Escória de alto forno e seu papel na operação do forno
Escória de Alto Forno e seu Papel na Operação do Forno
A importância da escória de alto-forno (BF) para o bom funcionamento do BF é ilustrada pelo velho ditado “se você cuidar da escória, o forno cuidará do resto”. Tem havido uma tremenda quantidade de trabalho feito na escória BF estudando as propriedades, mecanismos de formação e impactos nas operações do forno. Uma escória de boa qualidade é necessária para a produção de metal quente de boa qualidade no BF.
A prática de escória de BF é necessária para atender a certos requisitos para uma operação eficiente de BF. Esses requisitos incluem (i) absorver todos os componentes não voláteis não reduzidos da carga e removê-los do BF, (ii) ser líquido de baixa viscosidade, (iii) ser capaz de absorver o enxofre contidos principalmente nos combustíveis, (iv) deve conter a menor quantidade possível de óxido de ferro para aumentar o rendimento do metal quente, (v) seu volume deve ser o menor possível sem afetar a dessulfuração, ( vi) a faixa de temperatura em que os componentes de carga se tornam coesos deve ser estreita para garantir melhor permeabilidade da coluna de carga e (vii) sua qualidade deve ser tal que possa ser processada em material vendável. Esses requisitos são em parte complementares e em parte mutuamente exclusivos. Por isso, é necessário estabelecer prioridades.
Felizmente, existem relações gerais que fornecem uma visão mais prática da natureza das escórias que podem ser usadas no dia a dia. É importante, no entanto, ter uma compreensão básica da natureza fundamental da escória BF para entender as relações gerais.
Fundamentos da escória BF
Os fundamentos da escória BF são complexos. Em cerca de 40%, o oxigênio é o maior elemento individual na escória. A escória é, portanto, um sistema de óxido e de natureza iônica. Devido à natureza do processo BF, a formação da escória é um processo de várias etapas que envolve mudanças consideráveis na composição e temperatura. Os quatro componentes primários da escória BF são SiO2 (sílica), CaO (cal), MgO (magnésia) e Al2O3 (alumina). Esses quatro componentes da escória BF formam numerosos compostos que resultam em uma ampla gama de propriedades químicas e físicas. Os componentes menores da escória são de particular interesse no que diz respeito à química do metal quente e o controle do forno aumenta a complexidade das propriedades físico-químicas da escória.
Os fundamentos da escória de BF incluem questões relacionadas ao processo de BF. Essas questões incluem a formação da escória, o fluxo na fornalha, a estrutura molecular da escória e como a estrutura relaciona os índices químicos conhecidos como basicidade, solidificação da escória e o impacto das mudanças do estado térmico do forno na composição da escória.
Formação de escória – BF é um reator pressurizado, de troca de calor em contracorrente, refluxo, gás-sólido-líquido, reator de leito empacotado. Possui três funções primárias, a saber (i) redução de óxidos de ferro a ferro metálico (ii) fusão do ferro metálico e óxidos, que prevê a (iii) separação das impurezas da carga e combustível do ferro líquido. Estas características do processo conduzem à divisão do forno em três zonas verticais em relação às escórias (i) nomeadamente (i) zona granular, (ii) zona de formação de escória e (iii) zonas de fornalha. Essas três zonas e algumas reações específicas para cada zona são dadas na Fig 1.
Fig 1 Zonas de alto-forno e reações de zona
A zona granular está localizada na parte superior do forno onde todos os componentes carregados estão em fase sólida. A zona granular é delimitada pela linha de estoque na parte superior e pelo início da formação das fases líquidas, a zona coesiva, na parte inferior. À medida que a carga desce pela zona granular, ela é aquecida pelos gases da parte inferior do forno e parte da redução dos óxidos de ferro é realizada. A quantidade de redução que ocorre na zona granular é uma função da natureza dos materiais de suporte de ferro, distribuição de carga e composição do gás e padrões de fluxo.
A zona de formação de escória começa na zona coesiva, onde começa o amolecimento da carga, e continua até abaixo da elevação da ventaneira. A zona de formação de escória inclui, portanto, a zona coesiva, a zona de coque ativo, o homem morto e a pista. A escória formada na parte superior da zona de formação de escória é chamada de escória ‘bosh’ ou ‘primária’, e a escória que sai da zona na parte inferior é a escória ‘lar’. A escória primária é normalmente considerada composta por todos os componentes da escória de carga, incluindo os óxidos de ferro não reduzidos na zona granular, mas não inclui as cinzas do coque ou do carvão injetado. A composição da escória muda à medida que desce no forno devido à absorção das cinzas de coque e carvão, enxofre e silício do gás, e a redução do óxido de ferro. A temperatura da escória aumenta da ordem de 500 graus C à medida que desce até a elevação da ventaneira. Essas mudanças na composição e temperatura podem impactar consideravelmente as propriedades físicas da escória, especificamente a temperatura liquidus e a viscosidade.
A terceira zona é a camada de escória na lareira do forno. A escória produzida na zona de formação de escória se acumula na camada de escória, preenchendo os vazios no coque da lareira e “flutuando” na camada de metal quente. O metal quente passa através da camada de escória para alcançar a camada de metal quente. A alta área de superfície entre o metal quente e a escória à medida que o metal quente passa pela camada de escória melhora a cinética das reações químicas. Essas reações resultam em mudanças consideráveis na química do metal quente. Em particular, os teores de [Si] e [S] antes de entrar na camada de escória são muito maiores do que os da camada de metal quente. A formação de escórias na zona de formação de escória é muito específica do forno devido ao impacto das propriedades de carga e operação do forno.
Estrutura de escória – A conceituação da estrutura da escória (Fig. 2) é baseada na estrutura formada pela sílica. No nível molecular, o átomo de silício está localizado no centro de um tetraedro cercado por quatro átomos de oxigênio, um átomo de oxigênio em cada vértice do tetraedro, como mostrado na Figura 2a. Cada átomo de oxigênio está ligado a dois átomos de silício e, portanto, cada átomo de oxigênio é um vértice de dois tetraedros. O compartilhamento de átomos de oxigênio resulta em um polímero ou rede em três dimensões no estado cristalino onde todos os cantos são compartilhados (Fig. 2b). À medida que a sílica é aquecida, algumas das ligações dos cantos são quebradas, mas a natureza polimérica da estrutura é mantida mesmo quando fundida, como mostrado na Figura 2c.
Fig 2 Conceitualização da estrutura da escória
A adição de óxidos metálicos, como CaO e MgO, quebra a estrutura do polímero. Esses óxidos atuam como doadores de oxigênio, substituindo um átomo de oxigênio em um canto de um tetraedro e quebrando a ligação tetraedro-tetraedro nos cantos (Fig. 2d). A quebra da estrutura do polímero continua com a adição de mais óxidos metálicos até que a razão molar de óxidos metálicos para sílica seja igual a dois, ponto em que todas as ligações tetraedro-tetraedro nos cantos são quebradas (Fig. 2e). A razão molar de dois é a composição de orto-silicato, 2CaO-SiO2, 2MgO-SiO2 e CaO-MgO-SiO2. O Al2O3 atua de maneira semelhante ao SiO2 na formação de polímeros e na aceitação de átomos de oxigênio de óxidos básicos. Óxidos que aceitam oxigênio, SiO2 e Al2O3, são denominados como óxidos ácidos. Os óxidos que doam oxigênio, CaO e MgO são denominados óxidos básicos.
Basicidade da escória – É muito útil ao relacionar as propriedades de um sistema multicomponente à sua composição para desenvolver um índice baseado na composição. O problema no desenvolvimento de um índice é como refletir o significado de cada componente do sistema no índice. A natureza diferente dos óxidos ácidos (A) e óxidos básicos (B) tem sido utilizada no desenvolvimento de índices de composição da escória, normalmente denominados basicidades. Exemplos de índices de basicidade que foram desenvolvidos são (i) bases em excesso ={(CaO) + (MgO)} – {(SiO2) + (Al2O3)}, (ii) basicidade (B/A) ={(CaO) + (MgO)} / {(SiO2) + (Al2O3)}, (iii) razão de sino ={(CaO) + 0,7(MgO)} / {0,94(SiO2)+ 0,18(Al2O3)}, e (iv) basicidade óptica ={(CaO) + 1,11(MgO) + 0,915(SiO2) + 1,03 (Al2O3)} / {(CaO) + 1,42(MgO) + 1,91(SiO2) + 1,69(Al2O3)}.
Os índices de basicidade podem ser agrupados em categorias gerais, a saber (i) diferenças entre a quantidade de bases e ácidos, conforme mostrado na equação (i) acima, (ii) razões de bases para ácidos com base nas porcentagens em peso, conforme mostrado na equação (ii) acima, (iii) razões de bases para ácidos com base nas concentrações molares, conforme mostrado na equação (iii) acima, e (iv) soma da basicidade de cada componente e sua concentração molar, conforme mostrado na equação (iv) acima. Como seria de esperar com base na descrição anterior da estrutura da escória, aqueles índices que refletem a natureza molecular da composição da escória, as equações (iii) e a equação (iv) tendem a ser melhores preditores das propriedades da escória. No entanto, como o índice definido pela equação (ii) é provavelmente a definição mais utilizada.
Impacto da temperatura – [Si], basicidade e volume de escória – Há aumento da quantidade de [Si] com o aumento da temperatura do gusa no BF conforme mostrado na Fig 3. A quantidade de [Si] aumento para um dado aumento de temperatura varia de forno para forno, mas a tendência é a igual para todos os fornos. À medida que o [Si] aumenta, o (SiO2) diminui e, portanto, a basicidade aumenta e o volume da escória diminui. A quantidade de aumento na basicidade para um aumento específico em [Si] é uma função do volume de escória. A Fig. 3a mostra a mudança em B/A para volumes iniciais de escória de 200 kgs/tHM (quilogramas por tonelada de metal quente) e 300 kgs/tHM e para a relação [Si] e temperatura do metal quente dada na figura. A tendência normal demonstrada aqui é que quanto maior o volume de escória, menor é a mudança em B/A para a mesma mudança em [Si] ou temperatura do metal quente.
Fig 3 Impacto da temperatura e solidificação da escória
solidificação de escória – A definição comum de temperatura de fusão só se aplica a um sistema de componente único, como a água, onde somente água líquida existe acima da temperatura de fusão e somente água sólida existe abaixo da temperatura de fusão. A escória é um sistema multicomponente e, portanto, não possui a definição comum de temperatura de fusão, exceto em composições específicas. A maioria das composições de escória tem fases sólidas e líquidas presentes em uma faixa de temperaturas. A temperatura mais baixa na qual existe apenas a fase líquida para uma composição específica é chamada de temperatura liquidus.
A Fig. 3b mostra o caminho de solidificação de uma escória ilustrado no diagrama de fases simplificado. Comece com escória de composição Ccomeça em temperaturas onde existe apenas escória líquida. À medida que a escória esfria, descendo verticalmente no diagrama, a composição da escória líquida não muda até a interseção com a “linha líquida”. A interseção com a ‘linha liquidus’ é a temperatura liquidus para a composição Cstart. Uma quantidade muito pequena do composto sólido se forma na temperatura liquidus à esquerda. Três mudanças continuam à medida que a temperatura é reduzida ainda mais abaixo da temperatura liquidus, ou seja, (i) mais do composto sólido é formado, (ii) a quantidade de escória líquida diminui e (iii) a composição da escória líquida muda, movendo-se para o mesmo ao longo da 'linha líquida'. No exemplo, onde o composto formado é 2CaO.SiO2, a basicidade da escória líquida diminui à medida que a escória é resfriada, pois 2CaO.SiO2 contém cerca de duas vezes mais CaO que SiO2.
O caminho de solidificação mostra como um composto pode ser formado mesmo quando a composição da escória líquida é consideravelmente diferente da composição do composto. A razão em peso de CaO para SiO2 =1,86 para o composto silicato de dicálcio, 2CaO.SiO2. Embora nenhum BF tenha sido operado com sucesso usando escórias com CaO a SiO2 próximo a 1,86, quantidades consideráveis de silicato de dicálcio podem ser formadas nas escórias de BFs em operação. A formação de silicato dicálcico suficiente resulta em uma escória sólida que se decompõe em pó após o resfriamento, conhecida como escória de "queda" ou "poeira". A quebra é causada pela expansão do volume de 10% do silicato de dicálcio à medida que passa por uma mudança de fase a 675 graus C. A diretriz relatada para evitar uma escória 'queda' é (CaO) inferior a 0,9 (SiO2) + 0,6 ( A2O3) + 1,75(S).
É importante lembrar que os diagramas de fase são baseados em condições de equilíbrio. As condições de equilíbrio implicam que a taxa de resfriamento é lenta em relação à taxa das reações, como a formação de silicato dicálcico. O caminho de solidificação descrito acima é "desviado" se a taxa de resfriamento for muito alta como na granulação da escória e, em menor grau, na peletização da escória. O resfriamento rápido bloqueia a composição em uma fase de vidro sólido, onde a cinética das reações é muito lenta para a formação dos compostos.
Fluxo de escória na lareira – O controle do nível de escória na fornalha é importante para manter a operação estável do forno, principalmente porque as taxas de produção de gusa foram aumentadas. Altos níveis de escória resultam no aumento da pressão de explosão e no funcionamento da parede bosh, e interrompem a descida uniforme da carga. Um dos problemas no controle do nível de escória é o fluxo de escória na fornalha durante o rosqueamento. Na lareira, o fluxo de escória para o furo da torneira é mais difícil do que o fluxo de metal quente para o furo da torneira. O fluxo de metal quente tem uma força motriz maior devido à maior densidade do metal quente em comparação com a escória. Acredita-se que o caminho do fluxo de metal quente seja principalmente através de regiões "livres de coque" abaixo e/ou ao redor do coque de homem morto. O caminho do fluxo de escória para o furo da torneira é através do coque deadman.
A Fig. 4 mostra a configuração da fornalha e uma possível sequência de etapas da fornalha durante a extração que levam a uma condição falsa da fornalha seca no final da extração. Acredita-se que a superfície do metal quente permaneça relativamente plana em toda a área da fornalha ao longo do rosqueamento devido à alta densidade do metal quente e ao caminho “livre de coque” para o orifício da torneira. A superfície da escória pode ser consideravelmente mais baixa na região ao redor do furo da torneira do que em outras regiões da fornalha. Quando a taxa de vazamento de escória é maior do que a taxa de fluxo de escória através da fornalha para a região do furo da torneira, ocorre um esgotamento da escória na região do furo da torneira e a superfície da escória começa a se curvar em direção ao furo da torneira, como mostrado na etapa 4 do Fig 4. O esgotamento da escória continua até que não haja escória no furo da torneira e o forno pareça estar seco quando ainda houver escória considerável remanescente na fornalha, conforme mostrado na etapa 5 da Fig 4. Minimizando a resistência ao fluxo de escória em a fornalha minimiza a escória que permanece na fornalha no final de uma rosqueamento. A resistência ao fluxo de escória na fornalha é reduzida à medida que a porosidade do leito de coque da fornalha aumenta e a viscosidade da escória é reduzida.
Fig 4 Configuração da fornalha e uma possível sequência de etapas da fornalha durante a rosqueamento
Sistema de óxido
Cerca de 95% da escória consiste em SiO2, CaO, MgO e Al2O3. O requisito de baixa viscosidade pode ser atendido por uma variedade de componentes neste sistema quaternário. Ignorando a presença de MgO, o diagrama de fases do sistema óxido ternário CaO-Al2O3-SiO2 (Fig. 5) mostra uma região de baixa temperatura de fusão que é paralela ao binário CaO-SiO2 com baixo teor de Al2O3. Esta região se estende desde o alto teor de SiO2 até a isoterma de saturação para 2CaO.SiO2 e então para teor de CaO essencialmente constante em direção ao alto teor de Al2O3. O teor de MgO da escória não afeta substancialmente a posição relativa da região de baixa temperatura de fusão e afeta apenas os valores absolutos das temperaturas de fusão.
Fig 5 Diagrama de fases do sistema de óxido CaO-Al2O3-SiO2
O sistema óxido que constitui a base das escórias BF é o sistema cal-sílica-alumina (CaO-SiO2-Al2O3) modificado devido à presença de certa porcentagem de MgO na escória. A Fig. 6 mostra o diagrama de fases do sistema CaO-Al2O3-SiO2-10% MgO.
Fig 6 Diagrama de fases do sistema CaO-Al2O3-SiO2-10% MgO
As composições de escórias de BF encontradas em várias condições de operação são mostradas na Fig 7. A dessulfurização do metal quente aumenta com a basicidade da escória, ou seja, com o aumento do teor de CaO e/ou MgO, a região 1 na Fig 7 pode, portanto, ser usada apenas para processamento de baixa carga de enxofre. Como os constituintes da ganga normalmente formam uma escória de baixa basicidade, a região 1 representa em grande parte a composição da escória sem adição de fundentes. O forno pode ser operado a uma temperatura relativamente baixa devido aos baixos pontos de fusão. A região 2 é alcançada para carga de baixo teor de ferro com constituintes de ganga ácida. Este modo de operação prevalece e necessita de dessulfuração extensiva do metal quente fora do BF. A obtenção de uma basicidade que resulte em uma dessulfuração adequada dentro do forno requer uma grande adição de cal (CaO) que leva a um alto volume de escória e, portanto, a uma maior taxa de coque. A região 3 representa as composições de escória preferidas em todo o mundo para grandes altos-fornos. Neste caso, dependendo do teor de alumina, deve-se adicionar dolomita para satisfazer os teores de MgO necessários.
Fig 7 Composições de escórias BF encontradas em várias condições de operação
A aba 1 mostra os componentes ótimos da escória BF. As escórias com basicidades mais altas (B) como mostrado na Tab 1 favorecem condições ótimas de amolecimento. O amolecimento e a faixa de fusão dos constituintes da ganga é de cerca de 80 graus C a 130 graus C para B =0,5 e cerca de 20 graus C a 50 graus C para B =2. Por causa da temperatura de fusão mais alta da escória altamente básica e de energia extra necessária devido à maior quantidade de adição de fluxo, a basicidade da escória é, portanto, mantida em torno de 1,2.
Tab 1 Composição ideal da escória BF | |||
Al2O3 | CaO | MgO | SiO2 |
% | % | % | % |
5 | 43 | 16 | 36 |
10 | 44 | 14 | 32 |
15 | 44 | 12,5 | 28,5 |
20 | 45 | 11 | 24 |
25 | 48 | 8 | 19 |
30 | 56 | 5 | 9 |
35 | 54 | 4 | 7 |
Propriedades da escória
As propriedades físicas e químicas das escórias são principalmente uma função da composição da escória e da temperatura. A seguir, descrevem-se essas relações com o propósito de desenvolver tendências gerais.
Temperaturas do líquido – As relações de temperatura liquidus e composição para os quatro componentes primários da escória são representadas em um diagrama de fases quaternário. A Fig. 8 foi gerada a partir de planos ternários do diagrama de fases quaternário. As Figuras 8a e 8b não são diagramas de fase. Há duas tendências gerais derivadas desses números. A primeira é que as temperaturas liquidus aumentam com o aumento de (Al2O3) e B/A, e a segunda é que (MgO) na faixa de 8% a 14% tende a minimizar o aumento da temperatura liquidus causado pelo aumento da temperatura liquidus. ou (Al2O3) ou B/A.
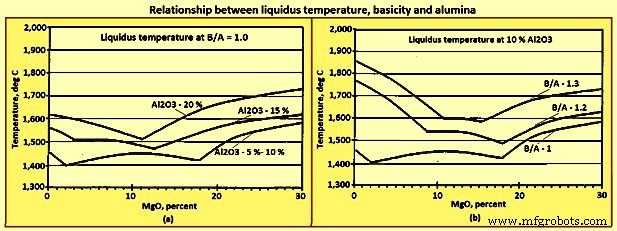
Fig 8 Relação temperatura liquidus, basicidade e alumina
viscosidade – A viscosidade é uma medida da quantidade de força necessária para alterar a forma de um material e é relatada em uma unidade chamada ‘poise’. Quanto maior a viscosidade, mais força é necessária para fazer com que um líquido flua. Para fins de comparação, considerando que a 20°C a viscosidade da água é 0,01002 poise, uma viscosidade típica de escória aceitável é de cerca de 2 a 5 poise, e a viscosidade do SiO2 líquido é da ordem de 100.000 poise. A alta viscosidade do SiO2 líquido é causada pela estrutura do polímero. A quebra da estrutura do polímero pelos óxidos básicos diminui a viscosidade. A diminuição da viscosidade de todas as escórias líquidas com o aumento do B/A é mostrada na Fig 9a. Em geral, a viscosidade de qualquer mistura líquido/sólido aumenta à medida que a quantidade de sólidos suspensos aumenta. O impacto da temperatura na viscosidade da escória é consideravelmente maior em temperaturas abaixo da temperatura liquidus do que acima da temperatura liquidus como mostrado na Fig 9b.
Fig 9 Relação entre viscosidade, B/A e temperatura
Existem duas tendências gerais que são observadas para a viscosidade. Acima da temperatura liquidus, a viscosidade das escórias líquidas diminui com o aumento da temperatura e B/A. Em temperaturas abaixo da temperatura liquidus, a viscosidade diminui com o aumento da temperatura e a diminuição do B/A.
Taxa de partição de enxofre – A siderurgia BF é um processo de dessulfuração muito bom em relação ao processo siderúrgico devido à diferença no potencial de oxigênio das escórias dos processos. O efeito do potencial de oxigênio na dessulfurização pode ser demonstrado usando a equação (CaO) + [S] =(CaS) + (FeO), onde o potencial de oxigênio é indicado pelo (FeO). Quanto maior o (FeO), mais a reação é direcionada para a esquerda e maior o [S]. As escórias de aciaria com (FeO) de 15 % a 25 % são, portanto, escórias dessulfurantes mais fracas do que as escórias de lareira BF com (FeO) inferior a 1 %.
Essencialmente, todo o enxofre no BF deixa o forno no metal quente e na escória. Uma relação para a previsão de [S] pode ser desenvolvida com base em um balanço de massa de enxofre para uma tonelada de metal quente, conforme a equação (i) abaixo, e o termo partição de enxofre definido conforme a equação (ii) abaixo. A predição de [S], pela equação (iii) abaixo, é derivada pela substituição de [S] da equação (i) na equação (ii) e então resolvendo para [S].
A Equação (i) é St =[S] /100 x 1.010 + (S) /100 x Svol onde 1.010 são os kgs de metal quente em uma tonelada de metal quente incluindo uma perda de rendimento de 1%, St é a carga de enxofre que é o peso total de enxofre em kgs/tHM. Svol é o volume de escória que é o peso da escória em kgs/tHM. Equação (ii) Sp =(S) /[S] onde Sp é a razão de partição de enxofre. A equação (iii) é [S] =St x 100 / (Sp x Svol + 1.010).
A escória Sp pode ser prevista com base na equação (iv) Sp =147,7 x BB + 37,7 x [Si] – 190 e na equação (v) BB ={(CaO) + 0,7(MgO)} / {0,94(SiO2) + 0,18 (Al2O3)}. Aqui BB é a basicidade definida pela razão do sino. Deve-se notar que os coeficientes da equação (iv) foram desenvolvidos a partir da análise de regressão de um forno específico. A equação (iv) e a equação (v) foram usadas para construir a Fig 10(a), e a equação (iii), a equação (iv) e a equação (v) foram usadas na construção da Fig 10 (b).
Fig 10 Divisória de enxofre entre escória e metal
As tendências gerais que podem ser derivadas das equações e figuras acima são (i) [S] diminui com a diminuição de St e aumento de Sp e Svol, (ii) no entanto, Sp normalmente aumenta com B/A, (iii) CaO é um melhor dessulfurizador do que o MgO e (iv) o Al2O3 tem um efeito menor no Sp do que o SiO2.
Capacidade alcalina – Um fenômeno de 'refluxo' ou 'reciclagem' ocorre no BF devido ao fluxo em contracorrente de gases versus sólidos / líquidos, principalmente para enxofre, zinco e álcalis. A reciclagem do potássio alcalino (K) é mostrada na Fig. 11a. The recycling phenomena is when an element travels down the furnace in a solid or liquid phase, reacts to form gas species in the higher temperature regions of the furnace, then travels back up the furnace as gases, where it reacts and is absorbed by the solid / liquid phases in the lower temperature region of the furnace. The recycling results in much higher internal concentrations of the recycled element than the concentration going in or out of the furnace. For example the internal loading of K can be 10 kgs/tHM, when the materials being charged contain only 2 kgs/tHM.
Alkalis have no beneficial, but many deleterious effects on the BF. Alkalis are absorbed by refractories, coke, and ore causing degradation of the refractories and coke, and ore swelling. Alkalis can also form scabs which can peel off upsetting the thermal condition of the furnace, or build up and constrict burden and gas flow. Alkalis cannot be avoided as they are contained in all coals, cokes, and to a lesser extent ores. The alkali loading is to be minimized wherever possible.
A portion of the alkalis leave the furnace in the top gas, the quantity being a function of the top temperature profile. The remaining alkalis are to be removed in the slag. The ability of slag to remove alkalis from the furnace is referred to as the alkali capacity of the slag. The relationships of alkali capacity to slag composition and temperature are shown in Fig 11b. In general the alkali capacity increases with lower B/A, and with lower temperature.
Fig 11 Alkali recycling and alkali capacity of slag
Silica activity – The [Si] produced is dependent upon the burden materials, furnace operation, and slag chemistry. The impact of the slag chemistry is shown in the equation [Si] =(SiO2) x GSiO2 / GSi x Keq / (P to the power 2)co. Here CO is carbon mono-oxide. This equation is developed from the equilibrium constant, equation Keq ={ASi x (P to the power 2)co} / { ASiO2 x Ac}, for the reaction given in equation (SiO2) + 2C =[Si] + 2COgas, the definitions of the activities of (SiO2) and [Si], equation ASiO2 =(SiO2) x GSiO2 and equation ASi =[Si] x GSi, and assuming that the activity of the carbon in the hearth is equal to one. The trend implied by Equation [Si] =(SiO2) x GSiO2 / GSi x Keq / (P to the power 2)co is that the [Si] decreases as the (SiO2) decreases.
Slag design factors
In some of the BFs, a typical slag composition which is formed from the gangue in the ore and ash of the coke is 9 % CaO, 5 % MgO, 75 % SiO2, and 10 % Al2O3. A slag of this composition has a liquidus temperature of the order of 1,600 deg C and does not flow well even above its liquidus temperature. Hence, CaO and MgO are added to the burden to ‘flux’ the gangue and ash resulting in acceptable liquidus temperatures and flow characteristics.
Basic slag design is the selection of the types and quantities of fluxes to be used with a burden and coke to produce a slag of acceptable properties. Burden and coke selections are largely driven by economic issues such as local versus imported sources and degree of beneficiation. These economic driving forces have resulted in a wide range of slag compositions throughout the world.
The general factors to be considered in designing a slag for normal operation are (i) liquidus temperature, that is, the slag is to be completely liquid in the hearth and cast house, (ii) viscosity, that is, the slag is to have a low viscosity, high fluidity, so as to drain from the hearth and down the cast house runners, (iii) sulphur capacity that is the Sp is to be sufficient to produce hot metal with sulphur contents within specifications, (iv) alkali capacity, that is, the slag alkali capacity is to be sufficient to prevent alkali build up in the furnace, (v) hot metal silicon control, that is, the effect of the slag chemistry on the [Si] is to be considered, (vi) slag volume, that is, the slag volume is to be high enough to contribute to the stability of the slag properties and hot metal quality, but not so high as to require excessive fuel or contribute to furnace instability, (vii) robust properties, that is, the slag properties are to be as insensitive to variations in normal variations in furnace operation as possible, specifically hot metal temperature, and (viii) end use, that is, the requirements of the end use of the slag is to be considered.
Slag design is to recognize that the above factors are not independent and that the design always involves a balancing of the above factors to resolve the conflicting trends (Tab 2).
Tab 2 Normal conflicting trends | ||
Desired parameter | Basicity | Al2O3 |
Lower liquidus temperature | Lower | Lower |
Lower viscosity | Higher | |
Higher K removal | Lower | Lower |
Lower [S] | Higher | Higher |
Lower [Si] | Higher | Higher |
Two examples of the slag design are described below. In the first example (Tab 3) , the issue is to increase the alkali removal without increasing the [S]. The resolution of the issue is to increase the slag volume through the use of additional SiO2 in the burden, while decreasing the slag basicity.
Tab 3 Example of designing slag for increased K2O removal | |||||
Basicity | Slag volume | K2O | K2O removed | (S) | S removed |
B/A | kgs/tHM | % | kgs/tHM | % | kgs/tHM |
1.10 | 225 | 0.47 | 1.30 | 1.82 | 5.00 |
1.05 | 282 | 0.55 | 1.55 | 1.77 | 5.00 |
1.00 | 290 | 0.63 | 1.85 | 1.72 | 5.00 |
0.95 | 298 | 0.71 | 2.10 | 1.68 | 5.00 |
The issue in the second example (Tab 4) is to lower the [Si] without negatively impacting the other properties of slag and furnace operation. The resolution of the issue is to decrease the (SiO2) by increasing the (Al2O3) using quartzite, a high (Al2O3) burden material, while holding the (CaO) and (MgO) constant. The change in slag chemistry results into a decrease of both [Si] and [S].
Tab 4 Example of designing slags with lower [Si] | |||||
Period | Unit | Base | Number 1 | Number 2 | Number 3 |
Basicity | 1.12 | 1.13 | 1.13 | 1.12 | |
(MgO) | % | 11.8 | 11.5 | 11.7 | 11.5 |
(Al2O3) | % | 7.8 | 10.2 | 10.3 | 11.7 |
[Si] | % | 0.76 | 0.53 | 0.54 | 0.49 |
[S] | % | 0.043 | 0.031 | 0.029 | 0.026 |
Slag after the BF
The use of BF slag is driven by the economics of processing and market demand. In the place, where the processing and marketing is performed by the organization producing the slag, the markets tend to be local in nature with minimal processing. As per the present trend, independent organizations take ownership of the liquid slag at the end of the slag runner which has led to wider markets with more extensive processing. The product slag can be classified by the rate of cooling.
Air-cooled slags are those produced with low cooling rates. These are slags which are solidified in pits and frequently cooled with water sprays. The largest uses for air cooled slag are in road construction, railroad ballast, and aggregate. Air-cooled slag has also been used in the production of cement, mineral wool insulation, roofing, and glass.
Pelletized and granulated slags are those produced with high cooling rates. Pelletized slag is produced by pouring liquid slag onto a rotating drum, sometimes with water. Granulated slags are produced by either pouring the liquid slag directly into a large slag pit of water or through the use of high pressure water sprays which breaks the slag up into droplets. Rapidly cooled slags have been used for the same applications as air-cooled slags. The high glass content of rapidly cooled slags makes it particularly suitable for Portland cement production.
Processo de manufatura
- Sistema de automação, medição e controle de processos de alto forno
- Geração e uso de gás de alto-forno
- Granulação de escória de alto-forno na casa de fundição
- Produtividade do Alto Forno e os Parâmetros Influenciadores
- Operação de alto-forno e escória de alta alumina
- Irregularidades do alto-forno durante a operação
- Tundish e seu papel na fundição contínua de aço
- Granulação a Seco de Escória de Alto Forno para Recuperação de Energia
- Fabricação de ferro por alto-forno e emissões de óxido de carbono
- Engenharia de precisão e seu papel na fabricação