Combinar
Antecedentes
Uma colheitadeira é uma grande máquina agrícola autopropelida usada para colher safras de grãos como trigo, milho, soja, milo, colza e arroz. Como o próprio nome sugere, a colheitadeira desempenha duas, e às vezes mais, funções básicas de colheita:primeiro ela colhe (corta) a safra e, em seguida, a debulha, separando os grãos de grãos das coberturas de sementes e outros detritos ( palha). Algumas colheitadeiras também podem enfardar a palha que sobra após a debulha; as máquinas também podem ser equipadas para colher algodão.
As ceifeiras-debulhadoras são peças de equipamento muito grandes. O operador senta-se no topo da máquina em uma cabine alta com janelas amplas para uma boa visão. Uma carroceria longa e quadrada, coberta com um tanque graneleiro e uma rampa através da qual os grãos debulhados podem ser removidos, circula em enormes rodas dianteiras e volantes menores e mais estreitos. Um motor a diesel turboalimentado impulsiona a colheitadeira e fornece energia para a plataforma, o cilindro debulhador, o sistema de limpeza e as brocas que movem os grãos da plataforma através do cilindro debulhador para o tanque graneleiro e depois para um caminhão de espera.
À medida que uma colheitadeira avança ao longo das fileiras de grãos, seu componente frontal - a bobina, uma grande peça de metal hexagonal paralela ao solo - gira, varrendo os talos de grãos para dentro da máquina. Diferentes designs de bobinas são necessários para colher diferentes safras. Por exemplo, enquanto um carretel de trigo desvia os caules para uma barra de corte que os corta logo abaixo das cabeças dos grãos maduros, um carretel de milho tira as espigas dos caules, deixando-os achatados contra o solo. Hoje, os agricultores podem escolher entre muitos tipos e tamanhos diferentes de modelos de plataformas. A explicação abaixo descreve o progresso do trigo por meio de uma colheitadeira.
Uma vez dentro do corpo da colheitadeira, os talos são empurrados contra a barra de corte, um componente que se parece com um pente. Com os "dentes" do pente pegando os talos, um instrumento em forma de faca os corta próximo ao nível do solo. Os talos são então transportados para um elevador por meio de uma verruma. Grandes cilindros de metal, augurs apresentam projeções em forma de parafuso que prendem o grão para que ele possa ser transportado. O augur do talo, colocado paralelo ao solo, varre os talos cortados para o elevador - um par de rolos equipados com esteiras transportadoras que carregam o grão para cima no coração da colheitadeira, o cilindro de debulha. Este cilindro é um grande rolo com protuberâncias. Girando em alta velocidade sobre uma fenda em forma de meia lua (o côncavo), o cilindro separa os grãos das pontas dos caules.
Uma vez separados dos grãos, os talos são varridos pelas barras do cilindro debulhador, que os depositam na primeira de uma série de passadores de palha. São plataformas quadradas grandes, ligeiramente sobrepostas, que descem gradualmente em direção à parte traseira da colheitadeira. Vibrando levemente, o primeiro andador faz com que o canudo caia no segundo, e o segundo agita até que o canudo caia no terceiro e mais baixo, momento em que é jogado por uma rampa no solo ou, em uma enfardadeira, embalado em fardos. Ao contrário dos talos de grãos, os grãos são pequenos o suficiente para cair pelas fendas no côncavo e são presos na bandeja de grãos que fica abaixo dele. A bandeja de grãos vibra, sacudindo os grãos, o joio e algumas cabeças que passaram intactas pelo cilindro debulhador até formar um conjunto de peneiras vibratórias.
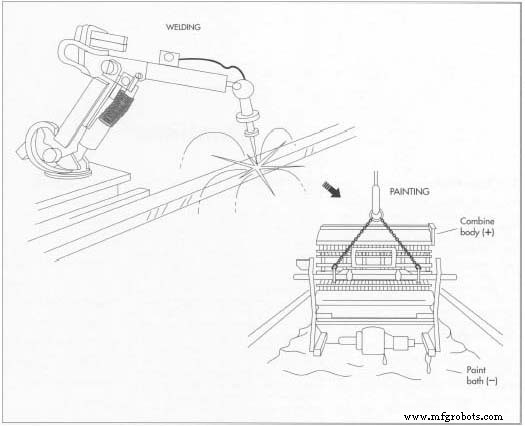
Depois que o corpo é construído, ele é preso a um transportador aéreo, que então o transporta para o banho de tinta. A pintura é feita eletrostaticamente - a pintura recebe uma carga oposta do corpo da colheitadeira. Essa técnica permite que a tinta alcance todas as partes expostas do metal, proporcionando uma superfície livre de corrosão.
As vibrações fazem com que os grãos caiam pelas peneiras, enquanto as cabeças não debulhadas ficam presas. Um ventilador adjacente às peneiras sopra ar sobre elas, fazendo com que o joio (que é muito leve) seja soprado para trás pela parte traseira da colheitadeira. Os cabeçotes não debulhados são então encaminhados, por meio de outra broca, para o elevador de rejeitos, que os transporta de volta ao cilindro debulhador. Enquanto isso, os grãos caem no áugure de grãos e são transportados para o elevador de grãos, que os deposita no tanque de grãos. Ainda outro áugure, o áugure de descarregamento, é inserido no tanque graneleiro, e o grão pode ser removido do tanque através dele.
A colheitadeira foi desenvolvida durante os anos 1800, quando muitos processos agrícolas estavam sendo automatizados. Já em 1826, inventores individuais e empresários produziram centenas de engenhocas para ajudar os fazendeiros na colheita de grãos. No entanto, essas primeiras máquinas desempenhavam apenas uma de duas funções importantes:eram ceifeiras, que cortavam os talos dos grãos, ou debulhadoras, que separavam os grãos do joio.
A primeira ceifeira foi projetada por um ministro escocês, Patrick Bell, em 1826. Das muitas outras desenvolvidas em meados de 1800, a máquina de maior sucesso foi criada por um americano, Robert McCormick, e aperfeiçoada por seu filho mais famoso, Cyrus. Robert McCormick trabalhou em vários designs de ceifeiras de 1809 até 1831, e Cyrus McCormick, continuando o trabalho de seu pai, vendeu o primeiro ceifeiro McCormick em 1839.
As debuladeiras, para separar e limpar os grãos dos grãos, foram montadas pela primeira vez no final dos anos 1700 e eram amplamente utilizadas na Inglaterra e na Escócia na década de 1830. Nas duas décadas seguintes, vários americanos inventaram a debulhadora. Os mais bem-sucedidos foram Hiram e John Pitts, irmãos que venderam a primeira debulhadora "Chicago Pitts" em 1852. Jerome Increase Case também produziu uma debulhadora duramente popular:fundada em 1844, a empresa que leva seu nome continua a prosperar até hoje.
A primeira máquina agrícola capaz de fazer o trabalho de ceifeira e debulhadora foi patenteada em 1828, embora o primeiro modelo só tenha sido vendido em 1838. Grande e pesada, a máquina exigia vinte cavalos para puxá-la. Por esse motivo, as colheitadeiras não eram usadas em grande número até o início do século XX, quando os refinamentos as tornaram mais fáceis de usar.
Hoje, colheitadeiras modernas são as máquinas mais complicadas produzidas em uma linha de montagem. Enquanto um passageiro automóvel é composta por 6.000 peças, uma ceifeira-debulhadora compreende mais de 17.000. Essa complexidade se reflete no preço:uma única colheitadeira pode custar até US $ 100.000. Hoje, existem dois grandes fabricantes de colheitadeiras nos Estados Unidos. Ambas as empresas, John Deere e J. I. Case, têm fábricas grandes e modernas que ficam próximas uma da outra ao longo do rio Mississippi em East Moline, Illinois, e em 1990, venderam cerca de 11.500 colheitadeiras nos Estados Unidos e Canadá.
Matérias-primas
A chapa de aço, principal matéria-prima usada na fabricação de colheitadeiras, é entregue à planta de fabricação em rolos maciços, de 48 polegadas (121,92 centímetros) de largura e pesando até 12.000 libras (5.448 quilos). Depois de desenrolados, os rolos são cortados em placas que são cortadas, perfuradas, moldadas e soldadas para formar o corpo da colheitadeira, os painéis externos e o tanque graneleiro. Barras de aço redondas e canais de aço ocos e quadrados também são cortados e perfurados para eixos, eixos de transmissão, brocas e estruturas de suporte. Subconjuntos complexos, como o motor e a transmissão, são construídos em outras fábricas da empresa ou adquiridos de empresas menores. Freqüentemente, um veículo de entrega transporta componentes para o ponto exato ao longo da linha de montagem onde as peças são necessárias. Após a montagem, a colheitadeira é pintada com tinta à base de água que chega à fábrica na forma de pó e é misturado com água altamente purificada.
O processo de fabricação
Cortando o aço em pedaços
- 1 A fabricação de uma colheitadeira começa com a entrega de grandes bobinas de chapa de aço para a loja de chapas. A bobina de aço é carregada em uma das várias máquinas que compõem a linha de corte sob medida na fábrica de chapas. Rolos controlados por computador puxam o aço da bobina, achatam-no e colocam-no na máquina de corte. O aço é cortado em blocos, formas retangulares básicas que mais tarde são soldadas para formar o corpo da colheitadeira e o tanque graneleiro montado no topo. Para máxima eficiência, a linha cut-to-length opera em programações de lote predeterminadas. As formas básicas de metal cortadas das bobinas de aço são usadas durante o dia ou semana em que são cortadas, portanto, não há armazenamento de componentes básicos.
- 2 A partir da linha cortada conforme o comprimento, os espaços em branco são movidos para a linha cortada conforme o comprimento. Em uma puncionadeira a laser, um laser industrial corta formas complexas e faz furos para eixos, tubulações e parafusos. Em seguida, a prensa exerce até 1.000 toneladas de pressão para dobrar o aço na forma final.
Soldando as peças formadas
- 3 Pequenos lotes de peças são movidos da oficina de chapas para a área de soldagem, onde as técnicas de fabricação celular são usadas para agilidade e controle de qualidade. Na manufatura celular, várias funções de manufatura são agrupadas em uma área para que as peças possam ser rapidamente passadas de uma operação para a próxima, e vários subcomponentes são carregados em um skid de transporte antes de serem enviados para a próxima etapa de montagem. Assim, todas as peças necessárias para montar um lote de componentes estão presentes quando o skid chega. Para aumentar ainda mais a eficiência, grande parte da soldagem de componentes de chapa de aço é feita por unidades poderosas controladas por computador. Elevadores hidráulicos posicionam corretamente os componentes que são soldados por robôs de um braço. Conforme os componentes menores da colheitadeira são montados, o corpo começa a tomar forma.
Ceifeiras-debulhadoras são veículos grandes, complexos e caros — uma ceifeira-debulhadora moderna contém cerca de 17.000 peças (um automóvel contém 6.000) e pode custar até US $ 100.000. Diferentes designs de bobinas permitem que as colheitadeiras executem funções diferentes. Na forma de uma estrutura simples, ele agora é preso a uma esteira transportadora da barra de carga superior que o transporta pelo restante do processo de produção.
Pintura
- 4 Depois que o corpo foi soldado, o transportador aéreo o transporta e o submerge no tanque de tinta, um enorme tanque de 48.000 galões (181.776 litros) cheio de tinta eletrostática. Como as colheitadeiras são usadas e armazenadas do lado de fora, sua tinta deve ser capaz de resistir aos efeitos nocivos da luz do sol e da umidade, e o processo eletrostático garante que isso acontecerá. Na pintura eletrostática, o corpo da colheitadeira de metal recebe uma carga elétrica positiva, enquanto a tinta à base de água recebe uma carga negativa. Como as cargas elétricas opostas são atraídas umas pelas outras, o corpo com carga positiva atrai a tinta com carga negativa, fazendo com que a tinta se ligue à combinação de forma firme e completa (apenas as juntas de borracha e outras partes não metálicas não são tocadas pela tinta).
- 5 Depois que o transportador levanta o corpo da colheitadeira do banho de tinta, ele o suspende sobre o tanque por alguns momentos para que o excesso de tinta possa pingar. O corpo é então movido para um forno de 363 graus Fahrenheit (182 graus Celsius), onde a tinta é cozida com um acabamento duro e resistente à ferrugem.
- 6 Após a pintura, o corpo da colheitadeira é transportado pela linha de montagem para que outros componentes principais possam ser instalados. Quando necessário, esses componentes também foram imersos no banho de tinta eletrostática. Depois que os eixos, cubos e pneus forem adicionados, a colheitadeira é removida do transportador aéreo e rebocada de uma estação para outra.
Soldando o tanque graneleiro
- 7 Depois do corpo da colheitadeira, a outra montagem estrutural significativa é o tanque graneleiro. Na área de montagem do tanque graneleiro, os trabalhadores qualificados usam um sistema complexo de posicionamento e soldagem para completar mais de 500 soldas separadas em duas sequências de 10-Y2 minutos. O equipamento automatizado de manuseio de chapas metálicas puxa chapas planas de patins recém-saídos da linha de corte sob medida na loja de chapas metálicas. Essas folhas são colocadas em uma enorme mesa de metal do tamanho de uma garagem para dois carros. Em seguida, os cilindros hidráulicos posicionam os painéis laterais enquanto os soldadores humanos lutam para proteger os cantos do tanque graneleiro com pontos de solda. Quando os soldadores humanos estão fora de perigo, os braços do robô entram em ação, fazendo centenas de soldas em poucos minutos.
Montagem final
- 8 Após a pintura do corpo e do tanque graneleiro, eles são levados para a linha de montagem final, onde são realizadas 22 operações de montagem diferentes. Os principais componentes, como o módulo do motor, são instalados, a fiação e as linhas hidráulicas são conectadas e todos os sistemas são testados. Óleo, anticongelante e gás são adicionados e o motor é ligado. Na parte externa, uma camada final de poliuretano transparente é aplicada na parte superior das superfícies largas e planas da cabine, tanque graneleiro e módulo do motor, e decalques são aplicados.
Controle de qualidade
Como uma colheitadeira é um implemento agrícola caro e é usada durante os dias críticos da colheita, cada unidade deve atender aos mais altos padrões de desempenho operacional. Falhas causadas por materiais ou mão de obra não podem ser toleradas. Portanto, o controle de qualidade começa com os fornecedores das matérias-primas e continua mesmo após a montagem final.
Hoje, os fabricantes de combinações testam aleatoriamente as amostras de entrada de chapas e barras para garantir que não existam deficiências no metal. Em cada etapa de fabricação, os trabalhadores estabelecem procedimentos para limitar a chance de defeitos causados por métodos de fabricação incorretos. Cada estação no processo de fabricação é responsável por entregar um componente sem defeitos na próxima estação. Essa filosofia de fabricação leva os funcionários individualmente a verificar se há defeitos em seu próprio trabalho.
O Futuro
Nos últimos anos, o projeto da colheitadeira mudou, dependendo menos de polias, correias e eixos de transmissão e mais de controles eletrônicos, atuadores solenóides e sistemas de energia hidráulica. Nos próximos anos, as melhorias no motor e na transmissão darão aos agricultores ainda mais potência e eficiência de combustível. Outra área de desenvolvimento está no cilindro debulhador. Um novo projeto em estudo agora apresenta duas gaiolas giratórias, uma dentro da outra, para limpar o grão. Tal projeto seria mais eficiente, permitindo que o corpo da colheitadeira fosse menor. Equipamentos de limpeza secundária e ventiladores para soprar a palha para longe dos grãos também podem ser eliminados. Esses esforços constantes para melhorar o design estão permitindo que os fabricantes de colheitadeiras ofereçam unidades com mais potência, maior capacidade e maior confiabilidade. Hoje, as colheitadeiras podem oferecer de 5.000 a 10.000 horas entre revisões do motor e 25 a 30 por cento a mais de potência em unidades com apenas 10 anos.
Processo de manufatura
- O que é VMC Machining?
- O molibdênio se combinará com outros elementos?
- Combinar
- ST:STM32H7 MCUs combinam desempenho dual-core com integração de recursos avançados
- Danaher, Cooper Industries para combinar negócios de ferramentas, formar nova empresa
- IoT e análises incorporadas se combinam para mostrar os efeitos das mudanças climáticas em nossos jardins
- Combine Business Intelligence e Process Mining para Tomada de Decisão Orientada por Dados
- Quando é apropriado usar o acabamento de grão de aço inoxidável?
- Como o tamanho e a direção do grão afetam as peças de chapa metálica
- O que é uma colheitadeira?