Fabricação de coque em baterias de forno de coque subproduto
Fabricação de coque em subprodutos de baterias de forno de coque
O coque causa até 50% dos custos durante a produção de metal quente. A produção rentável de coque de alta qualidade é, portanto, de primordial importância para a capacidade competitiva da produção de ferro.
O coque metalúrgico é usado nos processos da indústria siderúrgica (principalmente em altos-fornos) para reduzir o minério de ferro a ferro. Mais de 90 por cento da produção total de coque é dedicada às operações de alto-forno. O coque de fundição compreende a maior parte do restante e é utilizado pelas fundições em fornos para fusão de metal e na preparação de moldes. A produção de coque de fundição usa uma mistura diferente de carvões de coque, tempos de coqueamento mais longos e temperaturas de coqueamento mais baixas em relação às usadas para coque metalúrgico.
A maior parte do coque é produzida no mundo usando as baterias de fornos de coque subprodutos e a maioria das plantas de coque são integradas com instalações de produção de ferro e aço.
A fabricação de coque por aquecimento de carvão na ausência de ar tem suas origens no início da revolução industrial quando Abraham Darby o utilizou na fundição de minério de ferro em 1709 na Inglaterra. O método de produção de coque foi inicialmente o mesmo para a produção de carvão vegetal, armazenando carvão em pilhas redondas, incendiando as pilhas e depois cobrindo as laterais com argila. Isso lançou as bases para a fabricação de coque em colméia. Avanços graduais levaram ao desenvolvimento de fornos de colmeia, reverberação e subprodutos, culminando em fornos de coque regenerativos com recuperação dos subprodutos há cerca de um século.
O carvão é convertido em coque em grandes baterias de fornos de coque pela destilação destrutiva do carvão. O processo de coqueamento consiste em aquecer o carvão na ausência de ar para expulsar os compostos voláteis. O material resultante é uma massa de carbono chamada coque, que é um material de carbono duro, mas poroso. O forno de coque de subproduto recupera matéria volátil de carvão na forma de gás de forno de coque, alcatrão e óleos.
Existem três processos comprovados para a fabricação de coque metalúrgico. Estes são
- Fornos de coque tipo colmeia. Estes fornos não são fornos de recuperação
- Fornos de coque com recuperação de calor ou recuperação de energia. Esses fornos de coque também são chamados de fornos de coque sem recuperação.
- Fornos de coque de subproduto
O processo de fabricação de coque de subproduto envolve a carbonização do carvão em altas temperaturas em uma atmosfera onde não há oxigênio. O processo remove a matéria volátil do carvão e concentra o carbono. Nesse processo, o gás residual é coletado e enviado para a planta de subprodutos, onde vários subprodutos (gás de coqueria, alcatrão, amônia e benzol bruto) são recuperados.
Uma planta de forno de coque de subproduto tem três seções principais, a saber, planta de manuseio de carvão e seção de preparação de carvão, baterias de forno de coque de subproduto com instalações de têmpera de coque e planta de britagem e classificação de coque. Fluxo de processo típico e fluxos de emissão de uma planta de forno de coque de subprodutos são mostrados na Fig 1.
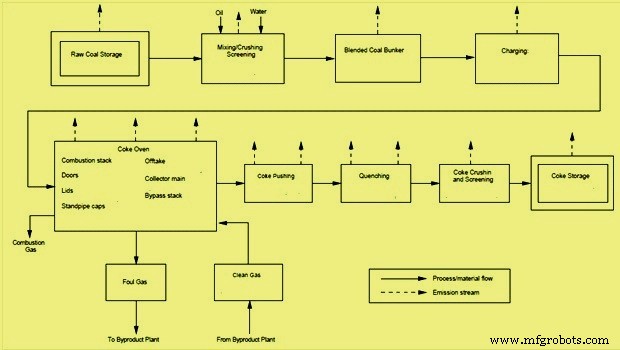
Fig 1 Fluxo de processo e fluxo de emissão típicos
Carvões de coque e fatores que afetam a qualidade do coque
O carvão coqueificável é uma importante matéria-prima na produção de coque nos subprodutos dos fornos de coque, uma vez que decide as propriedades do coque. As propriedades requeridas do coque são tamanho uniforme, boa resistência (valores CRI, CSR e micum), porosidade com mínimo de matéria volátil e mínimo de cinzas.
O carvão coqueificável pode ser classificado com base nas suas propriedades coqueificáveis. Eles são carvão coqueificável prime, carvão coqueificável médio, carvão coqueificável semi ou baixo. As propriedades de coqueificação do carvão para produzir um bom coque incluem fluidez, dilatação, número de inchamento do cadinho, valor do rei cinza, classificação do carvão indicada pelo valor médio de refletância máxima (MMR), vitrinita e distribuição de vitrinita (V9-V14). Além das propriedades de coqueificação, outras propriedades importantes do carvão incluem umidade, cinzas, teores de enxofre, fósforo e álcalis e temperatura de fusão das cinzas. Baixo teor de umidade, cinzas, enxofre e fósforo no carvão são desejáveis para a produção de coque de boa qualidade. Algumas das outras propriedades dos carvões que afetam a qualidade do coque são o tamanho das partículas, a densidade aparente e o desgaste do carvão. Os carvões de coque também podem ter matéria volátil baixa, média ou alta. A temperatura de coqueificação, a taxa de coqueificação, o tempo de imersão, a prática de têmpera e o manuseio do coque também afetam a qualidade do coque
O carvão que é carregado nos fornos de coque é geralmente uma mistura de dois ou mais carvões de coque. A mistura é necessária para controlar as propriedades do coque resultante, otimizar a qualidade e a quantidade de subprodutos e evitar a expansão exibida por certos tipos de carvão que podem causar pressão excessiva nas paredes do forno durante o processo de coqueificação.
Planta de manuseio de carvão e seção de preparação de carvão
A planta de manuseio de carvão e a seção de preparação de carvão preparam a mistura de carvão adequada para carbonização. Várias etapas envolvidas são descarga e armazenamento de carvão, mistura de carvão de vários graus, britagem de carvão e transporte para torre de armazenamento de carvão.
As esteiras transportadoras transferem o carvão do armazenamento de carvão conforme necessário para as caixas de mistura onde os vários tipos de carvões são armazenados. O carvão misturado é transferido dos recipientes de mistura para o triturador de carvão, onde é pulverizado normalmente para um tamanho de -3 mm.
O carvão pulverizado é então misturado e misturado e, às vezes, água e óleo são adicionados para controlar a densidade aparente da mistura. A mistura de carvão preparada é transportada para a torre de armazenamento de carvão no topo da bateria do forno de coque.
O carvão precisa ser armazenado em vários estágios do processo de preparação e transportado pela seção de preparação de carvão. Trituração e peneiramento são a parte importante da planta de manuseio de carvão. A britagem reduz o tamanho total do carvão para que possa ser processado e manuseado mais facilmente. As telas são usadas para variar o tamanho do carvão. As telas podem ser estáticas ou vibradas mecanicamente.
Baterias de forno de coque subproduto
Os fornos de coque são as câmaras feitas de refratários para converter carvão em coque, carbonizando o carvão na ausência de ar e destilando a matéria volátil do carvão. A coqueria de subprodutos consiste em uma ou mais baterias de fornos de coque contendo número de fornos de coque (pode variar de 20 a 100 em cada bateria). O carvão é carregado no forno de coque através de orifícios de carregamento. A seção transversal típica de uma bateria de forno de coque de 7 m de altura é mostrada na Fig 2.
Fig 2 Seção transversal típica de uma bateria de forno de coque de 7 m
Uma quantidade pesada de carvão é descarregada da torre de armazenamento de carvão em um carro de carregamento, que é o veículo de carregamento que pode percorrer o comprimento da bateria. O carro de carregamento é posicionado sobre o forno vazio e quente, as tampas dos orifícios de carregamento são removidas e o carvão é descarregado das tremonhas do carro de carregamento no forno.
Para minimizar a fuga de gases do forno durante o carregamento, a aspiração de vapor é usada para atrair gases do espaço acima do carvão carregado para o coletor principal. A descarga do carvão das tremonhas é “etapada” controlando a sequência em que cada tremonha é esvaziada para evitar picos de carvão que podem bloquear o espaço acima do carvão, o que dificulta a remoção dos gases gerados durante o carregamento. Perto do final da sequência de carregamento, os picos de carvão no forno são nivelados por uma barra de aço que é suspensa do carro empurrador através de uma pequena porta na lateral do forno, chamada de porta niveladora. Este processo de nivelamento ajuda na coqueificação uniforme e fornece um espaço de vapor claro e um túnel de saída para os gases que evoluem durante o processo de coqueificação para fluir para o sistema de coleta de gás. Depois que o forno é carregado com carvão, a porta de nivelamento é fechada, as tampas são recolocadas nas portas de carregamento e seladas (luted) com uma mistura de argila úmida, a aspiração é desligada e a mistura de gases, a aspiração é desligada, e os gases são direcionados para o sistema de saída e coletor principal.
Processo de carbonização do carvão
Começa a ocorrer a transformação do carvão em coque. O calor é transferido das paredes de tijolo aquecidas para a carga de carvão. De cerca de 375 a 475 graus C, o carvão se decompõe para formar camadas plásticas perto de cada parede. A cerca de 475 a 600 graus C, há uma evolução acentuada de alcatrão e compostos de hidrocarbonetos aromáticos, seguida de re-solidificação da massa plástica em semicoque. A 600 a 1100 graus C, inicia-se a fase de estabilização do coque. Isso é caracterizado pela contração da massa do coque, desenvolvimento estrutural do coque e evolução final do hidrogênio. Durante o estágio de plástico, as camadas de plástico se movem de cada parede em direção ao centro do forno, prendendo o gás liberado e criando um acúmulo de pressão de gás que é transferido para a parede de aquecimento. Uma vez que as camadas de plástico se encontraram no centro do forno, toda a massa foi carbonizada. A massa de coque incandescente é empurrada para fora do forno e é temperada úmida ou seca.
A destilação térmica ocorre em grupos de fornos chamados baterias. Uma bateria consiste em vários fornos adjacentes com paredes laterais comuns feitas de sílica de alta qualidade e outros tipos de tijolos refratários. A parede que separa os fornos adjacentes, bem como cada parede de extremidade, é composta por uma série de chaminés de aquecimento. A qualquer momento, metade das chaminés em uma determinada parede está queimando gás, enquanto a outra metade está transportando calor residual das chaminés de combustão para um trocador de calor de “tijolo xadrez” e depois para a chaminé de combustão. A cada 20 a 30 minutos, a bateria “inverte” e as chaminés de calor residual tornam-se chaminés de combustão, enquanto as chaminés de combustão tornam-se as chaminés de calor residual. Este processo proporciona um aquecimento mais uniforme da massa de carvão. A operação de cada forno é cíclica, mas a bateria contém um número suficientemente grande de fornos para produzir um fluxo essencialmente contínuo de gás bruto de coqueria. Os fornos individuais são carregados e esvaziados em intervalos de tempo aproximadamente iguais durante o ciclo de coqueamento. A coqueificação prossegue por 15 a 18 horas para produzir o coque de alto-forno. Durante este período, a matéria volátil do carvão destila como gás de coqueria. O tempo de coqueificação é determinado pela mistura de carvão, teor de umidade, taxa de queima e as propriedades desejadas do coque. Quando a demanda por coque é baixa, os tempos de coque podem ser aumentados para 24 horas. As temperaturas de coqueamento geralmente variam de 900 a 1100 graus C e são mantidas no lado mais alto da faixa para produzir coque de alto-forno. O ar é impedido de vazar para os fornos mantendo uma contrapressão positiva no coletor principal. Os fornos são mantidos sob pressão positiva mantendo alta pressão hidráulica principal de cerca de 10 mm de coluna de água nas baterias. Os gases e hidrocarbonetos que evoluem durante a destilação térmica são removidos através do sistema off take e enviados para a planta de subprodutos para recuperação.
A coqueificação está completa quando a temperatura central do forno está em torno de 950-1000 graus C. Neste ponto o forno é isolado da rede hidráulica e após a devida ventilação dos gases residuais, as portas são abertas para a coqueificação. No final do período de coqueificação, a massa de coque apresenta uma grande retração volumétrica que leva ao desprendimento da massa das paredes, garantindo um fácil empurrão.
O controle da pressão do forno é muito importante, pois a pressão mais baixa leva à entrada de ar enquanto a pressão mais alta leva a gaseificação excessiva, vazamento de portas, canos etc. mm) é mantida para evitar asfixia.
Ao final do ciclo de coqueificação, as portas em ambas as extremidades do forno são removidas e o coque incandescente é empurrado para fora do forno por um aríete que se estende da máquina empurradora. O coque é empurrado através de um guia de coque em um carro de têmpera. O carro de têmpera transporta o coque para uma torre de têmpera úmida ou para uma planta de têmpera a seco, onde é resfriado.
Fábrica de britagem e classificação de coque
O coque temperado é levado por transportador para uma planta de britagem e peneiramento também chamada planta de britagem e triagem de coque. Aqui o coque é triturado e peneirado nas frações de tamanho necessárias. Durante a britagem e peneiramento, o coque é classificado em três frações de tamanho. São coque brisa (tamanho – 10 mm), coque de castanha (tamanho +10 mm a – 25 mm) e coque de alto forno (+25 mm a – 80 mm). O coque de alto-forno e o coque de castanha são transportados para seus respectivos sistemas de armazenamento no alto-forno. A brisa de coque é enviada para a usina de sinterização.
Processo de manufatura
- Baterias da série
- Lanterna
- Forno Microondas
- Fabricação de um relógio LED de madeira
- Arduino Spider Robot (quadrúpede)
- Sistema de Automação, Controle e Medição de Coqueria
- ITmk 3 Processo de fabricação de pepitas de ferro
- Uso de Nut Coke em um Alto Forno
- Têmpera a Seco de Coca-Cola Quente
- Recuperação de amônia durante a produção de coque de carvão de coque