Entendendo as operações de pelotização e planta de pelotização
Compreendendo as operações de pellets e usinas de pelotização
A pelotização é um processo de aglomeração que converte minério de ferro de grão muito fino em bolas de uma certa faixa de diâmetro (normalmente 8 mm a 20 mm, também conhecidas como pellets. Essas pelotas são adequadas para processos de alto-forno e redução direta. pellet ou bola verde não cozida é formada e depois endurecida por aquecimento.
Pelotas de minério de ferro podem ser feitas a partir de finos de minério de ferro beneficiados ou extraídos da mina. Os minérios de ferro magros são normalmente atualizados para um teor mais alto de minério de ferro através do beneficiamento. Este processo gera torta de filtro de minério de ferro que precisa ser peletizada para que possa ser utilizada em um processo de fabricação de ferro. Também durante o processamento de minérios de ferro de alto teor que não necessitam de beneficiamento, os finos gerados podem ser pelotizados e utilizados ao invés de serem descartados.
As usinas de pelotização podem estar localizadas em minas, perto de portos ou podem ser anexadas a usinas siderúrgicas. Equipados com tecnologia ambiental avançada, são praticamente livres de poluição, não gerando resíduos sólidos ou líquidos.
Histórico de pelotização
A história dos pellets começou em 1912, quando A.G.Andersson, um sueco, inventou um método de peletização. O uso comercial de pellets, no entanto, começou nos EUA após a Guerra Mundial. Vários estudos foram realizados nos EUA com o objetivo de desenvolver as vastas reservas de taconita (minério de ferro de baixo teor) na área ao redor dos Grandes Lagos. O processo de enriquecimento do minério de taconita envolveu a moagem do minério para remover as gangas e a atualização do minério de ferro (ou seja, um processo de beneficiamento do minério). O minério de alto teor resultante está na forma de partículas finas, tão pequenas quanto 0,1 mm ou menos, que não são adequadas para sinterização. Essa questão levou ao desenvolvimento do processo de pelotização.
Em 1943, o Dr. Davis, professor da Universidade de Minnesota, Estação Experimental de Minas, e seus associados inventaram um método para processar taconita contendo minério de ferro de baixo teor. Sua invenção mostrou que era possível bolar ou peletizar concentrado de magnetita fina em um tambor de bolas e que se as bolas fossem disparadas a uma temperatura suficientemente alta (geralmente abaixo do ponto de fusão incipiente) um pellet duro e endurecido bem adaptado para uso na explosão forno, poderia ser feito. Consequentemente, apesar dos benefícios inquestionáveis do desempenho da sinterização no alto-forno (BF), o intenso interesse no processo de pelotização se desenvolveu devido ao excelente desempenho alcançado pelas siderúrgicas em operações prolongadas com pelotas como o principal material de suporte de ferro na carga do alto-forno.
Espera-se que as usinas de pelotização desempenhem um papel importante em uma era em que a reserva global de minério granulado de alto teor está diminuindo. As usinas promovem a concentração de minérios de ferro de baixo teor em pelotas atualizadas, que serão cada vez mais utilizadas por altos-fornos e fornos de redução direta nos próximos anos.
Pelotas de minério de ferro
As pelotas de minério de ferro podem ser pelotas ácidas ou básicas. As pelotas ácidas também são chamadas de pelotas de grau DRI (ferro reduzido direto), enquanto as pelotas básicas também são conhecidas como pelotas de grau BF ou pelotas fundidas.
- Pellets de grau DRI – A basicidade desses pellets é geralmente inferior a 0,1. A resistência do pellet queimado é, até certo ponto, devido às pontes de hematita de estrutura policristalina. Esses pellets normalmente possuem grande volume de poros abertos. O gás de redução penetra rapidamente através desses poros no núcleo do pellet e simultaneamente ataca a estrutura em muitos lugares. Isso resulta em uma mudança estrutural precoce que começa em baixas temperaturas em todo o volume do pellet.
- Pellets de grau BF – A basicidade desses pellets é maior que 0,1 e pode variar. A basicidade dos pellets básicos normais varia de 0,1 a 0,6 e tem baixa porcentagem de CaO. Durante a queima desses pellets, uma fase de escória vítrea consistindo de SiO2, CaO e Fe2O3 em porcentagem variável é formada. Devido ao aumento da adição de fluxo, há formação de alguma escória e devido a isso, há uma certa ligação da escória com os cristais de minério de ferro. Os pellets de alta basicidade têm um nível de basicidade maior que 0,6. Esses pellets contêm maior nível de CaO. Esses pellets não só possuem fase vítrea composta principalmente por SiO2, CaO e Fe2O3, mas também ferritas de cálcio (CaO.Fe2O3). Durante a queima desses pellets, a disponibilidade de CaO favorece consideravelmente o crescimento de cristais de hematita. Esses pellets normalmente possuem uma alta resistência mecânica após a queima do pellet. As pelotas fundidas exibem boa resistência, redutibilidade melhorada, características de intumescimento e derretimento de amolecimento. Devido a essas propriedades, essas pelotas apresentam melhor desempenho no alto-forno.
A qualidade das pelotas é influenciada pela natureza do minério ou concentrado, ganga associada, tipo e quantidade de fundentes adicionados. Esses fatores, por sua vez, resultam na variação das propriedades físico-químicas das fases coexistentes e sua distribuição durante o endurecimento do pellet. Portanto, as propriedades das pelotas são amplamente regidas pela forma e grau de ligação alcançado entre as partículas de minério e a estabilidade dessas fases de ligação durante a redução de óxidos de ferro. Como a formação de fases e microestrutura durante o endurecimento depende do tipo e da quantidade de fundentes adicionados, há um efeito dos fundentes em termos de relação CaO/SiO2 e teor de MgO na qualidade do pellet.
Mineralogicamente as pelotas compreendem essencialmente partículas de hematita (sobreviventes originais) de minério de ferro, sílica cristalina (quartzo, cristobalita e tridimita) e forsterita (Mg2SiO4). A principal variação na mineralogia do pellet está na proporção de fases de ganga presentes no produto. Estes irão variar dependendo do material de alimentação do pellet e do tipo e quantidade de quaisquer aditivos para alimentação, como calcário, dolomita, olivina e bentonita, etc.
A resistência das pelotas de minério de ferro é importante para minimizar a degradação por quebra e abrasão durante o manuseio e transporte e no alto-forno. Acredita-se que a forte ligação em pellets seja devido ao crescimento de grãos da oxidação acompanhante de magnetita para hematita, ou recristalização de hematita. Embora a ligação de escória possa promover um fortalecimento mais rápido em temperaturas de queima ligeiramente mais baixas, a resistência do pellet é normalmente diminuída, especialmente a resistência ao choque térmico. A resistência do pellet é mais comumente determinada por testes de compressão e tombo. As resistências à compressão de pellets individuais dependem da composição mineralógica e das propriedades físicas do concentrado, dos aditivos usados, do método de formação de bolas, do tamanho do pellet, da técnica e temperatura de queima e do procedimento de teste. As resistências à compressão de pellets comercialmente aceitáveis estão geralmente na faixa de 200 a 350 kg para pellets na faixa de tamanho de 9 mm a 18 mm. No teste do tambor 11,4 kg de pellets de +6 mm são rotacionados por 200 rotações a 25 rpm em um tambor tambor (ASTM E279-65T) e depois peneirados. Um pellet comercial satisfatório não deve conter mais do que cerca de 5% de finos de 0,6 mm menos (menos 28 mesh) e 94% ou mais de tamanho mais 6 mm, após o teste do tambor. Um mínimo de pellets quebrados entre 6 mm e 0,6 mm de tamanho também é desejável. Outras propriedades importantes das pelotas a serem usadas na alimentação do alto-forno são redutibilidade, porosidade e densidade aparente. Com alguns concentrados, estes podem variar dentro de certos limites.
Processo de pelotização
Uma planta de pelotização normalmente tem quatro etapas de processo, a saber, (i) recebimento de matérias-primas, (ii) pré-tratamento, (iii) esférico e (iv) endurecimento e resfriamento. Essas etapas do processo são descritas abaixo.
Recebimento de matérias-primas
A localização de uma usina de pelotização afeta o método de recebimento de matérias-primas como minério de ferro, aditivos e ligantes. Muitas usinas de pelotização estão localizadas próximas a minas de minério de ferro. Isso porque essas usinas são instaladas para pelotizar os minérios de ferro que são beneficiados nessas minas. Tais usinas recebem o minério de ferro por via férrea e/ou minerodutos. Muitas outras usinas de pelotização estão instaladas longe das minas de minério de ferro. Essas usinas são independentes das minas de minério de ferro. Essas usinas recebem minério de ferro principalmente por trilhos. alguma planta pode receber por oleoduto de longa distância. Nas usinas de pelotização localizadas no porto que dependem do minério de ferro importado, o método de recebimento envolve o transporte do minério em navio dedicado, descarregando o minério em um cais e estocando em um pátio. O minério de ferro geralmente é enviado para essas usinas a granel para máxima economia.
Processo de pré-tratamento
No processo de pré-tratamento, o minério de ferro é moído em finos com tamanhos necessários para o subsequente processo de balling. O pré-tratamento inclui concentração, desidratação, moagem, secagem e pré-umedecimento. Geralmente, minérios de ferro de baixo teor são moídos em finos para enriquecer a qualidade do minério, para remover gangas contendo enxofre e fósforo e para controlar o tamanho dos grãos. No caso de minérios de magnetita, separadores magnéticos são empregados para recalque e remoção de ganga. Por outro lado, com minérios hematíticos, essas operações são realizadas por beneficiamento por gravidade, flotação e/ou separadores magnéticos de alta intensidade do tipo úmido. Os métodos de moagem podem ser categorizados aproximadamente de acordo com os três aspectos a seguir.
- Moagem a seco ou moagem úmida
- Moagem de circuito fechado ou retificação de circuito aberto
- Retificação em estágio único ou retificação em vários estágios
Esses métodos são usados em combinação dependendo dos tipos e características dos minérios de ferro e da proporção de mistura, além de levar em consideração os fatores econômicos. Os sistemas de moagem úmida precisam de unidades de desaguamento com espessante e filtro, enquanto os sistemas de moagem a seco requerem unidades de pré-umedecimento. A pré-molhagem é geralmente associada à moagem a seco. A pré-molhagem inclui a adição de uma quantidade adequada de água homogeneamente ao material moído a seco para preparar o material pré-molhado adequado para a formação de bolas. Este é um processo para ajustar as características do material que afetam significativamente a qualidade do pellet. Ocasionalmente, a composição química dos pellets do produto também é ajustada neste processo para produzir pellets de alta qualidade.
Aglutinantes, como bentonita, argila, cal hidratada ou um aglutinante orgânico, são geralmente usados para aumentar a resistência à umidade das bolas verdes para níveis mais aceitáveis para manuseio. O consumo de bentonita na taxa de 6,3 a 10 kg por tonelada de ração é um elemento de custo significativo e aumenta o teor de sílica do produto final.
A adição de cal e/ou dolomita ao minério ajusta as pelotas para que tenham a composição química desejada.
Esforços consideráveis têm sido feitos para a redução do uso de bentonita e para o desenvolvimento de substitutos mais baratos. A capacidade de bola e a resistência das bolas verdes são influenciadas pelos aditivos e pelo teor de umidade e distribuição granulométrica dos concentrados. O teor de umidade ideal para um bom balling está geralmente na faixa de 9% a 12%. Parece que as características do balling são relativamente independentes da composição química de um concentrado, mas são fortemente afetadas por suas propriedades físicas. Por exemplo, as hematitas especulares são mais difíceis de formar bolas do que os concentrados de magnetita por causa da estrutura tipo placa das partículas de hematita especular. Em qualquer caso, a formação satisfatória de pellets é geralmente alcançada por moagem de cerca de 80% a 90% menos 43 micrômetros (menos 325 mesh). Normalmente, qualquer material considerado para peletização deve conter pelo menos 70% menos 43 micrômetros (menos 325 mesh) e ter uma área de superfície específica (Blaine) maior que 1200 sq cm/gram para características adequadas de balling.
Processo de arremesso
Neste processo, o equipamento de balling produz bolas verdes a partir do material pré-molhado preparado no processo anterior. O tambor balling e o disco peletizador são os dispositivos mais utilizados para a formação de bolas verdes. Ambas as unidades utilizam a força centrífuga para formar os materiais finos em esferóides.
As bolas verdes produzidas por um tambor não são uniformes em diâmetro. Uma parte significativa da descarga (cerca de 70%) é menor do que o tamanho do alvo e geralmente é devolvida ao tambor após a triagem. É difícil ajustar a operação do tambor para condições variadas de matéria-prima. A operação, no entanto, é estável para condições uniformes de matéria-prima (composição química, tamanho de partícula, umidade, etc.).
Comparado com o tambor balling, o peletizador de disco tem as vantagens de menor peso e maior possibilidade de ajuste. Seu design inerente calcula a média do efeito de flutuações instantâneas na alimentação, enquanto o tambor não. A peletizadora de disco classifica as bolas verdes por si só, reduzindo a quantidade de pellets devolvidos. A ação classificadora do disco promove a descarga de bolas de tamanho mais uniforme, o que simplifica o peneiramento do produto. A operação da peletizadora de disco pode ser facilmente ajustada para diferentes condições de matéria-prima, alterando a rotação, o ângulo de inclinação e a profundidade do disco. No entanto, a capacidade dos discos é baixa e os discos geralmente exigem um controle mais próximo do que os tambores.
O melhor controle do tamanho da esfera é alcançado quando o dispositivo de esfera está em circuito fechado com uma tela para remover e reciclar o material subdimensionado. Tanto a resistência à queda quanto à compressão dos pellets verdes são importantes.
Processo de endurecimento
A queima de pellets estabelece a ligação das partículas de hematita a uma temperatura elevada variando de 1250°C a 1350°C em condição oxidante. A escória com baixo ponto de fusão pode se formar nos pellets durante esta etapa de queima, se a matéria-prima contiver ganga fundida ou se for adicionado calcário a ela. Nestes casos, o produto pode ter uma estrutura intermediária com ligação de hematita e ligação de escória. O processo de queima é caracterizado por temperaturas de processo inferiores às exigidas pela sinterização que requer a fusão parcial e a sinterização do minério fino misturado com coque brisa, combustível que gera calor de combustão.
Três sistemas são normalmente usados para o endurecimento de pellets. São eles:(i) sistema de forno de cuba vertical, (ii) sistema de grelha reta ou grelha móvel e (iii) sistema de grelha – forno resfriador. Cada sistema foi usado comercialmente para fazer pelotas de qualidade aceitável e, portanto, fatores de custo de capital e operacional geralmente estão envolvidos na escolha de um ou outro sistema.
A oxidação da magnetita em hematita durante a peletização fornecerá uma proporção significativa, em torno de 100 M cal por tonelada da necessidade de calor em todos os sistemas. Para peletização de hematitas, o uso de coque brisa (ou alguma fonte de carbono) na mistura de pellet feed tornou-se uma prática comum para fornecer a energia de endurecimento adicional normalmente fornecida pela oxidação da magnetita.
O sistema de forno de eixo vertical é a instalação mais tradicional. No entanto, os fornos de cuba vertical não são tão comuns como os sistemas de grelha móvel ou forno de grelha. Existem várias variações no projeto do forno de cuba, mas o mais comum é o tipo Erie, mostrado na Fig. 1. As esferas verdes são carregadas no topo e descem através do forno a uma taxa de 25 a 40 mm por minuto em contracorrente ao fluxo de gases quentes. Cerca de 25% do ar total entra no forno através da entrada de gás quente em temperaturas de 1280 graus C a 1300 graus C. Os pellets nesta zona do forno atingem temperaturas de 1315 graus C ou mais porque calor exotérmico é liberado quando a magnetita oxida à hematita, aumentando a temperatura. Os 75% restantes do ar do forno entram pela entrada de ar de resfriamento. Os pellets são descarregados a cerca de 370°C e a temperatura do gás no topo é de cerca de 200°C. As capacidades típicas do forno são de 1.000 a 2.000 toneladas por dia.
Os fornos de eixo são mais eficientes em termos energéticos do que os sistemas de grelha móvel ou forno de grelha. O forno de poço é adequado para a peletização de magnetita, mas não de materiais de minério hematítico ou limonítico. As desvantagens dos fornos de cuba são a baixa produtividade unitária e a dificuldade em manter a temperatura uniforme na zona de combustão. Podem ocorrer pontos quentes que fazem com que os pellets se fundam em grandes massas, produzindo problemas de descarga. Também é muito difícil produzir pelotas fundidas em um forno de cuba. O diagrama esquemático típico do sistema de forno de poço vertical é mostrado na Fig 1.
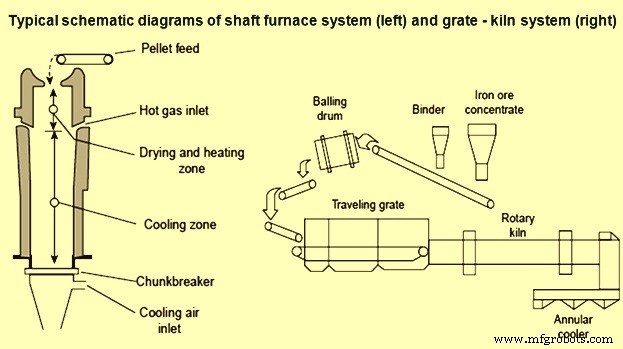
Fig 1 Diagrama esquemático típico de sistemas de eixo vertical e grelha-forno
Um sistema de grelha reta surgiu na indústria logo após os fornos de cuba. É essencialmente uma modificação do processo de sinterização. As bolas verdes são alimentadas na grelha continuamente para fornecer uma profundidade de leito de cerca de 300 mm a 400 mm e são secas nas primeiras caixas de vento por ar ascendente recuperado da zona de queima, seguido de secagem descendente usando ar recuperado do resfriador. Este arranjo de fluxos de ar quente limita os danos dos pellets resultantes da condensação de umidade no leito. Após a secagem, os pellets são pré-aquecidos por ar descendente da zona de resfriamento. A queima é feita a jusante na zona de combustão pela queima de óleo combustível ou gás natural com ar quente da zona de resfriamento. A zona de resfriamento segue a zona de combustão e usa ar fresco ascendente.
O sistema de grelha móvel para produção de pellets consiste em uma única unidade que movimenta uma camada estática de pellets. O sistema possui uma estrutura simples para secagem, pré-aquecimento, queima e resfriamento de pellets. Devido à sua relativa facilidade de operação, juntamente com a facilidade de ampliação, torna o sistema utilizado por muitas plantas.
O consumo de combustível no sistema de grelha móvel é de cerca de 85-140 M cal por tonelada de pellets produzidos a partir de magnetita e até 240 M cal por tonelada ao peletizar hematita. O sistema oferece um bom controle de temperatura na zona de queima. A consistência dos pellets em todo o leito pode ser alcançada pela recirculação de alguns pellets queimados para formar camadas laterais e de lareira na grelha. As grandes máquinas de grelha têm 4 m de largura e são capazes de produzir mais de 3 milhões de toneladas de pellets por ano. Máquinas de grelha circular também foram projetadas e estão em operação. Um diagrama esquemático típico do sistema de grelha reta é mostrado na Fig 2.
Fig 2 Diagrama esquemático típico do sistema de grelha reta
O sistema grelha-forno representado na Figura 1 consiste em uma grelha móvel para secar e pré-aquecer os pellets a cerca de 1040°C, um forno rotativo para aquecer uniformemente o rendimento até a temperatura final de endurecimento de 1315°C e um resfriador anular para resfriamento o produto e a recuperação de calor. O calor para queima é fornecido por um queimador central de óleo, gás, carvão ou resíduos de madeira na extremidade de descarga do forno. Os gases quentes produzidos no forno são utilizados para o pré-aquecimento da corrente descendente dos pellets. O ar quente do resfriador é usado para suportar a combustão no forno e também é recuperado para a grelha móvel para secagem e pré-aquecimento do revenido.
O sistema de grelha-forno oferece excelente controle de temperatura em todas as etapas do processo e produz um pellet de qualidade consistentemente uniforme. O consumo de combustível é de 75 M cal a 100 M cal por tonelada de pellets padrão produzidos ao usar minério de magnetita, e até 170 M cal por tonelada de pellets padrão produzidos quando a ração é hematita. Esses números de consumo de combustível aumentam em 60 M cal por tonelada ao produzir pelotas fundidas. O consumo de energia, desde o balling até o carregamento do pellet, é de cerca de 23 kWh por tonelada.
O sistema de grelha-forno é fácil de controlar e os pellets do produto têm uma qualidade uniforme. Também pode ser dimensionado para um grau bastante grande. Os sistemas de forno de grelha podem ser projetados para capacidades de produção de até 6 milhões de toneladas por ano por linha. Esses sistemas são usados por muitas plantas.
Os processos de pelotização estão sendo aprimorados constantemente. A produção de pelotas autofluxantes é um exemplo de inovação que vem sendo aceita em escala comercial e tem levado a grandes avanços no desempenho dos altos-fornos. Outros artigos sobre pellets e processo de peletização estão disponíveis nos links a seguir.
http://www.ispatguru.com/iron-ore-pellets-and-pelletizing-processes/
http://www.ispatguru.com/iron-ore-pellets/
http://www.ispatguru.com/iron-ore-pellets-and-pelletization-process/
Processo de manufatura
- Aniversários e prêmios
- Entendendo o aço ferramenta e como ele é feito
- Propriedades e graus do ferro cinzento explicados
- Entendendo o ferro forjado
- Propriedades e Composição do Ferro Gusa
- Entendendo o processo de fundição de minério de ferro
- Entendendo o parafuso e o parafuso
- Entendendo a manutenção da planta
- Entendendo o processo de usinagem e a máquina-ferramenta
- Entendendo os pneus com câmara e sem câmara