Fitas termoplásticas multicamadas, AFP e infusão de resina para compósitos mais democráticos
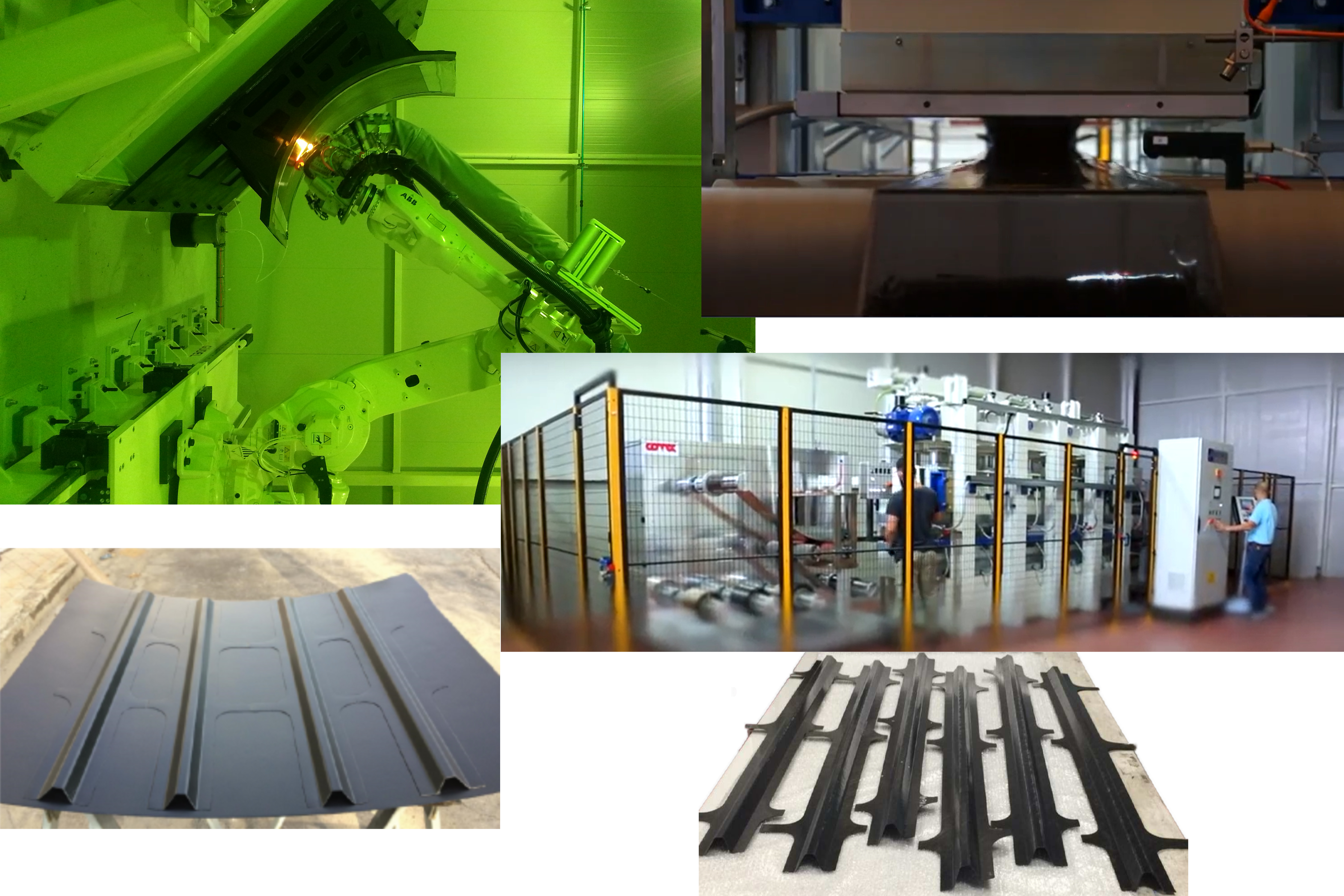
Novotech (Nápoles, Itália) começou como um spin-off da Universidade de Nápoles “Federico II” no sul da Itália, fundada pelo professor Leonardo Lecce em 1992. “Apoiamos empresas de aviação geral e fornecemos serviços de P&D em toda a Itália”, diz Lecce que agora é o CEO da Novotech. “Fornecemos análises estruturais para peças de aeronaves e também ajudamos no desenvolvimento de aeronaves.”
Localizada perto da fábrica da Leonardo que faz as seções de fuselagem de compósitos para o Boeing 787, a Novotech começou a se concentrar em compósitos em 2014. Ela comprou uma célula de colocação automática de fibra (AFP) da Coriolis Composites (Queven, França) e desenvolvida em autoclave ( OOA) processamento, incluindo infusão de resina e fabricação de compósitos termoplásticos, com especialização em consolidação in-situ usando AFP.
A Novotech participou de vários projetos de pesquisa da indústria, incluindo:
- MESEMA (Sistemas de energia magnetoelástica para aeronaves ainda mais elétricas)
- SARISTU (Estruturas de aeronaves inteligentes inteligentes)
- ASAM (Simulação Avançada de Mecanismos de Aeronave)
- LAMITECH (Métodos de teste inovadores para estratificação automática de materiais compostos híbridos)
- PROALATECH (Caracterização Estrutural e Análise de Soluções de Reparo de Empennages CFRP Inovadores)
- FACE (Ambiente amigável da cabine da aeronave)
- AIRGREEN 2 - CLEAN SKY 2 (Desenvolvimento de conceitos e metodologias de asa inovadores para aeronaves regionais de próxima geração)
- SISTER CHECK (Investigação e integração de sistema inovador para inspeção não destrutiva AFP)
- TRINITI - CLEAN SKY 2 (tanques termoplásticos de nitrogênio de alta pressão multimateriais para aeronaves)
- NHYTE - H2020 (novas aeroestruturas compostas termoplásticas híbridas fabricadas por OOA)
“Também temos um relacionamento especial com a Cytec no Reino Unido, desenvolvendo novos materiais e processos compostos”, diz Lecce. Observe que a Cytec foi adquirida pela Solvay e o local referenciado é Solvay Composite Materials em Heanor, Reino Unido - um local com uma longa história de inovação, incluindo o processo de formação de diafragma duplo recentemente testado por meio do programa RAPM. “Nossa última atividade foi desenvolver um processo termoplástico OOA que usa uma nova e inovadora prensa que combina PEEK (polieteretercetona) e PEI (polieterimida) em um novo material composto.” Este novo material, equipamento e processo agora foi demonstrado em uma longarina de aeronave de plástico reforçado com fibra de carbono (CFRP), feita usando consolidação in-situ AFP e soldagem por meio do projeto NHYTE.
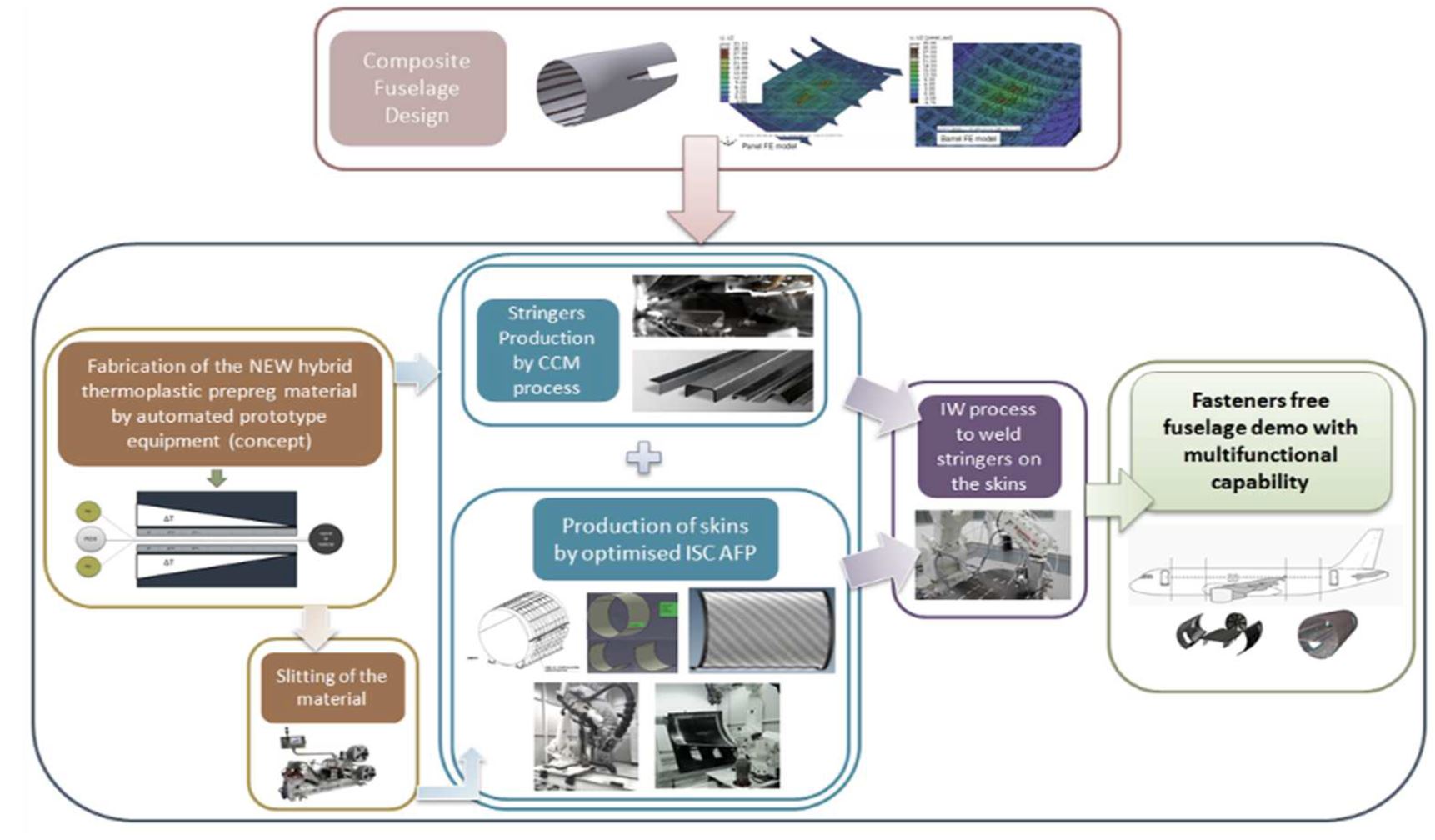
NHYTE
Financiado pelo programa Horizonte 2020 da Comissão Europeia, NHYTE é um projeto de pesquisa conduzido de maio de 2017 a outubro de 2020. “NHYTE é sobre o uso de ligação amorfa para permitir temperatura sustentável e condições de processo para compósitos termoplásticos”, explica Dr. Marco Barile, coordenador do projeto NHYTE e CTO da Novotech. Essa ligação amorfa (veja o diagrama abaixo) é um conceito patenteado por outro parceiro da NHYTE, a divisão de aeroestruturas da Leonardo (Roma, Itália), que possui várias instalações de produção no sul da Itália.
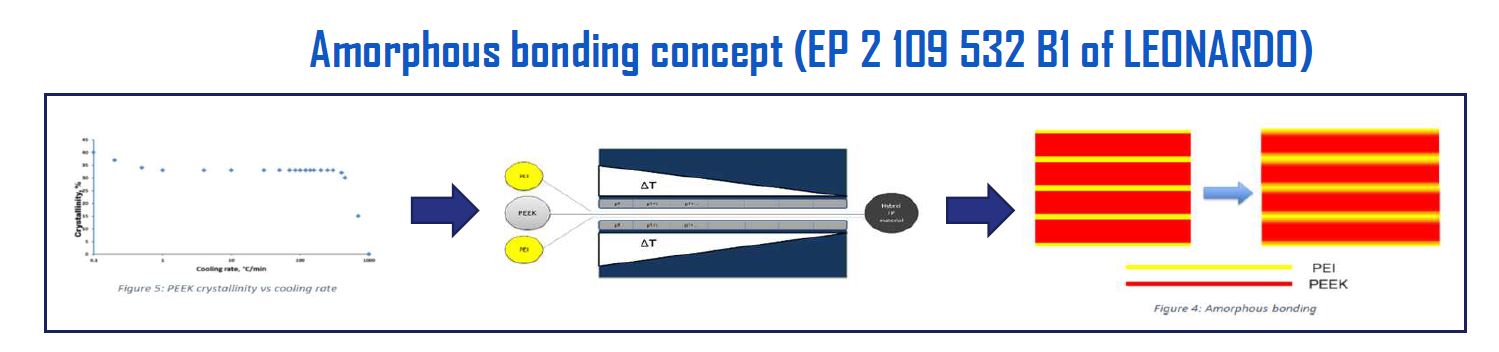
Crédito da foto:projeto NHYTE
“Com o material desenvolvido no NHYTE, podemos superar as atuais limitações do material com a consolidação in-situ AFP (ISC) de compósitos termoplásticos (TPC). Em vez de processar a temperaturas abaixo de 400 graus C para os polímeros PEEK semicristalinos, podemos aquecer um pouco acima da temperatura de transição vítrea de 215 graus (Tg) para a camada PEI amorfa. O derretimento e o resfriamento do PEI também são mais rápidos, não precisando ser tão controlados em relação ao PEEK. ” Barile observa que esse conceito pode usar outros termoplásticos amorfos. O PEI foi escolhido porque adere bem ao PEEK, um material comprovado em vários demonstradores de aeroestrutura AFP.
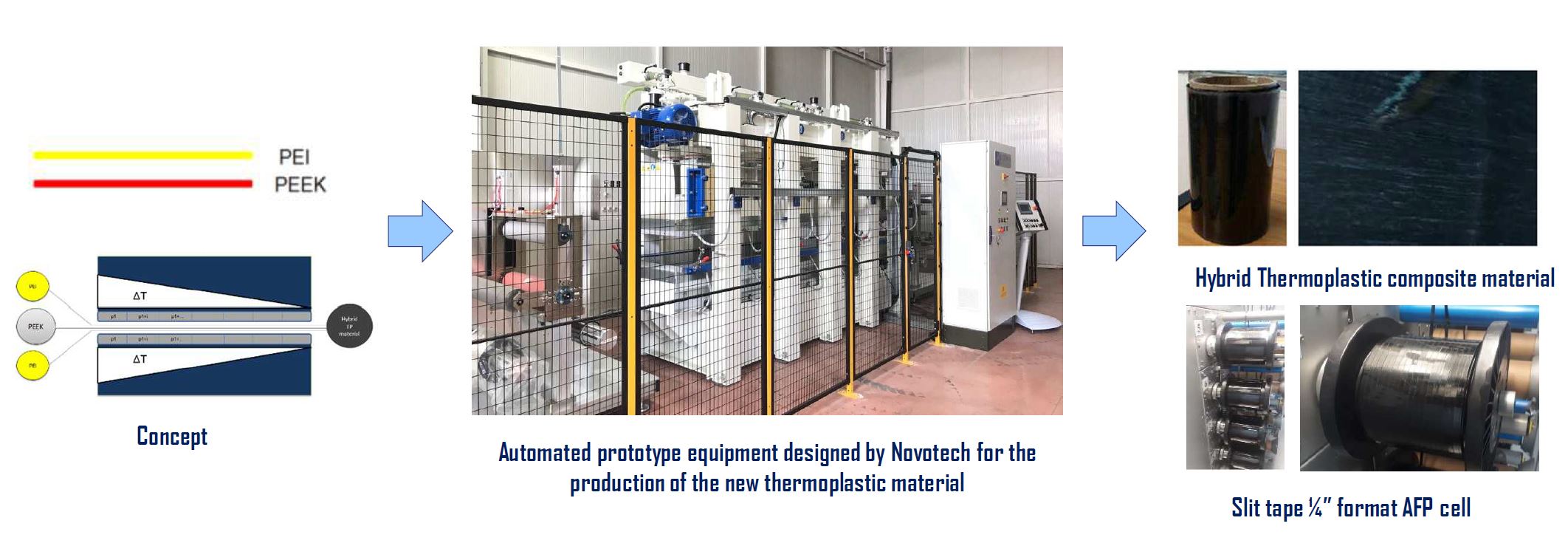
Este novo material desenvolvido na NHYTE foi produzido em uma prensa contínua projetada pela NOVOTECH. Orma Macchine (Bergamo, Itália) forneceu o corpo da prensa e a COMEC Innovative (Chieti, Itália) forneceu os módulos de enrolamento e desenrolamento. “Esta prensa pode fazer um rolo contínuo de material que então cortamos em fita cortada para uso em uma máquina AFP”, diz Barile. Três materiais diferentes entram na prensa pela esquerda, como pode ser visto na imagem acima. “Temos PEI na parte superior e inferior e, em seguida, PEEK no meio”, explica Barile.
Como um polímero semicristalino, PEEK fornece as altas propriedades mecânicas necessárias para estruturas primárias, enquanto as camadas de PEI amorfas fornecem fusão rápida e simples para ligação. “Controlamos a pressão e o resfriamento do material ao longo das placas da prensa, partindo de cerca de 400 graus C no início da prensa até menos de 200 graus C no final da prensa. O resultado é um material que é uma combinação das três camadas de entrada. ”
Este novo tipo de fita termoplástica já está consolidado durante a fabricação, de forma que durante o AFP, basta ser aquecido para derreter e compactar as camadas de PEI para a colagem amorfa. O resultado é um laminado compreendendo fita PEEK para PEI totalmente consolidada e camadas de PEI para PEI, conforme mostrado na patente de Leonardo. Este processo AFP apresenta menos obstáculos em relação ao AFP ISC atual usando fitas PEEK e PEKK (polieteretercetona). Conforme explicado na Parte 2 do meu recurso de 2018 sobre consolidação in-situ, o AFP ISC atual requer o aquecimento da fita e do substrato até a temperatura de fusão, colocando a fita no substrato e, em seguida, consolidando com um rolo para que o processo de resfriamento seja precisamente controlado, permitindo os polímeros semicristalinos para atingir cristalinidade suficientemente alta (30-40%) e baixos vazios (<3-5%) para propriedades estruturais.
Os críticos do ISC AFP afirmam que é muito lento - uma taxa de deposição de 60-100 mm / s versus 600-700 mm / s para o método de "duas etapas" que compreende uma disposição AFP rápida seguida por uma etapa secundária no forno ou autoclave para totalmente consolidar / recozer o estresse térmico no laminado. “Com nosso material, você pode alcançar taxas de deposição de AFP que não são tão lentas quanto a consolidação in-situ típica e o aquecimento necessário durante a AFP também pode ser mantido abaixo de 300 graus C”, diz Barile. “Você pode fechar a lacuna de desempenho com materiais padrão que temos agora.” Aqui, Barile está comparando o AFP ISC de compostos termoplásticos aos compostos termofixos usados nas aeronaves Boeing 787 e Airbus A350. “Com componentes grandes, como seções da fuselagem, o problema é a acessibilidade ao usar a cura em autoclave. Os termoplásticos permitem um processo de produção mais acessível, mas você tem altas temperaturas e taxas de AFP lentas com os materiais de grau aeroespacial atualmente disponíveis no mercado. Nossa abordagem ajuda a resolver esses problemas. Podemos atingir cerca de 30 por cento de cristalinidade na fita por meio da prensa contínua. Assim, você tem aquela cristalinidade na peça e está trabalhando apenas com a camada amorfa durante o AFP. Embora este ainda seja um material experimental, que pode ser melhorado, o objetivo do projeto NHYTE é ter um processo de fabricação de uma etapa que você pode usar em aplicações aeroespaciais estruturais. ”
Otimização de fita e AFP
“Os primeiros materiais de fita multicamadas foram feitos aqui na Novotech”, diz Barile. Essas fitas usaram a película de fenda não preenchida Sabic (Riyadh, Arábia Saudita) Ultem 1000 para PEI e fita PEEK reforçada com fibra de carbono APC-2 / AS4 da Solvay. A espessura total era de ≈0,26 milímetros, compreendendo camadas PEI com 1 ou 2 mils (0,001 ou 0,002 polegadas) de espessura. Na primeira fase do projeto, múltiplos cupons de ambas as variações foram testados para resistência ao cisalhamento interlaminar (ILSS) a fim de validar o processo de fabricação do material termoplástico híbrido. Pequenos cupons também foram testados pelo parceiro da NHYTE, Applus Laboratories (Barcelona, Espanha) para uma gama completa de propriedades mecânicas, incluindo resistência à tração e compressão e módulo, compressão de orifício aberto (OHC), tensão de orifício preenchido, compressão após impacto (CAI), pouco visível dano por impacto (BVID) e propriedades após o condicionamento do fluido.
“Não tínhamos a mesma experiência que os fornecedores de fitas compostas termoplásticas, então a qualidade do material pode ser melhorada. Por exemplo, o volume da fibra varia de baixo a alto ao longo da espessura, o que afeta as propriedades da fita e do laminado, incluindo ILSS. Mas NHYTE teve como objetivo demonstrar o conceito, o que temos feito. ”
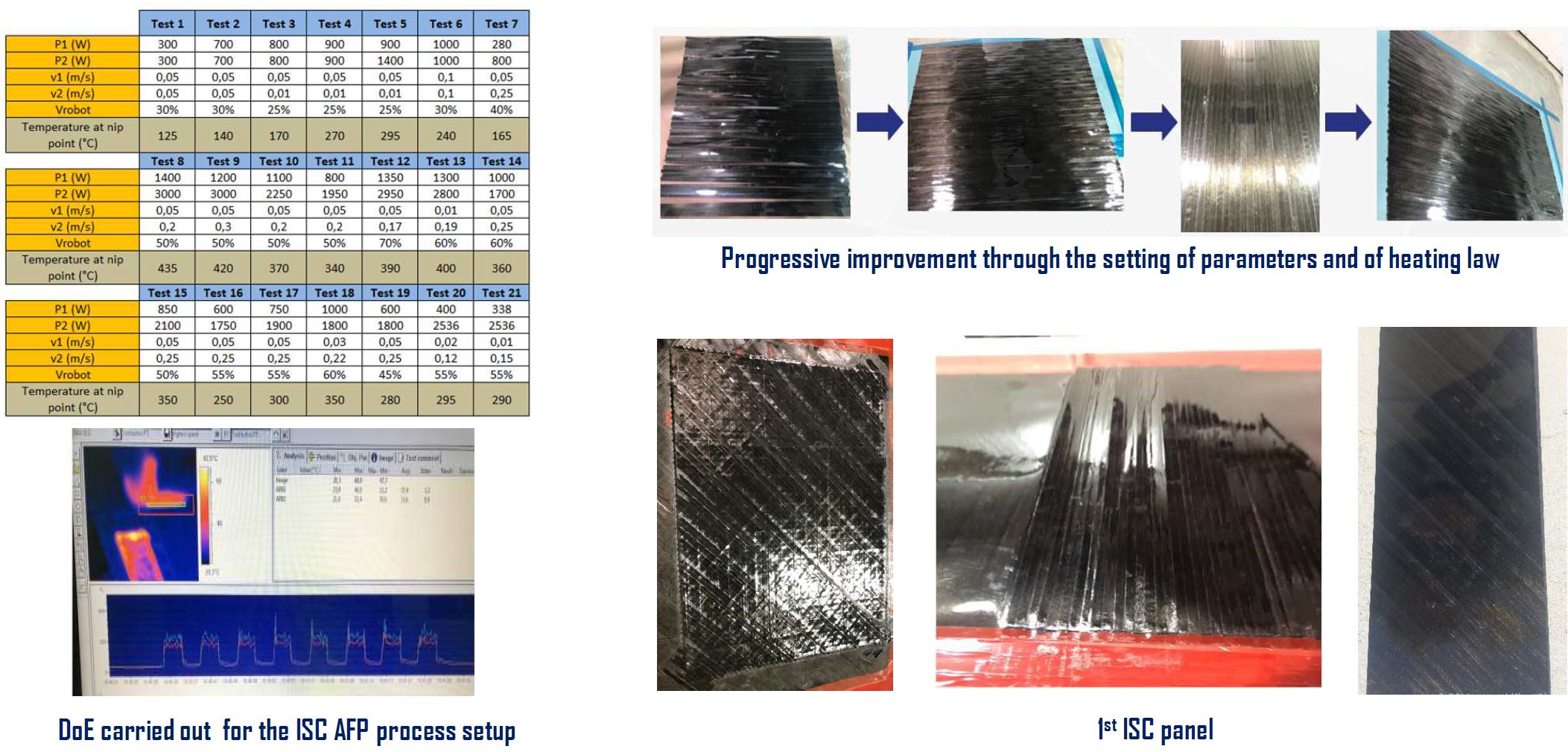
Como pode ser visto nas imagens acima, otimizar o processo AFP para o novo material exigiu um trabalho experimental significativo. “Também usamos uma abordagem de design de experimentos (DOE) para otimizar os parâmetros AFP e uma ferramenta foi desenvolvida pela Universidade de South Brittany (USB, Lorient, França), parceira da NHYTE, para melhorar a carga de aquecimento do laser por meio de simulação numérica preditiva.” notas Barile.
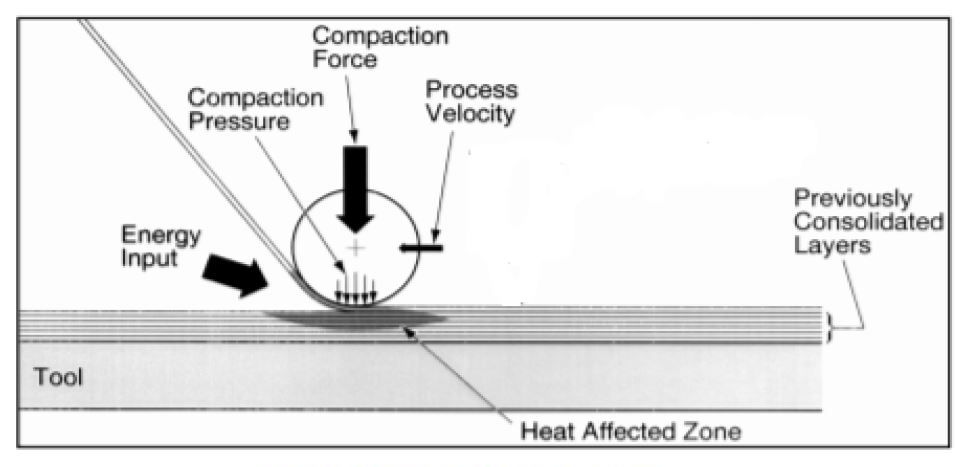
Essa simulação foi usada pela primeira vez na fita APC-2 para verificar a qualidade da ferramenta preditiva e, em seguida, foi aplicada ao novo material multicamadas. Um artigo sobre este trabalho foi submetido para publicação na revista Composite Structures . “Você está modelando as condutividades de calor no ponto de contato”, diz Barile. “A seguir verificamos experimentalmente o que foi previsto na simulação numérica. Isso é necessário para determinar o melhor compromisso entre a velocidade de deposição, o fluxo de fusão dos polímeros e o envelhecimento [cozimento] da lâmina composta. É um equilíbrio de várias variáveis durante o processo de consolidação in-situ. Observamos a diminuição da temperatura da fita que entra na fita já colocada na ferramenta. Se você conseguir controlar essa mudança de temperatura, poderá reduzir a tensão residual no laminado. Portanto, trabalhamos para avaliar a variação de temperatura durante a colocação. Você deve personalizar o aquecimento de acordo com a forma do caminho e a orientação da lâmina.
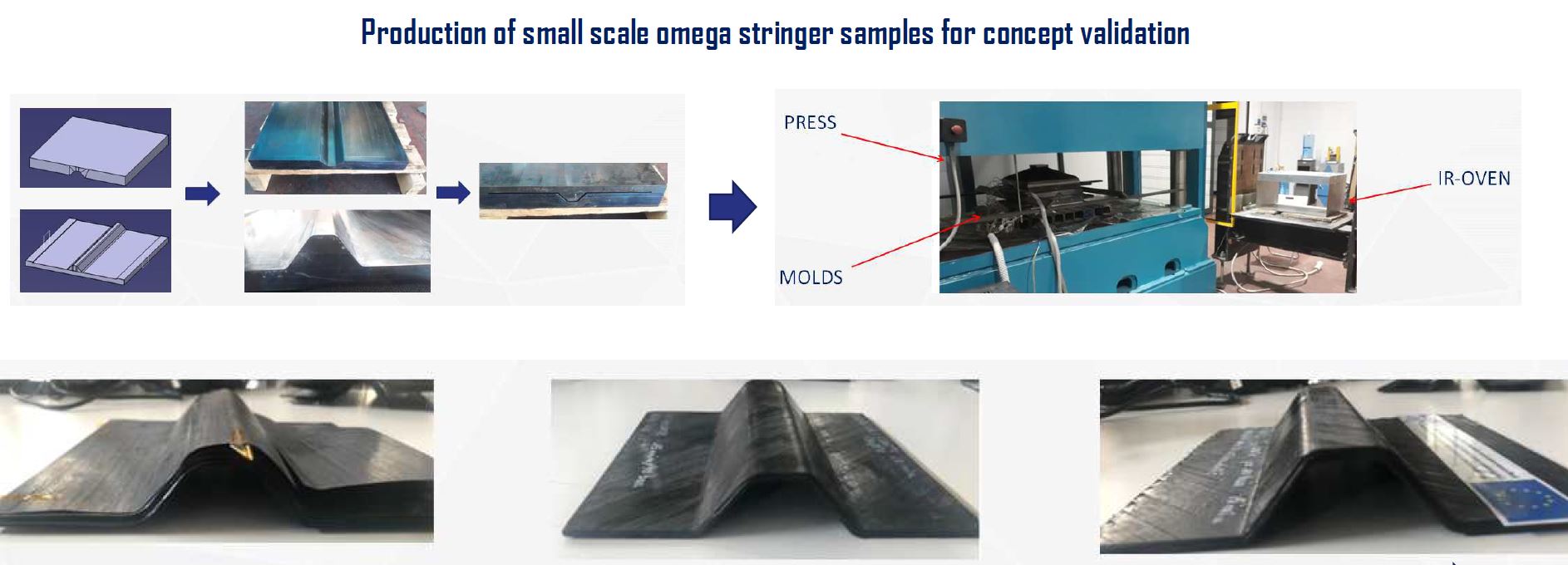
Demonstradores de longarinas e fuselagem
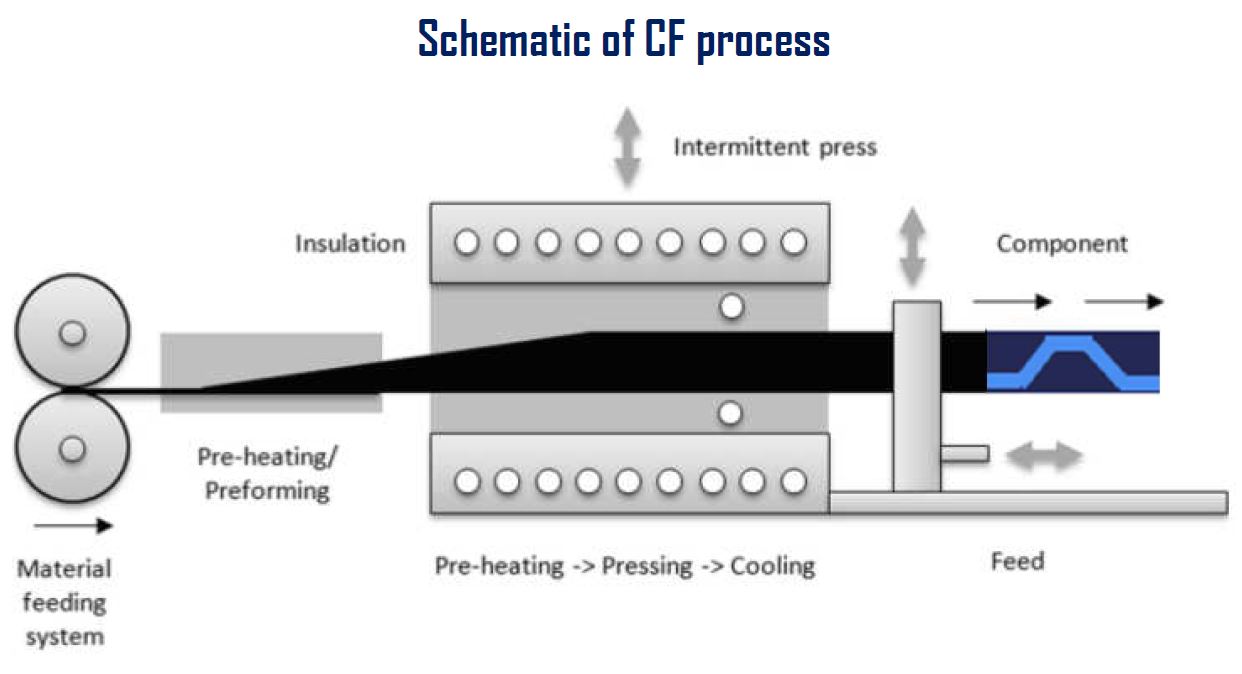
A próxima etapa foi produzir demonstradores de longarina, primeiro como amostras em pequena escala feitas com uma prensa estacionária e, em seguida, como demonstradores de um processo de conformação contínua de longarina para verificar o que seria necessário para a produção de peças industriais. Essas longarinas foram então anexadas a um demonstrador de painel de pele da fuselagem AFP usando soldagem por indução desenvolvida pela organização de P&D CETMA (Brindisi, Itália).
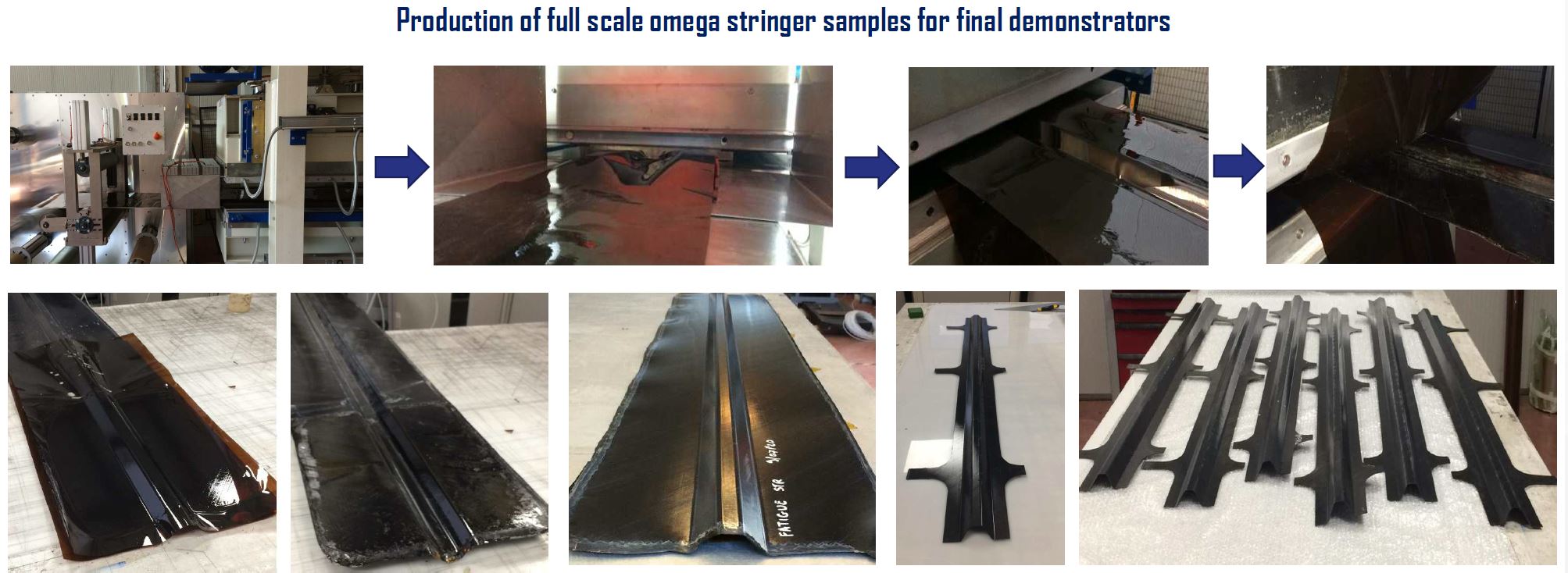
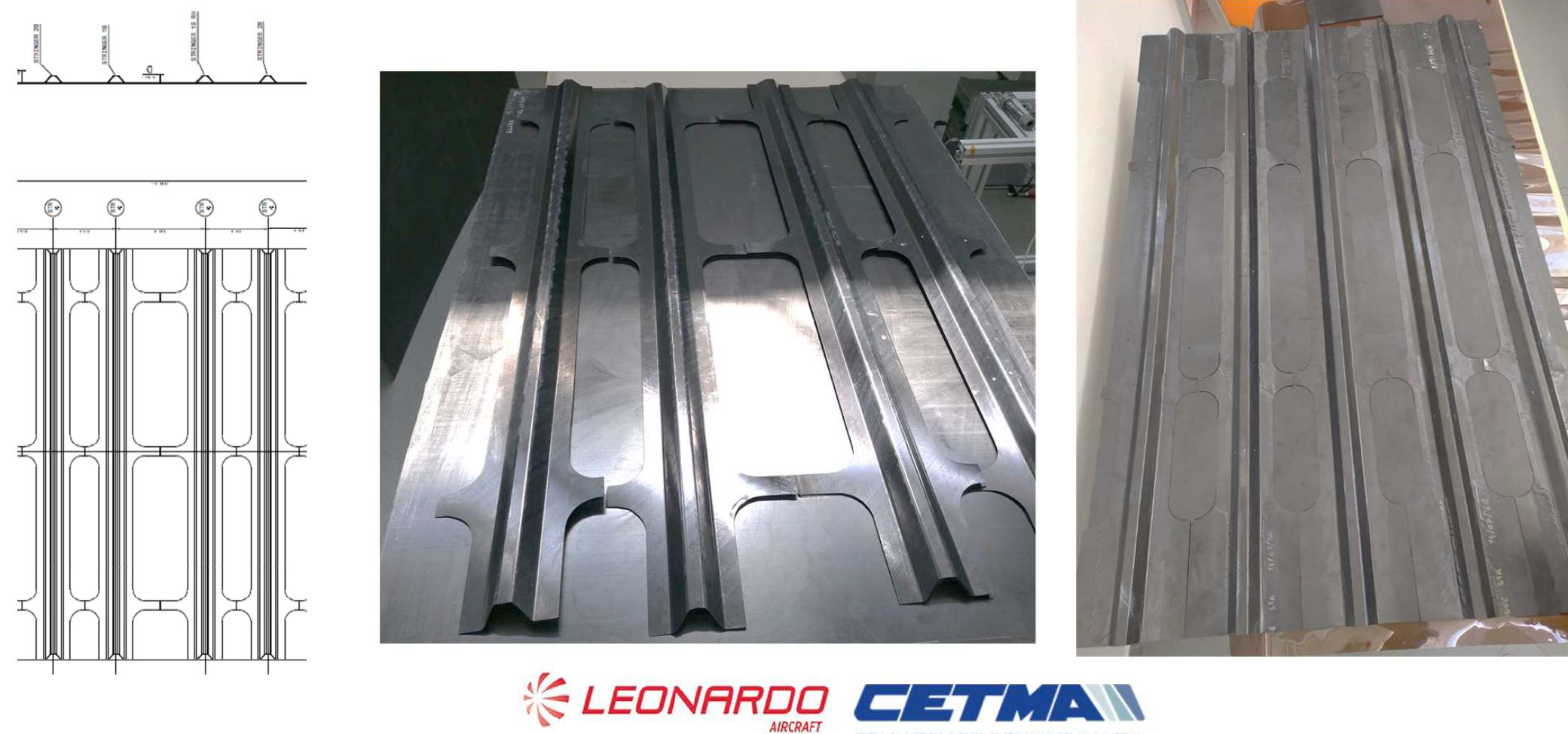
O novo material multicamadas oferece alguma vantagem para a soldagem por indução? “Ele basicamente processou o mesmo”, diz Barile. “No entanto, não foi fácil para o CETMA definir os parâmetros do processo de soldagem porque nosso novo material tem uma quantidade menor de fibra de carbono em comparação com as fitas padrão.” Os demonstradores de longarina e o demonstrador final do painel da fuselagem foram então testados por Applus. Os parceiros do projeto NHYTE University of Bath (Bath, Reino Unido) e Leonardo Aircraft também usaram o NDI para avaliar a qualidade dos painéis e longarinas.
“Fizemos muitos cupons e peças pequenas, assim como o grande demonstrador”, observa Barile. “Os resultados dos testes da Applus são muito bons considerando o custo mais baixo do processo de fabricação em comparação ao que é padrão agora. Somos 20-25% mais baixos em propriedades de resistência e rigidez em relação aos materiais de fita termoplástica padrão disponíveis atualmente, mas identificamos melhorias no processo que devem ajudar a melhorar isso. ”
A NHYTE terminou em 30 de outubro de 2020. “Nossa ideia é prosseguir com um novo projeto que inclua todas as melhorias que temos em mente”, diz Barile. “Nós provamos como fazer o material e como processar usando consolidação in-situ AFP, conformação contínua e soldagem por indução. Agora precisamos otimizar ainda mais para a industrialização. ” A Novotech busca prosseguir com o mesmo consórcio enriquecido com novos parceiros.
Notavelmente, Leonardo também está trabalhando para melhorar a consolidação in-situ AFP usando soldagem por indução e fita TPC que pode ser aquecida e resfriada rapidamente. Além disso, resultados encorajadores sobre compósitos multicamadas PEI / PEEK acabam de ser publicados por pesquisadores do Instituto de Materiais IMDEA (Madri, Espanha) e FIDAMC (Madri, Espanha), este último sendo um líder em consolidação AFP in-situ por muitos anos. Para mais artigos técnicos, consulte as publicações da NHYTE.
projeto SWING
O Smart Wing para a Nova Aviação Geral (SWING) é um projeto que começou com o endosso da Piaggio Aerospace (Villanova d’Albenga, Itália) e é co-financiado pelo Ministério Italiano de Desenvolvimento Econômico (MISE). Além da Novotech, o consórcio do projeto italiano inclui a empresa de desenvolvimento de tecnologia Protom (Nápoles) como coordenadora, a Laer Aeronautical Manufacturing (Airola), a A. Abete Aerostructures (Nola) e a especialista em design aeroespacial ItalSystem (Avellino). Um dos objetivos do SWING é adaptar processos de compósitos automatizados fora de autoclave (OOA) - incluindo AFP e infusão de resina líquida (LRI) - para produção econômica e sustentável de aeronaves menores, usando o P.180 Avanti asa dianteira como uma plataforma de demonstração.
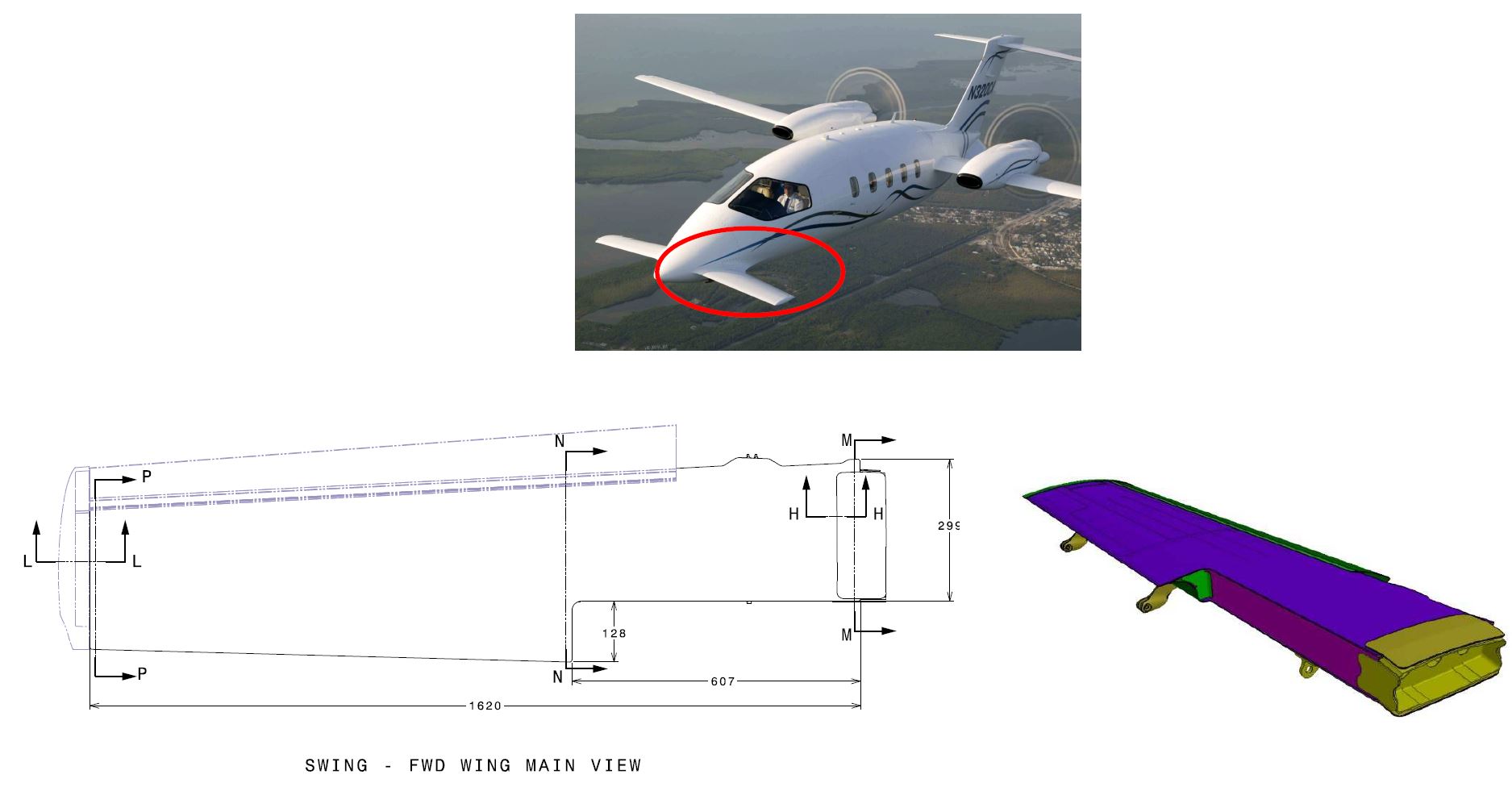
“A ideia é produzir a asa dianteira do P.180 em apenas duas partes principais:um painel superior e um painel inferior, ambos moldados com longarina e longarinas integradas”, diz Lecce.
“Para nós, isso começou com nosso trabalho como um laboratório qualificado para a Solvay no Reino Unido. Cooperamos desde 2015 em novos materiais e processos para AFP, LRI e compostos termoplásticos. Estávamos fazendo pré-formas secas usando a fita de fibra seca PRISM TX1100 da Solvay para uso com AFP. Essas pré-formas foram então infundidas com resina epóxi endurecida Solvay PRISM EP 2400 e curadas em um forno. Estávamos fazendo este trabalho no âmbito do projeto AIRGREEN 2 para o programa de aeronaves regionais verdes Clean Sky 2 e, em seguida, continuamos em frente no projeto SWING. ” Observe que o PRISM TX1100 e o PRISM EP 2400 foram qualificados pela United Aircraft Corporation para a produção da primeira asa com infusão de resina para uma aeronave comercial - o jato Irkut MS-21 de corredor único fabricado pela AeroComposit.
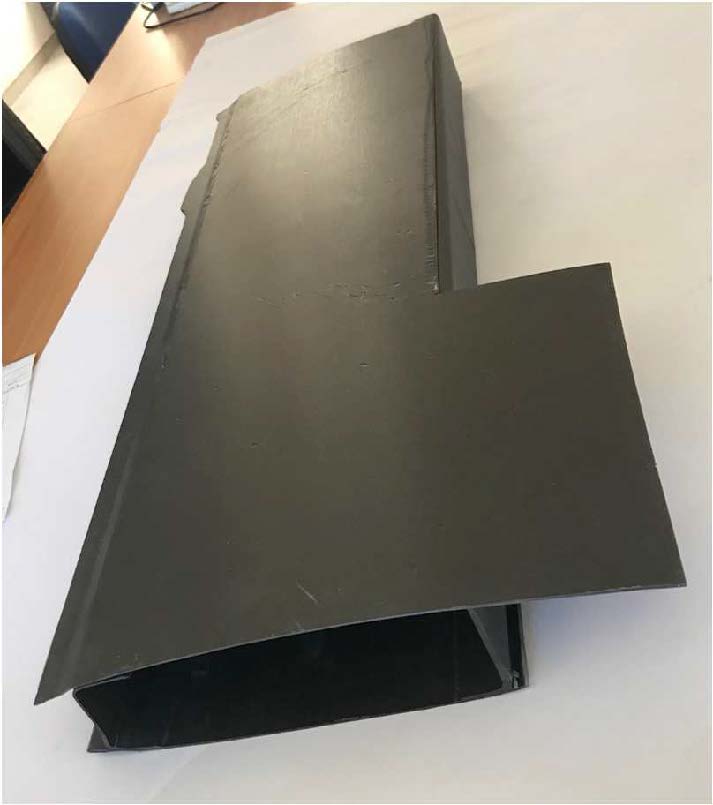
Os painéis moldados superiores e inferiores serão unidos com adesivos estruturais e testados estaticamente no próximo ano. “Paralelamente, estamos caracterizando outro compósito baseado em fita seca TX1100 e uma mistura de resina da Covestro (Leverkusen, Alemanha) que pode ser uma alternativa valiosa às resinas de grau aeroespacial, em particular para setores que exigem maiores taxas de produção”, acrescenta Barile. “Essa resina não tem um desempenho tão alto quanto aqueles sistemas, mas funciona bem com infusão e atende aos requisitos para a caixa da asa. Deve haver algum compromisso se você quiser reduzir custos. Esperamos que este desenvolvimento contribua para a introdução da tecnologia AFP na aviação geral. Também pode ser usado no setor automotivo. ”
TRINITI
A Novotech também está trabalhando no projeto Clean Sky 2 TRINITI - Tanques de nitrogênio termoplástico multimaterial de alta pressão para aeronaves - que começou em 2019 e terminará em 2021. A entrada da Novotech neste projeto mais uma vez evoluiu do desenvolvimento com uma empresa aeroespacial italiana. “Estávamos trabalhando para verificar o potencial do AFP usando nossa fita multicamadas na produção de tanques de combustível criogênico para veículos lançadores em comparação com os atuais processos de enrolamento de filamento usados”, explica Barile. “Essencialmente, a TRINITI desenvolverá um conceito de material multicamadas semelhante ao NHYTE e, em seguida, fará um tanque usando AFP consolidação in-situ.”
“A vantagem do AFP em relação ao FW”, continua ele, “é que você pode decidir onde deseja colocar o material. Você não é restringido por filamentos continuamente enrolados em torno da peça. Considere um tanque onde você tem muito material nas tampas porque você não pode cortar o material durante o enrolamento do filamento. Ao cortar e reiniciar fibras / fitas onde você quiser com o AFP, o material é usado apenas onde é necessário. Assim, você pode gerenciar lacunas entre as fitas, o que é importante para evitar a penetração de gás. Para fazer isso com enrolamento filamentar tem que aumentar o material aplicado, até porque com AFP você usa fita de fenda, não prega. E então, com a consolidação in-situ, não há necessidade de autoclave. Demonstramos que a AFP pode ser uma alternativa viável e muito acessível. ”
“Atualmente, o CETMA está realizando testes de permeação de gás para avaliar o desempenho dos materiais multicamadas em relação às especificações”, diz Barile. Os requisitos foram fornecidos pelo gerente de tópico, Diehl Aviation (Gilching e Dresden, Alemanha) para um tanque de nitrogênio de alta pressão usado em sistemas de supressão de incêndio em aeronaves. Esses tanques devem suportar temperaturas de -55 ° C a 85 ° C no solo, -40 ° C a 70 ° C durante a operação em vôo e pressões de até 1.000 bar.
“O objetivo é reduzir o peso e as etapas de fabricação”, observa. “No entanto, o custo de fabricação usando este método tem que ser definido. O peso é economizado ao não colocar material desnecessário, mas o enrolamento do filamento é um processo mais rápido em comparação com o AFP. ” Outro fator é que esse tipo de tanque normalmente tem um revestimento de metal ou plástico coberto com CFRP. Barile diz que a TRINITI está tentando um tanque sem revestimento (Tipo V). “Evitaremos a permeação de gás usando um laminado AFP de baixo vazio. Estamos testando no CETMA agora com diferentes combinações de materiais e nos preparando para fazer a seleção. Em seguida, construiremos um tanque protótipo, mas o projeto do tanque depende do material selecionado e do processo final. Então, é para isso que estamos trabalhando agora. A atividade de teste será realizada pela CTL Composites (Galway, Irlanda). ”
GAIVOTA
O desafiador projeto SEAGULL foi iniciado há três anos. “Nosso objetivo é desenvolver um pequeno hidroavião de nova geração que incorpore uma nova tecnologia de fabricação de compósitos, propulsão elétrica híbrida e uma asa dobrável automatizada, que desenvolvemos e patenteamos”, explica Lecce. “A intenção era uma aeronave de decolagem e pouso curta (STOL) que fosse competitiva com aeronaves de decolagem e pouso vertical (VTOL), mas que oferecesse mais acessibilidade. Acreditamos que esta poderia ser uma aeronave pessoal operada de qualquer superfície e é uma possibilidade importante para a futura aeronáutica e mobilidade. ”
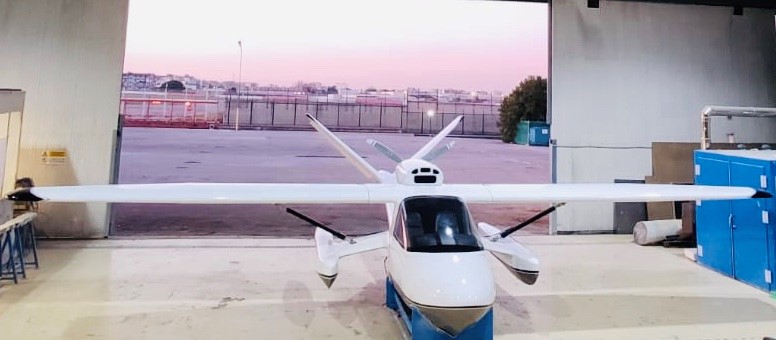
A equipe SEAGULL testou um sistema de propulsão híbrido, construiu um primeiro protótipo na água e começou os testes na água em outubro. “Após a conclusão desse teste, construiremos um protótipo voador dentro de alguns meses”, disse Lecce. “Esta é uma equipe muito experiente, composta por empresas significativas com mais de 50 anos de experiência na aviação geral.”
O protótipo voador SEAGULL contará com fuselagem, cauda e asa compostas. “Mais uma vez, vamos impulsionar a aplicação de fabricação automatizada usando AFP e infusão de resina”, diz Barile. “Um dos principais problemas com os compósitos que usam esses processos é o custo dos materiais. Na verdade, o que estamos tentando fazer é encontrar também uma combinação de material e processo que seja mais democrática em termos de custo ”.
Resina
- Fraunhofer IPT desenvolve compósitos termoplásticos em armazenamento de hidrogênio, pás de motor e muito mais
- Composites Evolution apresenta pré-impregnados de alto desempenho, novas fitas UD termoplásticas
- Projeto para fabricação automatizada de compósitos de aeroestruturas de baixo volume
- Fitas termoplásticas continuam a mostrar potencial para aeroestruturas compostas
- Resinas epóxi reprocessáveis, reparáveis e recicláveis para compósitos
- Karl Mayer lança linha de produção para fitas UD termoplásticas
- SWM lança meio de fluxo Naltex para infusão de resina
- Porta termoplástica a primeira para compósitos automotivos
- Consórcio de compósitos termoplásticos visa produção de alto volume para automotivo e aeroespacial
- Atendendo ao mundo dos compósitos em Israel e nos EUA