Efeito de defeitos de subsuperfície induzidos por usinagem na evolução de deslocamento e propriedades mecânicas de materiais por nanorredentação
Resumo
Os defeitos de subsuperfície têm um impacto significativo na precisão e no desempenho das nanoestruturas. Neste artigo, simulação de dinâmica molecular de nanodentação é realizada para investigar o efeito de defeitos de subsuperfície induzidos por usinagem na evolução de deslocamento e propriedades mecânicas de materiais, em que o modelo de espécime com defeitos de subsuperfície é construído por nano corte em conformidade com a realidade. O mecanismo de formação de defeitos de subsuperfície e o mecanismo de interação entre os defeitos induzidos por máquina e a evolução do deslocamento são discutidos. A dureza e o módulo de elasticidade de Young de espécimes de cobre de cristal único são calculados. Os resultados da simulação indicam que existem resíduos de estrutura de defeitos estáveis na subsuperfície da peça de trabalho, como aglomerados atômicos, falha de empilhamento tetraédrica e deslocamentos de haste de escada. O processamento secundário de nanodentação pode restaurar defeitos internos da peça de trabalho, mas o dano subterrâneo na área de processamento secundário é agravado. A dureza de nanodentação dos espécimes aumenta com a introdução de defeitos de subsuperfície, o que resulta na formação do efeito de endurecimento por trabalho. A existência de defeitos de subsuperfície pode enfraquecer a capacidade do material de resistir à deformação elástica, na qual a evolução mútua entre deslocamentos e defeitos de subsuperfície desempenha um papel importante.
Histórico
Fabricação de ultra-precisão em escala nanométrica é amplamente considerada um método eficaz para obter nano-componentes com precisão dimensional submicron e qualidade de superfície em nanoescala [1]. Alguns defeitos de subsuperfície estáveis são deixados dentro da peça após a fabricação [2,3,4,5]. Os defeitos de subsuperfície não afetam apenas a precisão do processamento e a qualidade da superfície, mas também afetam criticamente as propriedades mecânicas e a vida útil dos nano-componentes. Muitos estudos sobre defeitos de subsuperfície têm sido realizados pelo método de dinâmica molecular (MD), principalmente com foco na formação e evolução de defeitos de subsuperfície s [6, 7], a espessura da camada de defeitos de subsuperfície (SSD) [8, 9], e a influência dos defeitos de subsuperfície na integridade da superfície [10, 11]. No entanto, o efeito dos defeitos de subsuperfície nas propriedades mecânicas dos materiais da peça é menos estudado. As propriedades mecânicas das nanoestruturas são críticas para seu desempenho e vida útil. Portanto, o efeito dos defeitos de subsuperfície nas propriedades mecânicas dos materiais tornou-se as principais questões a serem investigadas.
Muitas pesquisas têm sido conduzidas para deliberar a camada SSD por simulação de dinâmica molecular do processo de nano-corte. Narayanan [12] estudou a formação da falha de empilhamento tetraédrica (SFT) em ouro de cristal único e introduziu o mecanismo de SFT induzido por deformação. Inamura [13] explorou a formação de cavacos e a deformação por deslizamento do material durante o processo de nano-corte e apontou que a formação de cavacos é induzida principalmente pela deformação por cisalhamento-deslizamento. Pei [14] estudou o efeito dos parâmetros de corte na evolução do deslocamento e corte forçado durante o processo de nano corte e descobriu que quando a peça é maior que 40 nm, o efeito do tamanho não é significativo. Dai [15] e Liu [16] adotaram simulação MD e métodos experimentais, respectivamente, para estudar a influência da estrutura da ferramenta de diamante e o efeito do tamanho na evolução dos defeitos de subsuperfície da peça. Os estudos anteriores mostram que existem defeitos de subsuperfície estáveis na peça após o nano-corte. Os parâmetros de corte e os parâmetros de geometria da ferramenta têm grande influência na espessura e evolução da camada de dano subsuperficial e até mesmo na precisão do processamento. No entanto, as propriedades mecânicas dos materiais da peça não podem ser calculadas analisando os dados relevantes obtidos por nanocorte.
A nanodentação é uma técnica eficaz para caracterizar as propriedades mecânicas como dureza e módulo de elasticidade [17]. Vários estudos sobre nanoindentação têm sido realizados para avaliar o desempenho de propriedades mecânicas por meio de modelos experimentais e teóricos. Zimmerman [18] analisou a emissão de deslocamento no processo de nanoindentação pelo vetor de deslizamento. Ruestes [19] estudou a nanodentação de Fe de cristal único por simulação MD e descobriu que a geração de deslocamento em subsuperfície é necessária para remover o material da zona de indentação. Huang [20] realizou simulações MD de nano indentação em matriz de diamante de cristal único e descobriu que a deformação do material de diamante sob indentação foi dominada pela nucleação e propagação de loops de deslocamento 〈110〉 {111}. Sharma [21] construiu um modelo de partícula dura artificialmente em matriz de cobre e analisou a influência da partícula dura na evolução de defeitos de subsuperfície no processo de usinagem. Peng [22] investigou os mecanismos de fortalecimento de revestimentos de grafeno em substrato de Cu por nanoindentação, que é resultado do efeito de homogeneização de tensões gerado pela interface. A partir da análise acima, pode-se ver que os estudos anteriores sobre o efeito de defeitos de subsuperfície são baseados principalmente em materiais de cristal perfeito ou defeitos hipotéticos de construção artificial, o que está longe dos defeitos reais de subsuperfície. Portanto, construir o modelo da peça de trabalho com defeitos de subsuperfície em realismo é essencial para analisar a influência dos defeitos de subsuperfície nas propriedades mecânicas da peça de trabalho.
Neste trabalho, o método de nano-corte foi adotado para obter o modelo da peça com defeitos de subsuperfície de acordo com as características práticas. Com base nisso, a simulação de nanodentação foi realizada para estudar o efeito de defeitos de subsuperfície nas propriedades mecânicas do cobre de cristal único. Em primeiro lugar, a formação e o mecanismo de evolução de defeitos de subsuperfície durante o processo de nano-corte serão discutidos, e as estruturas de defeito típicas de subsuperfície da peça após o nano-corte serão analisadas. Em segundo lugar, será analisado o mecanismo de interação entre defeitos de subsuperfície induzidos por usinagem e nucleação por deslocamento durante a indentação. Em terceiro lugar, com base nos dados de deslocamento de carga obtidos por nano indentação, a dureza e o módulo de elasticidade de Young de espécimes de cobre de cristal único serão calculados. Finalmente, algumas novas conclusões serão resumidas.
Métodos
Modelo de simulação
A fim de investigar o efeito de defeitos de subsuperfície nas propriedades mecânicas de materiais em nano-usinagem, o modelo de espécime com defeitos de subsuperfície deve ser construído. Nesta pesquisa, ela é realizada por simulação MD do processo de nano-corte. Em primeiro lugar, o modelo de simulação MD é estabelecido e a simulação do processo de nano corte é realizada. Em seguida, a amostra e a ferramenta de corte relaxaram por tempo suficiente durante a simulação MD . Finalmente, alguns defeitos estáveis permaneceram na subsuperfície da peça de trabalho. O diagrama esquemático dos modelos de simulação tridimensionais MD é mostrado na Fig. 1, em que o modelo de nano corte é mostrado na Fig. 1a e o modelo de nano indentação com defeitos de subsuperfície é mostrado na Fig. 1b. Na Fig. 1, os materiais da peça de trabalho e da amostra são de cobre de cristal único e a ferramenta e o penetrador são materiais de diamante. A ferramenta de lâmina de arco de diamante é usada no processo de nano corte, e o raio da borda da ferramenta é de 3 nm. O penetrador tem forma hemisférica em processo de nanodentação e o diâmetro é de 6 nm. A peça de trabalho e a amostra são divididas em três partes, que são camada de Newton, camada de temperatura e camada limite, respectivamente. Para reduzir o efeito de tamanho e o efeito de contorno, a condição de contorno periódica (PBC) é adotada na direção [010] do sistema de simulação. Para evitar a interação inicial entre a ferramenta e a peça de trabalho, a ferramenta de corte é colocada 3 nm na parte superior direita da peça de trabalho e o penetrador é colocado 6 nm até a amostra. Os parâmetros de simulação detalhados são mostrados na Tabela 1.
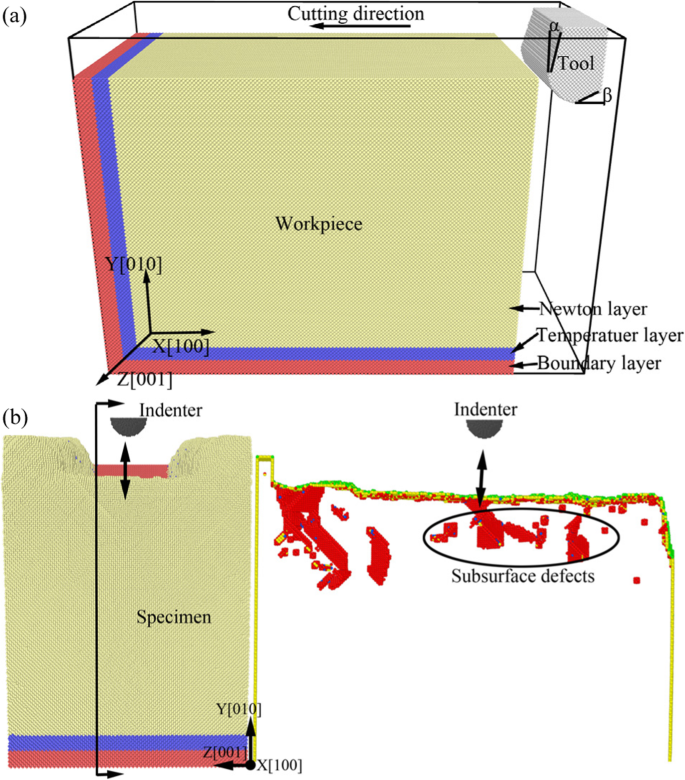
Diagrama esquemático de modelos de simulação 3D MD de cobre de cristal único para nano corte e nano indentação. a O modelo para o processo de nano corte. b O modelo para o processo de nanodentação com defeitos de subsuperfície
Funções potenciais interatômicas
Nesta pesquisa, as simulações tridimensionais de MD foram realizadas por um simulador atômico / molecular massivamente paralelo em grande escala (LAMMPS). A computação paralela foi realizada com a ajuda da biblioteca de interface de passagem de mensagem. O potencial Morse, o potencial Embedded-atom Method (EAM) e o potencial Tersoff são usados na simulação, os quais são invocados a partir do pacote de software LAMMPS. A interação entre os átomos de Cu na peça de trabalho e os átomos de C na ferramenta é calculada pelo potencial de Morse, que é mostrado na Eq. 1 [23].
$$ u \ left ({r} _ {ij} \ right) =D \ left [\ exp \ left (-2 \ alpha \ left ({r} _ {ij} - {r} _0 \ right) \ right ) -2 \ exp \ left (- \ alpha \ left ({r} _ {ij} - {r} _0 \ right) \ right) \ right] $$ (1)
onde r 0 , α e D respectivamente, são espaçamento atômico, módulo de elasticidade e energia de ligação. O valor é mostrado na Tabela 2.
A função interatômica entre os átomos de Cu na peça de trabalho é descrita pelo potencial EAM que é mostrado nas Eqs. 2, 3 [24, 25].
$$ E =\ sum \ limits_i ^ N \ left [F \ left ({\ rho} _i \ right) + \ sum \ limits_ {j> i} ^ Nu \ left ({r} _ {ij} \ right) \ right] $$ (2) $$ {\ rho} _i =\ sum \ limits_jf \ left ({r} _ {ij} \ right) $$ (3)
A interação entre os átomos de carbono na ferramenta de diamante é calculada pelo potencial Tersoff que é mostrado nas Eqs. 4, 5 [26].
$$ E =\ frac {1} {2} \ sum \ limits_ {i \ ne j} {V} _ {ij} $$ (4) $$ {V} _ {ij} ={f} _c \ left ({r} _ {ij} \ right) \ left [{V} _R ^ {\ hbox {'}} \ left ({r} _ {ij} \ right) + {b} _ {ij} {V} _A \ esquerda ({r} _ {ij} \ direita) \ direita] $$ (5)
onde f c ( r ij ) é a função de truncamento entre átomos, V A ( r ij ) é o termo de potencial duplo de absorção, V R ( r ij ) é o potencial duplo do termo de repulsão, e r ij é a distância atômica entre o átomo i e átomo j .
Métodos de análise de defeito
No nano corte de cobre de cristal único, deformações e deslocamentos são nucleados na subsuperfície da peça. Neste artigo, o parâmetro de centrossimetria (CSP) é introduzido para analisar a nucleação de deslocamento e a evolução do defeito da peça de trabalho. Para materiais cúbicos de centro de face (FCC), o valor CSP pode ser calculado pela Eq. 6 [27].
$$ CSP =\ sum \ limits_ {i =1} ^ 6 {\ left | {R} _i + {R} _ {i + 6} \ right |} ^ 2 $$ (6)
onde R i tem o mesmo comprimento de átomos vizinhos e R i + 6 é a direção oposta dos átomos vizinhos. Os valores CSP do cristal FCC, deslocamento parcial, falha de empilhamento e átomos da superfície são 0, 2,1, 8,3 e 24,9, respectivamente [27].
O método CSP é capaz de identificar o escalonamento atômico, mas não pode reconhecer o estado da estrutura cristalina atômica local da peça de trabalho. Portanto, a análise de vizinho comum (CNA) é introduzida para identificar o defeito da estrutura cristalina local. No método CNA original, proposto por Honeycutt e Andersen [28], as várias estruturas são representadas por diagramas. Atualmente, existem cinco tipos de padrões CNA em OVITO [29], onde as estruturas cristalinas locais são identificadas como centro cúbico da face (FCC), hexagonal compactado (HCP), cúbico centrado no corpo (BCC), icosoédrico (ICO), e desconhecido, respectivamente. Neste artigo, o algoritmo de extração de deslocamento (DXA) [30] também é apresentado para analisar a evolução do defeito de deslocamento. Por DXA, as diferentes estruturas de cristal na peça de trabalho serão marcadas com cores diferentes e os defeitos de deslocamento na peça de trabalho serão representados por linhas de cores diferentes.
Resultados e discussão
Evolução do defeito da subsuperfície no processo de nanodecorte
No processo de nano-corte, sob a ação de extrusão e cisalhamento da ferramenta de corte na peça, o material da superfície da peça com a espessura da profundidade de corte é removido e uma nova superfície usinada com uma certa precisão de tamanho e qualidade de superfície é formada. A deformação elástica-plástica complexa, incluindo a deformação por tensão e a deformação térmica, ocorre na superfície e na subsuperfície da peça de trabalho, acompanhando a transformação de energia e a concentração de tensão. Portanto, a camada de dano subsuperficial é formada e o chip é removido. A Figura 2 mostra as vistas instantâneas da evolução do defeito de subsuperfície e a remoção de material durante o processo de nano-corte de cobre de cristal único. Na Fig. 2, os átomos são coloridos pelo valor dos resultados da análise CSP e CNA. Na Fig. 2a e c, os átomos amarelos, verdes, vermelhos e azuis são átomos de superfície, átomos de defeitos de superfície, átomos de defeito de subsuperfície e átomos de FCC. Pode ser visto na Fig. 2 que uma abundância de estruturas de defeito típicas são formadas na subsuperfície da peça de trabalho durante o processo de nano-corte, como defeitos pontuais, defeitos de vacância, falhas de empilhamento, defeitos de agrupamento, deslocamentos prismáticos e loop de deslocamento do parafuso.
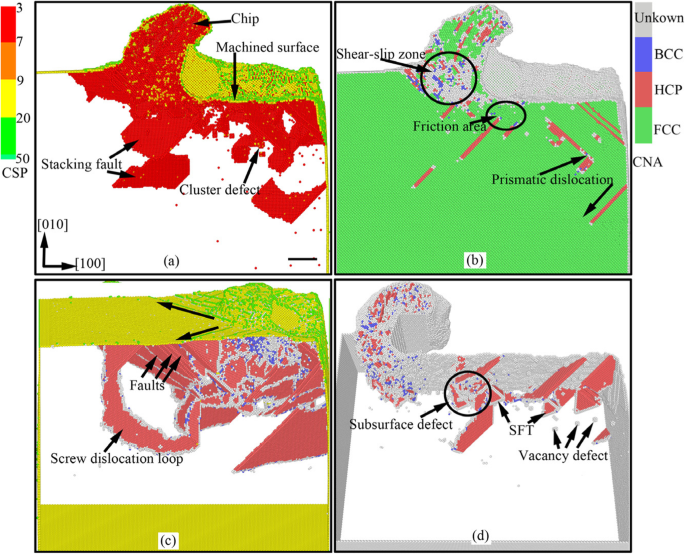
Visualizações instantâneas da evolução do defeito de subsuperfície durante o processo de nano corte de cobre de cristal único (cor online, escala de barra 5 nm). As distâncias de corte de a , b , c , e d respectivamente são 18 nm, 18 nm, 6 nm e 32 nm
Devido ao efeito de compressão e cisalhamento da ferramenta de corte, a deformação de cisalhamento é gerada para os átomos na frente da face de saída e a zona primária de cisalhamento é formada na peça de trabalho durante o processo de nanocorte, como mostrado na Fig 2b. Alguns desses átomos escorregam ao longo da face de saída e o chip de corte é formado como mostrado na Fig. 2a. Alguns se movem para baixo e a superfície usinada é formada sob o atrito de compressão da face do flanco da ferramenta, como mostrado na Fig. 2b. Outros se movem para dentro e os defeitos de subsuperfície são formados, como falhas de empilhamento, defeitos de agrupamento e deslocamentos prismáticos, mostrados nas Fig. 2a e b.
Por conta do atrito e extrusão da superfície do flanco da ferramenta, o acúmulo de energia ocorre para os átomos próximos à face do flanco e os átomos se transformam em átomos de alta energia. Quando a energia atômica é ultrapassada um determinado nível, a energia carregada pelos átomos energéticos será liberada e o deslocamento se formará sob a direção dos átomos energéticos. Portanto, muitos deslocamentos são formados na área de atrito da face do flanco, mostrado na Fig. 2d. Com a superfície usinada sendo formada, os deslocamentos nucleados, estendem-se e aniquilam-se na subsuperfície. Finalmente, as estruturas de defeitos, como falhas de empilhamento, SFT e defeitos de vacância, são deixadas na subsuperfície, conforme indicado na Fig. 2d. As falhas de empilhamento são nucleadas na zona de cisalhamento abaixo da ferramenta de corte, em seguida, estendidas para a peça de trabalho e, finalmente, aniquiladas na superfície livre da peça de trabalho. Eventualmente, a linha de deslocamento é formada na superfície da peça. E a linha de deslocamento é estendida ao longo de \ (\ left [\ overline {1} 0 \ overline {1} \ right] \), \ (\ left [\ overline {1} 01 \ right] \), e [101] instruções. O loop de deslocamento do parafuso, que está localizado na borda da zona de cisalhamento-deslizamento, é composto por várias falhas de empilhamento e uma série de deslocamentos do parafuso. O deslocamento do parafuso é formado sob a condução do estado de tensão de compressão da zona de cisalhamento-deslizamento [11].
No processo de nanocorte, os deslocamentos são nucleados e estendidos sob a ação da ferramenta de corte. Acompanhando a agregação e liberação de energia, a força de corte é oscilada com o aumento da distância de corte, que é mostrada na Fig. 3 em três dimensões. Na Fig. 3, as curvas preta, vermelha e azul, respectivamente, são a força de alimentação (Fx), a força de retorno (Fy) e a força tangencial (Fz). Pode-se ver na Fig. 3 que o processo de corte é dividido em dois períodos, que são o estágio de corte inicial e o estágio de corte estável. Durante o estágio inicial de corte, a força de avanço e a força de retorno aumentam rapidamente, retilinearmente. O valor máximo da força de alimentação é atingido em mais de 1100 nN, mas a força de retorno acaba de chegar em torno de 600 nN. Quando a ponta da ferramenta corta a peça completamente, a superfície usinada é formada, mostrado como o primeiro pequeno gráfico marcado como Superfície usinada na Fig. 3. Em seguida, o processo de nanocorte é transferido para o estágio de corte estável. No estágio de corte estável, todas as três forças estão flutuando em suas posições de equilíbrio. A força de alimentação média é de cerca de 1000 nN, e a força de retorno média é de apenas cerca de 500 nN. Pode-se observar na Fig. 3 que a força de avanço diminui rapidamente na distância de corte de 20 nm. É porque o acúmulo de energia é atingido em um certo nível que é a energia de deformação crítica da rede, mostrado como o segundo pequeno gráfico na Fig. 3. Enquanto isso, uma grande resistência é atuada na ferramenta de corte que resulta na força de corte sendo um valor de pico. Em seguida, a energia é liberada, resultando na emissão de deslocamento, e a força de corte é diminuída, mostrado no terceiro pequeno gráfico da Fig. 3. Portanto, a força de corte é flutuada durante o estágio de corte estável. A nucleação, extensão e aniquilação dos deslocamentos levam à flutuação da força de corte e resultam no defeito subsuperficial existente na peça, por fim.
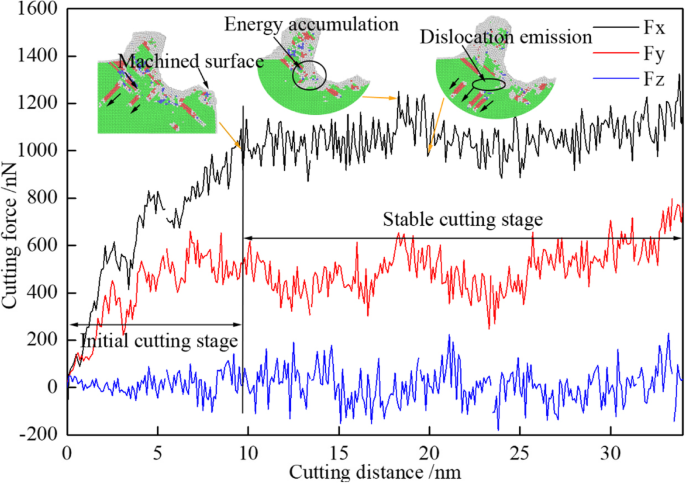
A curva de variação da força de corte com a distância de corte (cor online). As curvas preta, vermelha e azul, respectivamente, são a força de alimentação (Fx), a força de retorno (Fy) e a força tangencial (Fz)
Para investigar detalhadamente a evolução e a emoção dos defeitos de deslocamento em subsuperfície da peça durante o processo de nano corte, a distribuição do deslocamento e sua variação com a distância de corte são minuciosamente analisadas pelo método CNA. A evolução do defeito subsuperficial da peça em uma determinada área é mostrada na Fig. 4, em que as distâncias de corte da Fig. 4a, b, c, d, e e f respectivamente são 8 nm, 10 nm, 12 nm, 20 nm , 24 nm e 32 nm. Pode ser visto na Fig. 4a que muitos defeitos de deslocamento são nucleados na zona de cisalhamento sob a ação de cisalhamento de extrusão da ferramenta de corte durante o estágio preliminar do processo de corte. Particularmente, um deslocamento em forma de V e uma falha são formados sob a ação motriz de tensão atômica e energia na zona de cisalhamento-deslizamento, mostrada na Fig. 4b. No processo de processamento subsequente, a zona de cisalhamento-deslizamento é movida para a frente com a ferramenta de corte em movimento. Devido à diminuição da energia de deformação, a falha é gradualmente aniquilada. Durante o movimento da ferramenta de corte para frente, a zona de fricção da face do flanco é movida para perto da falha. E a rugosidade da superfície usinada é formada sob a extrusão e fricção da face do flanco. Em seguida, a falha é continuada aniquilando e sendo gradualmente destacada da superfície da peça de trabalho, como mostrado na Fig. 4d. Finalmente, a falha é transformada em defeito de agrupamento que existe de forma constante na subsuperfície da peça de trabalho. Da mesma forma, o deslocamento em forma de V formado evolui gradualmente para SFT sob a interação de duas falhas de empilhamento e um bloqueio de deslocamento. Esses defeitos estáveis são compostos juntos pela camada deformada subsuperficial, conforme mostrado na Fig. 4e e na Fig. 4f.
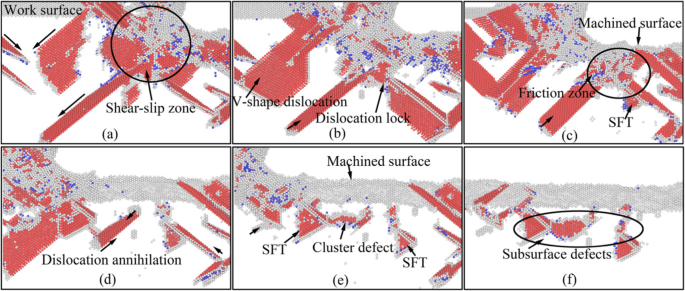
Evolução de defeitos de subsuperfície da peça de trabalho (cor online). As distâncias de corte de a , b , c , d , e , e f respectivamente são 8 nm, 10 nm, 12 nm, 20 nm, 24 nm e 32 nm
Como sabemos, a liberação de tensão residual e recuperação de defeito interno ocorrerá na peça de trabalho após o tratamento de envelhecimento. Na nanofabricação real, alguns dos defeitos de subsuperfície formados durante o processamento desaparecerão após o processo de usinagem. Para simular o estado da peça após o tratamento de envelhecimento, o relaxamento da dinâmica molecular é realizado no sistema de corte por um longo tempo. O diagrama de distribuição do defeito residual em subsuperfície da peça após relaxamento MD por um longo tempo é mostrado na Fig. 5, na qual os átomos são coloridos de acordo com os resultados da análise pelos métodos CSP e CNA. Pode-se observar na Fig. 5 que as luxações primárias são aniquiladas após o relaxamento. Os defeitos de vacância, falhas de empilhamento, aglomerado atômico, deslocamento prismático, deslocamento do parafuso, SFT e deslocamento da haste da escada existem na subsuperfície da peça, conforme mostrado na Fig. 5. De acordo com a análise acima, esses defeitos, que são formados sob a indução de tensões internas complexas e a interação de defeitos de deslocamento afetarão a precisão do tamanho e a qualidade da superfície da peça após o nanoprocessamento.
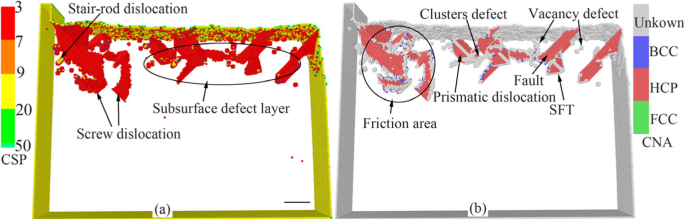
Distribuição de defeitos residuais na subsuperfície da peça após o corte nanométrico (cor online, barra de escala 5 nm). a Os átomos amarelos, verdes, vermelhos e azuis são átomos de superfície, átomos de defeitos de superfície, átomos de defeito de subsuperfície e átomos de FCC. b Os átomos verdes, vermelhos, cinzas e azuis são FCC, HCP, desconhecido e estrutura BCC
Teste de nanodentação em amostra de cobre com defeitos de subsuperfície induzidos por usinagem
Os defeitos residuais de subsuperfície induzidos por usinagem governam as propriedades mecânicas da superfície, especialmente a dureza e o módulo de Young. Portanto, a investigação da nucleação e interação de luxações durante a nanoindentação parece fortemente necessária. A fim de investigar a influência dos defeitos de subsuperfície induzidos por usinagem nas propriedades mecânicas do cobre monocristalino, o processo de nanodentação na amostra após o nano corte foi colocado em prática com os mesmos parâmetros da simulação de nano corte. O resultado da simulação é mostrado nas Figs. 6, 7, 8, 9 e 10. A imagem atômica instantânea da distribuição do defeito subsuperficial no estado inicial de nano-indentação é mostrada na Fig. 6. Pode-se ver na figura que existem vários SFTs, um em forma de V deslocamento, alguns deslocamentos prismáticos e alguns defeitos de agrupamento abaixo do penetrador. Esses defeitos de subsuperfície podem afetar a nucleação do deslocamento e a expansão da peça de trabalho durante o processo de nanodentação. E então as propriedades mecânicas do material da peça são alteradas.
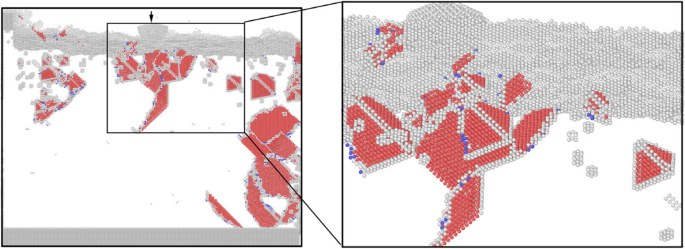
Distribuição de defeitos subterrâneos da peça de trabalho no estado de indentação inicial (cor online). Os átomos vermelho, cinza e azul são HCP, desconhecido e estrutura BCC
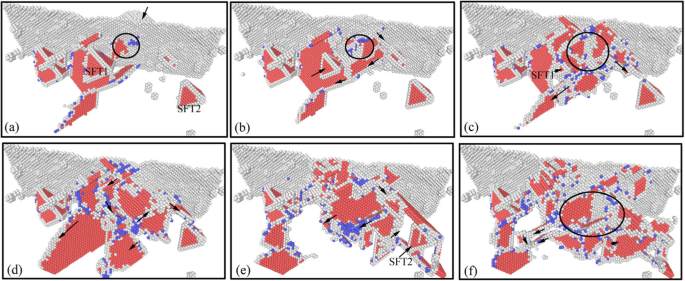
Evolução de defeitos de deslocamento de subsuperfície no processo de carregamento de nanodentação (cor online). As profundidades de indentação correspondentes de a - f são 0 nm, 0,5 nm, 1 nm, 2 nm, 3 nm e 4 nm, respectivamente
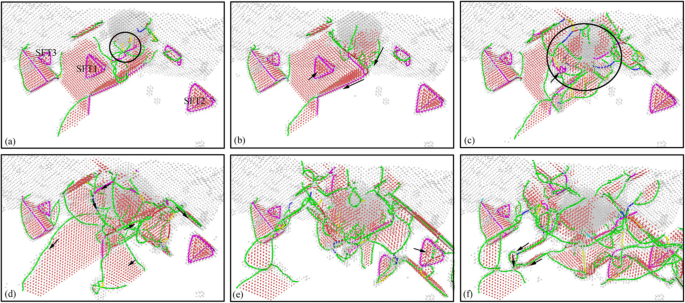
Distribuição de deslocamentos de subsuperfície no processo de carregamento de nano-indentação (cor online). As profundidades de indentação correspondentes de a - f são 0 nm, 0,5 nm, 1 nm, 2 nm, 3 nm e 4 nm, respectivamente. Esquema de cores:azul profundo para luxações perfeitas, verde para luxações Shockley, rosa para luxações Stair-rod, amarelo para luxações Hirth, azul claro para luxações Frank e vermelho para luxações não identificadas
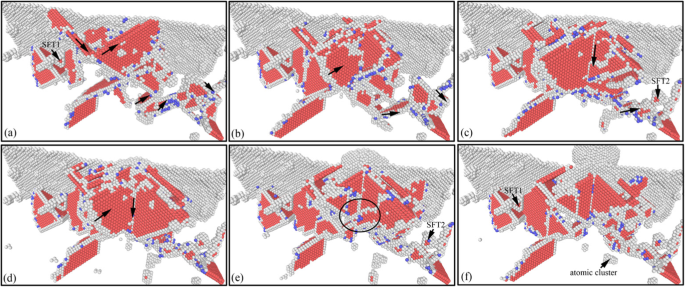
Evolução de defeitos de subsuperfície no processo de descarga de nanodentação (cor online). As profundidades de indentação correspondentes de a –F são 4 nm, 3 nm, 2 nm, 1 nm, 0 nm e -1 nm, respectivamente
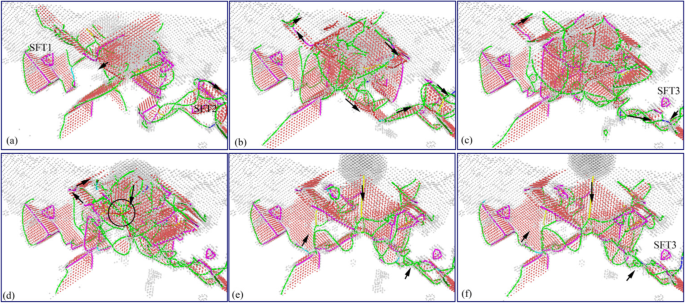
Distribuição de deslocamentos de subsuperfície no processo de descarga de nano-indentação (cor online). As profundidades de indentação correspondentes de a - f são 4 nm, 3 nm, 2 nm, 1 nm, 0 nm e -1 nm, respectivamente. Esquema de cores:azul profundo para luxações perfeitas, verde para luxações Shockley, rosa para luxações Stair-rod, amarelo para luxações Hirth, azul claro para luxações Frank e vermelho para luxações não identificadas
A imagem da evolução atômica de deslocamentos de subsuperfície durante o processo de carregamento de nano-indentação é mostrada na Fig. 7. Pode ser visto na Fig. 7a que a nucleação inicial do deslocamento ocorre na superfície da amostra quando o indentador entra em contato com a superfície do espécime. Com a pressão descendente do penetrador, os deslocamentos nucleados são expandidos gradualmente. Enquanto isso, sob a influência da tensão exercida pelo indentador, um grande número de deslocamentos nucleados e movidos ao longo do sistema de deslizamento, conforme mostrado na Fig. 7b. Sob a interação entre as luxações recém-formadas e defeitos subsuperficiais originais, alguns defeitos simples desaparecem gradualmente, e as luxações em forma de V continuam a evoluir e aniquilar gradualmente. O SFT sob o indentador é diminuído gradualmente, conforme mostrado na Fig. 7c. Conforme o processo de indentação prossegue, a escala de novos defeitos de luxação nucleada aumenta, e a luxação em forma de V e SFT1 sob o indentador desaparecem gradualmente. Simultaneamente, os defeitos de deslocamento formados durante a indentação gradualmente evoluem para alça de deslocamento prismática, em que as falhas de empilhamento desaparecem gradativamente, conforme mostrado na Fig. 7d. A alça de deslocamento prismática recém-formada continua se estendendo até SFT2 na parte inferior direita do penetrador. Por causa de sua estrutura estável, o SFT2 permanece indeformado durante a expansão da alça de deslocamento prismática, conforme mostrado na Fig. 7e. À medida que o penetrador pressiona para baixo, a alça de deslocamento prismática continua se expandindo para baixo e a escala dos defeitos de deslocamento na área subsuperficial é aumentada gradualmente. A estrutura SFT2 existe de forma estável na subsuperfície do espécime e não tem alteração durante o movimento e interferência dos defeitos de deslocamento, como mostrado na Fig. 7 f.
A fim de mostrar a evolução e distribuição dos defeitos de subsuperfície durante o processo de indentação mais claramente, o método DXA é usado para analisar a amostra após a indentação. A imagem da distribuição do deslocamento subsuperficial em cada tempo correspondente à Fig. 7 é obtida por análise DXA, como mostrado na Fig. 8. Os deslocamentos são coloridos com base no seguinte esquema:azul profundo para deslocamentos perfeitos, verde para deslocamentos Shockley, rosa para haste de escada luxações, amarelo para luxações de Hirth, azul claro para luxações de Frank e vermelho para luxações não identificadas.
Pode ser visto na Fig. 8 que a subsuperfície da peça de trabalho consiste principalmente no deslocamento de Shockley e no deslocamento da haste da escada no estado de indentação inicial. O SFT existente em subsuperfície é uma estrutura tetraédrica regular que consiste em seis deslocamentos de haste de escada. Quando o penetrador entra em contato com a peça de trabalho, a nucleação de deslocamento na superfície da peça de trabalho são os deslocamentos de Hirsh amarelos, como mostrado na Fig. 8a. À medida que o penetrador pressiona para baixo, um grande número de deslocamentos é nucleado e movido ao longo do sistema de deslizamento. As luxações de Hirsh amarelas são gradualmente alteradas para luxações de Shockley verdes, como mostrado na Fig. 8b. Sob a interação entre os deslocamentos recém-formados e o SFT1 original, alguns deslocamentos simples desaparecem, gradualmente, como mostrado na Fig. 8c. A escala dos deslocamentos de subsuperfície aumenta com a queda do penetrador, e os deslocamentos recém-formados são principalmente deslocamentos de Shackley verdes. A interação entre os deslocamentos de Shockley e SFT1 resulta no tamanho da diminuição gradual de SFT1 e eventual desaparecimento de SFT1, como mostrado na Fig. 8d. Com o aumento da escala dos defeitos, o número e os tipos de deslocamentos na subsuperfície do corpo de prova aumentam. Existem tipos desconhecidos de luxações vermelhas formadas na subsuperfície, e várias luxações de Shockley constituíram a alça de luxação do prisma, como mostrado na Fig. 8e. Sob a interação do deslocamento de Shockley e do deslocamento do Stair-rod, o SFT2 e SFT3 longe da região de indentação não desapareceram por último, devido à extrusão mais fraca do indentador, conforme mostrado na Fig. 8f.
A imagem da evolução do deslocamento subsuperficial durante o processo de descarregamento de nanodentação é mostrada na Fig. 9. A Figura 10 mostra a imagem da distribuição do deslocamento subsuperficial correspondente na Fig. 9. A partir dos dois gráficos, pode-se ver que a escala de defeitos subterrâneos aumenta no início, e depois diminui gradualmente durante o processo de movimento ascendente do penetrador. É causado pela função abrangente entre a liberação contínua da energia de deformação do material e a força de adesão exercida pelo penetrador na amostra. No estágio inicial do processo de descarregamento, a força de adsorção para cima do efeito do indentador na amostra não é significativa. A evolução do defeito do subsolo é impulsionada principalmente pela energia de deformação do material, o que resulta no aumento da escala dos defeitos do subsolo. E os principais tipos de deslocamento no estágio são o deslocamento de Shockley verde e o deslocamento em escada rosa, conforme mostrado nas Figs. 9a, be 10a, b. A interação entre o SFT2 e o deslocamento de Shockley próximo faz com que o deslocamento rosa da haste da escada se transforme em deslocamento de Shackley verde na área distante da ação do penetrador. Enquanto isso, o SFT2 é transformado em um defeito menor que é SFT3, como mostrado nas Figs. 9c e 10c. Com o levantamento contínuo do penetrador, o efeito de adesão e adsorção exercido pelo penetrador na amostra aumenta gradualmente. Acompanhando a liberação de energia de deformação, o tamanho e os tipos de deslocamentos no subsolo aumentam. And more perfect dislocations, Hirh dislocations, and unknown dislocations are formed, as shown in Figs. 9d and 10d. In later stage of unloading process, the material deformation energy is basically released, and the evolution of subsurface defects is dominated by the adsorption from the indenter. Therefore, the subsurface defects are annihilated rapidly, and the scale of subsurface defects decreases rapidly. And a typical Hirsch dislocation is formed in the direction of the indenter upward, which is shown in Figs. 9e, f and 10e, f. Finally, the scale of subsurface defects decreases considerably, and some typical subsurface defects, such as SFT and atomic clusters, are gradually disappeared. From the above analysis, it can be seen that secondary processing (nano-indentation) can restore the typical internal defects formed in nano-cutting, and the subsurface damage becomes more serious in the secondary processing area. These characteristics of subsurface defects will affect the mechanical properties of materials. Hence, it is necessary to study the effect of subsurface defects on the mechanical properties of material.
Mechanical properties of materials can be calculated by load-displacement curve, such as hardness, elastic modulus, and yield strength. In this study, hardness and Young’s modulus of single crystal copper were investigated. The variation of load on the indenter was monitored during the nano-indentation process, and the load-displacement curve of the nano-indentation process was drawn, as shown in Fig. 11. The max indentation depth of the red and black curves respectively is 2 nm and 3 nm, in which both loading and unloading processes are included. The upward direction of load is defined as positive direction, so the load-displacement curves are all above the zero line in the process of loading, while the load on the indenter changes from positive to negative during unloading. The elasticity restore of deformed matrix material exerts an upward force on the indenter. Therefore, in order to keep the indenter raising in uniform speed, a downward force (positive) is required. With the gradual recovery of deformation, the force gradually decreases until it disappears. Then the force applied on the indenter becomes negative, and the absolute value of the force first increases and then decreases. From the graph, it can be seen that the specimen is in the stage of elastic deformation during loading process, and the load increases in proportion to the displacement. When the displacement of the indenter is 1 nm, the load on the indenter is fluctuated dramatically, as indicated by the arrow on the left side of Fig. 11. This is because that the indenter is pressed down to the SFT1 shown in Fig. 7, which results in the greater impediment to the indenter. When the indenter displacement is in the range of 2 to 3 nm, the fluctuation amplitude of the load increases. This is because the indenter is pressed down to the SSD layer, and the impediment of the indenter to the subsurface defect in the specimen is more significant, so the fluctuation amplitude of the load increases significantly.
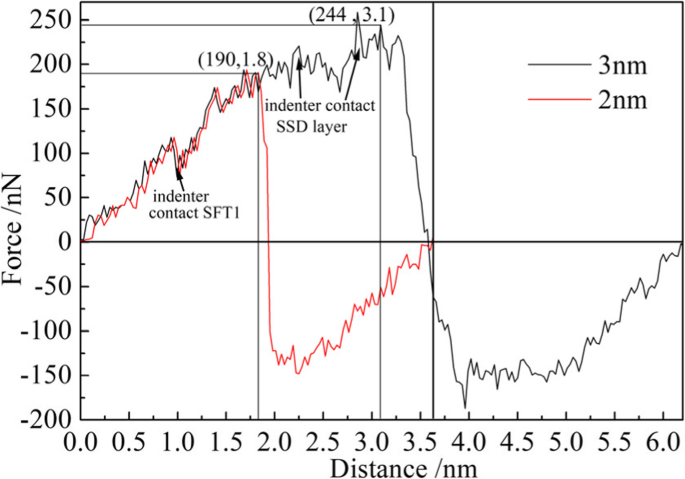
Load-displacement curve of nano-indentation on the machining-induced specimen (color online). The maximum indentation depth of the black curve and the red curve respectively is 3 nm and 2 nm
According to Oliver-Pharr Method [31], nano-indentation hardness can be defined as indentation load divided by the contact area between indenter and specimen, which is calculated by Eq. 7
$$ H={F}_{\mathrm{max}}/{A}_c $$ (7)
In which, F máximo is the peak value of the load. A c is projected contact area for indenter and specimen, which can be obtained by
$$ {A}_c=\pi {r}^2 $$ (8)
onde r is contact radius for indenter. Because the indenter is hemispherical in shape, r is approximately equal to indentation depth.
The elastic deformation of single crystal copper material is caused by the load exerted from indenter. Based on the previous load-displacement curve, Young’s modulus (E ) of single crystal copper can be calculated by Eq. 9
$$ E=\frac{\sigma }{\varepsilon }=\frac{F/S}{DL/L}=\frac{F/\pi {r}^2}{DL/L} $$ (9)
where F is applied load, S is contact area, r is projection radius of indenter, DL is material deformation along loading direction, which is equal to indentation depth, and L is the total length of material along loading direction. In this study, L is equal to 30 nm.
According to the Oliver-Pharr method and load-displacement data, nano-indentation hardness and Young’s elastic modulus of single crystal copper materials with subsurface defects can be calculated based on Eqs. 7, 8, 9. Table 3 shows the applied load acting on the specimens by indenter with different indentation depths.
The nano-indentation hardness of single crystal copper can be calculated by Eqs. 7 and 8 combining the data in Table 3. When the maximum depth is 2 nm, F máximo =190.67 nN and from Fig. 11 r =2.75 nm. The calculated value of nano-indentation hardness H2 is 8.029 GPa. When the maximum depth is 3 nm, F máximo =244.66 nN and r =3 nm. The calculated value of nano-indentation hardness H3 is 8.675 GPa, which is slightly larger than it obtained at indentation depth of 2 nm. It is because the indenter is pressed down to the subsurface defects area at indentation depth of 3 nm, and the deformation resistance of the subsurface defects increases. Therefore, the hardness of the single crystal copper increased. It can be concluded from the result that the subsurface defects make the machined surface much harder, which is work-hardening phenomenon.
The Young’s modulus E of single crystal copper can be calculated by Eq. 9 combining the data in the Table 3. The calculation results are shown in Table 4. It can be noted that the Young’s modulus becomes distinctly higher when the indentation depth is smaller than 1.5 nm. In the initial stage of nano-indentation, the indenter does not contact the defects residual area in subsurface. However, the work-hardening effect makes the specimen material not easily be occurred elastic deformation; therefore, the Young’s modulus of single crystal copper is larger in the initial stage of indentation. The value of Young’s modulus is 119.4 GPa when indentation depth is 2 nm, which is almost the same with Zhang’s research (120.4 GPa) [14]. With the increase of indentation depth, the Young’s elastic modulus of single crystal copper specimens decreases gradually, and the ability of materials to resist elastic deformation is weakened. It is due to the permanent elastic deformation is derived from the dislocation motion and its interaction with subsurface defects. It has been revealed that the nano-cutting-induced subsurface defects will affect the physical and mechanical properties of single crystal copper materials, which is also applicable to other FCC materials. The existence of subsurface defects will enhance the hardness of machined surface and weaken the ability of material to resist elastic deformation, in which the mutual evolution between dislocations and subsurface defects plays an important role. Therefore, it is very important to predict the thickness of subsurface deformation layer and study the surface properties for nano-fabrication.
Conclusões
The subsurface defects stable exist in workpiece after nano-cutting can affect the mechanical properties, which is critical to the service performance and life of nano-structures. The previous studies are mainly based on perfect crystal materials or artificial constructing hypothetical defects, which is far from the actual subsurface defects. In this paper, molecular dynamics simulation of nano-cutting is performed to construct the specimen model with subsurface defects. Based on the built MD model, nano-indentation simulation is carried out to study the influence of machining-induced subsurface defects on the physical and mechanical properties of single crystal copper materials. The interaction mechanism between dislocation and complex defects during nano-indentation is studied. The nano-indentation hardness and Young’s elastic modulus of single crystal copper materials are calculated. Based on the above analysis, some interesting conclusions can be drawn as follows.
- 1.
The dislocation nucleation and expansion in workpiece subsurface are driven by the extrusion and shearing action of cutting tool during the nano-cutting process, which results in the fluctuation of cutting force. After nano-cutting, there are stable defect structure residues in the subsurface of workpiece, such as vacancy defects, stacking faults, atomic clusters, SFT, and stair-rod dislocations, which together constitute the subsurface defect layer of workpiece.
- 2.
The existence of subsurface defects affects the nucleation and expansion of dislocations during nano-indentation process. Some stable defects directly below the indenter, such as V-shaped dislocation and SFT1, are annihilated after indentation. And SFT2 far from the indentation region is transformed into a smaller one. Secondary processing of nano-indentation can restore typical internal defects of the workpiece, but the subsurface defects in the secondary processing area are aggravated.
- 3.
The nano-indentation hardness of specimens increases with the introduction of subsurface defects, which results in the formation of work-hardening effect. The Young’s modulus of single crystal copper is larger in the initial stage of indentation and gradually decreases with the increase of indentation depth. The existence of subsurface defects can weaken the ability of material to resist elastic deformation, in which the mutual evolution between dislocations and subsurface defects plays an important role.
Disponibilidade de dados e materiais
The conclusions made in this manuscript are based on the data which are all presented and shown in this paper.
Abreviações
- MD:
-
Dinâmica Molecular
- SSD:
-
Subsurface defects
- SFT:
-
Stacking fault tetrahedral
- PBC:
-
Periodic boundary condition
- LAMMPS:
-
Large-scale atomic/molecular massively parallel simulator
- EAM:
-
Embedded-atom method
- CSP:
-
Centro-symmetry parameter
- FCC:
-
Face center cubic
- CNA:
-
Common neighbor analysis
- HCP:
-
Close-packed hexagonal
- BCC:
-
Body centered cubic
- ICO:
-
Icosohedral
- DXA:
-
Dislocation extract algorithm
Nanomateriais
- A evolução do mercado de materiais de impressão 3D:tendências e oportunidades em 2019
- A evolução do SLS:novas tecnologias, materiais e aplicações
- Como os engenheiros avaliam os materiais plásticos e a resistência do material?
- Composto Híbrido de Sílica Nanoestruturada / Ouro-Celulose Ligado Amino-POSS via Processo Sol-Gel e Suas Propriedades
- O efeito do plasma sem equilíbrio de contato nas propriedades estruturais e magnéticas de Mn Х Fe3 - X О4 Spinels
- Propriedades paramagnéticas de nanomateriais derivados do fulereno e seus compostos de polímero:efeito drástico de bombeamento
- Propriedades dos Materiais de Engenharia:Gerais, Físicas e Mecânicas
- Lista de 14 Propriedades Mecânicas Diferentes dos Materiais
- Propriedades dos materiais de aço e ferramentas usadas para punções
- Diferentes tipos de propriedades mecânicas do material