Bateria de forno de coque sem recuperação
Bateria de forno de coque sem recuperação
O coque metalúrgico é um material de carbono duro produzido no processo de “destilação destrutiva” de várias misturas de carvão betuminoso. É produzido pela carbonização do carvão a altas temperaturas (cerca de 1100 graus C) em uma atmosfera deficiente em oxigênio em um forno de coque.
A fabricação de coque por aquecimento de carvão com deficiência de ar tem suas origens no início da revolução industrial quando Abraham Darby o utilizou na fundição de minério de ferro em 1709 na Inglaterra. O método de produção de coque era inicialmente o mesmo para a produção de carvão vegetal, armazenando carvão em pilhas redondas, incendiando as pilhas e depois cobrindo as laterais com argila. Isso lançou as bases para a fabricação de coque em colméia. Avanços graduais levaram ao desenvolvimento de fornos de colmeia, reverberação e subprodutos, culminando em fornos de coque regenerativos com recuperação dos subprodutos há cerca de um século.
A tecnologia dos fornos de coque sem recuperação surgiu a partir dos fornos de colmeia clássicos que forneceram desde o século XVIII o coque para a revolução industrial. Os fornos das colmeias eram operados manualmente, com pequena recuperação de calor, apenas para aquecimento do forno. Agora, os fornos sem recuperação são de construção moderna, com operação altamente mecanizada e automatizados até certo ponto. Os gases gerados pela combustão da matéria volátil são enviados pelos cantos inferiores e posteriormente queimados para aquecer o fundo e as laterais do forno.
Existem três processos comprovados para a fabricação de coque metalúrgico. Estes são (i) fornos de coque de colmeia, (ii) fornos de coque de subprodutos e (iii) fornos de coque sem recuperação. Quando a energia térmica dos gases de combustão é recuperada na forma de vapor, os fornos de coque sem recuperação são conhecidos como fornos de coque de recuperação de calor ou de recuperação de energia. Em todos os três processos, os fornos são geralmente construídos em filas, um forno ao lado do outro com paredes comuns entre fornos vizinhos. Essa fileira de fornos é chamada de bateria. Uma bateria geralmente consiste em muitos fornos, às vezes centenas, seguidos.
Um forno de colmeia é uma câmara simples de tijolos refratários construída com um telhado arqueado para que a forma interna seja a de uma colméia antiquada. A coqueificação da colmeia é agora um processo obsoleto devido à pequena quantidade que produzia e à grande quantidade de poluição que produzia. No entanto, ainda está sendo usado em alguns lugares.
Na bateria do forno de coque subproduto, o carvão é carbonizado na ausência de ar, uma vez que essas baterias são operadas com pressão positiva nos fornos. O processo de fabricação de coque nessas baterias de coqueria é chamado de coqueificação de subprodutos, uma vez que o gás residual é coletado e enviado para a planta de subprodutos, onde diferentes subprodutos são recuperados.
No processo de fabricação de coque nos fornos sem recuperação, os voláteis evoluídos durante a carbonização do carvão não são recuperados como subprodutos, mas são queimados no próprio forno na presença de quantidade controlada de ar e o calor dos voláteis dos gases em evolução é utilizado para coque da massa de carvão em coque e, portanto, não é necessário aquecimento externo. O calor é gerado pela combustão de matéria volátil que é então penetrada na massa de carvão através da radiação do topo do forno e também por condução. O nível mais alto de calor é usado para quebrar os hidrocarbonetos potencialmente poluentes nos compostos combustíveis constituintes e para queimá-los, evitando assim a poluição potencialmente perigosa. O calor resultante da combustão é apenas parcialmente utilizado durante o processo e o calor restante no gás de combustão residual é recuperado para geração de energia.
O gás de combustão que sai do forno de coque carrega uma quantidade significativa de calor sensível, além de alguns combustíveis. Como nada além de coque é recuperado dos fornos de coque que incorporam essa tecnologia, os fornos de coque são chamados de fornos de coque sem recuperação. Quando os combustíveis presentes nos gases residuais são queimados e o calor gerado juntamente com o calor sensível dos gases de combustão é utilizado para a produção de vapor e geração de energia, os fornos de coque são chamados de fornos de coque de recuperação de calor ou fornos de coque de recuperação de energia.
A base para os fornos de coque sem recuperação com recuperação de calor é o chamado “forno Jewel-Thompson”. Esses fornos foram desenvolvidos em 1960, quando três fornos de teste foram construídos com sucesso em Vansant, VA. Em 1972, 16 grandes fornos Jewell Thompson foram construídos. A primeira coqueria sem recuperação com recuperação de calor foi inaugurada em Indiana USA em março de 1998. A planta tinha 268 fornos com capacidade de 1,3 milhão de toneladas por ano e uma planta de recuperação de calor de 100 MW. O forno Jewell-Thomson é moldado com uma área de solo retangular. O revestimento do tijolo do forno é composto de material refratário de sílica.
Os elementos-chave da tecnologia de fornos de coque sem recuperação são (i) o coque é produzido por aquecimento do carvão, em atmosfera controlada, liberando assim matéria volátil (gás e umidade), (ii) o gás é queimado de forma ambientalmente 'inteligente' maneira de produzir o calor para fazer o coque, (iii) o excesso de calor que é produzido no processo é usado para gerar eletricidade, (iv) o processo não depende da combustão do carvão, apenas do gás liberado do carvão , (v) as emissões de gases de efeito estufa do processo são típicas de um gerador de energia simples a gás, ou seja, aquele que gera vapor que passa por uma turbina.
Os fornos de coque sem recuperação produzem um coque de qualidade para altos-fornos, cúpulas e fornos de ferro-liga etc. Esses fornos são úteis para obter coque de alta qualidade para operação de alto-forno com injeção de carvão pulverizado, onde são necessárias melhores propriedades de coque, ou para obter qualidade padrão baseada em blends com alguma proporção de carvões não-coqueificáveis.
Comparação com fornos de subprodutos
A comparação da produção de coque no forno de coque de subproduto e no forno de coque sem recuperação é mostrada na Fig 1.
Fig 1 Comparação de forno de coque sem recuperação com forno de coque por produto
A comparação de vários parâmetros de produção de coque pelo forno de coque de subproduto e pelo forno de coque sem recuperação é dada na Tab 1.
Guia 1 Comparação de fornos de subprodutos e fornos sem recuperação | |||
Sl. No. | Parâmetro | Forno de subproduto | Forno sem recuperação |
1 | Pressão do forno | Levemente positivo | Ligeiro negativo |
2 | Altura do forno | Fornos altos | Fornos largos horizontais |
3 | Formas de tijolos | Números grandes | Alguns números |
4 | Fornecimento de calor | Externo através de gás combustível | Interno por combustão parcial de voláteis |
5 | Transferência de calor | condução indireta, horizontal | Direto, vertical, radiação e convecção de cima e condução indireta de baixo |
6 | Poluição | Não amigo do ambiente | Praticamente sem poluição |
7 | Custo de capital | Superior | Baixo |
8 | Energia | Maior necessidade de energia | Baixa necessidade de energia |
9 | Custo operacional | Superior | Baixo |
10 | Tempo de construção | Mais longo | Curto |
11 | Comissionamento | lento | rápido |
12 | Carvão de coque | Restrições de qualidade | Flexibilidade disponível |
13 | Subprodutos | Números grandes | Nenhum subproduto |
14 | Coproduto | gás CO | Vapor/Energia |
15 | Pressão da parede | suscetível | Não suscetível |
16 | Temperatura de carbonização | Baixo | Superior |
17 | Rendimento de coque | Superior | Baixo |
18 | Qualidade do coque | Baixo | Superior |
19 | Recursos humanos | qualificado | Não tão habilidoso |
20 | Manutenção | Manutenção a quente | Os fornos podem ser resfriados para manutenção |
A comparação dos diagramas de Sankey da coqueria de subprodutos e as configurações da coqueria de recuperação de calor é dada na Fig 2.
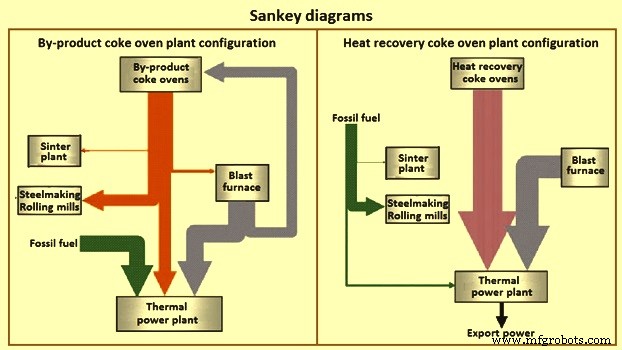
Fig 2 Diagramas de Sankey
Características de projeto e construção de forno de coque sem recuperação
Existem vários modelos disponíveis para os fornos de coque sem recuperação. As principais características de alguns dos projetos são descritas abaixo.
Os fornos de coque Jewell-Thompson –As dimensões típicas das câmaras dos fornos de coque são 14 m de comprimento, 3,5 m a 3,7 m de largura e 2,4 m a 2,8 m de altura. São cobradas de 40 toneladas a 50 toneladas de carvão por forno. A altura de carregamento típica é de 1000 mm. Os fornos são construídos com 23 formas de tijolos refratários. A mistura de carvão é carregada por um lado, por meio de uma máquina chamada "pusher carregador" (PCM) que se desloca sobre trilhos próximos aos fornos. Imediatamente após o carregamento, as misturas de carvão absorvem o calor dos refratários e inicia a combustão da matéria volátil.
Abaixo do teto do forno, ocorre a combustão parcial de matéria volátil, em cima da massa de carvão. Logo em seguida, os gases são aspirados para a fornalha, onde mais ar é introduzido para completar a combustão. A frente de coque avança de baixo para cima, juntando-se em algum lugar no meio. Não há acúmulo de pressão como nos fornos de coque de subprodutos, de modo que carvões de baixa volatilidade podem ser misturados.
Temperatura, pressão e combustão interna são controladas nos fornos. O tempo de coqueificação é da ordem de 48 horas. A retirada de coque é realizada com o mesmo PCM usado para o carregamento. A Coca-Cola é temperada com água. Toda a água utilizada para a têmpera do coque é recuperada, com exceção da perda por evaporação. Uma seção transversal do forno de coque Jewell-Thompson é mostrada na Fig 3.
Fig 3 Seção transversal típica de um forno sem recuperação
Os fornos sem recuperação projetados pelos chineses – Os chineses também construíram, além dos fornos de coque horizontais padrão com recuperação de calor, um forno sem recuperação do tipo vertical. No que diz respeito aos fornos horizontais, o teto do forno é uma estrutura em arco de 120 graus. As entradas de ar primário ajustáveis são instaladas uniformemente no arco, formando uma camada protetora de gases residuais entre o carvão e a zona de queima no teto do forno. Quatro arcos ligados são usados na parte inferior do forno. Na base dos arcos são instaladas entradas de ar secundárias ajustáveis para distribuir o ar na chaminé, para posterior combustão do gás de saída para aquecer o fundo do forno. As chaminés dentro da parede e do fundo podem ser coordenadas. Uma camada de ventilação entre a base do forno e a sola evita o superaquecimento da placa de base. A parede principal está equipada com instalações de ajuste de sucção.
A porta do forno é dividida em duas seções, a superior é fixa e a inferior móvel, para evitar vazamento de fuligem. São fabricados em ferro fundido e revestidos com fibra cerâmica.
As dimensões da câmara de carbonização da bateria horizontal do forno de coque de recuperação de calor de um dos projetos consistem em 13.340 mm de comprimento, 3.596 mm de largura, 2.758 mm de altura com 4.292 mm de distância de centro a centro das câmaras. A dimensão efetiva da torta de carvão é de 1.300 mm de comprimento, 3.400 mm de largura e 1.100 mm de altura. A densidade aparente do carvão de carga é de 1,0 toneladas/cum a 1,5 toneladas/cum. O forno tem capacidade de carga de carvão em torno de 50 toneladas e tem tempo de coqueificação de 72 horas.
Existem mais dois modelos disponíveis. As dimensões da câmara de carbonização nestes dois projetos consistem em 13.334 mm e 15.440 mm de comprimento, 3.598 mm e 3.700 mm de largura, 2.888 mm e 2.693 mm de altura com 4.530 mm e 4.300 mm de distância centro a centro das câmaras, respectivamente. A dimensão efetiva da torta de carvão é de 12.750 mm e 14.850 mm de comprimento, 3.500 mm e 3.600 mm de largura e 1.050 mm e 1.000 mm de altura, respectivamente. Os fornos têm capacidade de carga de carvão (em base seca) de 42.393 toneladas e 51.856 toneladas e tempo de coqueamento de 72 horas e 70 horas respectivamente.
A primeira bateria vertical de recuperação de calor para fornos de coque foi construída em 2002 na China. Em comparação com o tipo horizontal, esses fornos de coque requerem menos espaço e 20% a 30% menos custo de construção. Mais importante, diz-se que a separação entre a câmara de coque e a câmara de combustão evita a queima do coque que pode ocorrer em forno do tipo horizontal. O calor vem apenas através de refratários, como nas baterias convencionais. Existem duas camadas de canais de resfriamento de ar na parte inferior das baterias. A temperatura da fundação está entre 100 graus C a 150 graus C, evitando falhas. As principais dimensões e características dos fornos verticais estão listadas na Tab 2.
Tab 2 Parâmetros técnicos de fornos de coque vertical com recuperação de calor | |||
Sl. No. | Parâmetro | Unidade | Valor |
1 | Câmara de carbonização | ||
Altura | mm | 3.200-4.830 | |
Comprimento | mm | 12.570-16.940 | |
Largura média | mm | 560 | |
Distância do centro | mm | 1.180 | |
2 | Peso da carga | toneladas | Cerca de 24 |
3 | Densidade a granel do bolo | t/cum | 1.0-1.1 |
4 | Tempo de coque | horas | 38 |
5 | Número de fornos | números | 4×35 |
6 | Espessura da parede divisória | mm | 100 |
7 | Espessura da sola do forno | mm | 1.182 |
8 | Altura útil | mm | 2.800-4.400 |
9 | Temperatura central | graus C | 1.000 +/- 50 |
10 | Empurrando o peso do coque | toneladas | Por volta dos 18 |
11 | Saída de gás | N cum/h | 350.000 |
12 | Temperatura do gás de saída | graus C | 950 +/- 50 |
O design dos fornos de coque da Sesa Goa –Os fornos de coque são mais estreitos que os fornos de coque Jewell-Thompson. Isso torna possível usar arco romano para o telhado. Os fornos são construídos com refratários aluminosos, o que implica em uma largura menor. O forno tem 10.760 mm de comprimento e 2.745 mm de largura. 21 números de fornos estão conectados a uma pilha. Os fornos estão com carregamento superior. A utilização de refratários aluminosos ao invés de refratários de sílica deve-se ao seu melhor comportamento sob atmosfera oxidante, melhor resistência ao choque térmico e menor variação de volume no resfriamento, quando há algum atraso na recarga do forno. Os fornos estão sendo operados com carga de carvão compactado.
O design Uhde – No projeto Uhde atual, os fornos de coque são carregados com carimbo. Mas a máquina de carregamento não entra no forno. As dimensões dos fornos são de 3,8 m de largura e 15 m de comprimento. O forro é de tijolos de sílica. O túnel para o gás de saída corre lateralmente abaixo do nível do piso do forno, em vez de sobre os fornos.
Fornos de coque SJ 96 -Este forno foi desenvolvido internamente pela Shanxi Sanjia e é caracterizado pelo peso excepcional da carga de carvão que 120 toneladas. Portanto, há necessidade de um tempo de coqueamento longo de dez dias em comparação com as 48 horas a 72 horas de tempo de coqueamento típico dos outros processos. A altura da massa de carvão é de 1,8 m e o nivelamento é feito nos níveis de 90 cm e 180 cm. Tanto a carga como a descarga são manuais e com o forno refrigerado. As temperaturas são da ordem de 1.200°C na camada de carvão superior e 1.150°C na camada de carvão inferior. O gás é queimado completamente nas chaminés abaixo do forno, e sua temperatura é usada para produzir vapor para geração de energia.
Processo de fabricação de coque em fornos sem recuperação
Em fornos de coque sem recuperação, todos os voláteis do carvão são queimados dentro do forno para fornecer o calor necessário para o processo de fabricação de coque. O forno funciona sob pressão negativa. O ar de combustão primário introduzido através de portas nas portas do forno, queima parcialmente a matéria volátil na câmara do forno. O ar secundário é introduzido nas chaminés únicas, que correm em forma de serpentina sob a massa de carvão. O projeto das chaminés e o controle do fluxo de ar a taxa de coqueificação a ser equalizada tanto na parte superior quanto na inferior da massa de carvão.
Em contraste com o processo de coqueamento de subprodutos, no qual o coque é aquecido indiretamente pela combustão de gás dentro das chaminés de aquecimento fora da câmara do forno, exclusivamente durante o coqueamento sem recuperação o calor necessário é transferido direta e indiretamente para a câmara do forno.
O carvão é carregado no piso do forno no início do ciclo. O processo de carbonização é iniciado pelo calor que existe do ciclo de carbonização anterior. O carregamento de carvão dos fornos é realizado através da porta lateral do empurrador aberta. Muitas vezes, o carvão é carimbado antes e, em seguida, o carvão é carregado na câmara do forno quente. Os níveis de carga típicos são de 1.000 mm.
O gás bruto da coqueria liberado é parcialmente queimado na coroa pela adição de ar ambiente através das portas do forno e os gases passam pelos condutos descendentes para as chaminés de aquecimento situadas na base do forno. Este sistema de chaminé está abaixo do piso do forno e aqui, por meio de um suprimento adicional de ar ambiente, a combustão completa do gás bruto ocorre a uma temperatura que varia de 1.200 graus C a 1.400 graus C. Os gases passam então para um túnel de pós-combustão onde quaisquer gases remanescentes não queimados são oxidados. O sistema de túnel de pós-combustão direciona os gases quentes para os geradores de vapor de recuperação de calor.
Em todas as instalações recentes, o gás residual quente é utilizado para gerar energia e, posteriormente, é submetido à dessulfuração antes de ser expelido para a atmosfera. O tempo de coqueamento varia com os tipos de fornos e varia de cerca de 48 horas a 72 horas, dependendo do projeto dos fornos de coque. Após a conclusão do tempo de coqueificação, o coque é empurrado para fora e normalmente temperado a úmido.
Devido à pressão negativa, sob a qual o processo de coqueamento está sendo executado, as emissões de vazamentos nas portas são evitadas em princípio. As emissões de poeira que ocorrem durante a extração do coque são expelidas através de um galpão do lado do coque. Muitas vezes, os dispositivos de sucção também são instalados no lado do empurrador, para capturar as emissões causadas durante o carregamento.
As técnicas de controle de emissão durante o carregamento, empurrão e têmpera são semelhantes às aplicadas aos fornos de subprodutos.
Devido às temperaturas geradas, todos os hidrocarbonetos tóxicos e subprodutos da matéria volátil são incinerados dentro do forno. Os gases quentes passam em um túnel de gás residual para os geradores de vapor de recuperação de calor, onde o vapor de alta pressão é produzido para fins de aquecimento ou geração de energia. O gás residual frio é limpo em uma planta de dessulfurização de gases de combustão antes de ser descarregado na atmosfera. O diagrama de fluxo do processo é mostrado na Fig 4.
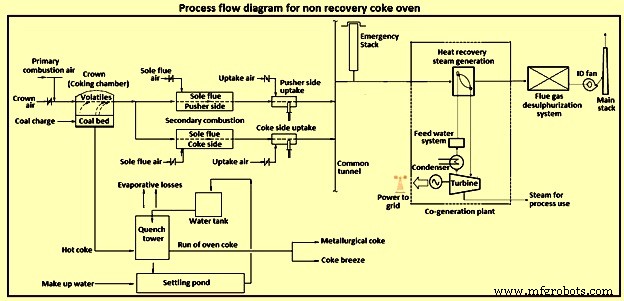
Fig 4 Diagrama de fluxo do processo para forno de coque sem recuperação
Benefícios dos fornos de coque sem recuperação
Os vários benefícios dos fornos sem recuperação incluem (i) nenhuma estação de tratamento de águas residuais é necessária, (ii) nenhuma descarga líquida de águas residuais, uma vez que todas as águas residuais são usadas na têmpera de coque, (iii) maior flexibilidade está disponível na mistura de carvão seleção devido à eliminação das restrições de pressão da parede, (iv) a resistência melhorada do coque é atribuída ao aquecimento lento em temperaturas mais altas e maior tempo de imersão causando crescimento consistente do cristal, (v) precisa de menos espaço quando comparado com o forno de coque e planta de subprodutos, (vi) a planta pode ser construída com construção modular, (vii) uma vez que os fornos sem recuperação trabalham sob pressão negativa, o ar ambiente é puxado para o forno de coque em qualquer ponto de entrada disponível e, assim, elimina quaisquer emissões fugitivas, (viii) ar perigoso os poluentes são destruídos no forno por oxidação térmica e (ix) há um número menor de pontos de controle do processo.
Processo de manufatura
- Bateria
- Forno Microondas
- Arduino Power
- UltraV:Um medidor portátil de índice UV
- Robô Companheiro Asi (Anansi)
- Rádio FM simples
- Gás ou eletricidade? Restringindo a busca por um forno industrial
- Recuperação de amônia durante a produção de coque de carvão de coque
- Qual é a diferença entre um forno a gás e um forno elétrico?
- Entendendo a bateria usada em automóveis