Produção de tubos sem costura
Produção de tubos sem costura
Os tubos são sem costura ou soldados. Os processos de fabricação de tubos sem costura foram desenvolvidos no final do século XIX. Apesar de muitos testes, testes e tecnologias anteriores, a invenção do processo de perfuração de rolos cruzados pelos irmãos Mannesmann no final da década de 1880 é amplamente considerada como um sinal do início da produção em escala industrial de tubos sem costura. No processo de perfuração de rolos cruzados, os eixos dos rolos foram dispostos paralelamente ao eixo do estoque, mas em ângulo em relação ao plano do estoque. Com os rolos girando na mesma direção, esse arranjo produzia uma passagem helicoidal para o estoque através do intervalo do rolo. Além disso, a velocidade de saída foi mais lenta em cerca de 10 de potência do que a velocidade circunferencial dos rolos.
Ao introduzir um mandril perfurante disposto no intervalo do rolo, materiais redondos sólidos podem ser perfurados para produzir uma casca oca no calor de laminação pela ação dos rolos transversais. No entanto, ainda não era possível produzir tubos de espessuras de parede normais em comprimentos utilizáveis apenas pelo processo de perfuração cruzada. Foi somente após o desenvolvimento e introdução de um segundo processo de conformação, chamado “processo de laminação pilger” (novamente pelos irmãos Mannesmann), que se tornou possível e economicamente viável produzir tubos de aço sem costura. O processo pilger também constituiu uma tecnologia incomum e inovadora em que a casca oca de parede espessa foi alongada para a dimensão do tubo acabado pela ação de forjamento descontínuo dos rolos de pilger (ou matrizes) em um mandril localizado dentro da casca oca.
Atualmente, o tubo sem costura é feito de tarugo redondo, que é perfurado no centro para torná-lo uma casca oca e depois enrolado ou extrudado e desenhado sob medida. O processo de fabricação de tubos sem costura consiste nas seguintes etapas principais.
- Fabricação de um casco de tubo oco na operação de perfuração ou extrusão
- Alongar o casco do tubo oco reduzindo seu diâmetro e espessura de parede
- Fabricação de tubo final no processo de laminação a quente ou a frio
Como o processo de fabricação não inclui nenhuma soldagem, o tubo sem costura é percebido como mais forte e confiável. Tubo sem costura é considerado como resistente à pressão melhor do que outros tipos de tubos.
À medida que os direitos de patente e propriedade expiraram, os vários desenvolvimentos paralelos inicialmente perseguidos tornaram-se menos distintos e seus estágios individuais de formação foram fundidos em novos processos. Hoje, os processos de produção de tubos sem costura foram desenvolvidos para os níveis em que esses processos se tornaram modernos processos de alto desempenho de última geração. Dependendo do tamanho do tubo, do mix de produtos e também da disponibilidade do material inicial, foram construídas as seguintes fábricas de tubos sem costura.
- O processo de laminação de mandril contínuo e o processo de bancada de empurrar na faixa de tamanho de cerca de 21 mm a 178 mm de diâmetro externo
- O moinho de plugues de suporte múltiplo com barra de mandril flutuante controlada (restringida e o processo de moinho de plugue na faixa de tamanho de cerca de 140 mm a 406 mm de diâmetro externo
- O processo de perfuração de rolo cruzado e laminação pilger na faixa de tamanho de cerca de 250 mm a 660 mm de diâmetro externo
Além disso, novos processos também foram desenvolvidos, como os derivados do moinho de perfuração de rolos cruzados na forma dos processos Assel e Diescher, ou o processo de extrusão de tubos derivado da prensa Ehrhardt. Um processo sem costura típico é mostrado na Fig 1.
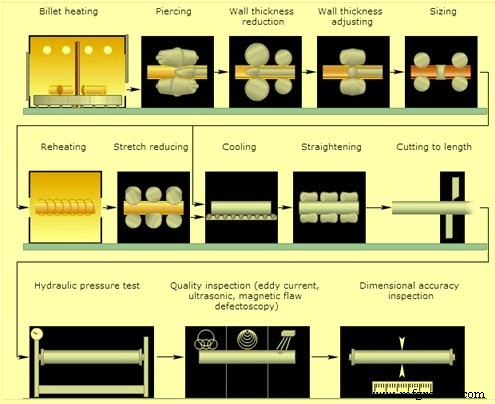
Fig 1 Processo típico de laminação de tubos sem costura
Processo de perfuração e remoção
Neste processo, os cartuchos de entrada são aquecidos em um forno de fornalha rotativa a uma temperatura na faixa de 1250 a 1300 graus C. Do forno os cartuchos são descalcificados por jatos de água de alta pressão e alimentados no moinho de perfuração de rolos cruzados, onde são perfurados para produzir uma casca oca de paredes espessas. Neste processo o material é alongado entre 1,5 e 2 vezes e a seção transversal reduz entre 33% e 50%. A perfuratriz possui dois cilindros de trabalho com contornos especiais que são acionados na mesma direção de rotação. Os eixos são inclinados em aproximadamente 3° a 6° em relação ao plano horizontal de estoque. A folga do rolo é geralmente fechada por um rolo de suporte não acionado na parte superior e uma sapata de suporte na parte inferior. Um ponto de perfuração que funciona como uma ferramenta interna está localizado no centro da folga do rolo e é mantido em posição por um bloco de impulso externo por meio de um mandril.
A casca oca de parede espessa após a operação de perfuração de rolos cruzados é desenrolada ainda mais no suporte de peregrinação para produzir o tubo acabado. A razão de alongamento durante o processo de peregrinação fica entre 5 e 10, e é acompanhada por uma redução na seção transversal de cerca de 80% a 90%. O estande de peregrinação tem dois rolos (às vezes chamados de matrizes por causa de sua ação de forjamento) com uma passagem cônica em torno de sua circunferência. Os rolos giram contra a direção do fluxo de material. O passe de trabalho abrange entre 200° a 220° da circunferência do rolo e consiste na entrada cônica, um passe de polimento cilíndrico uniforme que se funde em uma folga maior para liberar a peça de trabalho. O processo de peregrinação é um processo de forjamento cum por etapas com seu movimento recorrente para trás e para frente.
Após a conclusão do processo de peregrinação, o tubo acabado é retirado do mandril. A parte não trabalhada da concha oca conhecida como cabeça de peregrino é cortada por uma serra quente. O tubo é então alimentado em um moinho de dimensionamento ou redutor após reaquecimento em um forno. O moinho de dimensionamento produz um diâmetro externo preciso, bem como melhora a concentricidade do tubo. Geralmente consiste em três suportes com dois arranjos de rolos altos ou três altos. Os rolos de trabalho formam um passe fechado, com (em configurações de vários suportes) cada passe do suporte sendo ajustado em um ângulo em relação ao passe anterior.
No moinho de redução ou de redução de estiramento, o diâmetro externo do tubo é substancialmente reduzido com a espessura da parede sendo ligeiramente aumentada ou diminuída no processo. Dependendo do mix de produtos, as fábricas têm de 5 a 28 estandes.
Após a última operação de conformação, os tubos acabados são resfriados à temperatura ambiente em um leito de resfriamento e após a verificação dimensional são transferidos para a seção de acabamento onde são realizados os processos como usinagem de pontas de tubos, endireitamento e testes hidráulicos.
Moinhos pilger pesados são usados no caso de tubos de grande diâmetro onde o material de entrada é geralmente um lingote poligonal. Este lingote após aquecimento em um forno rotativo é inicialmente inserido em uma matriz redonda em uma prensa perfurante geralmente vertical. O lingote sólido é perfurado por um punção cilíndrico de aproximadamente metade do diâmetro da matriz, para produzir uma casca oca com base fechada. A próxima operação consiste na redução da espessura da parede acompanhada por um pequeno grau de alongamento em um laminador de rolos cruzados. Durante este processo, a extremidade fechada é perfurada. A casca oca é então alongada no moinho peregrino, seguida da operação de dimensionamento em um moinho de dimensionamento.
Processo de rolagem de plugues
O processo de laminação de plug é usado para laminar tubos sem costura na faixa de diâmetro de cerca de 60 a 406 mm com espessuras de parede de cerca de 3 mm a 40 mm e comprimentos de tubo variando entre 12 me 16 m. Neste moinho a perfuração é feita em um moinho de perfuração de rolo cruzado para produzir uma casca oca de parede fina que é alongada entre 3 e 4,5 vezes o seu comprimento original, correspondendo a um nível de deformação de 65% a 75%. A fresadora de perfuração de rolos cruzados possui dois rolos de trabalho acionados com uma passagem bicônica. Os eixos dos rolos são paralelos ao estoque e estão inclinados em relação à horizontal entre 6° e 12°. A folga entre os rolos de trabalho é ajustada extensivamente por uma sapata guia superior e inferior. Essas sapatas-guia contribuem para o processo de alongamento atuando como rolos estacionários, permitindo a produção de uma casca oca de paredes finas. A coronha segue uma linha helicoidal à medida que passa pela abertura do rolo, permitindo assim que o mandril de perfuração, atuando como uma ferramenta interna, desloque o material de forma mais eficaz. Devido ao ângulo de inclinação do rolo relativamente grande e às velocidades de laminação mais altas, a velocidade de saída do material é consideravelmente mais rápida. Isso é necessário devido ao tempo de ciclo do cordão de plugue a jusante. No caso de tubos de grande diâmetro, há um segundo moinho de perfuração (também chamado de alongador) antes do suporte do plugue. Os recentes moinhos de cilindros para serviço pesado têm apenas uma unidade de perfuração de cone com cilindros de trabalho com design bicônico. Cada um deles está inclinado em aproximadamente 30° em relação ao eixo da coronha oca e inclinado em cerca de 10° a 12° em relação à horizontal. A folga do rolo é fechada por meio de dois discos laterais que também são acionados.
O processo de formação do invólucro oco no tubo acabado é realizado no suporte do plugue a jusante com alongamento de cerca de duas vezes (redução da seção transversal de 50%), com normalmente dois passes de laminação sendo aplicados. No suporte do plug são montados os dois rolos de trabalho cilíndricos que são fornecidos com ranhuras aproximadamente circulares, e também os dois rolos de decapagem acionados separadamente. Um bujão, que está localizado no centro do passe de laminação, é mantido em posição por um mandril suportado por um bloco de impulso localizado a jusante da mesa de laminação. A folga anular resultante entre os rolos e o plugue corresponde à espessura da parede do tubo acabado.
Processo contínuo de rolagem
Após a retirada do mandril, os tubos laminados são reaquecidos antes de serem processados em um moinho de dimensionamento ou em um moinho de redução de tensão ou "estiramento". O estirador, de construção semelhante ao laminador contínuo, consiste em doze suportes de rolos de duas alturas. A redução de tensão é única porque, sem o uso de um mandril de suporte, a espessura da parede é diminuída enquanto o diâmetro é reduzido. As forças de tensão a que o tubo é submetido entre os suportes de rolos não são apenas eficazes na redução da espessura da parede do tubo, mas a redução do diâmetro realizada em cada suporte pode ser triplicada em relação à prática convencional.
O processo de redução e dimensionamento é usado no caso de tubos de pequeno diâmetro. Como não é econômico perfurar, enrolar e enrolar tubos de pequeno diâmetro, a produção de tubos acabados a quente com menos de cerca de 75 mm de diâmetro requer um processo de redução e dimensionamento para o qual é empregada uma máquina especial. Esta máquina é semelhante a um laminador contínuo. Consiste em 8 a 16 suportes de rolos ranhurados de duas alturas com cerca de 305 mm de diâmetro.
Para tamanhos de aproximadamente 140 mm ou mais, o dimensionamento deve garantir tamanho e redondeza uniformes em todo o comprimento do tubo. Assim, o processo de dimensionamento é simplesmente passar o tubo através de dois ou três suportes de rolos de dimensionamento cujas ranhuras são ligeiramente menores do que o tubo enrolado. Em alguns casos, o reaquecimento é necessário.
Em alguns casos, o laminador e a bobinagem dos processos convencionais são substituídos por um laminador contínuo, por exemplo, com nove suportes tandem alimentados individualmente de rolos ranhurados de duas alturas. Após um tarugo ter sido perfurado por um moinho de perfuração convencional, um mandril lubrificado, consideravelmente mais longo que a casca perfurada, é inserido e ambos passam pelo laminador.
O processo de laminação de mandril contínuo tem arranjo em tandem vários passes de laminação em uma série de carrinhos de laminação para formar uma linha de laminação. Este tipo de fresa alonga a casca oca perfurada na fresa de perfuração sobre uma barra de mandril flutuante que atua como uma ferramenta interna para produzir o tubo acabado. Nos últimos tempos, a prática de laminação em laminadores deste tipo emprega barras de mandril controladas em vez de livremente flutuantes. A vantagem desta variante de processo reside no fato de que são necessárias barras de mandril substancialmente mais curtas e em menor número. Esta versão do processo de laminação de mandril contínuo também é chamada simplesmente de MPM (multi stand pipe mill).
O laminador de tubos de suporte múltiplo (MPM) faz parte de um processo eficiente de laminação a quente de tubos sem costura a partir da casca perfurada a quente. O moinho é normalmente composto por 8 suportes de dois cilindros ranhurados inclinados 90° de um suporte para outro. O material é montado em um mandril resfriado e lubrificado e empurrado para o primeiro suporte onde começa a laminação. O mandril corre ao longo do MPM com velocidade constante. O tubo é então cortado, calibrado, tratado e controlado antes da entrega.
Com o processo, o alongamento máximo pode ser obtido. O comprimento do tubo produzido pode ser de até 30 metros. A excentricidade pode ser inferior a 10%.
No caso do processo de laminação contínua até a extração da barra do mandril, a temperatura do tubo cai para cerca de 500°C. O tubo é reaquecido a 950 a 980°C e depois é laminado no moinho redutor de estiramento. Os moinhos redutores de estiramento podem conter qualquer coisa entre 24 e 28 estandes ou mais, todos dispostos em uma formação de linha próxima. Cada suporte tem seu próprio acionamento variável e está equipado com três rolos do menor diâmetro possível. Os três rolos juntos formam uma passagem que é deslocada e progressivamente menor de suporte para suporte.
Neste moinho nenhuma ferramenta interna é utilizada e a velocidade circunferencial dos cilindros aumenta continuamente desde a entrada até a saída do trem de laminação.
Existem vários outros processos para laminação de tubos sem costura. Esses processos incluem processo de bancada, processo de perfuração e extração, processo de extrusão de tubos e processos de laminação cruzada. Os processos de laminação cruzada incluem o processo de laminação assel e o processo de laminação diescher. Além de tubos sem costura também estão sendo produzidos por conformação a frio, trefilação a frio e processo de peregrinação a frio.
Processo de manufatura
- Processo de Produção de Liga de Tungstênio Níquel Ferro
- Processo de Fabricação de Tubos Sem Costura SS
- Como um tubo e um tubo diferem?
- Processo de produção do roteador CNC
- Processo Finex para Produção de Ferro Líquido
- O que é assentamento de tubos?
- O que é uma união de tubos?
- Protótipos para Manufatura de Produção:O Processo
- Protótipos para Produção
- O processo de fabricação de tubos requer planejamento de rota imaginativo