Quão maduras estão as tecnologias de impressão Metal 3D?

[Crédito da imagem:Laboratório de Pesquisa do Exército CCDC]
A impressão 3D em metal abrange uma ampla gama de tecnologias, cada uma com seus próprios benefícios e aplicações - bem como seu próprio nível de maturidade.
Ao procurar adotar uma tecnologia de impressão 3D de metal específica para a produção, é crucial entender onde estão suas capacidades e limitações atualmente. No entanto, quando se trata de impressão 3D de metal, as empresas enfrentam o desafio de separar a realidade do exagero.
Para ajudar as empresas a avaliar a maturidade das principais tecnologias de impressão 3D de metal, hoje estaremos ver como estão prontos para a produção de peças finais, com base em um sistema Technology Readiness Level (TRL), desenvolvido pela primeira vez pela NASA.
O que exatamente é o nível de preparação da tecnologia (TRL)?
Desenvolvido pela primeira vez pela NASA no início dos anos 1970, o “Nível de preparação da tecnologia” é uma abordagem usada para avaliar se uma tecnologia emergente é adequada para a exploração espacial. Na década de 1990, os TRLs foram aplicados em muitas agências do governo dos Estados Unidos e agora são de uso comum em muitos setores.
O sistema TRL mede a maturidade de uma tecnologia do Nível 1 (Avaliação de Conceito) até o Nível 9 (Implementação com Sucesso) . Cada um dos nove níveis demonstra um marco no desenvolvimento da tecnologia.
Como o TRL pode ser usado para avaliar a maturidade das tecnologias de impressão 3D de metal?
Aplicamos essa abordagem para avaliar a maturidade das diferentes tecnologias de impressão 3D. Para identificar um TRL para cada tecnologia de impressão 3D de metal, analisamos sua evolução, as indústrias que a adotam, como está sendo usada hoje e os desenvolvimentos que estão moldando seu futuro.
Notavelmente, em alguns casos o TRL pode ser específico da aplicação. Por exemplo, a tecnologia de Deposição de Energia Direta fica em um TRL 8 para aplicações de produção, enquanto suas aplicações de reparo alcançaram o Nível 9.
Com base em nossa pesquisa, acreditamos que a maioria do metal 3D tecnologias de impressão cruzaram o TRL 7, que se refere a testes em um ambiente operacional para resolver problemas de desempenho e aplicações em prototipagem funcional e ferramentas.
Algumas também provaram ser bem-sucedidas em condições normais de operação (TRL 8) e estão caminhando para a integração no ecossistema de manufatura mais amplo (TRL 9).
Fusão de leito de pó a laser

Nível de preparação da tecnologia:8 A fusão da cama do pó do laser (PBF) é uma das tecnologias de impressão 3D do metal as mais estabelecidas. O processo de metal PBF envolve a aplicação seletiva de um poderoso laser de ajuste fino a uma camada de pó metálico. Desta forma, as partículas de metal são fundidas camada por camada para criar uma peça.
As origens do metal PBF remontam a 1995, quando o Instituto Fraunhofer em Aachen, Alemanha, registrou a primeira patente para fusão de metais a laser. Desde então, muitas empresas, incluindo players consagrados como EOS, Concept Laser (adquirida pela GE) e SLM Solutions, entraram no mercado de PBF com sua abordagem da tecnologia.
Ao longo da última década, os fabricantes de impressoras 3D de metal PBF têm trabalhado arduamente na otimização da tecnologia para a produção. Para tanto, vimos os principais participantes do mercado lançando soluções para produção automatizada e integrada.
A maioria dessas soluções compartilham características semelhantes:são modulares, configuráveis e oferecem um alto nível de automação em uma tentativa de maximizar a eficiência e reduzir a quantidade de trabalho manual necessário. Ao mesmo tempo, a escolha material para o PBF tem se expandido continuamente. Por exemplo, a EOS lançou quatro novos pós de metal para suas impressoras 3D de metal no mês passado. Entre eles estão aço inoxidável CX, alumínio AlF357, titânio Ti64 grau 5 e titânio Ti64 grau 23.
Graças a esses desenvolvimentos, o laser PBF encontrou seu caminho em muitas indústrias e aplicações. Uma indústria que tem estado particularmente interessada em adotar o metal PBF é a aeroespacial.
Hoje, as peças de metal PBF impressas em 3D estão alimentando aeronaves e sistemas espaciais cruciais, como motores. É aqui que os principais recursos da tecnologia - a produção de peças complexas com montagem simplificada e menos desperdício de material - realmente brilham.
A partir de agora, a tecnologia de PBF a laser é capaz de fornecer peças funcionais repetidamente. No entanto, ainda requer alguns ajustes e testes antes que os fabricantes possam se comprometer com a produção em grande escala. É por isso que sugerimos que está atualmente no Nível 8 de Prontidão de Tecnologia.
Daqui para frente, a facilidade de uso e confiabilidade dos sistemas de PBF de metal aumentará, impulsionado de muitas maneiras pelos avanços em software e em geral fluxo de trabalho.
Um exemplo que apóia essa tendência vem do fabricante de impressoras 3D de metal com sede na Califórnia, VELO3D.
No desenvolvimento de sua tecnologia de PBF a laser, chamada Intelligent Fusion, a empresa colocou um foco principal na integração de software e hardware. O resultado é um sistema totalmente integrado que pode imprimir peças com menos suportes, melhor acabamento de superfície e, supostamente, maior taxa de sucesso. Isso, por sua vez, leva a uma maior confiabilidade, produção mais rápida e menos pós-processamento. O laser PBF continua a ser a força motriz da indústria de impressão 3D do metal. As impressoras 3D de metal PBF têm a maior base instalada entre outras tecnologias de impressão 3D de metal. E os fabricantes de impressoras 3D PBF têm as maiores participações no mercado de impressão 3D de metal quando comparados às empresas que produzem outros tipos de impressoras 3D de metal.
Por causa disso, vários materiais estão sendo desenvolvidos primeiramente para as tecnologias de metal PBF. Isso significa que a evolução dessa tecnologia continuará, impulsionada pela demanda por peças de metal complexas e de alto desempenho impressas em 3D.
Derretimento do feixe de elétrons
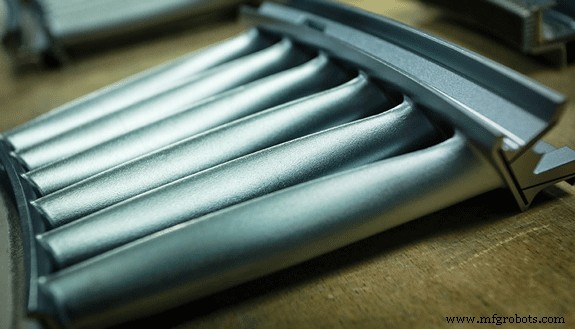
Nível de preparação da tecnologia:8 O derretimento do feixe de elétrons, como o laser PBF, pertence à família da fusão do leito de pó das tecnologias de impressão 3D. EBM opera de forma semelhante ao laser PBF em que os pós de metal também são fundidos para criar uma peça de metal totalmente densa.
A principal diferença entre as duas tecnologias é a fonte de energia:em vez de um laser, os sistemas EBM usam um feixe de elétrons de alta potência como fonte de calor para derreter camadas de pó metálico.
Desde o patenteamento da tecnologia em 2000, a empresa sueca Arcam continua sendo o principal fabricante de impressoras 3D EBM.
Após a aquisição da empresa pela GE em 2016, a tecnologia EBM continuou a evoluir. Em 2018, a Arcam lançou sua próxima geração de máquinas EBM, a Spectra H.
O 'H' significa 'metal quente', o que significa que pode processar alto calor e materiais sujeitos a rachaduras, como o alumineto de titânio (TiAl) em temperaturas que chegam a 1000 ° C.
Arcam EBM Spectra H tem uma série de novos recursos que visam aumentar a produtividade e reduzir os custos gerais.
Por exemplo, o EBM Spectra H está equipado com uma potência de 6kW HV , o que ajuda a reduzir as etapas de pré e pós-aquecimento em 50% em comparação com outras máquinas EBM atualmente no mercado.
Além disso, o processo de estratificação foi atualizado para reduzir as altas temperaturas. Isso permite que os fabricantes economizem até cinco horas em uma construção de altura total e aumentem as velocidades de impressão em até 50% em comparação com outras máquinas EBM.
O negócio da GE Aviation, Avio Aero, está supostamente usando 35 Arcam máquinas:31 máquinas Arcam A2X e 4 máquinas Arcam EBM Spectra H. Na Avio Aero, as impressoras 3D são usadas para produzir lâminas TiAl para turbinas de baixa pressão do novo grande motor GE9X.
Além da indústria aeroespacial, a indústria médica está usando extensivamente a tecnologia para produzir implantes médicos . O uso mais antigo de EBM para esta aplicação remonta a 2007.
Amparada pelos recursos e experiência da GE em metal AM, a tecnologia EBM está no caminho para a industrialização. A tecnologia está sendo aplicada em ambientes de produção em setores altamente regulamentados, como aeroespacial e médico. Considerando essas aplicações, o EBM atingiu o TRL 8.
Deposição de energia direta
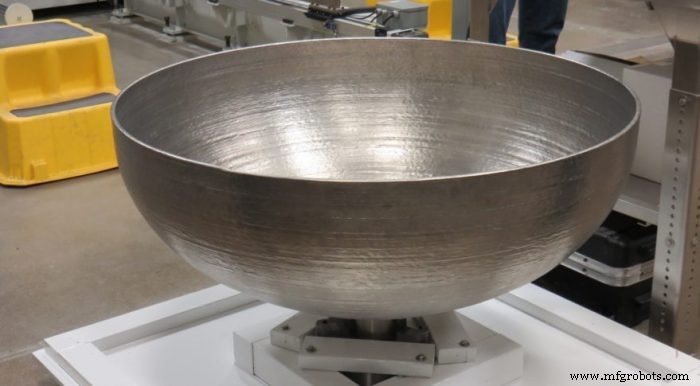
Nível de preparação da tecnologia:8
Originário de processos de soldagem, o Direct Energy Deposition (DED) envolve a fusão de metal com um laser ou feixe de elétrons conforme o material é empurrado através de um bico para uma plataforma de construção. Os sistemas DED usam arame ou pó como matéria-prima. A maioria dos sistemas usa materiais comerciais prontos para uso, desenvolvidos para soldagem ou metalurgia do pó. O uso de materiais prontos para uso tem muitas vantagens, incluindo uma seleção mais ampla de materiais, maior qualidade e preço mais baixo.
Uma das primeiras e mais bem-sucedidas aplicações do DED tem sido o reparo de componentes danificados. A tecnologia é usada para adicionar material às peças danificadas, como lâminas de turbina e inserções de molde de injeção. Ao reparar peças desgastadas, o DED ajuda a reduzir o tempo de inatividade e os custos associados à substituição de uma peça, ao mesmo tempo que estende a vida útil da peça.
Para permitir o uso do DED além das aplicações de reparo, os fabricantes de sistemas DED têm desenvolvido e otimizado soluções para a produção de peças metálicas funcionais.
Por exemplo, Sciaky, um dos pioneiros da tecnologia DED, introduziu o controle de malha fechada em seus sistemas de manufatura de aditivos de feixe de elétrons. O sistema de monitoramento de processo da Sciaky combina imagens ópticas em tempo real com visão de máquina para medir o tamanho, a forma e a temperatura da poça de fusão.
Com base nos dados obtidos da imagem, um sistema de controle de circuito fechado então fornece comandos de ajuste ao software que controla a potência do feixe, a taxa de alimentação do arame e o movimento da máquina. Graças a isso, a repetibilidade do processo pode ser substancialmente melhorada. A tecnologia DED já foi aplicada em várias aplicações aeroespaciais e de defesa. Os exemplos incluem cúpulas de tanques de combustível de titânio para satélites, peças estruturais de titânio para o Boeing 787 Dreamliner e peças de reposição para veículos militares.
A tecnologia se estabeleceu como uma solução de manutenção prontamente disponível. Com esta aplicação, o DED está em TRL 9.
Quando se trata de aplicações de produção, o DED também pode ser usado como uma ferramenta de manufatura. No entanto, mais desenvolvimentos são necessários em termos de avanço no controle do processo e melhoria da resolução de impressão.
A partir de agora, a tecnologia produz formatos quase líquidos, que precisam de usinagem substancial para atingir a especificação da peça e um bom acabamento superficial. Melhorar a resolução de impressão permitirá que os fabricantes reduzam o tempo e o custo necessários para a usinagem secundária.
Jateamento de ligantes metálicos
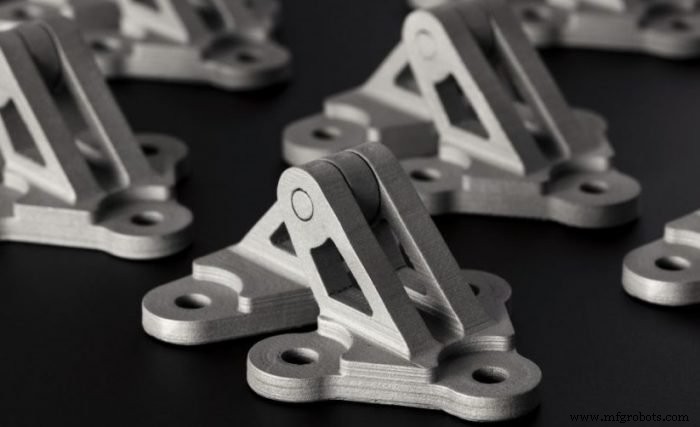
Nível de preparação da tecnologia:varia
O jato de ligantes metálicos está evoluindo rapidamente para uma tecnologia de fabricação muito promissora. No entanto, o nível de preparação da tecnologia varia muito entre as tecnologias de jato de aglutinante de metal no mercado hoje.
O jato de ligantes metálicos foi desenvolvido pela primeira vez em 1993 no MIT. O processo de impressão começa espalhando uma fina camada de pó, com os cabeçotes de impressão estrategicamente depositando gotículas de aglutinante no leito de pó. O processo se repete camada por camada até que a peça esteja completa, com o pó não utilizado (cerca de 95%) reciclado.
A ExOne, que licencia a tecnologia do MIT desde 1996, continuou sendo a única empresa a oferecer metal binder jetting services e sistemas até o início de 2010. Os sistemas de jato de aglutinante de metal da ExOne foram amplamente usados para criar protótipos de metal e ferramentas.
No entanto, à medida que as patentes de jateamento de ligantes metálicos começaram a expirar, a competição se acirrou, encorajando a empresa a iniciar o desenvolvimento de soluções em nível de produção. A mais recente, a impressora X1 25PRO 3D, foi lançada comercialmente há alguns meses.
Outro grande player no mercado de jateamento de aglutinantes de metal é o Digital Metal. Suas impressoras 3D DM P2500, apresentadas pela primeira vez em 2017, já produziram mais de 300.000 componentes em vários setores, incluindo aeroespacial, produtos de luxo, ferramentas odontológicas e equipamentos industriais.
Existem também alguns recém-chegados à arena de jateamento de aglutinantes de metal, incluindo HP e Desktop Metal.
Depois de revelar sua tecnologia Multi Jet Fusion para peças de polímero em 2016, a HP introduziu a próxima extensão de suas ofertas de aditivos em 2018:um sistema de impressão 3D Metal Jet. Com um novo sistema, a HP pretende colocar a tecnologia em um ambiente de produção de alto volume.
Para o conseguir, a empresa equipou o seu sistema com mais bicos e introduziu um agente de ligação inovador. Combinados, esses avanços tornam o processo de impressão mais rápido e simples.
A tecnologia por trás da impressora 3D Desktop Metal é o que a empresa chama de Single Pass Jetting (SPJ), uma versão mais rápida do processo típico de jato de aglutinante. A empresa afirma que seu sistema pode imprimir a até 12.000 cm3 / h, o que se traduz em mais de 60 kg de peças de metal por hora.
Curiosamente, o Metal Jet da HP e o sistema de produção de Desktop Metal compartilham um valor um tanto semelhante proposição. Ambas as máquinas baseadas em jato de aglutinante visam interromper a fabricação tradicional, permitindo maior velocidade e escalabilidade.
Embora o sistema de produção do Desktop Metal tenha sido lançado no início deste ano, a tecnologia da HP está programada para um lançamento em 2020 e está atualmente disponível apenas através do HP Metal Jet Production Service.
É certo que muitas das tecnologias de jato de aglutinante de metal surgiram apenas recentemente. Isso significa que eles precisarão de algum tempo para provar que estão prontos para aplicativos de produção em série por meio de testes adicionais, seja internamente ou nas instalações do cliente.
Com um histórico em aplicações de produção, as tecnologias mais antigas, como as da Digital Metal e ExOne, estão entre os níveis de preparação de tecnologia 7 e 8. Esperamos que as tecnologias de jato de aglutinante de metal mais recentes alcancem e excedam o TRL 8 nos próximos anos. Os sistemas de jato de metal aglutinante continuarão a evoluir em uma tentativa de atender aos desafios de mercado para a penetração de outras tecnologias de impressão 3D de metal, incluindo a produção de bens automotivos e industriais de alto volume. Isso cria muitas oportunidades de crescimento empolgantes para esta tecnologia no futuro.
Deposição de metal ligado
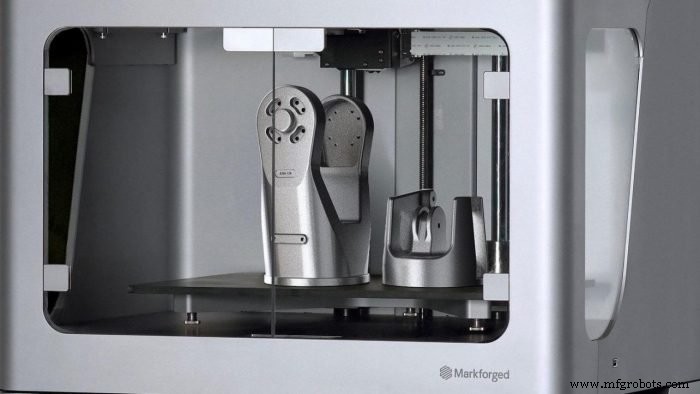
Nível de preparação da tecnologia:7
A deposição de metal vinculado é uma novidade empolgante no espaço de manufatura aditiva de metal. A tecnologia funciona de maneira semelhante à Fused Filament Fabrication (FFF), em que um filamento é aquecido e extrudado através de um bico, criando uma peça camada por camada. No entanto, ao contrário dos filamentos de plástico usados em FDM, a extrusão de metal usa filamentos feitos de pós de metal ou pellets envoltos em aglutinantes de plástico.
As duas empresas de maior destaque a trabalhar nesta área são a Markforged e a Desktop Metal. Ambas as empresas revelaram pela primeira vez seus sistemas de impressão 3D de metal (Metal X da Markforged e Desktop Metal’s Studio System) em 2017.
Atualmente, a tecnologia é amplamente usada para criar protótipos de metal e ferramentas de forma mais rápida e econômica.
Um exemplo é a Dixon Valve &Coupling Company, fabricante e fornecedora de acessórios para as indústrias de transferência de fluidos. A empresa usou as garras de pinça de impressão de Metal X para 3D da Markforged. Essas ferramentas são essencialmente braçadeiras, que são montadas em um braço robótico que adiciona anéis de vedação aos acoplamentos de aço.
A produção dessas ferramentas leva 14 dias e custa US $ 355. Para comparar, a impressão 3D de uma garra de metal custa US $ 7 e requer 1,25 dias para ser concluída - uma redução de mais de 90% para o custo e o tempo de espera.
Enquanto a tecnologia de deposição ligada está fazendo grandes avanços em custos effective prototyping and speeding time to market, its use on the production side remains limited. For one, such systems are positioned as compact metal 3D printers, which can be difficult to scale.
However, as more companies adopt the technology, especially for remote locations like oil platforms, we may see more examples of spare and end-use parts created using bound metal deposition in the years to come.
Innovating with metal 3D printing
The majority of metal 3D printing technologies have reached quite high technology readiness levels, meaning that they are suitable for production applications.
Obviously, a lot of work remains to be done, particularly on improving the economics and speed of metal 3D printing technologies. Currently, powder bed processes, DED and metal binder jetting are considerably more expensive than conventional manufacturing systems.
Lower-cost bound powder deposition systems bring some accessibility to metal 3D printing and could offer a good entry point for smaller businesses.
Ultimately, advancing the technology itself is only one piece of the puzzle. It’s equally crucial for the ecosystem around metal 3D printing to continue to evolve. This may involve the development of better integrated and easier to use software solution, automation of post-processing operations and creation of streamlined workflows.
Only by putting all the pieces together, there is a way to achieve significant process and product innovation with metal 3D printing.
impressao 3D
- Como os modelos de objetos são projetados para impressão 3D
- Como as pontes são usadas na impressão 3D
- Como a impressão 3D pode beneficiar a fundição de metal? Aqui estão três maneiras
- Impressão 3D de metal:Onde estamos hoje?
- Quão madura é a sua indústria na adoção da impressão 3D? [Infográfico]
- 10 empolgantes tecnologias de impressão 3D que surgiram nos últimos 12 meses
- Como as impressoras 3D de mesa estão transformando a impressão 3D
- AM ao redor do mundo:quão madura é a impressão 3D na região da Ásia-Pacífico?
- Como o mercado de hardware de impressão 3D está evoluindo em 2020
- Quão sustentável é a impressão 3D industrial?