História de sucesso do controle de temperatura
Sucesso no controle de temperatura:a Film Tech, uma empresa em Stanley, WI, comprou uma linha de filme soprado de 3 camadas usada de uma empresa em Ohio. A máquina foi desmontada e levada para suas instalações na primavera de 2015. A Film Tech solicitou que uma atualização completa dos controles fosse concluída na linha devido a lapsos na documentação da máquina em seu estado original. O escopo do projeto concentrou-se em atualizar o controle de temperatura das extrusoras e matrizes, atualizando o manuseio de bandas da linha com novos acionamentos e motores, além de fornecer uma nova estação de operador para controlar os processos da linha. Com esses itens, também foram necessárias atualizações nas seguranças da máquina. A atualização exigia não apenas suporte elétrico para os itens que a Sure Controls estava fornecendo, mas também a interface do equipamento para o novo equipamento Process Control Corporation (PCC) e QC Electronics. Além do suporte elétrico, o suporte mecânico também deveria ser fornecido para a montagem do motor, um novo rolo de resfriamento, melhorias no enrolador, bem como auxiliar na localização de gabinetes de controle e conduítes.
Solução
A parte da atualização que se concentrou na atualização dos controles de temperatura exigia a substituição do sistema antigo por novos controladores Eurotherm 3216 a serem montados no gabinete de controle no 2 nd piso. Cada seção de aquecimento e resfriamento no nível do solo seria habilitada com relés de estado sólido Carlo Gavazzi no gabinete de controle principal. Condutos separados foram executados do gabinete de controle para as caixas de junção em cada uma das extrusoras para fornecer separação dos fios de alta tensão da fiação de sinal para cada seção. A partir da nova estação Wonderware, o operador poderia ajustar os pontos de ajuste de temperatura e observar os feedbacks de temperatura dos termopares instalados em cada seção. Os transformadores de corrente também foram instalados nos SSRs para fornecer feedback de corrente à IHM. Esse feedback junto com a porcentagem de saída do controlador de temperatura pode ser usado como uma ótima ferramenta de solução de problemas para determinar se um aquecedor não está funcionando corretamente.
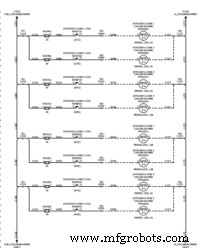
Para operar o enrolador, um Redlion Graphite HMI de 9" foi montado no enrolador para permitir que o operador para controlar os modos de enrolamento, como enrolamento na parte superior ou inferior, modo acima ou abaixo, engatando os rolos de colocação, abrindo/fechando o nip do enrolador enquanto fornece diagnósticos de linha para as paradas de emergência na linha. O layout e os esquemas de cores na IHM do enrolador imitavam o painel principal do operador, que possui uma tela sensível ao toque de 19” com Wonderware. Este painel principal do operador permitia uma localização central para controlar os pontos de ajuste de temperatura nas extrusoras e na matriz, a velocidade da linha, bem como controles auxiliares, como o Oscillating Haul Off, Bubble Cage e Treater. Telas de tendências foram fornecidas para permitir o monitoramento de temperaturas, velocidades e outras características da linha que podem ajudar no diagnóstico de defeitos em seus produtos. A estação Wonderware foi configurada para se comunicar com os misturadores PCC e o sistema de carregamento a vácuo. A partir do MOP, o sistema de carregamento a vácuo pode ser totalmente controlado ativando/desativando as tremonhas, enquanto o controle dos Blenders foi ligeiramente restrito. Os liquidificadores podiam ser desligados ou colocados no modo automático, no entanto, se qualquer ação manual fosse necessária, esse controle era deixado fora do MOP para exigir que o operador estivesse à vista do liquidificador. Os pesos da tremonha, o status do misturador e a produtividade (lbs/h) foram todos trazidos para a IHM para fins de monitoramento/tendência.
Para fornecer ao operador um ambiente seguro para trabalhar, a máquina tinha um PLC de segurança Logix de controle Allen Bradley instalado. Com o uso do Allen Bradley Point IO, racks de segurança foram instalados em cada nível da máquina para fornecer ao operador a capacidade de desligar a máquina com vários dispositivos de segurança, como linhas de vida, botões de parada de emergência, tapetes de segurança e scanners de segurança .
Suporte contínuo
Com a solução principal implementada, foi solicitado um serviço adicional para resolver alguns itens da linha. Uma delas foi a adição de automatizar o A-Frame no Top Nip. Isso exigia a colocação de 4 servomotores no Nip superior e lógica adicional a ser adicionada ao processador Logix de controle. O operador inseriria uma distância desejada entre os lados no A-Frame e pressionaria o botão Go to Position na HMI. Sinais analógicos de potenciômetros internos dentro dos Servos foram trazidos de volta ao PLC e dimensionados para que um feedback preciso da posição pudesse ser exibido ao operador. O controle para isso foi fornecido no painel principal do operador, mas um Redlion HMI adicional de 9" foi programado e fornecido à Film Tech para fornecer ao operador a capacidade de controlar o ajuste do quadro A a partir do Nip superior.
Em além das mudanças no Top Nip, havia o desejo de melhorar o sistema IBC existente na linha. Durante os testes realizados na Film Tech, o filme apresentou rugas. Acreditava-se que as rugas fossem causadas pelo fato de o sistema IBC não controlar a pressão adequada no interior da bolha, fazendo com que o filme surgisse. Novos sensores ultrassônicos e um controlador Eurotherm 2704 foram usados para substituir o equipamento existente dentro de um novo gabinete IBC. Na porta do gabinete do IBC havia 3 potenciômetros para controlar a velocidade dos VFDs Powerflex de alimentação e exaustão. Uma grande válvula de controle também foi fornecida para restringir a quantidade de ar que sai da bolha. Com os novos controles instalados e alguns ajustes, uma bolha estável foi produzida, resolvendo o problema de enrugamento.
Sistema de controle de automação
- Circuitos de controle
- Skate
- Carrossel
- Sofá
- Termômetro
- Controle de acesso com QR, RFID e verificação de temperatura
- Sistema de controle de dispositivo baseado em temperatura usando LM35
- História de sucesso:Smart Talent Success for Growing Company
- História de sucesso:rápido ROI e crescimento da empresa
- Erros em gabinetes de painéis de controle industriais de resfriamento