A industrialização do epóxi termoplástico
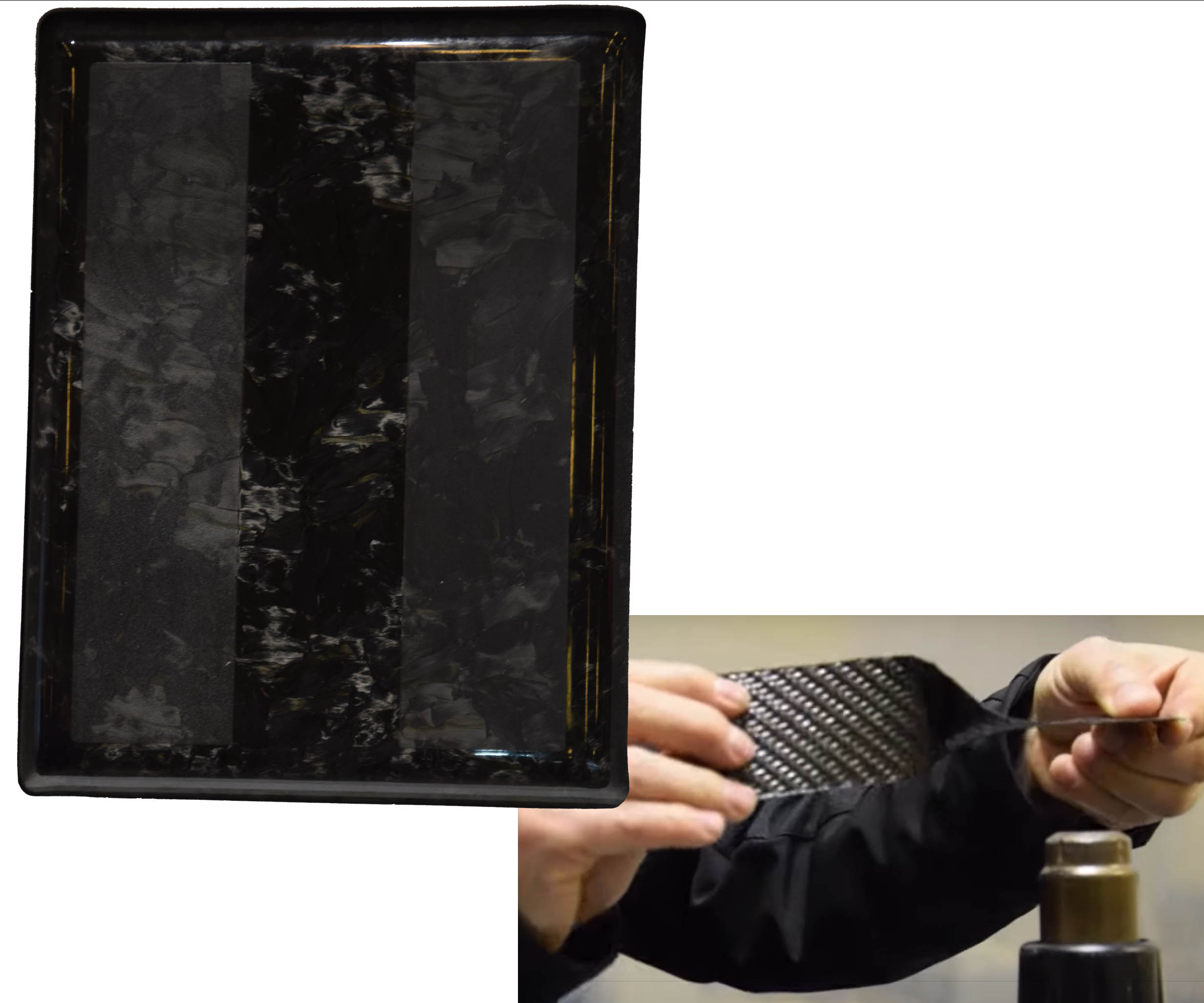
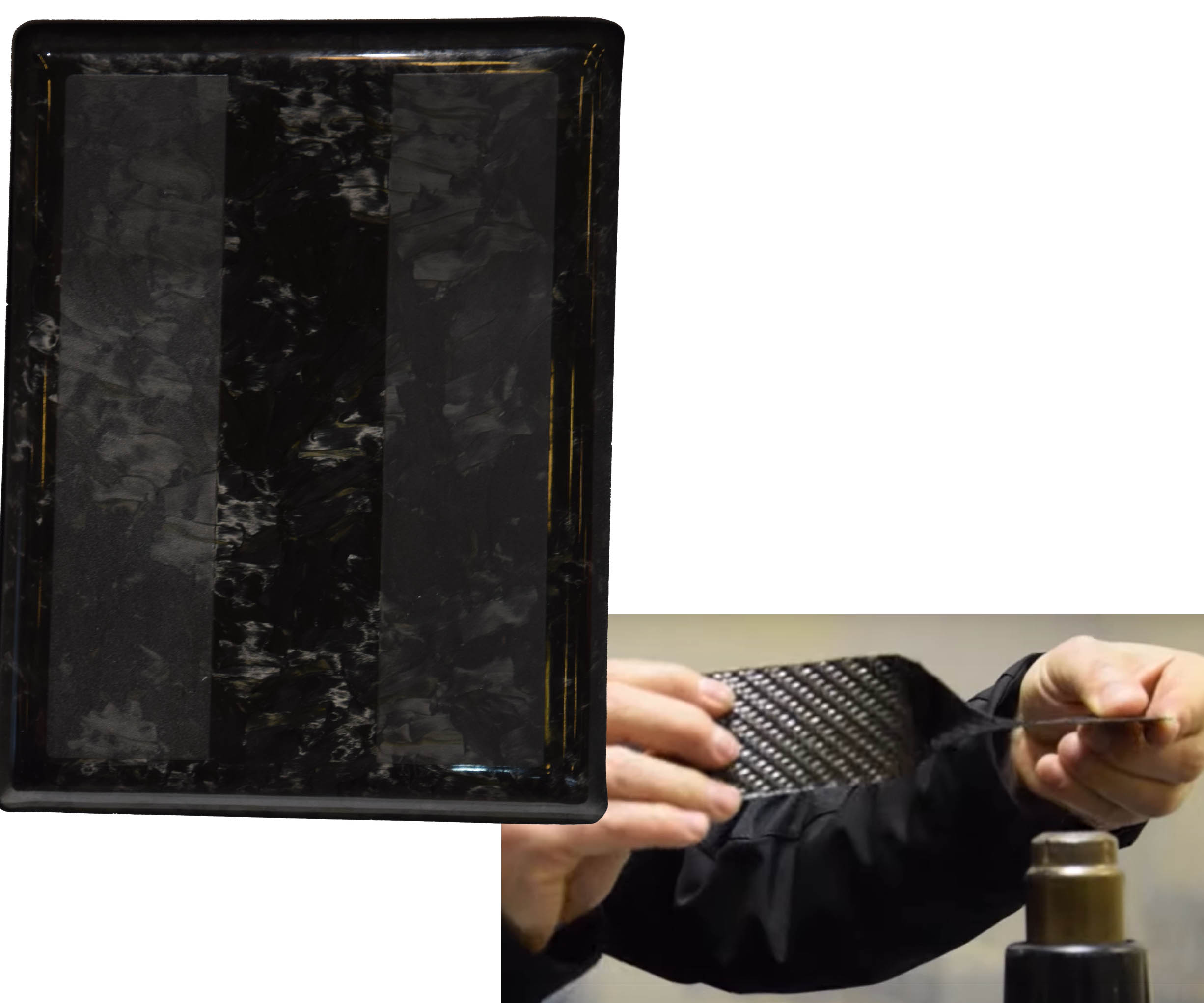
A Cecence (Salisbury, Reino Unido) foi fundada em 2014 por três fundadores com décadas de experiência em compósitos. O diretor Mike Orange tinha uma longa história em aparelhamento de polímero reforçado com fibra de carbono (CFRP) e mastros para iates. Chefe de inovação Humphrey Bunyan foi anteriormente chefe de inovação da Future Fibers (Valência, Espanha). “Eles [Future Fibers] estavam fazendo aparelhagem totalmente composta para a America’s Cup e outras embarcações de corrida, bem como amarras de CFRP para prender as rodas em carros de Fórmula 1”, diz Orange (consulte “Compostos de construção de iates:preparados para o sucesso”). “Nós entendemos as vantagens do peso leve, mas estávamos nos envolvendo com outros setores que não tinham nossa experiência e lutamos com os custos, aumentando a produção e atendendo às regulamentações contra incêndio.”
Assim, a Cecence (pronuncia-se “ver sentido, como no senso comum com compósitos de fibra de carbono) foi fundada para focar na resistência ao fogo, manufatura industrializada e sustentabilidade. Isso resultou em desenvolvimentos como um encosto de banco de fibra de carbono moldado por compressão / bioresina para aeronaves de passageiros que pesava apenas 7,5 quilogramas, espessura reduzida do assento para menos de 20 milímetros e maior espaço para passageiros e conforto, ao mesmo tempo em que atende a todos os requisitos de incêndio, fumaça e toxicidade (FST).
“Em um projeto anterior, a Cecence desenvolveu um método de fabricação de prensagem a quente que reduziu o tempo de ciclo de 2,5 horas para 7 minutos para um encosto da classe econômica usando fenólicos de cura instantânea desenvolvido com U.K. prepregger FTI (Somerset) ”, diz Orange. Para este último encosto descrito acima, que desenvolveu com Design Q (Redditch, Reino Unido), a Cecence expandiu seu portfólio FST usando um pré-impregnado de resina de álcool polifurílico (PFA) desenvolvido pela SHD Composites (Sleaford, Reino Unido). O PFA é um polímero termofixo derivado da biomassa que atua como um fenólico com excelente processamento de superfície e sustentabilidade (consulte “Resistindo ao fogo sem o peso”). “Trabalhamos com SHD Composites e impulsionamos sua química para uma cura mais rápida”, disse Orange. “Isso é o que fazemos:pegamos materiais, processos e designs e os desenvolvemos ainda mais para que produtos compostos possam ser fabricados em escala de uma forma comercialmente viável, mas sustentável”.
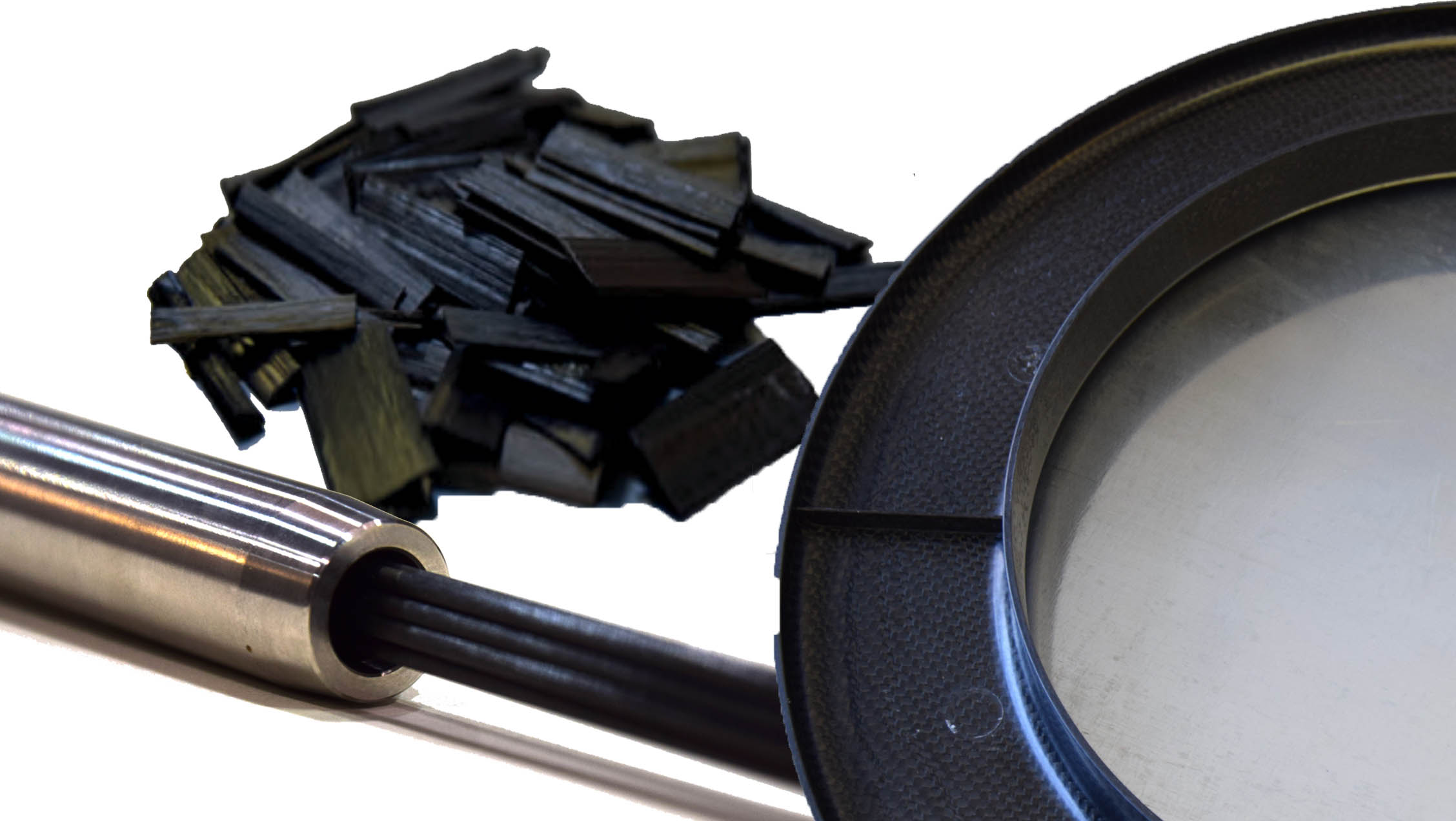
A velocidade de fabricação e a sustentabilidade foram fatores-chave quando a Cecence encontrou um sistema de resina epóxi termoplástica há vários anos. “Este termoplástico com componentes epóxi no final de suas cadeias de polímero estava sendo usado por uma empresa de tecidos que não percebeu seu potencial em compósitos”, explica Orange.
“Nós entendemos imediatamente as vantagens de um termoplástico de baixa viscosidade que poderia impregnar as fibras muito bem enquanto possibilitava um epóxi termoformável”, disse Humphrey Bunyan. A Cecence desenvolveu um pré-impregnado com base nesta tecnologia de epóxi termoplástico e, em seguida, uma família de produtos sob a marca K_Series:K_Rod enrolável, K_Plate semi-preg de 0,25 a 1,98 mm de espessura e composto para moldagem K_Chip (Fig. 1). “Conseguimos moldar componentes sob pressão em menos de três minutos”, diz Orange, “e demonstramos uma variante FR que atende aos requisitos da FST para interiores de aeronaves”. A Cecence também usou o material para desenvolver um sistema de equipamento de linha aérea composta (COHLE) para linhas ferroviárias elétricas que reduz o número de postes / postes de apoio pela metade e o custo geral de instalação e operação em £ 100.000 ($ 124.200) por quilômetro.
Epóxi termoformável
“Com termoplásticos típicos, você tem um polímero de matriz de alta viscosidade que é difícil de forçar nas fibras”, explica Bunyan. “Assim, é difícil conseguir uma boa impregnação dos estopas ou tecidos. Mas o epóxi termoformável da série K tem uma viscosidade muito baixa - 80 centipoise a 100 ° C. Isso nos permite pré-impregnar reforços de fibra de vidro, carbono e natural com excelente distribuição de resina a fibra e, normalmente, 60% de teor de fibra por peso. Também podemos usar fibras com dimensionamento para epóxi, que normalmente não é compatível com termoplásticos. ” E ainda, este sistema é um verdadeiro termoplástico, permitindo a reforma de peças acabadas a 180-200 ° C sem nenhuma reação química ou exotérmica.
“Assim como o epóxi, ele adere bem à fibra, de forma que não há separação da fibra da matriz, mesmo que você use pressões mais altas durante a moldagem”, observa Orange. Isso se refere a um problema que ele viu com poliamida reforçada com fibra curta (PA) e compostos de polipropileno. “Estávamos trabalhando com uma camada de PA derretida em um tecido por meio de prensagem a quente para fazer uma folha plana. A matriz não estava aderindo às fibras, apenas em torno delas. Então, quando ele foi pressionado em uma parte, você obteria o arrancamento de fibra. ”
K_Plate, que processa a 150-220 ° C, oferece uma temperatura de serviço de 100 ° C para exposições curtas e uso contínuo a 90 ° C. Os compostos K_Chip de reboque unidirecional picado são pressionados a 240 ° C. “O T g [temperatura de transição vítrea] e início da deformação por calor para a série K são mais baixos do que os epóxis típicos, mas isso também torna a reforma e a reciclagem viáveis ”, diz Orange. Os processos da K_Series também são rápidos. “Cecence trabalhou com RocTool [Le Bourget du Lac, França] no JEC 2016 para demonstrar o termoplástico de formação mais rápida que eles viram”, diz ele, observando um tempo de ciclo de 2 minutos e 40 segundos para um capô automotivo. “O tempo de espera foi de apenas 25 segundos antes do resfriamento, usando 8-9 bar de pressão acima da membrana de vácuo. Eles também ficaram satisfeitos com o acabamento das superfícies fosca e brilhante [veja a imagem de abertura], observando que nosso material forneceu o melhor acabamento de todos os testados. ”
Além disso, os componentes epóxi nos produtos da série K tornam as peças compostas fáceis de pintar e colar, sem os primários especiais e a preparação necessária para os termoplásticos tradicionais. “Você pode colá-los em segundo lugar usando adesivos padrão”, acrescenta Bunyan. “Você também obtém boas propriedades de cisalhamento interlaminar e, em geral, tornam-se estruturas resistentes e de absorção de energia, graças ao termoplástico.”
Catenária CFRP para ferrovias elétricas de baixo custo
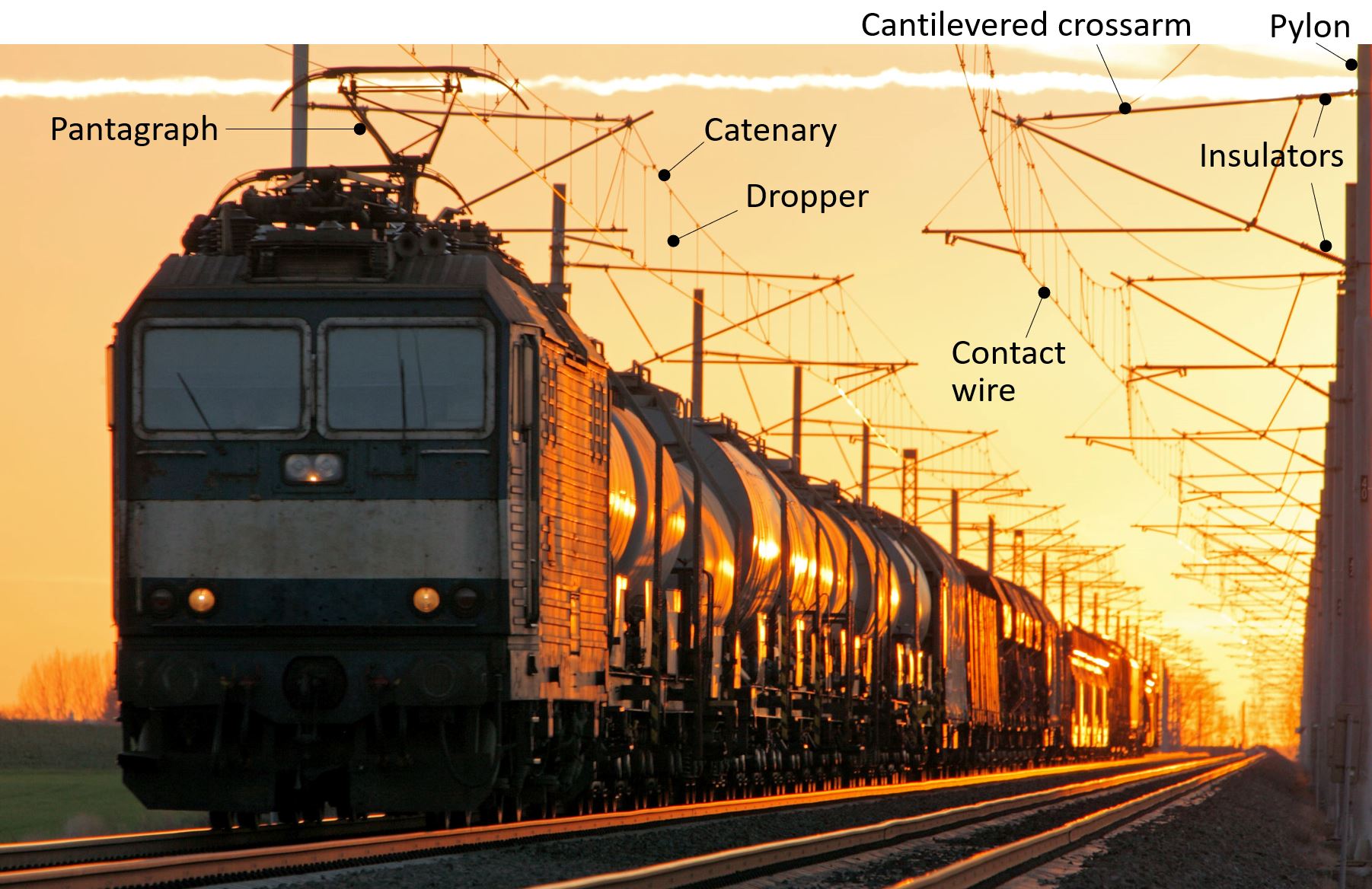
A natureza dupla deste epóxi termoplástico é exemplificada em um sistema de equipamento de linha aérea (OHLE) desenvolvido pela Cecence usando uma catenária CFRP feita com K_Rod. A catenária e o fio de contato condutor de corrente são os dois fios principais em um OHLE de ferrovia elétrica (Fig. 2). A eletricidade é fornecida à locomotiva de um trem por meio de um pantógrafo, que se estende do topo da locomotiva para pressionar contra o fio de contato. “A catenária funciona como uma ponte pênsil entre postes (mastros, postes), que são espaçados a cada 25 metros ao longo dos trilhos”, explica Orange. O fio de contato de cobre é suspenso da catenária por fios de conta-gotas verticais, da mesma forma que a estrada é sustentada por cabos em uma ponte pênsil.
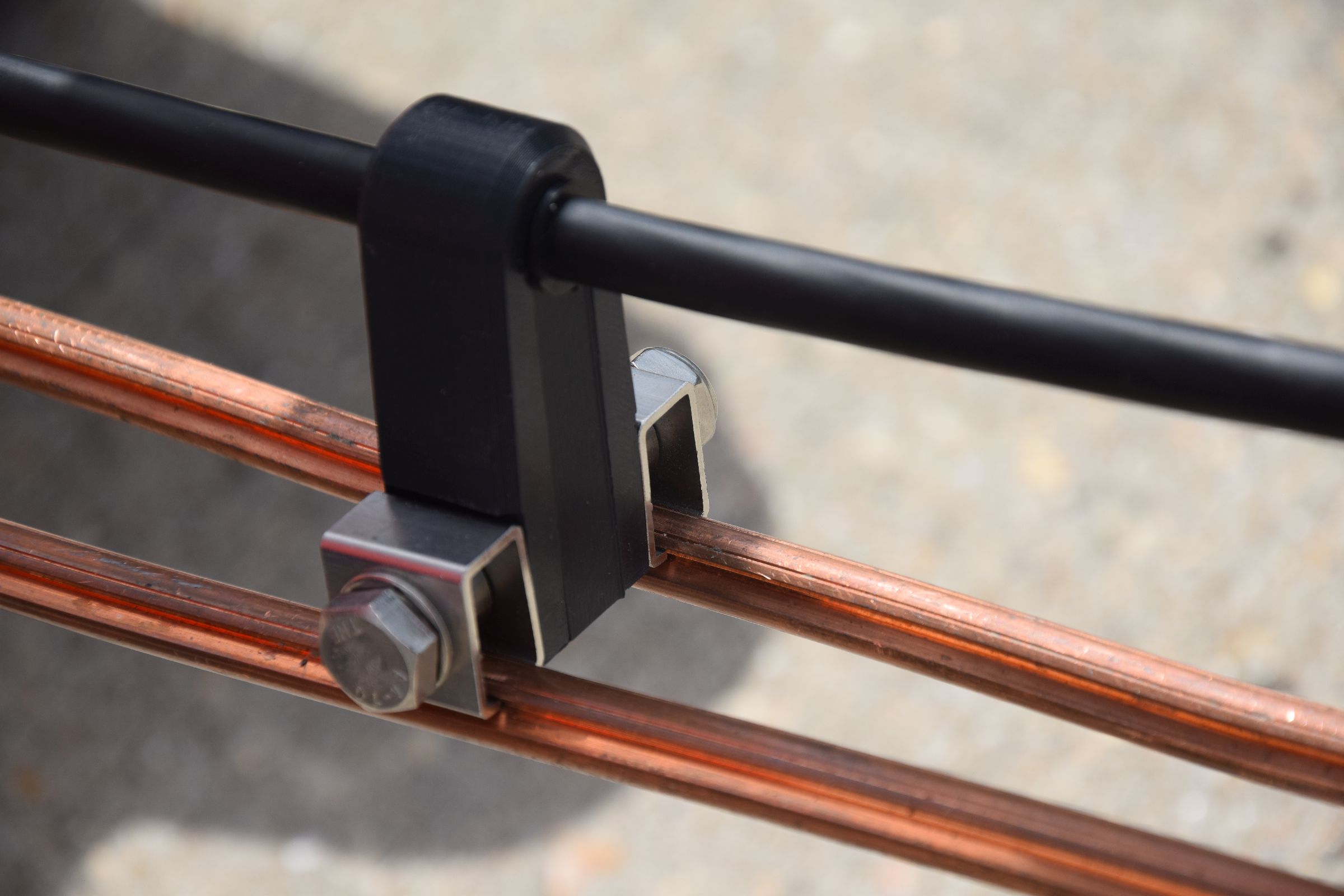
“Usando um cabo de tensão K_Rod como catenária, ele pode ficar a apenas 70 milímetros acima do fio de contato de cobre”, destaca Orange (Fig. 3). “Todo o sistema é mais compacto, com muito menor impacto visual no meio ambiente.” Os sistemas OHLE atuais usam cabos catenários de aço, que mudam de comprimento com a mudança de temperatura. “No verão, eles se estendem por até 400 milímetros por quilômetro”, observa ele. Para neutralizar essa flacidez nas linhas, contrapesos de concreto em polias são instalados como um sistema de autotensão, mas aumentam o custo geral.
“O peso da linha de aço e seu perfil de curvatura também são a razão pela qual tantos postes são necessários”, observa Orange. “Nosso cabo CFRP muda o comprimento em apenas 7 milímetros por quilômetro no verão porque a expansão térmica insignificante da fibra de carbono cria um composto termicamente estável. Também é 80 por cento mais leve que o cabo de aço, não cede e permite espaçar os postes de 50 metros, o que reduz pela metade o número de postes necessários. ” Isso permite uma maior economia de custos porque para cada poste há uma cruzeta em balanço, suportada por um arame.
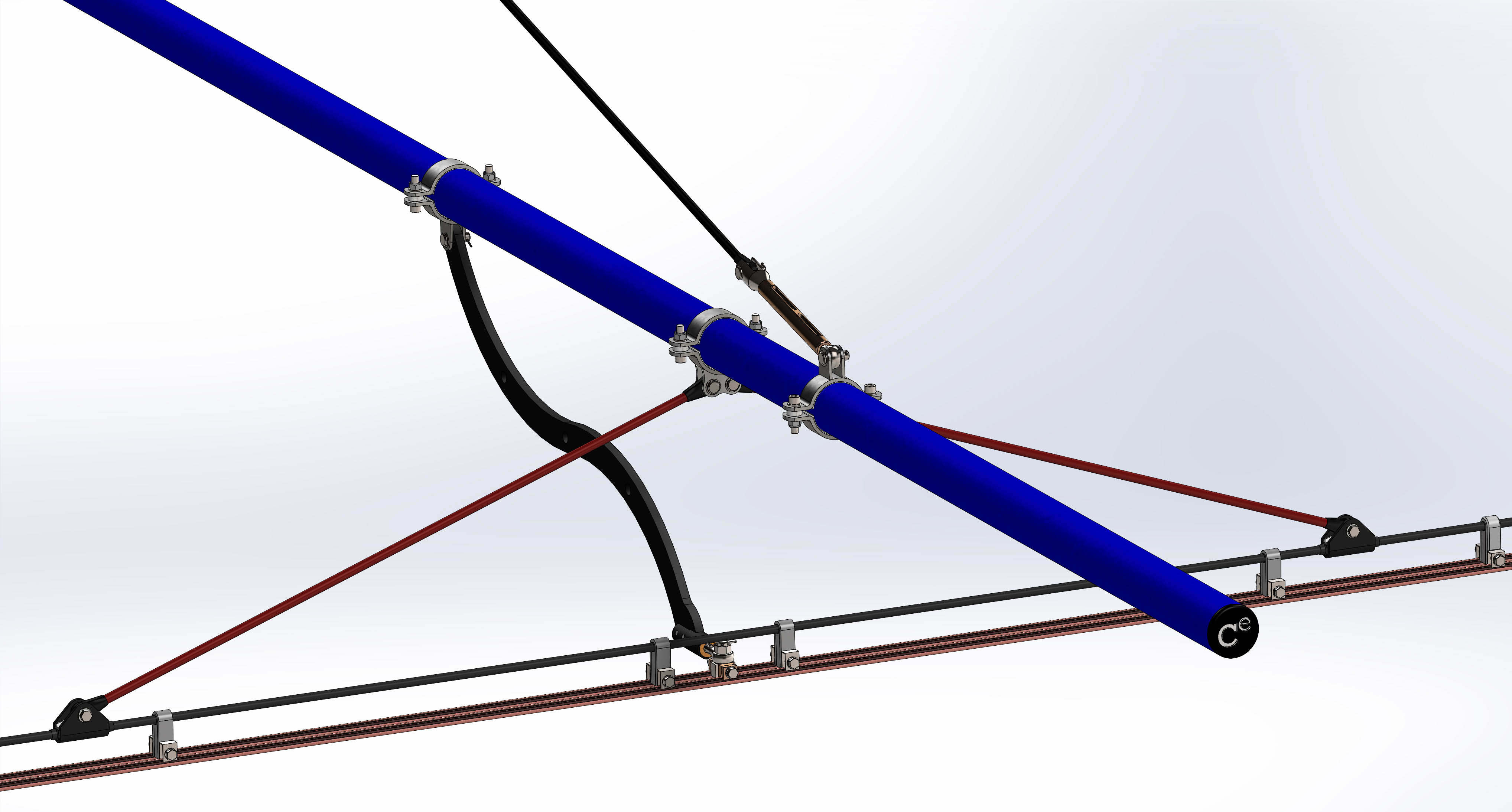
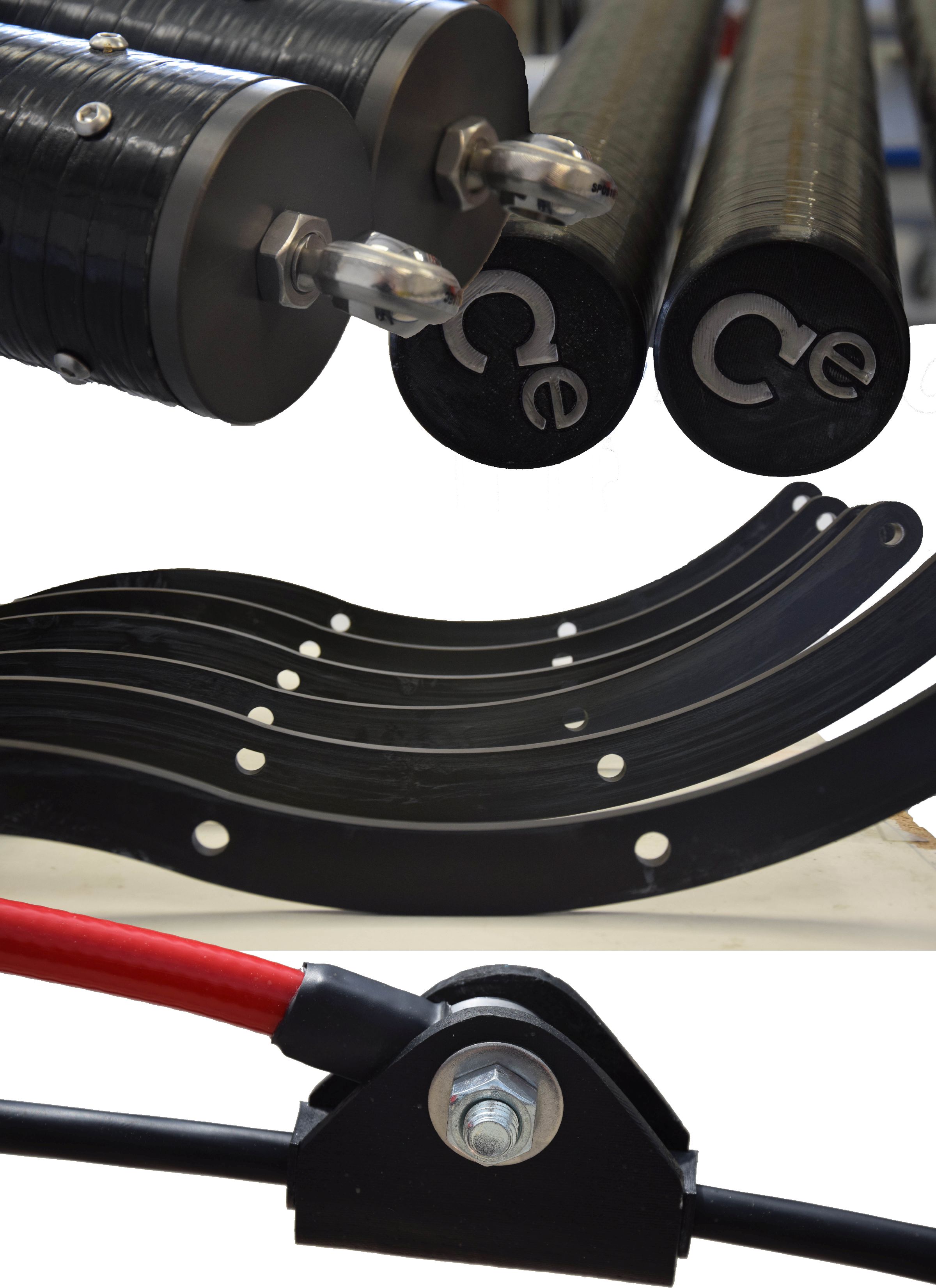
Além disso, os sistemas OHLE convencionais usam componentes totalmente metálicos, o que requer a adição de isoladores para evitar a condução indesejada da corrente elétrica. “O Cecence COHLE não precisa de todos os isoladores porque usa postes compostos de fibra de vidro não condutora (GF) e cruzetas com cabos de sustentação compostos não condutores”, explica Orange. “Também usamos conta-gotas intermediários feitos de ácido polilático impresso em 3D (PLA). Ao contrário de um sistema de metal, os postes não precisam de pintura regular e os compostos resistentes à corrosão exigem menos manutenção. ”
“O epóxi termoplástico desempenha um papel fundamental na catenária CFRP”, continua ele. “A Cecence o usa tanto no núcleo de fibra de carbono K_Rod quanto na jaqueta de compósito GF overtrançado. O resultado é um cabo isolado leve, de alta resistência que pode ser enrolado e se liga bem quando colado em um soquete, resolvendo o problema de terminação normalmente complicado para cabos compostos de fibra de carbono. Graças à incrível transferência de carga do núcleo para o soquete através da trança, não precisamos de um grande comprimento de soquete e este sistema é fácil, por isso é prático para instalar no campo por técnicos ferroviários. ”
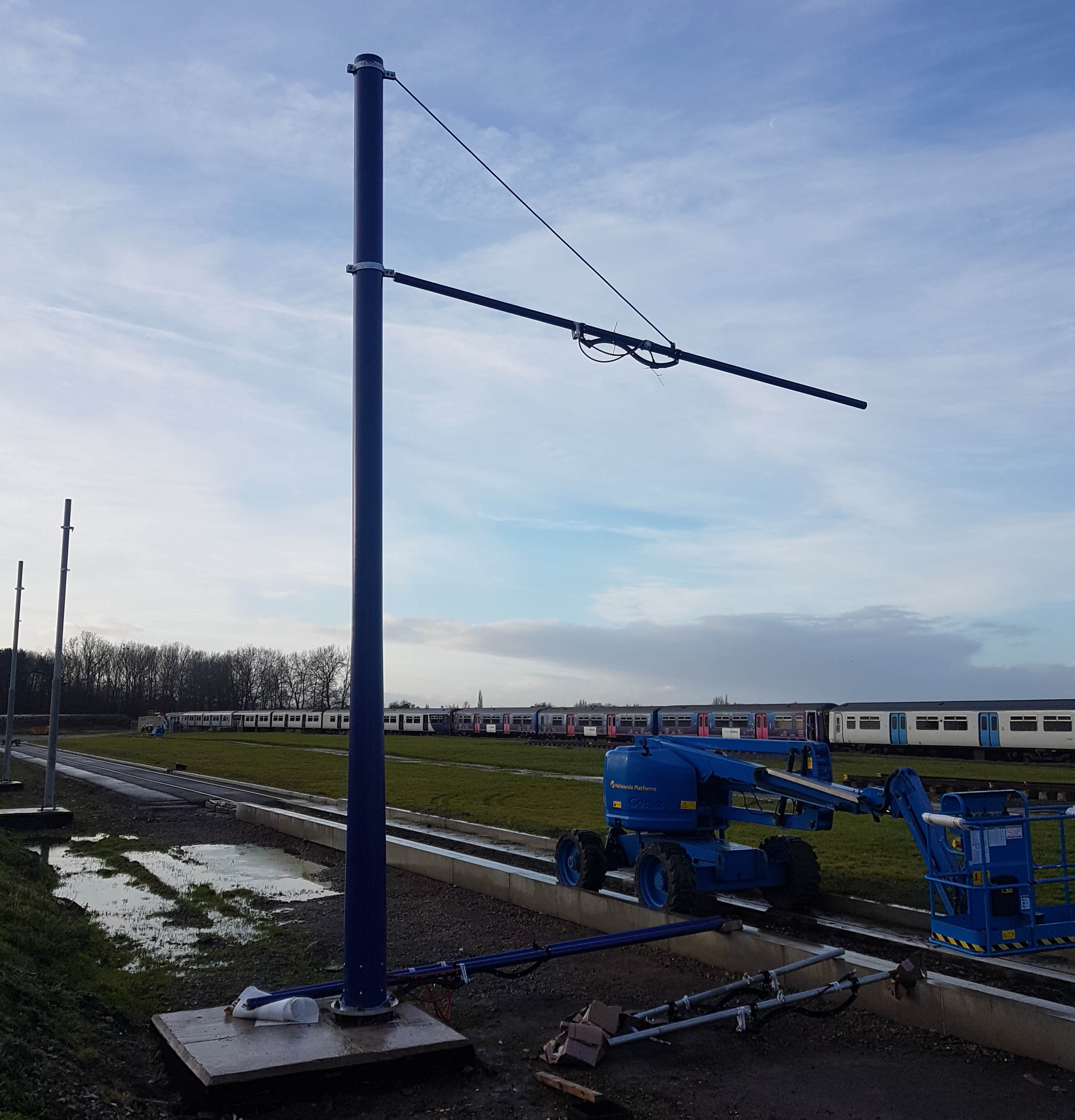
Mesmo que o cabo CFRP custe três vezes mais que uma catenária de aço, o custo geral do sistema é reduzido de £ 512.000 para £ 413.000 por quilômetro, diz Orange. Esses custos, calculados com a empresa multinacional de engenharia e infraestrutura Atkins (Londres, Reino Unido), incluem economias de operação / manutenção de £ 400.000 a £ 3,4 milhões por quilômetro durante a vida útil do sistema.
“A Cecence entregou os componentes do protótipo em maio de 2019”, diz Orange, “e nossos parceiros de desenvolvimento planejaram instalar as linhas elétricas em fevereiro de 2020, mas isso foi adiado devido ao COVID-19. Todo o sistema foi exibido no Advanced Engineering Show em 2019 e ganhou o Composites UK Innovation Award. ”
Mais aplicativos e desenvolvimento da série K_Series
Além da aplicação OHLE, a Cecence está buscando outras oportunidades para aplicar seus produtos K_Series. “A Cecence também trabalhou em projetos em que os cabos K_Rod foram usados como âncoras para a face de um penhasco de pedra em um projeto de construção na Suíça”, diz Orange. “Nossos parceiros de projeto foram perfurar furos de 80 metros de profundidade na rocha, inserir os cabos de CFRP e, em seguida, preencher com concreto. Houve alguns resultados de teste incríveis, mas o parceiro acadêmico nunca se conectou com a indústria para desenvolver o projeto além da escala de laboratório . Estamos realizando outras demonstrações, no entanto, este sistema é à prova de corrosão e fornece uma boa transferência de carga. Também pode ser aplicado como âncoras no solo para vários sistemas de construção, como edifícios à prova de furacões ”.
Vídeos no YouTube e no site da Cecence demonstram a termoformabilidade de seus produtos K_Plate. “Também houve discussões para explorar as aplicações de aerofólios de geometria variável / metamorfose com uma empresa aeroespacial do Reino Unido”, disse Orange. A Cecence demonstrou um material automotivo de baixo custo usando K_Chip feito com rebocadores compostos cortados como um material epóxi termoplástico / CF / GF híbrido, mantendo uma proporção de 2:1 de carbono para vidro, confirmada por meio de testes. . ”
A empresa também desenvolveu uma série K de alta temperatura com um T g de 250-300 ° C que processa a 360-400 ° C. “Isso foi usado por um fabricante automotivo que queria que as peças CFRP sobrevivessem ao processo de pintura E-Coat a 180 ° C”, diz Orange. “Também temos o material K-FR, que pode passar pelos requisitos de queima vertical de FST de aeronaves, liberação de calor e toxicidade de fumaça, e estamos estudando como ajudar no amortecimento de vibração para reduzir o ruído da cabine da aeronave. Podemos ajustar o termoplástico e adicionar camadas de material elastomérico para obter uma redução significativa de ruído ”.
Samantha Bunyan, a terceira fundadora da Cecence e sua chefe de engajamento da indústria, destaca que a reciclabilidade também é uma área-chave de desenvolvimento. A Cecence faz parte do consórcio ReDisCoveR Composites, operado pelo National Composites Centre (Bristol, Reino Unido). Foi criada em abril de 2019 e desenvolve 24 projetos em quatro vertentes:reciclagem, desmontagem, materiais circulares e reaproveitamento. “Dentro desses projetos, estamos analisando a desmontagem de componentes e demonstrando a real reciclabilidade dos compósitos termoplásticos”, diz Bunyan. “A indústria está finalmente sendo forçada a provar a reciclabilidade que reivindica há muitos anos. A Cecence vê os benefícios de ser capaz de reciclar produtos epóxi termoplásticos K_Series, mas também tem que demonstrar os processos e a viabilidade econômica para isso. ”
“Acreditamos que haja muito mais espaço para compostos sustentáveis no transporte de massa, incluindo interiores de aeronaves, assentos e aplicações ferroviárias”, diz Orange, acrescentando que a Cecence não é apenas uma parceira no desenvolvimento, mas também na fabricação. “Fizemos 2.500 encostos de assento compostos para aeronaves do tipo A320 até o momento e estávamos no caminho certo para produzir os encostos de assento mais leves e finos da indústria antes da eclosão do COVID-19. Sucata de assentos compostos pode ser reutilizada em apoios de pés e braços. Recyclate também pode ser usado em outras peças auxiliares que atualmente usam plásticos virgens. Tudo isso pode ajudar a reduzir o consumo de combustível fóssil e as emissões, bem como facilitar a eletrificação e aumentar a sustentabilidade ”.
Em compósitos, observa Samantha Bunyan, “a sustentabilidade é tripla:materiais, processamento (rápido e de baixo consumo de energia) e cadeia de suprimentos. Estamos interrompendo tudo isso, trabalhando com inovadores de todo o mundo que não são vistos porque a maioria das pessoas olha apenas para as grandes empresas. O mundo precisa de novas soluções que funcionem para a indústria. Isso é o que Cecence faz. ”
Resina
- Fabricação de compostos:A fabricação de materiais compostos
- Covestro Aumenta o Investimento em Compósitos Termoplásticos
- A história da resina epóxi
- Compostos termoplásticos na Oribi Composites:CW Trending, episódio 4
- Resolução de problemas de termoformação de compósitos termoplásticos
- A evolução dos compostos aditivos
- Compostos termoplásticos:Suporte de pára-choque estrutural
- Mar-Ball, Lattice Composites se fundem para estender as capacidades de epóxi
- Compostos termoplásticos:Vista panorâmica
- Compósitos termoplásticos de soldagem