PLC vs DCS
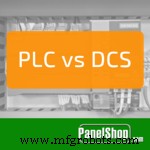
DCS entra em cena
A DCS apareceu em cena por volta de 1975, época em que a PLC estava estabelecendo seu domínio no setor de automação. O aumento do uso de microcomputadores foi a força motriz por trás da criação do DCS. O maior e mais óbvio benefício do DCS foi sua capacidade de controlar uma planta inteira por meio de comunicações proprietárias e um sistema distribuído. Por exemplo, se houvesse uma fábrica que fabricasse sanduíches de sorvete, um único DCS seria responsável pelos processos de preparação de ponta a ponta. Um controlador seria responsável pela linha de produção, o outro controlador autônomo cuidaria da refrigeração enquanto outro poderia interromper o processo de cozimento. Isso significa que, caso um único controlador falhe, o restante da operação continua, levando a um sistema robusto.
Além disso, o DCS também oferece monitoramento e controle integrados, muito parecido com os sistemas SCADA com toda a base de tags armazenados em um repositório. Por fim, o DCS apresentava um paradigma de programação que era funcional, possibilitando a reutilização do código.
Diferença
Os DCSs modernos podem ser pensados como vários PLCs em operação paralela, apesar do monitoramento e controle integrados. Graças às comunicações de código aberto, vários PLCs agora têm a capacidade de se comunicar entre si e realizar tarefas de forma autônoma enquanto coordenam entre si. O desenvolvimento de um DCS através de múltiplos PLCs interconectados tornou-se possível, borrando a linha que separa as duas entidades.
Mas uma grande diferença entre um PLC e um DCS vem do fator preço. Ter um DCS pode resultar em economias de custo significativas, para uma planta de grande porte, em comparação com a construção de um sistema do zero por meio de vários PLCs. Graças aos protocolos proprietários, a comunicação é mais segura, robusta e fácil para os desenvolvedores codificarem. Além disso, um DCS inclui um sistema de monitoramento e controle, enquanto para um sistema baseado em PLC , um sistema SCADA teria que ser adquirido ou desenvolvido, aumentando ainda mais o nível de complexidade.
Com tudo isso dito, a DCS tem algumas desvantagens, uma das principais é a falta de qualificação no mercado. Mesmo a maioria dos técnicos de piso estão cientes da programação da lógica ladder e podem realizar modificações básicas se necessário. Por outro lado, os programadores DCS são difíceis de encontrar e, mesmo que o façam, são caros. Portanto, no final das contas, a escolha entre DCS e PLC seria totalmente dependente da aplicação e suas análises de custo/benefício.
Quatro principais aspectos de um bom design do painel de controle
Substituindo IHMs estacionárias por IHMs contextuais
Sistema de controle de automação
- Dicas gerais para solução de problemas
- C# usando
- Automação:Software Vision System Atualizado
- Java 9 - Sistema de Módulos
- C# - Tratamento de Exceções
- Sistemas incorporados e integração de sistemas
- Sobrevivendo a um projeto de migração do sistema de controle
- Integração do sistema de controle
- Lógica Ladder 201- Varredura PLC
- Um sistema de automação adaptável em ação