5 maneiras de entender desenhos de usinagem complexos
1. O método de dimensionamento da estrutura comum
Método de dimensionamento de furo comum:
Buraco cego
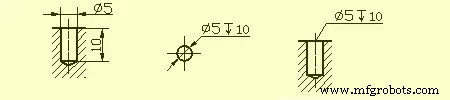
Orifício rosqueado
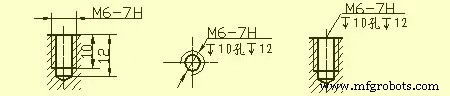
Rebaixamento
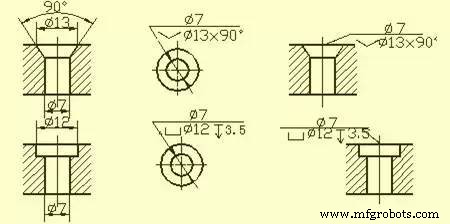
Orifício de rebaixamento
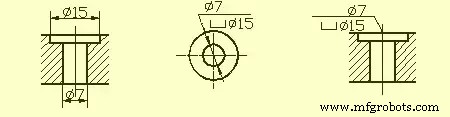
O método de dimensionamento do chanfro
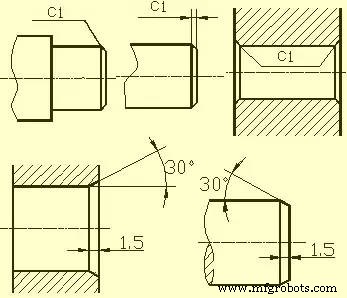
2. Estrutura de usinagem em peças
Rebaixo e sulco de sobrecurso do rebolo
Quando as peças são cortadas, a fim de facilitar a retirada da ferramenta e garantir que as superfícies de contato das peças relevantes estejam próximas durante a montagem, a ranhura de rebaixo ou a ranhura de sobrecurso do rebolo deve ser pré-usinada na etapa da superfície processada .
O tamanho do rebaixo ao girar o círculo externo geralmente pode ser marcado como “largura da ranhura × diâmetro” ou “largura da ranhura × profundidade da ranhura”. Ranhura de sobrecurso do rebolo ao retificar o círculo externo ou retificar o círculo externo e a face final.
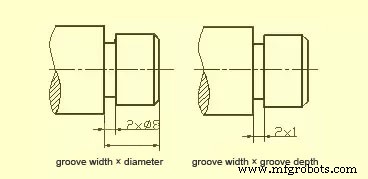
Um furo cego feito com uma broca tem um ângulo de cone de 120° na parte inferior. A profundidade de perfuração refere-se à profundidade da peça cilíndrica, excluindo o poço do cone. Na transição da furação escalonada, há também um ângulo de cone de mesa redonda de 120°, seu desenho e notação de tamanho.
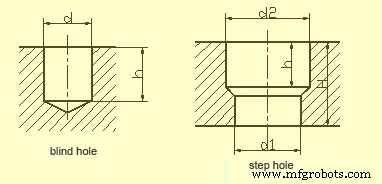
Ao perfurar com uma broca, é necessário que o eixo da broca esteja o mais perpendicular possível à face final do furo perfurado para garantir a precisão da perfuração e evitar que a broca se quebre. A estrutura correta das três faces finais de perfuração.
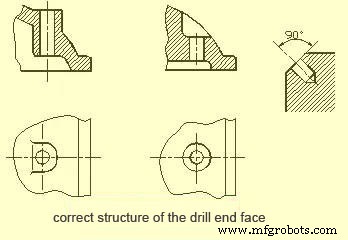
Chefes e poços
A superfície de contato de uma peça com outras peças é geralmente processada. Para reduzir a área de processamento e garantir um bom contato entre as superfícies das peças, muitas vezes são projetados ressaltos e poços nas peças fundidas. Ressalto da superfície de suporte aparafusado ou forma rebaixada da superfície de suporte. para reduzir a área de processamento, é feita uma estrutura de ranhura.
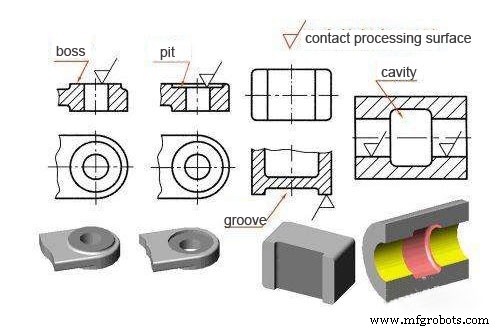
3 Estrutura de peças comuns
Peças do eixo
Tais peças geralmente incluem eixos, buchas e outras peças. Ao expressar as vistas, contanto que você desenhe uma vista básica e adicione vistas e dimensões de seção transversal apropriadas, você pode expressar seus principais recursos de forma e estrutura local. Para facilitar a visualização das imagens durante o processamento, geralmente o eixo é colocado horizontalmente para projeção, sendo melhor escolher a posição onde o eixo é a linha vertical lateral.
Ao marcar o tamanho das peças da bucha, seu eixo é frequentemente usado como referência de tamanho radial. A partir disso, os Ф14 e Ф11 mostrados na figura (consulte a seção A-A), etc., são anotados. Desta forma, os requisitos de projeto e a referência do processo durante o processamento (quando as peças do eixo são processadas no torno, o furo central do eixo é mantido pelo tambor em ambas as extremidades) são unificados. A referência de direção do comprimento geralmente escolhe faces finais importantes, faces de contato (ombros) ou faces usinadas.
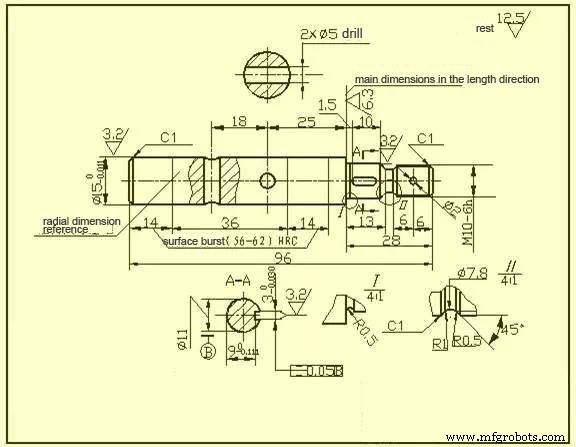
O ombro direito com rugosidade superficial de Ra6,3 como mostrado na figura é selecionado como a principal referência de dimensão na direção do comprimento, e dimensões como 13, 28, 1,5 e 26,5 são injetadas.
Em seguida, pegue a extremidade direita do eixo como base auxiliar na direção do comprimento para marcar o comprimento total do eixo 96.
Peças da tampa do disco
A forma básica deste tipo de peças é um disco plano, geralmente incluindo tampas de extremidade, tampas de válvulas, engrenagens e outras peças. Sua estrutura principal é basicamente um corpo giratório, geralmente com vários formatos de flanges e furos circulares uniformemente distribuídos. E costelas e outras estruturas locais. Ao selecionar uma vista, geralmente selecione a vista transversal do plano de simetria ou o eixo de rotação como a vista frontal e também precisa adicionar outras vistas apropriadas (como vista esquerda, vista direita ou vista superior) para expressar a forma e estrutura uniforme da peça. Conforme mostrado na figura, uma vista esquerda é adicionada para expressar um flange quadrado com cantos arredondados e quatro furos passantes uniformemente distribuídos.
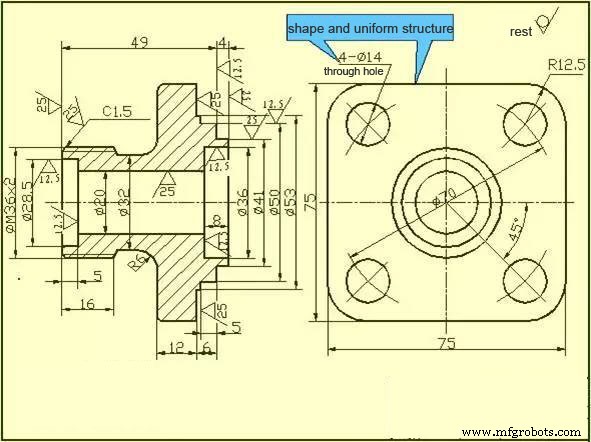
Ao marcar o tamanho das peças da tampa do disco, o eixo através do furo do eixo é geralmente selecionado como referência de dimensão radial, e a referência de dimensão principal na direção do comprimento é geralmente a face final importante.
Peças da estrutura do garfo
Tais peças geralmente incluem garfos, bielas, rolamentos e outras peças. Devido às suas posições de processamento variáveis, ao escolher a vista principal, a principal consideração é a posição de trabalho e as características de forma. Para a seleção de outras vistas, muitas vezes são necessárias duas ou mais vistas básicas, e as vistas locais apropriadas, vistas em corte transversal, etc. devem ser usadas para expressar a estrutura local da peça. A vista mostrada no desenho das peças do apoio para os pés é refinada e clara. A vista direita não é necessária para expressar a largura do rolamento e das nervuras. Para nervuras em forma de T, a seção transversal é mais apropriada.
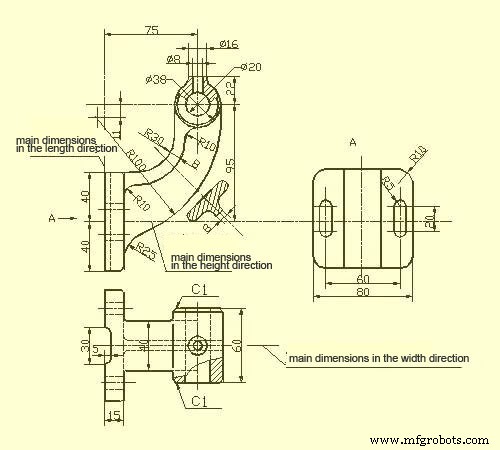
Ao marcar as dimensões das peças do suporte do garfo, a superfície da base de instalação ou o plano de simetria da peça geralmente é selecionado como referência de dimensão. Consulte a figura para o método de dimensionamento.
Peças da caixa
De um modo geral, a forma e a estrutura deste tipo de peças são mais complexas do que os três tipos anteriores de peças, e a posição de processamento muda mais. Tais peças geralmente incluem corpo de válvula, corpo de bomba, caixa redutora e outras peças. Ao escolher a vista principal, a posição de trabalho e as características de forma são consideradas principalmente. Ao selecionar outras vistas, as vistas seccionais apropriadas, cortes transversais, vistas parciais e vistas oblíquas devem ser adotadas de acordo com a situação real para expressar claramente a estrutura interna e externa da peça.
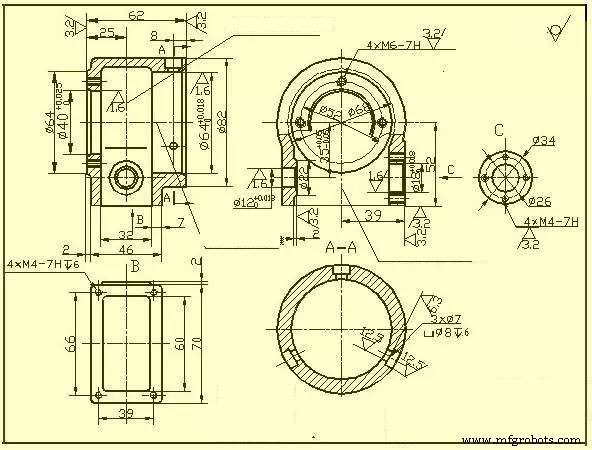
Em termos de dimensionamento, o eixo, superfície de instalação importante, superfície de contato (ou superfície de processamento) e a superfície de simetria (largura, comprimento) de algumas estruturas principais da caixa são geralmente selecionadas como referência dimensional. Para as peças da caixa que precisam ser cortadas, as dimensões devem ser marcadas o máximo possível para facilitar o processamento e a inspeção.
4 Rugosidade da Superfície
As características microgeométricas dos picos e vales com pequenos espaçamentos na superfície da peça são chamadas de rugosidade superficial. Isso se deve principalmente às marcas da ferramenta deixadas pela ferramenta na superfície da peça e à deformação plástica da superfície metálica durante o corte.
A rugosidade superficial das peças também é um índice técnico para avaliar a qualidade superficial das peças. Tem um impacto nas propriedades de acoplamento, precisão de trabalho, resistência ao desgaste, resistência à corrosão, estanqueidade e aparência das peças.
O código, símbolo e marca de rugosidade da superfície
GB/T 131-1993 especifica o código de rugosidade da superfície e sua notação. Os símbolos no desenho que indicam a rugosidade da superfície das peças são mostrados na tabela abaixo.
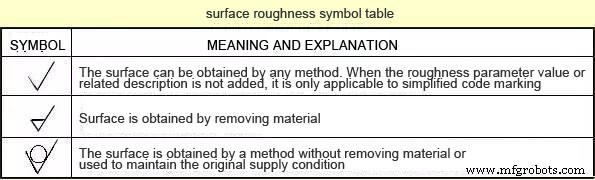
Principais parâmetros de avaliação da rugosidade da superfície da peça
1) O desvio médio aritmético do contorno (Ra)
Dentro do comprimento de amostragem, a média aritmética do valor absoluto do deslocamento de contorno.
2) Altura máxima do perfil (Rz)
A distância entre a linha superior do pico de contorno e a linha inferior do pico de contorno dentro do comprimento de amostragem.
Nota:O parâmetro Ra é preferível ao usá-lo.
Método de marcação de símbolos de rugosidade de superfície em desenhos
1) O código de rugosidade da superfície (símbolo) geralmente deve ser anotado na linha de contorno visível, na linha de fronteira ou na sua extensão, e a ponta do símbolo deve apontar do lado de fora do material para a superfície.
2) A direção dos números e símbolos no código de rugosidade da superfície deve ser marcada conforme necessário.
No mesmo desenho, cada superfície é geralmente marcada com um código (símbolo) apenas uma vez e o mais próximo possível da linha de dimensão relevante. Quando o espaço é estreito ou é inconveniente rotular, pode levar ao rótulo. Quando todas as superfícies da peça têm os mesmos requisitos de rugosidade superficial, elas podem ser marcadas uniformemente no canto superior direito do desenho. Quando a maioria das peças tem os mesmos requisitos de rugosidade superficial, pode-se utilizar o código (símbolo) mais utilizado. Observe ao mesmo tempo no canto superior direito do desenho e adicione as palavras “o resto”. A altura do código de rugosidade da superfície uniformemente marcada (símbolo) e do texto explicativo deve ser 1,4 vezes a da marca do desenho.
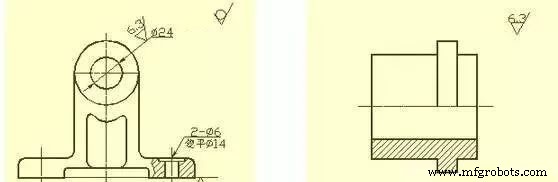
O número do código de rugosidade da superfície (símbolo) da superfície contínua na peça, a superfície dos elementos repetidos (como furos, dentes, ranhuras, etc.) e a superfície descontínua conectada por uma linha sólida fina são anotados apenas uma vez.
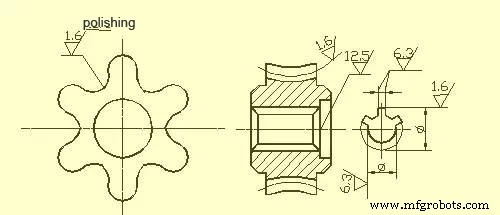
Quando houver diferentes requisitos de rugosidade de superfície na mesma superfície, use linhas finas e sólidas para desenhar a linha divisória e observe o código e o tamanho de rugosidade da superfície correspondente.
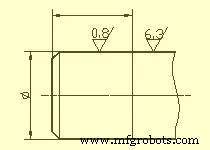
Quando a forma do dente (dente) não é desenhada na superfície de trabalho de engrenagens, roscas, etc., o método de notação do código de rugosidade da superfície (símbolo) é mostrado na figura.
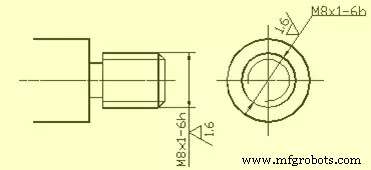
A superfície de trabalho do furo central, a superfície de trabalho do rasgo de chaveta, o código de rugosidade da superfície do chanfro e o canto arredondado podem ser simplificados e marcados.
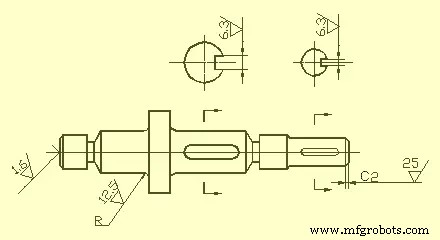
Quando as peças precisam ser parcialmente tratadas termicamente ou parcialmente chapeadas (revestidas), linhas pontilhadas grossas devem ser usadas para traçar a faixa e marcar as dimensões correspondentes. Os requisitos também podem ser escritos na linha horizontal do lado comprido do símbolo de rugosidade da superfície.
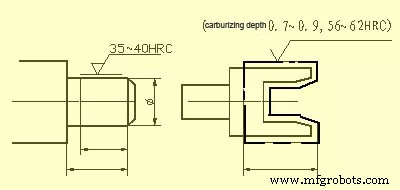
5 tolerâncias padrão e desvios básicos
Para facilitar a produção, perceber a intercambialidade das peças e atender aos diferentes requisitos de uso, a norma nacional “Limites e Ajustes” estipula que a zona de tolerância é composta por dois elementos:tolerância padrão e desvio básico. A tolerância padrão determina o tamanho da zona de tolerância e o desvio básico determina a localização da zona de tolerância.
1) Tolerância padrão (TI)
O valor da tolerância padrão é determinado pelo tamanho básico e classe de tolerância. O nível de tolerância é uma marca para determinar a precisão do tamanho. A tolerância padrão é dividida em 20 níveis, a saber, IT01, IT0, IT1,…, IT18. A precisão de seu tamanho diminui de IT01 para IT18. Os valores específicos das tolerâncias padrão podem ser encontrados nas normas relevantes.
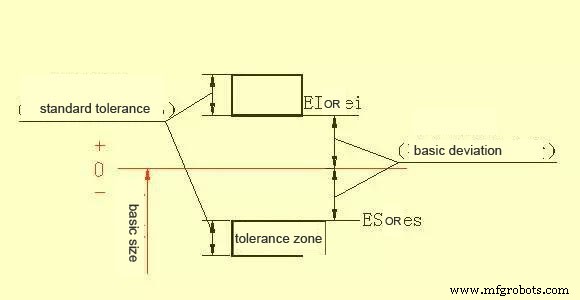
2) Desvio básico
O desvio básico refere-se ao desvio superior ou inferior da zona de tolerância em relação à posição da linha zero no limite padrão e ajuste, geralmente se refere ao desvio próximo à linha zero. Quando a zona de tolerância está acima da linha zero, o desvio básico é o desvio inferior; caso contrário, é o desvio superior. Há 28 desvios básicos no total, e o código é expresso em letras latinas, com maiúsculas como furo e minúsculas como eixo.
O desvio básico e a tolerância padrão têm as seguintes fórmulas de cálculo de acordo com a definição de tolerância dimensional:
ES=EI+IT ou EI=ES-IT
Processo de manufatura
- Peças personalizadas de usinagem CNC
- Usinagem CNC de peças grandes
- Serviços de usinagem CNC garantem precisão em peças mais complexas
- O que entender sobre técnicas de usinagem de precisão para peças de aeronaves
- Evite "excesso de engenharia" no projeto de peças de usinagem
- Tudo sobre usinagem de peças de alumínio anodizado
- Como analisar desenhos de peças de usinagem?
- Usinagem de precisão fora do padrão VS Usinagem de peças padrão
- Quer entender Usinagem CNC? Leia isso!
- Peças de automóveis exigem precisão