Processos de Beneficiamento de Minérios de Ferro
Processos para Beneficiamento de Minérios de Ferro
O ferro é um elemento abundante na crosta terrestre, em média de 2% a 3% em rochas sedimentares a 8,5% em basalto e gabro. Como o ferro está presente em muitas áreas, é de valor relativamente baixo e, portanto, um depósito deve ter uma alta porcentagem de metal para ser considerado como minério. Normalmente, um depósito deve conter pelo menos 25% de ferro para ser considerado economicamente recuperável.
Mais de 300 minerais contêm ferro, mas cinco minerais são as principais fontes de minério de ferro. Eles são (i) magnetita (Fe3O4), (ii) hematita (Fe2O3), (iii) goetita (Fe2O3.H2O), (iv) siderita (FeCO3) e (v) pirita (FeS2). A mineração de minérios de ferro requer perfuração, detonação, britagem, peneiramento e mistura dos minérios.
A britagem e peneiramento são parte integrante das instalações de produção de minério. A britagem geralmente envolve um britador primário e britadores secundários operando em circuito fechado com peneiras vibratórias. A seleção do equipamento é determinada em grande parte pela friabilidade do minério. A maioria das operações de peneiramento em minérios de alto teor são secas, exceto quando a fração de finos pode ser efetivamente aprimorada por deslamagem.
Os minérios de ferro normalmente se enquadram em uma das três categorias, a saber (i) remessa direta, ou minérios de alto teor, que contêm ferro suficiente para ser carregado diretamente no forno de fabricação de ferro e só podem exigir britagem, peneiramento e mistura, (ii) minérios comerciais de baixo teor que ocorrem em torno dos minérios de alto teor que podem ser extraídos simultaneamente e que requerem uma pequena atualização por lavagem para aumentar seu teor de ferro, (iii) minérios de baixo teor que requerem britagem, moagem e concentração extensiva para produzir um concentrado aceitável. Os minérios de ferro que se enquadram nessas três categorias têm requisitos de processamento bastante diferentes. Para obter um produto uniforme, minérios de diferentes graus, composições e tamanhos são geralmente misturados.
O termo beneficiamento em relação aos minérios de ferro engloba todos os métodos usados para processar o minério para melhorar suas características químicas, físicas e metalúrgicas de forma a torná-lo uma alimentação mais desejável para o forno de fabricação de ferro. Tais métodos incluem britagem e moagem, lavagem, filtração, classificação, dimensionamento, concentração por gravidade, separação magnética, flotação juntamente com aglomeração. As operações de beneficiamento resultam na produção de dois produtos a saber (i) um concentrado e (ii) um rejeito (resíduo), que é descartado.
Esmagamento e moagem
O beneficiamento começa com a britagem e moagem juntamente com a classificação úmida ou seca dos minérios extraídos em preparação para outras atividades para o aprimoramento do teor de ferro dos minérios. A britagem e a moagem são processos de vários estágios e podem usar alimentação de minério seca ou úmida. Dependendo da dureza do minério, dois, três e, às vezes, quatro estágios de britagem são usados para reduzir o minério run of mine (ROM) para o tamanho de alimentação necessário. A britagem primária e secundária é normalmente por britadores giratórios ou cônicos. Os britadores de mandíbula raramente têm capacidade ou durabilidade para serem usados como unidade de britagem primária, a menos que o minério seja excepcionalmente macio. A britagem terciária até um tamanho superior de 25 mm é geralmente por britadores de cabeça curta operando em circuito fechado com telas. Normalmente, britagem primária, britagem secundária e peneiramento ocorrem no local da mina.
O investimento de capital e os custos de operação de britagem e moagem são substanciais. Assim, a economia desempenha um papel importante na determinação do uso desses equipamentos e do grau de britagem e moagem a ser realizada do minério para posterior beneficiamento. Outros fatores importantes incluem a concentração de valor do minério, sua mineralogia, dureza e teor de umidade.
Após a britagem inicial, a moagem fina reduz as partículas de minério à consistência de pó fino (malha 325, 0,44 mícron). A escolha do circuito de moagem é baseada na densidade e dureza do minério a ser moído. Embora o uso da moagem do moinho de barras ou bolas seja bastante comum, algumas instalações utilizam sistemas de moagem autógenos ou semi-autógenos. A moagem autógena usa pedaços grossos do próprio minério como meio de moagem no moinho. As operações semi-autógenas utilizam esferas e/ou varetas metálicas para complementar a ação de moagem das peças de minério. A moagem autógena é mais adequada para minérios fracamente cimentados contendo algum material duro. O benefício da moagem autógena é que ela é menos intensiva em capital e mão de obra. A moagem semi-autógena elimina a necessidade de um circuito secundário de britagem. O desgaste da haste e da esfera, o principal custo de manutenção das esmerilhadeiras tradicionais, também é eliminado com este método.
Os moinhos de haste geralmente são projetados para moer normalmente menos 35 mm de alimentação para menos 3 mesh. São moinhos rolantes com uma relação comprimento/diâmetro de 1,5 a 2,0. Os meios de moagem são hastes de aço de até 100 mm de diâmetro. O minério é moído úmido com teor de sólidos em torno de 68% a 80%. O tamanho do produto é controlado por combinações de taxa de alimentação, características de carga da haste, velocidade do moinho, densidade da pasta e viscosidade.
Os moinhos de bolas são os principais meios de moagem fina de minério de ferro. Eles são moinhos rolantes como os moinhos de barras, mas geralmente com uma relação comprimento/diâmetro menor que varia até 1,5. O meio de moagem é bolas de aço em vez de hastes. A eficiência de moagem é muito afetada pela eficiência de classificação e pelos parâmetros operacionais do moinho, como velocidade do moinho, carga do meio, densidade da pasta e viscosidade.
Moinhos de seixos também são usados para moagem fina. Eles são semelhantes aos moinhos de bolas, exceto que são carregados com seixos de 25 mm a 100 mm, em vez de bolas de aço. Sua principal vantagem é que os meios de moagem de aço não são necessários e o desgaste do revestimento do moinho é reduzido. No entanto, eles normalmente têm alto consumo de energia.
Entre cada operação da unidade de moagem, hidrociclones são usados para classificar partículas grossas e finas. Partículas grossas são devolvidas ao moinho de moagem para maior redução de tamanho. O minério moído na forma de uma pasta é bombeado para a próxima etapa de beneficiamento. Se o minério que está sendo moído for destinado à atividade de flotação, os reagentes químicos utilizados durante o processo são normalmente adicionados à lama durante esta etapa.
Flotação
A flotação é eficaz para a concentração de minérios de ferro finos (menos 100 mesh). O processo de flotação depende do fato de que certos reagentes adicionados a suspensões aquosas de minério de ferro finamente moído fazem com que minerais de óxido de ferro ou partículas de ganga exibam uma afinidade pelo ar. Os minerais que têm essa afinidade de se ligarem às bolhas de ar e passarem pela suspensão são removidos da suspensão como um produto de espuma. Fatores importantes para o sucesso das atividades de flotação incluem uniformidade de tamanho de partícula, uso de reagentes compatíveis com o minério e condições da água que não interfiram na fixação dos reagentes no minério ou nas bolhas de ar.
Os quatro tipos de reagentes químicos a seguir são normalmente usados na flotação.
- Coletores/aminas – São os reagentes adicionados para induzir a afinidade preferencial pelo ar. Eles causam aderência entre partículas sólidas e bolhas de ar em uma célula de flotação.
- Espumas – São as substâncias adicionadas para causar a formação de bolhas ou espumas estáveis. Eles são usados para estabilizar as bolhas de ar reduzindo a tensão superficial, permitindo assim a coleta de material valioso por raspagem do topo da célula.
- Antiespumantes – Eles reagem com as superfícies das partículas na célula de flotação para evitar que os materiais permaneçam na espuma. Em vez disso, os materiais caem no fundo como rejeitos.
- Outras substâncias – São adicionadas para fins de controle, como ajuste de pH, ou para causar melhor dispersão ou floculação, conhecidas como modificadores, dispersantes e depressores.
Os fatores importantes ao condicionar o minério para flotação com reagentes químicos incluem a mistura completa e dispersão dos reagentes através da polpa, contato repetido entre os reagentes e todas as partículas de minério relevantes e tempo para o desenvolvimento de contatos com os reagentes e partículas de minério para produzir as reações desejadas.
Os reagentes podem ser adicionados em várias formas, incluindo sólido, líquido imiscível, emulsão e solução em água. A concentração dos reagentes é normalmente controlada de perto durante o condicionamento. A adição de mais reagente do que o necessário pode retardar a reação e reduzir a eficiência.
A tendência atual é o desenvolvimento de células de flotação maiores e mais eficientes em termos energéticos. Uma polpa contendo minério moído, reagentes de flotação e água é alimentada às células de flotação. Normalmente, 10 a 14 células são dispostas em uma série de ásperos a necrófagos. Desbastes são usados para fazer uma separação grosseira de minerais metálicos contendo ferro (valores) da ganga. Os catadores recuperam quantidades menores de valores remanescentes da polpa. A polpa se move das células mais ásperas para as necrófagas à medida que os valores são removidos. Os concentrados recuperados da espuma nas células de desbaste e limpeza são enviados para células de limpeza para produzir o concentrado mineral metálico final com ferro.
Os coletores de flotação são de dois tipos gerais:(i) aniônicos e (ii) catiônicos. Os coletores aniônicos ionizam em solução de tal forma que a espécie ativa (aquela que se liga à superfície mineral carregada positivamente) é carregada negativamente. Por outro lado, as espécies iônicas ativas em coletores de flotação catiônica são carregadas positivamente.
A principal aplicação da flotação aniônica é a flutuação de minerais contendo ferro para longe do material de ganga. Os coletores mais comuns usados são ácidos graxos ou sulfonatos de petróleo. O óleo combustível é frequentemente adicionado junto com os coletores para promover a recuperação de partículas de óxido de ferro mais finas que cerca de 10 mícrons. Por outro lado, a flotação catiônica é usada para flutuar a ganga para longe do minério bruto finamente moído e para remover pequenas quantidades de material de ganga de alguns concentrados de minério. Os coletores catiônicos são aminas ou diaminas alifáticas primárias, beta-aminas ou aminas de éter, geralmente na forma de acetato.
Os resíduos da célula de flotação são coletados da barragem de transbordamento de rejeitos. Dependendo do grau da espuma, ela é reciclada para posterior recuperação de unidades de ferro ou descarregada como rejeitos. Os rejeitos contêm ganga remanescente, minerais de ferro não recuperados, reagentes químicos e águas residuais do processo. Geralmente, os rejeitos seguem para um espessador antes de irem para um represamento de rejeitos. O teor de sólidos da pasta varia entre 30% e 60%. Após o espessamento, os rejeitos são bombeados para um represamento e os sólidos são reciclados para posterior beneficiamento para coletar os valores remanescentes, e a água clarificada é devolvida ao processo de britagem e moagem. Na bacia de rejeitos, os sólidos são sedimentados da suspensão e o componente líquido é reciclado para o moinho. Os reagentes químicos utilizados na flotação geralmente aderem às partículas de rejeitos e permanecem no represamento de rejeitos.
Espessamento/filtragem
Os espessantes são usados para remover a maior parte do líquido de concentrados em pasta e pastas de resíduos (rejeitos). Técnicas de espessamento são geralmente empregadas em duas fases da produção de minério de ferro. Elas são (i) concentrados são engrossados para reduzir o teor de umidade e recuperar água e (ii) rejeitos em pasta são engrossados para recuperar água. As instalações geralmente empregam vários espessantes simultaneamente.
Normalmente, as operações de minério de ferro usam espessantes contínuos equipados com um mecanismo de raspagem para remover sólidos. Diversas variações de ancinhos são normalmente usadas em espessantes. Quando os concentrados estão sendo engrossados, o underflow do espessante (concentrado) é coletado e posteriormente tratado em um filtro a vácuo de disco cerâmico. O filtro remove a maior parte da água restante do concentrado. O componente líquido removido durante o processo de espessamento pode conter reagentes de flotação e/ou produtos minerais dissolvidos e suspensos. O líquido geralmente é reciclado para uma lagoa de retenção para ser reutilizado no moinho. Quando os concentrados são engrossados, o material sólido resultante dessas operações é coletado como concentrado final para aglomeração e posterior processamento. Os rejeitos engrossados são descarregados em um represamento de rejeitos.
Concentração de gravidade
A concentração gravitacional está sendo amplamente utilizada no beneficiamento de minérios de ferro hematita. Esta tecnologia é usada para suspender e transportar ganga mais leve para longe do mineral mais pesado e valioso. Este processo de separação é baseado principalmente nas diferenças nas gravidades específicas dos materiais e no tamanho das partículas que estão sendo separadas. Os valores podem ser removidos juntamente com o material de ganga (rejeitos) apesar das diferenças de densidade se os tamanhos das partículas variarem. Devido a este problema potencial, os tamanhos das partículas devem ser mantidos uniformes com o uso de classificadores (como telas e hidrociclones). Três métodos de separação por gravidade têm sido historicamente usados para minério de ferro, a saber:(i) lavagem, (ii) jigging e (iii) separadores de mídia pesada. Espirais e cones de Reichert são outros dois métodos para separação por gravidade.
Os resíduos da concentração por gravidade são rejeitos compostos de ganga na forma de partículas de granulação grossa e fina e água de processo. Este material é bombeado como uma pasta para uma bacia de rejeitos. O teor de sólidos da pasta varia a cada operação, variando entre 30% a 60%. Após a separação de sólidos em uma bacia de rejeitos, a água de rejeitos pode ser reciclada ou descartada.
Lavando
A lavagem é o processo de concentração de minério de ferro mais simples que aproveita a alta gravidade específica e o tamanho comparativamente grosseiro dos minerais contendo ferro para separá-los da ganga siliciosa, mais fina, mais leve, que é predominantemente quartzo e minerais de argila. O minério é preparado para lavagem por britagem em uma ou duas etapas até um tamanho menor que 50 mm. O minério triturado é alimentado para lavadoras de toras. A intensa agitação do minério pelas pás (semelhante a um moinho pug moderno) combinada com a água em contracorrente comuta eficientemente e remove a sílica fina para deixar um produto residual grosso rico em ferro. O transbordamento da lavadora de toras é frequentemente retraído em classificadores de ancinho ou espiral para recuperar ferro fino adicional. Algumas plantas de lavagem empregam classificadores em espiral em um ou dois estágios sem lavador de toras em minérios contendo uma quantidade mínima de ganga de argila pegajosa. Classificadores de sedimentação dificultada de vários tipos também são usados às vezes para recuperar ferro fino.
Agitando
O jigging é uma forma mais complexa de beneficiamento do que a simples lavagem e é usado nos minérios mais duros que requerem britagem para quebrar as camadas ricas em ganga. Os jigs utilizados para o beneficiamento de minério de ferro são basicamente telas horizontais que carregam um leito de minério de cerca de 150 mm a 250 mm de profundidade. O minério é alimentado em uma extremidade e é estratificado pela ação pulsante da água, seja causada por uma bomba oscilante ou pelo movimento físico para cima e para baixo da própria tela do gabarito. À medida que o minério desce pelo convés, a pulsação permite que as partículas mais leves cheguem ao topo do leito, enquanto as partículas mais pesadas, ricas em ferro, segregam ao longo da base. Os dois produtos são separados no final do gabarito, as partículas mais leves na parte superior do vertedor de descarga e o minério de ferro concentrado na parte inferior. Os gabaritos de minério de ferro funcionaram melhor nas partículas que variam de 1 mm a 25 m.
Separação de mídia pesada
Dispositivos de separação de mídia pesada foram desenvolvidos na década de 1950 como uma alternativa mais eficaz ao jigging para a atualização dos minérios de ferro. Os processos de separação de mídia pesada operam no princípio do dissipador e flutuador. Uma suspensão de ferrossilício fino (menos 200 mesh) em água é usada para criar um meio fluido com uma gravidade específica de cerca de 3,0. Partículas ricas em sílica com gravidade específica de cerca de 2,6 flutuam na superfície de tal meio, enquanto as partículas de minério de ferro mais densas e pesadas com gravidade específica superior a 4,0 se depositam no fundo. O meio convencional para concentração de minério grosso é o ferrosilício contendo 15% de silício e 85% de ferro. Suspensões aquosas contendo 64% a 85% de ferrossilício finamente moído têm densidades que variam de 2,2 a 3,6.
Os vasos de separação para minério grosso (mais 9 mm) são comumente classificadores espirais, classificadores ancinho ou tambores rotativos. Minérios mais finos que 9 mm e mais grossos que 3 mm podem ser separados em ciclones de meios pesados, onde as altas forças gravitacionais aceleram a sedimentação das partículas pesadas de minério de ferro. Magnetita finamente moída é usada para compor o meio pesado para os separadores de ciclone em vez de ferro-silício. A dinâmica do ciclone cria a densidade e a fluidez do meio necessárias, apesar da menor gravidade específica da magnetita. Além disso, o custo da magnetita é muito menor do que o ferro-silício moído.
O meio, ferrosilício e magnetita, é lavado da pia e dos produtos flutuantes em telas finas equipadas com calha de lavagem e jatos de água e é recuperado da água de lavagem com separadores magnéticos e reciclado.
Espirais
A espiral, desenvolvida inicialmente para o tratamento de areias de praia, é utilizada na concentração de minério de ferro para tratar minérios de menos 6 mesh (3,36 mm) a 100 mesh (0,149 mm). A eficiência abaixo de 100 mesh diminui rapidamente e as espirais são ineficazes em materiais mais finos. As espirais são normalmente operadas com uma densidade de polpa de 25% a 30% de sólidos.
As espirais são amplamente utilizadas para a recuperação suplementar de ferro fino de minérios comerciais e são o principal dispositivo de concentração para os minérios de hematita especular do Labrador e minérios similares que podem ser liberados por moagem não mais fina que 20 mesh.
Os concentradores espirais são dispositivos de separação de filmes fluidos. A operação geral é um fluxo laminar gravitacional contínuo para baixo em uma superfície inclinada. O mecanismo de separação envolve padrões de fluxo primário e secundário. O fluxo primário é essencialmente a pasta que flui pela calha em espiral sob a força da gravidade. O padrão de fluxo secundário é radial através da calha. Aqui, as camadas de fluido mais superiores compreendendo partículas de densidade mais alta se afastam do centro, enquanto as camadas de concentrado mais baixas de partículas de densidade mais alta se movem em direção ao centro. As espirais requerem adição de água em vários pontos ao longo da espiral para auxiliar a lavagem do minério de ferro, ou seja, transportar a ganga leve do minério denso. A quantidade de água de lavagem e sua distribuição pela calha em espiral podem ser ajustadas para atender aos requisitos operacionais. O controle de ponto minimiza os requisitos totais de água direcionando a água de forma eficiente para a polpa que flui no ângulo mais eficaz.
O concentrador espiral é uma calha de fundo curvo, enrolada em torno de um eixo vertical na forma de uma hélice. Quando alimentada no topo com uma pasta de minério de ferro e ganga, a ganga menos densa, sendo mais facilmente suspensa pela água, atinge maior velocidade tangencial do que os minerais de ferro e migra em direção à borda externa da calha espiral. A água de lavagem adicionada ao longo da borda interna ajuda a lavar a ganga mais leve. Após algumas voltas, uma faixa de mineral de ferro se forma ao longo da borda interna e a ganga forma faixas em direção à borda externa. As portas são espaçadas ao longo da borda interna para coletar e remover os minerais de ferro.
A ganga permanece na espiral e descarrega no fundo.
Cone Reichert
As principais vantagens do cone Reichert são a capacidade e a capacidade de recuperar minerais pesados finos com eficiência até cerca de 325 mesh, mais fino do que o atingível em espirais. Um único cone Reichert tem capacidade de até 100 toneladas por hora e pode ser usado efetivamente para recuperar finos de hematita especular.
O cone Reichert é um concentrador de filme fluido. As partículas mais densas concentram-se no fundo de uma película fluida de pasta com um teor de sólidos de cerca de 60% em peso. O mecanismo de separação é uma combinação de sedimentação dificultada das partículas densas e gotejamento intersticial das partículas finas. O elemento de separação na unidade Reichert é um cone de 1,9 m de diâmetro inclinado para dentro. A polpa de alimentação é distribuída uniformemente ao redor da periferia do cone. À medida que a polpa flui por gravidade em direção ao centro, as partículas finas e pesadas concentram-se no fundo e são removidas através de uma ranhura anular próxima ao ápice do cone. O rejeito flui sobre a ranhura e é coletado no ápice ou centro do cone. Como a eficiência desse processo de separação é relativamente baixa, ele é repetido várias vezes em um único arranjo empilhado de cones para aumentar a recuperação. Geralmente, o concentrado de grau mais alto é produzido no cone de separação primário.
Separação magnética
A separação magnética é normalmente usada para separar o minério de ferro magnético natural (magnetita) de uma variedade de materiais menos magnéticos ou não magnéticos. Durante a separação magnética, uma porcentagem substancial das unidades de ferro beneficiadas são perdidas para rejeitos, uma vez que a hematita é apenas fracamente magnética.
A separação magnética é conduzida em um ambiente seco ou úmido. Sistemas úmidos são mais comuns. A separação magnética de minérios de ferro pode ser categorizada como de baixa ou alta intensidade. Separadores de baixa intensidade usam campos magnéticos entre 1000 e 3000 gauss. A técnica de baixa intensidade é normalmente usada em minério de magnetita e é um método de separação barato e eficaz. O método de baixa intensidade captura apenas material altamente magnético (magnetita). O separador de alta intensidade emprega campos tão fortes quanto 20.000 gauss. Este método é usado para separar minerais de ferro fracamente magnéticos (hematita) de materiais de ganga não magnéticos ou menos magnéticos. Outros fatores importantes para determinar que tipo de sistema de separador magnético é usado incluem o tamanho das partículas e o teor de sólidos da pasta de minério.
Vários tipos de tecnologias de separação magnética são usados. Estes são descritos abaixo.
- Separação magnética de baixa intensidade (LIMS) úmida e seca
- Separação magnética de alto gradiente (HGMS)
- Separação magnética de alta intensidade úmida (WHIMS)
- Separadores magnéticos de rolo para processamento de minérios magnéticos fracos
- Separação magnética por rolo de indução (IRMS) para concentração de minérios secos
Outros mecanismos usados incluem polias magnéticas, separadores de rolos induzidos, separadores de correia cruzada e separadores tipo anel.
Normalmente, a separação magnética envolve três estágios de separação. São eles (i) cobagem, (ii) limpeza/desbaste e (iii) acabamento. Cada estágio emprega vários tambores em série para aumentar a eficiência da separação. Cada estágio sucessivo trabalha em partículas mais finas como resultado da remoção de partículas superdimensionadas em separações anteriores. Os sapateiros trabalham em partículas maiores (9 mm) e rejeitam cerca de 40% da ração como restos. A separação a seco de baixa intensidade às vezes é usada no estágio de cobagem do processo de separação. Limpadores ou scavengers trabalham em partículas na faixa de 48 mesh (0,32 mm) e removem apenas 10% a 15% da ração como restos. Por fim, os finalizadores trabalham em partículas de minério com menos de 100 mesh (0,149 mm) e removem os 5% restantes de ganga. Isto é devido à natureza altamente concentrada da alimentação nesta fase.
Processos úmidos de baixa intensidade normalmente envolvem transportadores e separadores de tambor rotativo usando ímãs permanentes e são usados principalmente em partículas de minério de 9 mm de tamanho ou menos. Nesse processo, o minério é alimentado por transportador no separador onde as partículas de magnetita são atraídas e mantidas nas laterais do tambor até serem transportadas para fora do campo magnético e transferidas para um receptor de concentrado apropriado. O material de ganga não magnético ou menos magnético permanece e é enviado para uma bacia de rejeitos. Em algumas operações, vários tambores são montados em série para maximizar a recuperação.
Separadores úmidos de alta intensidade produzem gradientes de campo magnético altos usando uma matriz de peças de ferro moldadas que atuam como locais de coleta de partículas paramagnéticas. Essas formas podem incluir esferas, hastes, placas ranhuradas, metal expandido e fibras.
Os resíduos primários desse tipo de operação são rejeitos constituídos de ganga na forma de partículas de granulação grossa e fina, e lama de efluentes no caso de separação úmida. Os resíduos particulados da separação a seco também podem ser empastados. Após a separação dos sólidos em um espessador ou tanque de decantação, os sólidos são enviados para um depósito de rejeitos e o componente líquido pode ser reciclado para a fábrica ou descarregado se os critérios de qualidade da água forem atendidos.
A separação magnética de alta intensidade úmida (WHIMS) foi desenvolvida para recuperar unidades de ferro não magnético. Elas podem ser aplicadas de forma eficaz em uma ampla faixa de tamanho de partícula de 10 mesh (2 mm) a 500 mesh, dependendo da matriz usada. As aplicações do WHIMS incluem recuperação de ferro de finos de minério natural, atualização de concentrados espirais e recuperação de hematita de rejeitos. Em separações magnéticas de alta intensidade úmida (WHIMS), os eletroímãs produzem um campo magnético de alta resistência que é aplicado a uma matriz composta por esferas de aço, placas ranhuradas espaçadas, lã de aço ou pedaços de metal expandido. A matriz está contida em um anel anular que é girado entre os ímãs de alta intensidade. A pasta de minério de ferro é introduzida em um ponto onde a matriz está no campo. Os altos gradientes magnéticos desenvolvidos ao redor da matriz retêm a hematita enquanto a ganga é lavada. O concentrado de hematita é liberado e descarregado à medida que a matriz se move para fora do campo magnético.
A Fig. 1 mostra um diagrama esquemático de uma espiral e um WHIMS.
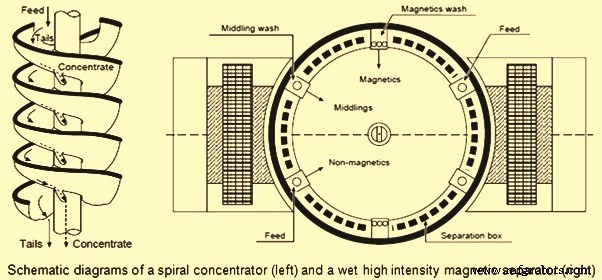
Fig 1 Diagrama esquemático uma espiral e um WHIMS
Processo de manufatura
- Introdução aos processos de pelotização e pelotização de minério de ferro
- Processo Finex para Produção de Ferro Líquido
- Processos FASTMET e FASTMELT de fabricação de ferro
- Beneficiamento de Minérios de Ferro
- Mineração de minérios de ferro
- Geologia, Prospecção e Exploração de Depósitos de Minério de Ferro
- Noções básicas sobre minérios de ferro e mineração de minério de ferro
- Processos de Beneficiamento de Minérios de Ferro
- Processos para Forjamento de Metais
- Um guia rápido para moedor centerless para venda