Enrolamento de filamento 3D permite o conceito de assento de veículo
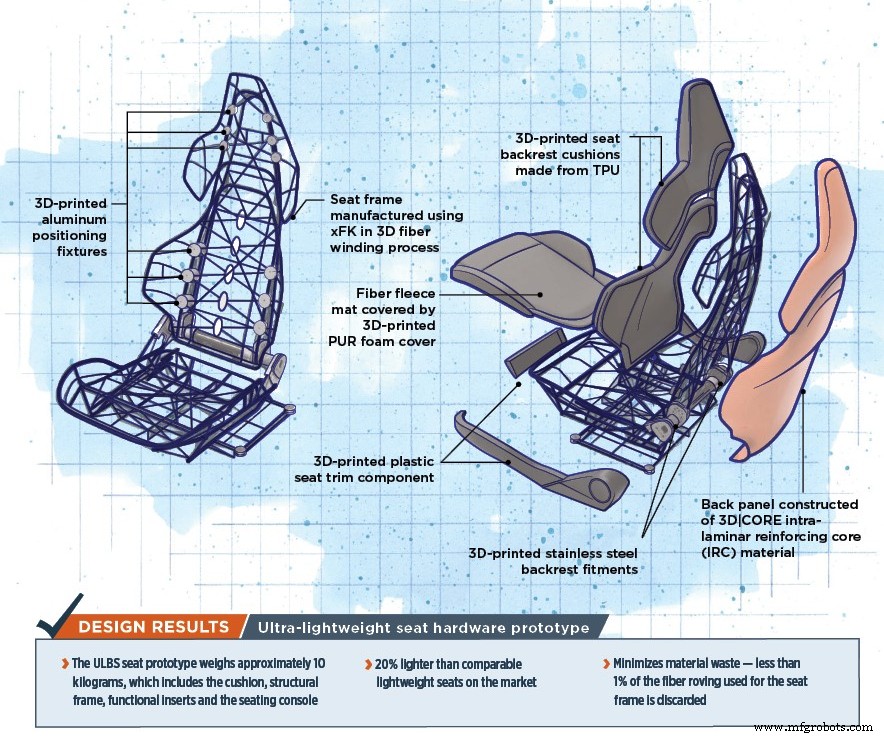
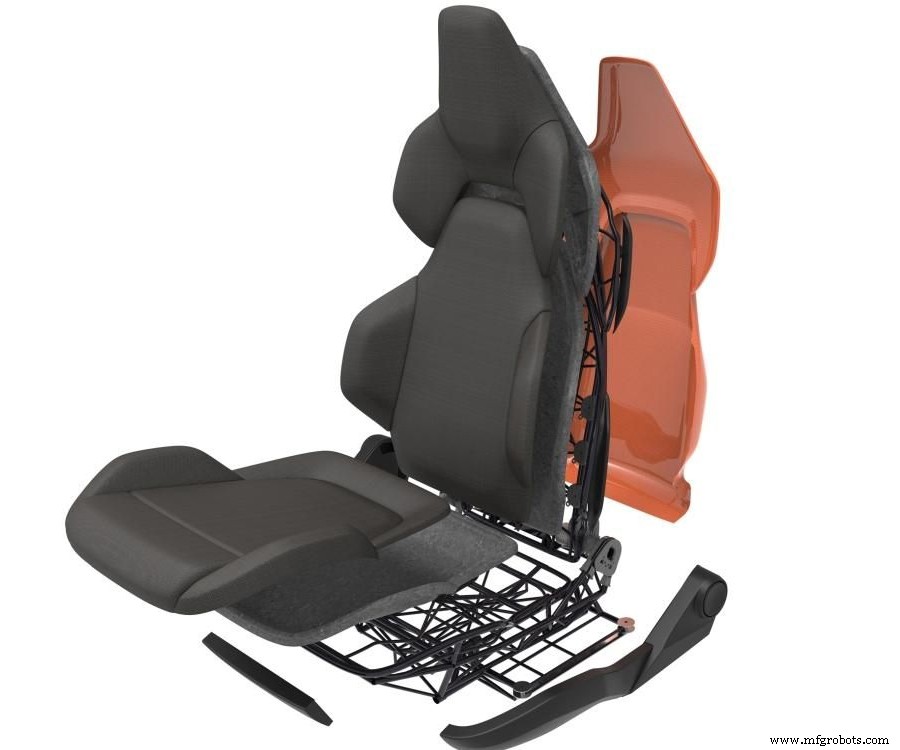
Sustentabilidade e responsabilidade ambiental estão se tornando condutores cada vez mais prevalentes das tendências tecnológicas na indústria automotiva. Veículos de baixo consumo de energia e baixas emissões tornaram-se uma prioridade para o setor automotivo internacional, e as tendências em direção a tecnologias alternativas de transporte, como eletromobilidade e mobilidade aérea urbana (UAM), estão ganhando impulso. Os OEMs estão buscando materiais e processos emergentes como um facilitador para esses modos de transporte em perspectiva, mas as mudanças no setor automotivo costumam ser lentas. Para que novos materiais e processos sejam totalmente adotados, eles devem ser não apenas qualificados, mas também econômicos e possibilitar uma produção em alto volume.
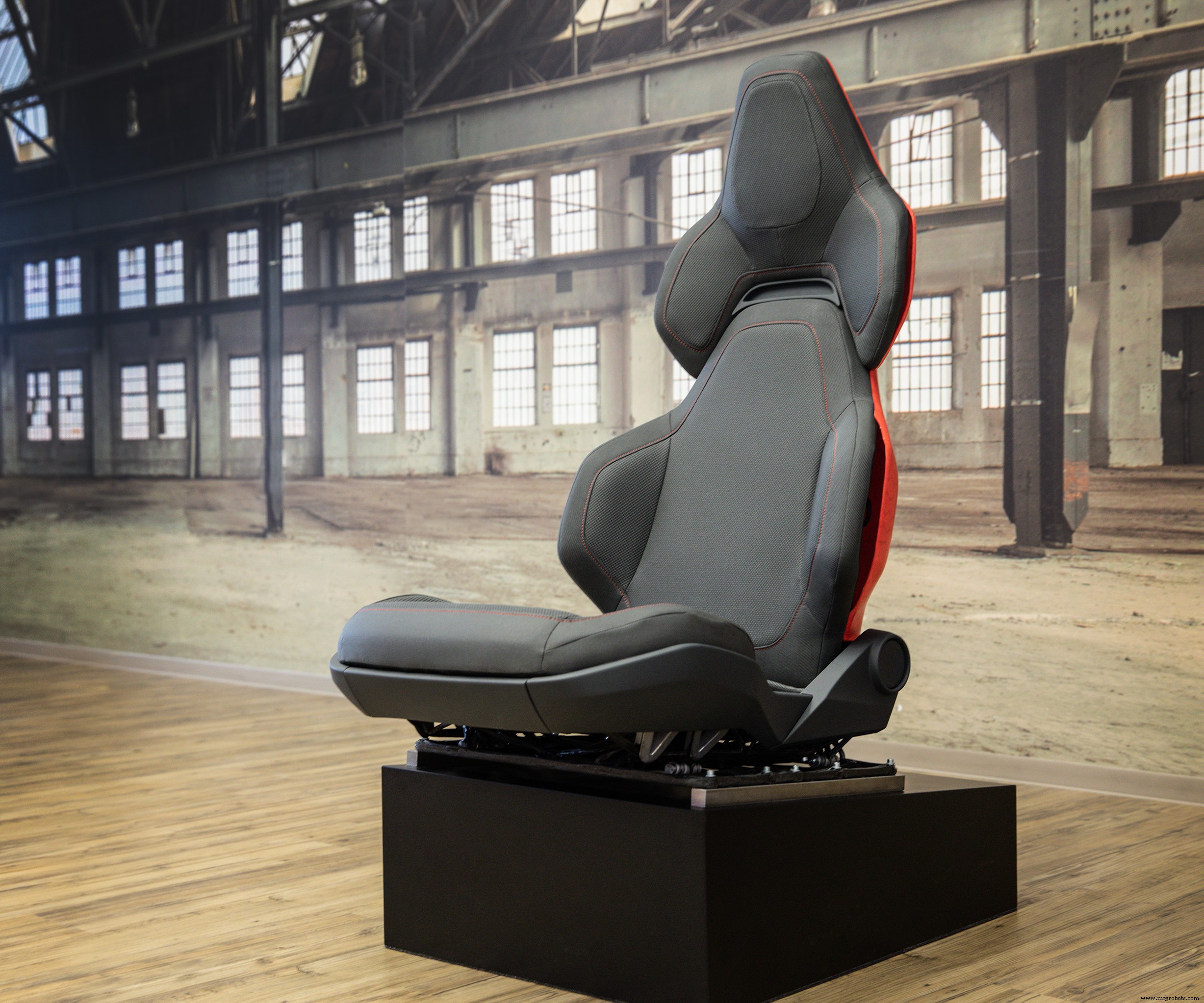
Assento ultraleve. O conceito de assento Ultra Leichtbausitz (ULBS) foi desenvolvido por meio de uma colaboração entre várias empresas usando uma combinação de tecnologias. Fonte | csi entwicklungstechnik
Recentemente, um projeto inovador com potencial para o setor automotivo - bem como para mercados emergentes como hipercarros e táxis aéreos - demonstrou como novos materiais, processos e tecnologias, e a estreita colaboração entre empresas, podem permitir modos de transporte de próxima geração. O objetivo do projeto era repensar completamente uma cadeira de carro usando tecnologias geradoras de ponta e fazer isso usando apenas o material certo, conforme necessário, no lugar certo - e para produzir resultados rapidamente. O protótipo de assento de veículo híbrido de metal compósito ultraleve resultante foi desenvolvido, do projeto à fabricação, em apenas sete meses, por meio de uma abordagem de projeto orientada por simulação, métodos de gerenciamento de projeto ágeis e estreita cooperação e integração de sistema entre as empresas envolvidas.
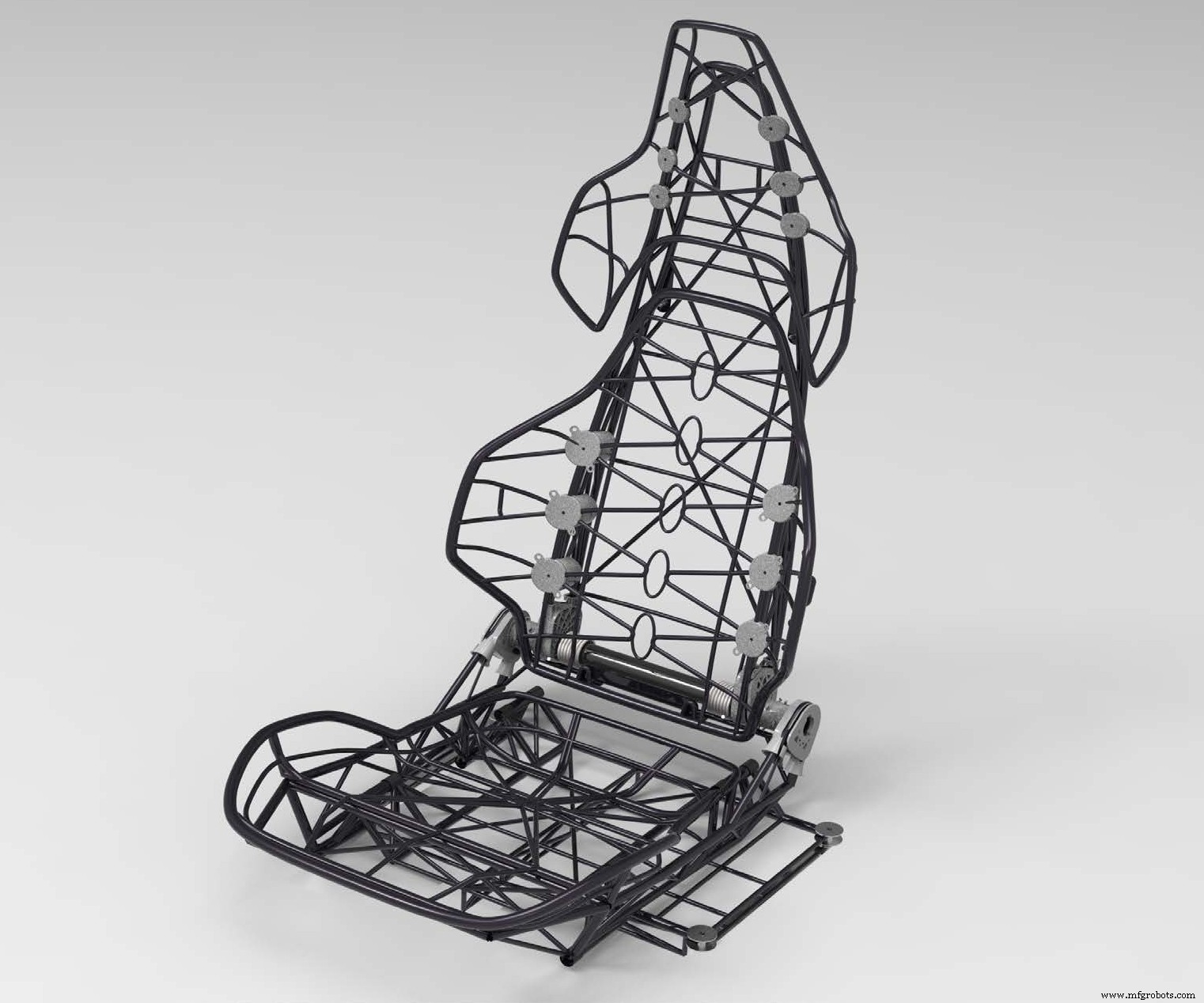
Construindo um assento melhor
O estudo de viabilidade do assento ultraleve Ultraleichtbausitz (ULBS) foi desenvolvido por meio de uma colaboração entre várias empresas usando uma combinação de tecnologias. A visão do projeto era, nas palavras do grupo, “criar um conceito de assento ultraleve, destacado no mercado em termos de otimização de peso”. As empresas iniciantes csi entwicklungstechnik GmbH (csi, Neckarsulm, Alemanha), Alba Tooling &Engineering (Forstau, Áustria) e Automotive Management Consulting (AMC, Penzberg, Alemanha) desenvolveram o conceito de assento protótipo em colaboração com Covestro (Leverkusen, Alemanha), LBK Fertigung (Friedberg, Alemanha), Robert Hofmann (Lichtenfels, Alemanha) e 3D | CORE (Herford, Alemanha).
O projeto colaborativo resultou em um protótipo de assento com um peso de pouco mais de 10 quilos, que inclui a almofada, quadro estrutural, inserções funcionais e o console do assento que permite sua montagem em um veículo. O assento é 20% mais leve do que os assentos leves comparáveis no mercado, muitos dos quais sendo assentos de reposição. De acordo com o líder do projeto ULBS Stefan Herrmann, que é responsável pelo design leve na CSI, atualmente não há assentos concorrentes no mercado que pesem menos de 12 quilos.
“No entanto, uma comparação direta muitas vezes não é igual, porque os assentos do mercado de reposição muitas vezes não incluem o console de assento na definição de peso”, diz Herrmann, “Além disso, o conforto do assento do ULBS é muito maior em comparação com os assentos com peso semelhante. Os assentos existentes geralmente são assentos anatômicos, que têm peso ainda mais baixo, mas não tão confortáveis, ou assentos supersportivos tradicionais, que têm um peso muito maior ”.
O ULBS apresenta várias tecnologias inovadoras, das quais a estrutura do esqueleto da mecha de fibra baseada na tecnologia de processo xFK em 3D desempenha o papel mais proeminente. (Consulte "Enrolamento de filamento, reinventado" para obter mais informações sobre xFK em 3D e outras tecnologias de enrolamento de filamento.) A importância fundamental da tecnologia premiada para deposição de mecha de fibra infinita reside em sua liberdade de design, na simulação orientada e material- posicionamento otimizado da fibra exatamente na direção da carga, bem como na aplicação simples, econômica e sem desperdício de material de fibra. Para a transferência de carga nesta estrutura, foram utilizadas peças impressas em 3D. Em áreas com maiores cargas, como os encaixes do encosto, o assento utiliza estruturas impressas em 3D feitas de aço inoxidável com alta resistência e alto módulo. Em áreas menos carregadas, a impressão 3D de alumínio é usada.
csi entwicklungstechnik, uma empresa de engenharia especializada em estruturas de carroceria de veículos (BIW), bem como interiores e exteriores automotivos com áreas de negócios incluindo polímeros reforçados com fibra de carbono (CFRP) e manufatura aditiva, supervisionou e coordenou o projeto com base no ideia iniciada pela AMC. A csi forneceu o estilo, a superfície, o conceito, a simulação, a engenharia de design e o gerenciamento do projeto para o projeto.
Herrmann explica:“csi foi responsável pelos pacotes de trabalho no domínio da cadeia de processo digital - estilo, design de engenharia, design de superfície, simulação CAE, simulação de topologia, simulação de validação e confirmação virtual do projeto.”
Ele ressalta que o que torna o projeto ULBS digno de nota não é apenas o uso de materiais e métodos de fabricação inovadores, mas o desenvolvimento de uma peça complexa que compreende novos projetos de componentes em um curto período de sete meses, em estreita colaboração entre os parceiros.
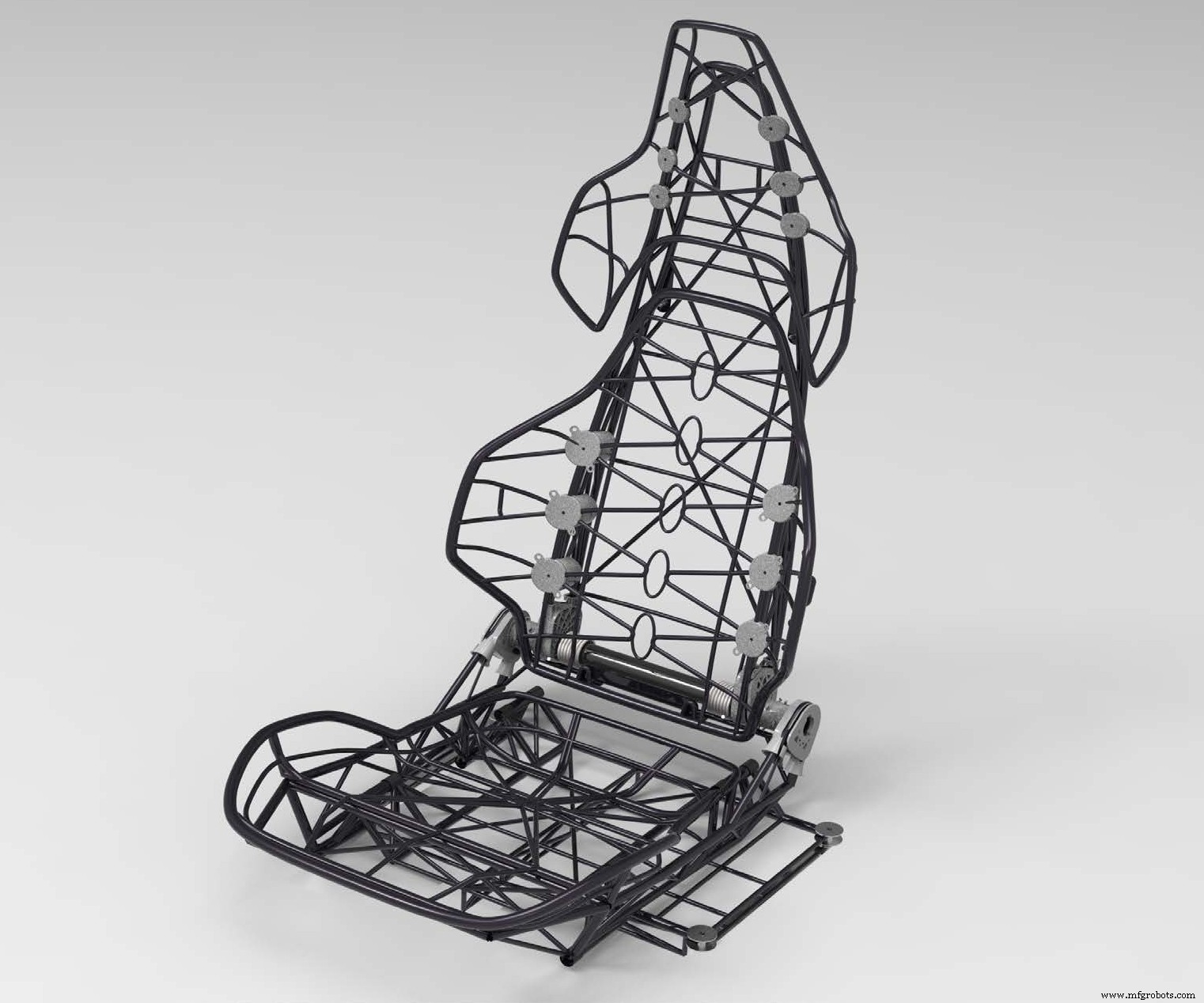
Estrutura do assento enrolada em filamento. Grande parte da redução de peso no projeto ULBS resulta da tecnologia de processo de enrolamento de fibra xFK em 3D da AMC. Fonte | csi entwicklungstechnik
Enrolando um quadro
Grande parte da redução de peso no projeto ULBS resulta do xFK em 3D da AMC, uma tecnologia composta de fibra altamente flexível, configurável, econômica e sustentável para componentes de enrolamento.
O xFK em 3D já foi usado para uma variedade de produtos e aplicações para várias indústrias e segmentos de mercado. SGL Group Wiesbaden, Alemanha) exibiu várias peças automotivas e de bicicletas fabricadas com essa tecnologia na feira internacional de compósitos JEC World 2018. Uma das peças exibidas, um anel de corrente de bicicleta de fibra de carbono desenvolvido pela AMC, pode reduzir o peso em até 70% em comparação com uma versão de alumínio.
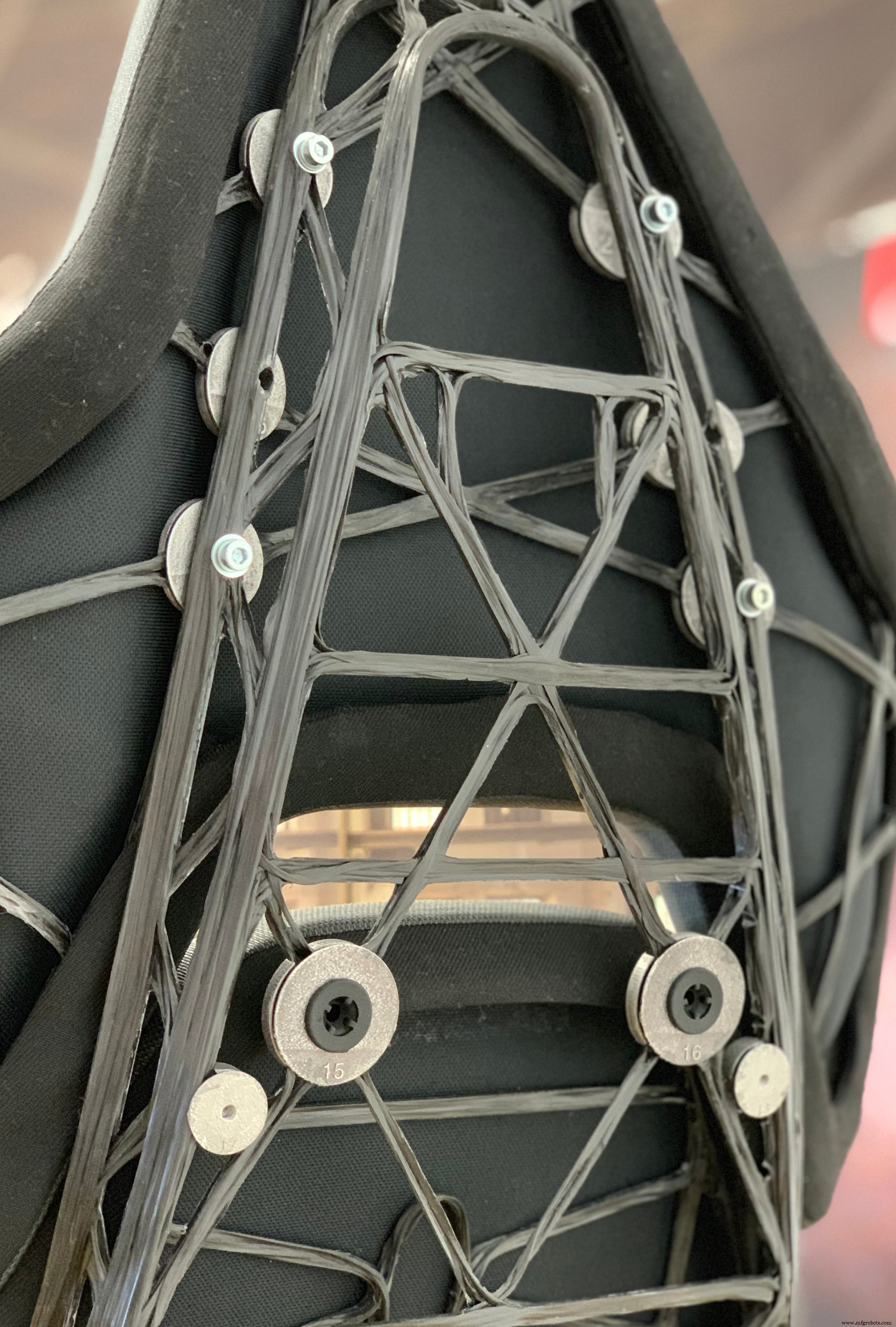
Buchas de enrolamento. Uma mecha de fibra impregnada de resina termoendurecida é enrolada em torno de um acessório de posicionamento, permitindo que as fibras sejam dispostas para corresponder às cargas de cada peça e às funções desejadas. Fonte | csi entwicklungstechnik
O processo xFK em 3D enrola estruturas de suporte de carga de uma maneira livre de resíduos usando fibras contínuas impregnadas de resina termofixa. Uma fibra roving saturada com resina epóxi é enrolada em torno de um acessório de posicionamento, ou buchas de enrolamento, permitindo que as fibras sejam dispostas especificamente para corresponder às cargas de cada peça e funções desejadas.
“Um grande benefício do xFK em 3D é a eliminação dos pontos fracos em relação à transferência de carga e introdução de carga nas estruturas”, diz Herrmann. Ele explica que os pontos fracos muitas vezes não estão no contínuo da estrutura, mas nas áreas onde as cargas são introduzidas na estrutura, especialmente onde os componentes vizinhos são conectados à estrutura . A tecnologia xFK em 3D permite transferências de carga entre conexões e permite que as fibras sejam alinhadas de acordo com as funções de componentes e casos de carga desejados e fabricadas em três dimensões.
O processo de enrolamento do filamento também traz benefícios adicionais. O processo ajuda a minimizar o desperdício de material - menos de 1% da mecha de fibra é desperdiçada.
A csi reconheceu o xFK nos pontos fortes do 3D e projetou a estrutura do assento ULBS para ser construída sob a consultoria do Dr. Clause Georg Bayreuther, chefe de tecnologia da AMC.
“Trabalhando com engenheiros csi, consultores AMC e especialistas em ferramentas da Alba, desenvolveu este conceito e estrutura para a estrutura do assento a ser fabricada usando o xFK no processo 3D”, diz Peter Fassbaender, consultor de tecnologia e iniciador do xFK na tecnologia 3D.
Alba fabricou as ferramentas para a estrutura do assento CFRP e forneceu suporte de engenharia. Além disso, embora a estrutura do assento tenha sido enrolada em fibra de carbono, fibras naturais ou fibras de basalto também são boas candidatas.
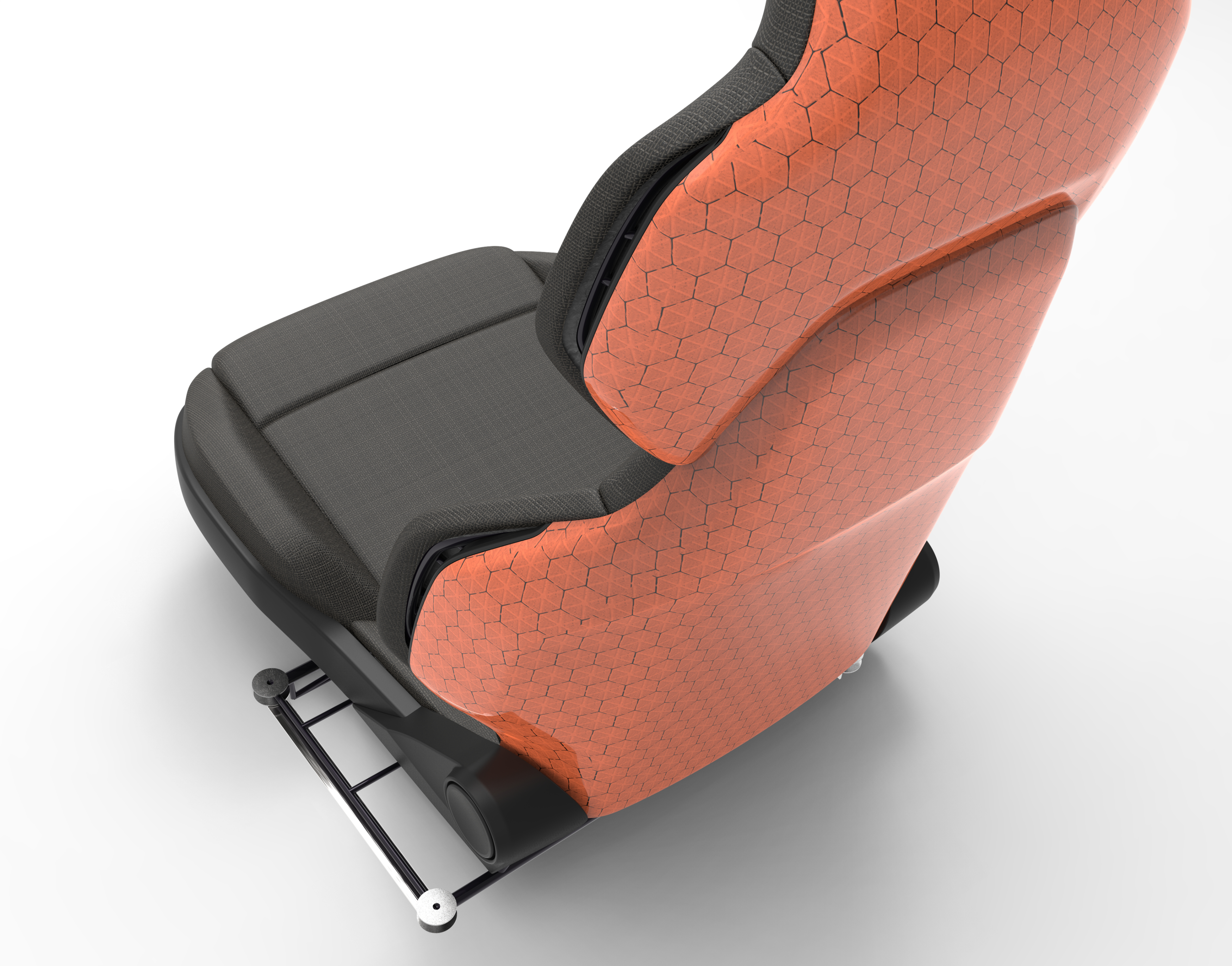
Novas tecnologias. O protótipo ULBS usa uma combinação de novas tecnologias, incluindo um revestimento do painel traseiro feito de material de núcleo de reforço intralaminar (IRC) e almofadas do encosto do assento impressas em 3D feitas de poliuretano termoplástico (TPU). Fonte | csi entwicklungstechnik
Uma estrutura de material híbrido
Além da estrutura, o protótipo ULBS inclui várias outras inovações. Alba, que forneceu as ferramentas, também forneceu as ferramentas, engenharia e fabricação para o corpo de espuma da sede e executou a montagem da sede. Um tapete de lã de fibra cobre a estrutura CFRP do assento, que é então coberta por uma capa de espuma PUR impressa em 3D. A área da almofada do assento é feita de espuma tradicional.
A redução de peso foi conseguida com o uso de 3D | CORE, um material de núcleo de reforço intralaminar (IRC), na estrutura do revestimento do painel traseiro do encosto do banco. O material é um material de núcleo de reforço intra-laminar (IRC) - um núcleo de sanduíche estrutural que compreende poliestireno extrudado (XPS) e corpos de núcleo de espuma de polietileno tereftalato (PET) em um padrão de favo de mel integrado. Durante a produção de peças compostas, a estrutura em favo de mel é preenchida com resina, resultando em alta resistência intra-laminar. O 3D | Core é montado entre duas camadas de fibra de vidro para criar uma pré-forma, que é infundida com resina epóxi termoplástica usando moldagem por transferência de resina assistida a vácuo (VA-RTM).
A Covestro forneceu seu adesivo Dispercoll como um aglutinante para os tapetes de lã de fibra, bem como a almofada do encosto impressa em 3D. De acordo com Herrmann, as propriedades mecânicas de Dispercoll fornecem boa resistência à abrasão, o que é importante porque o contato da superfície entre a almofada e a estrutura pode sujeitar o velo ao desgaste com o tempo.
“Se você tem uma mecha de fibra única, ao colocá-la em um têxtil, obtém micromovimentos entre as partes rígidas de CFRP e as esteiras de lã. Os componentes da estrutura do assento podem esfregar no tecido e destruí-lo ”, explica Herrmann.
Os assentos tradicionais normalmente têm uma área de superfície maior de apoio ao amortecimento e não têm esse problema. Com o xFK em 3D, no entanto, há uma área de superfície de contato menor devido à estrutura do quadro.
“Quando o xFK em estruturas 3D empurra o tecido de lã, você deve ter um fichário específico e durável; é isso que o Dispercoll oferece nesse contexto ”, acrescenta Herrmann.
A Covestro também forneceu o que é considerado a primeira almofada impressa em 3D do mundo. Embora a espuma convencional e intensiva com ferramentas seja normalmente usada nos encostos dos assentos, o uso das almofadas do encosto do assento impressas em 3D, que são feitas de TPU (poliuretano termoplástico), aumenta ainda mais a flexibilidade e adaptabilidade do assento ULBS no que diz respeito à sua estética, opções de integração funcional e conforto.
Um assento para o futuro
O projeto ULBS atinge vários objetivos. O conceito resultante, embora ainda não esteja no mercado, tem potencial para atender a vários nichos de mercado, como hipercarros, táxis aéreos, veículos ultraleves, micromobilidade, helicópteros, multicópteros e aviação. Embora reconhecidamente mais caro do que assentos de carro de produção, o ULBS demonstra várias tecnologias que minimizam o desperdício, reduzindo assim os custos de material. Em comparação com outras tecnologias de fibra de carbono, o xFK em 3D produz uma quantidade muito baixa de resíduos. Na verdade, todo o projeto visa a utilização de recursos mínimos e apenas o mínimo necessário de material. O ULBS também oferece a possibilidade de utilizar recursos renováveis e sustentáveis como fibras naturais na estrutura do quadro, almofadas e tecidos.
Porém, o mais importante é que o projeto demonstra como as empresas podem minimizar o tempo de entrada no mercado trabalhando juntas por meio de procedimentos de coordenação curtos e ágeis. É também um bom exemplo de como usar o pensamento de design para levar um produto da ideia ao protótipo de hardware com sucesso, concentrando-se nos requisitos funcionais e olhando para aplicações futuras e metas de sustentabilidade.
fibra
- Configurações de enrolamento
- Assento para bicicleta
- Monociclo
- Assento para criança
- Chip de banda ultralarga permite acesso de veículos com base em smartphone
- A plataforma de computação Edge permite acesso profundo aos dados automotivos
- Características de desempenho do fio de fibra de vidro
- Tampa do assento do vaso sanitário de fibra de carbono
- Novas tecnologias e mercados no evento World of Filament Winding
- Enrolador de filamento Roth para facilitar grandes cortes de peso / custo Ariane 6