Laminado de amortecimento
Antecedentes
O plástico bolha é o nome comercial de um material de embalagem que consiste em duas folhas de plástico laminadas juntas de forma a reter as bolhas de ar em pequenos bolsos uniformes. Este conjunto de folha de plástico é usado como uma almofada flexível para proteger objetos frágeis durante o armazenamento ou transporte. O nome Bubble wrap é registrado pela Sealed Air Corporation de Saddle Brook, New Jersey; no entanto, o nome se tornou sinônimo do próprio material de embalagem. Materiais semelhantes são conhecidos na indústria como laminados de amortecimento.
A necessidade de um material de embalagem protetor e eficiente é reconhecida há muito tempo. Originalmente, papel picado e trapos eram usados para esse propósito. Outros materiais que têm sido usados historicamente incluem mica pulverizada e papelão ondulado. Conforme a tecnologia dos plásticos amadureceu nas décadas de 1950 e 1960, novos e aprimorados materiais de embalagem foram desenvolvidos. Contas de espuma feitas de plástico de poliestireno são um exemplo popular de material de embalagem de plástico; estes são mais comumente conhecidos como amendoim de isopor. Outra inovação baseada na tecnologia do plástico são os laminados de amortecimento, um material de embalagem que depende do ar para amortecer e proteger objetos altamente frágeis. O primeiro uso desses laminados remonta ao início dos anos 1970, quando os métodos de processamento de plásticos se tornaram cada vez mais sofisticados, permitindo uma fabricação rápida e barata. Hoje, eles são produzidos por diversas empresas, tanto nos Estados Unidos quanto no exterior. Embora uma variedade de métodos de fabricação sejam usados, o processo básico envolve bolhas de ar entre duas folhas laminadas de plástico.
Matérias-primas
Resina plástica
O laminado de amortecimento é feito principalmente de filme plástico ou folha fina formada a partir de resinas como polietileno e polipropileno. Essas resinas são amplamente utilizadas porque têm um bom desempenho e são relativamente baratas. Eles podem ser moldados em filmes fortes e flexíveis, que têm a capacidade de reter o ar sem vazar. Além disso, essas resinas são materiais termoplásticos, o que significa que podem ser facilmente fundidos e moldados. Esta é uma propriedade importante, pois as folhas de plástico podem ser reaquecidas durante o processamento. Diferentes tipos de resinas podem ser usados para fazer as folhas superior e inferior para dar ao laminado de amortecimento propriedades especiais. Por exemplo, uma camada pode ser feita com um material mais rígido para dar ao produto final uma maior rigidez.
Outros aditivos
Os filmes de polipropileno ou polietileno são formados com uma variedade de aditivos misturados com os polímeros de base para modificar suas propriedades e facilitar o processamento. Esses aditivos incluem lubrificantes e plastificantes que controlam a flexibilidade da mistura de resina; absorvedores de luz ultravioleta, estabilizadores de calor e antioxidantes que inibem diferentes tipos de degradação; e agentes de acoplamento e modificadores de força que melhoram a ligação entre o polímero e o enchimento. Além disso, agentes antiestáticos são adicionados para reduzir o acúmulo de eletricidade estática e biocidas podem ser incluídos para inibir o crescimento microbiano.
O processo de fabricação
O laminado de amortecimento é fabricado em um processo que consiste em três etapas principais:
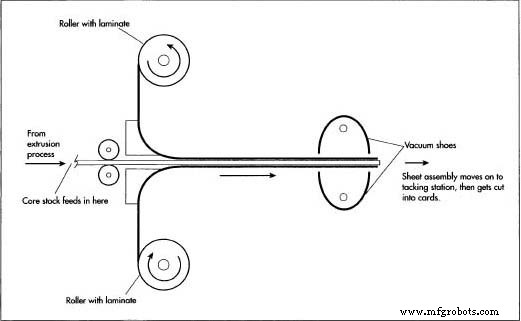
Composição de plástico e extrusão de folha
- 1 A resina plástica que foi composta de acordo com as especificações do fabricante é adquirida a granel de um fornecedor. Neste processo de composição, a resina de polietileno é aquecida e misturada com os aditivos descritos acima. Esta mistura é então fundida e formada em pequenos grânulos de 0,125 pol. (0,3175 cm) de diâmetro. No início do processo de fabricação, esses pellets são introduzidos em uma máquina de moldagem, conhecida como extrusora. Em uma extremidade da extrusora está uma tremonha na qual os pellets são despejados. Este funil alimenta os pellets em um barril longo aquecido. Este cano está equipado com um mecanismo de parafuso, que empurra o plástico para a frente. Na outra extremidade do cilindro está uma matriz de chapa de aço inoxidável que pode produzir chapas de até 10 pés (3 m) de largura.
- 2 A resina derrete à medida que se move ao longo do cilindro aquecido e, quando chega ao fim, pode ser facilmente forçada para fora pela abertura do molde. À medida que a resina fundida é comprimida através da matriz, ela é moldada em uma folha que é então processada posteriormente. Dependendo do processo, a folha pode ser laminada em outra camada imediatamente enquanto ainda está quente ou pode ser resfriada e laminada posteriormente. Em ambos os casos, após ser extrudada, a folha passa por uma série de rolos de aço inoxidável, conhecidos como finalizador de três rolos ou pilha de três rolos. Esses rolos têm 10-16 pol. (25,4-41 cm) de diâmetro e são resfriados internamente com água. Conforme a folha de plástico sai da matriz, ela entra no nip, o ponto onde os dois rolos superiores se encontram. A folha é puxada pelo movimento dos rolos e passada pelos rolos superior, central e inferior. Esses rolos resfriam a folha enquanto a ajudam a manter o tamanho e a forma corretos. Depois de passar pela pilha de três rolos, a folha entra em outra série de rolos conhecidos como rolos de puxar, que arrastam a folha pelo resto do processamento.
Laminação
- 3 Laminação é o processo usado para selar as duas folhas juntas de tal forma
Laminação é o processo usado para selar as duas folhas juntas de forma a reter as bolhas de ar. que retém bolhas de ar. A colocação uniforme dessas bolhas na face da folha pode ser conseguida esticando ou perfurando a folha de substrato em um padrão designado. Essas deformações uniformemente colocadas na folha reterão o ar e formarão bolsas individuais. O processo de deformar a folha de substrato requer calor para amolecer o plástico. Conforme observado, esta etapa pode ser realizada imediatamente após a extrusão enquanto a folha ainda está quente ou a folha pode ser reaquecida e moldada posteriormente. As bolhas podem então ser moldadas na folha amolecida, expondo-a a uma superfície de formação. Esta superfície pode ser um rolo ou uma placa com saliências na forma e distribuição desejadas. Quando a folha fundida é colocada em contato com a superfície de formação, o plástico é moldado no padrão desejado.
- 4 Um método de criação dessas bolsas de ar usa uma correia giratória como superfície de formação. Este cinto tem vários orifícios espalhados por ele. Conforme a folha de substrato se move ao longo da correia, a sucção é aplicada de uma fonte de vácuo aos orifícios da correia. O diferencial de pressão do ar faz com que o plástico se estique para os orifícios da correia, criando uma série de bolsas. Outro método emprega uma placa de moldagem como superfície de formação. A folha de plástico é movida para o lugar abaixo desta placa, através da qual o vácuo é puxado. A sucção faz com que a folha se adapte às saliências na placa do molde e produz uma folha moldada com a superfície irregular desejada. Um terceiro método usa um cilindro de moldagem rotativo para formar as bolsas de ar no plástico.
- 5 Após as bolsas de ar terem sido formadas por um dos métodos descritos acima, a folha de substrato e uma segunda folha são alimentadas juntas através de um conjunto de rolos de laminação. Pelo menos uma das folhas deve estar na temperatura adequada para garantir que a colagem ocorrerá. A pressão e o calor selam as folhas e as bolhas de ar permanecem presas.
Operações especiais
- 6 Após a finalização da laminação, as folhas são resfriadas, se necessário, por sistemas de ar aberto ou forçado. O ar pode ser soprado por cima e por baixo da folha. O resfriamento com água às vezes é feito, mas isso requer tempo extra para a secagem e pode causar problemas de limpeza. Dependendo do tipo de laminado de amortecimento que está sendo feito, outro processamento especial pode ser necessário. Por exemplo, alguns tipos de laminado de amortecimento são tratados com um revestimento adesivo em um dos lados. Outros são formados em envelopes para conter pequenos objetos frágeis. Dependendo do processamento envolvido, essas operações adicionais
pode ser executado antes ou depois do processo de laminação.
Operações de acabamento
- 7 Após a conclusão do laminado de amortecimento, o material em folha é cortado no tamanho apropriado. Isso pode ser feito como parte do processamento primário ou a embalagem não cortada pode ser armazenada em rolos grandes e cortada no tamanho certo mais tarde. Este processo de corte é conhecido como corte e é realizado com facas especiais que podem cortar as espessas camadas de plástico. O laminado pode ser embalado e vendido em rolos ou em folha.
Subprodutos / resíduos
O principal resíduo da fabricação de laminados de amortecimento é a resina plástica. A resina que está contaminada, superaquecida ou estragada deve ser descartada. No entanto, as folhas que falham nas verificações de qualidade por motivos relacionados a problemas físicos de moldagem podem ser retrabalhadas. Esse processo de reciclagem é conhecido como reafiação e trituração das folhas, refusão e reextrusão como novas folhas. Para garantir que o plástico atenda às especificações físicas, o material reciclado pode ser misturado com resina virgem. Isso pode ser feito sem perda de qualidade devido à natureza termoplástica do polipropileno.
Controle de qualidade
Tal como acontece com outros processos de fabricação de plástico, existem várias áreas-chave que devem ser controladas de perto para garantir que um produto de qualidade seja produzido. Durante o processo de composição, a resina e os aditivos devem ser adicionados com cuidado para garantir que os componentes da fórmula sejam misturados nas proporções adequadas. A resina acabada pode ser analisada para garantir que suas propriedades químicas e físicas atendam às especificações antes do início das operações de extrusão da folha. No início do processo de extrusão, uma pequena quantidade pode ser liberada através do cilindro da extrusora. Este processo de purga limpa o cilindro e revela quaisquer problemas com os sistemas de moldagem.
Durante a extrusão, é fundamental que a resina seja mantida na temperatura adequada. A taxa de fluxo do polímero variará de acordo com seu peso molecular e temperatura. Se a temperatura estiver muito baixa, a resina não se moverá pelo molde corretamente. Se a temperatura for muito alta, o polímero pode sofrer degradação térmica. O superaquecimento pode causar alterações químicas na resina, tornando-a inutilizável. As interações químicas indesejadas também podem afetar a qualidade das folhas de plástico durante o processo de extrusão. Um problema é a oxidação, uma reação com o ar que pode afetar negativamente o plástico. Da mesma forma, a interação com a umidade afeta a qualidade do plástico. Se houver pouca umidade, certas misturas de plásticos podem se tornar muito frágeis.
Após a conclusão do processo de extrusão, a extrusora deve ser devidamente limpa. É necessária uma limpeza completa antes de trabalhar com uma resina diferente, pois traços da resina usada anteriormente podem contaminar o novo lote. A limpeza da matriz é melhor feita enquanto a máquina ainda está quente e a resina que sobrou pode ser facilmente removida.
Outros fatores também devem ser monitorados. Por exemplo, em certos métodos de fabricação, é importante que as folhas de plástico superior e inferior respondam ao calor de forma diferente, de modo que durante o processo de laminação uma folha distorce, mas a outra não. Para este tipo de operação, é fundamental que a distorção por calor das duas folhas difira em pelo menos 77 ° F (25 ° C) ou ocorrerão problemas durante a laminação.
Após a conclusão do laminado de amortecimento, as amostras podem ser avaliadas para garantir que as folhas atendam às especificações de resistência, ponto de estouro da bolha e outros critérios.
O Futuro
As melhorias na tecnologia de plásticos continuam ocorrendo em um ritmo rápido. É provável que esses avanços produzam compostos plásticos aprimorados que são mais fáceis de processar, fornecem melhor capacidade de amortecimento e são biodegradáveis. Esta última qualidade é de particular importância considerando que o material de embalagem é um produto descartável e é usado em quantidades consideráveis. O laminado de amortecimento feito de plástico, que poderia quebrar com segurança sem impactar negativamente o meio ambiente, seria um grande trunfo para a indústria. Embora as melhorias nos equipamentos usados no processo de fabricação continuem a ser feitas, elas podem demorar para chegar ao mercado porque a substituição das máquinas existentes pode ser proibitivamente cara. Um novo método de fabricação contorna a necessidade de equipamentos de conformação caros. Em vez disso, este método usa uma folha de substrato de plástico como um padrão para formar as bolhas sem equipamento de moldagem caro. Neste processo, uma folha de plástico fina é primeiro perfurada no padrão de bolha desejado. Esta camada é laminada a uma folha de substrato e a combinação é então passada por rolos de compressão aquecidos. Vácuo ou pressão de gás é aplicado para puxar o filme através das perfurações no substrato. Este processo cria bolhas sem o uso de uma superfície de formação. Resta saber se este ou outros novos métodos de fabricação serão adotados pela indústria no futuro.
Processo de manufatura