Fundamentos de Hidráulica e Sistemas Hidráulicos
Noções básicas de hidráulica e sistemas hidráulicos
A hidráulica é a geração de forças e movimento usando fluidos hidráulicos que representam o meio para a transmissão de energia. Os sistemas hidráulicos são extremamente importantes para a operação de equipamentos pesados. A palavra “hidráulica” é baseada na palavra grega para água e originalmente significava o estudo do comportamento físico da água em repouso e em movimento. Hoje, o significado foi expandido para incluir o comportamento físico de todos os líquidos, incluindo fluidos hidráulicos. Os sistemas hidráulicos não são novidade na indústria. Eles forneceram um meio para a operação de muitos tipos de equipamentos industriais. À medida que os equipamentos industriais se tornam mais sofisticados, novos sistemas com energia hidráulica estão sendo desenvolvidos.
Os sistemas hidráulicos são usados em plantas de produção modernas e instalações de fabricação e desempenham um papel importante na indústria siderúrgica, mineração, construção e equipamentos de manuseio de materiais. Os sistemas hidráulicos são usados para operar implementos para levantar, empurrar e mover materiais. A ampla gama de aplicações de sistemas hidráulicos na indústria só começou a partir da década de 1950. Desde então, esta forma de energia tornou-se padrão para o funcionamento de equipamentos industriais. Hoje, os sistemas hidráulicos ocupam um lugar muito importante na moderna tecnologia de automação. Existem muitas razões. Algumas delas são que os sistemas hidráulicos são versáteis, eficientes e simples para a transmissão de energia.
A transmissão de energia é o trabalho do sistema hidráulico, pois altera a energia de uma forma para outra. Nos sistemas hidráulicos, as forças que são aplicadas pelo fluido são transmitidas a um mecanismo mecânico. Para entender como os sistemas hidráulicos operam, é necessário entender os princípios da hidráulica. A hidráulica é o estudo dos líquidos em movimento e pressão em tubos e cilindros.
A ciência da hidráulica pode ser dividida em dois ramos:(i) hidrodinâmica e (ii) hidrostática. A hidrodinâmica lida com os líquidos em movimento. Exemplos de aplicações da hidrodinâmica são roda d'água ou turbina; a energia que é usada é aquela criada pelo movimento ou água e o conversor de torque. A hidrostática lida com os líquidos sob pressão. Exemplos de aplicações da hidrostática são macacos hidráulicos ou prensas hidráulicas e acionamento de cilindros hidráulicos. Em dispositivos hidrostáticos, empurrar um líquido que está preso (confinado) transfere energia. Se o líquido se move ou flui em um sistema, o movimento nesse sistema acontece. A maioria dos equipamentos baseados em hidráulica em uso hoje opera hidrostaticamente.
As três tecnologias mais comumente usadas no contexto da tecnologia de controle para geração de forças, movimentos e sinais são hidráulica, elétrica e pneumática. A vantagem da hidráulica sobre outras tecnologias é apresentada abaixo.
- Transmissão de grandes forças usando componentes pequenos que significam grande intensidade de energia
- Posicionamento preciso
- O sistema hidráulico fornece potência consistente, o que é difícil em sistemas de acionamento pneumático ou mecânico
- A inicialização é viável sob carga pesada
- Mesmo os movimentos são possíveis independentemente das cargas, uma vez que os líquidos são pouco compressíveis e podem ser usadas válvulas de controle de fluxo
- Operação e reversão suaves
- Bom controle e regulamentação
- Dissipação de calor favorável
- A possibilidade de vazamento é menor no sistema hidráulico em comparação com o sistema pneumático
- Facilidade de instalação, simplificação da inspeção e requisitos mínimos de manutenção
- O sistema hidráulico usa fluido incompressível que resulta em maior eficiência. tem apenas perda insignificante devido ao atrito do fluido
- O sistema funciona bem em condições de ambiente quente.
As desvantagens dos sistemas hidráulicos incluem (i) poluição do meio ambiente por óleos usados (perigo de incêndio ou acidentes), (ii) sensibilidade à sujeira, (iii) perigo de pressões excessivas (linhas cortadas) e (iv) dependência da temperatura (mudança de viscosidade).
Há uma distinção básica entre sistemas hidráulicos estacionários e sistemas hidráulicos móveis. Enquanto os sistemas hidráulicos móveis se movem sobre rodas ou esteiras, os sistemas hidráulicos estacionários permanecem firmemente fixos em uma posição. Uma característica dos sistemas hidráulicos móveis é que as válvulas são frequentemente operadas manualmente. No caso de sistemas hidráulicos estacionários, normalmente são usadas válvulas solenóides.
As áreas de aplicação típicas dos sistemas hidráulicos móveis incluem (i) equipamentos de construção, (ii) basculantes, escavadeiras, plataformas elevatórias, (iii) dispositivos de elevação e transporte e (iv) equipamentos de manuseio de materiais de pátio. As principais áreas de aplicação dos sistemas hidráulicos estacionários são (i) máquinas de produção e montagem de todos os tipos, (ii) linhas de transferência, (iii) dispositivos de elevação e transporte, (iv) laminadores, (v) prensas, (vi) elevadores , e (vii) máquinas de moldagem por injeção etc. Máquinas-ferramentas são uma área de aplicação típica.
No século XVII, um cientista francês chamado Blaise Pascal formulou a lei fundamental que forma a base da hidráulica. A Lei de Pascal afirma que “a pressão aplicada a um líquido confinado é transmitida sem diminuição em todas as direções e atua com igual força em todas as áreas iguais e em ângulos retos a essas áreas”. Este princípio também é conhecido como as leis dos fluidos confinados. Pascal demonstrou o uso prático de suas leis e demonstrou que aplicar uma pequena força de entrada contra uma pequena área pode resultar em uma grande força aumentando a área de saída. Esta pressão quando aplicada à área de saída maior produz uma força maior. É um método de multiplicar a força.
A multiplicação das forças é apenas uma vantagem do uso de fluido hidráulico para transmitir energia. Além disso, as forças não precisam ser transmitidas em linha reta (linearmente). A força pode ser transmitida em cantos ou de qualquer outra forma não linear enquanto é amplificada. A energia fluida é verdadeiramente um conceito de transmissão de energia flexível. Na verdade, a energia fluida é a transmissão de energia de uma fonte rotativa essencialmente estacionária para um dispositivo de amplificação de força rotativa (circular) ou linear (linha reta) posicionado remotamente chamado de atuador. A energia fluida também pode ser vista como parte do processo de transformação de converter um tipo de energia potencial em uma forma mecânica ativa (força e potência linear ou rotativa). Uma vez que a energia básica é convertida em energia fluida, existem outras vantagens, conforme indicado abaixo.
- As forças podem ser facilmente alteradas mudando sua direção ou invertendo-as.
- Dispositivos de proteção podem ser adicionados para permitir que o equipamento de operação de carga pare, mas evite que o motor principal seja sobrecarregado e os componentes do equipamento sejam excessivamente sobrecarregados.
- A velocidade de diferentes componentes no equipamento pode ser controlada independentemente um do outro, bem como independentemente da velocidade do motor principal.
Fluidos hidráulicos
Os fluidos do sistema hidráulico são usados principalmente para transmitir e distribuir forças para várias unidades a serem acionadas. Os líquidos são capazes de fazer isso porque são quase incompressíveis. A água é imprópria como fluido hidráulico, pois congela em temperaturas frias e ferve a 100°C e também porque causa corrosão e ferrugem e fornece pouca lubrificação. A maioria dos sistemas hidráulicos utiliza óleo (fluido hidráulico), pois não pode ser comprimido e lubrifica o sistema. Muitos tipos de fluidos são usados em sistemas hidráulicos por diversos motivos, dependendo da tarefa e do ambiente de trabalho, mas todos realizam as seguintes funções básicas.
- O fluido é usado para transmitir forças e energia através de conduítes (ou linhas) para um atuador onde o trabalho pode ser feito.
- O fluido é um meio lubrificante para os componentes hidráulicos usados no circuito.
- O fluido é um meio de resfriamento, levando o calor para longe dos “pontos quentes” no circuito ou componentes hidráulicos e descarregando-o em outro lugar.
- O fluido veda as folgas entre as partes móveis dos componentes para aumentar a eficiência e reduzir o calor gerado pelo excesso de vazamento.
Algumas das propriedades e características que devem ser consideradas ao selecionar um líquido como fluido hidráulico satisfatório para um determinado sistema são dadas abaixo.
- Viscosidade – É uma das propriedades mais importantes de qualquer fluido hidráulico. É a resistência interna ao fluxo. A viscosidade aumenta à medida que a temperatura diminui. Um fluido satisfatório para um determinado sistema hidráulico deve ter corpo suficiente para dar uma boa vedação em bombas, válvulas e pistões, mas não deve ser tão espesso que ofereça resistência ao fluxo, levando a perda de potência e temperaturas de operação mais elevadas. Esses fatores aumentam a carga e o desgaste excessivo das peças. Um fluido muito fino também leva ao desgaste rápido de peças móveis ou de peças com cargas pesadas.
- Estabilidade química – A estabilidade química é a propriedade extremamente importante na seleção de um fluido hidráulico. É a capacidade do fluido de resistir à oxidação e deterioração por longos períodos. Todos os fluidos tendem a sofrer alterações químicas desfavoráveis sob condições severas de operação. Este é o caso, por exemplo, quando um sistema opera por um período de tempo considerável em altas temperaturas. Temperaturas excessivas têm um grande efeito na vida útil de um fluido. Normalmente a temperatura do fluido no reservatório de um sistema hidráulico em operação nem sempre representa um verdadeiro estado das condições de operação. Pontos quentes localizados ocorrem em rolamentos, dentes de engrenagem ou no ponto onde o fluido sob pressão é forçado através de um pequeno orifício. A passagem contínua do fluido por esses pontos pode produzir temperaturas locais altas o suficiente para carbonizar ou borrar o fluido, mas o fluido no reservatório pode não indicar uma temperatura excessivamente alta.
- Ponto de fulgor – O ponto de fulgor é a temperatura na qual um fluido libera vapor em quantidade suficiente para inflamar momentaneamente ou flash quando uma chama é aplicada. Um alto ponto de fulgor é desejável para fluidos hidráulicos porque indica boa resistência à combustão e um baixo grau de evaporação em temperaturas normais.
- Ponto de incêndio – Ponto de incêndio é a temperatura na qual um fluido libera vapor em quantidade suficiente para inflamar e continuar a queimar quando exposto a uma faísca ou chama. Assim como o ponto de fulgor, é necessário um alto ponto de ignição dos fluidos hidráulicos desejáveis.
Para garantir o bom funcionamento do sistema hidráulico e evitar danos aos componentes não metálicos do sistema hidráulico, deve-se usar o fluido correto. As três principais categorias de fluidos hidráulicos são (i) óleos minerais, (ii) poli-alfa-olefinas e (iii) ésteres de fosfato.
Fluidos hidráulicos à base de óleo mineral são usados em muitos sistemas hidráulicos, onde o risco de incêndio é comparativamente baixo. Eles são processados a partir do petróleo. As vedações de borracha sintética são usadas com fluidos à base de petróleo. O fluido hidráulico à base de poli-alfa-olefina é um fluido hidrogenado resistente ao fogo para superar as características de inflamabilidade dos fluidos hidráulicos à base de óleo mineral. É significativamente mais resistente a chamas, mas tem a desvantagem de alta viscosidade em baixa temperatura. O uso deste fluido é geralmente limitado a – 40°C. Os fluidos hidráulicos à base de éster de fosfato são extremamente resistentes ao fogo. No entanto, eles não são à prova de fogo e sob certas condições, eles queimam. Devido à diferença de composição, os fluidos à base de petróleo e à base de éster de fosfato não se misturam. Além disso, as vedações para qualquer fluido não são utilizáveis ou tolerantes a qualquer um dos outros fluidos.
Os sistemas hidráulicos requerem o uso de acessórios especiais compatíveis com o fluido hidráulico. Vedações, gaxetas e mangueiras apropriadas devem ser especificamente designadas para o tipo de fluido em uso. Deve-se tomar cuidado para garantir que os componentes instalados no sistema sejam compatíveis com o fluido hidráulico.
Sistemas hidráulicos
Os sistemas hidráulicos podem ser sistema de centro aberto ou sistema de centro fechado. Um sistema de centro aberto é aquele com fluxo de fluido, mas sem pressão no sistema quando os mecanismos de atuação estão ociosos. A bomba circula o fluido do reservatório, através das válvulas seletoras, e de volta ao reservatório. O sistema de centro aberto pode empregar qualquer número de subsistemas, com uma válvula seletora para cada subsistema. As válvulas seletoras do sistema de centro aberto são sempre conectadas em série umas com as outras. Neste arranjo, a linha de pressão do sistema passa por cada válvula seletora. O fluido sempre tem passagem livre através de cada válvula seletora e de volta ao reservatório até que uma das válvulas seletoras seja posicionada para operar um mecanismo. Quando uma das válvulas seletoras está posicionada para operar um dispositivo de atuação, o fluido é direcionado da bomba através de uma das linhas de trabalho para o atuador. Com a válvula seletora nesta posição, o fluxo de fluido através da válvula para o reservatório é bloqueado. A pressão se acumula no sistema para vencer a resistência e movimenta o pistão do cilindro atuador; fluido da extremidade oposta do atuador retorna para a válvula seletora e flui de volta para o reservatório. A operação do sistema após a atuação do componente depende do tipo de válvula seletora utilizada.
No sistema de centro fechado, o fluido está sob pressão sempre que a bomba de força está operando. Há vários atuadores dispostos em paralelo e várias unidades de atuação estão operando ao mesmo tempo, enquanto algumas outras unidades de atuação não estão operando. Este sistema difere do sistema de centro aberto, pois as válvulas seletoras ou de controle direcional são dispostas em paralelo e não em série. Os meios de controle da pressão da bomba variam no sistema de centro fechado. Se for utilizada uma bomba de fornecimento constante, a pressão do sistema é regulada por um regulador de pressão. Uma válvula de alívio atua como um dispositivo de segurança de backup caso o regulador falhe. Se for usada uma bomba de deslocamento variável, a pressão do sistema é controlada pelo compensador do mecanismo de pressão integral da bomba. O compensador varia automaticamente a saída de volume. Quando a pressão se aproxima da pressão normal do sistema, o compensador começa a reduzir a saída de fluxo da bomba. A bomba é totalmente compensada (vazão próxima de zero) quando a pressão normal do sistema é atingida. Quando a bomba está nesta condição totalmente compensada, seu mecanismo de desvio interno fornece circulação de fluido através da bomba para resfriamento e lubrificação. Uma válvula de alívio é instalada no sistema como backup de segurança.
Uma vantagem do sistema de centro aberto sobre o sistema de centro fechado é que a pressurização contínua do sistema é eliminada. Como a pressão é aumentada gradualmente após a válvula seletora ser movida para uma posição de operação, há muito pouco choque de picos de pressão. Esta ação proporciona uma operação mais suave dos mecanismos de acionamento. A operação é mais lenta que o sistema de centro fechado, no qual a pressão está disponível no momento em que a válvula seletora é posicionada.
Componentes básicos de um sistema hidráulico
Independentemente de sua função e projeto, um sistema hidráulico possui um número mínimo de componentes básicos, além de um meio pelo qual o fluido é transmitido. Um sistema básico consiste em uma bomba hidráulica, reservatório para fluido hidráulico, válvula direcional, válvula de retenção, válvula de alívio de pressão, válvula seletora, atuador e filtro. O sistema hidráulico básico é mostrado na Fig 1.
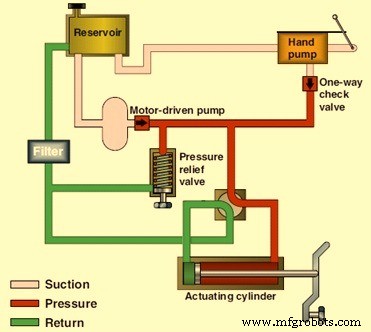
Fig 1 Sistema hidráulico básico
O reservatório hidráulico é um recipiente para armazenar o fluido necessário para abastecer o sistema, incluindo uma reserva para cobrir eventuais perdas por pequenos vazamentos e evaporação. O reservatório geralmente é projetado para fornecer espaço para a expansão do fluido, permitir que o ar aprisionado no fluido escape e ajudar a resfriar o fluido. Os reservatórios hidráulicos são ventilados para a atmosfera ou fechados para a atmosfera e pressurizados. O fluido flui do reservatório para a bomba, onde é forçado através do sistema e eventualmente retorna ao reservatório. O reservatório não apenas supre as necessidades operacionais do sistema, mas também repõe o fluido perdido por vazamento. Além disso, o reservatório serve como uma bacia de transbordamento para o excesso de fluido forçado para fora do sistema pela expansão térmica (aumento do volume do fluido causado por mudanças de temperatura), pelos acumuladores e pelo deslocamento do pistão e da haste. O reservatório também fornece um local para o fluido se purgar das bolhas de ar que podem entrar no sistema. A matéria estranha apanhada no sistema também pode ser separada do fluido no reservatório ou à medida que flui através dos filtros de linha. Os reservatórios são pressurizados ou não pressurizados. Defletores e/ou aletas são incorporados na maioria dos reservatórios para evitar que o fluido dentro do reservatório tenha movimento aleatório, como vórtice (turbilhão) e oscilação. Essas condições podem fazer com que o fluido espume e o ar entre na bomba junto com o fluido.
Para que os componentes hidráulicos funcionem corretamente, o fluido deve ser mantido o mais limpo possível. A contaminação do fluido hidráulico é uma das causas comuns de problemas no sistema hidráulico.
Matérias estranhas e pequenas partículas metálicas do desgaste normal de válvulas, bombas e outros componentes geralmente entram no sistema hidráulico. Filtros, filtros e plugues magnéticos são usados para remover partículas estranhas de um fluido hidráulico e são eficazes como proteção contra contaminação. Plugues magnéticos, localizados em um reservatório, são usados para remover as partículas de ferro ou aço do fluido. O filtro é o principal sistema de filtragem que remove grandes partículas de matéria estranha do fluido hidráulico. Embora sua ação de peneiramento não seja tão boa quanto a de um filtro, um filtro oferece menos resistência ao fluxo. Filtros são usados para bombear linhas de entrada onde a queda de pressão deve ser mantida ao mínimo. O filtro remove pequenas partículas estranhas de um fluido hidráulico e é mais eficaz como proteção contra contaminantes. Os filtros estão localizados em um reservatório, uma linha de pressão, uma linha de retorno ou em qualquer outro local onde necessário. Eles são classificados como fluxo total ou fluxo proporcional. Uma válvula de alívio de desvio em um corpo permite que um líquido contorne o elemento filtrante e passe diretamente por uma porta de saída quando o elemento estiver entupido. Os filtros que não possuem válvula de alívio de desvio possuem um indicador de contaminação. Este indicador funciona com base no princípio da diferença de pressão de um fluido ao entrar em um filtro e depois de sair de um elemento.
Os acumuladores são como uma bateria de armazenamento elétrico. Um acumulador hidráulico armazena potência potencial, neste caso fluido hidráulico sob pressão para futura conversão em trabalho útil. Este trabalho pode incluir a operação de cilindros e motores de fluido, mantendo a pressão necessária do sistema em caso de falha da bomba ou de energia e compensando a perda de pressão devido a vazamento. Os acumuladores podem ser empregados como dispensadores de fluidos e barreiras de fluidos e podem fornecer uma ação de absorção de choque (amortecimento). Os acumuladores podem ser carregados por mola, tipo saco ou tipo pistão.
As bombas hidráulicas convertem a energia mecânica de um motor principal (motor elétrico) em energia hidráulica (pressão). A energia de pressão é então usada para operar um atuador. As bombas empurram um fluido hidráulico e criam fluxo. A unidade de motor combinada de bombeamento e acionamento é conhecida como bomba hidráulica. A bomba hidráulica retira o fluido hidráulico do tanque de armazenamento e o entrega ao restante do circuito hidráulico. Em geral, a velocidade da bomba é constante e a bomba fornece um volume igual de fluido em cada revolução. A quantidade e a direção do fluxo de fluido são controladas por alguns mecanismos externos. Em alguns casos, a própria bomba hidráulica é operada por um motor servo controlado, mas torna o sistema complexo. As bombas hidráulicas são caracterizadas pela sua capacidade de vazão, consumo de energia, velocidade de acionamento, pressão fornecida na saída e eficiência da bomba. As bombas não são 100% eficientes. A eficiência de uma bomba pode ser especificada de duas maneiras. Uma é a eficiência volumétrica, que é a razão entre o volume real de fluido fornecido e o volume teórico máximo possível. A segunda é a eficiência energética, que é a relação entre a potência hidráulica de saída e a potência mecânica / elétrica de entrada. A eficiência típica das bombas varia de 90% a 98%. As bombas hidráulicas são geralmente de dois tipos, a saber (i) bomba centrífuga, e (ii) bomba alternativa.
O atuador hidráulico recebe energia de pressão e a converte em força mecânica e movimento. Um atuador pode ser linear ou rotativo. Um atuador linear fornece saídas de força e movimento em linha reta. É mais comumente chamado de cilindro, mas também é chamado de aríete, motor alternativo ou motor linear. Um atuador rotativo produz torque e movimento rotativo. É mais comumente chamado de motor hidráulico ou motor.
A regulação da pressão é o processo de redução da alta pressão da fonte para uma pressão de trabalho mais baixa adequada para a aplicação. É uma tentativa de manter a pressão de saída dentro de limites aceitáveis. A regulagem da pressão é realizada por meio do regulador de pressão. A função primária de um regulador de pressão é combinar o fluxo de fluido com a demanda. Ao mesmo tempo, o regulador deve manter a pressão de saída dentro de certos limites aceitáveis
As válvulas são usadas em sistemas hidráulicos para controlar a operação dos atuadores. As válvulas regulam a pressão criando condições especiais de pressão e controlando a quantidade de fluido que fluirá em partes de um circuito e para onde irá. As três categorias de válvulas hidráulicas são controle de pressão, controle de fluxo (volume) e controle direcional. Algumas válvulas têm múltiplas funções, colocando-as em mais de uma categoria. As válvulas são classificadas por seu tamanho, capacidade de pressão e queda/fluxo de pressão.
Os três tipos comuns de linhas de tubulação em sistemas hidráulicos são tubos, tubulações e mangueiras flexíveis, que também são chamadas de linhas rígidas, semi-rígidas e flexíveis. Os dois tipos de tubos usados para linhas hidráulicas são sem costura e soldados elétricos. Ambos são adequados para sistemas hidráulicos. Conhecer o fluxo, o tipo de fluido, a velocidade do fluido e a pressão do sistema ajudam a determinar o tipo de tubulação que precisa ser usada. As mangueiras são usadas quando a flexibilidade é necessária.
As conexões são usadas para conectar as unidades de um sistema hidráulico, incluindo as seções individuais de um sistema circulatório. Muitos tipos diferentes de conectores estão disponíveis para sistemas hidráulicos. Os tipos que devem ser usados dependem do tipo de sistema circulatório (tubulação, tubulação ou mangueira flexível), do meio fluido e da pressão máxima de operação de um sistema. Alguns dos tipos mais comuns de conectores são conectores rosqueados, conectores alargados, acoplamentos de mangueiras flexíveis e conexões reutilizáveis.
Diagramas de circuitos hidráulicos
Diagramas de circuitos hidráulicos são desenhos completos de um circuito hidráulico. Incluído nos diagramas está uma descrição, uma sequência de operações, notas e uma lista de componentes. Diagramas precisos são essenciais para o projetista, as pessoas que constroem a máquina e as pessoas que mantêm o sistema hidráulico. Existem quatro tipos de diagramas de circuitos hidráulicos. Eles são bloco, corte, pictórico e gráfico. Esses diagramas mostram (i) os componentes e como eles irão interagir, (ii) como conectar os componentes e (iii) como o sistema funciona e o que cada componente está fazendo.
O diagrama de blocos mostra os componentes com linhas entre os blocos, que indicam conexões e/ou interações. O diagrama de corte mostra a construção interna dos componentes, bem como os caminhos de fluxo. Como o diagrama usa cores, sombras ou vários padrões nas linhas e passagens, ele pode mostrar as diversas condições de fluxo e pressão. O diagrama pictórico mostra o arranjo da tubulação de um circuito. Os componentes são vistos externamente e geralmente estão em uma reprodução próxima de suas formas e tamanhos reais. O diagrama gráfico é o sistema abreviado da indústria e geralmente é o preferido para design e solução de problemas. Símbolos geométricos simples representam os componentes e seus controles e conexões. Um diagrama gráfico típico para um circuito hidráulico é mostrado na Fig 2.
Fig 2 Diagrama gráfico típico de um circuito hidráulico
Processo de manufatura
- Noções básicas sobre adesivos anaeróbios e bloqueadores de fios
- Instituto de Hidráulica e Assuntos de Sistemas de Bombas oferecem novo curso
- O que é Fracking? Prós e contras
- Sistemas incorporados e integração de sistemas
- sistemas SCADA e indústria 4.0
- Construção de sistemas hidráulicos
- Indústria 4.0 e hidráulica
- Atuador hidráulico para elétrico:discutindo o básico
- Práticas recomendadas e dicas de manutenção para sistemas hidráulicos
- Mais do que apenas o básico sobre hidráulica