Kanfit lidando com COVID-19 e gerenciando o crescimento usando sistemas Composites 4.0
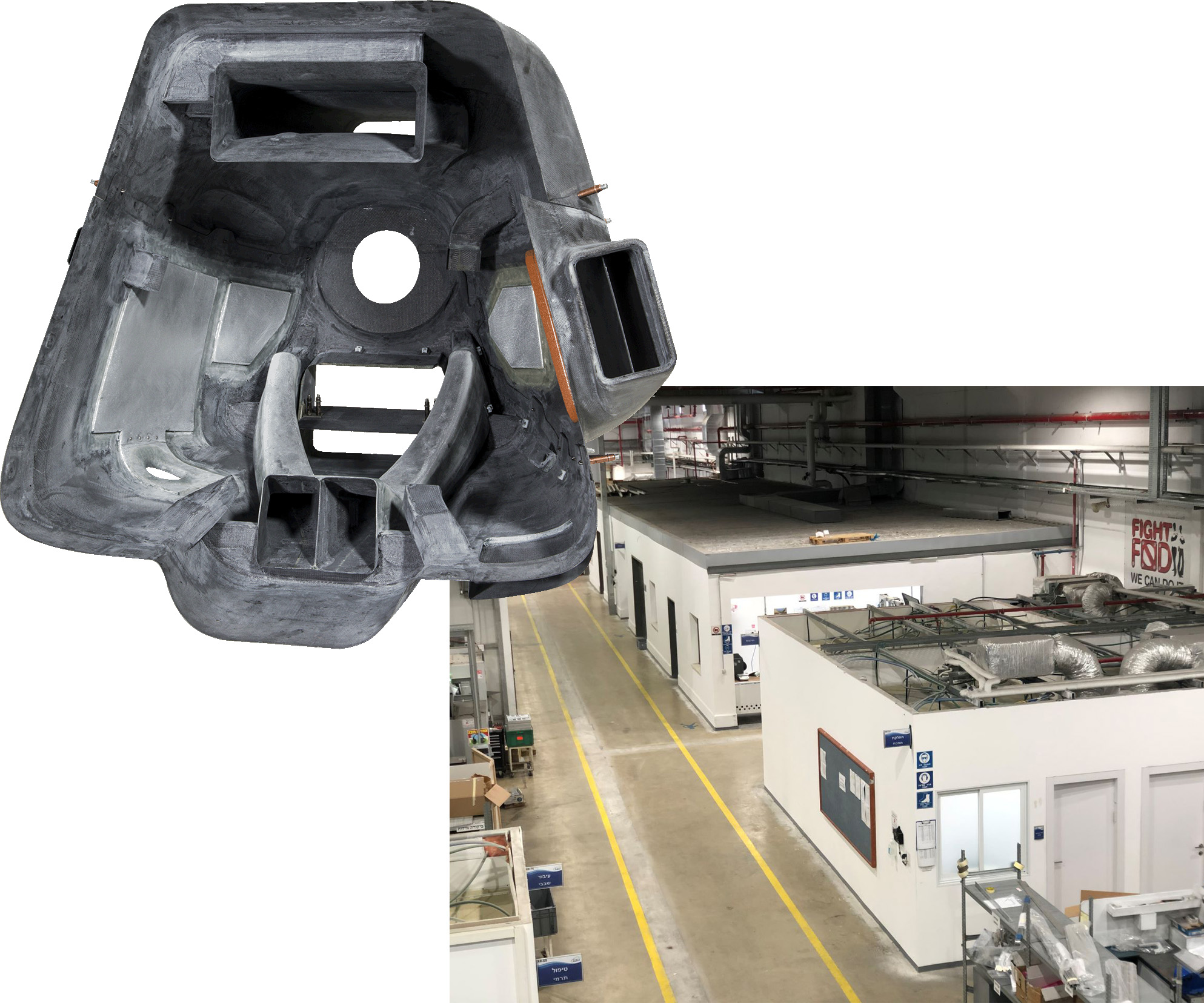
Enquanto preparava um artigo sobre digitalização da produção de compósitos para nossa edição de julho, entrevistei Shachar Fine, EVP de desenvolvimento de negócios, marketing e vendas da Kanfit Ltd. (Nof-Hagalil, Israel), um fabricante de compósitos diversificado e de alto crescimento e nível aeroespacial fornecedor. CW mencionou brevemente o uso de sensores Bluetooth da Kanfit em nossa série de visitas à fábrica de 2018 em Israel (consulte "Próspera empresa pioneira em negócios de construção aeroespacial ..."). Neste blog, explorarei esse sistema baseado em inteligência artificial (IA) com mais detalhes.
Lidando com COVID-19
Mas, primeiro, Shachar Fine e eu discutimos brevemente como Kanfit está lidando com COVID-19 e mantendo a produção de compósitos. “O governo israelense emitiu diretivas que certos negócios 'não essenciais' devem fechar (por exemplo, academias, salões de beleza, etc.)”, explica ele, “mas aqueles definidos como 'essenciais' (por exemplo, COVID-19 e suprimentos de saúde, alimentos, etc.) podem funcionar em qualquer taxa, desde que os funcionários fiquem a pelo menos dois metros de distância. A indústria de defesa pode ter até 50% de seus funcionários e o restante da indústria pode ter até 30% de sua força de trabalho, desde que essas empresas cumpram a exigência de distância. ”
“Estamos trazendo até 50% de nossos funcionários por turno e operando em dois turnos”, diz Fine. “Um terceiro turno nunca se justificou porque a produtividade era muito baixa. Mesmo agora, não faremos isso. Mas estamos estendendo algumas de nossas mudanças. Por exemplo, em departamentos como usinagem, onde os funcionários monitoram principalmente equipamentos automatizados, faremos turnos de 12 horas. Mas para departamentos onde os funcionários estão realizando mais tarefas manuais, executaremos turnos de 8 a 10 horas. ” Ele explica que isso é basicamente para ajudar a compensar a perda de produtividade devido ao necessário distanciamento social.
Fine indicou que gostaria de ouvir como outros fabricantes de compósitos estão se adaptando. “Tenho certeza de que poderia aprender com o que as fábricas de compósitos em outras partes do mundo estão fazendo. Estou em um Grupo de Desenvolvimento de Negócios no WhatsApp aqui em Israel e compartilhamos conselhos sobre como continuar o desenvolvimento de negócios quando você não pode se encontrar ou viajar. Claro, a prioridade é manter todos seguros e saudáveis. ”
Bluetooth vs. sistema RFID
Conforme explicado no artigo da turnê de 2018, o sistema que a Kanfit instalou foi fornecido por uma start-up de Tel-Aviv, Trekeye. O sistema compreende etiquetas Bluetooth (sem fio) que são anexadas ao viajante de cada peça, significando a ordem de serviço que viaja com a peça.
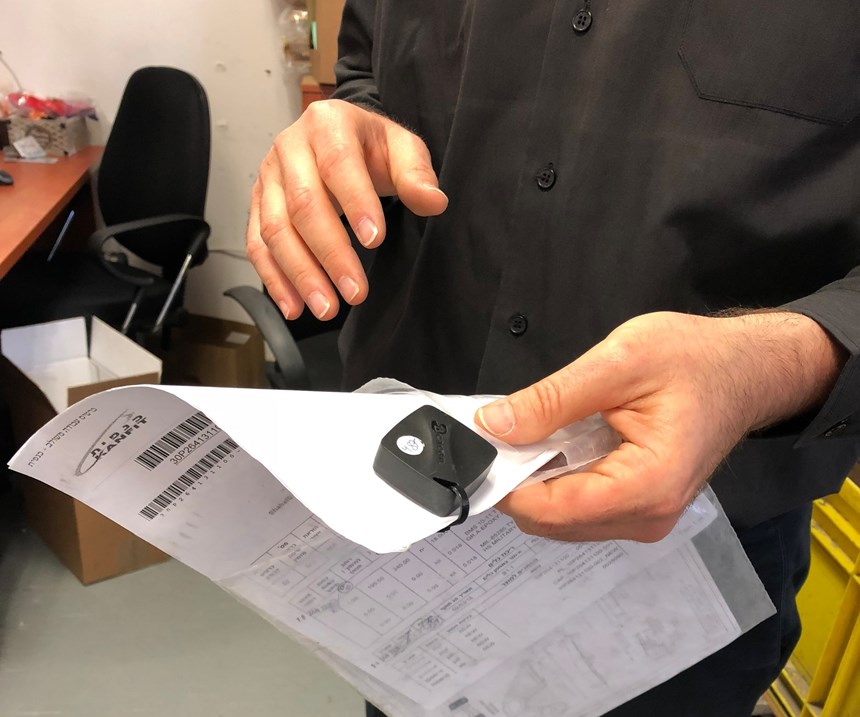
Quando a ordem de serviço para uma peça é impressa, a etiqueta é anexada a ela e então entregue para produção. Para peças compostas, as próximas etapas podem incluir corte e kits automatizados de prepregs ou reforços secos, layup, pré-formação / redução de volume, moldagem por transferência de resina (RTM) ou ensacamento a vácuo e cura em autoclave, corte, teste não destrutivo (NDT) e pintura. Normalmente, há várias inspeções entre essas etapas. A cadeia de processo também pode incluir montagem com peças de metal pequenas e grandes em módulos maiores. A produção de tais módulos, incluindo a instalação de vários sistemas (por exemplo, fiação, isolamento, energia distribuída, etc.) é uma tendência crescente para fornecedores de camada aeroespacial. Assim que a cadeia de processo estiver concluída e a peça / montagem pronta para envio, a etiqueta Bluetooth é removida e reutilizada em uma nova ordem de serviço.
Fine explica que são tags, não sensores. “Uma tag não detecta, apenas transmite um sinal”, observa ele. Nesse caso, cada uma das tags Bluetooth transmite seu número de série a cada 10 segundos. “As antenas recebem esses sinais e triangulam a posição de cada etiqueta”, diz Fine. O componente final do sistema é o software, que coleta os dados, aplica algoritmos para analisá-los e responde com alarmes e / ou ações sugeridas. As tags Bluetooth são alimentadas por bateria, mas o software alerta quando as baterias estão com pouca carga e duram mais de um ano.
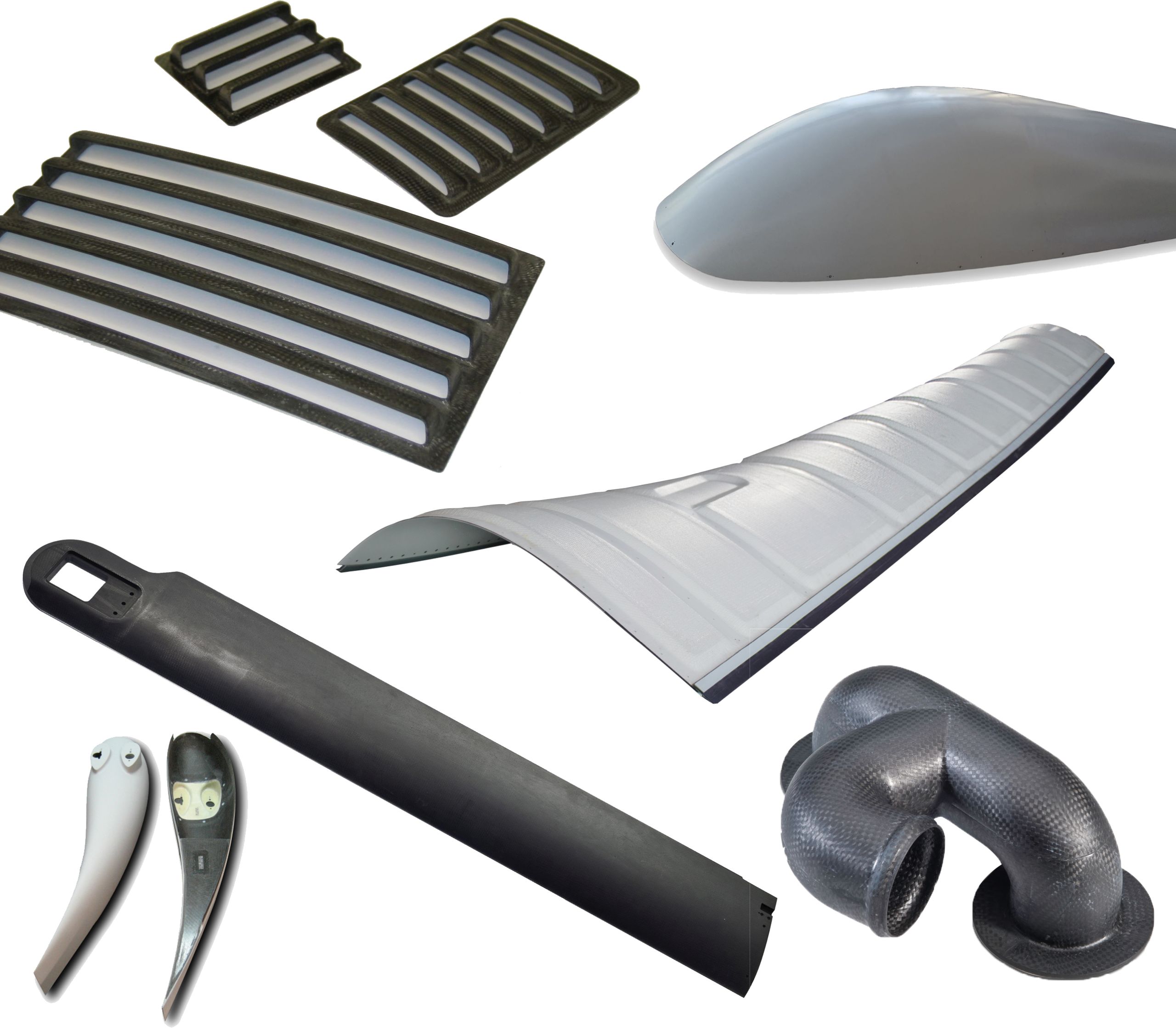
Kanfit explorou usando tags RFID, mas como eles usam radiofrequência (campos eletromagnéticos) para transmitir dados, o metal interfere no sinal. “Temos muito metal em nosso ambiente de produção”, explica Fine. “Então, você tem que pensar onde colocar as antenas RFID no prédio para que o sinal de cada tag seja sempre recebido. Se as etiquetas RFID não forem registradas periodicamente, todo o fluxo de dados está comprometido. Com nossas tags Bluetooth, comprovamos 100% de registro. Nós os juntamos com peças de metal e os colocamos perto de diferentes antenas. Todas as vezes, o sistema pegou 100% das tags. ”
Outra diferença, explica ele, é que as tags Bluetooth estão ativas, enviando um sinal, enquanto as tags RFID são tipicamente passivas - seus sinais só são captados se passarem por uma antena posicionada apropriadamente. “Com as tags Bluetooth, você posiciona as antenas onde deseja que o sistema relate as peças”, diz Fine. "Portanto, não há restrição tecnológica como com o sistema RFID. Você pode colocar as antenas em uma parede, teto ou uma estação de trabalho. Onde você as coloca e quantas você usa em uma área é uma questão de qual resolução você precisa. por exemplo, em uma área de espera, uma antena no teto é suficiente, mas em uma área com várias etapas do processo, você pode precisar de várias antenas. ”
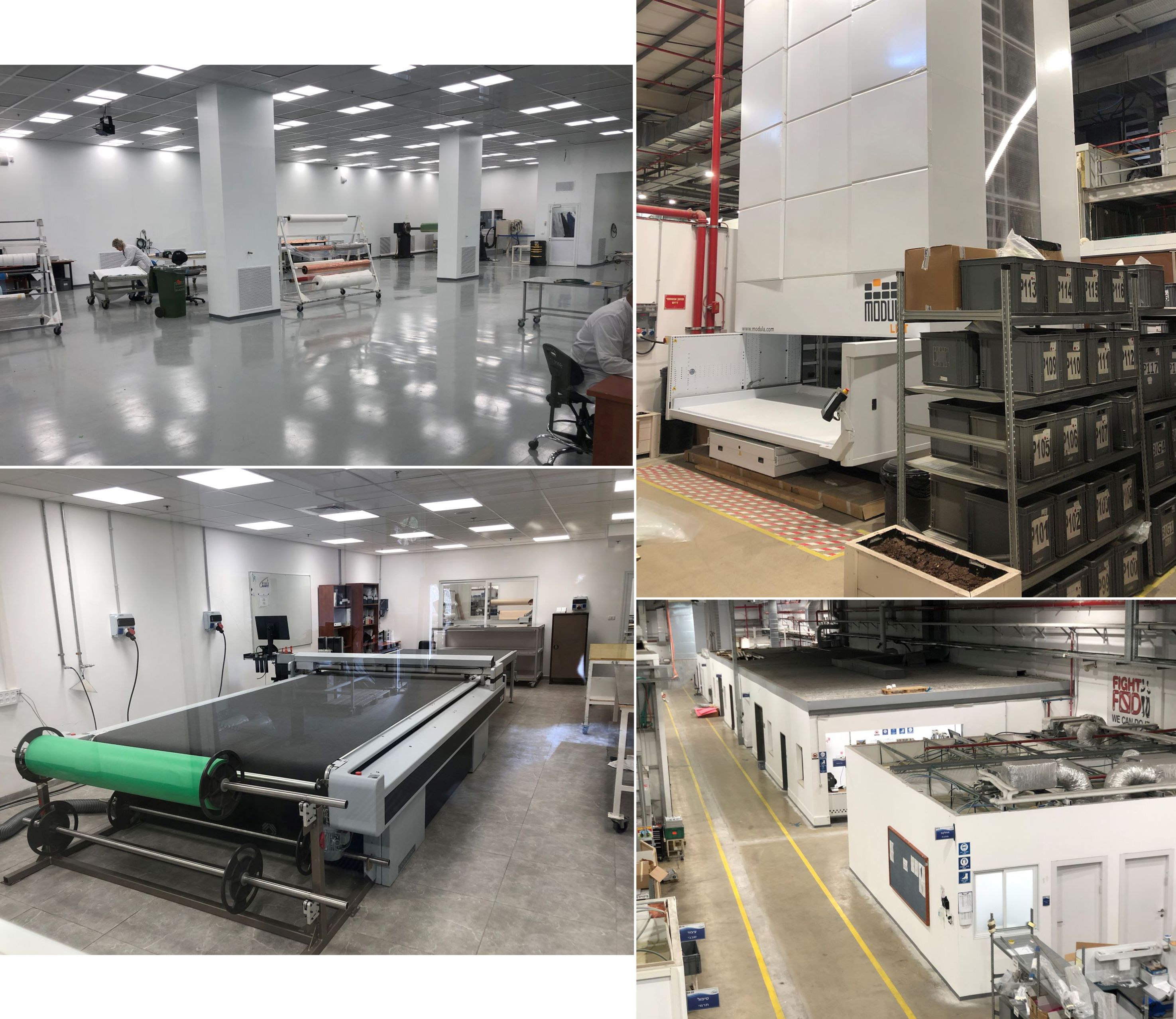
Uma desvantagem do sistema Bluetooth que a Kanfit instalou a partir do Trackeye é o custo. “Há muita infraestrutura”, diz Fine, “e essas etiquetas Bluetooth custam dólares, não centavos como as etiquetas RFID”. Houve também um desenvolvimento significativo exigindo que os desenvolvedores do Trekeye estivessem no local. “Eles nos ajudaram a localizar as antenas para que as informações coletadas fossem otimizadas para o que estávamos tentando alcançar”, explica ele. “Eles nos ensinaram como resolver problemas com áreas de sobreposição de antenas para que o sistema não seja confundido por uma etiqueta sendo lida por duas antenas na mesma intensidade. Foi um processo. ”
Mapas de peças e gráficos espaguete
Depois que o sistema foi instalado e funcionando, os resultados retornados incluíram mapas de peças e gráficos espaguete. “Nosso departamento de TI tinha o mapa online aberto para o sistema o tempo todo”, explica Fine. “Quando um trabalhador estava procurando uma peça, ele foi ao TI, localizou rapidamente a peça e foi retirá-la na fábrica. Foi muito fácil ver onde todas as partes estavam. ”
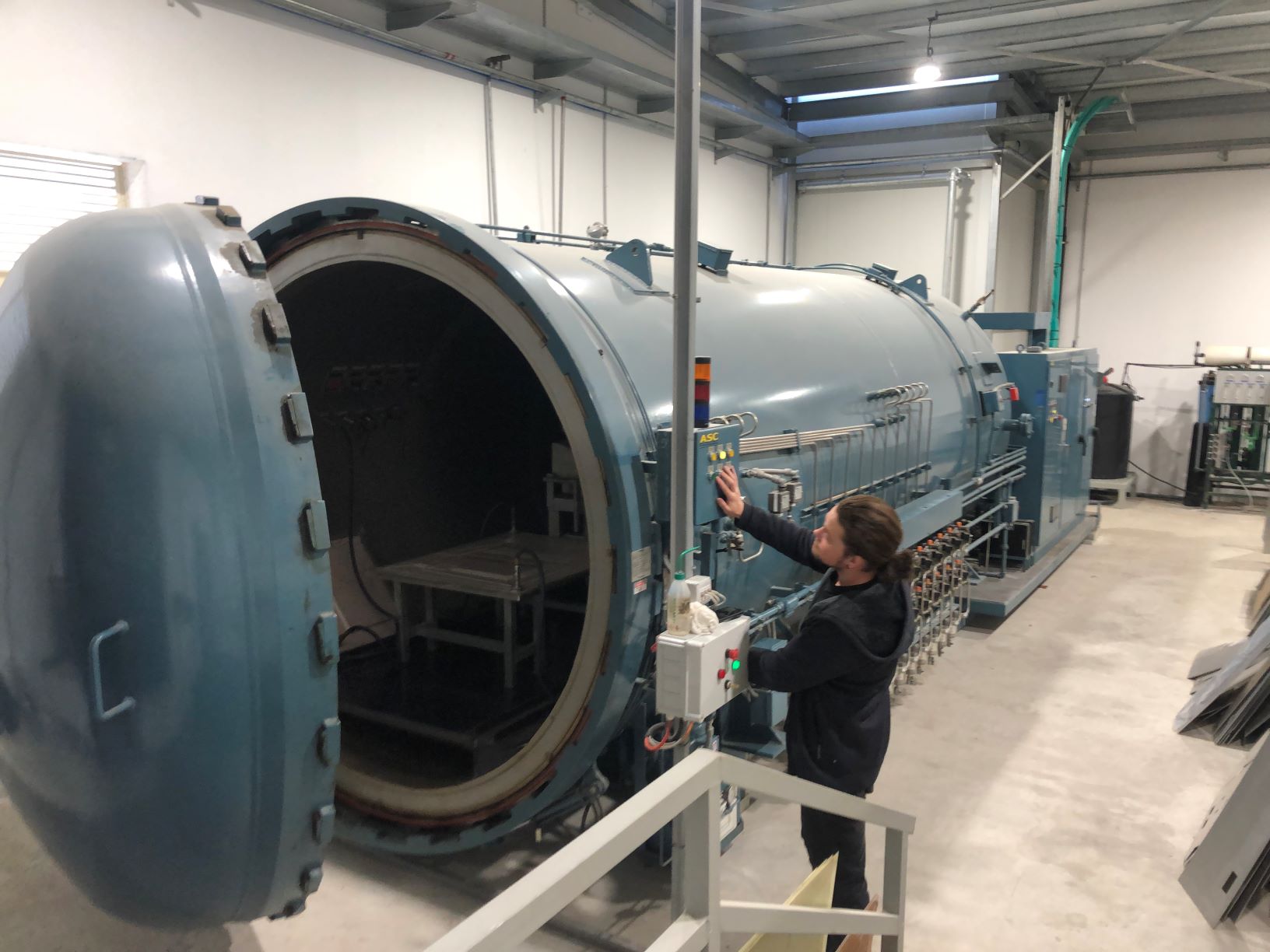
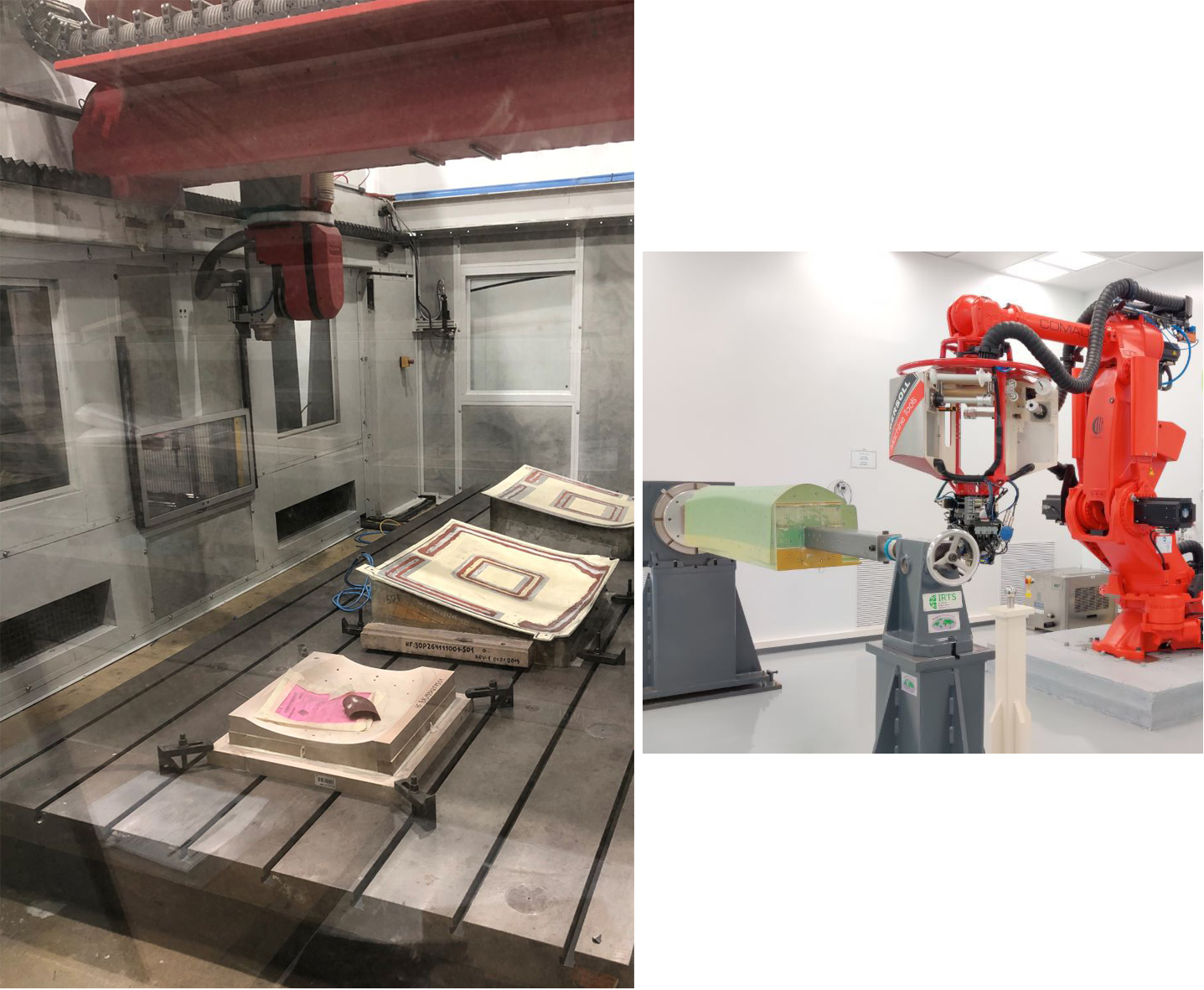
Ele explica que a Kanfit tem milhares de peças em todo o chão de fábrica (3.000 ordens de serviço abertas a cada minuto), “e não é uma linha de montagem padronizada. A combinação de partes que estão sendo feitas muda e algumas partes requerem etapas diferentes das outras. Por exemplo, nem todas as peças são autoclavadas ou usinadas. Quando você vê uma peça, nem sempre sabe se ela está no lugar certo. Você precisa verificar a papelada da peça para entender que ”
O sistema Trekeye, entretanto, funcionou incrivelmente bem. “Mesmo não sendo um sistema barato, o ROI (retorno sobre o investimento) era muito curto”, diz Fine. “O sistema tem uma IA muito avançada. Não esperou até que faltasse uma peça. Ele enviaria um SMS (mensagem de texto) para o gerente informando que a parte do “ABC” foi para a estação errada. Não houve espera. O sistema alertaria quando uma peça não seguisse sua rota normal. ”
Essas rotas ou caminhos parciais são mostrados nos chamados gráficos espaguete. “Eles mostram os caminhos das peças através de nossa fábrica e cadeias de processo”, diz Fine. “Estávamos começando a ver tendências. Por exemplo, conforme os engenheiros criavam as ordens de serviço para as peças, eles colocavam as etapas de inspeção de acordo com seu conhecimento e experiência. As peças iriam primeiro para a inspeção antes de passar para a próxima estação. Os gráficos espaguete mostram que você pode alterar algumas ações e reduzir a distância que as peças estão viajando. Veríamos uma parte indo e voltando entre os departamentos para várias ações. Então, sentávamos com a engenharia e perguntávamos por que ela está indo e voltando? Como poderíamos reduzir quatro vezes para duas vezes, por exemplo? Isso é fácil de ver no gráfico, mas difícil de ver nas operações reais do dia-a-dia na fábrica, e também qual é o efeito real disso e para trás na produção geral. Você pode ver as etapas como itens de linha à medida que as escreve na ordem de serviço, mas ver os caminhos no gráfico espaguete envolve mais dados e uma visualização desses dados que tem um impacto real ”.
“Isso também nos ajudou, pois nos mudamos para nossas novas e maiores instalações”, acrescenta Fine. “Uma das lições que aprendemos é localizar centralmente o departamento de inspeção dentro da área de produção. Portanto, com o tempo, tenho certeza de que a IA continuaria a nos ajudar a localizar melhor as máquinas e estações, e até mesmo à medida que nossas peças e operações mudam com o tempo. Ele também pode rastrear ferramentas. ”
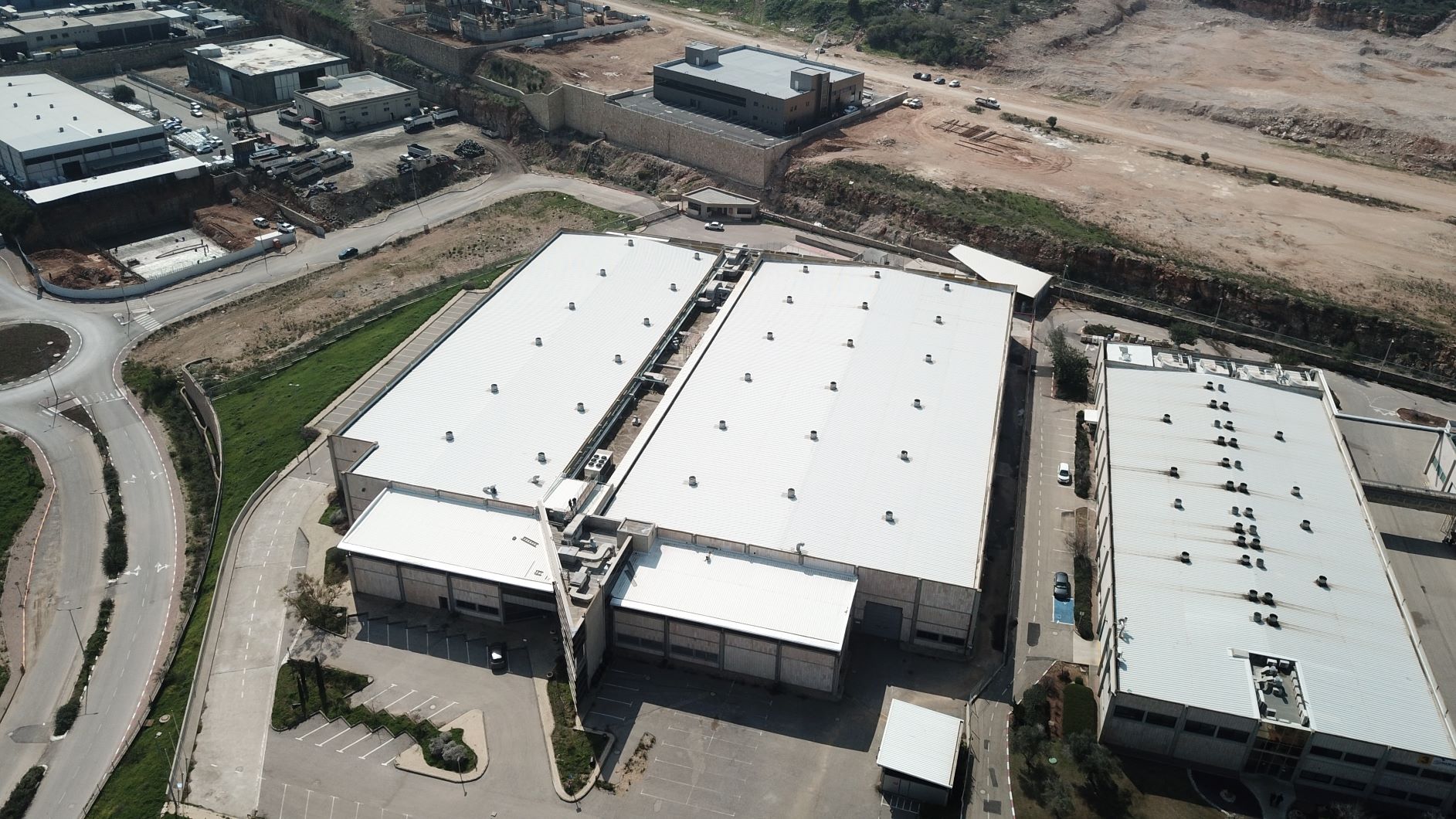
Outro benefício é que o Kanfit pode rastrear quanto tempo uma peça passa em cada estação. “Embora ainda não tenhamos implementado isso, pode reduzir o tempo que os funcionários gastam inserindo esses dados”, observa Fine. “Ainda temos um sistema ERP ao qual os funcionários se reportam, mas o sistema de tag Bluetooth deu mais detalhes de quando uma peça entrou e saiu de uma estação, etc.”
Fine observa que esses sistemas de monitoramento de peças e ferramentas não substituem o ERP, mas devem ser integrados para funcionar com ele. “Continuamos desenvolvendo nosso sistema ERP internamente porque temos grandes clientes e cada um deles tem suas próprias necessidades. Portanto, temos que desenvolver muito em nosso sistema, a fim de fornecer todas as informações que cada cliente deseja. ” Mas ele vê o poder da tecnologia Bluetooth tag / AI para melhorar esses sistemas e a vantagem em maior eficiência que isso oferece.
Sem entrada de dados
Você teve que inserir muitos dados para cada peça ao criar a ordem de serviço e anexar o sensor? “Não, essa é a parte mais incrível”, diz Fine. “Não houve entrada de dados. É o sistema de IA. Tudo o que recebeu foram os números das ordens de serviço. Estes incluem letras e números, mas há uma espécie de lógica na maneira como os criamos e o que significam. A IA deve ter aprendido isso. Assim que começou a coletar dados, aprendeu onde as partes deveriam estar. Por exemplo, todas as ordens de serviço “ABC” eram apenas de metal e nunca deveriam ir para o departamento de compósitos. Então, quando uma peça de metal foi para o departamento de compósitos por engano, o sistema deu um alarme. Até os designers de IA ficaram surpresos com a rapidez com que o sistema aprendeu. Inicialmente testamos 100 peças. Aprendeu neste primeiro lote. ”
Fine explica que é para isso que o sistema foi projetado. Trekeye começou em hospitais, trabalhando com uma empresa de manutenção de dispositivos médicos móveis que ajudava a manter medidores de pressão arterial, termômetros, monitores, etc. Essa empresa reclamou que eles gastavam 80% do tempo do técnico de manutenção apenas procurando os dispositivos que precisavam de manutenção. “Com esse sistema instalado, o técnico entrava, se conectava ao sistema e ver exatamente onde todos os dispositivos estavam no hospital”, diz Fine. “Um benefício adicional foi que o roubo diminuiu. Sempre que alguém saía com um dispositivo, o sistema soava um alarme e um oficial de segurança era enviado para recuperar o dispositivo. ”
Implementação futura
Infelizmente, Trekeye não passou do estágio crítico do “Vale da Morte” como uma startup e não está mais operando. “Temos tudo de que precisamos para manter o sistema funcionando, exceto alguém para supervisioná-lo”, diz Fine. “Para este tipo de sistema, você não pode ter apenas um profissional de TI geral. Você precisa de alguém muito proficiente em IA. Também acabamos de mudar para nossas novas instalações e ainda não reiniciámos o sistema. ” Ele procurou outra empresa fazendo algo semelhante, mas diz que ainda não encontrou nada que atenda às necessidades de Kanfit. “Encontraremos uma maneira de colocá-lo novamente em operação em breve”, acrescenta.
Então, qual é o benefício real? “Em primeiro lugar, tudo o que você não pode medir, você não pode gerenciar”, diz Fine. “Em segundo lugar, a quantidade de dados que temos é tão grande, mesmo para nós como uma pequena fábrica, que passamos do ponto de ter uma ou mais pessoas capazes de lidar com todos esses dados. Eu nem consigo imaginar o que isso deve ser para Boeing ou Airbus. Precisamos que as máquinas conversem entre si agora. Deixe-os fazer o que são bons e deixe que nós, humanos, vejamos o quadro geral e desenvolvamos novas soluções com base no que eles podem nos mostrar. ”
Fique ligado em mais blogs sobre Composites 4.0 e CW Artigo de destaque de julho.
Resina
- Como projetar sistemas industriais de IoT com DDS e LabVIEW 2017
- Calor e rolamentos:Lidando com a expansão do eixo
- Fabricação de aditivos com compostos na indústria aeroespacial e defesa
- Braskem faz parceria com universidade para produção de plástico sustentável usando captura e uso de CO2
- Os sistemas ERP e MES podem acompanhar a IIoT?
- Lidando com a Black Friday 2020 - e a ‘Crazy Thursday’ dos fabricantes
- TxV Aero Composites está em conformidade com os padrões AS9100
- Compostos Um e IACMI para sediar workshop de dois dias
- Compósitos para impressão 3D com fibra contínua
- Emparelhamento de IA e robótica com vários sistemas de inspeção