Especialistas:maior automação é fundamental para atender à demanda de aeronaves
Somente as necessidades comerciais nos próximos 20 anos sugerem a duplicação das taxas de produção
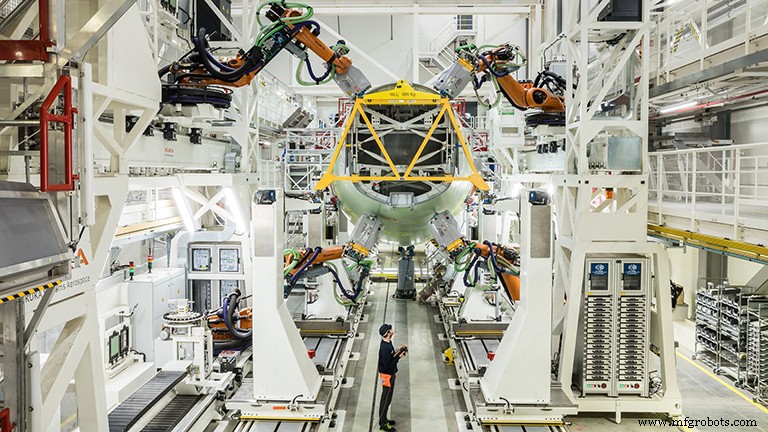
Antes que a pandemia de coronavírus derrubasse a vida normal e essencialmente fechasse os aviões comerciais, a indústria da aviação tinha uma necessidade projetada de 40.000 novas aeronaves – aviões, helicópteros, táxis aéreos e veículos aéreos não tripulados – nos próximos 20 anos. O volume inclui substituições para embarcações que ficam fora de serviço após uma vida útil média de 25 a 30 anos e está no topo de uma carteira de pedidos de aproximadamente oito anos.
Se a demanda por voos retomar seu nível anterior quando as restrições relacionadas à pandemia diminuirem, a única maneira de satisfazer a necessidade projetada é por meio do aumento da automação, disseram alguns especialistas do setor.
Ao contrário de muitos outros setores, a indústria da aviação é aquela em que o trabalho manual é comum porque não existem processos de fabricação alternativos atuais que sejam viáveis. Mas considerando o registro da Statista de aumentos ano após ano na demanda de 2006-2019 para a demanda global de passageiros de tráfego aéreo (os aumentos variaram de 2,4% a 8,1%, exceto 2009 no auge da Grande Recessão) e outros fatores, maior eficiência é obrigatório se a indústria vai manter-se.
Os pesquisadores estão tentando descobrir como automatizar alguns processos, como o hand layup. Mas existem outras medidas automatizadas atualmente disponíveis, incluindo instruções de projeto para montagem em estações de trabalho e para processos automatizados de vedação, fixação, marcação e manuseio de materiais.
Somente as necessidades da aviação comercial exigiriam uma duplicação efetiva das taxas de produção, disse John D. Russell, chefe do ramo de tecnologia de estruturas do Laboratório de Pesquisa da Força Aérea.
Além de aviões comerciais, os militares estão explorando aeronaves que podem ser produzidas aos milhares.
Finalmente, o conceito de táxi aéreo vem ganhando força de empresas de aviação tradicionais e empresas como Uber e exigiria ainda mais produção.
“Para qualquer um desses casos individualmente, estou ouvindo de meus contatos no setor que os EUA não têm capacidade atualmente”, disse Russell, alertando que suas informações são anteriores ao vírus em todo o mundo. “Se todos os três se tornarem realidade ao mesmo tempo, a indústria terá que ser criativa sobre como resolver o problema de capacidade.
“A grande alternativa que estou ouvindo é o uso da automação para aumentar a produtividade e o throughput, especialmente para a aviação comercial. As empresas estão pesquisando como a automação pode melhorar as coisas, desde a fabricação de peças até a montagem. Estou ouvindo que a despesa de capital para automação é menor do que para adicionar novas linhas de produção.”
Russell disse que não ficaria surpreso ao ver a indústria de táxi aéreo procurar produção no exterior porque o preço do veículo provavelmente será um grande impulsionador para seu modelo de negócios. Ele tem dúvidas de que veríamos offshoring para a aviação comercial porque a indústria provavelmente manteria as relações estabelecidas com os fornecedores devido ao alto nível de habilidade envolvido para a força de trabalho. Obviamente, o offshoring não seria uma opção para qualquer veículo militar, observou ele.
Entregar 40.000 aeronaves em 20 anos exigiria a produção de 2.000 aviões por ano, o que é muito maior do que as entregas antes da pandemia.
Um atraso nas entregas foi criado quando os fabricantes não conseguiram se preparar com rapidez suficiente para atender ao aumento da demanda criado por um aumento no transporte aéreo.
Além disso, os consumidores agora veem as viagens aéreas como uma necessidade em vez de um luxo e têm meios para pagar por viagens pessoais.
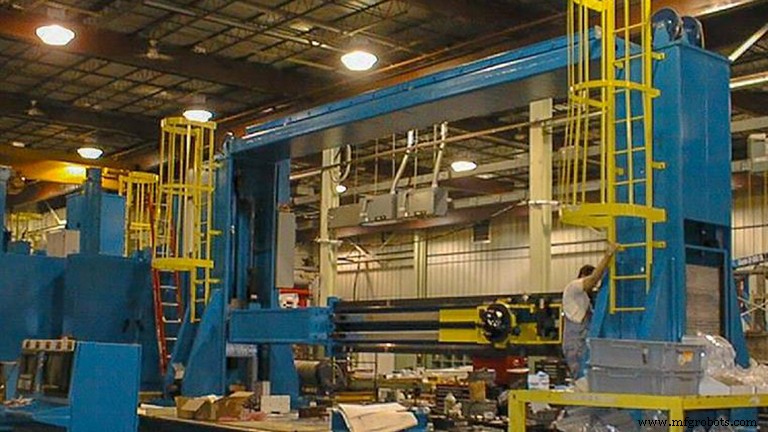
Como resultado, as companhias aéreas comerciais expandiram suas ofertas para oferecer aos consumidores famintos por voos flexibilidade nos horários de decolagem.
A Boeing tinha uma carteira de 5.049 aeronaves em 1º de maio, enquanto os pedidos pendentes da Airbus haviam acumulado até 7.650 em 31 de março.
Antes da pandemia, esperava-se que um renascimento da concorrência entre a Boeing e a Airbus resultasse em entrega recorde de suas plataformas de fuselagem estreita altamente populares e um crescimento de 9,4% na produção anual em 2019. A Boeing e a Airbus foram projetadas para produzir mais de 1.750 aeronaves no ano passado, contra 1.606 unidades em 2018, de acordo com um comunicado de imprensa de meados de junho de 2019 da empresa de pesquisa e análise Frost &Sullivan.
Em agosto, porém, outros estavam cortando esses números.
A produção global de aeronaves caiu um quarto após o aterramento do jato 737 Max da Boeing em março de 2019, após dois acidentes fatais, de acordo com um artigo do jornal The Guardian. ADS, o grupo de lobby aeroespacial britânico, disse que 88 aeronaves foram entregues em julho de 2019, uma queda de 24 por cento nas entregas durante o mesmo mês do ano anterior, com a queda em grande parte devido à queda na produção de aviões de corredor único como o 737.
Até o final do ano passado, a Airbus e a Boeing juntas entregaram 1.243 aeronaves.
A indústria está agindo para aumentar esses números.
“Os dois maiores fabricantes de aeronaves comerciais, Boeing e Airbus, estão investindo muito dinheiro adicional para aumentar a taxa de produção”, disse Bill Bigot, vice-presidente de desenvolvimento de negócios para aeroespacial e defesa da JR Automation.
No final do ano passado, em Hamburgo, na Alemanha, a Airbus implementou sua linha de montagem altamente automatizada da estrutura da fuselagem da Família A320.
A nova instalação conta com 20 robôs, um novo conceito de logística, posicionamento automatizado por medição a laser, além de um sistema digital de aquisição de dados, informou a empresa.
Além do uso de robôs, a Airbus também está implementando novos métodos e tecnologias na logística de materiais e peças para otimizar a produção, melhorar a ergonomia e reduzir os prazos de entrega. Isso inclui a separação dos níveis de logística e produção, reposição de materiais orientada para a demanda e o uso de veículos autônomos guiados.
Na mesma época, no entanto, a Boeing encerrou um esforço de automação total de quatro anos em sua fábrica de Everett, Washington, que usava braços robóticos para inserir fixadores em duas seções principais da fuselagem de seus jatos 777 e 777X, optando pela inserção manual por mecânicos habilidosos.
Os robôs ainda fazem os furos para os fixadores em um sistema automatizado de “faixa flexível”, resultando em um processo combinado humano-robótico, de acordo com relatórios publicados.
O esforço pode valer a pena no final, no entanto.
Os esforços fracassados para usar a robótica ensinaram à Boeing algumas lições valiosas de seu “primeiro mergulho profundo nesse tipo de tecnologia”, disse Jason Clark, vice-presidente da Boeing que supervisiona a produção do 777X, ao Los Angeles Times. “Isso nos ensinou a projetar para automação”, Clark foi citado em um artigo de novembro.
O novo método cria menos desgaste nos trabalhadores, já que as máquinas desenvolvidas pela Electroimpact Inc. lidam com uma das tarefas mais exigentes fisicamente da montagem da fuselagem:fazer furos em metal, de acordo com o artigo do Times.
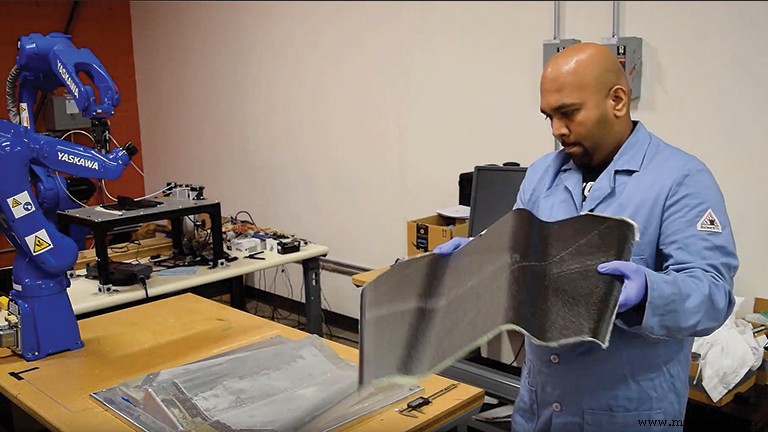
Além disso, “reprojetamos partes da construção para substituir os rebites por formas menos difíceis de fixadores, melhorando ainda mais a ergonomia”, disse um porta-voz da empresa.
Nem todas as medidas para aumentar a produção incluem novas linhas e robôs.
Em sua fábrica de North Charleston, S.C., Boeing:mecânica equipada com exoesqueletos projetados para reduzir a tensão do trabalho aéreo sustentado; implantou chaves inteligentes habilitadas para Bluetooth para garantir que os trabalhadores apliquem o torque correto a uma porca e usem realidade virtual para mecânicos testarem novas ferramentas, de acordo com a Reuters.
Os robôs podem assumir a bandeja de mão?
Antes de qualquer estrutura de fuselagem ser enviada para as fábricas de Hamburgo ou da Boeing no estado de Washington, elas são fabricadas em processos automatizados de fabricação de compósitos (ACM), incluindo colocação automatizada de fibras e colocação automatizada de fitas.
O ACM é adequado para peças médias ou grandes, como fuselagens, asas e anteparas, que também são planas ou levemente contornadas.
Mas peças compostas pequenas e médias são fabricadas manualmente, um processo muito ineficiente que desperdiça muito material.
Isso é um grande negócio porque essas peças - clipes, suportes, vigas em I e portas de acesso - podem representar até metade do peso de uma estrutura e chegar aos milhares para apenas um plano.
“Além disso, essas peças que precisam ser colocadas à mão precisam ser cortadas e perfuradas, espremidas, o que você quiser”, disse Les Cohen, consultor de compósitos. “Isso significa que sua taxa de compra para voar pode ser um fator de 2:se você estiver trabalhando com um material que custa US $ 40 por libra, é efetivamente um material de US $ 80 por libra”.
Uma equipe da Universidade do Sul da Califórnia concluiu recentemente um projeto de demonstração para automatizar o layup com braços robóticos.
Embora não seja automação, ainda há espaço para melhorar os materiais usados na construção do avião.
A indústria entende que o tempo que leva para autoclave as peças em andamento nas operações de debulking a cada poucas camadas, juntamente com a cura da peça final, leva muito tempo. Resinas de cura rápida que têm as propriedades de peças curadas em autoclave, mas sem o processo de autoclave, são a resposta, mas não estão disponíveis, disse Cohen. Com investimentos de até cinco anos em média e custos estimados de US$ 10 milhões para desenvolver novos materiais, sem garantia de que serão aceitos, é compreensível que esse desafio não seja cumprido, disse ele.
4ª Revolução Industrial demora para decolar na indústria aeroespacial
A Indústria 4.0, com sua promessa de maior produtividade e qualidade, também pode ajudar a impulsionar a produção da aviação, mas a indústria tem demorado a adotar o mundo conectado, digitalizado e orientado a dados da quarta revolução industrial.
“Eu diria que as coisas estão entrando online agora em produção e entregando resultados. Estamos muito envolvidos com isso e estamos no ponto em que podemos implementar isso em um nível de programa e realmente dar algo a uma fábrica que afetará absolutamente sua eficiência”, disse Andrew Purvis, gerente de projeto para layup e automação de compósitos. na Electroimpact Inc. “Quando você começa a obter os dados e começa a processar os números, você começa a encontrar muito ouro naquela montanha de dados e muitas vezes diamantes, coisas que realmente começam a aumentar sua produção.”
Pronto para a automação está o lado da qualidade da produção, disse Purvis.
A Electroimpact incorpora monitoramento de qualidade em sistemas com tecnologia de inspeção que medem tudo o que suas máquinas AFP fazem enquanto constroem ou imprimem uma peça. A inspeção automática possibilita um processo que a empresa chama de “ajuste contínuo”.
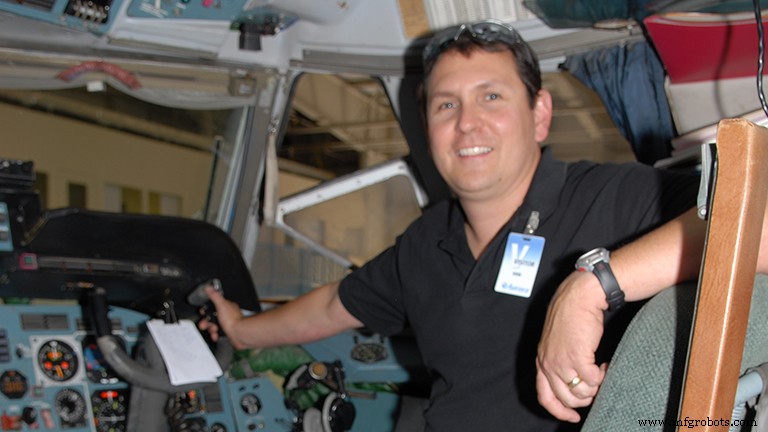
“O sistema está realmente se mantendo calibrado observando o que está fazendo e se ajusta continuamente”, disse ele. "Como uma máquina ou impressora AFP pode olhar para a saída com uma câmera ou sensores e dizer 'Ei, notei que você está começando a se desviar um pouco, então vou compensar'."
Neste momento, adotar a Indústria 4.0 é mais uma aspiração do que uma conquista, em parte devido às implicações de segurança cibernética e gerenciamento de dados, disse Mick Maher, presidente da consultoria Maher Associates.
“Não acho que a indústria aeroespacial esteja pegando mais devagar do que qualquer outra indústria”, disse ele. “Acho que a Indústria 4.0 ainda é muito imatura para entregar as rédeas neste momento. Dito isto, a automação é um componente chave da Indústria 4.0. Mas, assim como há partes da automação que estão maduras, como colocação de fita, colocação de fibra, ainda há muito desenvolvimento necessário.”
Grandes ganhos a serem obtidos
Randy Rounkles, que foi diretor técnico aeroespacial da JR Automation, esteve anteriormente na Spirit Aerosystems, onde fez parte de uma equipe para implantar a Indústria 4.0 no início de 2019.
A produção-alvo de legado na Spirit, uma fábrica anterior da Boeing que foi vendida em 2005, era de 21 aeronaves por mês com base em suas limitações físicas e tamanho, disse Ronkles. Antes de sair, a produção mensal da fábrica era de 57 aeronaves, ajudadas com turnos adicionais, mais funcionários e maior automação, especificamente na fixação.
“Um dos (últimos) projetos antes de eu sair foi a coleta de dados da Indústria 4.0 sobre a utilização de equipamentos e isso realmente mudou a face dessa empresa em entender o que seus equipamentos estavam fazendo e o que eram capazes de fazer”, disse Rounkles. “E teve um impacto significativo nos gastos de capital para taxas futuras.”
'Investigando no digital'
Há pesquisas em andamento em todo o mundo sobre a aplicação da Indústria 4.0 na fabricação aeroespacial, mas a adoção é lenta e a produção atual de aeronaves é mais analógica do que digital, disse Russell da AFRL.
“As empresas estão se interessando pelo digital para resolver pontos problemáticos específicos, como rastreamento de ativos, mas poucos fabricantes têm um verdadeiro ambiente da Indústria 4.0 em toda a empresa”, disse ele.
Em termos do estado atual dos componentes da Indústria 4.0, a manufatura aditiva está sendo procurada para ferramentas e peças não estruturais, alguns processos são automatizados com o uso de robôs e, em relação à análise de dados, foi feito P&D para amarrar a inspeção não destrutiva dados de volta aos modelos originais para entender o impacto dos defeitos de fabricação no desempenho da peça, disse Russell.
No vídeo postado no YouTube, um braço robótico Kuka com um rolo no final do braço suaviza a camada de compósito pré-impregnado sobre a camada anterior, enquanto dois robôs com garras mantêm o material esticado em ambos os lados.
Quantos artistas de hand layup desejaram esse equivalente a uma terceira mão que foi demonstrada na gravação da célula robótica inteligente?
A célula, e toda a tecnologia por trás dela, é um projeto de demonstração de Satyandra K. Gupta, professor de engenharia mecânica e ciência da computação da Universidade do Sul da Califórnia, seus colegas e seus alunos. Eles fizeram a parte com base em sugestões da Boeing, Lockheed Martin e United Technologies, com o objetivo de avaliar a viabilidade da automação. Os resultados dos testes em peças feitas com sua automação robótica foram enviados para as três empresas, disse Gupta.
“Neste momento, o principal desafio que todos enfrentam no setor aeroespacial é a falta de mão de obra”, disse ele.
Com braços robóticos fazendo layup, um operador humano poderia supervisionar várias células ao mesmo tempo, explicou ele. Isso não apenas aumentaria a capacidade, como também poderia eliminar a etapa de debulking no processo de fabricação de peças, garantindo a qualidade.
Isso porque, para uma peça hipotética crítica feita de 100 camadas de pré-impregnados, a peça em processo tem que ser ensacada e submetida a aplicação de vácuo a cada três (ou cinco) camadas para garantir que não haja vazios, totalizando 33 debulkings.
Mas com robôs, a pressão da ferramenta robótica pode ser medida, ao contrário da mão humana, então a qualidade é garantida e o processo pode ser mais rápido.
Automatizar o processo não apenas o torna consistente e simplificado. Hand layup é um trabalho tedioso que é fisicamente exigente.
Trabalhando por mais de dois anos e meio, Gupta e sua equipe integraram os braços robóticos com ferramentas de ponta de braço, visão computacional, sensor de força, algoritmos de inteligência artificial, controladores avançados e uma interface homem-máquina. Suas peças de demonstração consistiam em até 15 camadas de fibra de carbono padrão à base de epóxi pré-preg ply.
A parte mais desafiadora de seu trabalho foi integrar a visão computacional em tempo real.
“Você tem que pegar a câmera para ver quais defeitos estão se formando”, disse Gupta. “(Agora) se o robô vê uma ruga às vezes ele vai puxar o lençol para este lado, então para aquele lado…”
Quando o celular encontra um problema que não pode ser corrigido, ele alerta um operador humano com um bipe, e-mail ou texto.
Mas isso só se for necessário.
“Às vezes, todo o processo ocorre sem problemas”, disse Gupta.
Olha, mãe, sem mãos! (As ferramentas de ponta de braço fazem a disposição pré-impregnada automatizada)
A adição Rego-Fix inaugurada há três anos incorpora recursos avançados de conservação de energia e recursos naturais. Estes incluem um sistema especial de ventilação de troca de ar, aquecimento a pellets de madeira, várias unidades de ar condicionado progressivo, um telhado “verde” e o uso de iluminação natural e controlada por sensores.
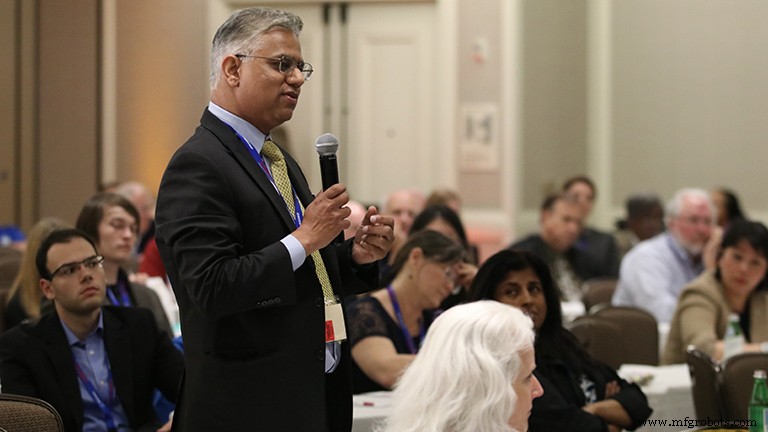
O sistema de ventilação de troca de ar troca o ar dentro do novo prédio sete vezes por hora. Ele extrai o calor residual do chão de fábrica – calor gerado principalmente pelo grande equipamento compressor de ar necessário para as máquinas-ferramentas da empresa. Durante os meses frios, que representam o saldo do ano, o calor residual recuperado é então usado para aquecer o ar fresco de entrada que o sistema extrai do exterior do edifício e circula para o chão de fábrica.
Além disso, a água circulada em um sistema fechado ajuda a manter os compressores de ar do chão de fábrica resfriados durante a operação. No processo de resfriamento, a água fica quente e essa água aquecida é então armazenada em um tanque de 7.007 litros. Esta água é usada para ajudar a aquecer ainda mais o edifício através de um sistema de aquecimento embutido nos pisos das áreas de escritórios do edifício.
A instalação também incorpora um sistema de aquecimento de 390 kW que queima pellets de madeira em oposição aos combustíveis fósseis. Os pellets são um subproduto das indústrias madeireiras e moveleiras, comuns na região. O sistema consome quantidades muito pequenas de pellets porque funciona como reserva às outras fontes de aquecimento e só é utilizado quando as temperaturas exteriores são extremamente baixas.
Durante os verões, um sistema de ar condicionado de três unidades do tipo progressivo com economia de energia, trabalhando em conjunto com o sistema no piso e o sistema de troca de ar, mantém a adição fresca. A unidade de troca de ar retira o calor do edifício e a água fria circula pelo sistema no piso.
Se a temperatura dentro do edifício subir acima de um determinado nível, uma das unidades do sistema de ar condicionado progressivo ligará para fazer backup do sistema de piso e da unidade de troca de ar. As unidades de ar condicionado são reguladas por rpm, portanto, se os níveis de temperatura continuarem a subir, forçando a primeira unidade de ar condicionado a ultrapassar seu limite, a segunda unidade de ar condicionado do sistema será ativada. E, por sua vez, se a segunda unidade atingir seu limite de rpm, a terceira unidade é ativada. Assim que o edifício começar a arrefecer, as unidades de ar condicionado individuais desligam-se na sequência inversa.
As paredes exteriores do edifício são completamente isoladas. Ao contrário dos projetos de telhados típicos, o que a Rego-Fix optou é bastante incomum com altas propriedades isolantes. Referido como um telhado “verde” ou “plantado”, é coberto com solo que tem grama real crescendo nele. Além de seu valor de isolamento, o telhado capta a água da chuva que é então coletada em um tanque de 13.200 gal (50.000 l) e é usada para dar descarga nos banheiros do prédio.
Combinados, todos os recursos de aquecimento e resfriamento do edifício fornecem temperaturas ambientes estáveis e constantes dentro da área de fabricação. Isso tem um benefício crítico de fabricação. A temperatura constante ajuda a manter a precisão consistente da máquina-ferramenta para produzir os sistemas de porta-ferramentas de alta precisão da empresa.
Para maior economia de energia, o novo edifício de fabricação apresenta muitas janelas grandes com isolamento de vidro triplo que permitem a entrada de luz natural abundante. Além disso, as janelas estão equipadas com persianas que abrem e fecham automaticamente. Esta é uma grande ajuda para manter o edifício fresco no verão. Enquanto as cortinas bloqueiam muito calor, elas são perfuradas para deixar entrar a luz.
Onde for necessária iluminação adicional, são usadas luzes de economia de energia do tipo LED, juntamente com a ativação do controle de movimento. Não há interruptores de parede no prédio e as luzes acendem apenas quando as áreas estão ocupadas e desligam quando não estão.
Sistema de controle de automação
- O futuro da automação na indústria da aviação
- Como a automação está atrapalhando todos os tipos de manufatura em 2020
- O papel da robótica e da automação na indústria 4.0
- Automação e indústria da moda:uma revolução silenciosa
- Automação na indústria 4.0
- Demanda global de veículos de passageiros cai 11%, diz pesquisa
- STAEDTLER:o valor da automação na indústria de manufatura
- Demanda por automação, picos de robôs
- Atendendo à grande necessidade de automação de compósitos
- Como os robôs podem ajudar as empresas a atender ao aumento da demanda?