O projeto PASSARO da Clean Sky 2 tem como alvo o cockpit composto OOA one-shot
O projeto PASSARO (caPAbilities para testes estruturais e funcionais inovadores de AeROstructures) visa desenvolver novos materiais multifuncionais - integrando isolamento acústico e alta resistência ao impacto de energia - e soluções de inspeção para novos cockpit compostos fabricados de uma só vez e complementados com out of autoclave (OOA) tecnologias como consolidação in-situ de compósitos termoplásticos e infusão de resina líquida. Este cockpit composto foi desenvolvido pela Airbus Defense and Space (Madrid, Espanha) durante o Clean Sky 1, baseado na aeronave C295. O projeto também visa a automatização dos processos de manufatura, bem como novas abordagens de testes baseadas nos conceitos da Indústria 4.0 e desenvolvimento de conceitos ergonômicos avançados que promovam o conforto do piloto e a melhoria da interface homem-máquina.
O projeto PASSARO, parte da plataforma Airframe da Clean Sky 2, teve início em julho de 2016 com uma duração total de 48 meses. É composta por onze parceiros de Portugal e Espanha que trabalham em estreita colaboração com a Airbus Defense and Space.
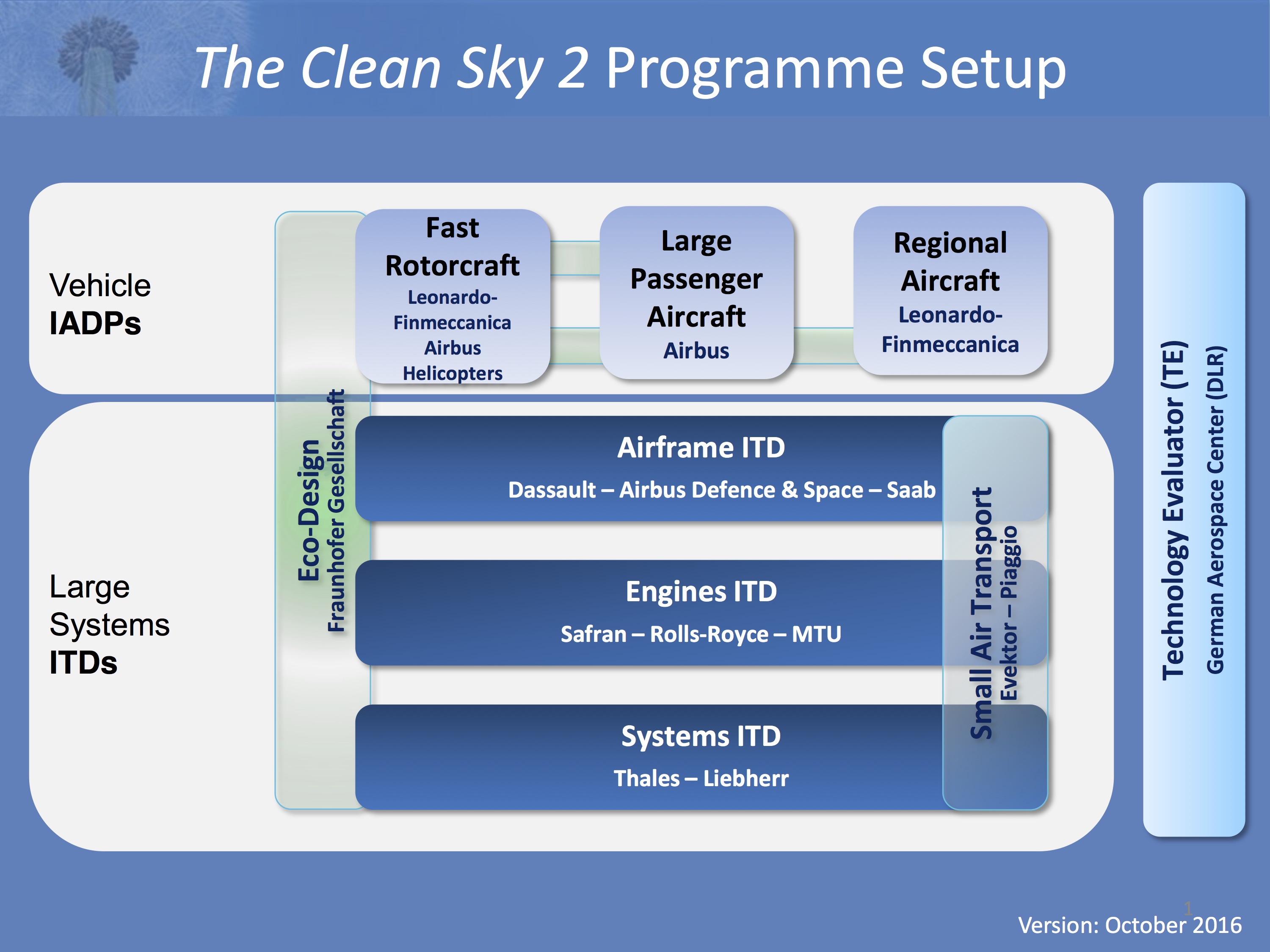
FONTE:Clean Sky 2
Sinergias com o projeto MOSHO regional de Portugal
Muitos projetos Clean Sky 2 (CS2) compartilham sinergias com iniciativas regionais de membros da UE (por exemplo, CORAC na França). O projeto PASSARO tem promovido atividades complementares com iniciativas nacionais de I&D portuguesas. O projeto MOSHO (Soluções avançadas para materiais de impacto, reparo de aeroestruturas compostas e seu monitoramento) complementa as atividades da PASSARO nas quais alguns dos parceiros estão envolvidos e é apoiado pela ADS (Airbus Defence and Space) como coordenador do Clean Sky 2 para o Airframe ITD. O projeto irá desenvolver e integrar soluções avançadas para o reparo de aeroestruturas compostas.
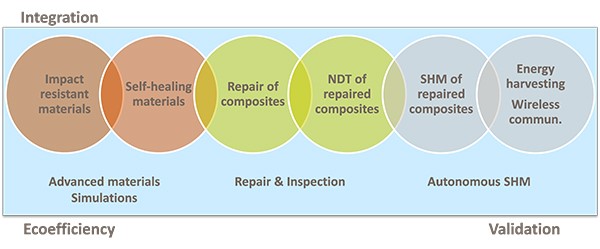
Figura 3:Escopo técnico do projeto MOSHO FONTE: https://www.cleansky.eu/commissioner-moedas-meets-passaro-at-isq
Os robôs colaborativos PASSARO reduzem o tempo do ciclo de lay-ups em até 70%
Como parte dos objetivos do projeto PASSARO de pesquisar e desenvolver como empregar robôs colaborativos na fabricação de compósitos, o projeto OPTIMAL desenvolveu uma solução automatizada prática e econômica para substituir o lay-up manual tradicional, usando materiais qualificados.
Tradicionalmente, a fabricação de componentes compostos usando prepreg é essencialmente uma atividade artesanal, mas algumas etapas estão sendo tomadas em direção à automação. Durante a última década, várias soluções automatizadas de lay-up surgiram para peças de geometria relativamente simples. Essas soluções costumam ser bastante caras e geralmente exigem que as fábricas sejam projetadas do zero para sua instalação. Eles normalmente requerem ambientes especiais na forma de células isoladas com sistemas de segurança dedicados. Como alternativa, robôs colaborativos (cobots) podem ser integrados aos fluxos de trabalho de manufatura existentes para automatizar algumas tarefas e melhorar a produtividade sem alterar drasticamente o ambiente circundante.
Os robôs industriais são rápidos, fortes e possuem excepcional precisão e repetibilidade, mas são desenvolvidos visando apenas a otimização do resultado final. Em comparação, os cobots são mais lentos, menos precisos e lidam com cargas úteis menores, mas têm o que é necessário para automatizar tarefas simples, especialmente ao lado de humanos, a um custo consideravelmente menor. Os Cobots possuem sensores de carga que detectam os menores impactos e param com segurança.
O objetivo da OPTIMAL ao desenvolver tecnologias cobot é melhorar a sua própria capacidade, e a de outras empresas, de oferecer produtos com maior repetibilidade e qualidade em grandes quantidades e a preços mais baixos.
Dentro do Pacote de Trabalho 10 do projeto PASSARO, três etapas principais foram desenvolvidas usando robôs colaborativos:
- Coleta e separação de lonas, diretamente do cortador automático de lonas;
- Ply peeling usando uma célula dedicada;
- Posicionamento e empilhamento de lonas em uma ferramenta.
Para implementar essas atividades, foi desenvolvida uma célula que recebe camadas de prepreg do cortador de camadas e as descasca e empilha automaticamente em um molde.
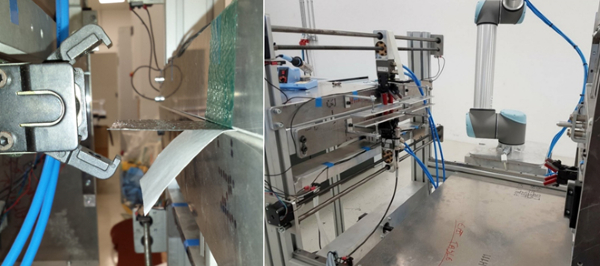
Robôs colaborativos usados para fabricação de compostos no projeto PASSARO. FONTE: Grupo ISQ
As tarefas de posicionamento e empilhamento são concluídas pelo braço do robô usando ventosas especiais para o manuseio do pré-impregnado. O descascador é uma máquina mais complexa, que utiliza ar comprimido para descascar o pré-impregnado, que é protegido por dois revestimentos - normalmente um de plástico e um de papel, ou simplesmente por dois plásticos. O conceito de peeling é baseado no fato de que diferentes materiais tendem a vibrar em diferentes frequências quando o mesmo estímulo é aplicado. As diferentes frequências de vibração produzem bolsas de ar entre o pré-impregnado e as camadas de cobertura. O ressonador de placa ajusta a amplitude de vibração para diferentes materiais. Este protótipo pode atingir taxas de descascamento com quase 100% de sucesso para materiais específicos e uma precisão de empilhamento de ± 0,5 mm, em cada um dos dois graus de liberdade no plano do molde, e ± 0,1º na rotação.
A abordagem modular adotada para este sistema o torna independente das dimensões das camadas. A largura é coberta pela adição de mais módulos de descascamento paralelos e o comprimento pelo ajuste da faixa de abertura do descascador. Essa tecnologia, quando comparada com um operador humano, oferece uma clara melhoria na precisão do processo, repetibilidade e principalmente no tempo de ciclo, com reduções de até 70%.
Autores:António Reis, Nicole Cruz, Marco Neves (OPTIMAL) e Rúben Buelga Sanchez (ADS). Para mais informações entre em contato:
INEGI
Campus da FEUP
Rua Dr. Roberto Frias, 400
4200-465, Porto, Portugal
Tel:(+351) 229 578 710
Email:[email protected]
Resina
- Solvay Expande a Capacidade do Composto Termoplástico
- Toray no Projeto Holandês para Tanques de Hidrogênio Líquido para Aeronaves
- O projeto Clean Sky 2 FUSINBUL desenvolve anteparas de pressão de fibra de carbono em escala real
- A importância da seleção de resina
- O projeto Clean Sky 2 FRAMES avança simulação de aquecimento de composto termoplástico AFP com lâmpada de xenon
- Clean Sky 2 lança resultados do projeto
- A especialista alemã em compostos INVENT colabora com a SUSTAINair para aumentar a circularidade da aeronave
- Costelas da Asa do Amanhã:One-shot, termoplástico, consolidação OOA
- Consórcio visa soluções para estruturas compostas termoplásticas de fibra de carbono
- Fabricação rápida de blanks compostos personalizados