Gêmeos virtuais otimizam as operações na CenterLine
Na ciência militar, um “multiplicador de força” é um sistema operacional que usa a estratégia para aumentar a eficácia dos armamentos existentes. Podemos usar a ideia como uma metáfora para melhorar a eficiência dos sistemas de informação de engenharia e manufatura, desde o conceito inicial até o atendimento contínuo ao cliente.
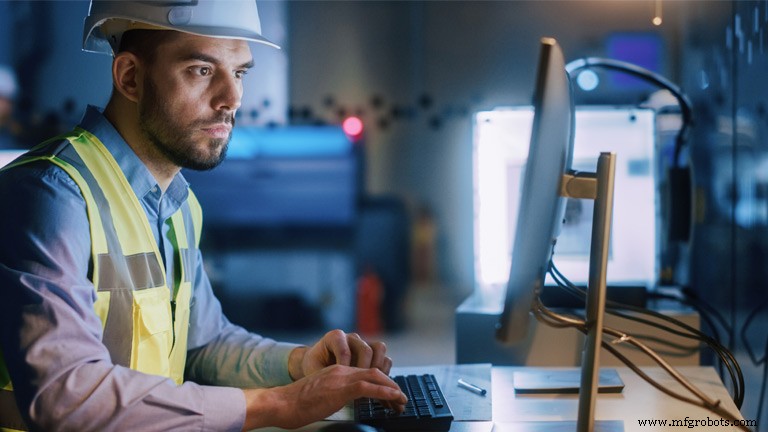
Os “armamentos” da automação industrial são representados por uma variedade de siglas:CAD, CAE, PDM, PLM, SCM, MES, CMS e muito mais. Quase todas as empresas de manufatura têm algum nível de automação de processos, mas muitas conversas sobre processos de manufatura terminam com a frase “depois copiamos os dados da lista de materiais”. É aqui que as melhorias de eficiência param. Para continuar nossa metáfora inicial, as empresas manufatureiras são donas dos armamentos, mas não há uma estratégia primordial para torná-las um multiplicador de força industrial.
Temos acesso a muitas soluções de criação, coleta e gerenciamento de dados em todo o espaço de fabricação que informam vários aspectos do que um produto deve se tornar e como um processo de fabricação deveria trabalho, sistema por sistema. O próximo passo é ir além do “deveria” para o “faz”. Transformar informações em inteligência em tempo real é o multiplicador de força — os dados de desempenho planejados que essas soluções fornecem podem se tornar informações sobre o desempenho em tempo real e no mundo real.
Estruturas de Informações Estratégicas
Virtual thread e virtual twin (também conhecido como digital twin/thread) são dois conceitos relacionados na vanguarda dessa busca por inteligência em tempo real. Como lembrete, um encadeamento virtual é a capacidade de os usuários melhorarem desempenhos específicos, fornecendo as informações certas para as pessoas certas no momento certo. Enquanto isso, um gêmeo virtual é uma representação visual constantemente atualizada de um produto, sistema ou processo com base em dados do mundo real.
Essas novas estruturas de informações impulsionam um novo modelo de processo no qual os dados são vistos como parte de um encadeamento virtual e de um gêmeo virtual. Na engenharia baseada em modelo, por exemplo, o thread e o gêmeo representam uma estrutura estratégica para a criação de valor máximo na empresa. Ambos incluem requisitos conforme projetado; registros de validação e calibração; e dados como construídos, operados e mantidos.
O encadeamento virtual e o gêmeo virtual são conceitos, não produtos ou serviços específicos:você não pode entrar em contato com seu integrador local e solicitar um encadeamento virtual. Em vez disso, eles fornecem soluções que ajudam os usuários a criar sistemas totalmente digitais nos quais cada indivíduo na organização tem todas as informações necessárias em um sistema fácil de acessar e compartilhar.
A conectividade é o objetivo primordial. Muitos problemas relacionados a dados se resumem a conexões e acesso, o que significa que as empresas precisam eliminar as ineficiências que afetam as operações de fabricação.
Quantos desses desafios existem em sua organização?
- As mudanças de engenharia não chegam ao chão de fábrica em tempo hábil
- Falta de visibilidade do fornecedor
- Nenhum padrão ou controle na criação de instruções de trabalho
- Gerenciamento e controle de conteúdo fora de sincronia
- O marketing cria conteúdo com informações de design desatualizadas
- Perda de produtividade devido a informações imprecisas e pouco claras
- Falta de acesso a dados para as pessoas certas.
Embora muitos desses problemas pareçam problemas de tecnologia ou metodologia, eles sempre afetam os indivíduos na operação downstream, impedindo sua capacidade de otimizar fluxos de trabalho. Para tornar as operações mais eficientes, você deve melhorar os sistemas em uso, não tentar “consertar” as pessoas que os utilizam. Os sistemas totalmente digitais atendem às necessidades dos membros da equipe, eliminando esses problemas de conectividade e acesso a dados.
O tópico virtual
O encadeamento virtual - o lado das comunicações da nova estrutura industrial - permite o fluxo de dados conectado para todas as informações de ativos e metadados relacionados. A ideia do fio virtual se originou na pesquisa aeroespacial há mais de 10 anos, quando pesquisadores do Laboratório de Pesquisa da Força Aérea dos EUA na Base Aérea de Wright-Patterson o usaram para descrever a montagem orientada por modelos no chão de fábrica. Vários encadeamentos se estendem do modelo (a fonte de dados comum) às equipes de projeto, aquisição, teste, produção, operações de campo e manutenção, o que significa que não há necessidade de nenhum indivíduo no encadeamento solicitar dados ou responder a solicitações de dados com uma cópia /cola e-mail. A informação está sempre “ativada” e sempre acessível, estabelecendo um verdadeiro recurso singular e um caminho de comunicação para todas as partes, independentemente do silo ou fluxo de trabalho.
O gêmeo virtual na CenterLine
Ter acesso sempre ativo e em tempo real aos dados de threads virtuais torna possível um gêmeo virtual. Os threads transmitem uma visão abrangente do produto, combinando detalhes da lista de materiais com dados CAD/CAE para uma representação visual, virtual e em tempo real. É preciso um fluxo bidirecional em threads virtuais para habilitar um verdadeiro gêmeo virtual, exigindo um loop de feedback em que calibração, validação, dados como construídos e usados atualizam o gêmeo. Juntos, o encadeamento virtual e o gêmeo virtual são a unificação de design e dados.
Por exemplo, a empresa canadense de tecnologia e processos de automação industrial CenterLine Limited (Windsor, Ontário), produtora de linhas de montagem e soldagem automatizadas personalizadas, enfrentou desafios com configurações de fábrica caras, especialmente se a empresa precisasse corrigir erros de projeto ou lidar com acidentes operacionais entre máquinas e trabalhadores humanos em sistemas físicos já instalados.
A CenterLine buscou otimizar seus projetos de células de trabalho robóticas e superar esses desafios por meio de simulação digital antes da implantação de equipamentos físicos no chão de fábrica. Para atingir esse objetivo, eles implementaram a solução DELMIA na plataforma 3DEXPERIENCE da Dassault Systèmes para simular virtualmente produtos, processos e operações de fábrica para movimentos otimizados do robô, layout da planta, fluxo de materiais e ergonomia.
Desde a implementação do DELMIA para cada célula de trabalho robótica, a CenterLine reduziu os problemas relacionados a ferramentas e retrabalho em até 90% e o tempo de programação no chão de fábrica em até 75%. O tempo economizado através da simulação de caminhos de ferramentas de soldagem a arco de robô melhorou a produtividade em 15% e reduziu o tempo de lançamento no mercado para simulação e projeto em 15% a 20%. Como uma única fonte de verdade para diferentes dados CAD, a plataforma unificada permite que os líderes da CenterLine se concentrem nas operações do dia-a-dia em vez de gerenciar dados e produtos
Quando todos os canais de dados estão conectados em uma estrutura Virtual Thread/Virtual Twin, os membros da equipe estão unidos em uma estratégia que permite um melhor uso dos dados existentes. Com efeito, os fabricantes acabam ganhando um novo multiplicador de força para o valor de fabricação.
Sistema de controle de automação
- Digital Twins:por que réplicas virtuais de ativos criam valor comercial real
- Como coletar dados de sistemas legados para melhorar as operações
- Tornando os dados de IoT significativos na agricultura na John Deere
- A precisão dos modelos digitais de dados gêmeos é a chave do sucesso
- Como gêmeos digitais podem ajudar a impulsionar o desempenho logístico
- Ridecell lança 'primeira plataforma' para converter dados de veículos em operações automatizadas
- O que é a vida útil da ferramenta? Como otimizar ferramentas com dados de máquina
- Três maneiras pelas quais a IA está melhorando as operações de fabricação
- Por que suas operações de armazém e fábrica precisam de IIoT
- Gêmeos Digitais:O que você quer dizer com isso?