O projeto Clean Sky 2 FRAMES avança simulação de aquecimento de composto termoplástico AFP com lâmpada de xenon
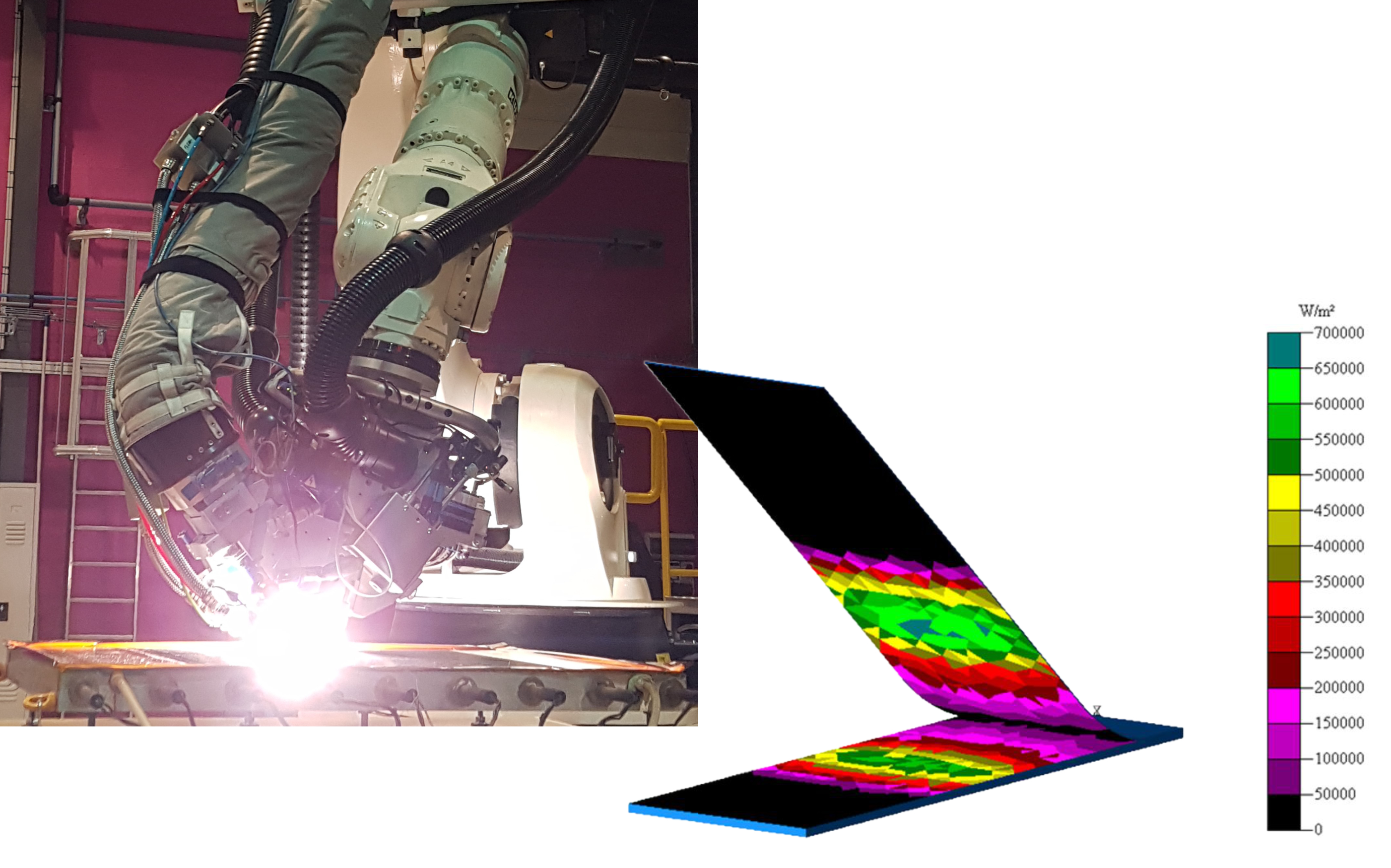
O objetivo principal do projeto Clean Sky 2 (CS2) FRAMES, que começou em julho de 2020, é validar uma abordagem de manufatura que está sendo usada para produzir o Demonstrador traseiro avançado fabricado pelo Centro Aeroespacial Alemão (DLR) como parte da tecnologia CS2 plataforma para grandes aeronaves de passageiros (LPA). Este demonstrador tem como objetivo trazer soluções confiáveis e competitivas para simulação de aquecimento durante a colocação automatizada de fibra (AFP) para alcançar alta taxa de fabricação de reforços termoplásticos e ferramentas autoaquecidas para apoiar a co-consolidação de um conjunto de reforço de pele.
Para obter mais contexto de como o FRAMES se encaixa nos objetivos do projeto Demonstrador traseiro avançado, consulte a última seção deste artigo.
Modelagem térmica óptica do aquecimento da lâmpada de xenônio sistema
AFP de compósitos termoplásticos reforçados com fibra de carbono (CFRTP) depende principalmente do aquecimento a laser para atingir as altas temperaturas necessárias para o processamento de materiais de matriz termoplástica de alto desempenho, como PEEK (poliéteretercetona), PEKK (polietercetonecetona) e LM-PAEK (baixo ponto de fusão poliariletercetona). No entanto, surgiu uma nova tecnologia baseada em uma lâmpada de xenônio pulsante. Neste método, pulsos de alta energia e curta duração fornecidos por uma poderosa fonte de calor de banda larga são coletados e fornecidos por um guia de luz de quartzo. Posicionado próximo ao ponto de aperto da cabeça AFP, o guia de luz de quartzo molda e posiciona a energia da luz para aquecer o substrato e os cabos de entrada antes que a consolidação seja alcançada sob um rolo de compactação. Este sistema de flashlamp de xenônio foi mostrado para corresponder ao rápido tempo de resposta de um laser e atingir as temperaturas necessárias para processar compostos termoplásticos.
Durante o processamento AFP, o pulso da lâmpada de xenônio deve ser controlado para levar em conta as mudanças na velocidade e geometria e manter uma temperatura alvo. Isso é obtido variando a energia do pulso da lâmpada, a duração e a frequência. Para otimizar esses parâmetros, um modelo de simulação opto-térmica foi criado que usa técnicas de rastreamento de raios ópticos (calculando o ângulo de refração / reflexão em cada superfície) para caracterizar a fonte da lâmpada, bem como a análise de elemento finito (FEA) para prever o temperatura de processamento resultante. Usando essas ferramentas de simulação, a tentativa e erro pode ser evitada; os parâmetros de pulso podem ser escolhidos para atingir uma temperatura de processamento desejada sem os testes físicos caros e demorados.
A Heraeus Noblelight (Cambridge, Reino Unido) está liderando o desenvolvimento do modelo térmico óptico aplicado ao seu sistema de lâmpada de flash Humm3. O processo para criar uma simulação confiável envolve a caracterização óptica da fonte da lâmpada de xenônio usando medições goniométricas (rotação em torno de um eixo) e medições de irradiância espectral (energia de luz recebida pela superfície) que são então usadas para determinar os níveis de energia espectral, distribuição espacial e eficiência de energia elétrica para radiativa da fonte.
Medindo energia espectral
A Fig. 1 abaixo mostra a configuração experimental concebida para determinar a emissão de energia de uma lâmpada de xenônio em relação ao comprimento de onda usando medições de irradiância espectral. Neste sistema, a luz da lâmpada de xenônio vai para um detector a uma distância predefinida (normalmente 0,5 a 1 metro, à esquerda abaixo). Essa luz é então transportada por meio de um cabo óptico para um sistema de monocromador duplo (no canto inferior esquerdo abaixo) que determina a intensidade da luz em um comprimento de onda específico. Isso resulta em um gráfico de irradiância espectral detalhado da fonte de luz - neste caso, toda a curva de emissão da energia de luz de xenônio da lâmpada Humm3 é medida (Fig. 2).
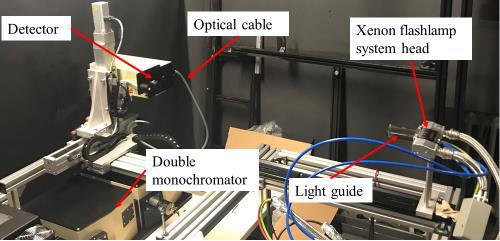
Fig. 1. Configuração de teste de monocromador duplo usada para medições de irradiância espectral. A luz da lâmpada de xenônio (canto superior direito) vai para um detector (canto superior esquerdo) que a transporta por meio de um cabo óptico para um monocromador duplo que mede a intensidade da luz em um comprimento de onda específico. Isso permite um gráfico detalhado em todo o espectro da energia de luz emitida pela lâmpada do flash. Crédito da foto:Heraeus Noblelight
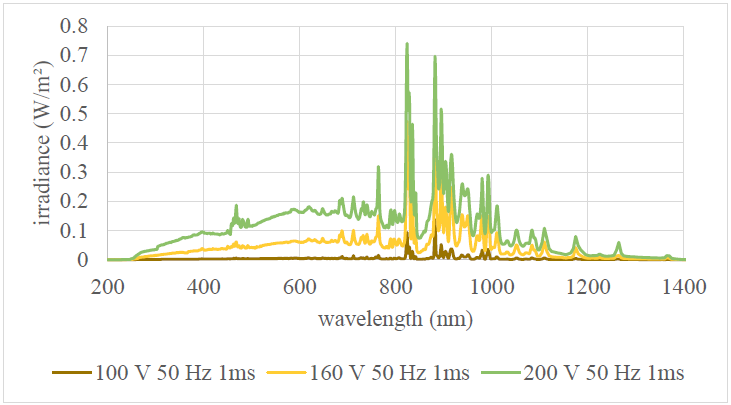
Fig. 2. Medições de irradiância espectral da luz que sai da lâmpada de xenônio Humm3. Crédito da foto:Heraeus Noblelight
Medindo a eficiência energética
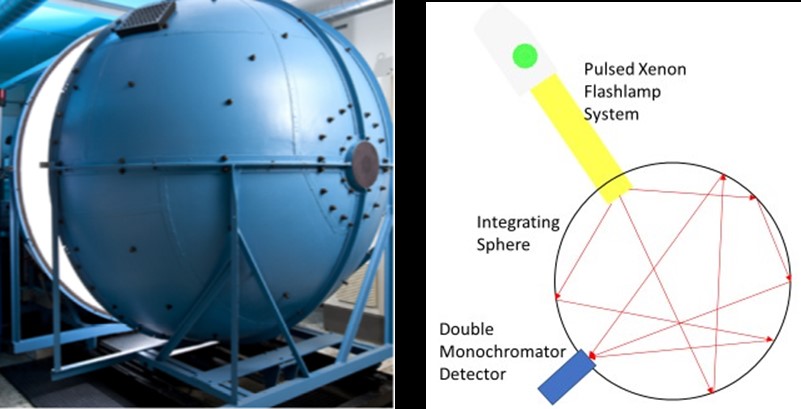
Fig. 3. Esquema da esfera de integração usada para medições de energia radiante espectral. Crédito da foto:Heraeus Noblelight
A eficiência do sistema também foi avaliada usando uma esfera de integração (Fig. 3) no laboratório Heraeus em Hanau, Alemanha, para determinar com precisão a energia espectral que sai do guia de luz Humm3 em diferentes níveis de voltagem. A esfera apresenta uma superfície difusa altamente reflexiva que direciona virtualmente toda a energia óptica que sai da cabeça da lâmpada para um detector de monocromador duplo. Ao modular a energia do pulso para uma determinada duração e frequência de pulso, a potência óptica média que sai da cabeça do Humm3 é medida como uma função do comprimento de onda para uma faixa de voltagens da lâmpada.
Analisando a distribuição angular de energia
A posição da cabeça da lanterna em relação ao ponto de aperto da cabeça AFP também é um aspecto crítico para obter uma disposição de compostos de alta qualidade. Paralelamente às medições da potência de saída, foi medida a variação na intensidade da luz da lâmpada de xenônio em relação ao seu ângulo em relação à fonte. Todas as medições foram normalizadas para investigar a distribuição angular de energia, em vez de saída de potência absoluta neste ponto. Esses resultados foram usados para validar uma simulação de traçado de raio da lamparina para prever como a energia dos pulsos da lamparina é distribuída entre o substrato, o ponto de contato e os reboques de chegada.
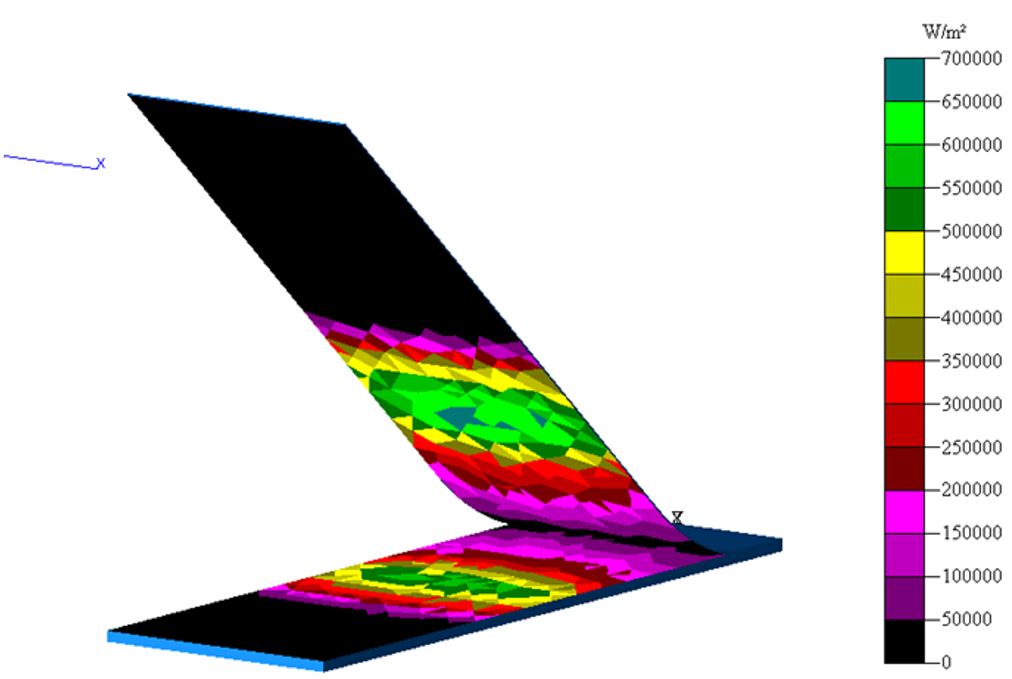
A análise de traçado de raio óptico (Fig. 4) - obtida usando o software TracePro (Lambda Research Corp., Littleton, Mass., U.S.) - é então detalhada para calcular perfis de irradiância de superfície na estopa composta e substrato. Esses perfis de irradiância são usados como condições de contorno de entrada para a simulação térmica. O comportamento óptico e térmico de fitas LM-PAEK reforçadas com fibra de carbono também foi caracterizado para alimentar o modelo nas temperaturas de processamento relevantes.
Validação por meio de testes físicos
Como uma etapa de validação, testes físicos de AFP foram realizados em Compositadour (Bayonne, França) para mostrar a capacidade da simulação de prever os valores de temperatura vistos durante a colocação real de AFP. Termografia infravermelha e termopares finos embutidos dentro de layups compostos foram usados para medir as temperaturas de processamento durante os testes AFP. As medições parecem mostrar concordância razoável com os perfis de temperatura previstos na região para fechar o ponto de estreitamento e também através da espessura.
Essas medições, no entanto, também destacam a influência do ferramental no gerenciamento térmico das primeiras camadas. No início do layup, as primeiras camadas estão muito próximas da superfície da ferramenta, o que pode atuar como dissipador de calor. Por esta razão, ferramentas aquecidas foram usadas. A temperatura da ferramenta tem uma forte influência na temperatura do ponto de contato AFP.
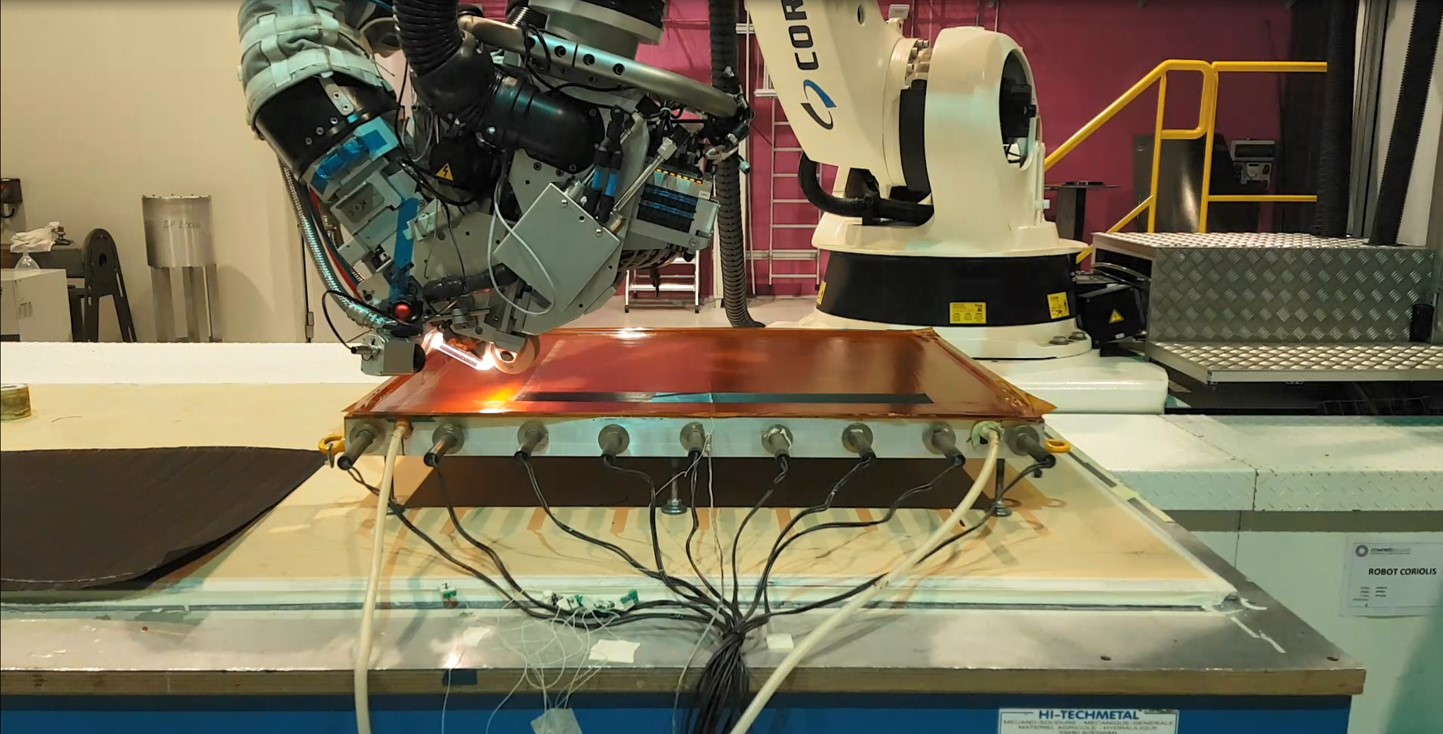
Durante esta fase inicial de layup, os parâmetros de pulso para a lâmpada de xenônio precisam ser ajustados para manter a temperatura do ponto de aperto constante. Mas, uma vez que algumas camadas são colocadas, a disposição começa a se tornar uma espécie de camada isolante e a influência da temperatura da ferramenta diminui. Neste ponto do processo, não há necessidade de mais ajustes de parâmetros de pulso.
Durante os testes de validação do projeto FRAMES, ferramentas aquecidas foram usadas para avaliar diferentes temperaturas de processamento durante o AFP, explica Guillaume Fourage, engenheiro-chefe para projetos de compósitos na Compositadour. “A abordagem de fabricação para o demonstrador traseiro avançado ainda não está congelada e estamos avaliando diferentes opções para o layup da pele com o objetivo de encontrar o equilíbrio certo entre o tempo de processo, consumo de energia e qualidade do layup. Alterar a temperatura da superfície da ferramenta exige que ajustemos os parâmetros de pulso de acordo para atingir a temperatura de ponto de aperto adequada. Isso faz parte do plano de desenvolvimento do modelo térmico óptico e nos ajuda a aumentar a confiabilidade e a robustez da simulação em diferentes condições de layup. ”
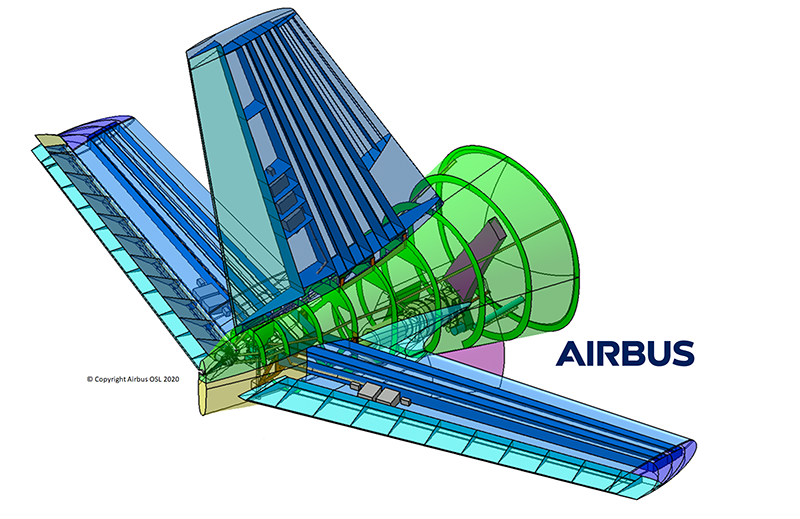
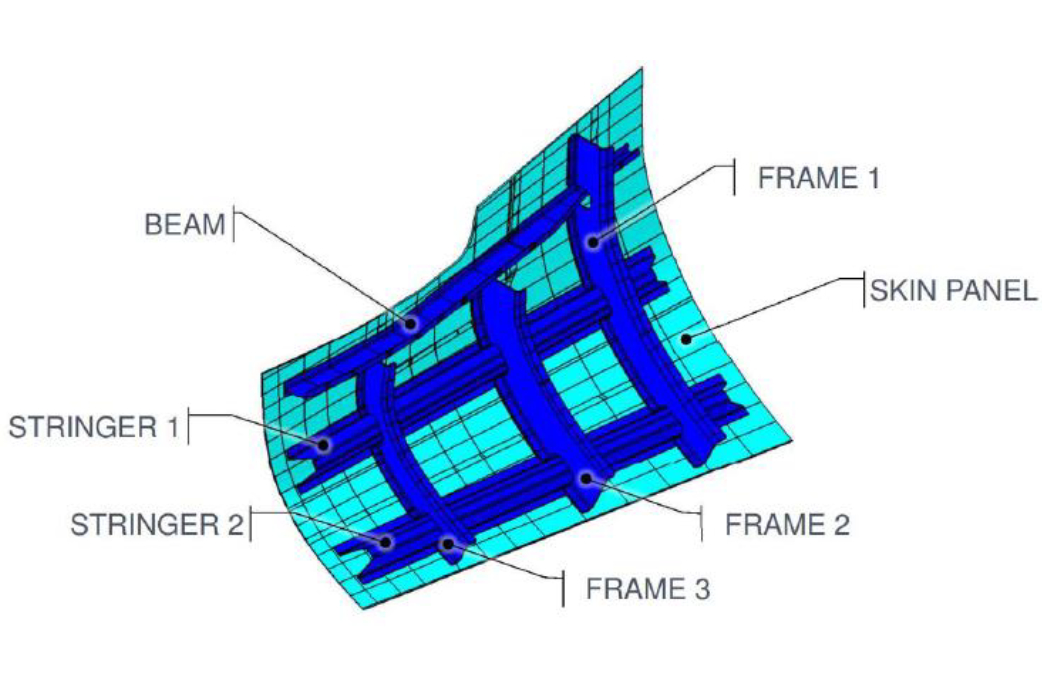
Demonstrador de extremidade traseira avançada (ARE) de composto termoplástico para Clean Sky 2. Foto: (topo) Airbus, (inferior) ESTIA-Compositadour
Este modelo de simulação está agora sendo adaptado para o sistema de aquecimento final e configuração de ferramentas que serão usados para fabricar o demonstrador de extremidade traseira avançada (ARE) composto termoplástico CS2. As peças estão sendo fabricadas em 2021 para montagem em 2022 com a meta de atingir o TRL 6 até o final do projeto em 2023. Paralelamente, um nível de prontidão de fabricação (MRL) de 5/6 está sendo perseguido, não apenas para o demonstrador ARE , mas também para os processos de fabricação e ferramentas associados que estão sendo desenvolvidos. As metas gerais do projeto demonstrador ARE incluem:Reduzir custos em até 20%, peso do componente em até 20% e queima de combustível em até 1,5%, bem como melhorar a aerodinâmica em linha com os objetivos ambientais da Clean Sky.
Este projeto recebeu financiamento da Empresa Comum Clean Sky 2 (JU) ao abrigo do acordo de subvenção n.º 886549. A Empresa Comum recebe apoio do programa de investigação e inovação Horizon 2020 da União Europeia e dos membros da Empresa Comum Clean Sky 2 que não a União.
Para obter mais informações, entre em contato com Guillaume Fourage, [email protected]
Resina
- Reciclagem:Compósitos termoplásticos reforçados com fibra contínua com policarbonato reciclado
- Solvay Expande a Capacidade do Composto Termoplástico
- Controle seu sistema de luz com sua voz
- O projeto Clean Sky 2 FUSINBUL desenvolve anteparas de pressão de fibra de carbono em escala real
- Clean Sky 2 lança resultados do projeto
- Strohm fornece à Austrália carretéis de jumper de composto termoplástico
- Consórcio visa soluções para estruturas compostas termoplásticas de fibra de carbono
- Hexcel faz parceria com Lavoisier Composites, Arkema
- Porta termoplástica a primeira para compósitos automotivos
- Fabricação rápida de blanks compostos personalizados