Como escolher as ferramentas da máquina CNC?
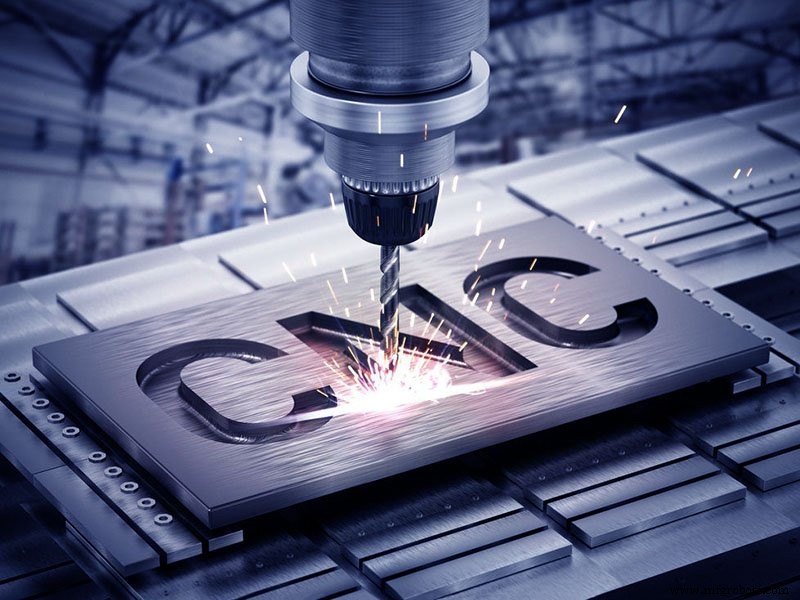
As regras para escolher máquinas-ferramentas CNC
A vida útil da ferramenta está intimamente relacionada ao volume de corte. Ao formular parâmetros de corte, uma vida útil razoável da ferramenta deve ser selecionada primeiro, e a vida útil razoável da ferramenta deve ser determinada de acordo com a meta de otimização. Geralmente dividido em dois tipos:vida útil da ferramenta de maior produtividade e vida útil da ferramenta de menor custo. O primeiro é determinado de acordo com a meta de menos horas de trabalho de uma única peça, e o último é determinado de acordo com a meta de menor custo de processo.
Os seguintes pontos podem ser considerados na escolha da vida útil da ferramenta de acordo com a complexidade da ferramenta, custos de fabricação e afiação. A vida útil de ferramentas complexas e de alta precisão deve ser maior do que a de ferramentas de aresta única. Para ferramentas intercambiáveis fixadas à máquina, devido ao curto tempo de troca da ferramenta, a fim de dar jogo total ao seu desempenho de corte e melhorar a eficiência da produção, a vida útil da ferramenta pode ser selecionada para ser menor, geralmente 15-30min. Para máquinas-ferramentas multiferramentas, máquinas-ferramentas modulares e ferramentas de usinagem automatizadas, onde a instalação da ferramenta, a troca e o ajuste da ferramenta são mais complicados, a vida útil da ferramenta deve ser maior e a confiabilidade da ferramenta deve ser garantida. Quando a produtividade de um determinado processo na oficina limita o aumento na produtividade de toda a oficina, a vida útil da ferramenta do processo deve ser selecionada menor. Quando o custo de toda a planta por unidade de tempo de um determinado processo é relativamente grande, a vida útil da ferramenta também deve ser selecionada. No acabamento de peças grandes, para garantir que pelo menos um passe seja concluído e para evitar a troca da ferramenta no meio do corte, a vida útil da ferramenta deve ser determinada de acordo com a precisão da peça e a rugosidade da superfície. Em comparação com os métodos de processamento de máquinas-ferramenta comuns, a usinagem CNC apresenta requisitos mais elevados em ferramentas de corte. Não requer apenas boa qualidade e alta precisão, mas também estabilidade dimensional, alta durabilidade e fácil instalação e ajuste. Atenda aos requisitos de alta eficiência das máquinas-ferramentas CNC. As ferramentas selecionadas em máquinas-ferramentas CNC geralmente adotam materiais de ferramenta adequados para corte de alta velocidade (como aço de alta velocidade, metal duro de granulação ultrafina) e usam pastilhas intercambiáveis.
Máquinas-ferramentas CNC para torneamento
As ferramentas de torneamento CNC comumente usadas são geralmente divididas em três categorias:ferramentas de torneamento de conformação, ferramentas de torneamento pontiagudo, ferramentas de torneamento de arco e três tipos. As ferramentas de torneamento de conformação também são chamadas de ferramentas de torneamento de protótipo. A forma do contorno das peças processadas é completamente determinada pela forma e tamanho da lâmina da ferramenta de torneamento. No processamento de torneamento CNC, as ferramentas de torneamento de conformação comuns incluem ferramentas de torneamento de arco de pequeno raio, ferramentas de torneamento não retangulares e ferramentas de rosca. Na usinagem CNC, a ferramenta de torneamento de conformação deve ser usada o menos possível ou não. A ferramenta de torneamento pontiaguda é uma ferramenta de torneamento caracterizada por uma aresta de corte reta. A ponta da ferramenta deste tipo de ferramenta de torneamento é composta por arestas de corte lineares principais e secundárias, como 900 ferramentas de torneamento internas e externas, ferramentas de torneamento de face esquerda e direita, ferramentas de torneamento de canal (corte) e várias arestas de corte externas e internas com pequenas dicas de ferramentas. Ferramenta de torneamento de furo. O método de seleção dos parâmetros geométricos da ferramenta de torneamento pontiagudo (principalmente o ângulo geométrico) é basicamente o mesmo do torneamento comum, mas as características da usinagem CNC (como rota de usinagem, interferência de usinagem, etc.) devem ser totalmente consideradas , e a própria ponta da ferramenta deve ser considerada. força.
A segunda é a ferramenta de torneamento em forma de arco. A ferramenta de torneamento em forma de arco é uma ferramenta de torneamento caracterizada por uma aresta de corte em forma de arco com um pequeno arredondamento ou erro de perfil linear. Cada ponto da borda do arco da ferramenta de torneamento é a ponta da ferramenta de torneamento em forma de arco. Consequentemente, o ponto de posição da ferramenta não está no arco, mas no centro do arco. A ferramenta de torneamento em forma de arco pode ser usada para girar superfícies internas e externas e é especialmente adequada para girar várias superfícies de formação de conexão lisa (côncava). Ao selecionar o raio do arco da ferramenta de torneamento, deve-se considerar que o raio do arco da aresta de corte da ferramenta de torneamento de dois pontos deve ser menor ou igual ao raio de curvatura mínimo no contorno côncavo da peça, de modo que para evitar o ressecamento do processamento. O raio não deve ser muito pequeno, caso contrário, não será apenas difícil de fabricar. A ferramenta de torneamento pode ser danificada devido à fraca resistência da ponta ou fraca capacidade de dissipação de calor do corpo da ferramenta.
Máquinas-ferramentas CNC para fresamento
Na usinagem CNC, fresas de topo de fundo plano são comumente usadas para fresar os contornos internos e externos de peças planas e o plano de fresamento. Os dados empíricos dos parâmetros relevantes da ferramenta são os seguintes:Primeiro, o raio da fresa RD deve ser menor que o raio mínimo de curvatura Rmin da superfície do contorno interno da peça, geralmente RD =(0,8-0,9) Rmin. A segunda é a altura de processamento da peça H <(1 / 4-1 / 6) RD para garantir que a faca tenha rigidez suficiente. Terceiro, ao fresar a parte inferior da ranhura interna com uma fresa de topo de fundo plano, porque as duas passagens da parte inferior da ranhura precisam ser sobrepostas, e o raio da borda inferior da ferramenta é Re =Rr, ou seja, o diâmetro é d =2Re =2 (Rr). Considere o raio da ferramenta como Re =0,95 (Rr). Para o processamento de alguns perfis e contornos tridimensionais com ângulos de chanfro variáveis, são normalmente utilizadas fresas esféricas, fresas de anel, fresas de tambor, fresas cônicas e fresas de disco.
A maioria das máquinas-ferramenta CNC usa ferramentas serializadas e padronizadas. Para porta-ferramentas e cabeçotes de ferramenta, como ferramentas de torneamento externo intercambiáveis fixadas à máquina e ferramentas de torneamento frontal, existem padrões nacionais e modelos serializados. Para centros de usinagem e trocadores automáticos de ferramentas Máquinas-ferramentas e porta-ferramentas foram serializados e padronizados. Por exemplo, o código padrão do sistema de ferramentas cônicas é TSG-JT, e o código padrão do sistema de ferramentas retas é DSG-JZ. Além disso, para a ferramenta selecionada, antes do uso, o tamanho da ferramenta precisa ser estritamente medido para obter dados precisos e o operador insere esses dados no sistema de dados e completa o processo de processamento por meio de chamada de programa, processando assim peças de trabalho qualificadas.
O ponto da ferramenta
De que posição a ferramenta começa a se mover para a posição especificada? Portanto, no início da execução do programa, a posição onde a ferramenta começa a se mover no sistema de coordenadas da peça deve ser determinada. Esta posição é o ponto inicial da ferramenta em relação à peça quando o programa é executado. Portanto, é chamado de ponto de partida ou ponto de partida do programa. Este ponto inicial é geralmente determinado pela configuração da ferramenta, portanto, este ponto também é chamado de ponto de configuração da ferramenta. Ao compilar o programa, escolha a posição do ponto de configuração da ferramenta corretamente. O princípio de definir o ponto de configuração da ferramenta é facilitar o processamento numérico e simplificar a programação. É fácil de alinhar e verificar durante o processamento; o erro de processamento causado é pequeno. O ponto de ajuste da ferramenta pode ser definido na peça usinada, no dispositivo de fixação ou na máquina-ferramenta. Para melhorar a precisão de usinagem da peça, o ponto de ajuste da ferramenta deve ser definido o máximo possível com base no projeto da peça ou no processo. Na operação real da máquina-ferramenta, o ponto de posição da ferramenta da ferramenta pode ser colocado no ponto de ajuste da ferramenta pela operação de ajuste manual da ferramenta, ou seja, a coincidência do "ponto de posição da ferramenta" e do "ponto de ajuste da ferramenta". O denominado "ponto de localização da ferramenta" refere-se ao ponto de referência de posicionamento da ferramenta. O ponto de localização da ferramenta da ferramenta de torneamento é a ponta da ferramenta ou o centro do arco da ponta da ferramenta. A fresa de topo de fundo plano é a interseção do eixo da ferramenta e a parte inferior da ferramenta; o moinho de ponta esférica é o centro da bola e a broca é o ponto. A operação de ajuste manual da ferramenta tem baixa precisão e baixa eficiência. Algumas fábricas usam espelhos de configuração ótica de ferramentas, instrumentos de configuração de ferramentas, dispositivos de configuração automática de ferramentas, etc. para reduzir o tempo de configuração da ferramenta e melhorar a precisão da configuração da ferramenta. Quando a ferramenta precisa ser trocada durante o processamento, o ponto de troca da ferramenta deve ser especificado. O denominado "ponto de troca da ferramenta" refere-se à posição do pino da ferramenta quando ele gira para trocar a ferramenta. O ponto de troca da ferramenta deve estar localizado fora da peça de trabalho ou fixação, e a peça de trabalho e outras peças não devem ser tocadas durante a troca da ferramenta.
Os dados de usinagem
Na programação NC, o programador deve determinar os dados de usinagem para cada processo e escrevê-los no programa na forma de instruções. Os parâmetros de corte incluem velocidade do fuso, dados de usinagem traseira e velocidade de alimentação. Para diferentes métodos de processamento, diferentes parâmetros de corte precisam ser selecionados. O princípio de seleção dos dados de usinagem é garantir a precisão de usinagem e aspereza da superfície das peças, dar folga total ao desempenho de corte da ferramenta, garantir durabilidade razoável da ferramenta e dar folga total ao desempenho da máquina-ferramenta para maximizar a produtividade e reduzir custos.
1. Determine a velocidade do fuso.
A velocidade do fuso deve ser selecionada de acordo com a velocidade de corte permitida e o diâmetro da peça (ou ferramenta). A fórmula de cálculo é:n =1000 v / 7 1D onde:V é a velocidade de corte, a unidade é o movimento m / m, que é determinado pela durabilidade da ferramenta; N é a velocidade do fuso, a unidade é r / min e D é o diâmetro da peça ou diâmetro da ferramenta em mm. Para a velocidade N calculada do fuso, a velocidade que a máquina-ferramenta tem ou está próxima deve ser selecionada por último.
2. Determine a taxa de alimentação.
A velocidade de avanço é um parâmetro importante nos parâmetros de corte de máquinas-ferramenta CNC, que é principalmente selecionada de acordo com a precisão de usinagem e os requisitos de rugosidade da superfície das peças e as propriedades do material das ferramentas e peças de trabalho. A taxa de avanço máxima é limitada pela rigidez da máquina-ferramenta e o desempenho do sistema de avanço. O princípio de determinação da taxa de avanço:Quando a qualidade da peça pode ser garantida, a fim de melhorar a eficiência da produção, uma taxa de avanço mais alta pode ser selecionada. Geralmente selecionado na faixa de 100-200 mm / min; ao cortar, processar furos profundos ou processar com ferramentas de aço de alta velocidade, uma velocidade de alimentação mais baixa deve ser selecionada, geralmente na faixa de 20-50 mm / min; quando a precisão de processamento, a superfície Quando a exigência de rugosidade é alta, a velocidade de alimentação deve ser menor selecionada, geralmente na faixa de 20-50 mm / min; quando a ferramenta está vazia, especialmente quando a longa distância "retorna a zero", pode-se definir as configurações do sistema CNC da máquina O avanço máximo.
3. Determine a profundidade do corte.
A profundidade de corte é determinada pela rigidez da máquina-ferramenta, da peça de trabalho e da ferramenta de corte. Quando a rigidez permitir, a profundidade de corte deve ser igual à permissão de usinagem da peça o máximo possível, o que pode reduzir o número de passadas e melhorar a eficiência da produção. Para garantir a qualidade da superfície usinada, uma pequena quantidade de sobremetal de acabamento pode ser deixada, geralmente 0,2-0,5 mm. Resumindo, o valor específico dos dados de usinagem deve ser determinado por analogia com base no desempenho da máquina, manuais relacionados e experiência real.
Ao mesmo tempo, a velocidade do fuso, a profundidade de corte e a velocidade de avanço podem ser adaptadas entre si para formar os melhores parâmetros de corte.
Os dados de usinagem não são apenas um parâmetro importante que deve ser determinado antes do ajuste da máquina-ferramenta, mas também se seu valor é razoável ou não tem uma influência muito importante na qualidade do processamento, na eficiência do processamento e no custo de produção. Os chamados dados de usinagem "razoáveis" referem-se aos dados de usinagem que fazem uso total do desempenho de corte da ferramenta e desempenho dinâmico da máquina-ferramenta (potência, torque) para obter alta produtividade e baixo custo de processamento sob a premissa de garantir a qualidade.
Máquina cnc
- Como Encontrar uma Máquina CNC Usada
- Como limpar uma máquina CNC usada
- Como fazer a manutenção das ferramentas de sua máquina CNC
- Como escolher sua máquina CNC
- Uma rápida comparação de máquinas-ferramentas CNC
- Como escolher sua ferramenta redonda de metal duro
- Os 4 principais problemas de máquinas CNC e como solucioná-los
- Como evitar esses quatro problemas comuns com máquinas-ferramentas CNC
- Como a máquina suíça CNC se destaca no torneamento?
- Como adicionar uma nova ferramenta