Como realizar uma análise de capacidade de fabricação
Os fabricantes enfrentam uma montanha de desafios para produzir os bens que usamos em nossas vidas. E cada um deve enfrentar esses desafios com recursos limitados na forma de capital, conjuntos de habilidades, avanços tecnológicos e muito mais. Os gerentes que orquestram essa arena complexa procuram melhor maneiras de maximizar as ferramentas que têm à sua disposição, entendendo a capacidade de sua fábrica. O melhor uso do espaço de fabricação, materiais, mão de obra e desempenho otimizado do equipamento é fundamental para que as empresas impulsionem a produção eficiente e obtenham a mais alta lucratividade.
Uma análise de capacidade pode ser uma excelente solução para auditar uma fábrica e diagnosticar se há capacidade oculta esperando para ser desbloqueada.
O que é capacidade de fabricação?
O objetivo de todo fabricante é executar suas operações em plena capacidade. Mas o que é capacidade de fabricação? A resposta curta é que a capacidade de fabricação representa o estado em que todos os equipamentos e recursos dentro de uma empresa são utilizados na mais alta taxa de operação para o mix de produtos e o volume que sua indústria exige. Isso significa que todos os processos, desde as operações até a manutenção, são otimizados com uma quantidade definida de recursos e que nenhum tempo de inatividade desnecessário é incorrido. Quando esta condição é atingida, o equipamento atingiu a capacidade total.
Muitos fatores complicam ainda mais a jornada para esse estado ideal. Uma fábrica pode sofrer uma série de perdas de disponibilidade, como falhas mecânicas, onde um tempo valioso é perdido para reparos. Ou eles podem perder uma valiosa capacidade de produção devido a trocas, configurações e ajustes.
A capacidade de fabricação também pode sofrer perdas de desempenho. Isso inclui ações de operadores não treinados ou inexperientes e paradas por atolamentos, marcha lenta, excentricidades. Estes são muitas vezes abordados às pressas com pouca análise sobre o que causou e como evitar que isso aconteça novamente.
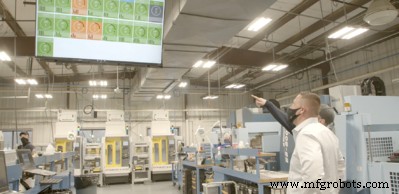
Finalmente, a capacidade de fabricação pode ser impactada negativamente por perdas de qualidade, incluindo defeitos de processo e reduções de rendimento. Algumas causas incluem um fluxo de trabalho sub-otimizado, erros humanos ou um processo interrompido. Além de roubar uma capacidade valiosa de uma fábrica, as perdas de qualidade também podem gerar resíduos adicionais que podem precisar ser retrabalhados ou descartados, aumentando o custo do produto.
Esses obstáculos à capacidade são frequentemente chamados de Seis Grandes Perdas. E seus efeitos podem ser devastadores. Na melhor das hipóteses, a falta de compreensão da capacidade pode desencadear horas extras caras, desperdícios, entregas perdidas ou despesas de capital desnecessárias na forma de novos equipamentos para compensar a perda.
O que é uma análise de capacidade?
Quando um fabricante precisa aumentar a capacidade, eles geralmente começam com as respostas automáticas acima. No entanto, só é possível comprar tantas máquinas e programar tantos turnos antes que o foco na melhoria da capacidade se mova. E a melhor maneira de identificar onde a ação deve ser tomada para aumentar a capacidade está nos dados.
O processo de análise de capacidade é a diferença entre a capacidade potencial e a produção real que uma empresa atinge atualmente. Ao coletar dados de produção, os fabricantes podem identificar qual processo, equipamento ou função precisa ser alterado para aumentar a capacidade. Isso permitirá essencialmente que os fabricantes gerem maior utilização de seus recursos existentes por meio da otimização do processo.
Leitura adicional:Como aumentar a capacidade de produção de manufatura
Como realizar uma análise de capacidade de fabricação
As empresas que realizam uma análise da capacidade de fabricação são capazes de reduzir o tempo de inatividade e o desperdício. Eles também podem minerar os dados para otimizar processos e otimizar fluxos de trabalho. Isso pode ajudá-los a entender quais são as restrições existentes e tomar decisões em tempo real para resolver problemas à medida que eles acontecem. À medida que os dados dão suporte a essas soluções, os gerentes podem promover melhorias em toda a operação e aumentar a capacidade sem investimento adicional em equipamentos ou mão de obra. Para empresas que desejam melhorar sua capacidade de fabricação, aqui estão as etapas necessárias para desbloquear a capacidade existente:
Dados comparativos
Se você não sabe onde está, não vai ver para onde está indo. É comum superestimar a utilização atual dos equipamentos, pois muitas empresas podem nem perceber que a utilização é tão baixa quanto é.
O benchmarking inclui determinar a capacidade existente. A velocidade da máquina, as perdas de qualidade, o tempo de inatividade por categorias – como quebras, trocas e perdas de desempenho – devem ser medidos para determinar a capacidade atual. E, em muitos casos, esse número é chocante. Várias práticas recomendadas podem ser usadas para criar uma estrutura sólida e prática para benchmarking:
- Reuniões internas:uma reunião inicial interna ajuda a definir as expectativas e garante que todos estejam na mesma página. Ao reunir a equipe certa, todos saberão qual deve ser a meta de utilização.
- Verificando os dados:há momentos em que os dados atuais relatados dizem pouco sobre o status real da máquina. Pode estar registrando incorretamente o status ou pode ser contagem de peças, tempo de inatividade ou algum outro parâmetro. Certificar-se de que os dados são verdadeiros ajudará a analisar o que precisa ser feito.
- Avaliando dados:é aqui que as premissas originais são comparadas com a utilização atual real. Ele representa um novo ponto de partida sobre quais melhorias podem ser feitas.
- Planejamento:ao criar um plano de melhoria, os gerentes podem reunir as partes das expectativas originais, o estado real da capacidade orientada por dados e quais melhorias podem ser feitas.
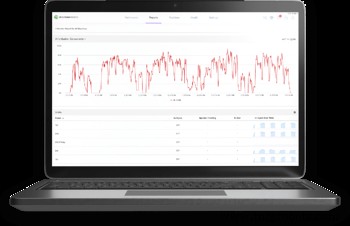
Um exemplo de relatório de utilização do MachineMetrics, um dos muitos relatórios pré-criados que podem ser usados para dados de comparação.
Analisar o tempo de inatividade
Depois que uma operação de fabricação compara seus dados e entende sua verdadeira utilização, uma análise de tempo de inatividade deve ser conduzida. Isso envolve gerentes, técnicos, engenheiros de fabricação, operadores e outros que podem ajudar a identificar todos os motivos do tempo de inatividade e planejar como reduzi-lo ou eliminá-lo.
Com as revelações que acompanharam o benchmarking da instalação, os membros da equipe podem passar a medir o tempo de inatividade que impulsiona essa utilização. Ao responder quanto tempo de inatividade está ocorrendo e em qual categoria o tempo de inatividade se enquadra, as etapas para melhoria se tornam mais aparentes. Isso é feito melhor pelo software automatizado de coleta de dados de máquina para garantir que dados precisos sejam usados, padronizados e em tempo real.
O tempo de inatividade também deve categorizar os motivos do tempo de inatividade. As categorias a serem consideradas podem incluir:
- Tempo de inatividade planejado x não planejado:cada um tira uma máquina de serviço, mas ambas têm abordagens bastante diferentes para minimizar ocorrências e colocar a máquina novamente on-line.
- Erro humano ou ação do operador:em um ambiente de fabricação grande e complexo, os operadores podem ter diferentes níveis de treinamento ou podem executar tarefas ou ações em uma ordem que reduz a eficiência. Muitas vezes, eles podem ser identificados e verificados por meio da análise de tempo de inatividade.
- Qualidade Fallout:Qualidade é uma categoria ampla que deve ser incluída na análise de tempo de inatividade. Isso pode levar a insights sobre treinamento, estado e manutenção da máquina, qualidade do fornecedor de entrada ou até condições ambientais dentro da instalação entre dias mais quentes e noites mais frias.
Depois que as categorias são determinadas, os membros da equipe podem detalhar para determinar os motivos do tempo de inatividade dentro da categoria. Por exemplo, pode haver muitos tipos de tempo de inatividade planejado, incluindo manutenção programada, produção sazonal e outros.
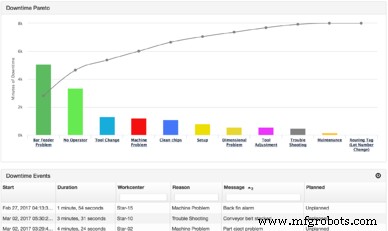
O MachineMetrics Downtime Pareto revela os motivos mais flagrantes de downtime e é um ótimo ponto de partida para encontrar processos para melhorar.
Da mesma forma, existem inúmeras razões para o tempo de inatividade não planejado. Estes podem variar de material que não está na máquina quando necessário a uma máquina com manutenção inadequada. Também pode apontar para um fluxo de trabalho mal projetado, onde o material do upstream não está pronto quando necessário, criando um efeito dominó.
O mesmo vale para o erro humano. As operações de fabricação estão se tornando mais automatizadas, mas ainda há necessidade de mão de obra. Fadiga, treinamento inadequado, falta de compreensão sobre o fluxo de trabalho ou etapas quebradas do processo podem significar que os trabalhadores cometem erros que de outra forma não cometeriam.
A melhor maneira de coletar essas informações é por meio de automação e software. Ao tornar a visualização de dados intuitiva e fácil de registrar, os operadores podem utilizar um painel para inserir dados reais e ver seu impacto. Assim como um operador pode inserir os motivos do tempo de inatividade, ferramentas como os gráficos de Pareto podem ajudar a entender a análise do tempo de inatividade à medida que avança. Isso fornece insights aos usuários e geralmente ajuda a acionar sugestões de melhoria.
Ao final da análise do tempo de inatividade, os custos reais do tempo de inatividade e seu impacto no resultado final podem ser determinados. Isso também ajuda a identificar os “frutos mais fáceis”, os itens mais rápidos e fáceis de consertar com o impacto mais significativo nos dólares economizados e na capacidade adicionada.
Leitura adicional:Como rastrear e analisar o tempo de inatividade da máquina
Mudanças no processo de implantação
Os gerentes agora estão equipados com dados precisos e verificáveis que impulsionam mudanças reais neste ponto da análise de capacidade. Essas alterações podem ser usadas para lidar com as restrições de capacidade mais significativas, desbloquear a capacidade oculta para eliminar horas extras, reduzir a necessidade de despesas de capital e aprimorar um programa de manutenção que funcione em sincronia com as trocas e outras condições operacionais, em vez de contenção com elas.
Há muitos exemplos de drenos significativos na capacidade. Aqui estão alguns que podem ser encontrados durante a maioria das transformações digitais:
Tempo de ciclo esperado maior que o tempo de ciclo real
O tamanho e a complexidade dos ambientes de fabricação atuais podem significar que o desempenho individual está enterrado sob uma montanha de dados, volume e um impulso para maior produção. Quando os dados são verdadeiros e as contagens de peças na máquina são precisas, os operadores são responsáveis por sua produção em vez de ficarem enterrados sob ela. Esta responsabilização pode ser uma ferramenta positiva que lhes permite fazer parte da identificação de áreas de melhoria. À medida que as melhorias no tempo de inatividade mais aparente começam a funcionar, a otimização adicional do tempo de ciclo pode ser iniciada para continuar o processo e incluir até mesmo pequenas alterações que se somam rapidamente.
Problemas de qualidade
Como mencionado anteriormente, a qualidade é um tema amplo que impacta muitas áreas. Mas isso oferece mais oportunidades de melhoria. A regra 80/20 não se aplica apenas à qualidade, mas também afeta as subcategorias dentro dela, incluindo erro humano/treinamento, qualidade do fornecedor, melhorias na manutenção, design do produto etc. o culpado em cada área pode passar por etapas de melhoria para gerar um impacto cumulativo mais considerável na qualidade geral. À medida que esses esforços se consolidam, a capacidade aumenta, a qualidade melhora, reduz custos e melhora o desempenho de pedidos e entregas.
Leitura adicional:Garantia de qualidade na fabricação:tudo o que você precisa saber
Com o MachineMetrics, você pode ver facilmente os principais motivos pelos quais as peças são rejeitadas e identificar a raiz do problema.
Falha de equipamento
Poucas coisas enlouquecem tanto os gerentes de manufatura quanto a falha do equipamento. E muitas vezes, essas falhas são o resultado de um programa de manutenção reativa. Ao funcionar até a falha ou pelo rastreamento inadequado do estado da máquina, as empresas cedem grandes quantidades de capacidade na forma de tempo de inatividade. Mas a análise de dados e as condições da máquina em tempo real oferecem novas oportunidades para aumentar a capacidade. Ao entender os estados da máquina e implantar sensores e tecnologia IIoT, os gerentes podem deixar a manutenção reativa para trás e aumentar a capacidade e reduzir os custos. Um estudo da Deloitte mostra que os programas de manutenção preditiva podem aumentar o tempo de atividade dos equipamentos em 10-20%.
Fluxo de trabalho
Medir a utilização do equipamento é mais do que simplesmente medir apenas a máquina. Ao capturar, contextualizar e analisar dados, os gerentes podem visualizar uma máquina individual e todo o ecossistema de equipamentos dentro da instalação. Isso pode levar a insights sobre o layout do equipamento, preparação, WIP e outras variáveis relacionadas ao processo que podem ser usadas para aumentar a capacidade. Embora possa apontar para a necessidade de reorganizar um piso ou célula de produção, também pode ser tão simples quanto mover algumas máquinas alguns metros ou alterar a maneira como o material flui de uma estação para a próxima dentro do fluxo de trabalho que faz a diferença.
Desbloquear a capacidade oculta
Uma análise de capacidade combinada com captura e análise avançada de dados pode ajudar as empresas a encontrar seu caminho para a capacidade total mais rapidamente do que a maioria imagina e levar a uma produção nivelada. Quando a Avalign Technologies lutou para rastrear o OEE e o tempo de inatividade, gargalos de produção, SOPs inadequados e outros fatores prejudicaram a capacidade.
Usando MachineMetrics, a Avalign adquiriu visibilidade instantânea em todo o chão de fábrica para obter um aumento de 25-30% no OEE e milhões em capacidade adicional, sem a adição de mão de obra, equipamentos ou recursos adicionais.
Assista ao estudo de caso em vídeo:
Tecnologia industrial
- Como se tornar um campeão digital em manufatura
- Como iniciar um projeto de análise de dados na manufatura
- Como o planejamento de capacidade alimentado por AI está mudando o cenário de fabricação - uma perspectiva de throughPut
- O que é a análise da árvore de falhas e como realizá-la
- Como implementar um programa de aprendizagem de manufatura
- Como a energia sem fio está transformando a manufatura
- Qual é a importância da indústria da Filadélfia?
- Como usar o rastreamento de lote na fabricação
- Como conduzir uma análise de gargalo
- Como aumentar a capacidade de fabricação com máquinas usadas