CosiMo:Processo RTM termoplástico inteligente demonstrado para o simulador de desafio da tampa da caixa da bateria
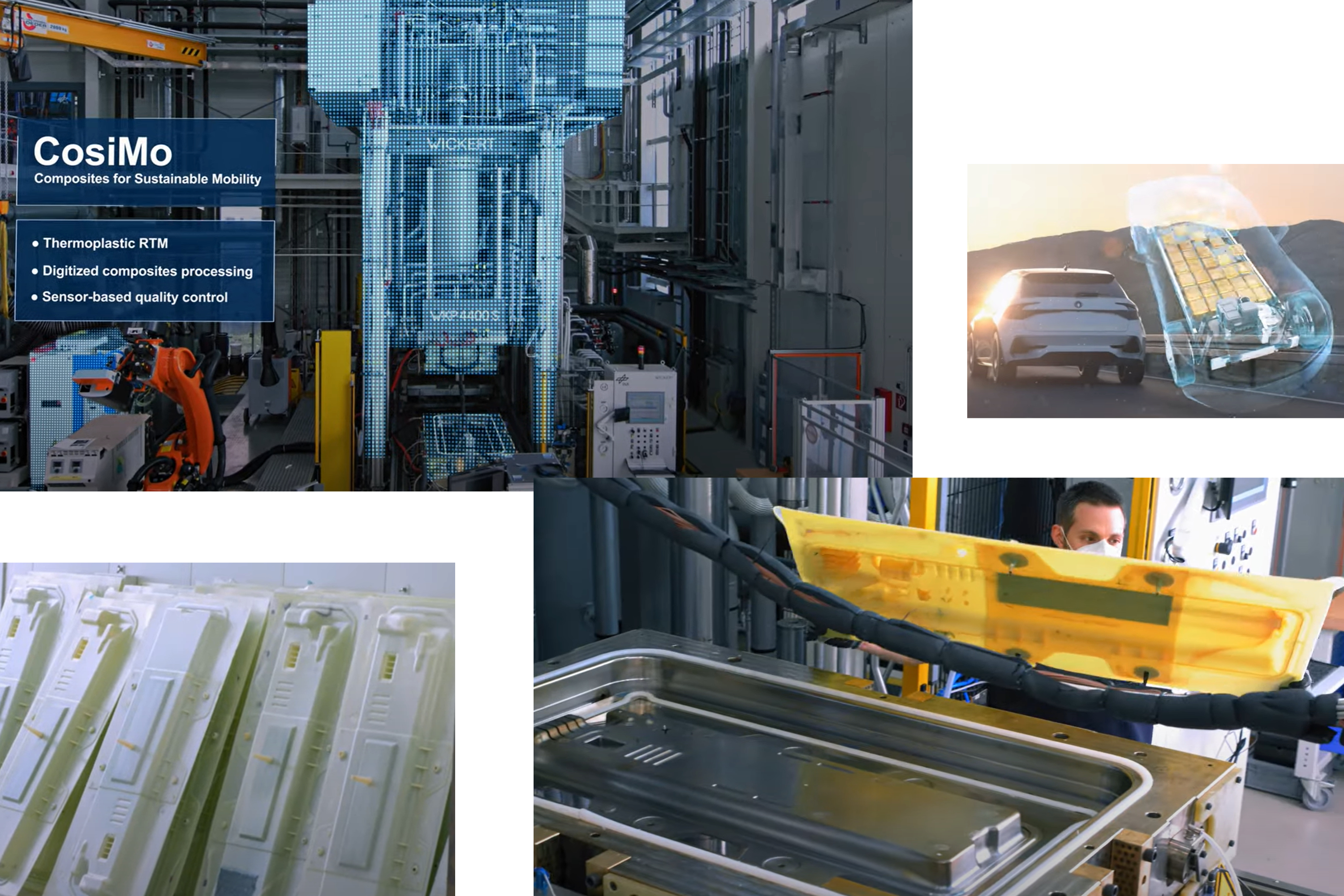
O projeto “compósitos para mobilidade sustentável” (CosiMo) foi lançado em 2018 pela Faurecia Clean Mobility (Nanterre, França) para desenvolver um processo inteligente de moldagem por transferência de resina composta termoplástica (RTM) usando uma rede de sensores abrangente, incluindo dados de um molde inteligente também como dados de máquina de uma máquina de injeção e prensa a quente. O projeto será concluído no final de 2021 e os parceiros da CosiMo ganharam conhecimento e experiência com controle de malha fechada combinando dados de sensor em tempo real com parâmetros de material de dados de laboratório e dados de simulação. CosiMo é financiado pelo ministério bávaro de assuntos econômicos, desenvolvimento regional e energia dentro do programa Campus Carbon 4.0.
A parte de demonstração, medindo 1.100 milímetros de comprimento e 530 milímetros de largura, foi projetada pelo centro de pesquisa da Faurecia Clean Mobility em Augsburg, Alemanha. O objetivo era explorar as limitações do material e do processo, incluindo núcleo de metal e espuma, geometria complexa, vários raios e espessuras variando de 2,5 a 10 milímetros. Tecidos não tecidos de fibra de vidro de até 1.000 gramas / metro quadrado foram fornecidos pela instalação do Instituto de Tecnologia Têxtil (ITA) em Augsburg. Tecidos de fibra de vidro não crimpados (NCF) e fitas unidirecionais de fibra de carbono para reforço local também foram investigados. Os materiais de fibra de vidro permitem o uso de fibras recicladas de peças compostas em fim de vida (EOL).
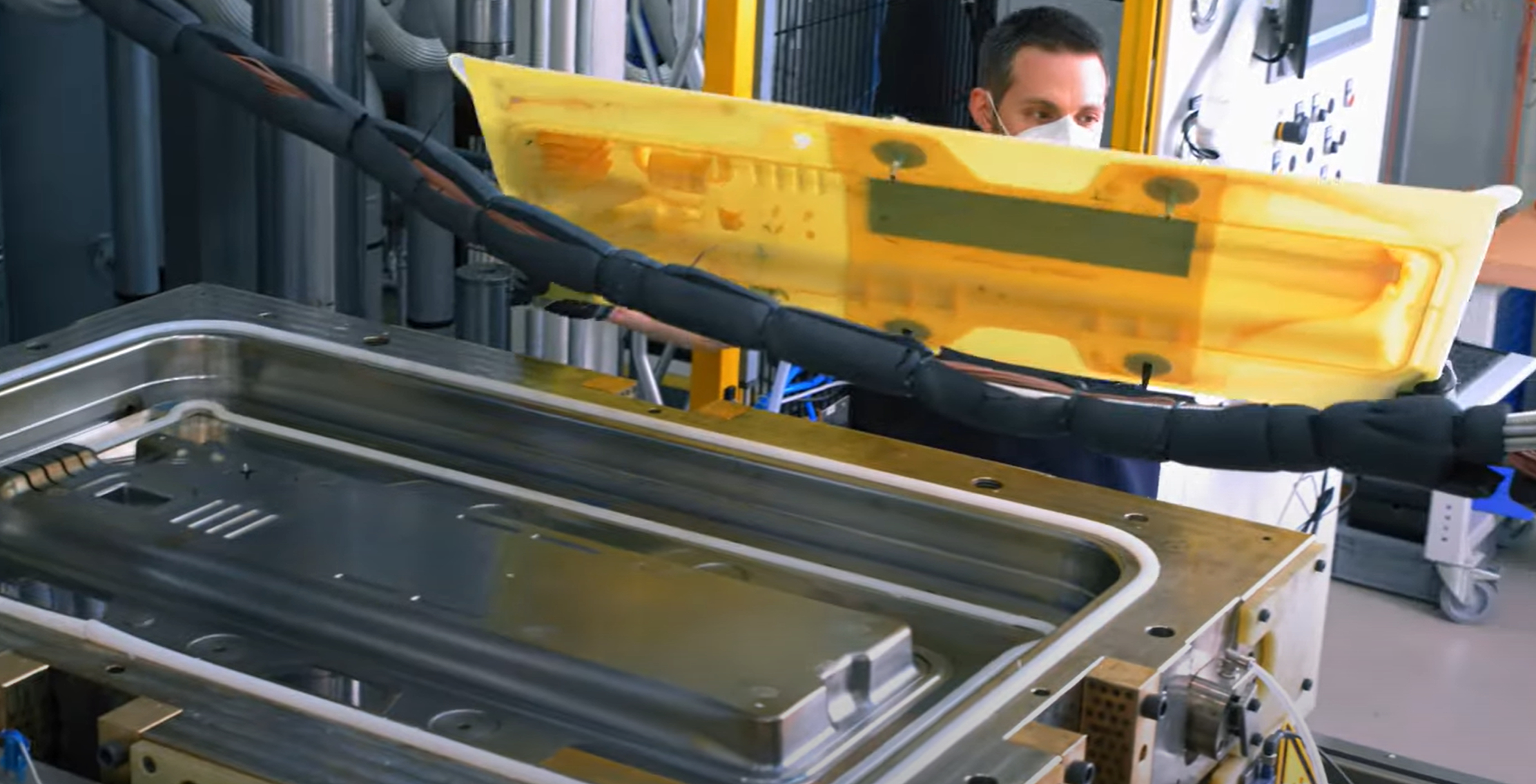
Com base no projeto da peça da Faurecia Clean Mobility e na ferramenta de pré-formação fabricada em Augsburg, o processo T-RTM em CosiMo usou uma máquina de injeção KraussMaffei (Munique, Alemanha) 3K (três componentes). O processo é um derivado de um processo 2K patenteado pela Tecnalia (Donostia-San Sebastián, Espanha), que foi demonstrado pela KraussMaffei na feira 2016 K em Düsseldorf, Alemanha. A máquina de injeção 3K foi combinada com uma prensa a quente de 4.400 kilonewton Wickert (Landau in der Pfalz, Alemanha) na qual uma ferramenta RTM de aço foi instalada. A ferramenta RTM foi fabricada pela Siebenwurst em Dietfurt, Alemanha.
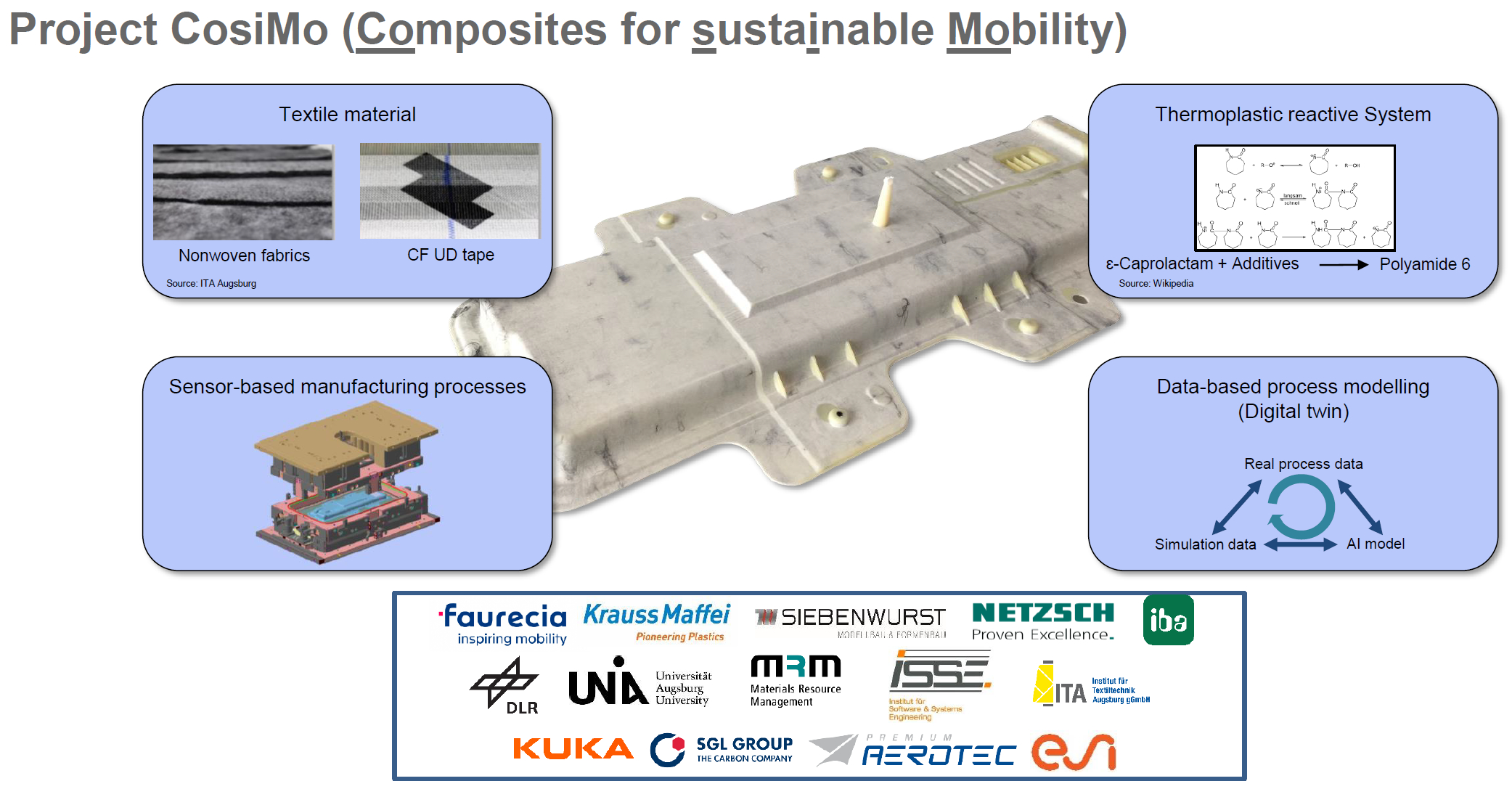
O objetivo principal do projeto era investigar a automação total e o controle de processo baseado em sensor para um processo T-RTM de etapa única usando um molde RTM com sensor e uma prensa a quente. Cerca de 100 peças de demonstração foram fabricadas neste projeto pelo Centro Aeroespacial Alemão (DLR), Centro de Tecnologias de Produção Leve (ZLP, Augsburg). “Essas peças, feitas com reforços variados, eram de alta qualidade e demonstraram alta reprodutibilidade”, disse o líder do projeto de manufatura da CosiMo na DLR ZLP, Jan Faber.
Como líder do projeto para o pacote de trabalho “HAP 3 - Ferramentas Inteligentes”, DLR ZLP também forneceu a interface chave entre as caracterizações básicas de material nos pacotes de trabalho “HAP 1 - Não Tecidos Sob Medida” e “HAP 2 - Sistemas Reativos” e os pacotes de trabalho “HAP 4 - Controle de processo baseado em dados ”.
Rede de sensores
Mais de 70 sensores foram integrados ao ferramental RTM de aço para monitorar os parâmetros do processo durante a injeção de resina e polimerização in-situ. Essa rede compreendia uma variedade de sensores, incluindo sensores combinados de pressão / temperatura da Kistler (Winterthur, Suíça), sensores dielétricos da Netzsch (Selb, Alemanha) e sensores ultrassônicos desenvolvidos pela Universidade de Augsburg. Os últimos são baseados em conceitos de sensores piezoelétricos comerciais amplamente usados, mas modificados para as altas temperaturas e requisitos de integração no molde do processamento de compósitos termoplásticos. Os dados do material, do processo e da máquina foram coletados, processados e publicados na plataforma de aprendizado de máquina por um sistema central de aquisição de dados fornecido pela iba AG (Fürth, Alemanha).
Simulação e otimização de processos
A rede de sensores permitiu o monitoramento do fluxo de resina e da polimerização, bem como o rastreamento de parâmetros de peças na geometria complexa da ferramenta. Os parâmetros do processo, como temperatura e pressão, foram usados para analisar o enchimento da resina em tempo real e o comportamento da polimerização.
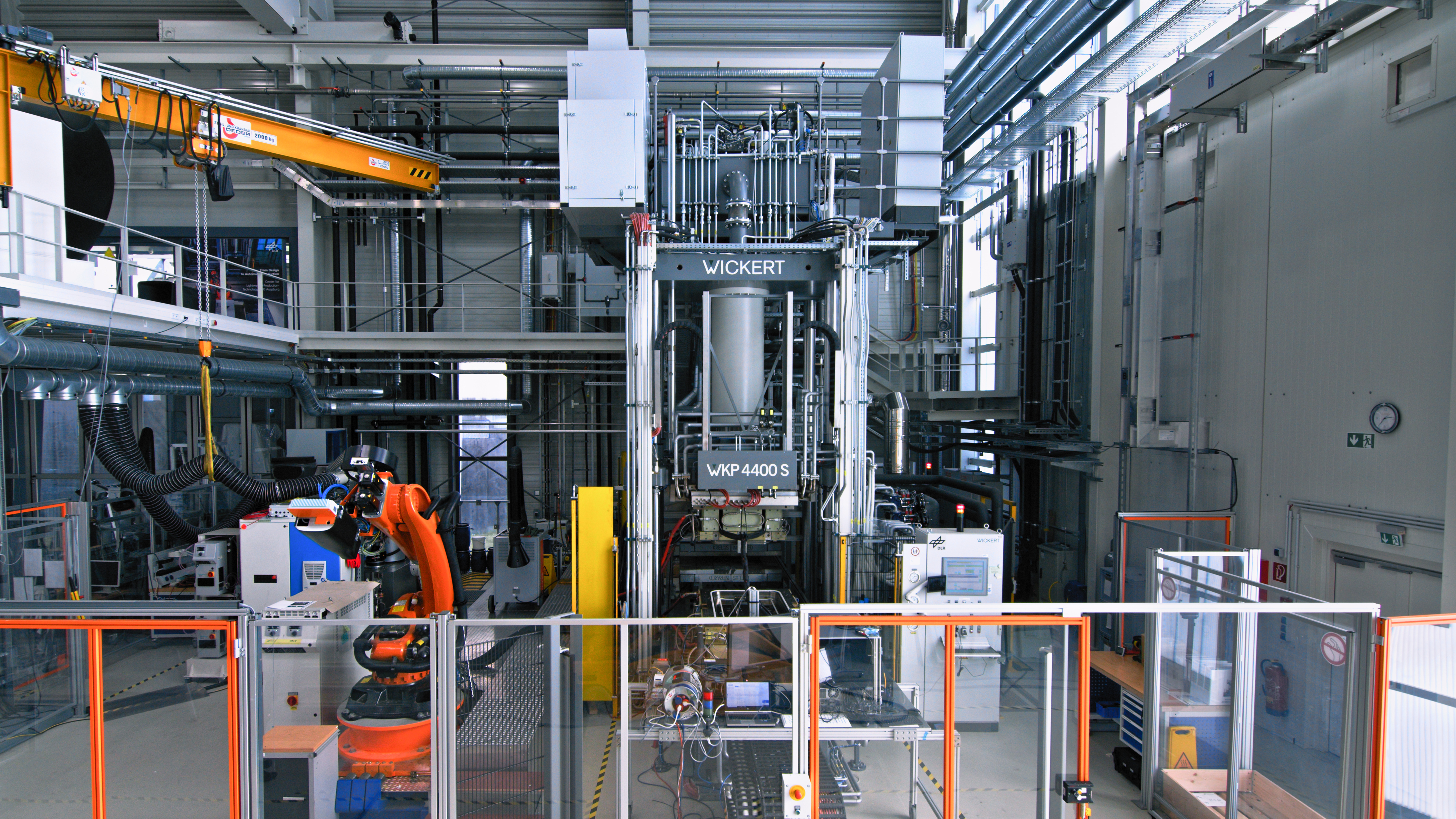
Dados de parâmetros de processo de sensores também foram usados para otimizar modelos de simulação de processo. Com base em um demonstrador de fabricação previamente definido, os subprocessos da fabricação da peça (por exemplo, simulação de enchimento de resina) e as características do componente polimerizado (por exemplo, simulação de distorção) foram modelados com software de compósitos ESI PAM (ESI Group, Rungis, França). DLR ZLP comparou esses resultados de simulação com dados de processo reais para otimizar o processo T-RTM, como parte das atividades do HP3-Workpackage.
O projeto, então, desenvolveu um controle de processo automatizado e baseado em dados de simulação baseado em métodos de aprendizado de máquina. O Instituto de Engenharia de Software e Sistemas (ISSE, prof. Reif) da Universidade de Augsburg gerou dados de treinamento de aprendizado de máquina e desenvolveu modelos de inteligência artificial (IA) prevendo o status de polimerização, bem como o tempo necessário para a polimerização e possíveis problemas durante subprocessos de injeção de resina, enchimento e polimerização. Isso foi feito em cooperação com Kuka (Augsburg, Alemanha), outro parceiro-chave do projeto.
Um modelo cinético que descreve o progresso da polimerização foi desenvolvido pelo Instituto de Gerenciamento de Recursos de Materiais (MRM) da Universidade de Augsburg. Netzsch também foi um colaborador importante, transferindo seu conhecimento de monitoramento de processo termofixo para monitoramento de processo termoplástico para ajudar a estabelecer a capacidade dos modelos de IA preditivos de prever em que momento a polimerização PA6 deve ser concluída e qual seria o estado de polimerização.
Fabricação e teste de peças
Para a produção de peças, o ferramental de aço foi aquecido a 170 ° C e os componentes da resina caprolactama reativa foram aquecidos a 120 ° C. A pré-forma foi colocada no molde, que foi então fechado. Após uma breve pausa para permitir que a pré-forma atinja a temperatura de molde, o monômero de caprolactama foi injetado, o que levou de 20 a 25 segundos. A simulação do processo mostrou que a polimerização in situ exigiu 5,7 minutos após a injeção para 98,5% de conversão. Após este tempo, a prensa foi aberta e a peça desmoldada a 170 ° C.
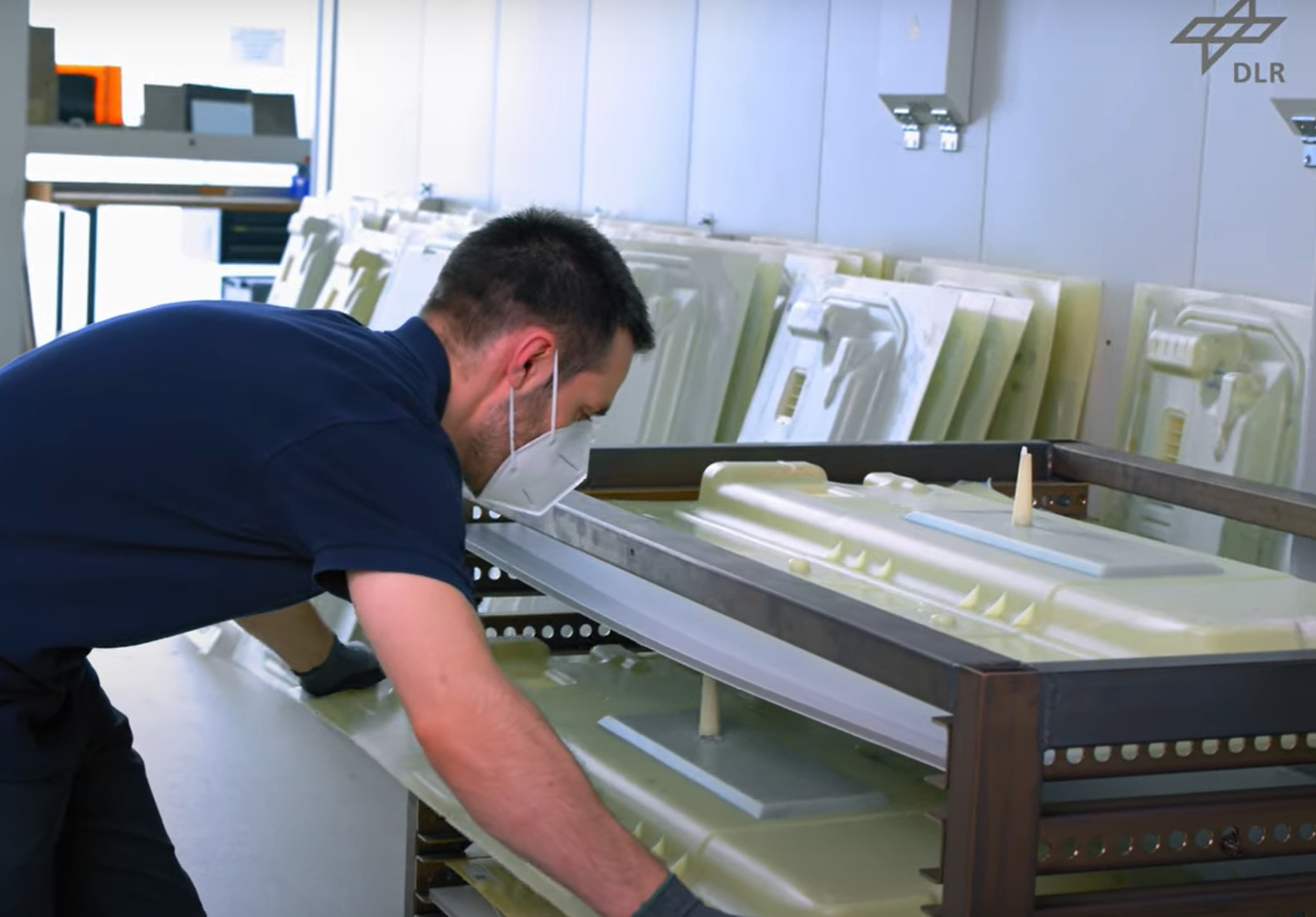
O grau de polimerização foi confirmado por espectroscopia de infravermelho, dados reométricos e análise de sensor DEA de polimerização. As peças acabadas foram avaliadas usando testes não destrutivos, incluindo microscopia, termografia e ultrassom acoplado a ar. A qualidade da peça foi correlacionada com os dados do sensor do processo e comparada com peças similares de fibra de vidro / termoplástico no mercado.
Desenvolvimento futuro
Para DLR ZLP, diz Faber, este projeto foi um sucesso. “Concluímos nossa parte e desenvolvemos muito conhecimento sobre o uso de sensores para obter controle totalmente digital de malha fechada do processamento de compósitos”, diz ele. “Para a produção industrial em série, ninguém instalaria tantos sensores e isso não é o que esperaríamos. Mas para esta investigação de pesquisa, esta grande rede de sensores foi muito precisa e nos ajudou a ter total visibilidade do processo e do comportamento do material. Pudemos ver os efeitos locais no processo em resposta às variações na espessura da peça ou nos materiais integrados, como o núcleo de espuma. ”
Ele observa que este projeto gerou muito conhecimento e vê potencial futuro para aplicá-lo a processos de RTM e infusão mais lentos, onde o risco de problemas de qualidade das peças tem sido historicamente muito alto. Faber também apresentará os desenvolvimentos do projeto CosiMo e os resultados em “Monitoramento do processo baseado em sensor de polimerização in-situ na fabricação de T-RTM com caprolactama” na quarta-feira, 29 de setembro durante o evento ao vivo e virtual, conferência SAMPE Europa 21, na Sessão 1, Sala 1 - Automotivo.
DLR ZLP também é um dos três principais parceiros da Augsburg AI (inteligência artificial) Production Network - fundada em janeiro de 2021 - que também reúne a Universidade de Augsburg e o Instituto Fraunhofer para Fundição, Compósitos e Tecnologia de Processamento (Fraunhofer IGCV). Conforme explicado pelo Dr. Markus Sause, diretor da AI Production Network e também pesquisador do projeto CosiMo desenvolvendo sensores ultrassônicos, “Vamos estender este projeto de colaboração que foi destacado no projeto CosiMo para uma escala muito maior, desenvolvendo Tecnologias de IA para produção com forte foco em compósitos. Nossa nova instalação de 5.000 metros quadrados em Augsburg será inaugurada em 2022 e equipada com uma variedade de máquinas ao longo do próximo ano, permitindo que as empresas vejam demonstrações do que a IA pode fazer por processos reais em um ambiente de produção. ”
A Faurecia Clean Mobility, por sua vez, estenderá internamente o conhecimento adquirido com o projeto CosiMo, que está totalmente alinhado com a estratégia de sustentabilidade e transição ecológica da Faurecia. Faurecia agradece também ao Ministério Federal da Bavária para Assuntos Econômicos, Desenvolvimento Regional e Energia, que apoiou financeiramente este projeto de pesquisa.
Resina
- Bateria
- Composto TPE usado para cotonetes de ‘algodão’ sustentáveis
- Biomaterial termoplástico ‘Ajustado’ para aplicações médicas
- TPE de nível médico usado para bola de terapia premiada
- Personalização de sensores ultrassônicos para otimização e controle de processos compostos
- Fitas termoplásticas continuam a mostrar potencial para aeroestruturas compostas
- Polyscope Polymers ganha Prêmio de Inovação JEC para trilhos-guia de composto termoplástico
- Porta termoplástica a primeira para compósitos automotivos
- Fatores importantes de consideração para terceirizar um processo de montagem de caixa
- Coisas a considerar para o processo de montagem da caixa