Personalização de sensores ultrassônicos para otimização e controle de processos compostos
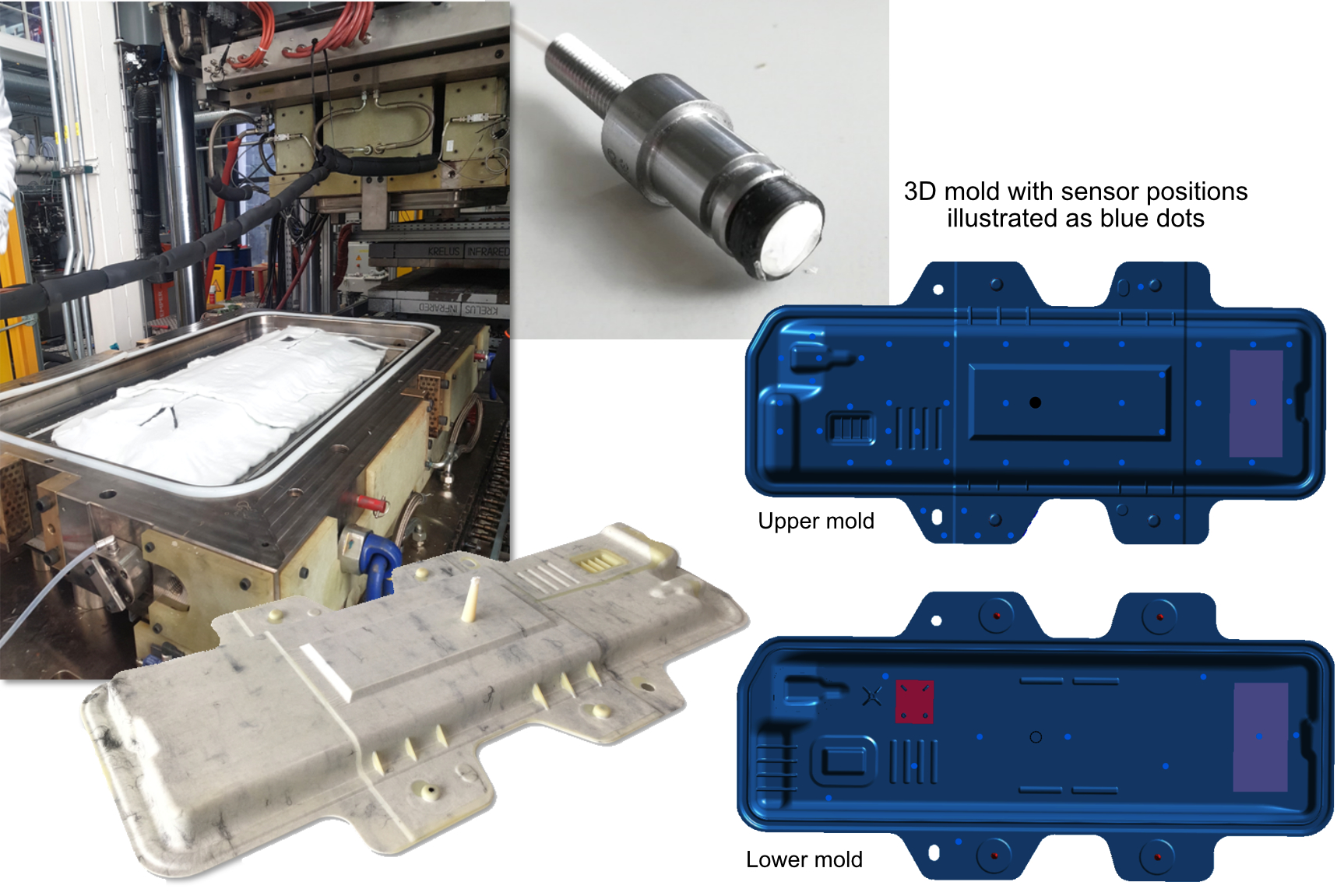
Este blog é uma continuação do meu relatório sobre o projeto CosiMo (“compósitos para mobilidade sustentável”). Esse projeto foi lançado em 2018 pela Faurecia Clean Mobility (Nanterre, França) para demonstrar a “fabricação inteligente” de uma tampa de caixa de bateria composta. A peça de desafio de 1.100 milímetros de comprimento e 530 milímetros de largura apresentava fibra de vidro não tecida e reforços de fibra de carbono unidirecionais, bem como inserções de metal e espuma, geometria complexa incluindo vários raios e espessuras variando de 2,5 a 10 milímetros. A peça foi moldada usando moldagem por transferência de resina termoplástica (T-RTM), onde o monômero de caprolactama foi injetado e polimerizado in-situ durante o ciclo de prensa aquecida para formar um compósito de poliamida 6 (PA6). O objetivo principal do projeto era investigar um processo totalmente automatizado usando controle de processo baseado em sensor de malha fechada.
Este blog explora em mais detalhes a rede de 74 sensores usados na parte do desafio CosiMo, e em particular os sensores ultrassônicos desenvolvidos pela Universidade de Augsburg (UNA, Augsburg, Alemanha) e como os dados de todos os sensores foram usados para construir um modelo digital do processo (gêmeo digital).
Com base no sucesso do CosiMo e na necessidade de um centro de desenvolvimento para o desenvolvimento de manufatura baseada em sensores e IA, a UNA formou a Augsburg AI Production Network, em colaboração com o parceiro do projeto CosiMo Centro Aeroespacial Alemão (DLR) Centro de Tecnologias de Produção Leve ( ZLP, Augsburg) e o Instituto Fraunhofer para Fundição, Compósitos e Tecnologia de Processamento (Fraunhofer IGCV). “Estamos montando uma nova instalação de 5.000 metros quadrados que operaremos em colaboração”, disse o Dr. Markus Sause, professor da UNA e diretor da Rede de Produção de AI de Augsburg. “Teremos células de produção automatizadas, muitas delas focadas em tecnologias de compósitos, o que nos permitirá demonstrar o que a IA pode fazer.”
Rede de sensores CosiMo
Para o projeto CosiMo, 74 sensores foram integrados ao ferramental RTM de aço fornecido por Christian Karl Siebenwurst GmbH &Co. KG (Dietfurt, Alemanha) para moldar a tampa da caixa da bateria T-RTM. Usado para monitorar os parâmetros do processo durante a injeção de resina, infiltração (monitoramento da frente de fluxo) e polimerização in-situ, esta rede incluiu:
- 1 sensor de vácuo
- 4 sensores de pressão / temperatura por Kistler (Winterthur, Suíça)
- 4 sensores de temperatura da Kistler
- 8 análises dielétricas (DEA) / sensores de temperatura da Netzsch (Selb, Alemanha)
- 57 sensores ultrassônicos desenvolvidos pela Universidade de Augsburg.
Em meu relatório inicial sobre o CosiMo, discuti como essa rede de sensores era para P&D, não para a produção padrão:
“Para a produção industrial em série, ninguém instalaria tantos sensores e isso não é o que esperaríamos”, disse o líder do projeto de manufatura da CosiMo na DLR ZLP, Jan Faber. “Mas para esta investigação de investigação, esta grande rede de sensores era muito precisa e nos ajudou a ter visibilidade total do processo e comportamento material . Pudemos ver os efeitos locais no processo em resposta a variações na espessura da peça ou nos materiais integrados, como o núcleo de espuma. ”
Então, como essa rede foi projetada? “A maioria eram sensores ultrassônicos porque eles têm o custo mais baixo”, explica Faber. “Nós os usamos em uma grade a uma distância definida um do outro. Em algumas posições, retiramos os sensores ultrassônicos e colocamos os sensores Kistler de temperatura / pressão ou Netzsch DEA / temperatura. E para esses sensores específicos, tanto o DEA quanto o Kistler, tentamos apenas ter um perto do canal, onde a resina entrava, e depois um bem longe. Assim, pudemos monitorar os locais de chegada da resina após já termos visto a temperatura do molde ”.
Por que usar diferentes tipos de sensores? “Uma das tarefas de pesquisa foi comparar os sinais e ver como os diferentes sensores funcionam”, diz Faber. Isso é importante porque os diferentes tipos de sensores são baseados em diferentes princípios de medição. Por exemplo, os sensores DEA medem a impedância AC da resina, que pode ser dividida em diferentes frações, que por sua vez apresentam diferentes efeitos no polímero. Kistler, por sua vez, usa sensores piezoresistivos que contam com uma ponte Wheatstone à base de silício - um tipo de circuito usado para medir a resistência elétrica dinâmica - conectada a uma membrana que forma a extremidade de detecção instalada na parede da cavidade de moldagem. A membrana se estende sob pressão, o que altera a resistência elétrica da ponte de Wheatstone de silício, que por sua vez emite um sinal elétrico. “Também usamos o novo sensor 4001a de Kistler, que mede pressão e temperatura”, observa Faber. “Foi muito útil ter ambos os valores para selecionar pontos locais na ferramenta.”
Sensores ultrassônicos UNA
A maioria dos sensores usados na rede de peças CosiMo eram sensores ultrassônicos desenvolvidos pela UNA. Sause observa que estes foram favorecidos não só pelo seu baixo custo (<10 euros), mas também porque podem fornecer uma vasta gama de informações.
Sensores ultrassônicos têm sido usados por décadas para inspecionar peças compostas acabadas, mas também têm uma longa história em moldagem por injeção. Sensores ultrassônicos enviam uma onda sonora de alta frequência para um meio e medem sua reflexão (eco de pulso) e / ou transmissão. No projeto CosiMo, a frequência nominal era de 2.000 quilohertz. Dos 57 sensores ultrassônicos instalados no molde - a uma distância de 20 milímetros da superfície da cavidade - 10 operavam em modo de transmissão e o restante em modo de pulso-eco. Os sensores ultrassônicos medem a velocidade da onda e diminuem a amplitude (atenuação); ambos são sensíveis às propriedades do polímero. Além disso, a velocidade da onda pode ser calculada em função da pressão e temperatura, mas os dados de ultrassom devem ser calibrados para o polímero que está sendo investigado.
“O sensor ultrassônico que desenvolvemos não é muito diferente do que está disponível comercialmente”, diz Sause. “É baseado em um material piezoelétrico, que é bastante sensível para converter um movimento elástico em um sinal elétrico. Mas onde os sensores típicos podem operar em temperaturas de até 150 ° C, tivemos que igualar as altas temperaturas da moldagem termoplástica a mais de 200 ° C, o que foi um pouco desafiador para os componentes eletrônicos do sensor ”.
“Também tivemos que conceber o sistema mecânico para integrar corretamente o sensor no molde”, explica ele, “que exigia carregamento de mola com boa vedação para fornecer um bom acoplamento. Havia um grande portfólio de requisitos que o sensor tinha que cumprir; então, tivemos que projetá-lo do zero. Também fizemos um projeto acústico adequado de todo o sistema. ”
Polimerização e monitoramento da frente de fluxo
“A acústica concentra-se nas propriedades elásticas dos materiais do molde”, continua Sause. “Basicamente, a rigidez de um líquido não é a mesma de quando a polimerização é concluída. Estamos monitorando essa transição de maneira eficaz. Observamos a intensidade acústica da reflexão da onda na interface do molde para o material polimérico em cada localização do sensor e, assim, rastreamos continuamente a cura ao longo do tempo. ”
A mecânica desta medição é explicada por Sause e Faber, et. al., no documento de conferência SAMPE Europe 2021, “Monitoramento do processo baseado em sensor de polimerização in-situ na fabricação de T-RTM com caprolactama”. A razão da amplitude do eco do sinal acústico antes e depois da impregnação do pré-molde depende do índice reflexivo na interface molde-peça, R. Isso se aproxima de um valor constante conforme a polimerização progride. Idealmente, quando a polimerização estiver quase concluída, a mudança em R será zero.
Também é possível, a partir do sinal de transmissão acústica, extrair o tempo de percurso para que as ondas ultrassônicas passem pela pré-forma impregnada. Isso é útil porque a velocidade do som através da pré-forma está ligada ao grau de polimerização. Para a experimentação concluída no momento do artigo SAMPE Europe 2021, o tempo entre o umedecimento completo da pré-forma no local do sensor até a conclusão da polimerização foi de 240 segundos.
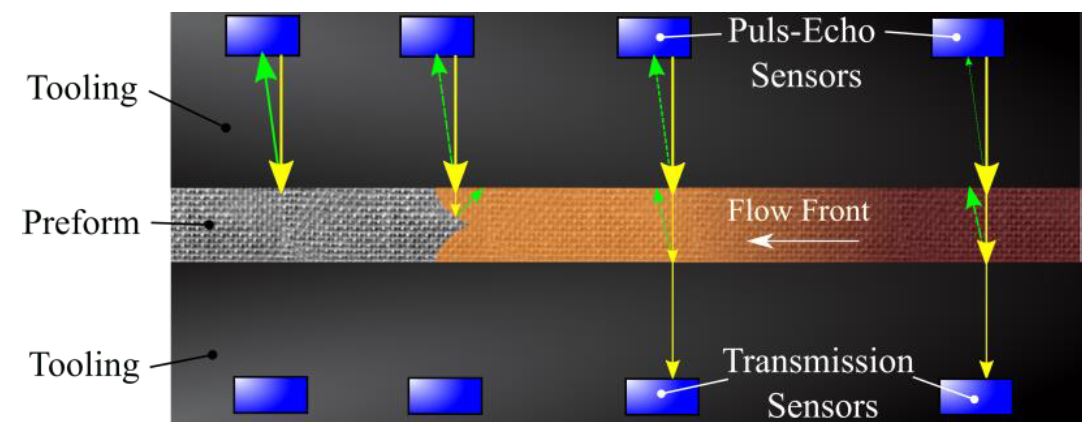
“Também podemos monitorar o fluxo durante a injeção”, explica Sause, “porque as informações do sinal acústico mudam conforme a frente do fluxo de polímero passa pelo sensor”. Também verificado no artigo SAMPE Europe 2021, o sinal acústico caiu abruptamente de um valor normalizado inicial de 1 para entre 0,85-0,9 na chegada da frente de fluxo de caprolactama para o sensor selecionado 15 segundos após o início da injeção.
Desenvolvendo um gêmeo digital do processo
Sause diz que desenvolver o sensor ultrassônico foi, na verdade, uma parte muito pequena do que a UNA fez no projeto CosiMo, “e nem mesmo a parte mais fascinante”. A verdadeira conquista, observa ele, foi na análise de dados e no desenvolvimento de um modelo digital do processo para permitir o controle de malha fechada durante a fabricação de peças.
“O que estamos tentando fazer é fornecer informações sobre o que realmente está ocorrendo no molde”, acrescenta. “Estabelecemos rotas para adaptar o processo com temperatura e pressão, mais ou menos, mas o que estamos fazendo agora é explorar as informações do sinal acústico fazendo pulsação ativa em cada localização do sensor. E isso nos permite determinar várias coisas, como a forma da frente de fluxo, o tempo para que ela alcance cada parte da pré-forma e o grau de polimerização em cada localização do sensor. ”
“Idealmente, você pode estabelecer configurações para habilitar o controle de malha fechada e ajustar durante o processo”, diz Sause. “Isso incluiria parâmetros como pressão de injeção e pressão e temperatura do molde. Você também pode usar essas informações para otimizar seus materiais. ”
O desenvolvimento do gêmeo digital foi um esforço de múltiplos estágios e múltiplos parceiros. Tudo começou com um dos pacotes de trabalho atribuídos ao DLR ZLP. “Montamos uma simulação baseada em uma placa 2D, onde queríamos simular o enchimento e a polimerização usando o software de simulação PAM-RTM do ESI Group (Rungis, França)”, diz Faber. “Obtivemos os dados de permeabilidade da pré-forma dos parceiros do projeto ITA (Instituto de Tecnologia Têxtil, RWTH Aachen, Alemanha) e SGL Carbon (Wiesbaden, Alemanha) e também um modelo reativo da reação de polímero termoplástico da Universidade de Augsburg. Em seguida, integramos tudo na simulação e tentamos ver o quão perto poderíamos realmente chegar dos dados reais do sensor. ”
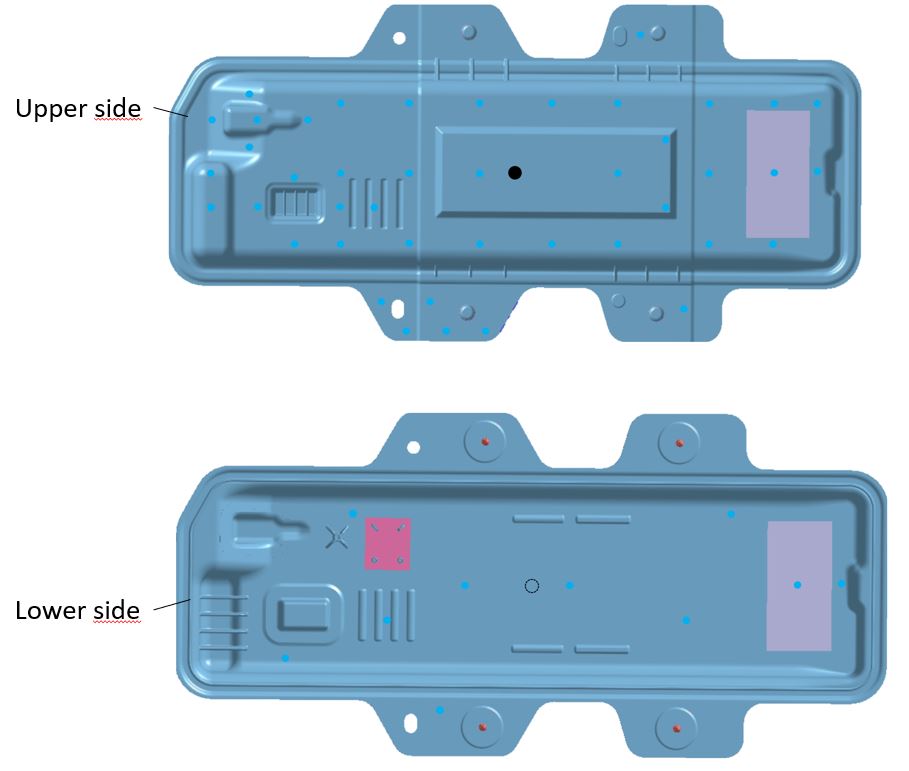
Os pontos azuis claros nos moldes superior e inferior da peça do demonstrador do projeto CosiMo forneceram dados em pontos específicos ao longo do processo. Isso foi então usado na simulação digital dupla para interpolar entre as localizações do sensor e modelar o processo na peça. Crédito da foto:CosiMo project, DLR ZLP Augsburg, University of Augsburg
“Descobrimos, com base no modelo de placa 2D, que, na verdade, estamos muito próximos em relação ao enchimento”, continua Faber. “Mas tivemos alguns efeitos de temperatura durante a polimerização que não pudemos descrever na simulação. Por exemplo, esta reação de polimerização é exotérmica e você vê um ligeiro aumento nos sensores de temperatura nos dados reais, mas o aumento na simulação foi muito maior. Portanto, esta é uma área em que continuamos a fazer algum trabalho ”.
Uma das coisas que a equipe queria descobrir na simulação era o tempo necessário para que a polimerização fosse concluída. “O que realmente queríamos era o tempo mínimo de que precisávamos no molde”, observa Faber. Essas informações foram derivadas do modelo de simulação e se baseavam, como toda a simulação, em vários tipos de sensores e algoritmos de IA. Por exemplo, a Netzsch forneceu os sensores dielétricos usados para análise dielétrica, mas também ajudou com partes do gêmeo digital do processo. “Eles montaram modelos de IA preditivos para investigar os mecanismos dentro da injeção e prever em que momento a polimerização deve ser concluída e qual seria o estado de polimerização”, diz Faber.
(Nota, Netzsch combinou suas competências em caracterização de material, simulação cinética e tecnologia de sensor para estabelecer novas ofertas em soluções de IA e nuvem. Este tipo de solução integrada foi demonstrado com sucesso no CosiMo para fornecer avaliação em tempo real do grau de polimerização e será comercializado sob a marca sensXPERT.)
Da rede completa de sensores e simulação, constatou-se que 96% foi a polimerização máxima alcançada e que exigiu 4,5 minutos. “Então, isso é muito mais rápido do que os processos de infusão, mas muito mais lento do que a injeção de alta velocidade usando termofixos, por exemplo.”
“Os dados do sensor se encaixam no modelo digital gêmeo”, diz Sause. “A ideia era ter um modelo rodando ao mesmo tempo que o processo que é estabilizado numericamente pelas informações do sensor. Os pontos azuis fornecem uma grade grosseira de sensores ultrassônicos e, então, fomos capazes de interpolar entre esses pontos. Por exemplo, fomos capazes de fornecer um vídeo de como a frente de fluxo se desenvolve na peça CosiMo em função do tempo, com base nos dados de medição de nossos sensores. ”
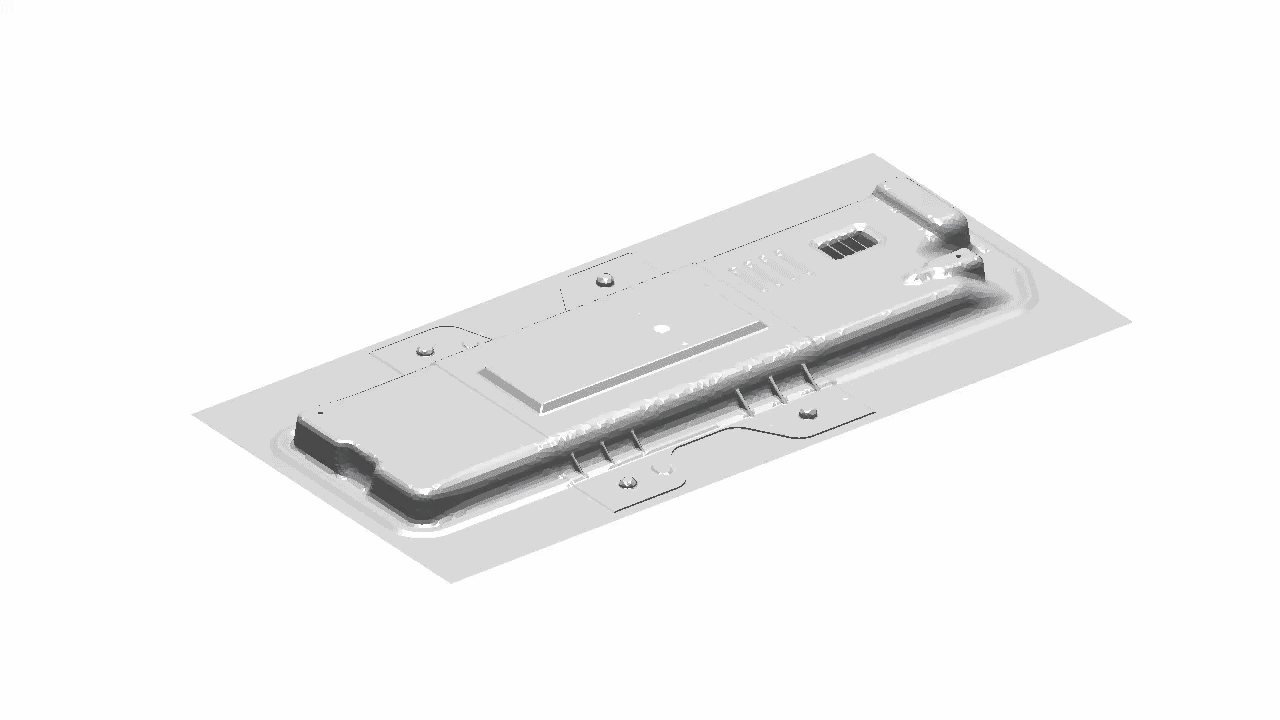
Como as previsões da taxa de polimerização foram validadas? “Tínhamos várias abordagens”, diz Sause. “Primeiro, um aluno de doutorado aqui na UNA estava fazendo um conjunto completo de modelagem para a cinética de reação do sistema de material caprolactama-para-PA6. Então, ele estava estudando espectroscopia infravermelha simultaneamente com dados reométricos e dados dos sensores de análise dielétrica para fornecer um modelo de material muito preciso para a cinética curada desse sistema e para validar esse modelo. Portanto, usamos o mesmo modelo para validação cruzada de nossos sensores. ”
Arquitetura do gêmeo digital
A arquitetura de como o gêmeo digital opera é descrita por Stieber, et. al. no artigo técnico de 2020, "Rumo ao monitoramento de processos em tempo real e aprendizado de máquina para estruturas compostas de fabricação":
Ele consiste em três partes:o maquinário T-RTM, os sensores in-situ nas ferramentas de molde e o gêmeo digital. Esta estrutura e o gêmeo digital, em particular, foram desenvolvidos com os seguintes objetivos O1 - O4 em mente:
- O1:Monitore o processo de fabricação de cada peça composta com os sensores in-situ das ferramentas.
- O2:visualize cada processo de manufatura em tempo real para obter mais informações sobre o processo.
- O3:treinar modelos de ML em dados simulados e reais para prever o resultado do processo de fabricação.
- O4:Use modelos de ML treinados para reduzir rejeições de produção.
Os sensores, então, alimentam dados para a análise de borda do gêmeo digital, que pode então ser usado para prever a dinâmica da frente de fluxo futura, determinar o conteúdo de volume de fibra de cada pré-forma têxtil, prever pontos secos e detectar anomalias que podem reduzir peças rejeitadas.
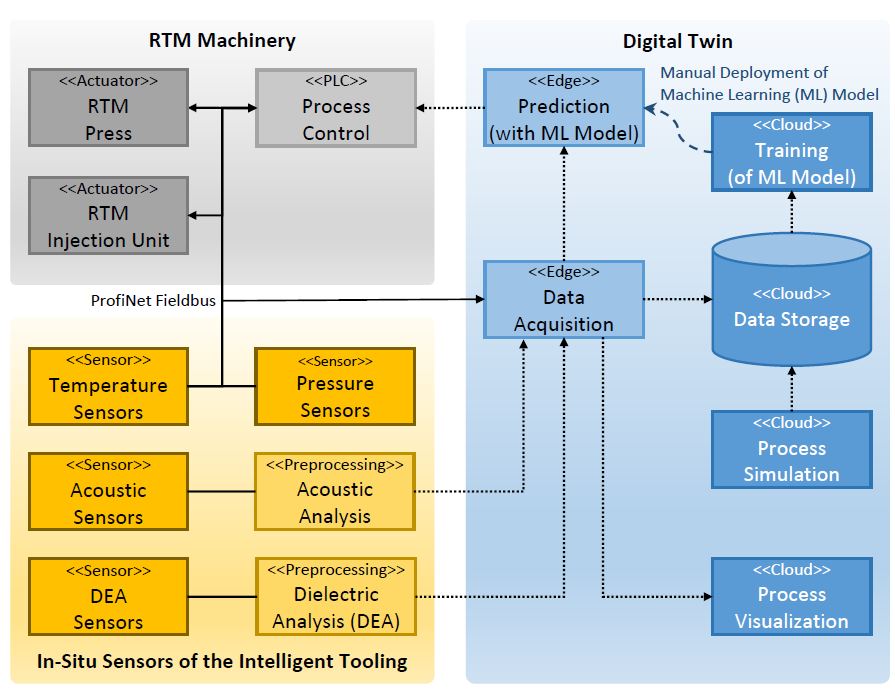
O maquinário T-RTM compreende dois componentes prontos para uso:uma prensa a quente Wickert (Landau in der Pfalz, Alemanha) de 440 kilonewton e uma unidade de injeção T-RTM da KrausMaffei (Munique, Alemanha). Ambas as máquinas, bem como toda a rede de sensores são conectadas a um PLC (controlador lógico programado) que é responsável por controlar todo o processo de fabricação.
Como os sensores precisam de pré-processamento em tempo real para transformar os dados brutos em informações de nível superior sobre a frente de fluxo ou a cura da resina, os dados pré-processados são registrados diretamente na borda usando uma unidade de aquisição de dados ibaPDA da iba AG ( Fürth, Alemanha). Assim, os dados do sensor são registrados e combinados com um carimbo de tempo consistente vinculado aos dados do processo e informações da peça com os dados do sensor por objetivos O1 e O2.
Para otimizar automaticamente o processo de manufatura, os dados armazenados são usados para treinar modelos de aprendizado de máquina (ML) para atender ao objetivo O3. Esses modelos são responsáveis, por exemplo, por reconstruir a frente de fluxo da resina da rede de sensores, por prever o progresso da frente de fluxo e - idealmente - por adaptar os parâmetros do processo para otimizar o resultado durante uma instância de processo ou para execuções subsequentes . Como os dados reais geralmente não são suficientes para treinar modelos confiáveis, a equipe dupla digital usou execuções simuladas do PAM-RTM para aumentar os dados medidos. Após o pré-treinamento usando dados simulados, o gêmeo digital foi ajustado com dados do mundo real. Essa estratégia é conhecida como Transfer Learning e tem sido adotada com sucesso em aplicações de visão computacional e processamento de linguagem natural. As análises avançadas possíveis com o ML permitem maiores recursos de previsão e visualização do processo, bem como controle de loop fechado.
Integração de sensores para produção de compósitos industriais
Então, como os fabricantes de peças compostas aplicam essa tecnologia para desenvolver o controle de malha fechada em seus próprios processos de produção? Sause diz que faz sentido usar vários tipos de sensores para validar o fluxo e monitorar a cura / polimerização e fornecer informações complementares. E então é uma questão de definir o posicionamento do sensor, incluindo quais tipos são colocados em cada local. “Por exemplo”, observa ele, “você não precisa de sensores de pressão e temperatura em todos os lugares, mas apenas onde você precisa desses pontos-chave de dados, como entrada de resina, pontos de geometria complexa, etc.”
Quantos sensores? “Para CosiMo, usamos 74 sensores, mas para uma peça de meio metro você usaria menos, talvez 35-40 dependendo de sua geometria e pontos-chave de interesse”, diz Sause. “Depende também do processo de produção. Existem processos na indústria aeroespacial, por exemplo, que são usados há décadas e estão bem estabelecidos. Para eles, você pode não precisar de muitos sensores e pode ser possível integrá-los sem muito trabalho de desenvolvimento no início. Mas outros processos são mais desconhecidos e exigirão mais trabalho inicial. Para CosiMo, estávamos estudando o uso de T-RTM com polimerização in-situ para PA6, e isso não foi tão bem documentado quanto RTM com epóxi, por exemplo. ”
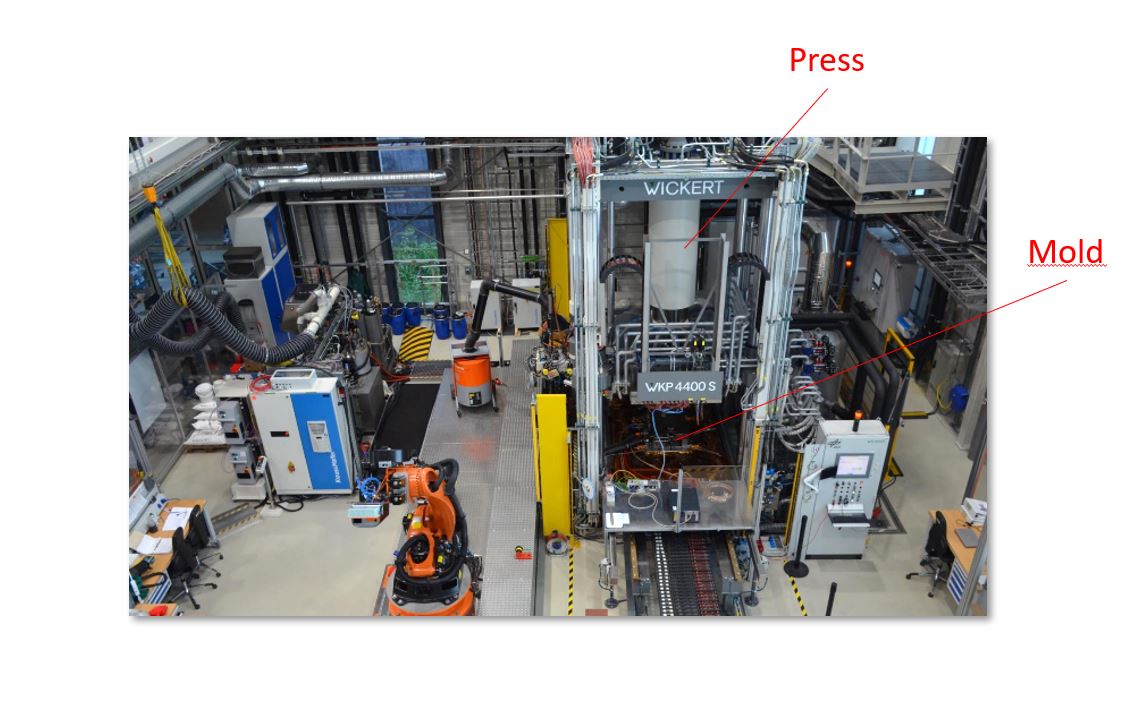
O equipamento de fabricação no projeto CosiMo compreendeu uma prensa Wickert 440-kN e uma máquina de injeção KraussMaffei. Crédito da foto para esta série:CosiMo project, DLR ZLP Augsburg, University of Augsburg
Quanto tempo leva para construir um modelo digital? E isso é sempre necessário para obter o controle de malha fechada? “Mais uma vez, depende do seu processo e do nível que você deseja atingir”, diz Sause. “Em primeiro lugar, ter as informações do sensor integradas permite que você visualize o que está acontecendo dentro de sua caixa preta de processamento e quais parâmetros usar.
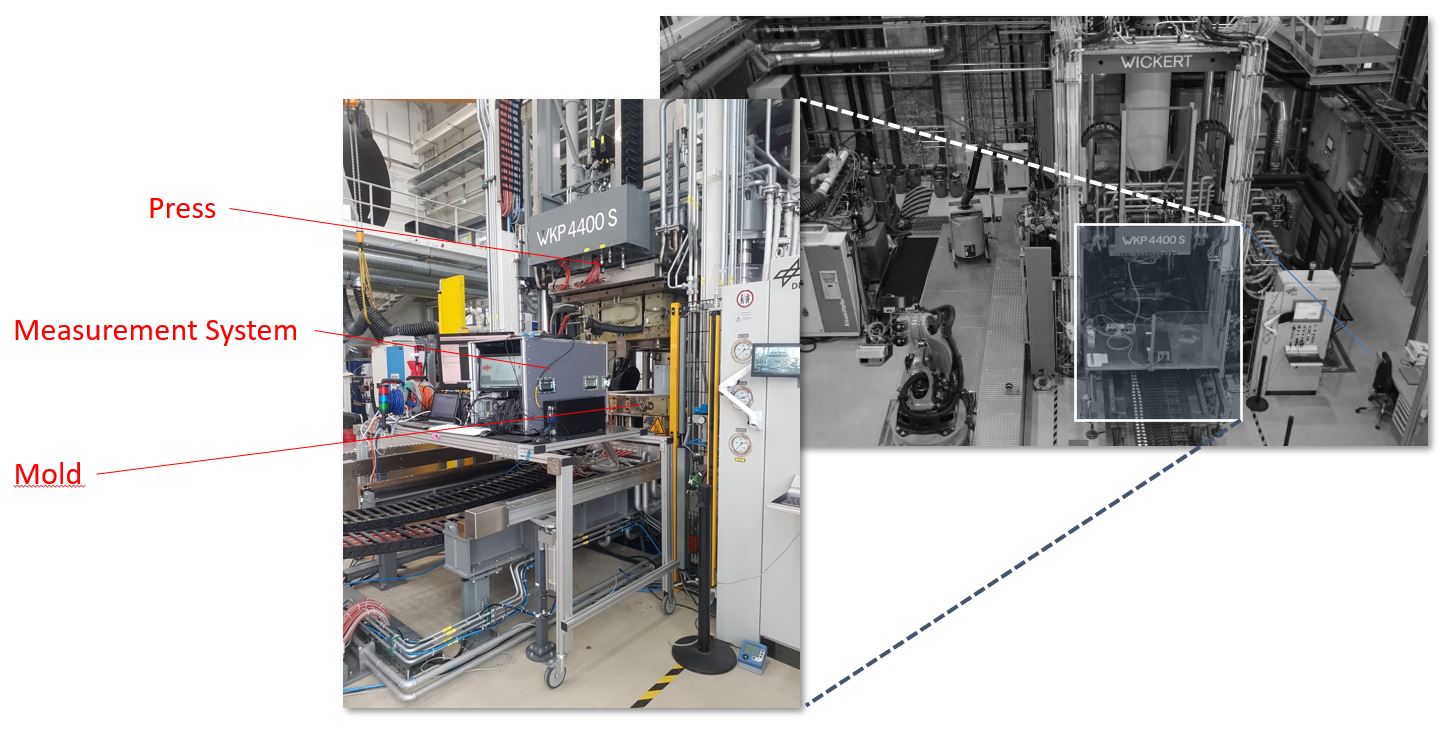
O sistema de controle de malha fechada desenvolvido no CosiMo também integrou sensores in-mold e um sistema de aquisição de dados (sistema de medição mostrado aqui) da iba AG.
Uma vez que o primeiro alvo seja alcançado, são necessárias mais algumas etapas para alcançar o controle do processo em malha fechada. No meio do caminho, talvez, seja para ter a visualização e você mesmo pode apertar o botão de parada para adaptar o processo e evitar rejeição de peças. Portanto, isso também é um começo. E então você pode desenvolver o gêmeo digital, mas ele precisa de dados de treinamento. Portanto, você deve fornecer isso de alguma forma, o que significa que pode produzir algumas peças para usar como dados de entrada. Mas então, você também precisa produzir peças de baixa qualidade. Portanto, é uma questão de sua disposição de investir no treinamento de sua abordagem de aprendizado de máquina. ”
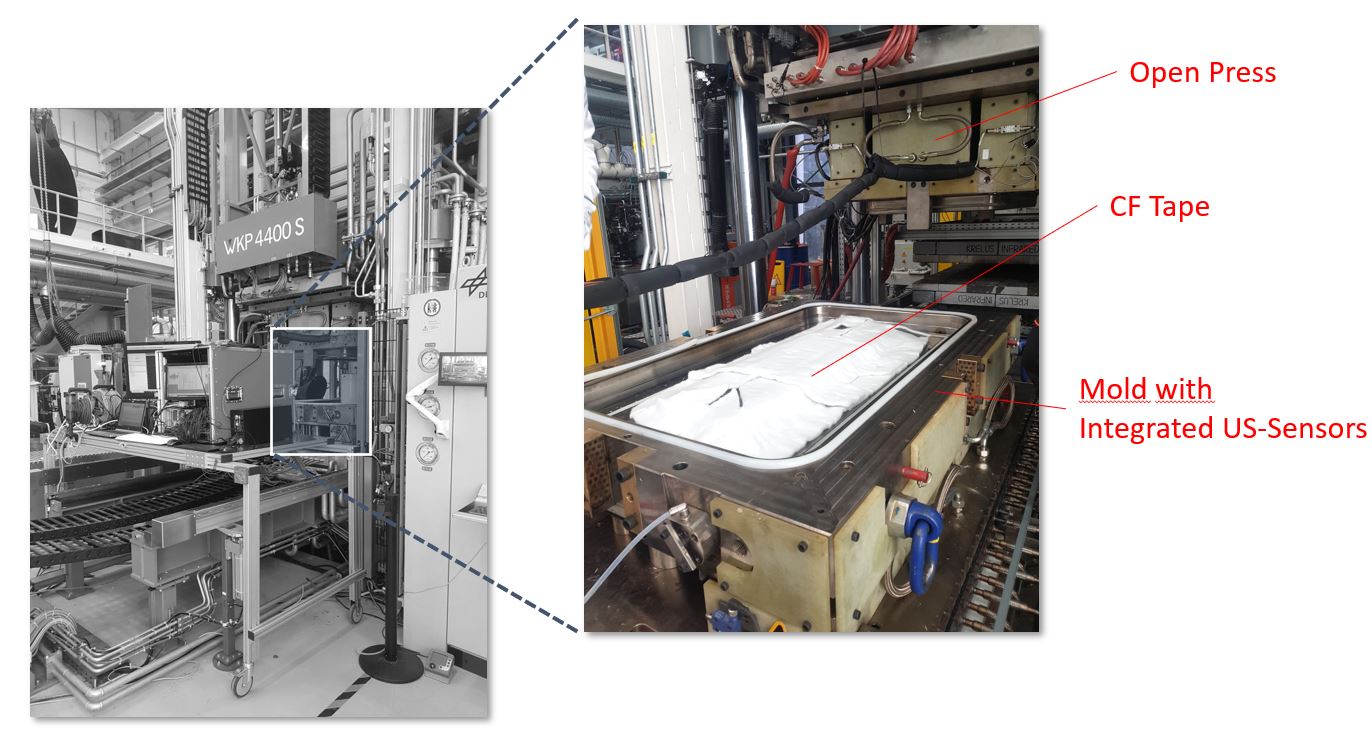
Uma vez treinado, o gêmeo digital pode otimizar os parâmetros do processo e fornecer controle de processo em malha fechada.
No entanto, Sause reconhece que a abordagem de aprendizagem por transferência tomada no CosiMo, “é transferível até um certo grau para geometrias semelhantes ou sistemas de materiais e outras variações que não mudam completamente a situação. Assim, você pode construir seu banco de dados dessa forma, com a possibilidade de identificar tendências de eficiência a partir dos dados já adquiridos. Você pode então usar isso para outras perguntas que você possa ter ao lado. ”
Então, o jeito de começar parece ser:começar a usar sensores e construir modelos digitais para ir com os sensores para que você possa entender seu processo? “Com certeza”, diz Sause. “E posso garantir que a maioria das máquinas usadas na produção hoje ainda é muito estúpida. Muitas máquinas não têm sensores que possam fornecer os bancos de dados para fornecer feedback sobre o que está acontecendo. Portanto, sim, a integração de sistemas de sensores seria o primeiro passo. Mas você precisa fazer uma sistemática aquisição de dados, e também fornecer uma arquitetura de armazenamento de dados, para ser capaz de fazer algo com os dados . Na verdade, você vê muitas empresas que têm sensores integrados, mas elas não fazem nada com os dados ”.
Rede de produção AI
Ao responder às perguntas acima, Sause continuou voltando para vários grupos dentro da UNA, bem como empresas spin-off que podem fornecer integração de sensores e serviços de gêmeos digitais. Para esse fim, a Augsburg AI Production Network foi lançada em janeiro de 2021 pela UNA, DLR ZLP e Fraunhofer IGCV. “A estrutura de colaboração vem de projetos que tivemos com DLR e Fraunhofer no passado”, diz Sause. “Estamos pegando o plano de desenvolvimento de produção baseado em IA da CosiMo e agora estendendo-o para uma escala muito ampla. Assim, por exemplo, o orçamento para o nosso trabalho no CosiMo foi de 10 milhões de euros, mas para a AI Production Network é de 92 milhões de euros como financiamento inicial. Isso nos dará a possibilidade de iniciar muitos novos projetos de pesquisa como o CosiMo na exploração de IA na manufatura. E não estamos trabalhando apenas com compósitos, mas temos um forte foco neles. ”
O uso de sensores ultrassônicos para melhorar a usinagem CNC é um projeto já iniciado em 2021. “Há um projeto prestes a começar na reciclagem de compósitos de matriz cerâmica (CMC)”, diz Sause, “e teremos vários projetos com uma estreita ligação entre manufatura aditiva e a reutilização de materiais reforçados com fibra especificamente reciclados. ”
Quanto aos papéis que cada organização vai desempenhar, Sause explica que não há competição, pois cada instituição tem um orçamento alocado. “Todos nós temos a nossa parte e, portanto, somos livres para colaborar como no passado. Além disso, nos conhecemos muito bem e conhecemos nossas competências, pontos fortes e fracos. É divertido trabalhar juntos porque sabemos o que podemos e o que não podemos fazer. Fomos procurados por muitas empresas que querem trabalhar conosco e estamos discutindo agora como encontrar a combinação ideal do nosso lado de competências ”.
Em relação à unidade de produção de 5.000 metros quadrados, “todos nós faremos isso juntos”, diz Sause. “Estamos planejando inaugurar no início de 2023 e começar a instalar máquinas. E forneceremos configurações de produção automatizadas que vinculam as células individuais. Muitos deles terão foco em tecnologias de produção de compostos. E faremos isso também para mostrar e demonstrar aos parceiros da indústria o que a IA pode fazer em tal ambiente de produção. Também queremos ter parceiros da indústria chegando e também colocando máquinas em nossas instalações para que possamos executar projetos juntos para ver como conectar e integrar novas soluções para seus locais. ”
Resina
- Válvulas para difícil desligamento e controle
- Sensores e sistemas para CBM
- Engenharia de processo de revestimento por imersão e otimização de desempenho para dispositivos eletrocrômicos de três estados
- OTOMcomposite desenvolve software para produção de Composites 4.0 usando colocação e enrolamento assistido por laser
- Resinas epóxi reprocessáveis, reparáveis e recicláveis para compósitos
- TPAC e TPRC desenvolvem processo de reciclagem de compósitos termoplásticos
- Dicas para configuração e fiação das caixas do painel de controle
- O que é usinagem ultrassônica? - Trabalho e processo
- Conexões para Controle:Interfaces de Comunicação para Sensores de Posição e Movimento
- Coletar dados de campo para otimização do processo