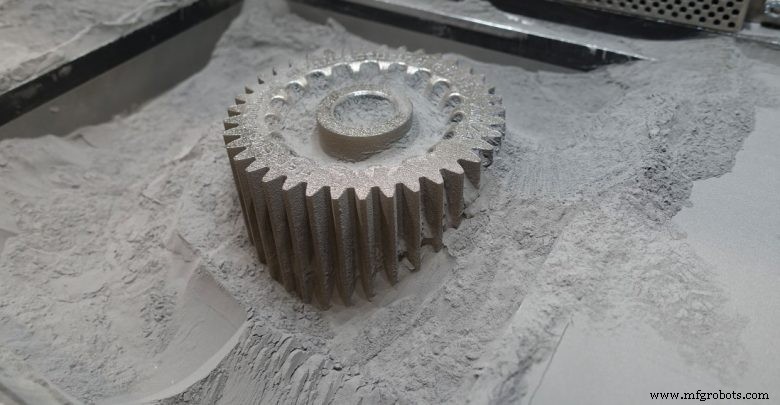
Os metais têm sido o segmento de crescimento mais rápido do mercado de materiais de impressão 3D desde 2012.
Os processos de impressão 3D de metal usam materiais metálicos de alta qualidade. Eles são normalmente produzidos na forma de pó e devem atender a certas características, como formato e tamanho das partículas e densidade do pó.
Em comparação com o processo de fabricação tradicional, a variedade de metais disponíveis para impressão em 3D permanece limitada.
Isso se deve ao fato de que materiais especializados adaptados ou produzidos para tecnologias de impressão 3D em metal podem levar anos para serem desenvolvidos.
No entanto, alguns processos como o DED podem usar metais originalmente desenvolvidos para processos tradicionais, por exemplo, na forma de fio.
Atualmente, os materiais mais comumente usados para impressão 3D de metal incluem metais leves como alumínio, titânio e aço inoxidável.
No entanto, o uso de metais refratários e ligas de cromo-cobalto também está se expandindo, em grande parte impulsionado por aplicações nas indústrias aeroespacial e de óleo e gás.
Na tabela abaixo, identificamos os materiais de impressão 3D de metal mais comuns e suas aplicações típicas.
(ligas AlSi10Mg, AlSi12, AlSi12Mg, Scalmalloy)
Comercialmente puro (Grau 1 e 2)
Liga de titânio Ti6Al4V (Grau 5)
Liga de titânio Ti 6AL-4V ELI (Grau 23)
Aplicação principal:O titânio é ideal para esportes motorizados, aviação e aplicações médicas / odontológicas. Aço inoxidável
(ligas 17-4PH e 316L)
Principais aplicações:aplicações de gerenciamento térmico (por exemplo, micro trocadores de calor), engenharia elétrica, inserções de ferramentas Aço maraging (aço ferramenta)
Principais aplicações:Ferramentas (núcleos e inserções de ferramentas de fundição e moldagem por injeção), protótipos funcionais Metais refratários (tântalo, nióbio e tungstênio)
Principais aplicações:Este grupo de metais é valioso para aplicações de alta tensão, como bicos, válvulas e manifolds de mísseis e propulsores de foguetes; implantes (tântalo) Metais preciosos (ouro, prata, platina)
Principais aplicações:Metais preciosos são usados para aplicações de nicho, como acessórios (joias e relógios), dentais (coroas, incrustações e onlays)
As máquinas
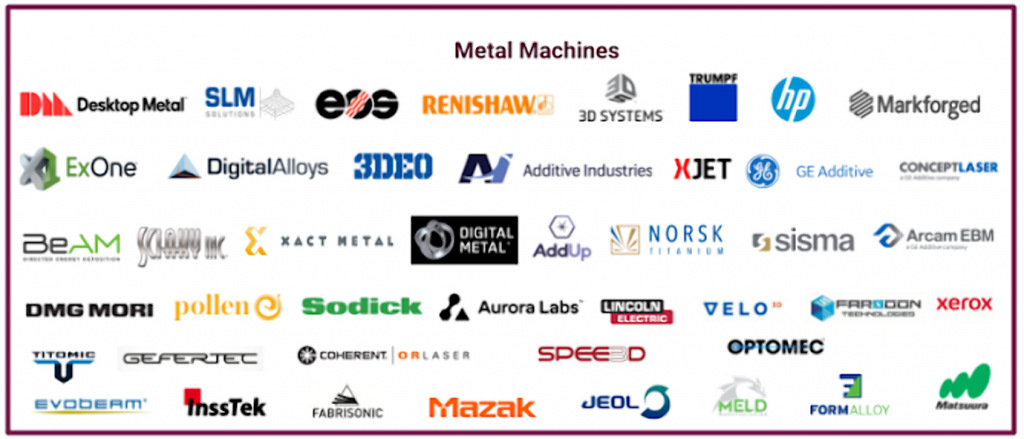
Com o aumento da impressão 3D de metal, o número de impressoras 3D de metal disponíveis no mercado está se expandindo.
De acordo com o Relatório Wohlers de 2018, as vendas de sistemas de metal AM cresceram 80% em 2017, com um aumento no número de fabricantes de sistemas de metal AM entrando no mercado.
Na tabela disponível para download, resumimos os principais fabricantes de impressoras 3D de metal, usando tecnologias de leito de pó, DED, Binder Jetting e impressão 3D de metal baseada em extrusão. Embora não seja uma lista completa, ela fornece uma visão geral de alto nível dos principais fabricantes de máquinas do mercado.
LaserForm CoCr (B) ou (C) DMLS &SLM3D SystemsProX DMP 200140 x 140 x 100 mmLaserForm Ni625 (B)
LaserForm 17-4PH (B)
LaserForm Aço Maraging (B)
LaserForm 316L (B)
LaserForm CoCr (B) ou (C)
LaserForm AlSi12 (B) DMLS &SLM3D SystemsProX DMP 300250 x 250 x 300 mmLaserForm 17-4PH (B),
LaserForm Maraging Steel (B),
LaserForm CoCr (B)
LaserForm AlSi12 (B)
( Ligas de cobalto-cromo, aço inoxidável, aço maraging, liga de alumínio (AlSi12)) DMLS &SLM3D SystemsProX DMP 320275 x 275 x 380 mmLaserForm Maraging Steel (A)
LaserForm 17-4PH (A)
LaserForm Ni625 ( A)
LaserForm AlSi10Mg (A)
LaserForm CoCrF75 (A)
LaserForm Ti Gr5 (A)
LaserForm Ti Gr23 (A)
LaserForm Ti Gr1 (A)
LaserForm 316L (A)
LaserForm Ni718 (A)
(ligas de titânio, alumínio, ligas de níquel, aço inoxidável, cromo de cobalto, aço maraging) DMLS &SLM3D SystemsDMP Fábrica 500 Solution500 x 500 x 500mm DMLS &SLMEOSEOS M 100100 mm x 95 mmCobalto Chrome
Aço inoxidável 316L
Titânio Ti64 DMLS &SLMEOSEOS M 290250 x 250 x 325 mmAlumínio
Cobalto Chrome
Aço maraging
Liga de níquel
Ligas de aço inoxidável
Titânio e ligas de titânio DMLS &SLMEOSEOS M 400400 x 400 x 400 mmAlumínio, aço maraging, liga de níquel, ligas de titânio DMLS &SLMEOSEOS M 400-4400 mm x 400 mm x 400 mmAlumínio, Ligas de Níquel, Aço Maraging, Aço Inoxidável, Titânio Ti64, Titânio Grau 2 DMLS &SLMEOSEOSINT M 280250 mm x 250 mm x 325 mmEOS MaragingSteel MS1
EOS CobaltChrome MP1
EOS Inoxidável EOS GP1
EOS Aço Inoxidável PH1
EOS Aço Inoxidável 316L
EOS Titânio Ti64
EOS Titânio Ti64ELI
EOS Alumínio AlSi10Mg
EOS NickelAlloy IN718
EOS NickelAlloy IN625
EOS NickelAlloy HX DMLS &SLMEOSPRECIOUS M 08080 x 80 x 95 mm Ligas de ouro, prata, platina e paládio DMLS &SLMRenishawRenAM250250 mm x 250 m m x 300 mmTi6Al4V ELI
AlSi10Mg
Aço inoxidável 316L
Aços ferramenta
Ligas de níquel
Liga de cobalto-cromo. DMLS &SLMRenishawRenAM400250 mm × 250 mm × 300 mmTi6Al4V ELI
AlSi10Mg
Aço inoxidável 316L
Aços ferramenta
Ligas de níquel
Liga de cobalto-cromo. DMLS &SLMRenishawRenAM 500M250 mm × 250 mm × 350 mmTi6Al4V ELI
AlSi10Mg
Aço inoxidável 316L
Aços ferramenta
Ligas de níquel
Liga de cobalto-cromo. DMLS &SLMRenishawRenAM 500Q250 mm x 250 mm x 350 mmTi6Al4V ELI
AlSi10Mg
Aço inoxidável 316L
Aços ferramenta
Ligas de níquel
Liga de cobalto-cromo. Soluções DMLS e SLMSLMSLM 125125 x 125 x 75 Aço Inoxidável
Aço Ferramenta
Cobalto-Cromo
Inconel
Alumínio
Titânio Soluções DMLS e SLMSLMSLM 280 2.0280 x 280 x 350Aço Inoxidável
Aço ferramenta,
Cobalto-cromo
Superligas
Alumínio
Titânio DMLS &SLMSLM SolutionsSLM 500500 x 280 x 325 Ligas de alumínio
Aço inoxidável
Ferramenta Aço
Titânio
Inconel
Cobalto-Cromo DMLS e SLMConcept Laser (aditivo GE) Mlab cusing50 x 50 x 80 mmAço inoxidável
Bronze
Ouro
Liga de prata
Liga de cobalto-cromo DMLS &SLMConcept Laser (aditivo GE) Mlab cusing R50 x 50 x 80 mmAço inoxidável
Bronze
Ouro
Liga de prata
Liga de cobalto-cromo
Titânio e ligas de titânio DMLS &SLMConcept Laser (aditivo GE) Mlab cusing 200R100 x 100 x 100 mmAço inoxidável
Alumínio
Liga de titânio
Titânio comercialmente puro grau 2
Aço maraging
Bronze
Aço inoxidável,
Liga à base de níquel
Liga de cobalto-cromo DMLS e SLMConcept Laser (aditivo GE) M1 cusing250 x 250 x 250 mmAço inoxidável
Aço ferramenta Maraging,
Aço ferramenta inoxidável
Ligas à base de níquel
Ligas de cobalto-cromo DMLS &SLMConcept Laser (aditivo GE) M2 cusing250 x 250 x 350 mmAço inoxidável
Ligas de alumínio
Ligas de titânio
Titânio puro Grau 2
Aço maraging
Aço de endurecimento por precipitação resistente à corrosão
Aço inoxidável de endurecimento por precipitação
Ligas à base de níquel
Ligas de cobalto-cromo DMLS &SLMConcept Laser (aditivo GE) M2 cusing Multilaser250 x 250 x 350 mmAço inoxidável
Ligas de alumínio
Ligas de titânio
Titânio puro
Aço maraging
Aço de endurecimento por precipitação
Ligas à base de níquel
Ligas de cobalto-cromo DMLS &SLMConcept Laser (GE Aditivo) LINHA M FÁBRICA500 x 500 x até 400 mm Ligas de alumínio
Ligas de titânio
Liga à base de níquel
Liga de cobalto-cromo DMLS &SLMConcept Laser (aditivo GE ) X LINE 2000R800 x 400 x 500 mmAlumínio (AlSi10Mg)
Liga de titânio (TiAl6V4)
Liga à base de níquel EBMArcam (aditivo GE) Arcam EBM A2X200x200x380 mmTiAl,
Liga de níquel 718 EBMArcam (aditivo GE) ) Arcam EBM Q10plus200 x 200 x 180mmTitânio Ti6Al4V
EBMArcam de Cobalto-Cromo (Aditivo GE) Arcam EBM Q20plus350 x 380mmTitânio Ti6Al4V
EBMArcam de Cobalto-Cromo (Aditivo GE) Arcam EBM Espectro H250 x 250 x 430mm Alumineto de Titânio H250 x 250 x 430mm )
Liga 718. DMLS &SLMSismamysint100100 mm x h100 mmCobalto Cromo
Metais preciosos
Bronze
Ligas de aço
Ligas de níquel
Cobre puro
Cobre ligas
Titânio
Ligas de alumínio DMLS &SLMSismamysint300300 x 400 mm Metais preciosos
Bronze
Cobalto Cromo
Aço inoxidável
Aço Maraging
Ligas de níquel
Ligas de alumínio
Titânio DMLS &SLMDMG MoriLASERTEC 30 SLM 2ª Geração.300 x 300 x 300mm Alumínio
Titânio
Aço ferramenta
Cobalto-cromo
Inconel DMLS &SLMXact MetalXM200C127x 127 x 127 mmAço inoxidável,
Superligas,
Cobalto-cromo,
Hastelloy® X,
Aços para ferramentas DMLS &SLMXact MetalXM200S127 x 127 x 127 mmAlumínio Si10Mg,
Bronze,
Aço inoxidável,
Superligas,
Cobalto Cromo,
Hastelloy® X,
Titânio Ti64,
Aços para ferramentas DMLS &SLMXact MetalXM300C254 x 330 x 330 mmAço inoxidável,
Superligas,
Cobalto-cromo,
Hastelloy® X,
Aços para ferramentas,
Bronze DMLS &SLMAddUpFormUp ™ 350350 x 350 x 350 mmAços inoxidáveis ,
Aços maraging,
Ligas de níquel,
Ligas de titânio,
Ligas de alumínio DMLS &SLMTRUMPFTruPrint 1000100 mm x 100 mm AlturaAços inoxidáveis,
Aços ferramenta,
Alumínio,
À base de níquel,
Cobalto-cromo,
Cobre,
Titânio,
Ligas de metais preciosos DMLS &SLMTRUMPFTruPrint 3000300 mm x 400 mm Aços inoxidáveis de altura,
Aços ferramenta,
Alumínio,
À base de níquel,
Cobalto-cromo,
Cobre,
Titânio,
Pré ligas metálicas ciosas
Bronze DMLS &SLMTRUMPFTruPrint 5000300 mm x 400 mm AlturaAços inoxidáveis,
Aços ferramenta,
Alumínio,
À base de níquel,
Cromo-cobalto,
Copper,
Titanium,
Precious metal alloys DMLS &SLMVELO3DSapphire315 mm diameter x 400 mmInconel 718, Titanium (6Al4V) DEDSciakyEBAM® 68711 x 635 x 1600 mmTitanium
Titanium alloys
Inconel 718, 625,
Tantalum,
Tungsten,
Niobium,
Stainless Steels (300 series),
Aluminum,
Steel Zircalloy,
Copper Nickel,
Nickel Copper DEDSciakyEBAM® 881219 x 89 x 1600 mmTitanium
Titanium alloys
Inconel 718, 625,
Tantalum,
Tungsten,
Niobium,
Stainless Steels (300 series),
Aluminum,
Steel Zircalloy,
Copper Nickel,
Nickel Copper DEDSciakyEBAM® 1101778 x 1194 x 1600 mmTitanium
Titanium alloys
Inconel 718, 625,
Tantalum,
Tungsten,
Niobium,
Stainless Steels (300 series),
Al uminum,
Steel Zircalloy,
Copper Nickel,
Nickel Copper DEDSciakyEBAM®1502794 x 1575 x 1575 mmTitanium, Titanium alloys, Inconel 718, 625, Tantalum, Tungsten, Niobium, Stainless Steels (300 series),
Aluminum, Steel Zircalloy, Copper Nickel, Nickel Copper DEDSciakyEBAM® 3005791 x 1219 mm x 1219 mmTitanium, Titanium alloys, Inconel 718, 625, Tantalum, Tungsten, Niobium, Stainless Steels (300 series),
Aluminum, Steel Zircalloy, Copper Nickel, Nickel Copper DEDOptomecLENS 450100 x 100 x 100 mmTitanium, Nickel, Tool Steel, Stainless Steel, Refractories, Composites, Cobalt, Aluminium, Copper DEDOptomecLENS MR-7300 x 300 x 300 mmTitanium, Nickel, Tool Steel, Stainless Steel, Refractories, Composites, Cobalt, Aluminium, Copper DEDOptomecLENS 850-R900 x 1500 x 900 mmTitanium, Nickel, Tool Steel, Stainless Steel, Refractories, Composites, Cobalt, Aluminium, Copper DEDOptomecLENS 860 Hybrid860 x 600 x 610 mmTitanium, Stainless Steel, Tool Steel, Inconel DEDOptomecLENS C S 600600 x 400 x 400 mmInconel Alloys, Stainless Steels, Titanium Alloys DEDOptomecLENS CS 800800 x 600 x 600 mmInconel Alloys, Stainless Steels, Titanium Alloys DEDBeAMModulo 250400 x 250 x 300Titanium Alloys, Steels, Nickel Alloys, Cobalt Alloys, and more DEDBeAMModulo 400650 x 400 x 400Titanium Alloys, Steels, Nickel Alloys, Cobalt Alloys, and more DEDBeAMMagic 8001200 x 800 x 800Titanium Alloys, Steels, Nickel Alloys, Cobalt Alloys, and more DEDInnsTekMX-600450 x 600 x 350 mmInconel, Steel DEDInnsTekMX-10001,000 x 800 x 650 mmInconel, Steel DEDInnsTekMX-Grande4,000 X 1,000 X 1,000 mmInconel, Steel DEDDMG MoriLASERTEC 65 3D735 x 650 x 560 mm Metal Binder JettingExOneM-Flex400 x 250 x 250 mmStainless steel, bronze, tungsten Metal Binder JettingExOneM-Print800 x 500 x 400 mmStainless steel (420 and 316) Metal Binder JettingExOneInnovent+160 x 65 x 65 mmStainless steel Metal Binder JettingExOneX1 25 PRO400 x 250 x 250 mmSteel (136L, 304 L and 17-4PH), Stainless steels, Inconel 718 and 625, M2 and H11 tool steels, Cobalt chrome, Copper, Tungsten carbide cobalt Metal Binder JettingDigital MetalDM P2500203 x 180 x 69 mmStainless steel (316L, 17-4PH), Titanium Ti6Al4V Metal Binder JettingHPMetal Jet430 x 320 x 200 mmStainless steel powders (developed for metal injection molding) Metal Binder JettingDesktop MetalProduction System337 x 337 x 330 mmAluminium, titanium, high-performance alloys Material ExtrusionDesktop MetalStudio System300 x 200 x 200 mmAlloy steel, Aluminium Carbide, Copper, Heavy alloy, High performance steel, Magnetics, Stainless steel, Super alloy, Titanium, Tool steel Material ExtrusionMarkforgedMetal X300 x 220 x 180 mmStainless Steel, Aluminum, Tool Steel, Inconel, Titanium
Industrial Applications
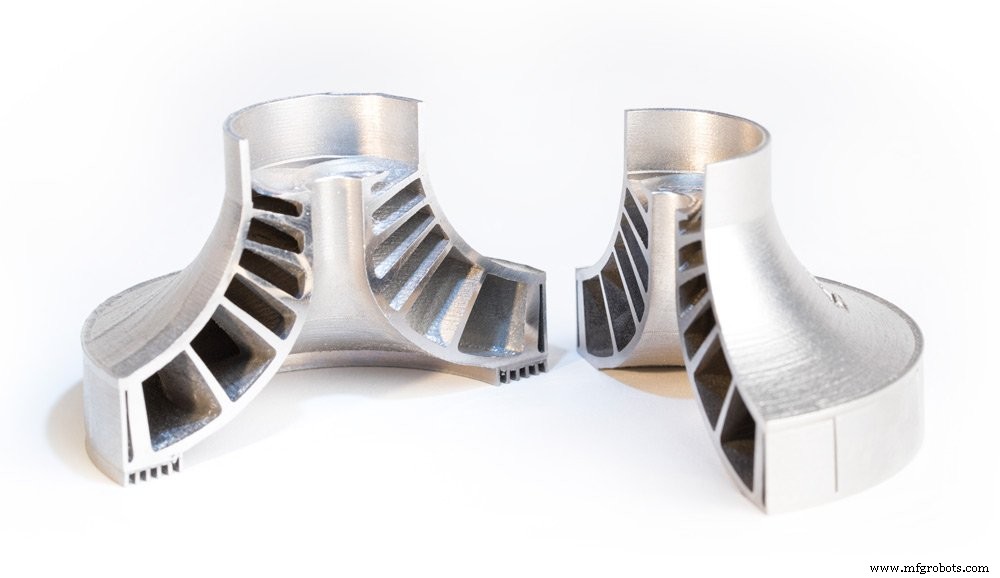
Metal 3D printing has found its niche in a number of industries, with players in the aerospace, automotive and medical industries at the forefront of driving innovation with the technology.
In this section, we take a look at the most common applications for the technology, as well as key use cases that have unlocked the benefits of metal 3D printing.
Aerospace
The aerospace industry has been a huge pioneer of metal 3D printing. By using the technology, aerospace companies hope to produce more efficient, lightweight aircraft parts to improve aircraft performance.
Within the aerospace industry, metal 3D printing is used in a range of applications, from functional prototypes to tooling, replacement parts and structural aircraft components.
General Electric
A great example is General Electric (GE), which is extensively using metal 3D printing to make and develop new products. GE’s subsidiary, GE Aviation, is producing fuel nozzles for the LEAP family of jet engines, with an aim to manufacture 100,000 fuel nozzles by 2020.
Having achieved the milestone of 30,000 3D-printed fuel nozzles in October 2018, GE looks like it’s well on its way to fulfilling this goal.
Using advanced design tools and Electron Beam Melting technology, GE’s engineers were able to create a fuel nozzle 25% lighter and 15% more fuel efficient than its traditionally produced counterpart.
The breakthrough in this case is that the fuel nozzle was printed as a single unit, whereas previous models incorporated 20 separate parts which needed to be subsequently assembled.
But GE has not stopped here. The company is also building its GE Catalyst, an advanced turboprop engine that has more than a third of its components 3D printed in various metals.
Similar to its fuel nozzles, the engineers behind the turboprop have achieved considerable part consolidation, reducing the number of parts produced from 855 to just 12. A redesign will also help to reduce the fuel burn of an engine by as much as 20%.
Automotive
Automakers have been using 3D printing since the technology’s early days — Ford Motor Company, for example, notably bought the third 3D printer ever made.
For many years, metal 3D printing has proved to be a cost-effective tool for prototyping and producing jigs and fixtures. However, advancements with the technology mean that more opportunities are opening up for end-part production.
Automotive companies can use metal 3D printing to create lightweight metal parts, leading to enhanced vehicle performance and lower fuel consumption. This is particularly beneficial for the motorsports industry, where 3D-printed car parts can offer racing teams significant performance advantages.
Another area of interest for the industry is also using 3D printing to produce spare parts that are typically produced in low volumes. 3D printing spare parts on demand enables automakers to receive parts at the point of need, reducing inventory costs and increasing agility.
BMW
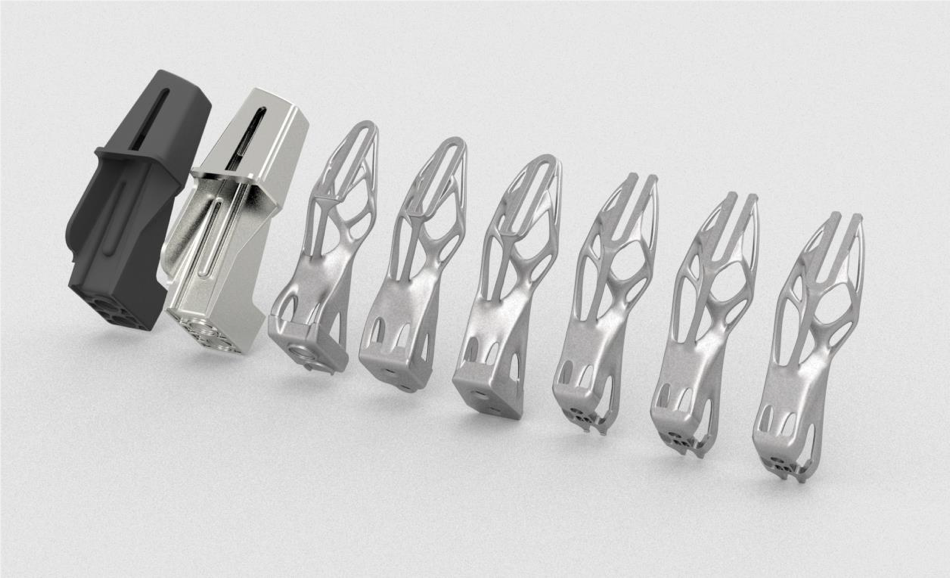
BMW is another company using 3D printing extensively. Most notably, the company has recently moved into the series production of a 3D-printed metal component for its 2018 BMW i8 Roadster vehicle.
Using topology optimisation, designers were able to optimise the vehicle’s roof bracket — a fixture for the folding/unfolding mechanism of the vehicle’s soft top. 3D printed in aluminium alloy powder (AlSi10Mg), the new roof bracket is 44% lighter than its conventionally made counterpart.
Furthermore, engineers optimised the design of the bracket to eliminate support structures. By doing so, the team was able to increase throughput from 51 to 238 of these parts per platform. This makes BMW’s roof bracket the first automotive component to be mass-produced with the help of metal 3D printing.
Bugatti
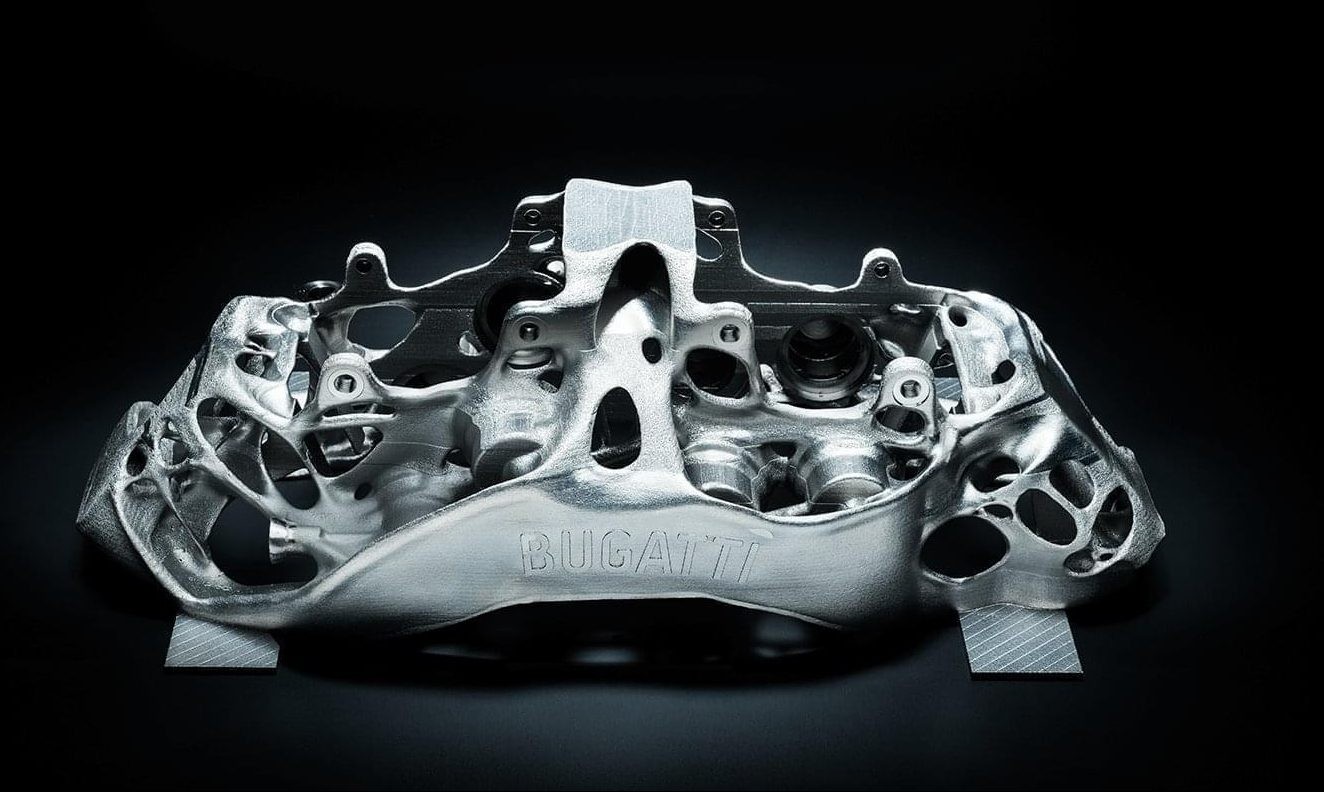
An exciting application of metal 3D printing comes from luxury car manufacturer, Bugatti. The French automaker has developed a 3D-printed brake caliper to be used on its Bugatti Chiron supercar.
An essential part of the braking system, the brake caliper has been made lighter and stronger thanks to 3D printing. Measuring 41 x 21 x 13.6 cm, the part took 45 hours to print using SLM technology and titanium powders.
By using 3D printing, Bugatti also achieved a 40% weight reduction for the caliper, when compared to machined aluminium alternative.
In 2018, the company successfully tested the brake caliper, proving that it can meet extreme strength, stiffness and temperature requirements.
Audi
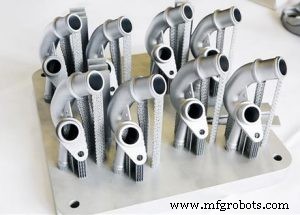
Audi presents a different business case for metal 3D printing. In this case, the German automaker is using the technology to produce spare parts that are in low demand.
Metal 3D printing allows Audi to produce these parts on demand, producing and supplying spare parts as they are needed. This in turn greatly simplifies logistics and warehousing.
Audi identified that smaller, complex components would be most suited for metal 3D printing. A good example of a component is water adapters, which Audi is already producing for the Audi W12 engine. The company says that the load capacity of the components is comparable to that of parts manufactured using traditional methods.
Medical
In the medical field, metal 3D printing allows highly customised medical devices, like orthopedic implants, to be created.
It’s far from unusual for off-the-shelf orthopaedic implants to be used for replacement surgeries. However, prefabricated implants can sometimes cause problems after the surgery as they don’t always fit properly.
To avoid this, 3D printing is increasingly being used to create customised, patient-specific implants with improved functionality.
For example, implants can be designed with improved porosity and surface texture, facilitating the growth of the tissue around the implant. This level of complexity can only be achieved with 3D printing. SmarTech Publishing predicts that more than 2 million implants will be 3D printed in metal by 2025.
Additionally, metal 3D printing can be used to create hip and knee joint replacements, cranial reconstruction implants and spinal implants.
Lima Corporate
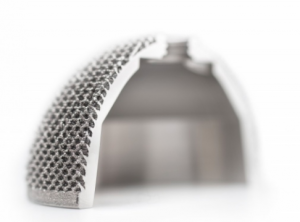
Italian medical device manufacturer Lima Corporate has been bringing additively manufactured hip implants to market for 10 years, using Electron Beam Melting (EBM) technology.
The company developed a technology for 3D printing biocompatible titanium in cellular solid structures that resemble natural bone. Such structures are used to coat an implant, allowing it to be better integrated with human tissue.
The technology is said to have helped almost 100,000 patients, enabling better implant performance and outcomes.
Industrial Goods
When it comes to the design and manufacture of tooling equipment, 3D printing can empower engineers to overcome traditional limitations. This can mean being able to create a mould or core in a matter of days instead of months, significantly reducing lead times.
Within the injection moulding industry, moulds are typically CNC-machined. Here, production costs can range from from $20,000 to hundreds of thousands of dollars. Lead times can last between 2 to 4 months. Additionally, moulds can often require multiple design iterations to achieve the final design, a costly and time-intensive process.
However, metal 3D printing can overcome these inefficiencies in several ways. First, the technology enables rapid design iterations, enabling changes to be made with relative ease.
Second, the performance of tooling aids and components can be enhanced with additive manufacturing.
For example, conformal cooling channels, lattice structures, and complex core/cavity shapes, which are too expensive or impossible to manufacture traditionally, can be factored into a mould design and 3D printed.
Conformal cooling channels are particularly beneficial as they help to achieve more homogenous heat transfer within the mould, compared to traditionally drilled straight-line cooling channels, resulting in greater cooling characteristics.
GW Plastics 3D prints moulds with conformal cooling
GW Plastics, US-based mould maker, has invested in hybrid metal 3D printing with the goal of building injection moulds with conformal cooling. One of the key reasons for this investment is faster cycles and better part quality enabled by 3D-printed moulds.
In fact, the company says 3D-printed moulds can save up to 30% of the cycle time by reducing cooling time. Furthermore, metal 3D printing allows GW Plastics to print a mould as a single piece, thus eliminating the need to assemble multiple components.
Post-processing
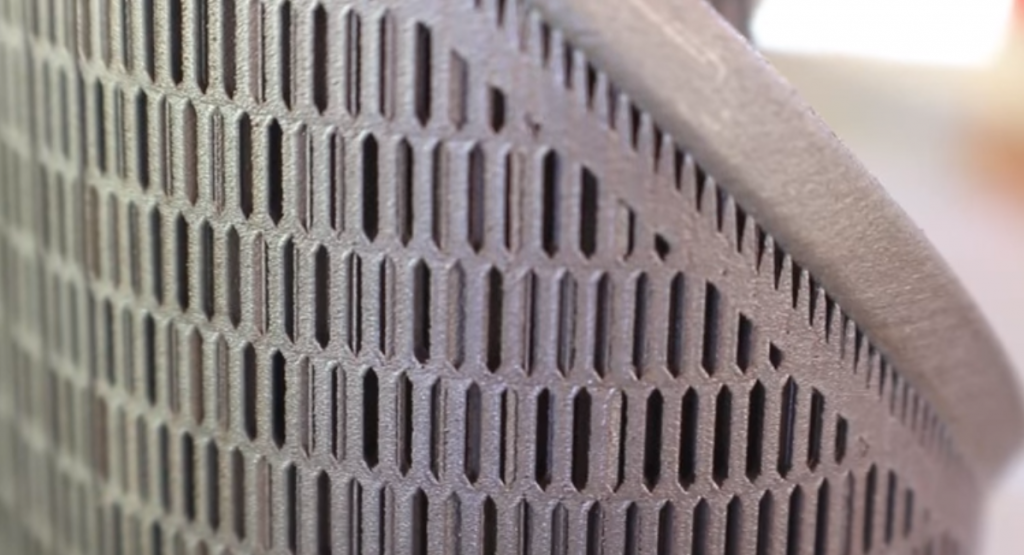
Post-processing is an unavoidable step when 3D printing metal parts. Post-processing helps to improve the mechanical properties, geometrical accuracy and aesthetics of a part, ensuring that a part meets the required design specifications.
Before printing your part, it’s important to understand the various post-processing methods that can be used to finish a metal part.
In this section, we’ll be looking at some of the main post-processing steps that can help to achieve the necessary finish for metal 3D-printed parts.
Stress relief
High temperatures and subsequent cooling are a common occurrence during the metal 3D printing process. However, when a metal part is subjected to such extreme temperature changes, this can lead to residual stress.
To avoid deformations that can occur as a result of a build-up of residual stress, parts produced with powder bed processes must undergo a stress relieving cycle. The number of stress relief cycles depends on the metal or alloy used to produce a part.
In order to protect the surface of a part from oxidation, the stress relieving heat treatment takes place in an inert (typically argon) atmosphere. Parts are typically heat treated while still attached to the build platform.
During the stress relieving cycle, the whole platform is placed in a furnace, where the part is heated to a temperature range between 550-675°C for 1 to 2 hours and then cooled down slowly. Stress corrosion cracking can also be reduced through this stress relief process.
Hot Isostatic Pressing (HIP)
Secondary heat treatment like Hot Isostatic Pressing (HIP) helps to improve the microstructure and mechanical properties of a metal part.
With HIP, high temperatures (up to 2200ºC) and isostatic inert gas pressure (from 100 to 3100 bar) are applied to a part to achieve the highest possible density, reduce porosity and eliminate internal voids.
The HIP treatment of metal parts results in optimum mechanical properties that can be compared with wrought and cast alloys.
Important to note is that the natural cooling in an HIP system can take between 8 and 12 hours. However, HIP systems powered by uniform rapid cooling technologies have been developed, allowing for the parts to be cooled from 1,260 to 300°C in less than 30 minutes.
Powder removal
With powder bed processes, a printed part is encapsulated in the unused powder which needs to be removed once the printing process is complete. The excess powder can be removed manually or automatically with the help of specialised equipment, and then recycled for later use.
The removal of any unmelted powder trapped inside a part should also be taken into consideration. For this reason, at least two escape holes should be factored into the design to help easily remove powder after printing.
Part removal
Once a part has been printed, it will need to be removed from the build platform. Build plates are then machined separately to remove excess material and return them to a usable state.
Wire Electrical Discharge Machining (WEDM) is the process of choice for cutting metal parts away from their build plates. WEDM involves creating electrical dischargers, releasing sparks which rapidly cut away material. Although the process is comparatively slow and used only with electrically conductive metals , it leaves a clean, smooth surface.
Cutting parts away with a bandsaw is another, considerably faster method. However, the process lacks the precision of wire EDM. However, if a part is going to be CNC machined afterwards, this precision can be sacrificed in favour of a faster post-processing time.
Support removal
Support structures are often considered a necessary evil when it comes to 3D printing, and this is particularly the case with metals.
Powder bed fusion technologies, like SLM and DMLS, will always require supports to ensure that they are anchored to the base plate and to mitigate the effects caused by residual stresses.
These supports are typically made from the same material as the part itself and help to minimise defects such as warping or cracking resulting from the high processing temperatures.
Supports are typically removed with the help of CNC machining. However, it’s a good practice to design as few supports as possible. In the Designing for Metal 3D printing section, we look at some of the ways to reduce the amount of support structures.
Surface finishing
As we’ve seen, a metal part that has just been printed won’t have the necessary properties required of the finished part. To achieve a smooth finish for a metal part, there are a number of common surface finishing techniques, including machining, sand blasting, media blasting and polishing.
For example, metal polishing can be used to achieve a ‘mirror-like’ finish for your part. Typically, polishing will be required before other surface treatments are conducted, in order to prevent corrosion and improve the appearance of the part. Applications are typically in the aerospace and automotive industries, as well as medical.
Abrasive blasting methods, such as sandblasting, bead blasting and media blasting, involves an abrasive material being forcibly sprayed onto a part to achieve a smooth surface.
Designing for Metal 3D Printing
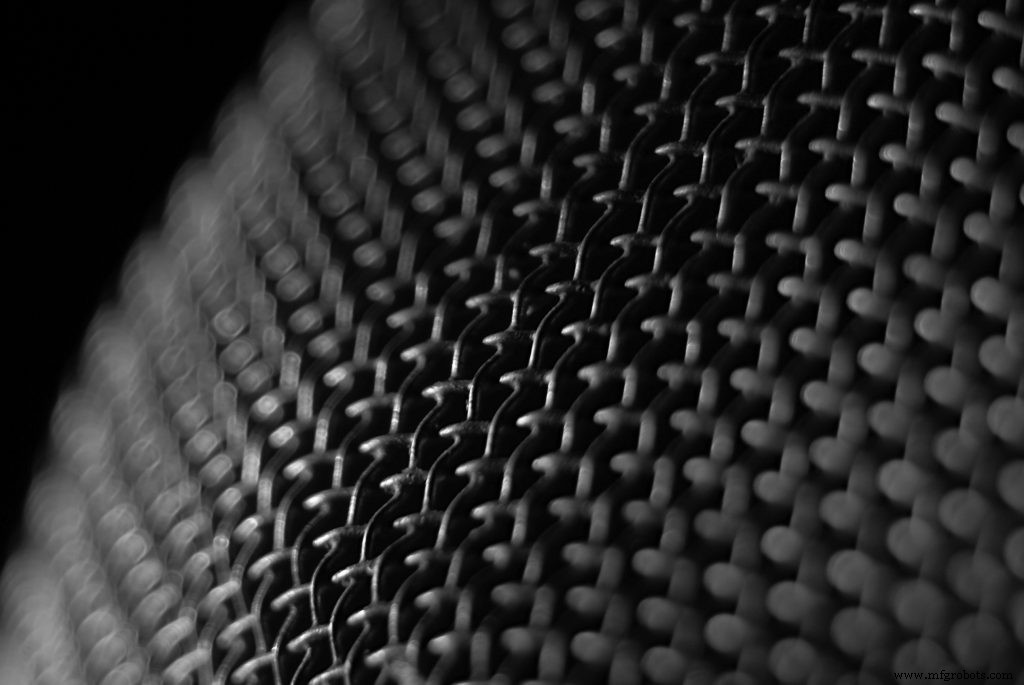
Key Considerations
Metal additive manufacturing gives us the freedom and flexibility to produce parts with complex shapes and intricate features. However, as with any technology, it does have its own set of capabilities and limitations. Understanding the basics of design for metal 3D printing is therefore crucial to obtain a successful print.
Below are some of the key considerations to keep in mind when designing for metal 3D printing.
1 Wall Thickness
Choosing the right wall thickness can make the difference between a successful and a failed print.
As a general rule of thumb, it’s recommended to design walls with a minimum wall thickness of 0.4mm.
It’s also important to ensure that the wall thickness of your parts are not too thin or thick, as this can result in deformation during the printing process or cause damage after removal from the build plate.
In the case of thick walls, the mass can be minimised by applying lattice or honeycomb structures, making the overall printing process cheaper and faster.
2. Support structures
While it’s ideal to design a part with the minimum amount of supports necessary, support structures will virtually always be required with metal 3D printing technologies (except for DED).
Supports play two main roles:first, they are used to anchor a metal part to the base plate to draw away heat, which could otherwise cause residual stresses and build failures.
Second, supports are required to successfully print complex features such as holes, angles and overhangs. For these features, angle measures should be noted:overhangs with an angle less than 45° will require supports.
For features located inside a part, such as horizontal holes along the X or Y axis, it’s generally recommended to design angled support structures.
Angled supports can help maintain a solid connection with the printing bed while minimising the amount of contact the supports have with your part’s surface area. This will make post-processing much easier.
Finally, make sure to check that all support structures will be accessible after printing. Qualquer suporte difícil de alcançar será difícil de remover de forma limpa.
3. Overhangs and Self-Supporting Angles
Overhangs are unsupported downward-facing surfaces, and will need to be carefully considered when designing a part.
Large overhangs (typically over 1mm) will require support structures to prevent them from collapsing during the printing process. The maximum length of an unsupported horizontal overhang is typically 0.5mm, and it is important to keep your overhangs below this length.
If your design requires overhangs, you can also design fillets and chamfers under the downfacing surfaces to make the overhang self-supporting.
Angled features can be designed self-supporting. For this, the angle of a feature should not be less than 45°.
4. Part Orientation
Part orientation is another critical consideration with metal 3D printing. Experimenting with the orientation of your part is the best way to minimise the amount of support structures needed.
For example, if you want to make a metal part with hollow tubular features, a horizontal orientation will take up more space, while a vertical or angled orientation will save space and reduce the amount of supports needed.
Part orientation is also important in determining the accuracy and surface roughness of a part. When selecting your part orientation, keep in mind that downward and upward facing surfaces will have different surface roughness (so-called down-skins tend to have inferior surface finish). If you want to produce detailed features with the best accuracy, make sure to orientate these on the upward facing surface of the part.
5. Channels and Holes
Metal additive manufacturing is notable for its ability to produce parts with internal complex channels for improved fluid flow and holes. A general rule of thumb is to not design such features under 0.4mm in powder-bed processes and under 0.2mm in Metal Binder Jetting. Holes and tubes larger than 10mm in diameter will require support structures.
Keep in mind that perfectly round horizontal holes are still a challenge to 3D print. Consider redesigning such shapes into a self-supporting teardrop or diamond shape.
Additionally, if you are designing a hollow part, you need to factor in the design escape holes to ensure the removal of the unmelted powder. A recommended diameter for escape holes is 2-5mm.
Conclusion
Metal 3D printing:a viable manufacturing technology
Metal 3D printing is emerging as a viable manufacturing technology, as advancements across the spectrum of hardware, materials and software continue to be made.
The technology could help to drive new business models and product development strategies by enabling economic low-volume and on-demand production, innovative design possibilities and, of course, mass customisation.
Of course, it will take some time for companies to become fully confident with the technology. However, an increase in knowledge sharing and education will not only help to further the potential of metal 3D printing, but will also spur a wider adoption of the technology across industries.
Discover More Metal 3D Printing Resources:
Expert Interviews
Digital Alloys CEO Duncan McCallum on Joule Printing and the Future of Metal 3D Printing
HP’s Global Head of Metals on the Impact of HP Metal Jet
ANSYS’ Chief Technologist on Achieving Metal 3D Printing Success with Simulation
Sintavia President Doug Hedges on Achieving Serial Production with Metal 3D Printing
APWORKS CEO Joachim Zettler on Finding the Right Business Case for Metal 3D Printing
SmarTech Analysis’ Scott Dunham on the Future of Metal 3D Printing, Service Bureaus and the AM Materials Market [Part Two]
MELD Manufacturing CEO Nanci Hardwick on Fulfilling the Potential of Metal Additive Manufacturing
3DEO’s President Matt Sand on Taking Metal 3D Printing Into High-Volume Production
VELO3D’s VP of Technology Partnerships on Expanding the Capabilities of Metal 3D Printing
Metal 3D Printing Technologies
Metal 3D Printing:Where are We Today?
All You Need to Know About Metal Binder Jetting
Metal 3D Printing:What is Direct Energy Deposition?
An Introduction to Electron Beam Melting
An Introduction to Wire Arc Additive Manufacturing
Your Guide to the Top DMLS Machines [2018]
Designing for Metal 3D Printing
6 Important Design Considerations for Metal 3D Printing
Making Metal Parts Lighter with Metal 3D Printing
Metal 3D printing Materials
Why Materials are the Key to Metal 3D Printing Success:Expert Interview with voestalpine’s Armin Wiedenegger
3D Printing Precious Metals – a New Approach?
Scalmalloy:The Latest High-Performance Material for Metal 3D Printing
A Quick Guide to 3D Printing Metals
A Guide to 3D Printing With Titanium
Metal 3D Printing Challenges
5 Common Problems Faced with Metal 3D printing – and How You Can Fix Them
Quality Assurance for Metal 3D Printing:Solving 3 Common Challenges
Metal 3D Printing Applications
5 Innovative Use Cases for Metal 3D Printing
How Can 3D Printing Benefit Metal Casting? Here Are 3 Ways
impressao 3D
- Um guia para iniciantes em impressão 3D de silicone
- Um breve guia para impressão 3D com jato de pasta
- Um guia abrangente para impressão 3D por jato de material
- Impressão 3D em TPU:um guia para a impressão 3D de peças flexíveis
- Impressão 3D interna x terceirizada:o guia definitivo
- 5 casos de uso inovadores para impressão 3D de metal
- Tornando peças de metal mais leves com impressão 3D de metal
- Estruturas de suporte de impressão 3D:um guia completo
- O guia completo para impressão 3D
- Guia de seleção de materiais de impressão 3D