Guia definitivo para melhorar suas causas raízes e processos de ação corretiva (RCCA)
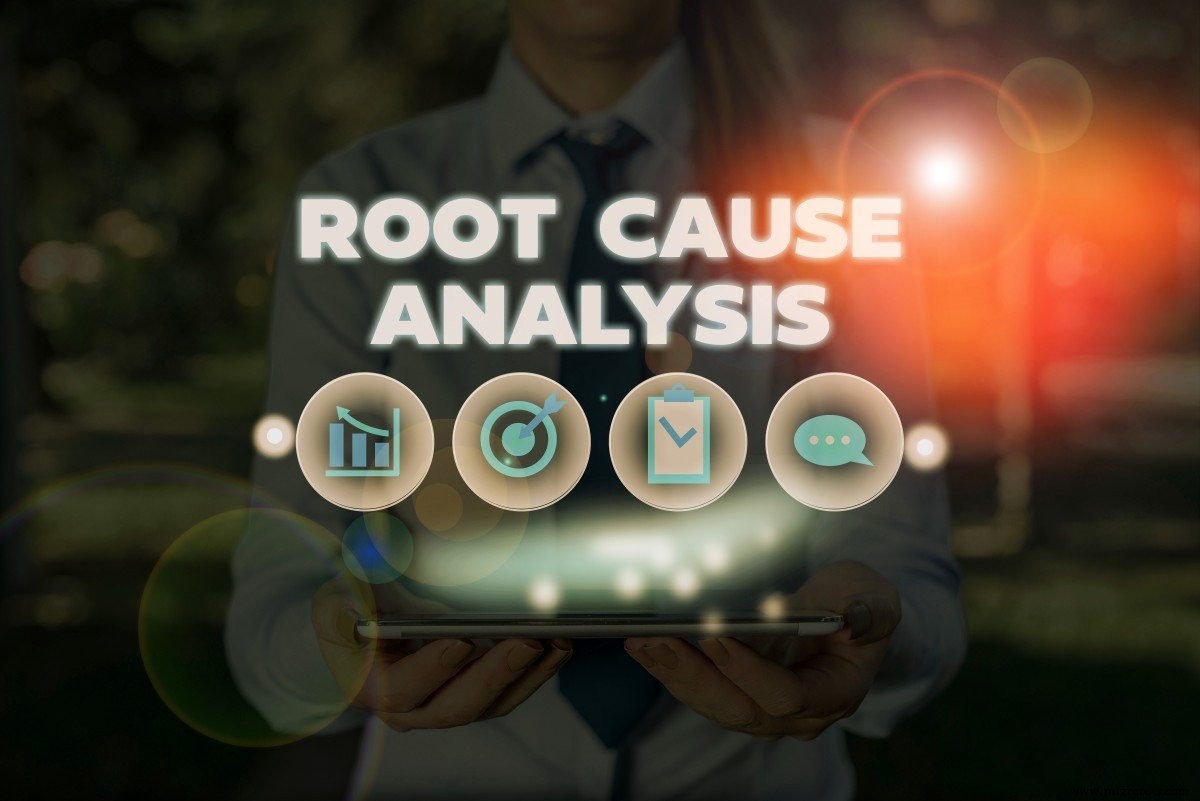.jpg)
Se sua empresa de manufatura desenvolver um problema ao longo do caminho com um de seus processos, como você o resolverá? Embora a opção de atalho seja simplesmente corrigir os sintomas de qualquer que seja esse problema, a solução a longo prazo é executar um processo RCCA.
Ao utilizar essa causa raiz e o processo de ação corretiva, sua organização de manufatura fortalece seus procedimentos internos e externos ao chegar ao cerne do problema em vez de gerenciar suas consequências. Mas o que é RCCA e como você pode implementá-lo em sua organização? Este guia completo tem tudo que você precisa para começar!
Links rápidos:
- O que é RCCA e por que é importante?
- Quando realizar RCCA
- Visão geral do processo RCCA
- Empregando uma abordagem de pensamento sistêmico para o processo RCCA
- Ferramentas de qualidade para utilizar em processos RCCA
- CMTC está aqui para ajudar a desenvolver seu processo RCCA!
O que é RCCA e por que é importante?
RCCA é um processo usado para analisar sistematicamente um problema para determinar suas causas subjacentes. Isso leva à identificação da relação de causa e efeito no processo de fabricação.
Em vez de culpar as pessoas pelos erros, a RCCA visa analisar cada etapa de um procedimento para entender verdadeiramente onde os erros podem surgir, rastrear padrões e muito mais.
Quando realizar RCCA
Sua organização de manufatura deve realizar o RCCA como parte de um plano de ação corretiva ou, quando não realizá-lo, poderá impactar seus níveis de qualidade, entrega ou satisfação do cliente. Alguns grandes clientes costumam fazer disso uma parte obrigatória de seus negócios; por exemplo, o RCCA da Toyota é reconhecido como o melhor da categoria na indústria automotiva.
Os problemas de qualidade devem ser sempre resolvidos em equipe; reúna os especialistas em processos que devem auxiliar neste problema e que possuem uma ampla variedade de habilidades e conhecimentos para fornecer diferentes perspectivas.
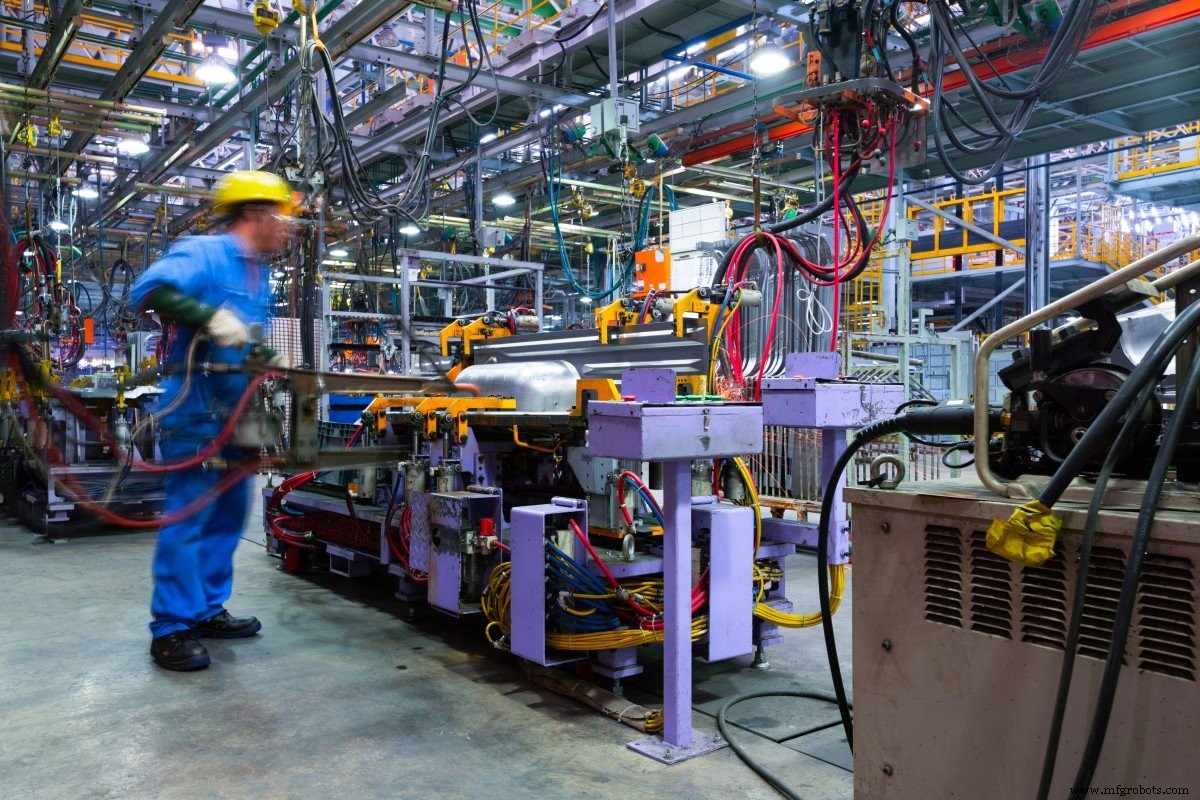.jpg)
Visão geral do processo RCCA
O processo RCCA geralmente segue estas etapas:
- Comece com a declaração do problema
- Confirme “Indo ao Gemba”
- Colete dados para análise
- Formule uma teoria
- Alcance contenção de curto prazo
- Desenvolva teorias para a ação corretiva de longo prazo
- Implementar as ações de longo prazo
- Monitore a solução
- Verifique se tudo está resolvido - não apenas corrigido
- Atualizar documentos relevantes
Antes de mergulhar em cada etapa, no entanto, é importante aplicar uma abordagem de pensamento sistêmico ao processo geral.
Empregando uma abordagem de pensamento sistêmico para o processo RCCA
Muitas vezes, devido à pressão de tempo e cronograma, e outros fatores, parece mais fácil resolver um problema tratando os sintomas, não a causa raiz. No entanto, o mesmo problema se repetirá - e se a Lei de Murphy tiver algo a dizer sobre isso, no pior momento possível. Com o tempo, as causas raízes não resolvidas se acumulam, resultando em uma situação em que se está pulando de uma crise para a outra. Rapidamente se torna uma situação bastante ineficaz e ineficiente.
Em vez disso, tente usar uma abordagem de pensamento sistêmico, listando todos os fatores que criaram a situação, considere o quadro geral, extraia perspectivas de outras pessoas e realmente busque compreender a fraqueza do processo. Essa abordagem é mais lenta e metódica, mas vale a pena o esforço para entender completamente o processo de fabricação e reduzir o número de “incêndios” a longo prazo.
Abaixo está uma visão geral de cada etapa do Processo RCCA:
Comece com a declaração do problema
A declaração do problema deve:
- Concentre-se em um problema estritamente definido
- Seja claro, conciso e factual
- Indique o resultado / consequência
- Descreva o problema em termos mensuráveis
A declaração do problema não:
- Atribua uma causa para o problema
- Descreva como resolver o problema
Essencialmente, você deve ser capaz de definir quem, o quê, quando, onde e como o problema ocorre!
Confirme "Indo para o Gemba"
'Ir para Gemba' é o ato de visitar o chão de fábrica no Lean. Traduzido como 'o lugar real', enfatiza a importância da compreensão da liderança do que está acontecendo em todos os níveis.
Isso envolve:
- Fazendo um passo-a-passo do processo; também conhecido como Genchi Genbutsu, que se traduz como "Vá e veja" ou "Vá ao lugar real para ver as circunstâncias reais"
- Analisando o processo - quais são os pontos fracos?
- Está se perguntando se o problema pode ser duplicado? Se não, o que teria que mudar para que isso acontecesse novamente?
Parte disso também inclui entrevistar os usuários do processo, como pessoal de chão, líderes de produção, supervisores, clientes e fornecedores para revisar procedimentos, métodos, atividades e tarefas.
Colete dados para análise
Depois de definir o problema, você e sua equipe precisam estabelecer por que ele aconteceu. Esta etapa incorpora reunir todos os fatos da situação e processá-los para determinar relações causais. Isso o levará na direção da causa raiz do problema!
Esses fatores a serem considerados incluem:
- Avalie o equipamento: O desempenho e a manutenção da máquina são adequados? Os métodos e procedimentos apropriados estão sendo seguidos? Essas políticas têm detalhes suficientes ou há espaço para erro humano?
- Materiais: Os materiais envolvidos têm o grau ou qualidade adequados? Eles estão sendo armazenados e manuseados adequadamente? Existe alguma evidência de contaminação?
Formule uma teoria
Depois de adquirir os fatos acima mencionados e o contexto do problema, indique a (s) causa (s) potencial (is) da não conformidade e liste todas as tarefas envolvidas no processo de fabricação específico. Formule uma teoria da causa raiz e designe como as informações - data de vencimento, dias, contagem, total, etc. - serão registradas objetivamente.
Revise esses registros; o que essa informação te diz? Você pode identificar possíveis fatores causais? Quais qualidades estão levando ao problema - ambiente de trabalho, fluxo de trabalho, iluminação, treinamento de pessoal, distrações ou outra coisa?
Alcance contenção de curto prazo
Para "estancar o sangramento", você precisará estabelecer ações de contenção. Isso pode envolver a troca de equipamentos, o treinamento de novos operadores e a troca de fornecedores de materiais. A contenção de curto prazo garante que o cliente esteja protegido de ser imediatamente afetado pelo problema; não é uma solução de longo prazo, nem conta como o problema foi resolvido.
.jpg)
Desenvolva teorias para a ação corretiva de longo prazo
Em seguida, selecione e implemente a solução de ação corretiva de longo prazo apropriada. Pode haver várias soluções disponíveis para você; certifique-se de escolher a solução que:
- Eliminará melhor a causa raiz
- É mais econômico
- É o mais apropriado para a magnitude do problema
- Altera efetivamente o processo
A partir desses fatores, identifique a melhor solução classificando-os e atribuindo importância a cada caminho possível. Isso ajudará a determinar objetivamente o melhor curso de ação para sua equipe de manufatura.
Implementar as ações de longo prazo
Depois de selecionar a melhor solução, você precisa implementar essas mudanças! Comece dividindo a solução em tarefas sequenciais e crie uma lista de itens de ação com responsabilidades e datas de vencimento atribuídas a cada membro da equipe pertinente. No entanto, certifique-se de ter um plano de contingência e pergunte a si mesmo o que pode dar errado, como você saberá que algo deu errado e o que pode ser feito para evitá-lo? Essas perguntas não são pessimistas - na verdade, elas demonstram ter iniciativa e se envolver ativamente com o processo RCCA!
Monitore a solução
Monitore o problema para garantir que a não conformidade não ocorra novamente. Se ocorrer novamente, rejeite a causa raiz e implemente uma solução alternativa. Sempre determine se a não conformidade afetou o produto em outra parte da organização ou se algum produto não conforme foi enviado ao cliente. Você vai querer resolver isso com eles o mais rápido possível!
Verifique se tudo está resolvido - não apenas corrigido
Dê tempo suficiente para que o problema ocorra novamente para determinar se você o tratou de maneira adequada. O problema pode não reaparecer por algumas semanas, por exemplo, mas isso não significa que não retornará se as ações corretivas escolhidas não forem duradouras. Verifique se o problema identificado foi resolvido e não ocorre mais; não há limite de tempo oficial, mas sua solução deve funcionar de forma consistente.
Atualizar os documentos relevantes
Revise documentos existentes com a nova solução; certifique-se de revisitar:
- Procedimentos e manuais do usuário
- Especificações das diretrizes
- Manuais de serviço
- Crie novas instruções de trabalho para documentar quaisquer novos processos
- Distribua os novos procedimentos
- Documente o processo RCCA na Solicitação de ação corretiva
Ferramentas de qualidade para utilizar em processos RCCA
Essas ferramentas de qualidade podem ajudar sua organização de manufatura a melhorar seu processo de RCCA:
Histograma
Um histograma é uma representação gráfica que organiza um grupo de pontos de dados em intervalos especificados pelo usuário. Semelhante em aparência a um gráfico de barras, o histograma condensa uma série de dados em um visual facilmente interpretado, pegando muitos pontos de dados e agrupando-os em intervalos lógicos ou compartimentos.
Brainstorming
Brainstorming é uma técnica de criatividade em grupo por meio da qual esforços são feitos para encontrar uma conclusão para um problema específico, reunindo uma lista de idéias espontaneamente contribuídas por seus membros. Seus funcionários podem fornecer informações valiosas sobre o processo de manufatura, portanto, reunir suas informações ao longo do processo de RCCA é importante.
Gráfico de controle
Os gráficos de controle, também conhecidos como gráficos de Shewhart ou gráficos de comportamento do processo, são uma ferramenta de controle de processo estatístico usada para determinar se um processo de fabricação ou de negócios está em estado de controle. Em outras palavras, é um gráfico usado para estudar como um processo muda ao longo do tempo.
Diagrama de dispersão
Um gráfico de dispersão é um tipo de gráfico ou diagrama matemático que usa coordenadas cartesianas para exibir valores para normalmente duas variáveis de um conjunto de dados. Este método de organização de dados pode revelar quaisquer correlações atuais entre as variáveis.
Análise de Pareto
A análise de Pareto é uma técnica formal útil para representar graficamente o impacto de várias causas. Eles são baseados no Princípio de Pareto, também conhecido como regra 80/20. De acordo com o Princípio de Pareto, ao longo do tempo, cerca de 80% dos defeitos, por exemplo, virão de 20% das causas. Portanto, ao coletar e mapear dados, você ganha visibilidade das causas que terão o maior impacto - ao fazer 20% do trabalho, você pode gerar 80% do benefício de fazer o trabalho inteiro.
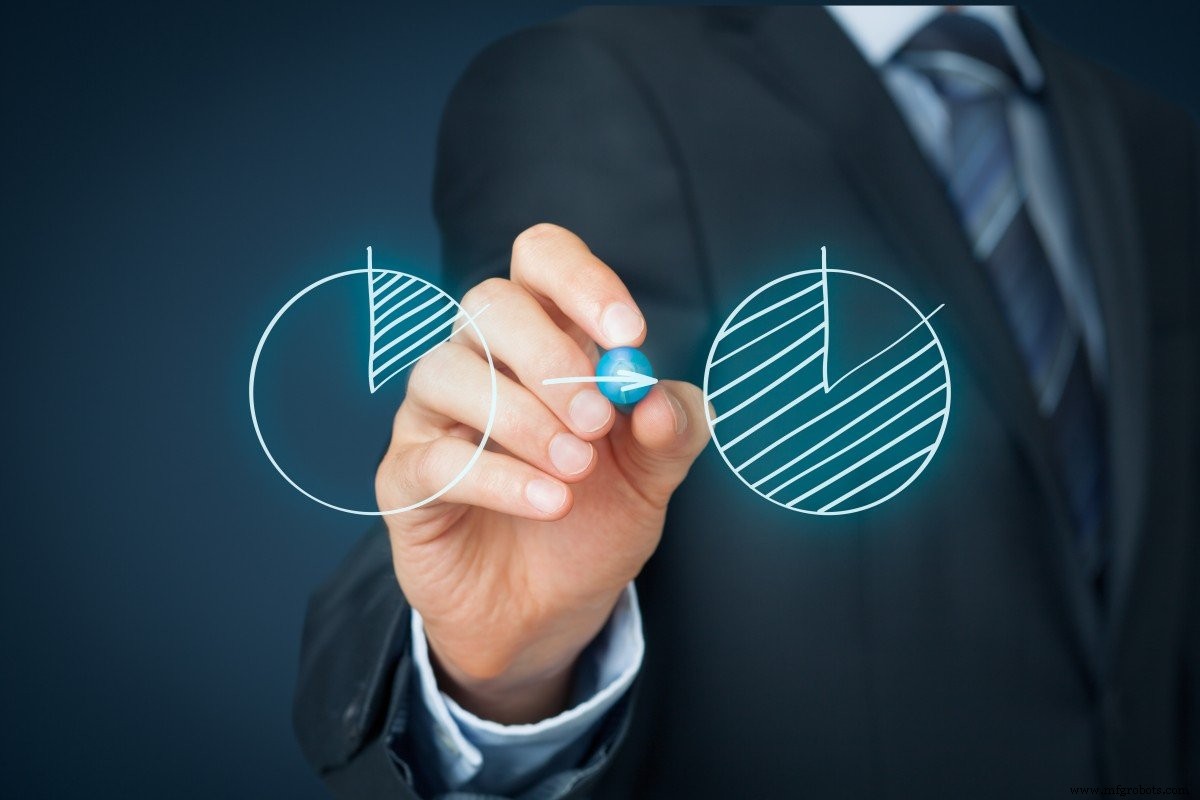
Verifique as planilhas
As folhas de verificação não são complicadas de criar. Mas, estranhamente, são provavelmente as ferramentas de qualidade menos usadas e mais valiosas. Uma folha de verificação é um formulário usado para coletar dados em tempo real no local onde os dados são gerados. Os dados que captura podem ser quantitativos ou qualitativos. Quando as informações são quantitativas, a folha de verificação é às vezes chamada de folha de contagem.
Diagramas de fluxo do processo
Um diagrama de fluxo de processo (PFD) é um diagrama comumente usado em engenharia química e de processo para indicar o fluxo geral de processos e equipamentos da planta. O PFD exibe a relação entre os principais equipamentos de uma instalação da planta e não mostra detalhes secundários, como detalhes e designações da tubulação.
Diagrama de causa e efeito
Às vezes referido como um diagrama de espinha de peixe, os diagramas de causa e efeito são uma ferramenta visual usada para organizar logicamente as possíveis causas para um problema ou efeito específico, exibindo-as graficamente em detalhes crescentes, sugerindo relações causais entre as teorias.
Os 5 porquês
Pergunte por que?" pelo menos 5 vezes; pare quando ir mais longe não agrega mais valor. Quando terminar, adicione a palavra "so" ou "portanto" no final de cada resposta e, em seguida, trabalhe de trás para frente, no topo da página, para confirmar a lógica.
Por exemplo:Por que as luzes se apagaram?
- W1-Por que as luzes se apagaram? O fusível queimou.
- W2- Por que o fusível queimou? O motor superaqueceu e causou um odor de queimado.
- W3- Por que o motor superaqueceu? O rolamento do motor falhou.
- W4- Por que o rolamento do motor falhou? A vedação errada foi instalada e permitiu que o lubrificante vazasse.
- W5- Por que a vedação de rolamento errada foi usada? Foi montado incorretamente.
- W6- Por que o rolamento foi montado incorretamente? O processo de montagem não foi robusto; foi projetado sem pontos de verificação para o operador e não havia instruções de trabalho a serem seguidas.
Diagrama SIPOC
Um diagrama SIPOC (Fornecedores, Entradas, Processo, Saídas, Clientes) é uma ferramenta usada por uma equipe para identificar todos os elementos relevantes de um projeto de melhoria de processo antes do início do trabalho. Ajuda a definir um projeto complexo que pode não ter um escopo bem definido e é normalmente empregado na fase de Medição da metodologia Six Sigma DMAIC (Definir, Medir, Analisar, Melhorar, Controlar). É semelhante e relacionado ao mapeamento de processos e ferramentas "dentro / fora do escopo", mas fornece detalhes adicionais.
Análise FMEA
A análise de efeitos e modos de falha é o processo de revisar tantos componentes, montagens e subsistemas quanto possível para identificar modos de falha em potencial em um sistema e suas causas e efeitos. É um método sistemático e proativo para avaliar um processo para identificar onde e como ele pode falhar e para avaliar o impacto relativo de diferentes falhas, identificando assim as partes do processo que mais precisam de mudança.
Diagrama de concentração
Um diagrama de concentração de defeito é uma ferramenta gráfica útil para analisar as causas dos defeitos do produto ou da peça. É um desenho do produto, com todas as vistas relevantes exibidas, em que as localizações e frequências de vários defeitos são mostradas.
Análise de 8 disciplinas
Este é um método desenvolvido na Ford Motor Company usado para abordar e resolver problemas, normalmente empregado por engenheiros de qualidade ou outros profissionais. Com foco na melhoria de produtos e processos, tem como objetivo identificar, corrigir e eliminar problemas recorrentes.
Existem 8 disciplinas de resolução de problemas:
- Estabeleça a equipe
- Descreva o problema
- Desenvolva ações provisórias de contenção
- Definir e verificar causas raízes e pontos de escape
- Escolha e verifique as ações corretivas permanentes
- Implementar e validar ações corretivas permanentes
- Previna a recorrência
- Reconhecer contribuições individuais e de equipes
O CMTC está aqui para ajudar a desenvolver seu processo de RCCA!
A RCCA apoia a melhoria da qualidade ao promover uma cultura de resolução de problemas de comunicação da equipe, o que resulta em mudança de comportamento e fortalecimento da cultura da empresa. As pessoas aprendem a lidar com as "causas profundas" e não com os sintomas. Essa linha de pensamento promove um envolvimento mais profundo dos funcionários e um empoderamento geral entre seus funcionários!
A CMTC oferece assistência técnica, desenvolvimento de força de trabalho e serviços de consultoria para fabricantes de pequeno e médio porte (SMMs) em toda a Califórnia para ajudar os SMMs a aumentar sua produtividade e competitividade global. Para obter mais informações sobre o CMTC, visite nosso website em www.cmtc.com ou entre em contato conosco pelo telefone 310-263-3060.
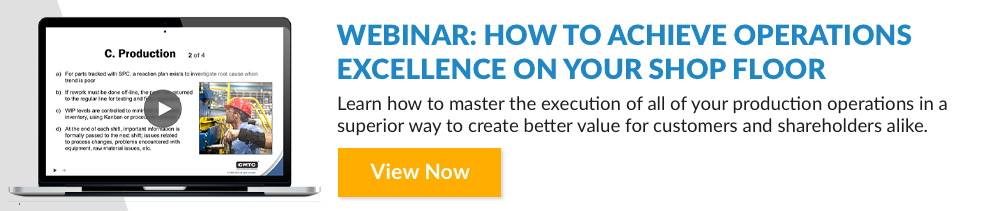
Tecnologia industrial
- Guia para PCBs e IoT
- Seu guia para operação e manutenção de guindastes
- Seu guia definitivo de compra de acoplamentos de motores
- Seu guia definitivo para entender os interruptores de limite
- Seu guia definitivo para os melhores produtos agrícolas industriais
- Seu guia para guindastes duplos e elevação crítica
- Seu guia para marcas de embreagem e freio de guindaste
- Seu guia para comprar um guindaste de torre e peças de fornecimento
- Seu guia definitivo para tipos de guindastes
- Seu guia para gerenciamento de manutenção