Sensores e sistemas para CBM
A manutenção baseada em condições (CBM) tem a promessa de prever os requisitos de manutenção de máquinas com base nas medições de desempenho do processo. Um sistema CBM pode minimizar as ações de manutenção no equipamento sem afetar a disponibilidade ou confiabilidade do sistema. CBM fornece um método de manutenção eficiente e econômico usando tecnologia de detecção, processamento de sinal e técnicas de software.
A manutenção baseada na condição permite que você tome medidas corretivas planejadas após a detecção e identificação da degradação do desempenho do maquinário. O principal benefício de um sistema CBM é o aumento da disponibilidade (tempo de atividade) de máquinas e equipamentos da fábrica. Outros benefícios incluem menores custos de manutenção, reduzindo as horas de manutenção preventiva e corretiva e a prevenção de danos secundários, detectando potenciais falhas de maquinário.
Historicamente, devido aos custos envolvidos, a manutenção baseada na condição tem sido aplicada a grandes máquinas rotativas, como motores, bombas, geradores, compressores e máquinas semelhantes. Os sensores são o primeiro elo em um sistema de manutenção baseado em condições implementado com sucesso.
Técnicas de detecção para CBM
Sensores tradicionais usados em aplicações de CBM em larga escala podem incluir os seguintes tipos de dispositivos:
Sensores de vibração (acelerômetros) medem o movimento da máquina e identificam falhas mecânicas que estão se desenvolvendo, como desalinhamentos no equipamento acionado ou montagens do motor com falha.
A bobina de fluxo e as leituras de corrente monitoram as condições elétricas. Níveis de corrente aumentados podem indicar desgaste do rolamento em um sistema de transporte ou uma correia pegajosa (pegajosa).
Transdutores de temperatura, como termistores, detectores de temperatura por resistência (RTDs) e termopares, monitoram a temperatura ambiente e a temperatura da superfície do motor. Eles podem determinar as condições de superaquecimento do motor e indicar altas temperaturas da estrutura causadas por desgaste excessivo do rolamento.
Os termovisores - unidades portáteis sem contato - são dispositivos usados para digitalizar e salvar a temperatura e a imagem infravermelha de equipamentos de produção. Esses dados são úteis para comparar operações normais e anormais. O calor pode ser um indicador precoce de dano ou mau funcionamento da máquina.
Transdutores ultrassônicos detectam vazamentos e inspecionam componentes mecânicos e elétricos.
Expansão das aplicações de CBM
Com o menor custo dos sensores e maior poder de processamento embutido disponível hoje, mais aplicações para CBM agora são viáveis e econômicas. Muitos dispositivos elétricos agora incorporam sensores que podem fornecer dados de desempenho junto com suas funções básicas de controle. Por exemplo, os usuários de servos e outros sistemas de acionamento podem implementar algoritmos de manutenção preditiva que monitoram o torque de saída do motor detectando a saída de corrente do inversor (consulte a Foto 1).
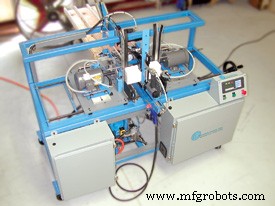
Foto 1. Máquina de produção de veneziana contendo um sistema de acionamento servo.
(Foto cortesia de G&L Technologies)
Uma vez que o torque necessário em cada ponto de um ciclo "normal" da máquina é conhecido, é bastante simples monitorar este perfil de torque e alertar o pessoal de manutenção sobre quaisquer anormalidades. O aumento da saída de torque pode indicar um rolamento que está começando a falhar ou outros problemas mecânicos iminentes. Com esse conhecimento, você pode reparar o equipamento mecânico durante o próximo período de manutenção programada, em vez de fazer reparos após uma avaria inesperada. Tipos menos sofisticados de controle de movimento (ou seja, sistemas de passo) que não têm capacidade de detecção de torque não podem fornecer este tipo de informação. Pode ser mais eficiente a longo prazo instalar um inversor mais capaz com base somente em sua capacidade de auxiliar na manutenção preditiva.
Os sensores usados para monitorar as condições da máquina ou do processo podem relatar dados, mas, em última análise, é o sistema ao qual eles estão conectados que fornece a inteligência para interpretar os dados e agir.
Um exemplo de manutenção baseada em condições usando uma plataforma lógica é um sistema de gerenciamento de medição de pH. Uma aplicação é um sistema integrado de autolimpeza, autocalibração e autodiagnóstico para sensores de pH instalados em um processo ativo. Um controlador lógico programável (PLC) testa, limpa e calibra automaticamente sondas de pH em aplicações onde as sondas são expostas a condições abrasivas ou cáusticas. Para medir o desvio e a eficiência, o PLC retrai a sonda de pH do processo, injeta buffers de pH conhecidos e lê as entradas de 4-20 miliamperes (mA). O PLC é capaz de compensar o desvio (polarização / deslocamento) e a eficiência diminuída (inclinação) ao longo do tempo para registrar e relatar uma medição de pH precisa. Com base na curva de degradação do desempenho, o sistema também pode prever quando a sonda exigirá a substituição completa.
O sistema CBM de conectividade aberta
Os sistemas de monitoramento distribuído de hoje mudaram para arquiteturas baseadas em padrões abertos para hardware e software. Plataformas baseadas em PLC e PC que se comunicam com dispositivos e sensores de entrada / saída distribuída (E / S) em uma variedade de redes fieldbus aceitas, abriram caminho para as aplicações CBM.
OPC, ou OLE (Object Linking and Embedding) para Controle de Processo, é um padrão da indústria criado por vários fornecedores líderes de hardware e software em cooperação com a Microsoft. Usando a tecnologia de conectividade aberta, os dados ao vivo de dispositivos industriais podem ser comunicados aos sistemas upstream ou a uma página da Web sem a necessidade de programação. Os dados ficam então disponíveis para visualização, impressão ou arquivamento em qualquer computador ou em qualquer lugar onde a Internet ou intranet da empresa esteja acessível. A tecnologia OPC permite uma coleta e exibição fácil e econômica de dados porque é suportada por muitos dispositivos diferentes. Como um benefício adicional, o software OPC é capaz de oferecer uma abordagem mais unificada para exibição de dados e registro para plantas que usam várias marcas de PLC (consulte o Gráfico 1).
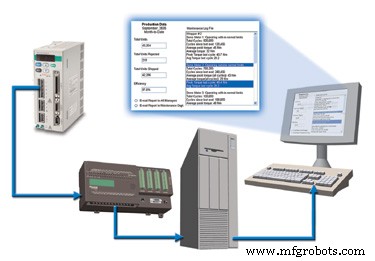
Gráfico 1. A coleta de dados baseada em OPC de um sistema de controle fornece dados úteis para decisões de manutenção.
O software OPC oferece muitos recursos úteis projetados para tornar os dados monitorados mais acessíveis e úteis. Por exemplo, as cores dinâmicas permitem que os usuários determinem o status de suas operações de processo em um piscar de olhos. Use-os como um sistema de alerta precoce para alertar o pessoal sobre anormalidades nas operações. As funções matemáticas podem realizar cálculos nos dados brutos antes de serem exibidos ou processados posteriormente. Muitos programas de CBM baseados em OPC já estão disponíveis para gerenciar os esforços de manutenção.
Conclusão
Quando implementado corretamente, um sistema de manutenção baseado em condições ajudará a reduzir os custos de manutenção, aumentar a disponibilidade e confiabilidade da máquina, melhorar a segurança, melhorar a qualidade do produto e, em muitos casos, prolongar a vida útil do equipamento. Carl Hamilton é um especialista técnico da AutomationDirect, um vendedor direto de produtos de automação e controle industrial. Para obter mais informações, ligue 800-633-0405 ou visite www.automationdirect.com. Saiba mais sobre automação. Um glossário de termos comuns de automação está disponível por e-mail, editor da Reliable Plant Paul V. Arnold em [email protected].
Manutenção e reparo de equipamentos
- Kontron e SYSGO:plataforma de computação SAFe-VX para sistemas críticos de segurança
- Sistema de recompensa conjunto impulsiona resultados e trabalho em equipe
- Uma lição de direção para operações e manutenção
- Estratégia e soluções do Exército para manutenção baseada em condições
- Deming, Drucker e um caso para planejamento e programação
- 5 Regras para operações e manutenção de parceria
- Inspeções audíveis, visuais e táteis para pessoal de manutenção preditiva
- Miller nomeado vice-presidente de manutenção e fabricação da divisão de empilhadeiras Toyota
- Extensão de controle para planejadores de manutenção e outros
- CBM e RCM ajudam a maximizar a segurança, tempo de atividade no YICT