Azulejo de cerâmica
Antecedentes
Ladrilhos de parede e piso usados para decoração de interiores e exteriores pertencem a uma classe de cerâmica conhecida como loiças brancas. A produção de azulejos remonta aos tempos e povos antigos, incluindo os egípcios, os babilônios e os assírios. Por exemplo, a pirâmide de degraus do Faraó Djoser, construída no antigo Egito por volta de 2600 a.C. , continha ladrilhos vidrados coloridos. Mais tarde, a telha cerâmica foi fabricada em praticamente todos os principais países europeus e nos Estados Unidos. No início do século XX, a telha era fabricada em escala industrial. A invenção do forno túnel por volta de 1910 aumentou a automação da fabricação de telhas. Hoje, a fabricação de ladrilhos é altamente automatizada.
O American National Standards Institute separa os ladrilhos em várias classificações. O ladrilho de mosaico cerâmico pode ser porcelana ou de composição de argila natural de tamanho inferior a 39 cm2 (6 pol.2). O ladrilho decorativo é um ladrilho envidraçado com um corpo fino utilizado para a decoração de interiores de paredes residenciais. O ladrilho para pavimentação é porcelana esmaltada ou não esmaltada ou ladrilho de argila natural de tamanho 39 cm2 (6 pol.2) ou mais. Ladrilho de porcelana é um ladrilho de mosaico cerâmico ou ladrilho de pavimentação feito por um determinado método denominado prensagem a seco. Os ladrilhos de pedreira são ladrilhos vidrados ou não do mesmo tamanho que ladrilhos de pavimentação, mas feitos por um método de formação diferente.
Europa, América Latina e Extremo Oriente são os maiores produtores de telhas, com a Itália liderando com 16,6 milhões de pés 2 / dia em 1989. Depois da Itália (com 24,6% do mercado mundial) está a Espanha (12,6%), Brasil e Alemanha (ambos com 11,2%) e Estados Unidos (4,5%). O mercado total de ladrilhos para pisos e paredes em 1990, de acordo com uma estimativa, era de US $ 2,4 bilhões.
Os Estados Unidos têm aproximadamente 100 fábricas que fabricam ladrilhos de cerâmica, que despacharam cerca de 507 milhões de pés 2 em 1990, de acordo com o Departamento de Comércio dos EUA. As importações dos EUA, em volume, responderam por aproximadamente 60% do consumo em 1990, avaliado em cerca de US $ 500 milhões. A Itália responde por quase metade de todas as importações, seguida pelo México e pela Espanha. As exportações dos EUA viram algum crescimento, de $ 12 milhões em 1988 para cerca de $ 20 milhões em 1990.
Como a indústria de ladrilhos é um mercado relativamente maduro e dependente da indústria de construção, o crescimento será lento. O Departamento de Comércio dos Estados Unidos estima um aumento de três a quatro por cento no consumo de ladrilhos nos próximos cinco anos. Outra análise econômica prevê que 494 milhões de pés 2 serão embarcados em 1992, um crescimento de cerca de 4% em relação ao ano anterior. Alguns fabricantes de ladrilhos são um pouco mais otimistas; uma pesquisa da American Ceramic Society mostrou um crescimento médio de cerca de 36% por fabricante nos próximos cinco anos.
Matérias-primas
As matérias-primas usadas para formar os azulejos consistem em minerais de argila extraídos da crosta terrestre, minerais naturais como o feldspato, que são usados para diminuir a temperatura de queima, e aditivos químicos necessários para o processo de moldagem. Os minerais são freqüentemente refinados ou beneficiados perto da mina antes do envio para a fábrica de cerâmica.
As matérias-primas devem ser pulverizadas e classificadas de acordo com o tamanho das partículas. Os britadores primários são usados para reduzir grandes pedaços de material. Tanto um britador de mandíbulas quanto um britador giratório são usados, que operam usando um britador horizontal
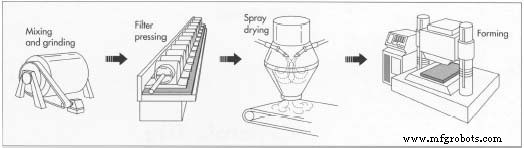
A britagem secundária reduz grumos menores a partículas. Moinhos de martelo ou muller são freqüentemente usados. Um moinho de muller usa rodas de aço em uma bandeja rotativa rasa, enquanto um moinho de martelo usa martelos de aço que se movem rapidamente para esmagar o material. Trituradores de rolo ou de cone também podem ser usados.
Uma terceira etapa de redução do tamanho de partícula pode ser necessária. Os tipos de moinhos de tombamento são usados em combinação com meios de moagem. Um dos tipos mais comuns de tais moinhos é o moinho de bolas, que consiste em grandes cilindros giratórios parcialmente preenchidos com mídia de moagem esférica.
As telas são usadas para separar as partículas em um intervalo de tamanho específico. Eles operam em uma posição inclinada e são vibrados mecanicamente ou eletromecanicamente para melhorar o fluxo do material. As telas são classificadas de acordo com o número da malha, que é o número de aberturas por polegada linear da superfície da tela. Quanto maior for o número da malha, menor será o tamanho da abertura.
Um esmalte é um material de vidro projetado para derreter na superfície do ladrilho durante o cozimento e que então adere à superfície do ladrilho durante o resfriamento. Os esmaltes são usados para fornecer resistência à umidade e decoração, pois podem ser coloridos ou produzir texturas especiais.
O processo de fabricação
Uma vez que as matérias-primas são processadas, uma série de etapas ocorrem para obter o produto acabado. Essas etapas incluem dosagem, mistura e trituração, secagem por pulverização, formação, secagem, polimento e queima. Muitas dessas etapas agora são realizadas por meio de equipamentos automatizados.
Em lote
- 1 Para muitos produtos cerâmicos, incluindo azulejos, a composição corporal é determinada pela quantidade e tipo de matéria-prima. As matérias-primas também determinam a cor do corpo do ladrilho, que pode ser vermelha ou branca, dependendo da quantidade de matéria-prima que contém ferro utilizada. Portanto, é importante misturar as quantidades certas para obter as propriedades desejadas. Portanto, são necessários cálculos de lote, que devem levar em consideração tanto as propriedades físicas quanto as composições químicas das matérias-primas. Uma vez que o peso apropriado de cada matéria-prima é determinado, as matérias-primas devem ser misturadas.
Mistura e trituração
- 2 Uma vez que os ingredientes são pesados, eles são adicionados juntos em um misturador de casca, misturador de fita ou misturador intensivo. Um misturador de casca consiste em dois cilindros unidos em um V, que gira para girar e misturar o material. Um misturador de fita usa palhetas helicoidais e um misturador intensivo usa arados giratórios rápidos. Esta etapa tritura ainda mais os ingredientes, resultando em um tamanho de partícula mais fino que melhora o processo de formação subsequente (consulte a etapa 4 abaixo).
Às vezes é necessário adicionar água para melhorar a mistura de um lote de vários ingredientes, bem como para obter uma moagem fina. Esse processo é chamado de moagem úmida e geralmente é realizado em um moinho de bolas. A mistura preenchida com água resultante é chamada de pasta ou deslizamento. A água é então removida da lama por meio de filtro prensado (que remove 40-50 por cento da umidade), seguido por moagem a seco.
Spray de secagem
- 3 Se a moagem úmida for usada primeiro, o excesso de água geralmente é removido por meio de secagem por spray. Isso envolve o bombeamento da pasta para um atomizador que consiste em um disco ou bico giratório rapidamente. As gotas da barbotina são secas à medida que são aquecidas por uma coluna de ar quente ascendente, formando pequenos grânulos de fluxo livre que resultam em um pó adequado para a formação.
Os corpos das telhas também podem ser preparados por moagem a seco seguida de granulação. A granulação utiliza uma máquina na qual a mistura do material previamente moído a seco é misturada com água para formar as partículas em grânulos, que novamente formam um pó pronto para a conformação.
Formação
- 4 A maioria dos ladrilhos é formada por prensagem a seco. Neste método, o pó de fluxo livre - contendo aglutinante orgânico ou uma baixa porcentagem de umidade - flui de uma tremonha para a matriz de formação. O material é comprimido em uma cavidade de aço por êmbolos de aço e então ejetado pelo êmbolo inferior. Prensas automatizadas são usadas com pressões operacionais de até 2.500 toneladas.
Vários outros métodos também são usados quando o corpo do ladrilho está em uma forma mais úmida e mais moldável. A extrusão mais puncionamento é usada para produzir ladrilhos de formato irregular e ladrilhos mais finos de forma mais rápida e econômica. Isso envolve compactar uma massa plástica em um cilindro de alta pressão e forçar o material a fluir para fora do cilindro em pequenos pacotes. Essas lesmas são então puncionadas em uma ou mais placas usando prensas puncionadeiras hidráulicas ou pneumáticas.
A prensagem de aríete é frequentemente usada para ladrilhos com muitos perfis. Com este método, os pedaços extrudados do corpo do ladrilho são pressionados entre as duas metades de um molde rígido ou poroso montado em uma prensa hidráulica. A parte formada é removida aplicando primeiro vácuo à metade superior do molde para liberar a parte da metade inferior, seguido de forçar o ar através da metade superior para liberar a parte superior. O excesso de material deve ser removido da peça e acabamento adicional pode ser necessário.
Outro processo, chamado de envidraçamento de pressão, foi desenvolvido recentemente. Este processo combina envidraçamento e modelagem simultaneamente pressionando o esmalte (na forma de pó seco por pulverização) diretamente na matriz preenchida com o pó do corpo do ladrilho. As vantagens incluem a eliminação das linhas de envidraçamento, bem como dos resíduos de envidraçamento (chamados de lodo) que são produzidos pelo método convencional.
Secagem
- 5 A telha cerâmica geralmente deve ser seca (com alta umidade relativa) após a formação, especialmente se um método úmido for usado. A secagem, que pode levar vários dias, remove a água em uma taxa lenta o suficiente para evitar rachaduras por retração. Secadores contínuos ou em túnel são usados para serem aquecidos com gás ou óleo, lâmpadas infravermelhas ou energia de micro-ondas. A secagem por infravermelho é mais adequada para ladrilhos finos, enquanto a secagem por micro-ondas funciona melhor para ladrilhos mais grossos. Outro método, a secagem por impulso, usa pulsos de ar quente fluindo na direção transversal em vez de continuamente na direção do fluxo de material.
Vidraças
- 6 Para preparar o esmalte, métodos semelhantes são usados para o corpo do ladrilho. Depois que uma formulação em lote é calculada, as matérias-primas são pesadas, misturadas e secas ou moídas a úmido. Os esmaltes fresados são então aplicados usando um dos muitos métodos disponíveis. No esmalte ou disco centrífugo, o esmalte é alimentado por meio de um disco giratório que arremessa ou joga o esmalte no azulejo. No método sino / cascata, um fluxo de esmalte cai sobre o ladrilho ao passar por uma esteira rolante embaixo dela. Às vezes, o esmalte é simplesmente pulverizado. Para múltiplas aplicações de esmalte, é usada a impressão em tela, embaixo ou entre os ladrilhos que foram esmaltados úmidos. Neste processo, o esmalte é forçado através de uma tela por um rodo de borracha ou outro dispositivo.
Vidros secos também estão sendo usados. Isso envolve a aplicação de pós, fritas trituradas (materiais de vidro), e esmaltes granulados em uma superfície de ladrilho vitrificado úmido. Após a queima, as partículas de esmalte se fundem para produzir uma superfície como o granito.
Demissão
- 7 Após a vitrificação, o ladrilho deve ser aquecido intensamente para fortalecê-lo e dar-lhe a porosidade desejada. Dois tipos de fornos, ou
Após a formação, a lima é seca lentamente (por vários dias) e em alta umidade, para evitar rachaduras e encolhimento . Em seguida, o esmalte é aplicado e, em seguida, o ladrilho é queimado em uma fornalha ou forno. Embora alguns tipos de ladrilhos exijam um processo de queima de duas etapas, os ladrilhos fresados a úmido são queimados apenas uma vez, a temperaturas de 2.000 graus Fahrenheit ou mais. Após o disparo, o ladrilho é embalado e despachado. fornos, são usados para a cozedura de azulejos. Ladrilho de parede, ou ladrilho que é preparado por moagem a seco em vez de moagem úmida (consulte # 2 e # 3 acima), geralmente requer um processo de duas etapas. Nesse processo, o ladrilho passa por uma queima de baixa temperatura, chamada de queima de bisque, antes da vitrificação. Esta etapa remove os voláteis do material e a maior parte ou todo o encolhimento. O corpo e o esmalte são então queimados juntos em um processo chamado de queima de glost. Ambos os processos de queima ocorrem em um túnel ou forno contínuo, que consiste em uma câmara pela qual a mercadoria é movimentada lentamente por uma esteira sobre mantas refratárias - prateleiras construídas com materiais resistentes a altas temperaturas - ou em recipientes chamados de flechas. A queima em um forno de túnel pode levar de dois a três dias, com temperaturas de queima em torno de 2.372 graus Fahrenheit (1.300 graus Celsius).
Para ladrilhos que requerem apenas uma única queima - geralmente ladrilhos que são preparados por moagem úmida - geralmente são usados fornos de rolos. Esses fornos movem as mercadorias em uma esteira rolante e não requerem móveis de forno, como mantas ou flechas. Os tempos de queima em fornos de rolos podem ser tão baixos quanto 60 minutos, com temperaturas de queima em torno de 2.102 graus Fahrenheit (1.150 graus Celsius) ou mais.
- 8 Depois de queimar e testar, o ladrilho está pronto para ser embalado e despachado.
Subprodutos
Uma variedade de poluentes é gerada durante as várias etapas de fabricação; essas emissões devem ser controladas para atender aos padrões de controle do ar. Entre os poluentes produzidos na fabricação de telhas estão compostos de flúor e chumbo, que são produzidos durante a queima e envidraçamento. Os compostos de chumbo foram significativamente reduzidos com o recente desenvolvimento de esmaltes sem ou com baixo teor de chumbo. As emissões de flúor podem ser controladas com purificadores, dispositivos que basicamente borrifam os gases com água para remover poluentes prejudiciais. Eles também podem ser controlados com processos secos, como filtros de tecido revestidos com cal. Esta cal pode então ser reciclada como matéria-prima para futuros ladrilhos.
A indústria de ladrilhos também está desenvolvendo processos para reciclar águas residuais e lamas produzidas durante a moagem, laminação e secagem por spray. Algumas fábricas já reciclam o excesso de pó gerado durante a prensagem a seco, bem como o excesso de pulverização produzido durante a vitrificação. Resíduos de esmalte e ladrilhos rejeitados também são devolvidos ao processo de preparação da carroceria para reutilização.
Controle de qualidade
A maioria dos fabricantes de ladrilhos agora usa controle estatístico de processo (SPC) para cada etapa do processo de fabricação. Muitos também trabalham em estreita colaboração com seus fornecedores de matéria-prima para garantir que as especificações sejam atendidas antes do material ser usado. O controle estatístico do processo consiste em gráficos usados para monitorar vários parâmetros de processamento, como tamanho de partícula, tempo de moagem, temperatura e tempo de secagem, pressão de compactação, dimensões após a prensagem, densidade, temperatura e tempo de queima e semelhantes. Esses gráficos identificam problemas com o equipamento, condições fora das especificações e ajudam a melhorar os rendimentos antes que o produto final seja concluído.
O produto final deve atender a certas especificações relativas às propriedades físicas e químicas. Essas propriedades são determinadas por testes padrão estabelecidos pela American Society of Testing and Materials (ASTM). As propriedades medidas incluem resistência mecânica, resistência à abrasão, resistência química, absorção de água, estabilidade dimensional, resistência ao gelo e coeficiente linear de expansão térmica. Mais recentemente, a resistência ao deslizamento, que pode ser determinada medindo o coeficiente de atrito, tornou-se uma preocupação. No entanto, nenhum padrão foi ainda estabelecido porque outros fatores (como design e cuidado adequados do piso) podem tornar os resultados sem sentido.
O Futuro
Para manter o crescimento do mercado, os fabricantes de ladrilhos se concentrarão no desenvolvimento e promoção de novos produtos de ladrilhos, incluindo ladrilhos modulares ou revestidos, ladrilhos maiores, ladrilhos antideslizantes e resistentes à abrasão e ladrilhos com acabamento polido em granito ou mármore. Isso está sendo realizado por meio do desenvolvimento de diferentes formulações corporais, novos esmaltes e aplicações de esmaltes, e por equipamentos e técnicas de processamento novos e aprimorados. A automação continuará a desempenhar um papel importante em um esforço para aumentar a produção, reduzir custos e melhorar a qualidade. Além disso, as mudanças na tecnologia de produção devido a questões ambientais e de recursos energéticos continuarão.
Processo de manufatura