Forno Cúpula - Peças, Princípio de Funcionamento, Aplicações
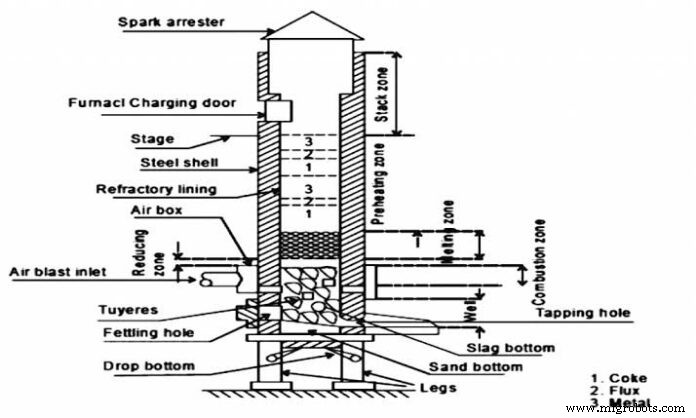
Neste artigo vamos discutir sobre Forno de Cúpula, Partes de Cúpula, Diagrama de Forno de Cúpula, Zonas em Cúpula, Operação de Cúpula.
O objetivo principal na cúpula é produzir ferro de desejo composição, temperatura e propriedades na taxa exigida da maneira mais econômica. Além disso, este forno tem muitas vantagens distintas sobre os outros tipos, por exemplo, simplicidade de operação , continuidade da produção e aumento da produção aliada a um alto grau de eficiência.
Vários tipos de fornos de fusão são usados em diferentes fundições, dependendo da quantidade de metal a ser fundido de cada vez e da natureza do trabalho realizado na oficina. Apenas forno de cúpula usado em fundições para fundir um ferro-gusa de refino junto com a sucata é descrito abaixo.
Partes do forno de cúpula
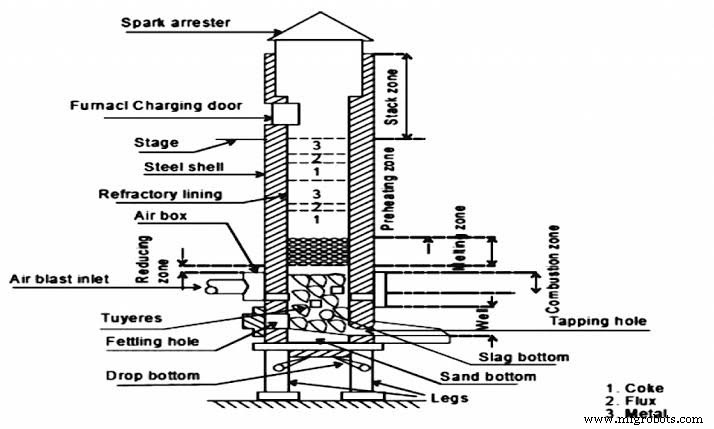
O forno de cúpula consiste em uma chapa de aço cilíndrica vertical, de 6 a 12 mm de espessura, e forrada internamente com tijolos refratários a ácido ou ácido. argila de compactação. Os tijolos refratários ou a argila de compactação utilizados consistem em óxido de silício ácido (SiO2) e alumina (Al2O3). O forro é geralmente mais espesso na região inferior onde as temperaturas encontradas são maiores do que na região superior.
A casca é montada em uma fundação de tijolos ou em colunas de aço. Em um arranjo de coluna de aço, usado na maioria das cúpulas modernas, o fundo do casco é fornecido com portas de fundo de gota através das quais os detritos, consistindo de coque, escória, etc., podem ser descarregados no final da fusão. Nas cúpulas de fundo rebaixado, o fundo de trabalho é construído com areia de moldagem que cobre as portas rebaixadas.
Este fundo inclina-se em direção ao furo metálico situado no ponto mais baixo na frente da cúpula. Oposto este orifício de torneira , e um pouco acima dele, há outro buraco, chamado buraco de escória , o que permite que a escória seja retirada.
Um volume constante de ar para combustão é obtido de um soprador motorizado. O ar é transportado do soprador através de um tubo chamado tubo de vento (entrada de sopro de ar), primeiro para uma jaqueta circular ao redor do invólucro chamada windbox e depois no forno através de várias aberturas chamadas tuyeres que são fornecidos a uma altura entre 450 e 500 mm acima do fundo de trabalho ou do leito da cúpula.
Essas tuyeres são geralmente 4, 6 ou 8 em número dependendo do tamanho da cúpula e podem ser encaixados em um ou mais números de linhas. A área total das ventaneiras deve ser cerca de um quinto a um sexto da área da seção transversal da cúpula dentro do forro ao nível das ventaneiras. Normalmente as ventaneiras têm um tamanho de 50×150 mm ou 100×300 mm. As ventaneiras auxiliares às vezes são fornecidas para aumentar a eficiência da fusão.
Uma válvula é fornecida no tubo de explosão para controlar o fornecimento de ar. Dependendo do tamanho do forno de cúpula, do tipo de ferro fundido e da compacidade da carga, a pressão do ar pode variar de 250 mm a 400 mm de água para fornos de pequeno e médio porte e de 400 mm a 850 mm para forno de grande porte.
Às vezes, um medidor de volume é instalado para saber o volume de ar que passa. A quantidade de ar necessária para fundir uma tonelada de ferro depende da qualidade do coque e da relação coque-ferro. A longa prática prova que são necessários cerca de 800 a 900 m3 de ar para derreter uma tonelada de ferro em um forno de cúpula, supondo que seja usada uma proporção de 10 para 1 de ferro para coque. Para uma relação mais baixa, serão necessários maiores volumes de ar.
Existe uma porta de carregamento através da qual o metal, o coque e o fluxo são introduzidos no forno, situado 3 a 6 m acima das ventaneiras, de acordo com o tamanho da cúpula. Uma grande plataforma ou palco geralmente envolve a cúpula no nível de cerca de 300 mm abaixo da parte inferior da porta de carregamento.
A casca é geralmente continuada por 4,5 a 6 m, acima da porta de carregamento para formar uma chaminé. Na parte superior do forno uma tampa cônica chamada de faísca retida, impede que a faísca saia para o exterior. A faísca retida esfria as faíscas e permite que apenas a fumaça escape da abertura. Às vezes, um forno de cúpula pode ser equipado com um coletor, instalador e precipitação para minimizar a poluição atmosférica.
Zonas no Forno Cúpula
Com base nas reações de combustão, todo o eixo da cúpula pode ser dividido da seguinte forma:
Zona do cadinho :- Fica entre o topo do leito de areia e o fundo das ventaneiras. O ferro fundido é acumulado aqui. Isso também é chamado de poço ou lareira .
Combustão ou zona de oxidação:- Está situado normalmente 150 a 300 mm acima do topo das ventaneiras. Todo o oxigênio no jato de ar é consumido aqui devido à combustão real que ocorre nesta zona. Assim, muito calor é liberado e este é fornecido daqui para outras zonas.
O calor também é desenvolvido devido à oxidação do silício e do manganês. Devido a este alto calor, a temperatura sendo de 1550° a 1850°C, gotas fundidas de ferro fundido caem na lareira. As reações químicas que ocorrem nesta zona são:
C + O2 —–>CO2 + Calor
Si + O2 —–>SiO2 + Calor
2 Mn + O2 —–> 2 MnO2 + Calor
Zona de redução:- Estende-se do topo da zona de combustão até o topo do leito de coque. Nesta zona ocorre a redução de CO2 a CO e a temperatura cai para cerca de 1200°C no leito de coque. Devido à atmosfera redutora, a carga é protegida de qualquer influência oxidante. A reação que ocorre nesta zona é:
CO2 + C (coque) —-> 2 CO-Calor
Zona de fusão:- Começa a partir da primeira camada de carga metálica acima do leito de coque e se estende até uma altura de 900 mm. A temperatura mais alta é desenvolvida nesta zona para a combustão completa do coque e o ferro é então fundido aqui. A temperatura nesta zona é de cerca de 1600°C. Uma considerável captação de carbono pelo metal fundido também ocorre nesta zona de acordo com as seguintes reações:
3 Fe + 2 CO—–>Fe3C + CO2
Zona de pré-aquecimento ou zona de carregamento :- Começa forma acima da zona de fusão e se estende até a parte inferior da porta de carregamento. A zona de pré-aquecimento contém a carga da cúpula como camadas alternadas de coque, fluxo e metal e são pré-aquecidos a uma temperatura de cerca de 1100°C antes de chegar à zona de fusão.
Zona de pilha :- A zona de empilhamento estende-se desde a zona de pré-aquecimento até ao topo da cúpula. Ele transporta os gases gerados dentro do forno para a atmosfera.
Capacidade do Forno Cúpula
A saída de um forno de cúpula é definida como as toneladas de metal fundido obtidas por hora de calor. As capacidades da cúpula (tamanhos) variam de 1 a 15 toneladas (ou até mais) de ferro fundido por hora. O tamanho depende não apenas da área da seção transversal da cúpula, mas também da intensidade do consumo de coque.
Mas a intensidade do consumo de coque entende-se as toneladas de coque queimadas por m2 da área da seção transversal da cúpula em unidade de tempo. Observou-se que 14 cm de área do plano da cúpula queima cerca de 1 kg de coque por hora. O diâmetro da cúpula varia de 1 a 2 m com altura de 3 a 5 vezes o diâmetro.
Funcionamento do Forno de Cúpula
As diferentes etapas envolvidas na operação do forno de cúpula são:
1. Preparação da cúpula
A primeira operação na preparação de um forno de cúpula é limpar a escória e refugo no forro e ao redor das ventaneiras da corrida anterior. Quaisquer pontos ruins ou tijolos quebrados são reparados com uma mistura de argila de fogo e areia de sílica ou ganister. A preparação do fundo de areia na cúpula é iniciada assim que o remendo do forro estiver concluído.
As portas inferiores são levantadas e mantidas nesta posição por suportes de metal. A areia do fundo é introduzida através da porta de carregamento e é compactada bem ao redor do revestimento e na interseção das portas inferiores. Esta camada de areia é construída a uma altura de 100 a 200 mm acima da porta de ferro fundido.
A superfície do fundo de areia é inclinada em todas as direções em direção ao furo de drenagem para que o metal fundido possa ser drenado completamente da cúpula a qualquer momento. Uma abertura de cerca de 35 mm de diâmetro é fornecida para a remoção da escória, e um orifício de torneira é formado em torno de um padrão de madeira com cerca de 20 mm de diâmetro. A cúpula deve ser bem seca antes do disparo.
2. Disparando a cúpula
Ao acender uma fornalha de cúpula, um fogo de lenha é aceso no fundo de areia. Isso deve ser feito 2,5 a 3 horas antes que o metal fundido seja necessário. No topo da madeira acesa, é construída uma cama de coque. Quando a madeira está queimando bem, o coque é despejado no poço por cima em várias porções, certificando-se de que o coque comece a queimar também.
O coque é adicionado a um nível ligeiramente acima das ventaneiras e o jato de ar é acionado em uma taxa de sopro menor que o normal para inflamar o coque. Assim que as manchas vermelhas começam a aparecer no topo do leito de combustível, coque adicional é introduzido na cúpula para atingir uma altura de 700 a 800 mm acima da fileira superior de ventaneiras.
A camada de coque deve estar completamente quente antes de ser finalizada até sua altura final. A altura do leito de coque é determinada usando uma haste de medição que foi preparada para indicar a distância da soleira da porta de carregamento até o topo do leito de coque. A camada de coque que repousa no fundo de areia antes de iniciar o aquecimento é chamada de carga do leito. A quantidade de coque no leito depende da pressão do ar fornecido à cúpula.
A altura da carga do leito ou coque-cama é muito importante para o funcionamento da cúpula; afeta a temperatura, a taxa de fusão e a composição química. Outras coisas sendo iguais, um leito baixo produzirá metal mais frio do que um que é alto.
3. Carregando a cúpula
Assim que o leito de coque é construído na altura correta e inflamado uniformemente, camadas alternadas de ferro-gusa, coque e fluxo (calcário) são carregadas da porta de carregamento até que a cúpula esteja cheia. Sucata adequada também é adicionada junto com o ferro-gusa, para controlar a composição química do ferro produzido. A proporção desta sucata é normalmente de 25 a 50 por cento do peso total do metal vazado.
Quando uma quantidade considerável de sucata de aço é usada junto com o ferro-gusa, uma pequena quantidade, digamos de 2 a 4% de ferromanganês, é usada como desoxidante. O peso da carga de metal deve ser de 10 a 15 por cento da produção horária da cúpula. O objetivo da adição de fluxo é remover impurezas no ferro e proteger o ferro da oxidação, reduzir o ponto de fusão da escória e aumentar sua fluidez para facilitar o descarte. Além do calcário, espatoflúor e carbonato de sódio também são usados às vezes como material fundente.
A quantidade de calcário necessária pode ser de 30 a 40 kg por tonelada de ferro fundido ou 25 por cento em peso de coque carregado. A relação entre o metal fundido e o coque carregado depende de um grande número de fatores. Portanto, não é possível dar recomendações definitivas para essa proporção que pode ser alcançada em diferentes classes de trabalho. A Tabela 11.11 é fornecida apenas como guia e mostra a boa prática média na indústria. Mais comumente é mantido 10:1. Isso significa que 1 tonelada de coque é necessária para derreter 10 toneladas de ferro.
4. Imersão de ferro
Depois que a cúpula estiver totalmente carregada até a porta de carregamento, a carga deve absorver o calor por cerca de 45 minutos. A carga é aquecida lentamente, uma vez que o jato de ar é mantido a uma taxa de sopro menor que o normal (praticamente mantida fechada) durante esse tempo. Isso faz com que o ferro fique encharcado.
5. Jato de ar
No final do período de imersão, a explosão total é ativada. Antes de ligar a detonação, as aberturas das ventaneiras e o furo de drenagem são mantidos fechados. Após a detonação ter durado alguns minutos, digamos cerca de 10 minutos, o metal derretido começa a se acumular na lareira. Quando o metal na cúpula começa a derreter, a taxa de carregamento deve ser igual à taxa de fusão, para que o forno seja mantido cheio durante todo o calor. No final da fusão, o carregamento é interrompido, mas a explosão é mantida até que todo o metal tenha derretido.
6. Batendo e slagging
A primeira batida pode ser feita 40 a 50 minutos após a ativação do jato de ar total. Durante este período, metal suficiente é coletado na lareira acima do leito de areia. Quando a escória se acumula no poço, o orifício de escória é aberto e a escória é escoada, preferencialmente em um bogie para facilitar a remoção. O metal fundido é coletado em conchas e levado para os moldes para vazamento. O mesmo procedimento é repetido até que todo o metal esteja derretido e a operação termine.
7. Fechando a cúpula
Quando a operação termina, a explosão é desligada e o suporte sob a porta inferior é derrubado para que as placas inferiores se abram. Isso permite que os restos da cúpula caiam no chão ou em um balde. Eles são então extintos e removidos por baixo da cúpula.
Geralmente, as cúpulas são operadas continuamente, assim como os altos-fornos, mas são operadas apenas por períodos que possam ser necessários. Em muitas fundições, o período de fusão não excede 4 horas, mas as cúpulas podem ser operadas continuamente por 10 horas ou mais.
Eficiência do forno de cúpula
A eficiência térmica ou de fusão de uma cúpula em porcentagem é expressa como:
(calor utilizado no pré-aquecimento, fusão e superaquecimento) / (calor potencial no coque + calor da oxidação de Fe, Si, Mn + calor no jato de ar) x 100
A eficiência de um forno de cúpula varia de 30 a 50 por cento, dependendo
1. Taxa de coque ou razão de coque expressa como o inverso da razão metal-combustível em porcentagem,
2. Taxa de explosão e
3. Tamanho médio do coque.
Requisitos de ar para o forno de cúpula
Para a combustão completa do combustível no forno de cúpula, são necessários cerca de 8,4 m³ de ar por kg de coque à pressão e temperatura atmosféricas normais. Se a relação farelo/coque for de 10:1, o que é considerado um valor satisfatório, o coque necessário por tonelada de ferro será de 1000/10 kg, ou seja, 100 kg. Assim, o volume de ar necessário por tonelada derretida é>
8,4 x 100 =840 m3.
Para permitir vazamentos, etc., o ar fornecido é geralmente um pouco em excesso, ou seja, cerca de 900 m3 por tonelada de ferro.
Dimensões do Forno Cúpula
As principais dimensões de uma cúpula são selecionadas com base em dados empíricos. Assim, a área da seção transversal A. de uma cúpula depende da produção horária projetada e é determinada pela fórmula
A =π d^2/4 =Q/Q1 m^2
Onde d =diâmetro da cúpula na clara, m, Q =saída projetada da cúpula, toneladas por hora, Q2 =saída específica por m² de área de seção transversal, toneladas por hora. Como regra, Q1 =6 a 8 toneladas por hora.
A altura útil de uma cúpula (distância do eixo das ventaneiras principais até a borda inferior do orifício de carregamento) depende do diâmetro e é projetada de acordo com a razão H:d =de 3 a 5.
A altura do forno da cúpula afeta diretamente a taxa de fusão , consumo de combustível e a temperatura e qualidade do metal fundido . Se for muito alto, o coque pode ser esmagado à medida que a carga cai; se for muito baixo, o metal não é aquecido a um grau suficiente, a tiragem é reduzida e a saída da cúpula é diminuída.
O diâmetro interno da cúpula determina a quantidade de coca consumida e a quantidade de ferro fundido por unidade de tempo. Verificou-se que 14 cm? da área da cúpula queima cerca de 1 kg de coque por hora. Assim, uma cúpula com capacidade de 3 toneladas por hora exigirá (3×100) ou 300 kg de coque por hora, assumindo uma relação metal-combustível de 10:1. A área da cúpula será, portanto, igual a (14×300) ou 4200 cm². O diâmetro interno será então
Raízes quadradas de (4200×4)/π
=73 cm (aprox.)
Encargos do Forno da Cúpula
Se forem desejados produtos de qualidade uniforme, deve-se considerar cuidadosamente a carga da cúpula. Normalmente, vários tipos de ferro-gusa e sucata estão disponíveis para o fundição. Para obter a composição desejada do metal fundido, esses graus precisam ser ajustados e controlados. Uma vez que os vários elementos do metal sofrem mudanças químicas durante a operação de refusão, devem ser dadas concessões para sua perda ou ganho durante a composição da carga. A perda ou ganho de vários elementos é a seguinte.
1. Carbono: O metal fundido pega carbono à medida que passa pelo coque incandescente que forma o leito. Com condições de fusão adequadamente controladas, pode-se esperar um ganho de 0,15%. Enquanto o teor de carbono do metal aumenta devido à absorção de carbono do coque, o mesmo sofre uma pequena perda devido à oxidação.
2. Silício : O silício sofre alguma perda devido à oxidação à medida que as gotas do ferro fundido passam pelas ventaneiras. A perda pode ser de 10 por cento do silício presente na carga.
3. Manganês: O manganês também tem uma tendência a se perder junto com o silício durante a fusão. A perda pode ser de cerca de 15 a 20 por cento do manganês presente na carga.
4. Enxofre: O enxofre é retirado do coque, sucata e fundente, etc. Geralmente, o ganho no teor de enxofre é estimado em cerca de 0,03 a 0,05 por cento.
5. Fósforo: Praticamente não há perda ou ganho no teor de fósforo.
6. Ferro: O próprio ferro também tende a ser oxidado e perdido, mas a perda, que é bem pequena, pode ser considerada de cerca de 3 a 4 por cento.
Isso foi tudo sobre o forno de cúpula, suas zonas, operações e peças. Espero que tenha gostado do artigo. Por favor, dê sua opinião nos comentários abaixo.
Tecnologia industrial
- Sensor de posição do acelerador - Princípio de funcionamento e aplicações
- Sensor RVG - Princípio de funcionamento e suas aplicações
- Sensor de pulso:Princípio de funcionamento e suas aplicações
- Princípio de funcionamento do sensor RTD e suas aplicações
- O que é impressão 3D? Princípio de funcionamento | Tipos | Aplicativos
- Forno Cúpula:Princípio, Construção, Funcionamento, Vantagens, Desvantagens e Aplicação
- Usinagem a Jato Abrasivo - Peças, Princípio de Funcionamento, Aplicação
- Usinagem a Jato de Água - Princípio de Funcionamento, Aplicações, Vantagens
- Folha de dados do Hc06: Introdução à pinagem, recursos, aplicativos e princípios de trabalho
- Princípio de funcionamento do processo de fundição e suas aplicações