AFP em evolução para a próxima geração
Se a colocação automatizada de fibra (AFP) e a colocação automática de fita (ATL) foram os processos de fabricação que permitiram a aplicação generalizada de compostos no Boeing 787 e Airbus A350, então também será AFP / ATL que abrirá o caminho para a próxima geração de comerciais aeronaves, agora em pranchetas. A diferença desta vez? Avaliar.
A Boeing estima que, em 2037, o mundo precisará de mais de 31.000 novas aeronaves de corredor único para atender à demanda de passageiros. A Airbus prevê a necessidade de mais de 28.000 aeronaves de corredor único até 2037. Ambas as empresas estão considerando a substituição de seus robustos de corredor único - o 737 (Boeing) e o A320 (Airbus). Espera-se que ambas as empresas empreguem compostos de forma significativa em qualquer nova aeronave que desenvolvam. Ambas as empresas estão dizendo às suas cadeias de abastecimento para esperar taxas de produção para esses aviões de 60-100 aviões por mês, com ênfase em 100. A categoria de corredor único, para ambas as empresas, representa cerca de dois terços da demanda global total, o que significa que o O ambiente de fabricação desenvolvido para aeronaves de corredor único se tornará o ambiente de fabricação padrão para aerocompósitos em um futuro próximo.
Tudo isso significa que a tecnologia de automação deve ser desenvolvida agora se quiser acompanhar os requisitos de qualidade e taxa de produção das aeronaves de próxima geração. Nada disso é perdido no engenheiro sênior da Electroimpact (EI, Mukilteo, Wash., EUA) Todd Rudberg. Rudberg e EI entraram no mundo dos compósitos em 2004 quando a empresa desenvolveu a tecnologia AFP para a fabricação da seção dianteira da fuselagem 787 Seção 41 fabricada pela Spirit AeroSystems (Wichita, Kan., EUA). A EI posteriormente passou a produzir sistemas AFP e ATL para a fabricação de outras estruturas do 787, estruturas do A350, estruturas do motor e, mais recentemente, longarinas do Boeing 777X. Agora, Rudberg está olhando para o futuro da fabricação de aeronaves de próxima geração e vê oportunidades para melhorar a AFP. Substancialmente.
As oportunidades, diz Rudberg, são óbvias quando olhamos para os dados. Na verdade, a EI desenvolveu várias métricas para ajudar a empresa a entender o que seu maquinário faz bem e o que ele pode melhorar. Em primeiro lugar, ao observar o panorama da AFP de 2019, Rudberg vê uma miríade de ameaças à tecnologia AFP atual, incluindo ATL, layup de mão, cargas planas de tecidos e, é claro, alumínio.
As métricas AFP desenvolvidas por Rudberg vêm de um projeto de demonstrador de produção total (FPD) para o qual a EI conduziu quatro compilações de pré-produção. Os dados de uma dessas construções, feita em fevereiro de 2019 com a tecnologia EI AFP "padrão", revelaram um desafio substancial de utilização da máquina, com o tempo de uso da máquina caindo em um dos sete intervalos:
- Projeção a laser:30%
- Corrida:27%
- Inspeção:22%
- Quebra:10%
- Parada induzida pelo operador:6%
- Recuperação de erro:3%
- Imagem:2%
Visto de outra forma, com a tecnologia atual, há uma operação de valor agregado no AFP (run), com todas as outras operações consideradas sem valor agregado. Portanto, a proporção de operações de valor para operações sem valor é 1:3. “A indústria realmente quer 3:1, e eu também”, diz Rudberg, “e gostaria de terminar isso antes de me aposentar”. O objetivo, simplesmente, é reduzir o tempo consumido por operações sem valor agregado.
Há também uma métrica AFP abrangente que precisa de explicação:faixas médias antes da falha (MSBF). Este é o número médio de cabos de fibra colocados entre falhas de posicionamento. É claro que quanto maior for esse número, mais confiável será a máquina e o processo. A compilação de fevereiro FPD, diz Rudberg, teve um 5.365 MSBF.
Os objetivos
Olhando mais de perto a operação AFP, diz Rudberg, EI tem controle direto sobre apenas três operações:execução, recuperação de erro e inspeção. E é aqui que a empresa concentra seus esforços. Dito isso, Rudberg aponta que o airframer também tem um papel a desempenhar, particularmente na redução das inspeções de qualidade, quebras e paradas induzidas pelo operador. “Temos que perceber que os tempos de execução ficaram muito baixos porque as máquinas são muito rápidas”, diz ele, “e qualquer coisa que não agregue valor tem um impacto enorme na sua utilização. Então, parece que este é um esporte de equipe. Não apenas o OEM - eu - tem que fazer melhor, o airframer também tem alguma responsabilidade. ”
Para a fabricação de aeronaves de última geração, Rudberg deseja aumentar o MSBF para> 20.000, aumentar o tempo de execução para 77% e eliminar completamente a projeção de laser, a parada induzida pelo operador e a imagem. Como? Rudberg identifica três áreas de tecnologia que podem facilitar essa transição:gaiolas acionadas por servo, inspeção 100% em processo e gerenciamento de dados ou EI 4.0.
Todos os três foram avaliados pela EI em uma série de compilações de projeto FPD recentes após a construção inicial de fevereiro. Dados do próprio projeto FPD comprovam que a EI está caminhando na direção certa. Rudberg diz que o sistema AFP usado - chamado MuSCLE - atingiu 1.500 cavalos de potência de pico, 0,5 G de aceleração / desaceleração, uma taxa de assentamento de 4.000 polegadas / minuto, um tempo de giro da cabeça de 1 segundo, uma velocidade de canto de longarina de 120 graus / segundo e 6.000 MSBF (alcançado na produção).
A conversão para gaiolas de servo motor, e longe das gaiolas servopneumáticas, diz Rudberg, foi feita para aumentar a velocidade de colocação do reboque, a precisão da colocação do reboque, o controle da tensão do reboque e a confiabilidade geral da construção. A empresa passou os últimos dois anos trabalhando em um servo drive compacto que pode ser instalado no cabeçote modular EI. Os resultados da tecnologia, até agora, são promissores; o teste mostra:15.000 MSBF, velocidade de adição 87% mais rápida, velocidade de corte 36% mais rápida, melhor precisão de posicionamento final. Além disso, a EI provou que o sistema de gaiola do servo motor pode ser usado para colocar fibras de carbono secas.
A chave para a inspeção é a parte “em processo”. EI já possui tecnologia de inspeção, desenvolvida com Aligned Vision (Chelmsford, Mass., EUA) e implantada na linha de fabricação de asas 777X que usa laser e tecnologia de visão para verificar voltas, lacunas, rugas, erros de posicionamento final e detritos de objetos estranhos ( FOD). Este sistema, entretanto, existe independente do sistema AFP e requer um campo de visão claro para operar - o que significa que a cabeça AFP deve ser movida. Rudberg e EI desenvolveram um novo sistema de inspeção, chamado RIPIT, que é parte integrante da cabeça AFP e inspeciona a colocação da fibra assim que ocorre.
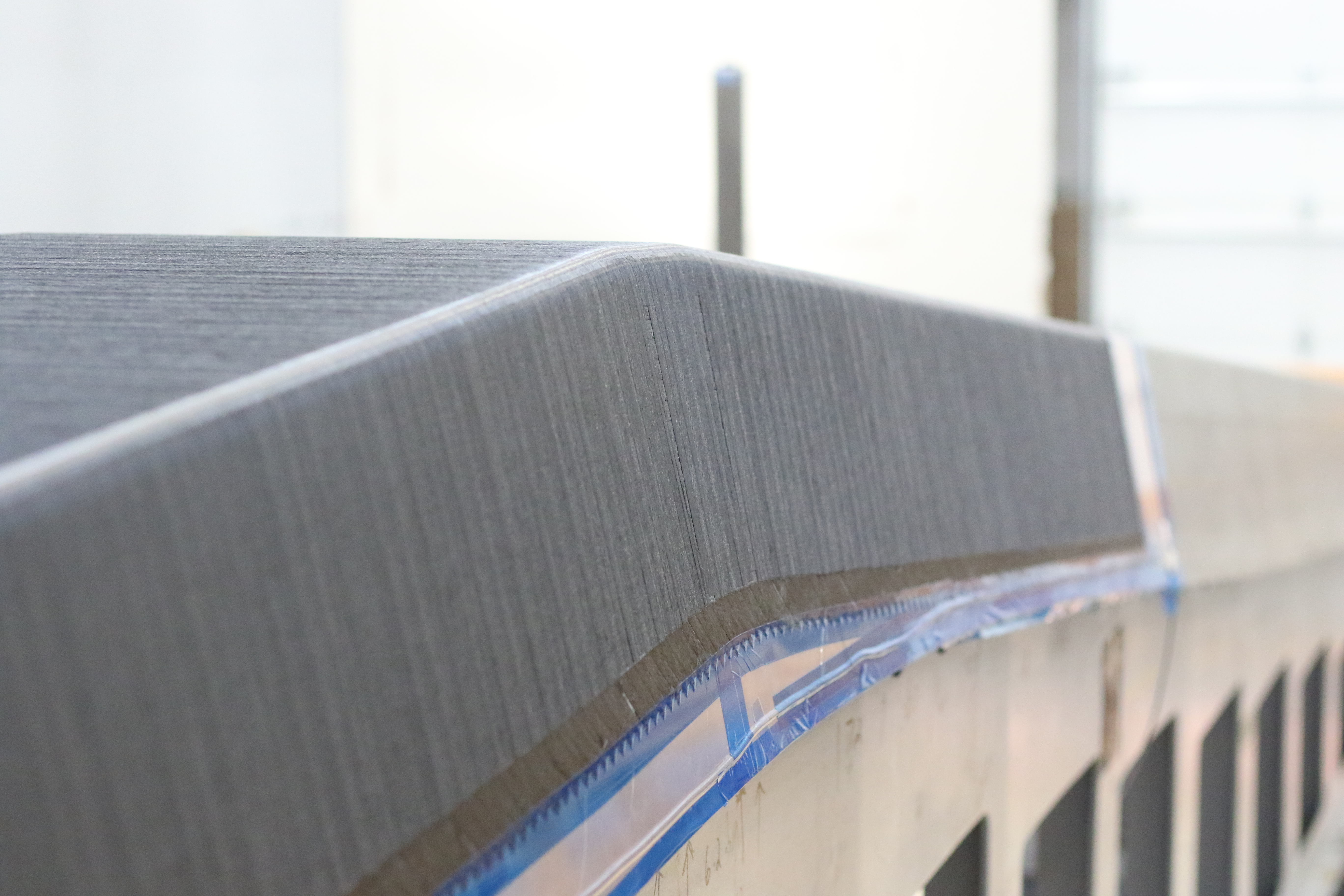
À medida que a Boeing e a Airbus consideram os processos de fabricação de compósitos fora da autoclave, a capacidade dos sistemas AFP de posicionar com eficiência as fibras de carbono secas será crítica. Este demonstrador mostra fibra seca colocada por um sistema de Electroimpact. Fonte | Eletroimpacto
A EI não divulgará a natureza da tecnologia por trás do RIPIT, exceto para dizer que não é baseada em laser ou visão. Em qualquer caso, Rudberg diz que os testes do sistema revelam que ele é capaz de detectar, em tempo real, o deslizamento do reboque a ± 0,030 polegada, adicionar posicionamento a ± 0,050 polegada e o posicionamento do corte a ± 0,050 polegada. Além disso, diz Rudberg, "Fizemos muitos testes correlacionando os dados RIPIT com o sistema de visão qualificado da Boeing existente [sistema de visão alinhado usado no 777X] e conseguimos correlação."
O valor do gerenciamento de dados, diz Rudberg, está na capacidade dos sistemas da EI de ajudar os fabricantes a ver mais claramente como o processo AFP está funcionando. Para tanto, a EI desenvolveu um software de visualização de dados - EI 4.0 - que oferece visibilidade não apenas de como uma determinada máquina funcionou (com base no MSBF) durante uma determinada construção, mas também de como os reboques e sequências individuais foram executados. Basicamente, o software ajuda o operador a ver exatamente onde está o problema na cabeça AFP. “Portanto, usaremos este EI 4.0 para indicar onde eles [operadores] precisam olhar no cabeçote AFP para fazer alterações”, diz Rudberg.
Usando este software, é possível exibir graficamente o MSBF para uma variedade de funções da máquina e identificar cabos de fibra problemáticos e sequências particularmente desafiadoras. O software também mede e relata outras atividades da máquina que podem prejudicar a utilização. Usando essas ferramentas de gerenciamento de dados, a EI foi capaz de otimizar e reduzir o tempo de construção do OPS de mais de 50 minutos para pouco menos de 40 minutos. Outras ferramentas incluem comparações de desempenho de mudança e comparações de ângulo de camada.
“Eu acredito que a utilização de 75% é uma meta ou expectativa realista”, afirma Rudberg. “Mas, vai ser necessário trabalho em equipe, vai exigir iniciativa organizacional e acompanhamento do airframer, vai levar nossa tecnologia aprimorada, vai precisar de melhor manutenção preventiva e preditiva, e melhores ferramentas para analisar o uso de células e desempenho da máquina. ”
Resina
- Indústria 4.0 e a IoT:Tendências de mercado para os próximos anos
- Realidade aumentada - a próxima grande novidade para RH?
- A DARPA está trabalhando em materiais de próxima geração para veículos hipersônicos
- Novos cristais para tecnologias de exibição de próxima geração
- Como se preparar para a próxima interrupção da cadeia de suprimentos
- Cinco regras para a próxima crise da cadeia de suprimentos
- Merchandising na nuvem é o próximo item obrigatório para o varejo
- Material para a próxima geração de sensores inteligentes
- COVID-19:Demanda pela próxima geração de fábrica inteligente
- O que vem a seguir para a revolução da automação?