Vela de ignição
Antecedentes
O objetivo de uma vela de ignição é fornecer um local para uma faísca elétrica que seja quente o suficiente para inflamar a mistura ar / combustível dentro da câmara de combustão de um motor de combustão interna. Isso é feito por uma corrente de alta tensão formando um arco através de uma lacuna na vela de ignição.
Uma vela de ignição é feita de um eletrodo central, um isolador, um invólucro ou concha de metal e um eletrodo lateral (também chamado de eletrodo de aterramento). O eletrodo central é um fio de metal grosso que fica longitudinalmente dentro do plugue e conduz eletricidade do cabo de ignição preso a uma extremidade do plugue até a lacuna do eletrodo na outra extremidade. O isolador é um revestimento de cerâmica que envolve grande parte do eletrodo central; ambas as porções superior e inferior do eletrodo central permanecem expostas. A carcaça ou concha de metal é uma concha em forma de hexágono com roscas, que permite que a vela de ignição seja instalada em um soquete roscado na cabeça do cilindro do motor. O eletrodo lateral é um fio curto e grosso feito de liga de níquel que é conectado ao invólucro de metal e se estende em direção ao eletrodo central. As pontas dos eletrodos lateral e central estão a cerca de 0,020 - 0,080 polegada de distância uma da outra (dependendo do tipo de motor), criando uma lacuna para a faísca saltar.
As várias centenas de tipos de velas de ignição disponíveis cobrem uma variedade de veículos de transporte, trabalho e lazer movidos a motor de combustão interna. As velas de ignição são usadas em automóveis, caminhões, ônibus, tratores, barcos (internos e externos), aeronaves, motocicletas, scooters, motores industriais e de campo de petróleo, queimadores de óleo, cortadores de grama e motosserras. Os ignitores de turbina, um tipo de vela de ignição, ajudam a alimentar os motores a jato na maioria das grandes aeronaves comerciais hoje, enquanto as velas de incandescência são usadas em aplicações de motores a diesel.
A faixa de calor ou classificação de uma vela de ignição se refere às suas características térmicas. É a medida de quanto tempo leva para que o calor seja removido da ponta do plugue, a ponta de ignição, e transferido para o cabeçote do motor. No momento da faísca, se a temperatura da ponta do plugue estiver muito baixa, carbono, óleo e produtos de combustão podem fazer com que o plugue "suja" ou falhe. Se a temperatura da ponta do plugue estiver muito alta, ocorre pré-ignição, o eletrodo central queima e o pistão pode ser danificado. A faixa de aquecimento é alterada alterando-se o comprimento do nariz do isolador, dependendo do tipo de motor, da carga do motor, do tipo de combustível e de outros fatores. Para um plug "quente", um isolador com um bico cônico longo é usado; para um plugue "frio", um isolador de ponta curta é usado.
As velas de ignição estão sob constante ataque químico, térmico, físico e elétrico por gases corrosivos a 4.500 graus Fahrenheit, pressões de esmagamento de 2.000 libras por polegada quadrada (PSI) e descargas elétricas de até 18.000 volts. Esse ataque implacável sob o capô de um automóvel típico ocorre dezenas de vezes por segundo e mais de um milhão de vezes em um dia inteiro de condução.
História
A vela de ignição evoluiu com o motor de combustão interna, mas a primeira demonstração do uso de uma faísca elétrica para acender uma mistura ar-combustível foi em 1777. Naquele ano, Alessandro Volta carregou uma pistola de brinquedo com uma mistura de gás do pântano e ar , arrolhou o focinho e acendeu a carga com uma faísca de uma jarra de Ley den.
Em 1860, o engenheiro francês Jean Lenoir criou o que mais se assemelha à vela de ignição
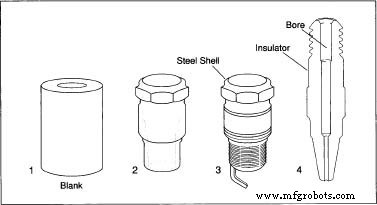
No início dos anos 1900, Robert e Frank Stranahan, irmãos e sócios em uma empresa de importação de peças automotivas, decidiram produzir uma vela de ignição mais eficiente e durável. Eles adicionaram juntas entre a carcaça de metal e a porcelana isolador, facilitou a fabricação e reduziu a possibilidade de vazamento de gás pelas juntas. Em 1909, Robert Stranahan vendeu a vela para um fabricante de automóveis e entrou no ramo de fabricação de velas, conquistando o mercado na época.
A indústria explodiu com o início da era do automóvel. Eventualmente, variações nos sistemas de ignição, combustível e requisitos de desempenho colocaram novas demandas nas velas de ignição. Embora o design básico e a função do plugue tenham mudado pouco desde seu início, uma variedade e um número impressionante de eletrodos e materiais isolantes foram testados.
Matérias-primas
Os eletrodos em uma vela de ignição normalmente consistem em ligas de alto teor de níquel, enquanto o isolador é geralmente feito de cerâmica de óxido de alumínio e a casca é feita de fio de aço.
A seleção de materiais tanto para os eletrodos quanto para o isolador consumiu muito tempo e custo de pesquisa e desenvolvimento. Um grande fabricante de velas de ignição afirma ter testado 2.000 materiais de eletrodo e mais de 25.000 combinações de isoladores. Conforme os eletrodos sofrem erosão, a lacuna entre eles aumenta e é necessária mais voltagem do que o sistema de ignição pode fornecer para acioná-los. Ligas com alto teor de níquel foram aprimoradas e eletrodos mais grossos foram usados para reduzir a perda de desempenho do motor. Além disso, metais preciosos e exóticos são cada vez mais usados pelos fabricantes. Muitos plugues modernos apresentam prata, ouro, e platina nos eletrodos, para não mencionar os eletrodos centrais com núcleos de cobre. A prata tem condutividade térmica superior em relação a outros metais do eletrodo, enquanto a platina tem excelente resistência à corrosão.
O material isolante também pode ter um efeito dramático no desempenho da vela de ignição. A pesquisa continua para encontrar um material que reduza melhor o flashover, ou vazamento elétrico, do terminal do plugue até a carcaça. O uso inovador da Sillimanita, um material que se encontra no estado natural e também produzido artificialmente, foi sucedido pelo uso de cerâmicas de óxido de alumínio mais resistentes ao calor, cuja composição é o segredo dos fabricantes.
O processo de um dos principais fabricantes para fazer o isolador envolve lotes de moagem úmida de pellets de cerâmica em moinhos de bolas, sob condições cuidadosamente controladas. O tamanho e a forma definidos das pelotas produzem a substância de fluxo livre necessária para fazer um isolante de qualidade. Os pellets são obtidos por meio de uma operação de secagem por spray-drying rígida que retira a água da mistura cerâmica, até que esteja pronta para o vazamento nos moldes.
O processo de fabricação
Cada elemento principal da vela de ignição - o eletrodo central, o eletrodo lateral, o isolador e a casca - é fabricado em um processo de montagem em linha contínuo. Em seguida, o eletrodo lateral é conectado à casca e o eletrodo central é colocado dentro do isolador. Finalmente, as peças principais são montadas em uma única unidade.
Shell
- 1 As cápsulas das velas de ignição inteiras podem ser feitas de várias maneiras. Quando o fio de aço sólido é usado, o aço pode ser conformado a frio, por meio do qual bobinas de aço são formadas e moldadas em temperaturas relativamente baixas. Ou, o aço pode ser extrudado, um processo no qual o metal é aquecido e então empurrado através de um orifício moldado (chamado de matriz) para produzir a forma oca adequada. Os invólucros também podem ser feitos de barras de aço que são alimentadas em parafusadeiras automáticas. Essas máquinas formam completamente a casca, fazem o furo através dela e a fresam - um processo que melhora o acabamento do furo feito e torna o tamanho do furo mais exato.
- 2 As cascas formadas ou extrudadas, chamadas de espaços em branco até que sejam moldados em suas formas finais - exigem que operações secundárias sejam realizadas neles, como usinagem e recartilhamento. O recartilhamento de uma peça em bruto envolve passá-la por rolos rígidos e padronizados, que formam uma série de saliências na parte externa da peça em bruto. Da mesma forma, a usinagem - em que máquinas-ferramentas cortam o exterior da casca da casca - gera formas e contornos do lado de fora da casca. As conchas agora estão em sua forma final e completas, exceto para roscas e eletrodos laterais.
Eletrodo lateral
- 3 O eletrodo lateral é feito de um fio de liga de níquel, que é alimentado a partir de rolos em um soldador elétrico, endireitado e soldado à casca. Em seguida, é cortado no comprimento adequado. Finalmente, o eletrodo lateral recebe uma dobra parcial; ele recebe sua dobra final depois que o resto do conjunto do plugue estiver no lugar.
- 4 Os fios são então enrolados nas cascas. Agora completos, os invólucros geralmente recebem um acabamento prateado permanente e protetor por um processo eletrolítico. Nesse processo, a casca é colocada em uma solução de ácidos, sais ou álcalis, e uma corrente elétrica passa pela solução. O resultado é um fino revestimento de metal aplicado uniformemente sobre a casca.
Isolador
- 5 Isoladores são fornecidos no estoque. O material cerâmico para o isolador na forma líquida é primeiro colocado em moldes de borracha. As prensas especiais aplicam automaticamente pressão hidráulica para produzir blocos de isoladores não queimados. As dimensões do orifício - a parte oca do isolador - no qual os eletrodos centrais serão pressionados são rigidamente controladas.
- 6 As máquinas de retificação de contorno especial dão aos isoladores prensados sua forma externa final antes que os isoladores sejam queimados em um forno de túnel a temperaturas superiores a 2.700 graus Fahrenheit. O processo controlado por computador produz isolantes que são uniformemente fortes, densos e resistentes à umidade. Os isoladores podem ser queimados novamente após a aplicação das marcas de identificação e do esmalte.
Eletrodo central
- 7 O eletrodo central de liga de níquel é primeiro eletricamente soldado ao pino terminal de aço básico, um fio de metal estreito que vai do meio do plugue à extremidade inferior (a extremidade oposta da lacuna do eletrodo). O pino do terminal é preso a uma porca, que por sua vez é conectada ao cabo de ignição que fornece a corrente elétrica para o plugue.
- 8 O conjunto do eletrodo central / pino do terminal é vedado no isolador e compactado sob extrema pressão. Os conjuntos de isoladores são então selados no invólucro de metal sob pressão de 6.000 libras. Após escarear para corrigir a profundidade e o ângulo, a borda ou borda da casca, chamada de flange - é dobrado ou frisado para completar uma vedação hermética. As juntas da vela de ignição do estoque são cravadas sobre o corpo da vela para que não caiam.
- 9 Para formar o espaço adequado entre os dois eletrodos, o eletrodo central da vela de ignição, agora completamente montada, é aparado à máquina de acordo com as especificações e o eletrodo de aterramento recebe uma dobra final.
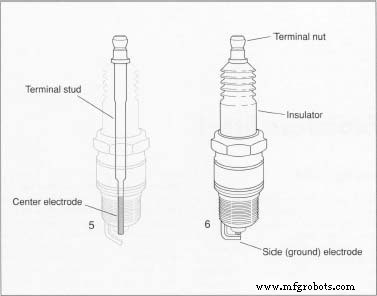
Embalagem
- 10 Após uma inspeção final, as velas de ignição são colocadas em caixas abertas que foram formadas automaticamente. Os plugues são geralmente embrulhados em filme plástico, colocados primeiro em uma caixa de papelão e, em seguida, preparados para serem enviados em grande quantidade aos usuários.
Controle de qualidade
As inspeções e medições são realizadas durante as operações de fabricação e montagem. Tanto as peças que chegam quanto as ferramentas são inspecionadas quanto à precisão. Novos medidores são configurados para uso na produção enquanto outros medidores são alterados e calibrados.
Inspeções detalhadas das carcaças de cada máquina são feitas constantemente para detectar falhas visíveis. O contorno do isolador de cerâmica pode ser verificado projetando sua silhueta em uma tela com uma ampliação de 20 vezes o tamanho real e combinando a silhueta com as linhas de tolerância. Além disso, podem ser feitas inspeções estatísticas regulares nos isoladores que saem da linha de produção.
Durante a montagem da vela de ignição, uma amostra aleatória é testada para verificar se o eletrodo central está devidamente vedado dentro do isolador. As inspeções visuais garantem que a montagem esteja de acordo com as especificações do projeto.
Processo de manufatura
- Por que uma vantagem mais inteligente gerará novos aplicativos de visão computacional em 2019
- ST torna o sensor IoT acessível com IoT plug and play, pronto para se conectar ao Microsoft Azure
- 3 dicas importantes para manter seu gerador ao longo do tempo
- O que é teste de faísca? – Um Guia Completo
- INDÚSTRIA 4.0:fabricantes alemães introduzem fábricas inteligentes para estimular o crescimento
- O que é um plugue de limpeza?
- Como funcionam as máquinas de erosão por centelha EDM?
- EDM Spark Erosion:Do que se trata?
- Usinagem de materiais com formas e tamanhos complexos:por que escolher a EDM Spark Eroding?
- Processo de Usinagem por Descarga Elétrica ou Erosão por Faísca Explicado