Princípios e ferramentas Lean
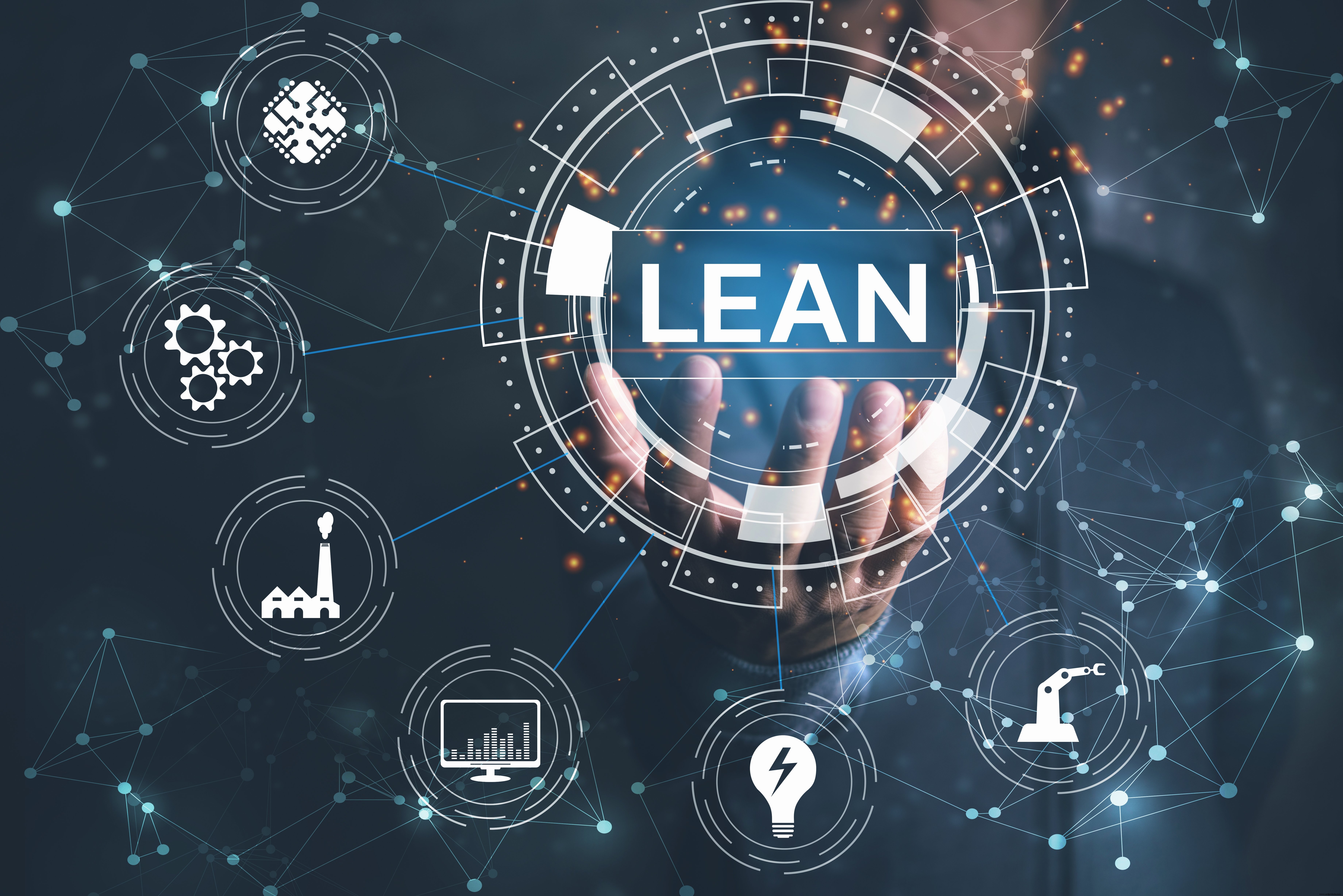
Bem-vindo ao segundo capítulo de nossa série sobre Lean e Six Sigma. Como vimos no primeiro post, Lean e Six Sigma são metodologias complementares de melhoria contínua que reduzem o desperdício geral e a variabilidade nos processos de produção, respectivamente. Embora essas duas metodologias usem abordagens e ferramentas diferentes para impulsionar melhorias na produtividade e na lucratividade, elas têm em comum o fato de que podem ser empregadas para melhorar todas as facetas do seu negócio.
Filosofia Enxuta
Pilares enxutos
A filosofia Lean tem dois pilares interligados:"Eliminar Lixo" e "Respeito pela Humanidade". Esses elementos fundamentais contribuem muito para o sucesso da Manufatura Enxuta. Vamos falar sobre eles individualmente - o segundo primeiro.
O conceito de Respeito pela Humanidade se manifesta pelo respeito aos trabalhadores e pelo reconhecimento de sua inteligência, criatividade e engenhosidade inerentes. Isso é conseguido capacitando-os e desafiando-os a melhorar os produtos que estão fabricando, juntamente com os processos de produção e as ferramentas empregadas para fazê-los.
O conceito de Eliminação de Desperdícios é o mecanismo pelo qual uma organização aumenta sua qualidade e lucratividade. De uma perspectiva Lean, o cliente define o preço com base no valor que recebe. Com base no preço definido pelo cliente, a melhor maneira de uma organização Lean melhorar a lucratividade e prosperar é eliminar qualquer causa de baixa qualidade, atraso na entrega, problemas de segurança e custos desnecessários - tudo definido no Lean como "desperdício".
5 princípios de Lean
- Compreenda o "valor" conforme definido pelo cliente
Entenda em detalhes o que o cliente valoriza e está disposto a pagar por um determinado produto, serviço ou informação - Defina o fluxo de valor para cada produto
Identifique todas as etapas vinculadas que constituem os processos de negócios e de produção atuais que são necessários para transformar os insumos em produtos, serviços e informações que os clientes valorizam. - Estabeleça um fluxo contínuo dentro da organização
Simplifique os processos, eliminando o máximo de desperdício possível, para que produtos, serviços e informações de qualidade fluam suavemente através do fluxo de valor - Manter o fluxo durante o uso de um sistema pull
Com base em fluxo contínuo, alinhe e equilibre a produção para atender a demanda "Just in Time" sem estoque excessivo, mantendo altos níveis de qualidade e serviço - Buscar a perfeição por meio da melhoria contínua dos processos
Comprometa-se a buscar implacavelmente o desperdício zero em todos os processos de fluxo de valor, repetindo essas etapas e adaptando produtos, serviços e informações às demandas dos clientes em constante mudança.
Trabalho "sem valor agregado"
Conforme mencionado acima, eliminar o desperdício é um pilar fundamental do Lean. Para identificar o desperdício, todas as tarefas que estão sendo executadas atualmente são vistas através da lente do trabalho com valor agregado e sem valor agregado. O trabalho com valor agregado cria diretamente os recursos, características e benefícios que o cliente deseja e está disposto a pagar (por exemplo, operar a máquina que produz um pente de plástico). O trabalho sem valor agregado é composto de tarefas com as quais o cliente não se preocupa e não quer pagar (por exemplo, custo de material e mão de obra de produtos de sucata repassados ao cliente no preço do pente). Algum trabalho sem valor agregado é necessário. Por exemplo, tarefas para atender aos requisitos de relatórios estatutários de uma empresa são tarefas que não contribuem diretamente para a produção do pente. Embora o cliente que compra o pente de plástico possa não se importar realmente com os relatórios legais, os acionistas e funcionários da empresa se preocupam - sem valor agregado, mas necessário. De qualquer forma, o objetivo é observar todas as tarefas sendo concluídas, otimizar e, idealmente, eliminar todo o trabalho desnecessário e sem valor agregado. Vários estudos realizados mostram que, em muitas organizações, mais de 90 a 95% do trabalho realizado para produzir um produto ou serviço é um trabalho sem valor agregado.
Ferramentas Lean
Há um número significativo de ferramentas no kit de ferramentas Lean - mais de 20 ou 30, dependendo de com quem você fala - todos os quais têm aplicação em várias situações. Abaixo está uma lista de algumas das ferramentas básicas do Lean.
Implementação de política (Hoshin Kanri)
Implementação de política é um processo de planejamento e execução estratégico. Ele é projetado para garantir que as metas e estratégias gerais da empresa sejam definidas e comunicadas em todos os níveis da organização. Além disso, por meio do processo, todos os níveis da organização identificam como seus objetivos de trabalho departamentais e individuais são mapeados para os objetivos e estratégias da empresa. Esse alinhamento, até o nível do colaborador individual, garante o entendimento e a adesão em toda a organização e elimina o desperdício corrigindo metas desalinhadas antes que os recursos sejam gastos.
Mapeamento do fluxo de valor
Um Mapa do Fluxo de Valor é uma ferramenta que permite uma visão '' horizontal '' das etapas de alto nível envolvidas em criar um produto, serviço ou informação. Ele documenta todos os fluxos de materiais e informações no processo, bem como a linha do tempo em todo o fluxo de valor. Ele mapeia o estado atual do processo e traz visibilidade às áreas de oportunidade no caminho para o estado futuro aprimorado, contrastando o tempo de ciclo total com o tempo de valor agregado.
Os 8 resíduos
No Lean, o desperdício é normalmente identificado como se encaixando em uma das oito categorias, todas as quais são trabalhos sem valor agregado. Basta lembrar " D.O.W.N.T.I.M.E . "
- D efeitos - produtos, serviços ou informações que não correspondem às especificações do cliente
- O verprodução - Criar mais produto, serviço ou informação do que o exigido do cliente em um determinado momento
- W aiting - Atrasos no processamento do produto e tempo ocioso experimentado por pessoas e máquinas devido ao fluxo desequilibrado
- N Habilidades utilizadas / Criatividade não utilizada - Falha em combinar as pessoas com seus talentos, envolvê-las e capacitá-las para desenvolver melhorias nos produtos e processos
- T ransportation - A movimentação desnecessária de produtos ou informações
- I nventory (Excesso) - Produtos, serviços ou informações além da quantidade que está sendo processada e que não são necessários para atender a demanda atual do cliente
- M otion - Movimento de pessoas e / ou máquinas que não agregam valor ao produto
- E Processamento excessivo - etapas de processo ou atividades desnecessárias e frequentemente desatualizadas que não agregam mais valor a um produto, serviço ou informação
Análise da causa raiz - os 5 por que?
Em instalações de manufatura modernas, há uma quantidade significativa de complexidade nos sistemas e processos usados para criar produtos, serviços e em formação. Quando ocorrem problemas, a abordagem Lean não deve se contentar em lidar com os sintomas, mas, em vez disso, trabalhar para identificar a causa raiz. É prática padrão fazer e responder à pergunta "Por quê?" pelo menos cinco vezes para rastrear a cadeia causal através dos sintomas até a verdadeira causa raiz. Essa causa raiz é então resolvida.
PDCA
Em Lean, o processo frequentemente usado para alcançar a eliminação de desperdícios é o ciclo PDCA. É um processo iterativo, às vezes exigindo a repetição várias vezes antes que as verdadeiras causas do desperdício possam ser identificadas e resolvidas.
PDCA é composto das seguintes etapas.
-
Plano - Defina a oportunidade / objetivo e as mudanças necessárias
-
Faça - Faça as alterações para concretizar a oportunidade identificada
-
Verificar - Medir e avaliar os resultados das mudanças feitas
-
Agir - Padronizar o novo processo ou reiniciar o ciclo, com base nos resultados
5S / CANDO
5S vem do Sistema Toyota de Produção. Trata-se de criar uma área de trabalho configurada para o sucesso onde tudo o que é necessário, e somente o que é necessário, esteja onde deve estar para minimizar o desperdício no processo. Cada S tem um significado baseado no quase equivalente em inglês das palavras japonesas. Eles são:
Classificar - Classifique todos os materiais na área de trabalho e remova tudo o que não for necessário
Definir em ordem - Organizar os itens necessários e estabelecer um lugar para tudo
Brilho - Limpe frequentemente a área de trabalho
Padronizar - Estabelecer padrões documentados para as etapas de classificação, configuração e iluminação
Sustentação - Inspecione e reforce os padrões definidos
5S é uma adaptação de um processo semelhante criado por Henry Ford na década de 1920 chamado CANDO :
C inclinado para cima, A variando, N alimentação, D isciplina, O melhoria contínua
Mudanças rápidas (troca de molde em um minuto - SMED)
Você já assistiu a uma corrida da NASCAR e se perguntou como eles trocam quatro pneus e enchem um tanque de gasolina em 7,3 segundos? É através da aplicação de Mudanças Rápidas ou S.M.E.D. técnicas. Os processos de troca rápida reduzem os tempos de configuração e transição para máquinas e processos. No Lean, o objetivo de tempos reduzidos de configuração e troca é aumentar a flexibilidade da programação da produção, reduzindo os tamanhos de lote ideais. As trocas rápidas são realizadas por meio de uma metodologia de cinco etapas:
Etapa 1 - Observar e estudar a configuração das etapas / atividades do processo de mudança
Etapa 2 - Classificar as etapas / atividades em internas e externas. Etapas internas só podem acontecer quando a máquina / processo é interrompido - por exemplo, o carro está nas boxes. Etapas externas podem acontecer enquanto a máquina / processo está em execução - por exemplo, o carro está na pista.
Etapa 3 - Converter etapas / atividades de processos internos em externos
Etapa 4 - Procure maneiras de reduzir o tempo e o esforço necessários para as etapas internas restantes
Etapa 5 - Procure maneiras de reduzir o tempo e o esforço necessários para as etapas externas restantes
Kanban
Um Kanban é uma metodologia para estruturar o fluxo de materiais através de um processo de manufatura baseado em pull. É normalmente baseado em kanbans, ou cartões puxados, que sinalizam os processos upstream quais peças devem ser produzidas e em quais quantidades, com base nas necessidades downstream. Um sistema Kanban minimiza os níveis de estoque e desperdício de superprodução.
Kaizen
Kaizen é um termo japonês que pode ser traduzido como "Mudança para o bem". É o processo de fazer continuamente melhorias incrementais, muitas vezes diárias, nos processos, alistando as perspectivas dos funcionários de nível de linha para aproveitar sua criatividade e engenhosidade. Kaizen pode ser feito ao vivo no chão de fábrica conforme as oportunidades são identificadas, ou em eventos de sala de conferências para oportunidades multifuncionais. Uma equipe Kaizen frequentemente empregará o ciclo PDCA.
Correção de erros (Poka-Yoke)
Uma maneira de eliminar o desperdício é projetar processos e ferramentas de forma a impossibilitar a conclusão incorreta da tarefa. Pense em um plugue elétrico de três pinos padrão dos EUA. Devido aos dois recursos retangulares paralelos e o único arredondado deslocado entre eles, não é possível conectá-lo a uma tomada incorretamente. Só se encaixa de uma maneira. Ao garantir que as tarefas não sejam realizadas incorretamente, a qualidade é incorporada e o desperdício é eliminado na estação de trabalho fornecida, bem como em qualquer estação de trabalho posterior no processo, onde o impacto do defeito seria ampliado.
Trabalho padrão
No lean, as etapas para realizar uma determinada tarefa de atividade são codificadas em trabalho padrão. O Trabalho Padrão é essencialmente a documentação do método atualmente mais conhecido para realizar uma tarefa. "Mais conhecido" porque, em um sistema de melhoria contínua, os trabalhadores estão sempre em alerta para maneiras cada vez melhores de fazer seu trabalho. Quaisquer melhorias são incorporadas à documentação de trabalho padrão e todos os trabalhadores são então treinados nos métodos mais recentes.
Para obter mais informações sobre Lean e Seis Sigma, confira nosso terceiro capítulo da série, “Princípios e ferramentas Seis Sigma,” em breve .
Quem somos no CMTC
CMTC oferece assistência técnica, desenvolvimento de força de trabalho e serviços de consultoria para fabricantes de pequeno e médio porte (SMMs) em toda a Califórnia para ajudar os SMMs a aumentar sua produtividade e competitividade global.
Para obter mais informações sobre o CMTC, visite nosso website em www.cmtc.com ou entre em contato pelo telefone 310-263-3060.
Tecnologia industrial
- Comparando Six Sigma e manufatura enxuta
- Seja lubrificado, confiável e magro
- Lubrificada, confiável e enxuta
- Operações de Torno e Ferramentas de Corte de Torno
- O que é aprimorar? - Definição, processo e ferramentas
- O que é usinagem de alumínio? - Ferramentas e operações
- Tipos de operações de torno e ferramentas de corte
- Operação de Usinagem e Tipos de Ferramentas de Usinagem
- As principais ferramentas de manufatura enxuta que os fabricantes de D2C precisam
- O que é Lean Digital e como integrá-lo?