O processo personalizado produz pedal de freio composto a cada minuto
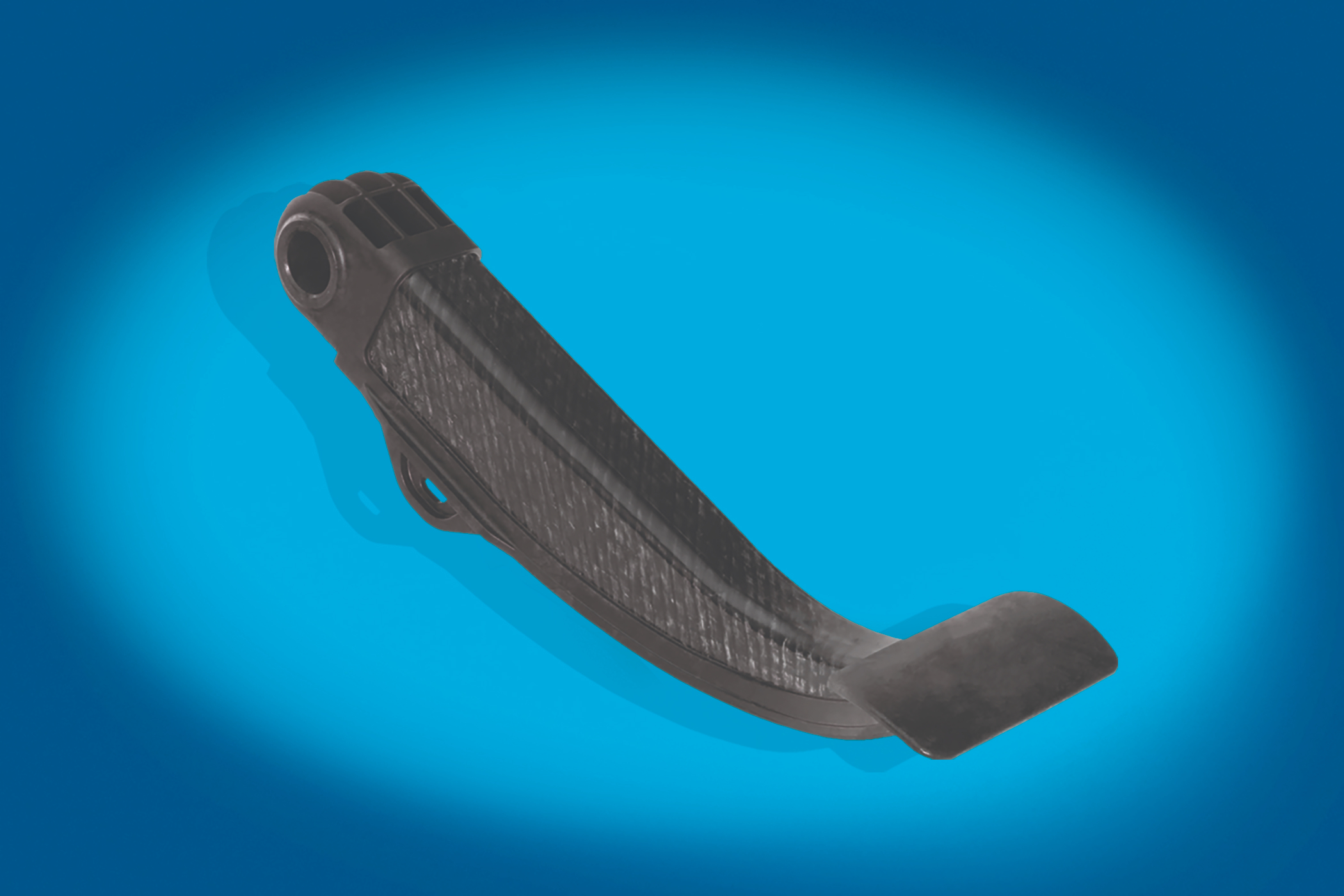
Tier 1 Boge Rubber &Plastics Group (Damme, Alemanha) produz o que diz ser os pedais de freio totalmente compostos mais leves, mais baratos e mais fortes do mundo, e os primeiros em produção comercial. Conforme detalhado no FOD de janeiro (consulte "Estrutura composta termoplástica substitui metais em pedais de freio de segurança crítica"), o fornecedor produz atualmente 250 mil pedais de freio por ano para quatro plataformas de veículos produzidas por montadoras alemãs e o sistema pode produzir até 1 milhões de pedais anualmente. Isso é significativo porque os pedais são estruturais, precisam atender aos mesmos requisitos rigorosos de desempenho do aço e alumínio tradicionais, e os projetos apresentam três tipos diferentes de compostos termoplásticos reforçados com vidro.
Três materiais aumentam a eficiência da fibra
Para manter os pedais leves, finos, econômicos e capazes de atender às especificações desafiadoras do OEM, Boge usa folha orgânica de fibra de vidro contínua como a estrutura da concha para transportar as cargas principais da peça, que podem chegar a 3.000 newtons. Os espaços em branco de organosheet são fornecidos pré-cortados no tamanho, com duas ou três camadas totalmente consolidadas pelo fornecedor Lanxess Deutschland GmbH (Colônia, Alemanha). Para reforçar os caminhos de carga principais na folha de organosheet, Boge adiciona tiras de fitas de fibra de vidro unidirecionais (UD) (fornecidas pela Celanese Corp., Irving, Texas, U.S.) em orientações e layups com base em resultados de simulação de elementos finitos. Para fazer isso, Boge usa um software que modificou e cartões de material que a empresa desenvolveu com seus fornecedores com base em curvas de tensão / deformação medidas para cada material sob condições de temperatura e umidade especificadas por clientes OEM. Para adicionar geometria funcional, Boge usa compostos de fibra de vidro cortada sobremoldada (de vários fornecedores) para fornecer nervuras estruturais e recursos de fixação.
Todos os materiais apresentam matrizes de poliamida 6 (PA6) preta pré-colorida, um polímero resistente amplamente utilizado na indústria automotiva. Caso as especificações do fabricante o exijam, Boge também tem a opção de usar uma matriz PA6 / 6 de temperatura mais alta e menos higroscópica no composto de sobremoldagem, uma vez que os dois polímeros são semelhantes o suficiente para se ligarem. Ao usar três tipos diferentes de compósitos com reforço de vidro em três formas diferentes, Boge é capaz de colocar a fibra precisamente onde necessário para atender aos requisitos de desempenho, evitando o excesso de engenharia. O efeito residual dessa abordagem de composto híbrido é que ela reduz o uso de material, a espessura nominal da parede, o tempo de ciclo e o custo geral da peça.
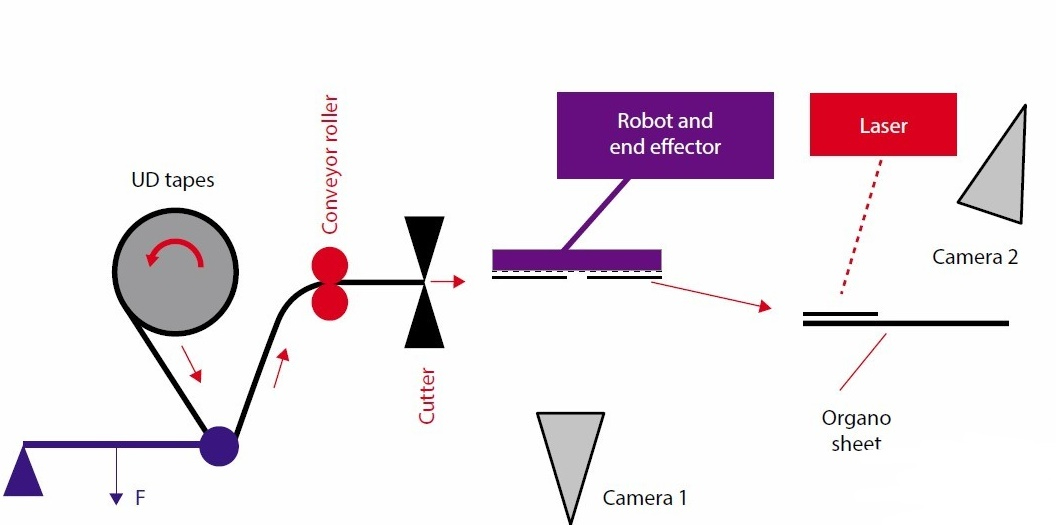
Etapas do processo e critérios do equipamento
Em parceria com o desenvolvedor de automação / linha de montagem M.A.i. GmbH &Co. KG (Kronach, Alemanha), Boge desenvolveu um processo de produção de três etapas que é rápido, eficiente e produz peças com qualidade verificada a custos acessíveis. Ao projetar processos e equipamentos, a equipe tinha uma série de requisitos. Primeiro, para manter baixos os custos das peças, as empresas precisavam manter o tempo de ciclo efetivo total de aproximadamente 1 minuto. Alcançar isso exigiria automação para garantir que os materiais se movessem suavemente pela célula de manufatura.
Em segundo lugar, enquanto as folhas de organosheet são fornecidas pré-empacotadas, totalmente consolidadas e pré-cortadas no tamanho (contornado), os requisitos de vários designs de pedal significavam que a equipe precisava de flexibilidade para cortar, orientar e colocar tiras de fita de diferentes comprimentos em diferentes locais e direções para reforçar o principais caminhos de carga do shell organosheet. Novamente, para manter os custos baixos, um processo de colocação de fita sob medida foi projetado para oferecer um alto nível de flexibilidade e controle, bem como velocidade.
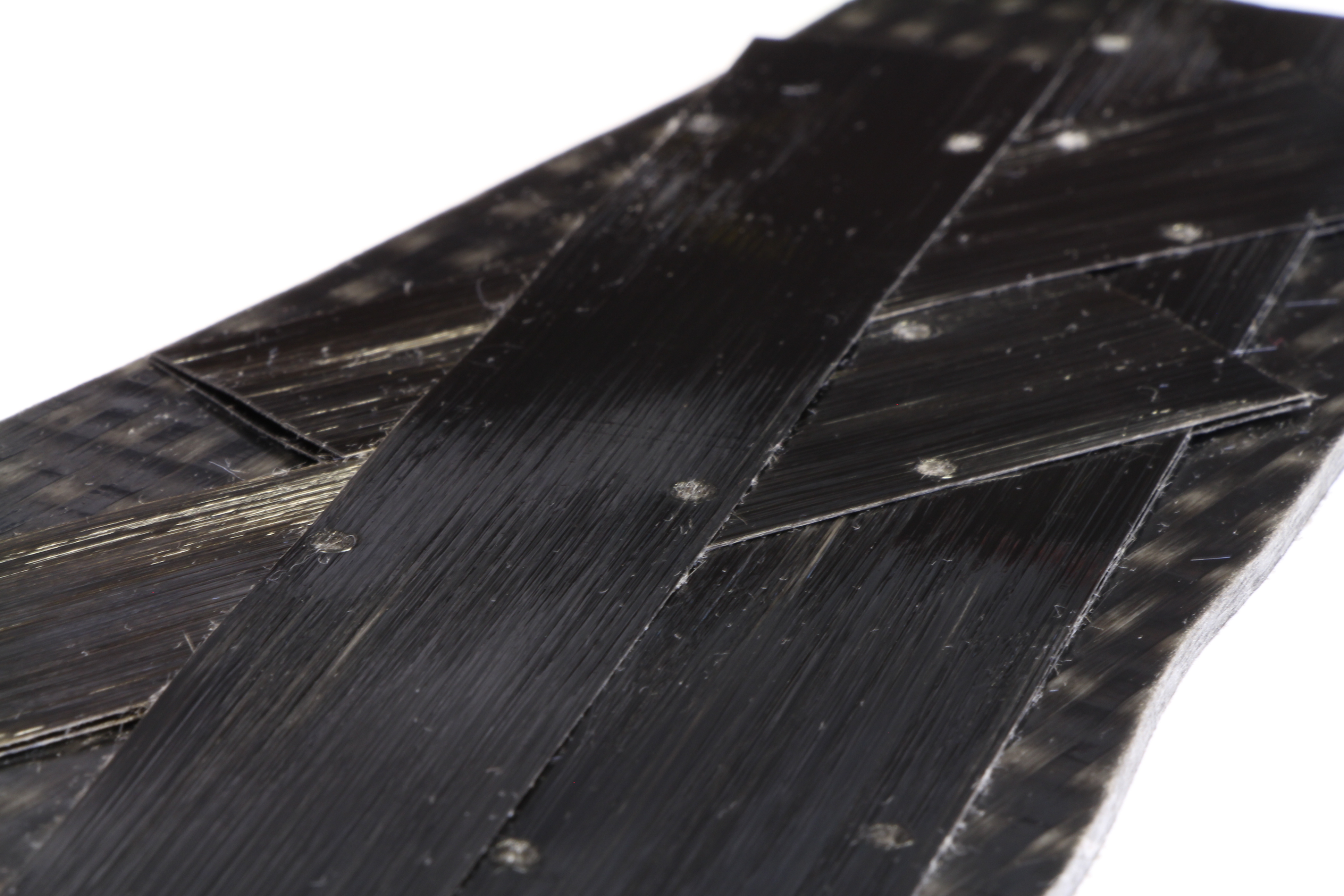
No início do processo, a célula de fabricação contém duas pilhas de pré-cortados blanks de organosheet em cassetes e quatro gaiolas de fitas UD de uma só vez. Primeiro, um robô pega uma peça em branco contornada de folha orgânica e a move para a superfície de trabalho. Ao mesmo tempo, a fita UD é alimentada e cortada no comprimento necessário. As tiras são então colocadas em uma correia de vácuo que as mantém no lugar conforme o transportador avança. Em seguida, um robô com uma unidade giratória pick-and-place (efetor final) arranca uma tira de cada vez da correia de vácuo e uma câmera verifica cada tira quanto à qualidade, dimensão e posição. Quando todas as quatro peças foram recolhidas, o robô se move para a área de trabalho e começa a colocar uma tira de cada vez na folha de organosheet no local e posição determinados pela correção de posição baseada em imagem. Conforme cada tira é posicionada, ela é impedida de se deslocar por vários pontos de solda criados por um laser. Enquanto isso, mais tiras de fita estão sendo cortadas e colocadas na esteira de vácuo e o processo se repete até que todas as fitas necessárias para um determinado projeto de pedal de freio sejam empilhadas e coladas na posição correta na folha organos.
O sistema que produz este blank de fibra sob medida é 100% controlado numericamente, com todos os aspectos da operação totalmente programáveis para máxima flexibilidade. Em cada etapa, as câmeras ou outros sensores, que estão conectados ao sistema de controle de qualidade online (QC) do sistema, detectam todas as bordas e posições das tiras de fita e do invólucro da folha orgânica e comparam os dados geométricos desses materiais com parâmetros conhecidos para garantir que cada material seja posicionado onde precisa estar.
Para manter as velocidades de produção altas, a folha de fibra sob medida segue em seguida para um forno infravermelho para aquecer ambos os materiais antes de colocar / pré-formar / consolidar as fitas na folha orgânica. Um pacote especial de antioxidantes em sistemas de fita e resina orgânica evita danos térmicos. Em seguida, a peça em bruto a quente é rapidamente movida para a cavidade de revestimento / pré-formação, onde a alta pressão é usada para formar a peça em formato de canal em U, garantindo uma superfície de alta qualidade. O sistema QC monitora novamente a consolidação e a qualidade da pré-formação por meio do tempo, temperatura e pressão.
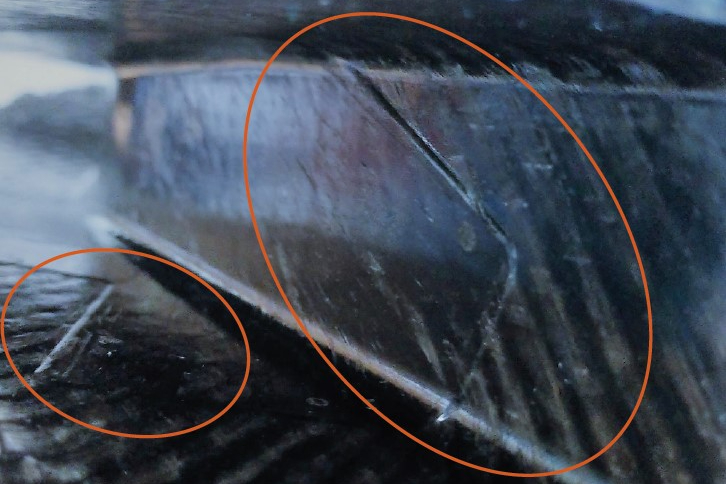
Finalmente, a peça ainda quente e drapeada é transportada para um molde de injeção onde é moldada com um composto de vidro curto / PA para criar geometria adicional, como uma estrutura de nervura complexa na parte inferior. Após a desmoldagem, um corte rápido e automatizado e uma inspeção visual são feitos. Nenhuma pintura ou outro acabamento de superfície é necessário. O tamanho final do pedal é de aproximadamente 350 x 90 x 60 milímetros. Antes de deixar a célula de fabricação, um código QR exclusivo é afixado a cada pedal para vinculá-lo aos dados de fabricação e materiais desse pedal no sistema de qualidade. Após a montagem, é realizado um teste funcional do pedal em seu suporte e uma inspeção robótica final. Presumindo que a unidade seja aprovada, outro código QR é afixado ao conjunto completo do pedal do freio para fornecer rastreabilidade completa de cada pedal e componentes adicionais antes do envio ao OEM.
Como os pedais de freio são peças essenciais para a segurança e devem atender às exigências do desempenho do OEM, bem como aos requisitos de qualidade, Boge e seus parceiros construíram vários mecanismos à prova de falhas no sistema de QC compatível com a Indústria 4.0 para verificar com rapidez e precisão se as especificações foram atendidas em cada etapa o processo. Os dados de CQ são armazenados e cada pedal recebe um número de identificação exclusivo na forma de um código QR para garantir 100% de rastreabilidade do material, mudanças e condições de processo envolvidas na produção daquela peça.
Os pedais de freio totalmente compostos que Boge está produzindo pesam cerca de metade do peso dos pedais de metal. Eles também melhoram a sensação ao toque de direção para os consumidores, são 100% recicláveis no final da vida útil e atendem ou excedem o requisito de resistência do aço incumbente.
Resina
- Os métodos de fabricação de compósitos mais populares
- Rebarbação e rebarbação criogênica
- Primeiro pedal de freio totalmente de plástico para carro esportivo elétrico a bateria
- Solvay Expande a Capacidade do Composto Termoplástico
- Roda termoplástica faz o caminho difícil
- Composto de revestimento arquitetônico revelado
- Fazendo melhores bicicletas compostas no Arkansas
- Como funciona o processo CMC
- As 4 coisas essenciais que todo operador de prensa dobradeira deve saber
- 4 coisas que todo operador de dobradeira deve saber durante o sono