Desenvolvimento da Tecnologia de Aciaria em Fornos Elétricos a Arco
Desenvolvimento da tecnologia de fabricação de aço em forno elétrico a arco
O desenvolvimento da tecnologia siderúrgica ocorre para atender a uma série de requisitos. Esses requisitos podem ser classificados em quatro grupos, conforme indicado abaixo.
- A tecnologia precisa atender aos requisitos do processo necessários para produzir diferentes graus de aço com as qualidades exigidas.
- A tecnologia deve atender aos requisitos econômicos necessários para controlar o custo de produção para que os produtos siderúrgicos produzidos sejam competitivos.
- A tecnologia deve atender aos níveis de emissão definidos pelos órgãos reguladores.
- A tecnologia é atender aos requisitos de saúde e segurança para que os operadores trabalhem na área sem riscos, estresse e manchas.
Para entender o forno elétrico a arco (EAF), é necessário entender o que é um arco elétrico. Um arco elétrico é uma forma de descarga elétrica entre dois eletrodos, separados por um pequeno espaço (normalmente, ar normal). O exemplo mais conhecido disso é o relâmpago. Qualquer pessoa que tenha realizado soldagem a arco também está familiarizada com arcos elétricos. Se conectar a peça de trabalho ao lado negativo de uma fonte de alimentação CC e um eletrodo ao lado positivo, toque o eletrodo momentaneamente e puxe-o um pouco distante da peça de trabalho, então um arco elétrico estável se forma entre os eletrodos e o peça de trabalho e o calor deste arco é suficiente para derreter o eletrodo e soldar as peças de trabalho. A mesma ideia é usada em maior escala em um forno elétrico a arco.
A história da siderurgia com fornos elétricos a arco (EAF) não é muito antiga. É apenas um pouco mais de um século quando o primeiro forno foi comissionado para derreter aço utilizando energia elétrica. O desenvolvimento inicial da tecnologia ocorreu, uma vez que essas unidades permitiam atingir facilmente as temperaturas mais altas e garantiam as melhores condições para a produção de aços ligados e ligas de alta qualidade. Desde então, grandes avanços foram feitos em equipamentos de fornos, tecnologia EAF, práticas de fusão, matérias-primas e produtos siderúrgicos. Os avanços na tecnologia EAF permitiram que a EAF competisse com mais sucesso com as usinas integradas que empregam a tecnologia de forno de oxigênio básico (BOF) de fabricação de aço. Hoje, a siderurgia EAF tem uma contribuição substancial na produção de aço do mundo, embora ainda esteja muito atrás da contribuição da produção de aço feita pela tecnologia de fabricação de aço dominante da BOF.
Desenvolvimentos iniciais
No século 19, uma série de testes foram feitos para empregar um arco elétrico para a fusão do ferro. Sir Humphry Davy conduziu uma demonstração experimental em 1810, a soldagem foi investigada por Pepys em 1815, Pinchon tentou criar um forno eletrotérmico em 1853, e em 1878-79, Carl Wilhelm Siemens retirou patentes para fornos elétricos do tipo arco.
De Laval havia patenteado um forno elétrico para a fusão e refino de ferro em 1892 e Paul Heroult demonstrou a fusão a arco elétrico de ligas de ferro entre 1888 e 1892. Novas tecnologias emergentes foram colocadas em uso comercial no início do século XX, quando uma ampla gama de geração de energia elétrica relativamente barata começou nessa época. Em 1906, o primeiro forno de fusão a arco elétrico nos Estados Unidos foi instalado na fábrica de Halcomb. Este forno de arco elétrico Heroult 'Antigo nº 1' agora está como um monumento histórico designado ASM (American Society for Materials) na Station Square em Pittsburgh, Pensilvânia (Fig 1).
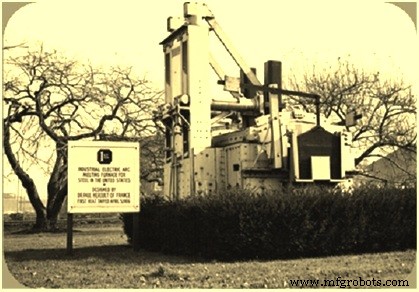
Fig 1 O primeiro forno de arco elétrico Heroult
Inicialmente, a siderurgia EAF foi desenvolvida para a produção de tipos especiais de aços usando formas sólidas de alimentação, como sucata e ligas de ferro. O material sólido foi primeiramente derretido por fusão direta a arco, refinado através da adição de fundentes apropriados e aproveitado para processamento posterior. Fornos elétricos a arco também foram usados para preparar carboneto de cálcio para uso em pedaços de carboneto. A tecnologia de fabricação de aço EAF agora evoluiu de um processo lento para um processo de fusão rápida que funciona em um nível que se aproxima do nível de produtividade de um BOF.
Uma seção transversal esquemática através de um forno de refino a arco Heroult é mostrado na Fig 2. Nesta Fig, E é um eletrodo (apenas um mostrado), levantado e abaixado pela cremalheira e pinhão R e S. O interior é revestido com tijolo refratário H, e K denota o forro inferior. Uma porta em A permite o acesso ao interior. A carcaça do forno repousa sobre balancins para permitir que seja inclinada para rosqueamento.
Fig 2 Forno de refino de arco Heroult
Evolução da tecnologia de fabricação de aço EAF
Desde que o primeiro EAF industrial para fabricação de aço entrou em operação, o desenvolvimento foi rápido e houve um aumento de dez vezes na produção de 1910 a 1920, com mais de 500.000 toneladas de aço sendo produzidas por EAFs em 1920, embora isso representasse apenas uma porcentagem muito pequena de a produção global de aço da época. Os fornos de primeira geração tinham capacidade entre 1 tonelada e 15 toneladas. A EAF tinha conversores Bessemer/Thomas e fornos Siemens Martin (lareira aberta) como fortes concorrentes, inicialmente. Mas seu nicho era a produção de aços especiais que exigiam alta temperatura, fusão de ferroligas e longos tempos de refino.
EAF é uma fase padrão no processo de fabricação de aço. Ao longo dos anos a EAF evoluiu dinamicamente e adotou métodos eficientes, competitivos e sustentáveis no processo e a produção global de aço da EAF está aumentando. Muitos países que não podem produzir ferro pela rota tradicional, ou seja, rota BF-BOF) estão adaptando a rota EAF de fabricação de aço. Uma das principais razões para esses países adaptarem a rota de fabricação de aço EAF é a indisponibilidade de carvões de coque e a fácil disponibilidade de energia de baixo custo devido à acessibilidade de combustível barato. A siderúrgica que utiliza a tecnologia EAF para a produção de aço é conhecida como mini-mills e esta indústria é a maior recicladora de sucata de aço.
Enquanto os EAFs foram amplamente utilizados na Segunda Guerra Mundial para a produção de ligas de aço, foi somente mais tarde que a fabricação de aço elétrico começou a se expandir. O baixo custo de capital para uma mini-mill permitiu que as usinas se estabelecessem rapidamente em um cenário global devastado pela guerra, e também permitiu que elas concorressem com sucesso com as grandes siderúrgicas por 'produtos longos' de aço carbono de baixo custo (aço estrutural, barras e vergalhões, e fio-máquina) no mercado.
Quando a Nucor, hoje uma das maiores produtoras de aço dos EUA, decidiu entrar no mercado de longos em 1969, optou por iniciar uma mini-mill, tendo um EAF como forno siderúrgico, logo seguido por outros fabricantes. Enquanto a Nucor se expandiu rapidamente no leste dos EUA, as organizações que as seguiram em operações de mini-mills concentraram-se nos mercados locais de produtos longos, onde o uso de um EAF permitiu que as plantas variassem a produção de acordo com a demanda local. Esse padrão também foi seguido globalmente, com a produção de aço EAF usada principalmente para produtos longos, enquanto as usinas integradas, usando a rota de produção BF – BOF, concentradas nos mercados de 'produtos planos' (chapas de aço, tiras e chapas de aço mais pesadas, etc.). .). Em 1987, a Nucor tomou a decisão de expandir para o mercado de produtos planos, ainda utilizando o método de produção EAF.
O aumento na produção e tecnologia de EAF em todo o mundo deve-se às seguintes razões.
- A descontinuação do processo de lareira aberta como um processo competitivo de fabricação de aço.
- O desejo de se afastar dos grandes custos operacionais e de capital associados à siderurgia integrada em larga escala em direção a mini usinas siderúrgicas menores e menos intensivas em capital.
- Uma melhoria muito rápida na tecnologia elétrica, reduzindo os custos de equipamentos elétricos de grande escala e também permitindo um controle muito melhor de dispositivos elétricos.
- A pronta disponibilidade de sucata em muitos países combinada com uma forte pressão social para a reciclagem de metais.
- A crescente disponibilidade de fontes alternativas de ferro, especialmente dos países em desenvolvimento.
- Uso de metais quentes e oxicombustíveis nos fornos elétricos a arco
- Uma grande melhoria na operação, controle, eficiência e qualidade do produto da tecnologia de fabricação de aço baseada em EAF.
O crescimento da siderurgia EAF tem sido acompanhado por diversas melhorias tecnológicas que permitiram grandes reduções nos requisitos de energia e melhorias na eficiência energética, produtividade do forno e ambiente de trabalho na aciaria. Essas melhorias tecnológicas trouxeram várias vantagens para as operações do EAF, que incluem, entre outras, operação estável do arco elétrico, baixo consumo de energia, baixo consumo de eletrodos, menos quebras de eletrodos, menor força aplicada aos eletrodos e braços de rolamento de eletrodos e menores distúrbios de rede.
O processo de fabricação de aço EAF dependia apenas da energia elétrica até que as energias químicas se tornassem suplementares para reduzir o custo de conversão através da melhoria da produtividade EAF. No entanto, o gerenciamento eficiente da energia elétrica e química se dá pela combinação do controle dinâmico eficiente do arco elétrico com uma injeção balanceada de oxigênio e carbono para aumentar a produtividade do EAF. As plantas EAF geralmente usam uma mistura de ferro reduzido direto (DRI) / ferro briquetado a quente (HBI) / DRI quente e alimentações de aço reciclado e materiais à base de carbono como agentes espumantes de escória e como carburadores. De acordo com os requisitos de redução do consumo de energia e emissões de gases de efeito estufa, o antracito tradicional e o coque metalúrgico são substituídos por materiais à base de carbono e agora as fontes alternativas de carbono, como pneus de borracha em fim de vida e plásticos reciclados, também estão substituindo parcialmente os materiais convencionais de carbono.
Melhorias nos projetos EAF
Muitas das melhorias tecnológicas no projeto dos EAFs foram feitas para a redução dos tempos de tap-to-tap. Essas melhorias incluíram o seguinte.
- Fornos elétricos a arco com design de ultra alta potência (UHP), com altas tensões secundárias e arco mais longo. Essa inovação desempenhou um papel decisivo na redução acentuada do tempo de tap to tap e no aumento da produtividade EAF por hora. O primeiro forno UHP foi instalado nos EUA em 1963. O forno de 135 toneladas foi equipado com transformadores de 70-80 MVA, o que significa uma potência específica de 520-600 kVA/ton. Devido às suas operações bem-sucedidas, os fornos UHP tornaram-se populares rapidamente e sua potência específica também foi aumentada para 1000 kVA/ton.
- Braços de eletrodos condutores de alta corrente em design de caixa revestida de cobre.
- Sistema de controle de eletrodo de última geração.
- várias aberturas no forno para uso extensivo de fontes alternativas de energia
- Projeto de construção pesada para sustentar condições de trabalho difíceis que permitem movimentos muito rápidos e operações seguras.
- Design de concha dividida do EAF para facilitar a manutenção e reduzir o tempo de manutenção.
- Painéis de resfriamento de cobre ou combinados com fluxo de água de resfriamento de alta velocidade.
- Sistemas de alimentação contínua para DRI/HBI/hot DRI resultando na redução do tempo de carregamento do forno.
- Mais entrada de calor na área fria EBT (excentric bottom taping) devido ao design especial do sistema de queimador EBT.
- Alta flexibilidade e alta eficiência de operação do forno com aplicação de porta de escória fechada.
- Fácil operação de manutenção para design especial, como sistema de elevação do telhado, sistema de travamento do forno.
- Inserção de energia química adicional baseada em carbono, combustível e oxigênio que é utilizada como substituto da energia elétrica.
- Projeto de regulagem para eletrodos – Normalmente, o conjunto eletrodo/braço/mastro/cabo pesa na faixa de 20 toneladas. Este é movido verticalmente para fins de controle por um cilindro hidráulico incorporado no mastro. Como o comprimento do arco depende, entre outras coisas, do nível em constante mudança de sucata ou líquido sob o eletrodo, é necessário ter um controle automático sobre a posição do eletrodo (o sistema de regulação). O sistema de regulação influencia muitos aspectos importantes do desempenho do forno, como entrada de energia, corrente média, estabilidade do arco, padrão de fusão da sucata, perdas de energia para painéis resfriados a água, consumo de energia, eletrodo e refratário. Todos esses parâmetros estão inter-relacionados de maneira complexa e há muitas diferenças de opinião sobre estratégias de controle "ótimas".
- Alcançar melhor energia e equilíbrio térmico dentro do forno devido à injeção de várias unidades.
Principais desenvolvimentos na tecnologia EAF
Algumas das principais melhorias tecnológicas durante os últimos quarenta anos são apresentadas a seguir.
- Prática de escória espumosa – Na siderurgia EAF, a fusão progressiva da sucata aumenta a transferência de calor por irradiação do arco para as paredes laterais do forno. Ao cobrir o arco com uma camada de escória, o arco é blindado e mais energia é transferida para o banho. A escória espumante durante este período é benéfica. A eficácia da formação de espuma de escória depende das basicidades da escória, teor de FeO da escória, temperatura da escória e disponibilidade de carbono para reagir com oxigênio ou FeO da escória. Uma escória espumante reduz os danos refratários e a perda de calor da região do arco. A economia líquida de energia é estimada em 6-8 kWh/ton de aço.
- Sopro de oxigênio no fundido – O sopro de oxigênio no aço fundido libera calor, porque a reação do oxigênio com carbono, silício e ferro no metal fundido é exotérmica e produz calor. Nestas condições, o tempo de fusão diminui e a produtividade aumenta. Por causa da liberação de calor, o consumo de eletricidade diminui, assim como o consumo de eletrodos juntamente com o consumo de refratários. No passado, quando o consumo de oxigênio de menos de 10 m³ por tonelada de aço era comum, as operações de punção eram realizadas manualmente usando uma lança de tubo consumível. A maioria das operações modernas agora usa lanças automáticas e a maioria das instalações agora usa uma lança não consumível refrigerada a água para injetar oxigênio no aço. Muitas dessas lanças também têm a capacidade de injetar carbono.
- Operação de salto quente – Na operação de salto quente, cerca de 15% a 20% de metal e certa quantidade de escória são deixados no fundo do forno após cada rosqueamento. O resto da escória é removido do forno sobre o peitoril. Isso auxilia na fusão da alimentação sólida fresca que entra no forno e permite um vazamento praticamente sem escória. A operação hot heel resulta em economia de ferro-ligas e eficiência energética.
- Toque excêntrico no fundo – O rosqueamento excêntrico no fundo (EBT) reduz os tempos de torneira, as perdas de temperatura e o transporte de escória para a panela. Economias de eletricidade de 12-15 kWh/ton de aço são estimadas usando esta tecnologia. O rosqueamento sem escória EBT resulta em alto rendimento de aditivos de liga e alta vida útil do refratário da panela.
- Prática de pós-combustão – O gás monoóxido de carbono (CO) gerado durante a descarbonetação é queimado com a injeção de oxigênio das lanças dentro do forno. A energia liberada é usada aquecendo o banho diretamente ou pré-aquecendo o material de alimentação de entrada. Um sistema específico de controle pós-combustão instalado em duas fábricas no México e nos EUA levou a reduções de, respectivamente, 2% e 4% no consumo de eletricidade, 8% e 16% no consumo de gás natural, 5% e 16% no uso de oxigênio, e 18% e 18% em carbono carregado e injetado.
- Injeção de carbono – A injeção de carbono traz os benefícios de (i) para a prática de 100% de sucata ou quando o teor de carbono do banho é insuficiente para produzir gás CO para formação de espuma de escória, a injeção de carbono é benéfica e (ii) a oxidação do carbono produz Gás CO que na pós-combustão gera energia térmica. Deve-se notar que a injeção de carbono requer injeção de oxigênio para iniciar a oxidação do carbono.
- Monitoramento e controle de gases de combustão - A taxa de recuperação de energia química dos gases de escape pode ser aumentada em 50% ajustando os níveis de injeção de oxigênio para pós-combustão com base nas leituras de CO e CO2 em tempo real nos gases de combustão, em vez de usar valores predefinidos. A economia de eletricidade de 12 a 15 kWh/ton de aço é estimada usando essa tecnologia.
- Queimadores de oxicombustível – Queimadores de oxicombustível/lancing podem ser instalados em EAFs para reduzir o consumo de eletricidade, substituindo a eletricidade por oxigênio e combustíveis de hidrocarbonetos. Esta tecnologia foi introduzida para melhorar as taxas de fusão e fornecer uma distribuição de calor mais uniforme em todo o forno. Reduz o consumo total de energia devido aos tempos de aquecimento reduzidos, aumenta a transferência de calor durante o período de refino e facilita a formação de espuma de escória, o que aumenta a eficiência do uso de oxigênio e carbono injetado. Deve-se ter o cuidado de usar os queimadores de oxicombustível corretamente, caso contrário existe o risco de aumento no consumo total de energia e geração de gases de efeito estufa. 2–3 kWh/ton de aço de energia podem ser economizados para cada minuto de tempo de aquecimento reduzido. Economias de eletricidade de 35-40 kWh/ton de aço podem ser alcançadas com taxas típicas de injeção de oxigênio de 18 N cum/ton de aço.
- Pré-aquecimento de sucata – Vários sistemas de pré-aquecimento de sucata que utilizam o calor associado a gases de escape foram desenvolvidos, alguns baseados em sistemas de caçamba em lote e outros em sistemas de eixo contínuo. Com sistema de eixo único pode-se economizar até 77 kWh/ton de aço de energia elétrica. O sistema de eixo de dedo permite uma economia de até 110 kWh/ton de aço, o que representa aproximadamente 25% do consumo de eletricidade.
- Eliminação de fontes de radiação na sucata de carga – A sucata comprada deve ser submetida à detecção de radiação para evitar que o aço produzido se torne propenso à radiação. Toda sucata recebida na instalação deve ser passada pelo equipamento de detecção 'Exploranium'. A sucata sinalizada como de alto risco passa por uma varredura adicional dos detectores manuais. Uma segunda varredura com o equipamento de detecção 'Exploranium' é realizada antes da entrega da aciaria e uma varredura final é realizada em cada carga de ímã à medida que os baldes de carga são preenchidos. Os detectores de sacos EAF definem quando, se houver, o material radioativo foi derretido.
- Carregamento de DRI quente - O carregamento de DRI quente em temperaturas de até 600 graus C em vez de DRI frio resulta em uma redução de energia de fusão de 150 kWh/ton de aço. Outros benefícios são o aumento da produtividade, diminuição do teor de elementos residuais, melhor formação de espuma de escória e aumento do teor de carbono na carga.
- Carregamento de metal quente – O carregamento de metal quente no EAF junto com a injeção de oxigênio reduz o consumo de energia elétrica devido à utilização de energia química. Isso reduz o tempo de torneira a torneira, o consumo de carbono e o consumo de eletricidade.
- Transformadores de ultra-alta potência – A economia de energia elétrica é estimada em 1,1 kWh/ton de aço para cada aumento de potência em MW. O consumo de energia caiu 11 kWh/te 22 kWh/t respectivamente para 2 linhas de forno quando a tensão de operação aumentou de 600 V para 660 V em um forno e de 400 V para 538 V em outro forno.
- Eletricidade do forno – Grandes melhorias no controle e eficiência energética foram alcançadas devido ao desenvolvimento de fontes de alimentação com tensões de operação mais altas.
- Controles do forno -Esta tecnologia resulta em 14% de redução no consumo de eletricidade. Além disso, uma redução de 6% no consumo de gás natural pode ser alcançada em conjunto.
- Controle de processo aprimorado (redes neurais) – O controle de processo aprimorado (redes neurais) pode ajudar a reduzir o consumo de eletricidade além do alcançado por meio de sistemas de controle clássicos. Por exemplo, redes neurais ou sistemas de “lógica difusa” analisam dados e emulam o melhor controlador. Para EAFs, os primeiros sistemas de controle de “lógica fuzzy” foram desenvolvidos usando o fator de potência atual e o uso de energia para controlar os eletrodos no banho. Estima-se que a economia de eletricidade de 30 kWh/ton de aço seja alcançada, e os valores podem mudar com base nas características da sucata e do forno.
- Agitação inferior/injeção de gás de agitação – Em fornos a arco convencionais há pouca turbulência elétrica natural dentro do banho. Devido à ausência de agitação, um pedaço grande de sucata pode levar muito tempo para derreter e pode exigir lancetagem de oxigênio. A agitação de argônio ou nitrogênio elimina os gradientes de temperatura e concentração, reduz os tempos de torneira a torneira, reduz o consumo de refratários, eletrodos e energia e melhora o rendimento de ferro e ligas. Com a introdução da tecnologia de agitação no banho, há economia de eletricidade. Essa economia de energia elétrica pode variar de 12 a 24 kWh por tonelada de aço.
- Forno a arco de corrente contínua – Os fornos a arco de corrente contínua (DC) representam um conceito diferente no projeto de forno a arco. A maioria dos fornos DC são com eletrodo único, onde a corrente flui do eletrodo de carbono para um ânodo montado na parte inferior do forno. O consumo reduzido de eletrodos da ordem de 50% a 60% é o principal benefício de um forno CC em comparação com um forno a arco trifásico convencional. Os níveis de ruído para os fornos DC são mais baixos. Custos de manutenção mais baixos são reivindicados e os custos refratários são menores para a parede lateral, mas maiores para o fundo do forno. Um forno a arco CC requer a adição do eletrodo inferior (ânodo), um reator CC e um tiristor, todos os quais aumentam o custo de um forno CC. Os fornos DC além de seu baixo consumo de energia e eletrodo garantem uma excelente homogeneização térmica e metalúrgica do aço líquido. Também há o aumento do efeito de agitação do arco de corrente contínua que suporta este processo. Em comparação com os fornos a arco elétrico CA, os fornos CC causam menos distúrbios na rede e, portanto, podem ser conectados mesmo às redes elétricas fracas. A economia líquida de energia em relação aos fornos AC mais antigos é estimada em 85-90 kWh/ton de aço. Em comparação com os novos fornos CA, a economia é limitada a 10 a 20 kWh/ton de aço.
- Recuperação de calor residual para EAF – Para um EAF derretendo 150 t/carga de DRI com tempo de derivação de 49 minutos e tempo de ativação de 40 minutos, aproximadamente 130 kWh/ton de aço de energia podem ser recuperados ( eficiência 30 %). Se a energia recuperada for usada para geração de energia com vapor saturado, 2,8 MWh/ano de eletricidade podem ser gerados. Se a energia recuperada for utilizada para geração de energia com vapor superaquecido, podem ser gerados 15,1 MWh/ano de energia.
- Acionamentos de frequência variável ou acionamentos de velocidade ajustável – O consumo total de energia do ventilador pode ser reduzido em 67%. A economia de eletricidade é estimada em 16,5 kWh por tonelada de aço.
- Forno a arco DC de casca dupla – pode resultar em economia de eletricidade de 15 a 20 kWh/ton de aço.
- Forno CONARC- Este forno combina as vantagens tecnológicas do forno elétrico a arco com as do processo de sopro convencional. CONARC reflete a combinação de CONverter e ARCing. O processo é dividido em duas fases. A fase do conversor que envolve o sopro de oxigênio no fundido através da lança superior para descarbonetá-lo e a fase do forno elétrico a arco durante a qual a energia elétrica é aplicada para derreter o material sólido e superaquecer o banho até a temperatura de vazamento.
- Tecnologia de injeção de polímeros – É um novo e interessante processo patenteado, que substitui parcialmente o uso de coque por polímeros, incluindo borracha (pneus usados), como um injetor alternativo de carbono para produzir escória espumante na fabricação de aço EAF. Os benefícios incluem (i) redução do consumo específico de energia elétrica de aproximadamente 3%, (ii) redução do injetor de carbono de aproximadamente 12%, (iii) aumento da produtividade do forno (toneladas por minuto) de 4%, (iv) níveis de FeO da escória são mantidos dentro da faixa exigida e (v) níveis reduzidos de emissão de NOx, CO e SO2.
EAF com pneus de borracha e plásticos
Um estudo realizado pela Sidney Steel Mill da One Steel em colaboração com a UNSW em testes de laboratório sobre o uso de pneus de borracha na fabricação de aço EAF para otimização de escória espumosa desenvolveu e comercializou um sistema de engenharia por meio de testes em plantas para EAFs para injetar misturas de borracha de pneus em fim de vida e coque em EAF como agentes espumantes de escória. O método resultou em benefícios como aumento de volume e espumosidade da escória, incluindo melhor eficiência de energia elétrica devido a um arco mais longo e melhor transferência de calor do arco para o aço, bem como diminuição da perda de calor através da escória e paredes laterais. Enquanto os fabricantes de aço EAF que usam a tecnologia de injeção de polímero (PIT) também podem esperar melhorias no rendimento, consumo de oxigênio injetado, consumo de refratários e eletrodos e desgaste do sistema de injeção. A tecnologia de injeção de borracha (RIT) tornou-se um processo padrão nas siderúrgicas da One Steel em Sydney e Laverton EAF e alcançou marcos significativos com 40.720 calores aproveitados com injeção de borracha, 13.721 toneladas de coque reduzido devido – substituído e redução na injeção devido a Controle de FeO e dimensionamento consistente, e 1.128.486 pneus de passageiros equivalentes usados. O aço verde resultante de pneus velhos de borracha e plásticos não produz resíduos ou gases tóxicos.
Processo de manufatura
- Automação de Controle e Modelagem de Forno Elétrico a Arco
- Forno de indução e siderurgia
- Utilização de Metal Quente para Siderurgia em Forno a Arco Elétrico
- Forno de arco elétrico DC
- A importância da tecnologia desenvolvida por startups
- Quais são os 7 tipos de tecnologia?
- A serra circular elétrica útil
- Diferentes tipos de processo de soldagem a arco elétrico
- Entendendo a soldagem a arco elétrico
- A tecnologia dos veículos autônomos