Importância da lareira, homem morto e torneira na operação do alto-forno
Importância da lareira, homem morto e torneira na operação do alto-forno
Uma tendência de deterioração da qualidade do minério é observada nos dias de hoje com o aumento da demanda por minério de ferro. A deterioração da qualidade do minério é acompanhada por maiores quantidades de escória que, por sua vez, afeta a descida da carga e o fluxo de líquido através da fornalha. Essas condições fornecem um catalisador para o mecanismo de desgaste do revestimento com revestimentos Bosh, Stack e Hearth sob estresse adicional. O rosqueamento no alto-forno é afetado de forma adversa e os canais e canais na casa de lingotamento ficam sob tensão devido ao maior volume de escória. Tudo isso aumentou a pressão sobre as operações do alto-forno.
A má qualidade do minério de ferro afeta a operação do alto-forno da seguinte maneira.
- Volume de escória – A má qualidade dos minérios de ferro traz para o forno maiores quantidades de impurezas, resultando em aumento nos volumes de escória.
- Carga de calor – A condição térmica do forno sofre alterações, pois é necessária uma grande quantidade de calor para fundir a escória adicional, bem como mantê-la em estado fluido adequado para sua drenagem. Isso introduz cargas de calor mais altas dentro do alto-forno.
- Taxa de coque e produtividade – O aumento dos volumes de escória exige uma maior entrada de combustível no forno, e onde as taxas de injeção de carvão pulverizado já estão operando no nível ideal, isso resulta em uma taxa de coque mais alta. Coque mais alto significa a introdução de maior quantidade de cinzas no forno, resultando em maior aumento no volume de escória. Isso tem um efeito de deterioração na produtividade do forno.
- Estabilidade do processo – A deterioração da qualidade do minério afeta negativamente a estabilidade do processo e tem um efeito desfavorável no bom funcionamento do alto-forno.
- Os maiores volumes de escória influenciam o fluxo de gás.
- Com volumes de escória mais altos, o fluxo de líquido através da fornalha é mais desafiador, levando a aumentos nos níveis flutuantes de líquido na fornalha. No caso extremo, a descida da carga é afetada.
- O aumento de incidentes de fluxo de gás comprometido devido à má qualidade do minério provavelmente aparecerá como aumento da suspensão com deslizamentos mais frequentes e graves. Isso, por sua vez, atua como um catalisador para um maior desgaste do revestimento, com os revestimentos bosh, stack e hearth sofrendo mais estresse.
- Taxas de escória mais altas fornecem uma grande restrição na casa de lingotamento, uma vez que a calha do forno e o sistema de canais na casa de lingotamento tornam-se um gargalo para acomodar os maiores volumes de escória.
- Iron first -Isto ocorre se a interface escória-ferro estiver acima do nível do furo quando o furo é aberto. O ciclo de rosqueamento começa com uma saída apenas de ferro, e a escória começa a fluir mais tarde quando a interface escória-ferro desce para o furo de derivação. Após isso, o ferro e a escória são drenados simultaneamente até o final da rosqueamento. O tempo decorrido desde o início do rosqueamento até a entrada da escória no corredor é chamado de atraso da escória.
- Simultâneo – Este padrão aparece se a interface escória-ferro estiver dentro ou a uma profundidade finita abaixo do furo de drenagem quando o rosqueamento começar. O alto gradiente de pressão na fase de escória pode promover o fluxo de ferro, ou até mesmo arrastar o ferro para cima do furo de drenagem. Como resultado, o ferro e a escória são drenados juntos durante todo o período de extração.
- Primeiro de escória- Este é o oposto do primeiro padrão de ferro. Neste padrão, a escória flui inicialmente e passa a ferro após um atraso. Isso ocorre porque a interface escória-ferro está muito abaixo do orifício de derivação quando o rosqueamento começa, e os fenômenos podem ser observados em fornos maiores com vários orifícios de derivação. O gradiente de pressão causado pela escória viscosa é inicialmente inadequado para levantar o ferro.
Devido aos fatores acima, o processo de produção no alto-forno varia muito. A grande variação no processo tem consequências na composição da escória e, portanto, na qualidade do metal quente. Os fatores acima também afetam o processo em muitas outras áreas, conforme indicado abaixo.
Para acomodar os cenários acima e muitos outros que podem ser esperados durante a operação do alto-forno, são necessárias várias ações para ter um controle adequado durante a extração do alto-forno, para evitar que o forno funcione a frio ou a quente e para uma operação suave do alto-forno forno. Essas ações incluem (i) gerenciamento da fornalha para drenagem ideal e desgaste mínimo para combater os maiores volumes de escória, (ii) adaptação do processo e estratégias de carregamento para estabilidade ideal e cargas de calor minimizadas na parede do forno, (iii) monitoramento próximo e manutenção adequada da o sistema de refrigeração do alto-forno para que possa absorver as maiores cargas de calor, e (iv) avaliação e desgargalamento dos layouts de lingotamento existentes para o aumento das vazões de líquido.
A lareira, o homem morto e o fluxo de metal quente e escória em direção ao furo de drenagem durante o rosqueamento do forno podem ser vistos na Figura 1.
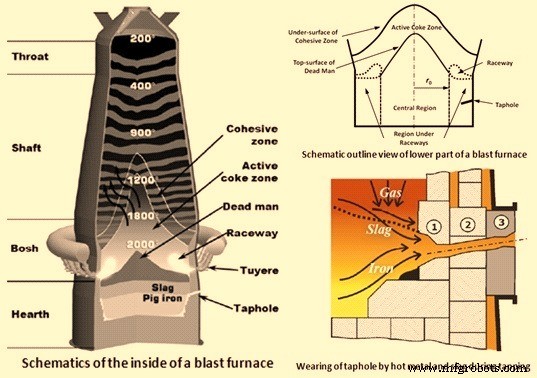
Fig 1 Lareira, homem morto e o fluxo de metal quente e escória durante o rosqueamento
Lareira do alto-forno e homem morto
O estado da lareira desempenha o papel mais importante para a operação estável do forno e longa vida útil. Esta região mais baixa do alto-forno está exposta ao ferro líquido (metal quente) e escória líquida que estão em contato direto com os materiais refratários, causando forte erosão e ataque químico e térmico do revestimento da fornalha. O ambiente mais agressivo em uma fornalha geralmente é encontrado nas proximidades do(s) orifício(s), que está sujeito a altas tensões térmicas e velocidades de fluxo do líquido. O gerenciamento do taphole (integrado com outras técnicas de orientação operacional) é crucial no desempenho do forno e, portanto, na operação geral do forno.
A lareira é a parte mais baixa, mas a mais importante do alto-forno. A vida útil do forno depende consideravelmente da durabilidade da lareira. A parede lateral e o fundo da lareira são geralmente construídos com blocos ou tijolos à base de carbono combinados com cerâmica de alta qualidade.
Em princípio, existem dois projetos básicos de lareira. O primeiro é o design de bloco pequeno ou tijolo, enquanto o segundo é o design de bloco grande. A diferença de projeto se deve ao tamanho dos refratários. A principal vantagem de uma pequena lareira de bloco é a facilidade de construção, pois os tijolos podem ser manipulados na posição e argamassados em todos os lados. Outra vantagem é que os tijolos são menos propensos a rachaduras, pois a lareira como um todo já está basicamente rachada. Isso, no entanto, também é uma desvantagem, pois cada junta pode servir como uma barreira de transferência de calor, especialmente se houver movimento e as juntas se tornarem lacunas. Os grandes blocos não sofrem a mesma desvantagem, pois há muito menos juntas. No entanto, devido à expansão térmica, os blocos grandes tendem a rachar, causando barreiras de transferência de calor semelhantes.
Dentro dos dois projetos básicos existem diversas variações e algumas semelhanças entre os projetos de blocos grandes e pequenos. Essas semelhanças e diferenças são o tipo de material refratário usado contra a parede, a face quente e ao redor dos furos. Uma das maiores considerações é a transferência de calor do interior do forno para o meio de resfriamento. Para isso, normalmente são utilizados vários tipos de refratários. Em geral, o custo aumenta com a condutividade térmica. Embora fosse muito caro, a melhor lareira é, em teoria, construída com os refratários de maior condutividade. Tal lareira duraria para sempre e nunca se desgastaria (devido a um revestimento de congelamento protegendo os refratários), mas também tiraria tanto calor do forno que o custo das operações seria alto. Tal lareira esfriaria tão rapidamente durante o desligamento do forno que seria difícil iniciar novamente, levando a custos ainda mais altos. Normalmente nos projetos da lareira, é mantido um equilíbrio entre os fatores mencionados acima.
Os revestimentos da lareira estão equipados com vários termopares e elementos de refrigeração. O morto está situado abaixo da zona de coque ativa e (principalmente) abaixo das pistas. A parte superior do morto é em forma de cone com o topo arredondado na região entre as pistas. A inclinação do ápice do homem morto para as pistas é aproximadamente o mesmo que o ângulo de repouso do coque carregado. A lareira é ocupada principalmente por um leito de coque, que é uma parte do morto que se estende desde o nível da ventaneira.
Ferro líquido e escória pingando da zona coesiva se acumulam nos espaços vazios do morto. Como resultado da gravidade, os líquidos segregam em duas camadas diferentes com o ferro mais pesado na parte inferior e a escória mais leve na parte superior. Como tanto o ferro quanto a escória pingam continuamente da zona coesiva, as gotículas de ferro devem afundar através da camada de escória até o fundo. A camada superior consiste, portanto, em uma mistura de escória e gotículas de ferro. A porosidade do morto está entre 0,3 e 0,5, o que indica que apenas 30% a 50% do volume total está disponível para os líquidos se o morto encher totalmente a lareira. De fato, o morto pode sentar-se no fundo da lareira ou flutuar parcial ou completamente no banho líquido se a força de empuxo dos líquidos for suficiente para levantar o morto. Um homem morto parcialmente flutuante fica no fundo da fornalha central e dá origem a uma zona anular livre de coque nas bordas da fornalha, que oferece pouca resistência ao fluxo quando a fornalha é drenada. Assim, forma-se um fluxo circunferencial, sendo o principal motivo do desgaste em forma de “pé de elefante” na lareira.
Os estudos de dissecação de altos-fornos temperados mostraram que há um leito de coque quase estagnado no núcleo do forno entre as calhas e na fornalha. A zona estagnada, onde o coque desce com uma velocidade fortemente reduzida, recebeu o nome de “homem morto”, uma vez que se presumia anteriormente que essa zona não tinha efeito ativo sobre o funcionamento do processo. No entanto, essa suposição foi posteriormente comprovada como incorreta, pois estudos mais relevantes revelaram que o homem morto desempenha um papel fundamental na operação do alto-forno. Os estudos relacionados ao homem morto geralmente são realizados por meio de modelos físicos e/ou matemáticos, uma vez que o estado de homem morto não pode ser medido diretamente em um forno em operação devido às altas temperaturas, desgaste e ambiente extremamente hostil para as sondas de medição.
A parte superior do morto é em forma de cone com o topo arredondado na região entre as canaletas e pode se estender do fundo da lareira até muito acima do nível das ventaneiras. A altura do homem morto depende do tamanho do forno e das condições de operação, como taxa de coque, velocidade de sopro, carga descendente e taxa de renovação do homem morto. As perdas de massa/volume sólida devido à retração (redução) e fusão do minério de ferro afetam fortemente o padrão de fluxo sólido e, portanto, também o perfil do homem morto. Verificou-se também que a altura do homem morto diminui à medida que a taxa de consumo de sólidos aumenta.
O limite superior do homem morto tem sido objeto de muitas investigações teóricas e experimentais. Essas investigações mostraram que o homem morto está cercado por uma zona quase estagnada onde as partículas carregadas eventualmente se movem para a pista. O tamanho do homem morto é sensível se a operação do forno é realizada com ou sem 'injeção de carvão pulverizado'. As investigações também mostraram que o morto é renovado a partir de uma pequena região de influxo central no topo do morto. Portanto, uma boa permeabilidade ao homem morto pode ser mantida carregando coque grande e de alta qualidade no centro do alto-forno. Verificou-se também que a acumulação e remoção cíclica de líquidos na fornalha devido à operação de rosqueamento está intimamente relacionada ao processo de renovação do homem morto. As partículas de homem morto se movem gradualmente para a pista à medida que a operação de rosqueamento é repetida. A renovação das partículas ocorre de tal forma que as partículas 'velhas' são forçadas a sair do morto pela força de empuxo (exercida na parte submersa do morto) e as 'novas' partículas entram para preencher o homem morto através de sua superfície superior.
O estado de homem morto e a forma do fundo têm forte influência no desgaste dos revestimentos da fornalha e na drenagem do líquido da fornalha do alto-forno. O morto é submerso em um grande banho de líquido e está sujeito à flutuação líquida exercida sobre ele. À medida que a flutuabilidade do líquido se torna suficiente para levantar o homem morto, as zonas livres de coque são formadas abaixo do homem morto, criando assim uma passagem livre para os fluxos de líquido. O morto tem um comportamento dinâmico à medida que se move com variação de nível de líquido. Verificou-se que o movimento do morto é afetado pela histerese à medida que sobe e desce na lareira.
A forma do homem morto é determinada por vários fatores. Pode ser estimado pelo equilíbrio entre a força que pressiona o morto e as forças de empuxo do ferro e da escória na lareira. A força de empuxo é estimada de forma relativamente direta, pois é uma função do nível do líquido e da porosidade do homem morto. No entanto, a força de ação para baixo, que geralmente é expressa na forma de uma pressão, depende das condições do forno, como peso da carga, comprimento da pista, retenção de líquido e arrasto de gás. O peso da carga acima do nível da ventaneira é compensado pela pressão de elevação do gás que flui para cima e a pressão de atuação para baixo sob as canaletas (ou seja, região sob as canaletas) é, portanto, atribuída apenas ao peso morto. Por outro lado, a pressão de atuação descendente na região central é formulada em função do peso morto, retenção de líquido e pressão dinâmica do fluxo de partículas. A pressão dinâmica, que é causada pelo fluxo de partículas convergentes dentro da zona de coque ativa, é assumida a diminuir linearmente ao longo da dimensão radial do centro do forno para a frente da pista. Geralmente é visto que o homem morto flutua mais alto sob as pistas. A distribuição da pressão de ação descendente desempenha um papel crucial na formação do fundo do homem morto. Alguns estudos classificaram o estado flutuante do homem morto em quatro categorias:(i) sentado, (ii) flutuando parcialmente na parede, (iii) flutuando completamente com um fundo plano e (iv) flutuando completamente, mas flutuando mais alto perto da parede. .
Torneamento do alto-forno
A perfuração de um alto-forno é necessária não apenas para entregar os produtos do alto-forno, mas também essencial para a segurança do forno e dos operadores na casa de fundição. O vazamento de alto-forno, também referido às vezes como fundição ou drenagem, é um processo que remove o metal quente e a escória líquida da fornalha do alto-forno. A tecnologia atual de rosqueamento de alto-forno emprega a prática de pool completo. Esta prática refere-se à tecnologia de manter a calha cheia de gusa e escória líquida durante curtos períodos em que o forno não está sendo rosqueado. Na torneira seguinte, a calha ainda está líquida, facilitando a separação do ferro e da escória, além de preservar o calor na calha, resultando em um ferro mais limpo e mais quente entregue à aciaria via transporte ferroviário em open top revestido de refratário ou conchas de torpedos.
O processo de rosqueamento determina criticamente a pressão do gás no forno e as quantidades residuais de ferro líquido e escória na fornalha. A drenagem deficiente da fornalha geralmente leva a uma operação instável do forno, que geralmente está ligada a perdas acentuadas na produtividade do forno e na vida útil da campanha. Uma drenagem ineficiente também dá origem a uma acumulação excessiva de líquidos e, portanto, a níveis elevados de líquidos na lareira. Se o líquido (escória) se aproximar do nível das ventaneiras, o fluxo de gás redutor no bosh é severamente perturbado, muitas vezes resultando em descida irregular da carga conhecida como suspensão e deslizamento.
Um ciclo de rosqueamento começa quando o furo é aberto e é encerrado tapando o furo com a massa do furo quando o gás do forno explode. Ao final do rosqueamento, a interface gás-escória se inclina para baixo em direção ao furo e uma quantidade considerável de escória permanece acima do nível do furo. A fase de ferro pode ser drenada de níveis abaixo do furo por causa do grande gradiente de pressão que se desenvolve perto do furo na fase de escória viscosa. A interface escória-ferro média é, portanto, inferior ao nível do furo de passagem. Dependendo de vários fatores, como taxas de produção de líquido, volume do forno e estratégias de extração, o estágio inicial de um ciclo de extração varia e pode ser categorizado da seguinte forma.
Um requisito primário do rosqueamento é garantir de forma confiável a taxa desejada de produtos do forno. Assim, é importante estabelecer os fatores que influenciam a taxa de sangria. Normalmente, nos grandes altos-fornos, taxas de vazamento de 7 ton/min e velocidades de vazamento de líquido de 5 m/s, em furos de 70 mm de diâmetro e 3,5 m de comprimento são normalmente encontrados. A condição do furo e o comprimento do furo influenciam fortemente a taxa de rosqueamento. Quando o alto-forno está em operação, o taphole é completamente preenchido com um material refratário conhecido como massa do taphole.
Fatores importantes que muitas vezes causam dificuldade durante a operação de rosqueamento são (i) defeitos nas pistolas e brocas, ou alinhamento defeituoso destes com o furo, (ii) má condição do furo, bico de rosqueamento, skimmer, comportas e inclinações, oscilantes ou outros corredores , (iii) capacidade inadequada das panelas para transporte de gusa, e (iv) problema no sistema de granulação da escória bem como espaço inadequado na cava de escória.
O cronograma de rosqueamento depende da quantidade de ferro líquido e escória, tamanho da fornalha, taxa de rosqueamento e as operações preparatórias necessárias entre cada operação de rosqueamento. Imediatamente antes de rosquear normalmente o furo, o correto funcionamento, posição e alinhamento das pistolas e brocas devem ser verificados para garantir que estejam corretamente alinhados ao furo (se necessário, suas posições podem ser corrigidas). A vantagem desta prática é que ela permite uma verificação final de defeitos ou ajustes ainda não observados e possibilita saná-los. O furo é aberto com brocas de determinados tamanhos, dependendo das condições de operação e, em alguns casos, a última parte do plugue é encaixada. Se o furo não for longo o suficiente, o furo deve ser aberto por uma lança de oxigênio , tomando todas as precauções necessárias para o uso de oxigênio.
A batida pode ser perturbada se o jato de metal quente fluir para os canais úmidos, pois isso pode causar ebulição nos canais, acompanhada de explosões. Portanto, é essencial realizar verificações minuciosas e secar bem as calhas e canais, pois a fervura nos canais muitas vezes atinge proporções tais que a operação de rosqueamento deve ser interrompida. Esta é uma das razões pelas quais as saídas de fuga devem ser mantidas livres o tempo todo.
Interromper o rosqueamento enquanto ele está em andamento é uma operação que exige potência máxima da pistola de furo (já que o tampões tem que neutralizar a força total do fluxo de metal fundido). Em alguns casos é necessário reduzir o jateamento e a pressão superior o suficiente para permitir que o taphole seja tapado. Reparos improvisados rápidos são realizados nas partes danificadas das calhas, usando material seco.
Se a pistola de taphole for afastada do taphole muito cedo, existe o perigo de que a argila de tamponamento injetada no taphole possa ser expelida repentinamente com uma explosão, pois o material pode não ter tido tempo de solidificar. Por isso, os operadores da fundição devem ficar fora da ‘linha de fogo’, caso ocorram tais explosões.
O fluxo de escória que antecede o gusa no início do rosqueamento também pode causar distúrbios. Neste caso, o operador da fundição é obrigado a fazer ajustes na área imediata do furo e do canal, para direcionar a escória para os canais destinados a transportá-la. Esta é uma das razões pelas quais deve haver um espaço livre disponível na frente da torneira em ambos os lados do canal de ferro, e esse espaço deve ser o maior possível.
O principal trabalho do operador da fundição, durante as operações normais de rosqueamento, é garantir que o fluxo de metal quente e escória líquida nas panelas de transporte ou instalações adjacentes seja suave e sem incidentes. O tamanho e inclinação dos corredores devem ser relacionados às demais características técnicas do alto-forno. No entanto, existe a possibilidade de estagnação e transbordamento de gusa e/ou escória, e isso exige ação imediata do operador da fundição. As ferramentas utilizadas nesta operação devem estar completamente secas; caso contrário, a água pode vaporizar repentinamente, levando a uma explosão.
Também é importante verificar com muito cuidado a condição das aberturas de descarga nas panelas, pois a matéria sólida pode ser transportada pelo fluxo de metal quente e pode bloquear as comportas que têm uma seção transversal relativamente pequena.
O furo pode ser obstruído (por exemplo, por coque) durante a extração. A furadeira é normalmente usada para desalojar tais obstruções, mas se isso falhar, são usadas hastes longas (rabbles). Esta operação é perigosa devido à possibilidade de explosões repentinas de metal quente e escória. Portanto, é essencial que os operadores da fundição tenham acesso imediato a uma saída de emergência livre de quaisquer obstáculos.
O maior cuidado deve ser tomado na construção dos corredores de escória. Devem ser dotados de comportas capazes de reter o metal quente e o coque carregados com a escória para minimizar o perigo de explosões durante a granulação da escória.
Uma das tarefas mais importantes dos operadores de fundição envolvidos na operação de rosqueamento é supervisionar o enchimento das panelas de metal quente, certificando-se de que este não ultrapasse um nível em que o conteúdo possa derramar durante o transporte ou transbordar durante o enchimento. Como as panelas geralmente são enchidas uma após a outra, o operador deve ser capaz de direcionar o fluxo de metal quente para os canais apropriados. As calhas e bicas basculantes e basculantes também têm a vantagem de minimizar o risco de umidade no revestimento refratário, que é muito maior nas comportas convencionais, pois o revestimento é renovado após cada rosqueamento.
Perto do final da rosqueamento, o fluxo de metal quente torna-se irregular e é acompanhado por uma forte rajada de ar e à medida que a fornalha se esvazia, esses fenômenos se tornam mais frequentes. Ao mesmo tempo, o metal quente e a escória se espalham e podem finalmente cobrir toda a área da fundição. Para evitar isso, o taphole deve ser tampado o mais rápido possível. O operador move a pistola de taphole até o taphole e tapa o furo injetando a quantidade correta de argila de tamponamento.
Processo de manufatura
- Escória de alto forno e seu papel na operação do forno
- Aspectos importantes do projeto de alto-forno e equipamentos auxiliares associados
- Sistema de automação, medição e controle de processos de alto forno
- Geração e uso de gás de alto-forno
- Produtividade do Alto Forno e os Parâmetros Influenciadores
- Proteção do Revestimento do Lar do Alto Forno pela Adição de TiO2
- Operação de alto-forno e escória de alta alumina
- Irregularidades do alto-forno durante a operação
- Sistema de resfriamento do alto-forno
- Fabricação de ferro por alto-forno e emissões de óxido de carbono