Gaseificação de carvão
Gaseificação de carvão
A gaseificação do carvão é uma tecnologia de conversão que converte qualquer material contendo carbono (C), como o carvão, em gás de síntese (syngas). É um processo de alta temperatura com temperatura atingindo tipicamente 1.225 graus C. A temperatura é otimizada para produzir um gás combustível com um mínimo de líquidos e sólidos. Este processo consiste em aquecer o carvão da matéria-prima em um recipiente com ou sem adição de oxigênio (O2). O carbono reage com a água na forma de vapor e O2 a uma pressão relativamente alta tipicamente superior a 30 quilogramas por centímetro quadrado (kg/sq cm) e produz gás de síntese bruto, uma mistura composta principalmente de monóxido de carbono (CO) e hidrogênio (H2) e alguns subprodutos menores. Os subprodutos são removidos para produzir um gás de síntese limpo que pode ser usado (i) como combustível para gerar energia ou vapor, (ii) como um bloco químico básico para um grande número de usos nas indústrias petroquímica e de refino, e (ii) ) para a produção de H2. A gaseificação agrega valor à matéria-prima de baixo valor ou valor negativo, convertendo-a em combustíveis e produtos comercializáveis. O básico do processo de gaseificação é dado na Fig 1.
Fig 1 Noções básicas do processo de gaseificação
História e desenvolvimento atual
O gás da cidade, um produto gasoso fabricado a partir do carvão, contendo aproximadamente 50% de H2, sendo o restante composto principalmente de metano (CH4) e dióxido de carbono (CO2), com 3% a 6% de CO, é um produto gasoso fabricado a partir do carvão. Ele está sendo usado desde o início de 1800.
O processo original de gaseificação do carvão foi desenvolvido pelos pesquisadores alemães Franz Fischer e Hans Tropsch no instituto Kaiser Wilhelm na década de 1920. A gaseificação foi usada extensivamente durante a Segunda Guerra Mundial para converter carvão em combustíveis de transporte através do processo Fischer-Tropsch. A Sasol construiu uma fábrica em Sasolburg com o objectivo principal de converter carvão de baixo teor em produtos petrolíferos e o primeiro líquido foi produzido a partir desta fábrica em 1955. O processo de gaseificação do carvão tem sido amplamente utilizado nos últimos 50 a 60 anos para converter carvão e óleo pesado em H2 para a produção de fertilizante amônia/uréia. A indústria química e a indústria de refinaria aplicaram a gaseificação nas décadas de 1960 e 1980, respectivamente, para a preparação da matéria-prima. Nos últimos 10 a 15 anos, o processo está sendo utilizado pela indústria de energia em usinas de Ciclo Combinado de Gaseificação Integrada (IGCC).
Processo Fischer-Tropsch
O processo Fischer-Tropsch é uma reação química catalisada na qual CO e H2 são convertidos em hidrocarbonetos líquidos de várias formas. Catalisadores típicos usados são cobalto e ferro. O principal objetivo deste processo é produzir combustível sintético. A utilidade deste processo deve-se principalmente à sua capacidade de produzir hidrocarbonetos fluidos ou H2 a partir de uma matéria-prima sólida.
O processo original de Fischer-Tropsch é descrito pela equação química (2n+1)H2 + nCO =CnH(2n+2) + nH2O. Os reagentes iniciais na reação acima (ou seja, CO + H2) podem ser produzidos por outras reações, como a combustão parcial de CH4 no caso de aplicações de GTL (gás para líquido) conforme a equação CH4 + 0,5O2 =2H2 + CO ou pela gaseificação do carvão no caso do CTL (coal to liquid) conforme a equação C + H2O =H2 + CO. A energia necessária para a reação do carvão e do vapor é fornecida pela adição de ar ou O2. Isso leva à reação C + 0,5O2 =CO. A produção e síntese de syngas pelo processo Fischer-Tropsch é mostrada na Fig 2.
Fig 2 Produção e síntese de syngas pelo processo Fischer-Tropsch
Comparação da gaseificação do carvão com a combustão do carvão
A gaseificação e a combustão podem ser consideradas essencialmente como duas extremidades de uma gama de reações. A combustão é oxidação total, enquanto a gaseificação é oxidação parcial. Além disso, a combustão ocorre em um ambiente oxidante (excesso de O2), enquanto a gaseificação ocorre em um ambiente redutor (empobrecido de O2). A gaseificação é mais eficiente e tem emissões mais baixas. No caso de gaseificação, a água pode ser adicionada como reagente para aumentar o teor de H2 do produto. A guia 1 fornece uma lista das reações mais significativas e a variação de entalpia associada a cada uma dessas reações. Observando as duas primeiras reações na tabela, vê-se que o carvão denotado como C reage com um átomo de O2 (0,5 O2) para obter CO e com dois átomos de O2 para obter CO2. Na realidade, a segunda reação não é um processo de uma etapa, pois a fase sólida C reage com um átomo de O2 para produzir CO, que então reage com o segundo átomo de O2 para formar CO2. Todas as reações na tabela são exotérmicas, exceto as duas reações identificadas como gaseificação com vapor e gaseificação com CO2. Essas duas reações endotérmicas são as reações mais frequentemente chamadas de gaseificação, onde o sólido C é transformado em um gás reativo através de uma reação com um gás “não reativo” (H2O ou CO2). Além disso, essas duas reações sendo endotérmicas requerem altas temperaturas para prosseguir.
A reação de oxidação parcial geral é 2CHn + O2 =2CO + nH2. O consumo de O2 no processo depende do teor de cinzas e do CV do carvão. O fornecimento insuficiente de O2 garante a oxidação parcial do carvão. Esta reação produz uma mistura de gases:H2, CO, CH4 e CO2. O produto final é syngas. A composição da mistura muda com a pressão.
Guia 1 Gaseificação e reações de combustão | |||
Sl. No. | Processo de reação | Equação | Mudança na entalpia |
1 | Gaseificação com O2 | C + 0,5O2 =CO | -2180,3 kcal/kg C |
2 | Combustão com O2 | C + O2 =CO2 | -7844,7 kcal/kg C |
3 | Gaseificação com CO2 | C + CO2 =2CO | 3484 kcal/kg C |
4 | Gaseificação com vapor | C + H2O =CO + H2 | 2640,7 kcal/kg C |
5 | Gaseificação com H2 | C + 2H2 =CH4 | -1485,4 kcal/kg C |
6 | Reação de deslocamento água-gás | CO + H2O =CO2 + H2 | -361,4 kcal/kg CO |
7 | Metanação | CO + 3H2 =CH4 + H2O | -1768,4 kcal/kg CO |
A gaseificação do carvão é realizada com uma quantidade limitada de O2, que é cerca de um quinto a um terço do O2 teoricamente necessário para a combustão completa. Apenas uma fração de C é queimada para geração de calor. H2 e CO são os principais produtos da gaseificação. CH4 e CO2 são os outros dois principais produtos e seu conteúdo aumenta com o aumento da pressão e o conteúdo de H2+CO diminui. Nos gaseificadores de carvão ocorrem dois processos físico-químicos. São eles (i) processo de pirólise ou desvolatilização e (ii) processo de gaseificação.
No processo de pirólise, ao entrar no gaseificador, o carvão é primeiramente seco pelos gases quentes presentes no gaseificador. Uma série de processos físicos e químicos complexos começam lentamente a temperaturas inferiores a 350 graus C e aceleram quando a temperatura excede 700 graus C. A composição dos produtos liberados da pirólise depende da temperatura, pressão e composição do gás durante a pirólise. O processo de pirólise pode ser representado pela reação Carvão –> Calor –> Carvão –> Gases –> Vapores ou líquido.
Os três produtos que são produzidos pela pirólise são (i) gases leves como CO, H2, CO2, CH4 e H2O (vapor de água), (ii) alcatrão que é um líquido corrosivo e viscoso composto de moléculas inorgânicas e orgânicas pesadas, e (iii) char que é um resíduo sólido contém principalmente C.
O processo de gaseificação envolve uma série de reações endotérmicas que são suportadas pelo calor produzido pelas reações de combustão que ocorrem dentro do gaseificador. Essas reações são representadas pelas equações (i) C + O2 =CO2 com delta H =-94,05 kcal/mol, e (ii) H2 + 0,5O2 =H2O com delta H =– 68,3 kcal/mol. As principais reações de gaseificação que ocorrem são (i) reação de deslocamento água-gás, (ii) reação de Boudouard, (iii) conversão de deslocamento e (iv) metanação.
Na reação de deslocamento água-gás ocorre a oxidação parcial do C pelo vapor e é representada pela equação C + H2O =H2 + CO com delta H =28/3 kcal/mol. Durante a reação de Boudouard, o carvão presente no gaseificador reage com o CO2 e produz CO. A reação reversível é representada pela equação CO2 + C =2CO com delta H =38 kcal/mol. A conversão de deslocamento é uma reação endotérmica e é conhecida como reação de deslocamento água-gás. Devido a esta reação, há um aumento na razão H2 para CO no gás. Esta reação é usada durante a produção de syngas. A reação é CO + H2O =CO2 + H2 com delta H =– 10,1 kcal/mol. Para a metanação, o catalisador à base de níquel é usado. Este catalisador a 1100 graus C e a uma pressão de 6 kg/cm² a 8 kg/cm² acelera a reação de formação de CH4 que é preferido em aplicações IGCC devido ao seu alto poder calorífico. A reação envolvida é dada pela equação C + 2H2 =CH4 com delta H =17,8 kcal/mol.
As reações de gaseificação completas são realizadas nos gaseificadores que devem ser operados em uma determinada temperatura para conduzir certas reações endotérmicas C – vapor e C – CO2. A temperatura necessária é mantida pelo calor desenvolvido a partir da reação exotérmica entre O2 e carvão.
Dependendo do meio de gaseificação, os gaseificadores são classificados em duas categorias:(i) soprado por ar e (ii) soprado por O2. Nos gaseificadores soprados a ar, o ar é usado como meio de gaseificação, enquanto nos gaseificadores soprados com O2 o O2 puro é usado como meio de gaseificação. Quando o ar é usado como meio de gaseificação, o N2 é trazido simultaneamente para o processo, o que resulta na diluição do gás do produto. Como resultado, o gás do produto tem um valor calorífico (CV) mais baixo.
Dependendo do contato entre gás e combustível, existem quatro tipos de gaseificadores (Fig. 3). São eles (i) gaseificador de leito fixo ou móvel, (ii) gaseificador de leito fluidizado, (iii) gaseificador de leito arrastado e (iv) gaseificador de fluxo de transporte. Todos os quatro tipos de gaseificadores são baseados na oxidação parcial (gaseificação) de um material de alimentação carbonáceo (contendo C) (carvão). Embora cada um deles possa produzir um gás redutor aceitável para a produção de DRI, os gaseificadores de leito fixo e de leito fluidizado são a escolha preferida para carvões com alto teor de cinzas.
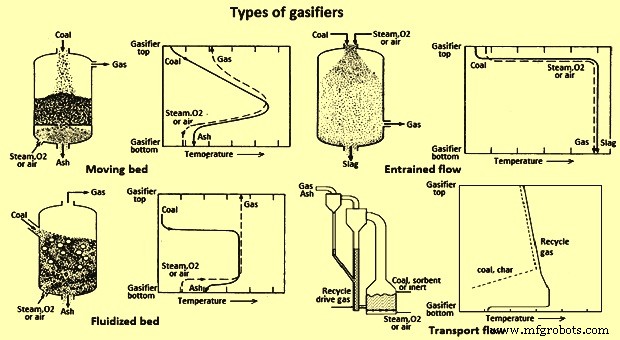
Fig 3 Tipos de gaseificadores
A tecnologia de gaseificação de leito móvel é a tecnologia mais antiga e está sendo amplamente utilizada. O gaseificador também é conhecido como gaseificador de leito fixo. O meio de gaseificação flui lentamente através de um leito fixo de partículas sólidas. As duas configurações possíveis deste tipo de gaseificadores são as de fluxo ascendente e descendente, dependendo da direção do fluxo do meio de gaseificação. A configuração up-draft é mais comumente usada, pois há baixo teor de alcatrão. O tamanho de carvão de alimentação preferido é de 5 mm a 80 mm. A zona de combustão atinge uma temperatura máxima em torno de 1500 graus C a 1800 graus C e para a zona de escória e gaseificação de cinzas secas uma temperatura máxima em torno de 1300 graus C. O perfil de temperatura é formado sobre o leito, de modo que o carvão de alimentação é sucessivamente pré-aquecido, seco, pirolisado, gaseificado e queimado. O gaseificador Lurgi é a mais antiga tecnologia de gaseificador de leito móvel.
O gaseificador de leito fluidizado possui o leito de partículas sólidas que se comporta como um fluido. Neste tipo de gaseificador, o tamanho de partícula da matéria-prima é menor que 5 mm e as partículas ficam suspensas no gás rico em O2. O gás ascendente reage com a matéria-prima e mantém o estado fluidizado das partículas de carvão. Uma distribuição de temperatura uniforme é alcançada neste tipo de gaseificadores. Além disso, neste tipo de gaseificador, a formação de clínquer e a desfluidização do leito são evitadas, uma vez que a temperatura de operação está na faixa de 800°C a 1050°C, que está bem abaixo da temperatura de fusão das cinzas. A descarga de cinzas pode ser realizada na forma de cinzas secas ou aglomeradas. O gaseificador de leito fluidizado de cinzas secas é tradicionalmente usado para carvões de baixo teor. O gaseificador de leito fluidizado de cinzas aglomeradas está sendo usado para qualquer classificação de carvão.
O gaseificador de fluxo arrastado usa partículas de carvão pulverizadas de tamanho inferior a 0,1 mm que são suspensas em uma corrente de vapor e O2 em alta velocidade. Dependendo do método de alimentação de carvão, seco (azoto sendo usado como gás de transporte) ou úmido (transportado em pasta de água), os gaseificadores aceitam quase qualquer tipo de carvão. Os gaseificadores de fluxo arrastado garantem alta conversão de C, pois operam em uma faixa de temperatura alta de 1400 graus C a 1600 graus C (bem acima da temperatura de escória de cinzas). Esses gaseificadores são de alta capacidade, pois o tempo de residência do gás é medido em segundos.
Os gaseificadores de transporte são gaseificadores sem escória alimentados a seco. O gaseificador de transporte é baseado no campo de fluxo hidrodinâmico. Possui excelente contato gás-sólido e baixíssima resistência à transferência de massa entre gás e sólidos. Possui uma atmosfera altamente turbulenta que permite alto rendimento de carvão e altas taxas de liberação de calor a baixa temperatura, evitando problemas com manuseio de escória e erosão do revestimento.
Além do CO e H2 desejados, o gás de síntese que sai de um gaseificador também contém outros compostos. O produto da gaseificação contém componentes desejáveis como CO, H2, CH4 e componentes indesejáveis como CO2, H2O, cinzas, fuligem arrastada, alcatrão, material particulado, certa quantidade de H2S (sulfeto de hidrogênio) e traços de amônia, ácido clorídrico, cianeto de hidrogênio . Portanto, a limpeza do gás de síntese é um aspecto importante do processo de gaseificação do carvão. Os componentes indesejáveis precisam ser removidos do gás do produto. Existem várias técnicas sendo usadas para remover os componentes indesejáveis.
Os gases do produto (CO, H2 e CH4) do processo de gaseificação do carvão têm valor combustível. Se for usada uma tecnologia de gaseificação de leito fixo, o gás de síntese também contém compostos orgânicos aromáticos. Normalmente, 1 kg de carvão betuminoso pode ser convertido em 1,5 cum a 1,7 cum de syngas.
Em termos de flexibilidade de matéria-prima, vários projetos de plantas de gaseificação foram desenvolvidos para utilizar vários tipos de carvão. A gaseificação resulta em emissões gasosas muito baixas de poluentes convencionais (não GEE), devido à natureza da operação do processo. Também oferece uma rota de custo marginal potencialmente baixo para capturar o subproduto de CO2 resultante para armazenamento geológico ou recuperação aprimorada de petróleo dos campos de petróleo.
Além disso, os processos de gaseificação do carvão requerem um uso significativo de água. Eles também são grandes emissores de CO2. Para 1 tonelada de syngas, o consumo típico de carvão é de cerca de 2,8 toneladas, a necessidade de água é de cerca de 6,6 toneladas e a geração de CO2 é de cerca de 2,5 toneladas. O CO2 é liberado como subproduto e pode ser vendido ou comprimido para transporte para o armazenamento subterrâneo.
Existem vários conceitos de gaseificador. Uma descrição geral dos reatores de alguns dos principais conceitos de gaseificador é dada abaixo.
GE Energy gaseificador – A GE Energy adquiriu sua tecnologia de gaseificação da Chevron em 2004. O gaseificador de carvão da GE compreende um gaseificador revestido de refratário de fluxo arrastado e alimentação descendente de estágio único para produzir gás de síntese. A pasta de carvão/água é bombeada para o topo do gaseificador, que junto com O2 é introduzido através de um único queimador (Fig. 4). O carvão reage exotermicamente com o O2 em alta temperatura (1200°C a 1480°C) para formar gás de síntese. O gás de síntese contém principalmente H2 e CO e escória.
Fig 4 Gaseificador de carvão da energia GE
A escória que flui para baixo é extinta e, em seguida, removida do fundo do gaseificador através de um arranjo de funil de bloqueio. A água que sai da tremonha é separada da escória e enviada para uma unidade de depuração, após a qual pode ser reciclada para a preparação da lama. O gás de síntese bruto que sai do gaseificador pode ser resfriado por um trocador de calor radiante e/ou convectivo e/ou por um sistema de têmpera direta, onde a água é injetada no gás de síntese bruto quente. A seleção dessas alternativas é uma escolha de custo e aplicação.
O projeto de resfriamento radiante usa um resfriador de syngas radiante tolerante à fuligem que gera vapor de alta pressão. A escória é extinta em uma piscina de água localizada na parte inferior do vaso do reator e removida através de uma tremonha de bloqueio. O gás de síntese é ainda resfriado após deixar o gaseificador por um purificador de água para remover o material particulado fino, antes que o gás seja enviado para o processamento a jusante. O sistema de têmpera direta usa uma têmpera de água com gás de saída onde o gás quente que sai do gaseificador é contatado diretamente com a água através de um anel de têmpera. Em seguida, é imerso em água na parte inferior do recipiente do gaseificador. O gás de síntese resfriado e saturado é então enviado para um purificador para remoção de fuligem e partículas. O projeto de têmpera é menos eficiente, mas também menos dispendioso, e é comumente usado quando um gás de síntese de razão H2 para CO mais alto é necessário.
Gaseificador Conoco Phillips E-Gas – O gaseificador Conoco Philips E-gas foi originalmente desenvolvido pela DOW Chemicals e demonstrado na Louisiana Gasification Technology Inc. (LGTI) de 1987 a 1995. É um gaseificador de fluxo arrastado e é mostrado na Fig 5. É um gaseificador de dois estágios gaseificador com 80 % de alimentação para o primeiro estágio (inferior). O gaseificador é alimentado com lama de carvão-água, gaseificador revestido com refratário e soprado com O2 com sistema de remoção contínua de escória e remoção de partículas secas. O processo E-Gas é bom para uma ampla gama de carvões.
Fig 5 Gaseificador Conoco Philips E-gas
Gaseificador Shell – A tecnologia de gaseificação da Shell compreende um gaseificador de escória de alimentação seca, pressurizado, de fluxo arrastado. A variante à base de carvão foi desenvolvida na década de 1970. O carvão é pulverizado e alimentado ao gaseificador através de dois conjuntos de queimadores opostos horizontalmente usando um gás de transporte (seja gás de síntese ou nitrogênio). O2 pré-aquecido e vapor (como moderador) são misturados e alimentados ao injetor, onde reagem com o carvão para produzir gás de síntese consistindo principalmente de H2 e CO com apenas uma pequena quantidade de CO2 e sem líquidos ou gases de hidrocarbonetos. Os gases quentes do produto fluem para cima através de uma parede cilíndrica de membrana vertical, como mostrado na Fig 6.
Fig 6 Gaseificador de fluxo tensionado do casco
As cinzas fundidas arrastadas com o gás de síntese que flui para cima são depositadas nas paredes da água e fluem para baixo. Ele é removido pela base do gaseificador onde é resfriado em banho-maria. O gás de síntese bruto deixa o gaseificador na faixa de temperatura de 1370°C a 1480°C e é então tratado com gás de produto reciclado de temperatura mais baixa para converter qualquer escória derretida em um material sólido endurecido. Em seguida, ele entra no resfriador de gás de síntese para recuperação de calor, gerando vapor superaquecido de alta pressão (HP). A maior parte das cinzas volantes contidas no gás de síntese bruto que sai do resfriador de gás de síntese é removida do gás usando equipamento de filtro comercial ou ciclones. Qualquer cinza volante restante é capturada a jusante com um purificador úmido.
Gaseificador Siemens – O gaseificador Siemens é um sistema de alimentação seca, pressurizado, de fluxo arrastado, com um queimador de queima superior através do qual é introduzido carvão junto com O2 e vapor (Fig 7). Ele pode ser projetado com revestimento refratário, para estoques de baixa cinza, ou com uma estrutura de parede de membrana à prova de gás na seção de gaseificação do gaseificador.
Fig 7 Gaseificador de fluxo incorporado Siemens
A escória fundida formada no gaseificador flui pela câmara do reator para a seção de têmpera, onde solidifica em contato com a água de um anel de bicos de têmpera e é removida através de um arranjo de tremonha. O gaseificador pode atingir taxas de conversão de C superiores a 99% e a tecnologia é adequada para todos os tipos de carvões de antracito a linhita.
Gaseificador de carvão KBR TRIG – A tecnologia Transport Integrated Gasification (TRIG) foi desenvolvida pela empresa Southern e KBR Inc. Ela é projetada para processar carvões reativos de baixo teor, incluindo aqueles com até 50% de cinzas e alto teor de umidade, e pode ser operado com vapor e ar ou O2 como meio de gaseificação. A operação por sopro de ar é preferível para geração de energia, enquanto a operação por sopro de O2 é mais adequada para a produção de gás de síntese. O layout simplificado do processo TRIG é mostrado na Fig 8.
Fig 8 Layout simplificado do processo TRIG
O sistema é composto por um gaseificador circulante, que consiste em uma zona de mistura, riser, desengajador, ciclone, tubo vertical, vedação em loop e perna em J. Ele foi projetado para operar em altas taxas de circulação de sólidos e velocidades de gás, resultando em maior rendimento, conversão de C e eficiência. O gás de síntese bruto é formado na porção do riser da unidade, da qual, carregado com sólidos não reagidos, passa por uma série de ciclones onde os sólidos são removidos. O material de cinzas é recirculado através do riser para permitir que o C não convertido seja utilizado e fornecer calor ao gaseificador. À medida que as cinzas se acumulam no canto inferior, elas são descarregadas da unidade. O gaseificador opera em temperaturas moderadas e abaixo do ponto de fusão das cinzas, o que pode aumentar a confiabilidade e disponibilidade do equipamento. Este último é aprimorado pelo uso de um filtro de partículas a jusante, que elimina a depuração da água e reduz significativamente o consumo de água da planta e a descarga de efluentes.
Gaseificador de carvão pressurizado de fundo seco Lurgi – O processo de gaseificação Sasol Lurgi compreende a reação de vapor e O2 com carvões de baixa ou média aglomeração em uma grelha rotativa a pressões de 20 kg/cm2 a 30 kg/cm2. O gaseificador para o processo de gaseificação de carvão pressurizado de fundo seco é mostrado na Fig 9.
Fig 9 Gaseificador de carvão pressurizado de fundo seco Lurgi
Na zona de combustão inferior da grelha, o carvão é queimado com O2 para fornecer energia para as reações de gaseificação. À medida que o carvão desce pelo gaseificador, ele é aquecido pelo gás de síntese ascendente que sai do gaseificador. O calor faz com que o carvão seque seguido de desvolatilização. Alguns dos produtos desvolatilizados escapam antes de reagir e saem do gaseificador com o gás de síntese bruto. À medida que o carvão desvolatilizado desce, é gaseificado com produtos de combustão da zona de combustão abaixo. No modo de operação cinza seca, o excesso de vapor é injetado com O2 para manter a temperatura abaixo da temperatura de fusão das cinzas. Uma grelha de cinzas rotativa acionada por motor é usada para remover cinzas em estado “seco” e também para suportar o leito de carvão.
O fluxo em contracorrente do agente de gaseificação e combustível resulta em uma alta eficiência térmica do gaseificador para produzir um gás bruto com valores de aquecimento de cerca de 2650 kcal/cum a 2850 kcal/cum. Dependendo das características do carvão de alimentação, o gás do produto contém em volume 25% a 33% CO2, 15% a 21% CO, 35% a 41% H2 e 10% a 13% CH4. Para uso como gás de síntese, é necessário remover CH4 e CO2.
Desde a década de 1960, o processo Lurgi foi aprimorado por meio de aumentos no tamanho e nos componentes do reator, extensão da ardósia de carvão de alimentação para incluir carvões de baixo teor e o uso de ar em vez de O2 como agente de gaseificação. Além disso, o projeto foi demonstrado para operação em até 100 kg/sq cm de pressão para aumentar o rendimento do gaseificador e, ao mesmo tempo, aumentar o teor de CH4 do gás bruto.
A British Gas Corporation, em cooperação com a Lurgi, desenvolveu um novo design do fundo do gaseificador para evitar os problemas associados aos equipamentos rotativos no leito combustível/cinzas, ao mesmo tempo em que superou a limitação imposta pela temperatura de amolecimento das cinzas no zona de gaseificação. Isso resultou no gaseificador de escória BGL. O gaseificador difere do reator Lurgi padrão pela (i) substituição da grelha e da escória por uma fornalha para extração de escória líquida, (ii) pela introdução do agente de gaseificação O2 e vapor por meio de ventaneiras ao invés da grelha, e (iii) o uso de revestimento refratário na parte inferior do corpo do reator para reduzir a perda de calor.
O gaseificador de escória BGL também opera em temperaturas de gaseificação mais altas do que o gaseificador Lurgi padrão e, portanto, a relação CO/CO2 no gás do produto é maior e o teor de CH4 correspondentemente menor. As composições típicas de gás em volume são 2% a 3% CO2, 55% a 60% CO, 25% a 28% H2 e 6% a 9% CH4. A alta temperatura proporciona um melhor aproveitamento do vapor e, portanto, a quantidade de água necessária para ser limpa e processada é muito reduzida. As cinzas de carvão são convertidas em escória que forma um vidro não lixiviável na remoção. Isso requer uma baixa viscosidade da escória, que é obtida pela adição de agentes fundentes, geralmente calcário ou escória básica de alto-forno (BF).
Gaseificador MHI – O gaseificador Mitsubishi Heavy Industries (MHI) é baseado no gaseificador de escória soprado a ar da Combustion Engineering e co-desenvolvido entre a Combustion Engineering (e seus proprietários subsequentes) e a MHI. Possui sistema de alimentação a seco, adequado para carvões de baixo teor de umidade. É um gaseificador de escória de leito arrastado de dois estágios, soprado a ar, utilizando construção de parede de água de membrana. O gaseificador é mostrado na Fig 10.
Fig 10 MHI gaseificador
Tecnologia de gaseificação da Synthesis Energy Systems
A Synthesis Energy Systems (SES) tem uma licença exclusiva mundial para a tecnologia de gaseificação U-Gas, que é um sistema de leito fluidizado de estágio único e que pode fornecer um gás de síntese de baixo a médio poder calorífico. O fluxograma da tecnologia de gaseificação SES é apresentado na Figura 11. A tecnologia de gaseificação SES é particularmente adequada para gaseificar combustíveis de baixa qualidade, incluindo todos os tipos de carvão.
O carvão seco e moído é alimentado através de uma tremonha no gaseificador, que é fluidizado por uma mistura de vapor e O2. Esses gases reagentes são introduzidos na parte inferior do gaseificador através de uma rede de distribuição e na porta de descarga de cinzas no centro da rede de distribuição. O leito é mantido a temperaturas que variam de 840°C a 1100°C, dependendo da temperatura de amolecimento das cinzas dentro do combustível. Nessas condições, a concentração de partículas de cinzas de combustível (conteúdo mineral) dentro do gaseificador aumenta de tal forma que elas começam a se aglomerar e formar partículas maiores, que são seletivamente removidas do leito fluidizado por gravidade. Este design permite que 95% ou mais do C do combustível seja gaseificado.
Fig 11 Fluxograma da tecnologia de gaseificação SES
Processo de manufatura
- Redução do desgaste e extensão da vida útil da engrenagem em uma caixa de engrenagens do pulverizador de carvão
- Redução de partículas de desgaste em uma caixa de engrenagens do pulverizador de carvão
- Arch Coal reconhecido por excelência em manutenção preditiva
- SOLUÇÃO DE CARBONO NEGRO E IMPACTO NO MEIO AMBIENTE
- Universidade de Kentucky recebe subsídio para transformar piche de carvão em fibra de carbono
- Injeção de carvão pulverizado em um alto-forno
- Tecnologias para Melhoria do Processo de Coqueamento em Fornos de Coque de Subprodutos
- Recuperação de amônia durante a produção de coque de carvão de coque
- O que é epóxi de alcatrão de carvão?
- Melhorando a montagem de transferência para uma mina de carvão de Buchanan