Seleção de carvão para inclusão na mistura de carvão na fabricação de coque
Seleção de carvão para inclusão na mistura de carvão na fabricação de coque
A mistura de carvões é necessária do ponto de vista econômico, reduzindo a porcentagem de carvões de alto custo, primários ou duros e substituindo-os por carvões médios ou macios. Em algumas coquerias, até mesmo uma pequena porcentagem de carvões não-coqueificáveis ou a vapor também foi usada na mistura.
A seleção de uma mistura de carvão adequada para uso em fornos de coque de subprodutos é sempre um grande desafio para o produtor de coque, uma vez que a mistura deve atender aos seguintes requisitos.
- É para atender à exigência de britagem durante a preparação do carvão. Todos os componentes dos carvões não devem ser esmagados ou esmagados. A mistura de carvão dimensionada para carregar os fornos de coque deve atender aos requisitos de densidade, fluxo e frações de tamanho.
- É ter as propriedades de coqueamento e aglomeração necessárias para a produção de coque de qualidade que atenda aos requisitos de qualidade do coque de alto-forno (BF). Os três requisitos básicos de qualidade do coque BF são (i) fornecer calor para as reações endotérmicas que ocorrem no alto-forno, (ii) atuar como agente redutor produzindo os gases de redução necessários e (iii) fornecer uma camada permeável suporte no BF para a carga de rolamento de ferro.
- É para fornecer desempenho de empurrão seguro em fornos de coque. Não deve exercer pressão excessiva sobre as paredes do forno de coque durante o processo de coqueificação e danificá-las.
- Deve atender aos requisitos de rendimento não apenas do coque BF, mas também do gás de coqueria. Uma mistura de carvão adequada não produzirá coque excessivo e brisa de coque.
- É ser econômico.
Tendo em conta os vários tipos de requisitos acima referidos, as decisões relativas às misturas de carvão não são tomadas numa base ad hoc, mas após cuidadosas considerações. Na verdade, a mistura de carvão precisa ser projetada para que um equilíbrio possa ser alcançado entre os conjuntos concorrentes de requisitos, como rendimento, alta qualidade e eficiência de custos, etc., mantendo a importância da vida útil da bateria em mente.
Com os requisitos acima em mente, os esforços de projeto da mistura de carvão precisam ser focados em (i) satisfazer as propriedades físicas do coque, (ii) satisfazer as propriedades químicas do coque, (iii) satisfazer o desempenho de empurrar o forno de coque, (iv) satisfazer uso máximo de materiais de carbono de baixo valor (carvões macios), (v) para atender aos requisitos econômicos e (vi) para garantir a disponibilidade contínua de frações de carvão para evitar mudanças frequentes de mistura. (Figura 1)
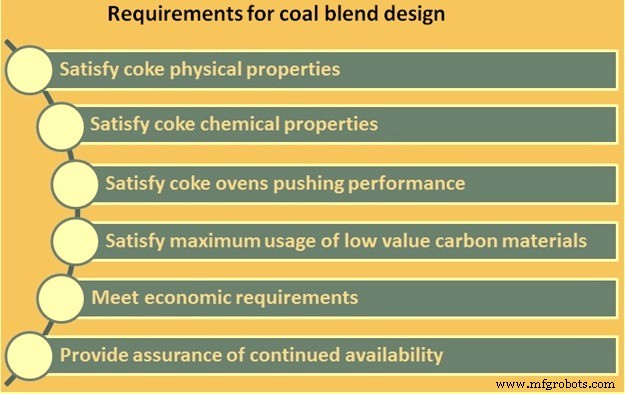
Fig 1 Requisitos do projeto de mistura de carvão
Normalmente, o projeto da mistura de carvão é feito através de uma série de etapas. Essas etapas também são necessárias para qualquer adição de novo carvão na mistura e são explicadas abaixo.
- Estudar a qualidade dos carvões a serem incluídos na mistura conforme a ficha de qualidade dos carvões fornecida pelo fornecedor. Com base na ficha técnica, a qualidade é avaliada para o uso de carvão na mistura. Também é determinado o custo e a disponibilidade a longo prazo do carvão. Uma vez que esses parâmetros são satisfeitos preliminarmente, uma amostra de 5 kg é solicitada.
- A partir desta amostra de 5 kg, são realizados diferentes testes de laboratório para determinar as qualidades do carvão e também para ter certeza de que essas qualidades estão de acordo com a ficha técnica do fornecedor. Esses resultados de teste decidem quanta porcentagem de carvão pode ser usada na mistura de carvão. Uma avaliação econômica preliminar é então realizada para o carvão. Ao obter uma avaliação satisfatória, uma quantidade suficiente de carvão é solicitada para testes de carbonização em forno piloto.
- Os testes de carbonização em forno piloto são normalmente realizados (i) em 100% de carvão novo, bem como (ii) na mistura de carvão com a porcentagem de carvão novo planejada na mistura. Durante a carbonização do forno piloto, também são realizados testes de contração e pressão do gás. Se os testes de carbonização do forno piloto forem bem-sucedidos, o carvão será usado na porcentagem planejada na mistura de carvão para os testes da planta. Durante os testes da planta, é realizado um monitoramento rigoroso de todos os parâmetros.
- Depois que os testes da planta são bem-sucedidos, o carvão é adotado para uso regular na mistura.
No entanto, a seleção final de carvão para adição à mistura também leva em consideração o preço, os requisitos da planta de preparação de carvão e o controle de qualidade necessário durante a aquisição.
As propriedades do carvão que devem ser focalizadas durante o projeto da mistura de carvão são dadas abaixo.
Design de mistura de carvão para propriedades físicas de coque
As propriedades físicas do coque que são importantes para a operação estável do alto-forno são (i) índice de reatividade do coque (CRI), resistência do coque após a reação (CSR) e (iii) índice de micum.
O CRI mede a capacidade do coque de resistir à quebra à temperatura ambiente e reflete o comportamento do coque fora do alto-forno e na parte superior do alto-forno. O CSR dá indicação da resistência do coque após ser exposto à atmosfera redutora do alto-forno. Ele mede o potencial do coque para quebrar em tamanho menor sob altas temperaturas de CO/CO2 ambiente que existe ao longo dos dois terços inferiores do alto-forno. O índice Micum é um teste de tambor e indica a resistência do coque à temperatura ambiente. Valores maiores de M40 (porcentagem de coque restante no furo redondo de +40 mm após 100 revoluções) e valores menores de M 10 (coque de furo redondo de -10 mm após 100 revoluções) normalmente indicam coque com maior resistência.
A análise petrográfica do carvão é uma ferramenta importante para prever a resistência do coque. As propriedades importantes do carvão para a previsão da resistência do coque são as seguintes.
- Número de dilatação do cadinho (CSN) – O intervalo de CSN em carvões de coque é de 3 no mínimo a 6 no máximo. Os carvões de coque primário têm valores de CSN mais altos, enquanto os carvões de coque macios têm valores de CSN baixos.
- Dilatação máxima – O valor da dilatação máxima é de 55% no mínimo. Depende do valor da dilatação máxima dos componentes da mistura de carvão.
- Fluidez máxima – O valor da fluidez máxima é de 600 ddpm mínimo em carvões de coque. Maior fluidez proporciona melhor fluidez nos fornos de coque.
- Tipo de coque cinza rei – O valor do cinza rei deve ser G 5 mínimo em carvões de coque. Para carvão coqueificável macio, o limite do valor Gray king é G min.
- Refletância Máxima Média (MMR) – O valor da MMR em carvões de coque variam na faixa de 0,85% – 1,35%. Carvões coqueificáveis macios têm MMR mais baixo, enquanto carvões coqueificáveis duros têm MMR mais alto.
- Vitrinita – O valor da vitrinita em carvões de coque é mínimo de 50%. Para carvões de coque macios, o limite é de 45%.
- Distribuição de vitrinita (V9 – V14) – O valor da distribuição de vitrinita em carvões de coque é mínimo de 70%.
Design de mistura de carvão para tamanho de coque
O tamanho do coque formado é influenciado pela quantidade de componentes inertes presentes na mistura de carvão. À medida que o teor de inertes diminui, o tamanho do coque diminui. Assim, o tipo de carvão influencia o tamanho do coque. O tamanho do coque também é altamente dependente das variáveis operacionais. Na prática normal, o tamanho do coque para alto-forno é controlado principalmente por peneiramento.
Projeto de mistura de carvão para rendimento de gás de coqueria e forno de coque
A quantidade de coque produzida em um forno de coque é inversamente proporcional à matéria volátil do carvão. A faixa de matéria volátil do carvão também é importante para a produção de coque de alta resistência. A matéria volátil do carvão também influencia o rendimento do gás de coqueria, que muitas vezes é um parâmetro importante para o balanço de gás na siderurgia.
Projeto de mistura de carvão para propriedades químicas de coque
Com um conjunto fisicamente estável de matérias-primas no alto-forno, o controle adicional do processo do alto-forno é obtido através do controle das propriedades químicas. As propriedades químicas mais importantes do coque são umidade, carbono fixo, cinzas, enxofre, fósforo e álcalis. A maioria dessas propriedades depende principalmente dos carvões usados. Cinzas de coque, enxofre e álcalis afetam negativamente a CSR. No entanto, o fósforo afeta positivamente a CSR, mas é indesejável, pois entra completamente no metal quente. Para obter um coque de alta qualidade e alto rendimento, é desejável que a mistura de carvão contenha baixas quantidades de umidade, cinzas, enxofre, álcalis, fósforo e alto teor de carbono fixo. Além disso, a temperatura de fusão das cinzas é uma propriedade importante para o processo de coqueificação. Deve ser superior à temperatura de coqueificação.
Design de mistura de carvão para melhor desempenho do forno de coque
A pressão máxima de coqueificação não deve exceder 0,14 kg/sq cm. De todas as propriedades inerentes do carvão, a graduação e o conteúdo inerte parecem ser de importância primordial para a pressão de coqueamento nas paredes do forno de coque. A classificação tem relação direta com a pressão de coqueificação. Carvões de baixa volatilidade exercem pressão excessiva de coqueificação. No entanto, eles também contribuem para a alta resistência do coque e produzem altos rendimentos de coque.
Carvões de classificação semelhante, mas possuindo altas inertinitas, produzem menor pressão. Os carvões australianos de baixa volatilidade geralmente produzem baixa pressão de parede e são incluídos em misturas para reduzir a pressão de coqueificação. Devido à dificuldade de medir a pressão de coqueamento (parede) em um forno comercial, as medições de pressão de parede e pressão de gás de um forno piloto são geralmente correlacionadas com medições de pressão de gás em fornos comerciais. Uma vez estabelecida a correlação, as medições de pressão do gás na instalação comercial são usadas para monitorar a pressão de coqueificação. A pressão do gás aumenta com a classificação e diminui com o teor de inertinita.
A contração da carga do carvão ocorre durante duas fases diferentes do processo de coqueificação. A primeira fase está presente durante a formação da camada plástica e depende principalmente das propriedades do carvão. Uma vez que as camadas plásticas se transformaram em semi-coque, a segunda fase começa durante a retração do semi-coque e depende principalmente das condições de operação. Geralmente os valores máximos de fluidez são usados para prever a primeira fase da contração lateral. A contração vertical depende principalmente de parâmetros operacionais, como temperatura de coqueamento e taxa de aquecimento.
Design de mistura de carvão para maximizar o uso de materiais de carbono de baixo valor
A fim de reduzir os custos operacionais mantendo a qualidade do coque, materiais de carbono de baixo valor são adicionados em quantidades variadas às misturas de carvão. Carvões moles, finos de carvão, coque brisa, alcatrão de carvão, coque de petróleo, asfaltenos (resíduos de destilação) e carvões não coqueificáveis demonstraram ter um efeito positivo na qualidade do coque e na operação de coqueamento, desde que adicionados na quantidade certa e para o tipo certo de mistura. Tais práticas resultaram em menor custo, melhor operação e conservação de recursos.
Carvões oxidados (intemperizados) também devem ser considerados como material de carbono de baixo valor, pois a oxidação geralmente resulta em uma queda na CSR, estabilidade, tamanho do coque, rendimento do coque e geralmente piora as características de expansão e pressão da parede. O CSR é mais sensível à oxidação do carvão; a magnitude da queda de CSR é maior para os carvões de classificação mais baixa. Portanto, o uso de carvão oxidado deve ser minimizado.
Design de mistura de carvão para atender aos requisitos econômicos
A avaliação tecnológica da mistura de carvão deve ser complementada por uma avaliação econômica do custo de utilização do coque produzido. Um carvão com baixo custo por tonelada pode não ser econômico quando o coque produzido a partir dele e seu uso no alto-forno são considerados de forma integrada. Isso porque a qualidade do carvão pode afetar negativamente o rendimento de coque na bateria do forno de coque e o consumo de coque BF no alto-forno, além de afetar negativamente a produtividade do alto-forno. Portanto, o design da mistura de carvão é para garantir que seja econômico no ponto de uso e não que pareça econômico em fornos de coque. A mistura de carvão que produz o coque com maior potencial de economia de custos no alto-forno normalmente deve ser adotada para implementação na coqueria.
Projeto de mistura de carvão com garantia de disponibilidade contínua de carvão
Para evitar mudanças frequentes na mistura de carvão, os carvões que não estão disponíveis a longo prazo devem ser evitados para serem considerados para inclusão na mistura.
O procedimento descrito acima para a seleção de carvão para inclusão na mistura de carvão na fabricação de coque explica que existe a necessidade de alcançar um equilíbrio entre os requisitos de rendimento, alta qualidade de coque, vida útil da bateria, eficiência de custo e economia geral com garantia de um fornecimento consistente de carvões.
Processo de manufatura
- Quando vale a pena fazer mudanças na engenharia de design industrial?
- Fazendo um telêmetro a laser barato para Arduino
- Fabricação de moldes para embalagens farmacêuticas
- Guia de seleção de materiais para usinagem CNC
- Processo de seleção do local para uma usina siderúrgica de campo verde
- Tecnologias para Melhoria do Processo de Coqueamento em Fornos de Coque de Subprodutos
- Recuperação de amônia durante a produção de coque de carvão de coque
- Defendendo o 5G na fabricação
- Punções e matrizes de qualidade para fabricação de ferramentas
- Qual é o critério de seleção para escolher um redutor?