Construindo o Museu do Futuro
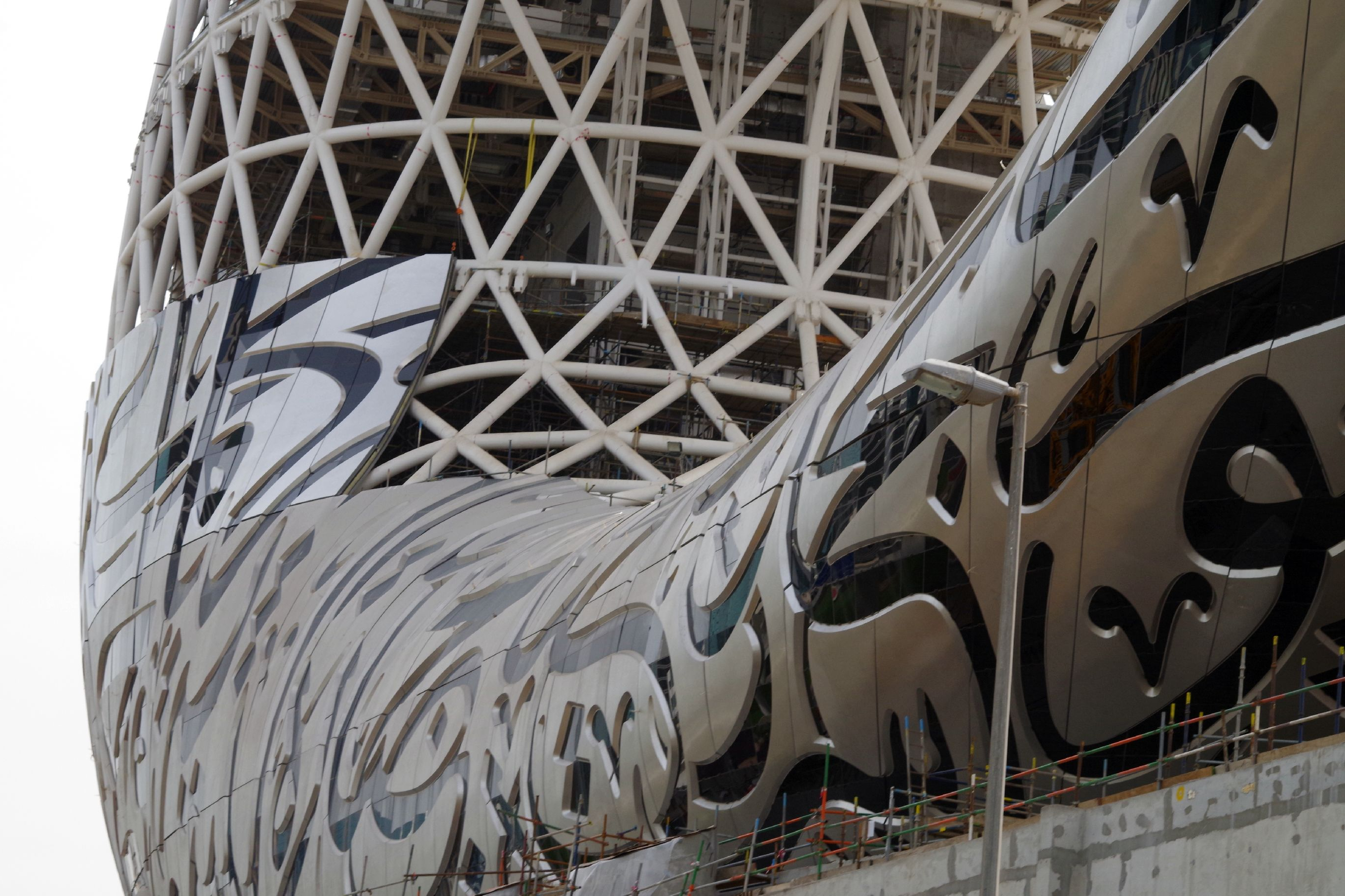
O Museu do Futuro em construção em Dubai, nos Emirados Árabes Unidos (Emirados Árabes Unidos), é uma das estruturas mais complexas já construídas. O prédio de 78 metros de altura abriga sete andares dentro de uma concha em forma de toro que fica no topo de um pódio de três andares. A fachada externa do toro compreende 1.024 painéis compostos retardadores de fogo (FR). Revestido com aço inoxidável, cada painel tem uma forma 3D exclusiva e integra caligrafia árabe moldada. A escrita fluida forma poemas que descrevem a visão para o futuro de Dubai de Sua Alteza Sheikh Mohammed bin Rashid Al Maktoum, vice-presidente e primeiro-ministro dos Emirados Árabes Unidos e governante do Emirado de Dubai. Eles também servem como janelas do edifício, lançando luz do dia através do interior sem colunas e criando um efeito dramático à noite por meio de 14 quilômetros de iluminação LED integrada.
Idealizado pelo Sheikh Mohammed como uma incubadora de inovação e invenção, o Museu do Futuro é considerado um dos edifícios mais avançados do mundo, um lugar onde as pessoas podem experimentar e pesquisar novas tecnologias. É também um símbolo da arquitetura que ultrapassa os limites por meio do design digital e do uso de materiais mais eficientes. O projeto paramétrico foi usado para desenvolver a grade de aço - uma estrutura de 2.400 membros de aço que se cruzam diagonalmente - à qual são fixadas lajes de piso de concreto e 17.000 metros quadrados de revestimento composto, o último usando 1 milhão de metros quadrados de vidro multiaxial e reforçado com fibra de carbono epoxy prepreg.
A Affan Innovative Structures, empresa de Dubai, forneceu o projeto composto para os painéis, bem como a fabricação e o suporte para a instalação. “Esta é a primeira vez que tal projeto foi realizado”, disse o CEO da empresa, Dr. Amer Affan. “E também a primeira vez que painéis compostos foram usados para integrar várias funções de construção por meio de formas tão complexas.”
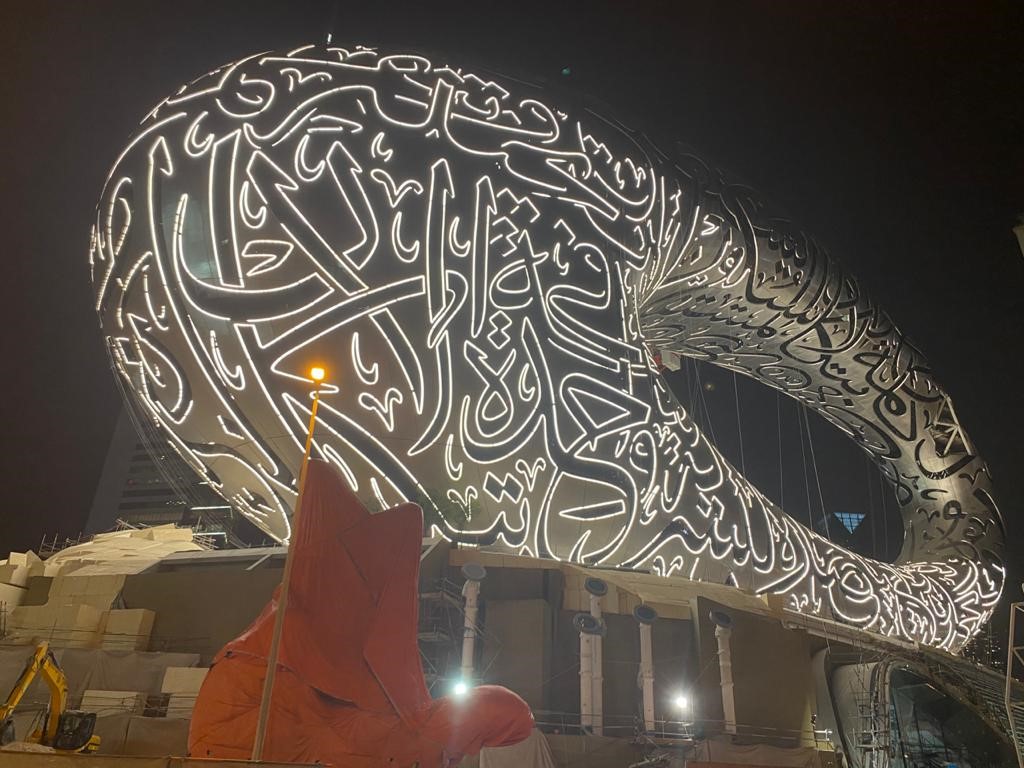
O arquiteto principal Shaun Killa explica que tais exteriores complexos são normalmente telas de chuva, com um edifício atrás que contém o sistema de impermeabilização. “Isso simplifica as coisas porque é um pouco mais tolerante ao criar essas formas tridimensionais”, observa ele. “Neste edifício, porém, o envelope faz a impermeabilização, a estanqueidade, a estrutura e a iluminação.” Affan admite que, para um projeto tão grande, sua empresa é pequena, “mas usamos nossa experiência técnica para alcançar algo único e mostramos como os edifícios serão construídos no futuro”.
Capacidade em designs digitais complexos
Affan Innovative Structures foi inicialmente contatado pela equipe de engenharia do Museu do Futuro. “Não havia muitas empresas que pudessem fazer o trabalho necessário para o revestimento externo”, observa Affan. “O único outro concorrente propôs uma parede de cortina normal com painéis de alumínio ou aço inoxidável do lado de fora.” As paredes de cortina, normalmente usadas em adição a uma estrutura de aço estrutural, são finas e feitas de molduras de alumínio que suportam painéis externos de vidro, metal e / ou pedra fina (consulte “A envolvente do edifício:fachadas unificadas de FRP”). Isso foi rejeitado pela equipe de engenharia como muito difícil e incapaz de fornecer a mesma aparência que seria possível usando uma fachada de painel composto multifuncional integrado. Assim, este último, proposto pela Affan Innovative Structures, foi selecionado para o projeto. “Também temos uma tecnologia exclusiva que nos permite fazer grandes painéis”, acrescenta Affan, “de até 3 metros de largura por 9 metros de altura, curvos em ambas as direções, o que significa menos juntas”.
A Affan Innovative Structures foi especialmente adequada para este projeto. Formada em 2004 pelo Dr. Affan, a empresa oferece soluções completas e prontas para uso - desde o projeto conceitual até a instalação e manutenção predial - gravitando em direção a desafios muito técnicos. O currículo da empresa inclui a complexa tela / revestimento geométrico de alumínio para o Estádio King Abdullah Sports City (Jeddah, Arábia Saudita), a cobertura composta da entrada e 64 claraboias de vidro e aço com padrões intrincados para o Yas Mall (Abu Dhabi, Emirados Árabes Unidos) , o telhado exterior composto do Hospital Sidra (Doha, Qatar) e muitos outros projetos desafiadores. Essa capacidade em conjuntos complexos de aço, vidro e composto seria exatamente o que era necessário para o exterior multifuncional do Museu do Futuro.
“Dentro de cada painel composto, há um sistema de vidro plano [painéis] dentro da escrita árabe”, explica Affan. “O vidro fica quase recuado dentro dos painéis, até 200 milímetros de profundidade.” Este recesso muda não só do topo do edifício, com menos recesso para evitar o aprisionamento de água, para o fundo, onde os painéis verticais e inferiores podem ser profundamente recuados sem reter água, mas também dentro de cada painel, inclinado e diminuindo para produzir uma vantagem para o script. “A localização e as bordas do recesso também variaram de acordo com a localização do vidro dentro do painel, porque o vidro era plano, mas os painéis eram curvos”, observa Affan. “Isso só foi possível com design digital e usinagem CNC.” Essa precisão também seria necessária para garantir que o script, que variava de um painel para o outro, fosse alinhado precisamente à medida que os painéis eram instalados, para que as letras e palavras fluíssem corretamente pelo exterior do edifício.
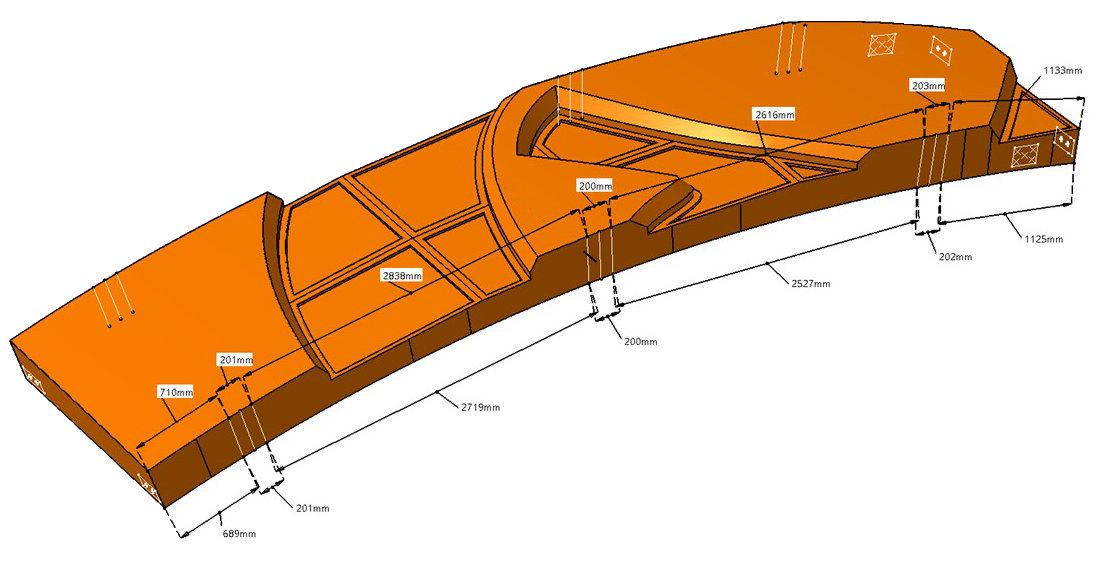
Para Affan, a única solução era moldar a escrita árabe e os recessos em cada painel composto. “Os reforços seriam colocados em moldes precisamente usinados em CNC”, explica ele. Felizmente, o software CATIA (Dassault Systèmes, Vélizy-Villacoublay, França) que a Affan Innovative Solutions usa para acionar suas máquinas CNC também é o programa CAD 3D usado pela indústria aeroespacial para projetar aeronaves complexas e estruturas compostas. Além disso, a equipe de Affan de 28 engenheiros também é proficiente no software Tekla BIM, Rhino 3D (Robert McNeel &Assoc., Seattle, Wash., EUA) e AutoCAD da Autodesk. “Fizemos todos os desenhos no CATIA, bem como o projeto do laminado, o que nos deu a capacidade de fazer uma usinagem tão complexa”, diz Affan.
O projeto, no entanto, não era trivial e precisava atender a uma variedade de cargas estruturais e de vento. Por exemplo, o interior do toro criou um efeito de túnel de vento, explica Affan. Esses painéis devem suportar até 450 kg / m 2 (92 lb / pés 2 ) da carga do vento. (Observe que o Código Internacional de Construção lista cargas de vento de 71 lb / ft 2 para áreas de furacão de alto risco em West Palm Beach, Flórida, EUA). Os painéis compostos para o Museu do Futuro também são ajustados para minimizar o peso. “Os painéis usam de 9 a 13 camadas, que variam conforme a localização e o carregamento”, diz Affan. Ele acrescenta que o Composite Technology Center (Stade, Alemanha), uma subsidiária da Airbus e um parceiro de longa data através da organização comercial CFK Valley ev (Stade, Alemanha), “forneceu uma verificação de terceiros sobre nosso design de laminado, deflexão e rigidez cálculos. ”
Uma complexidade adicional e inovação é que os painéis também integraram seu próprio sistema de fixação. “Nas bordas, 24 camadas formam a geometria de fixação semelhante a um cassete para se conectar ao prédio”, explica Affan. Um sistema de cassete é um método para anexar revestimento externo, originalmente desenvolvido para instalações do tipo tela de chuva. Embora os tipos e geometrias variem, os cassetes normalmente permitem uma superfície externa plana e à prova de chuva que é fixada atrás da estrutura de suporte de carga do edifício. Para os painéis de fachada do Museu do Futuro, peças separadas não eram necessárias para formar as bordas do cassete, mas, em vez disso, eram usinadas em cada molde e, portanto, integradas em cada painel composto.
Materiais, moldes e fabricação de painéis
Embora os 10.000 metros quadrados de espaço de fabricação de compostos da Affan Innovative Structures tenham 16 máquinas de infusão de resina e oito mesas de infusão de resina de aço com tampo de vidro medindo 3 metros por 20 metros, ela optou por usar prepreg. Por quê? “Alcançar o desempenho FR necessário requer muitos aditivos, então a resina se torna espessa e não flui na infusão”, explica Affan. Nesse caso, o aditivo era tri-hidrato de alumínio (ATH, consulte “Resistir ao fogo sem o peso”). Ele continua:“Assim, trabalhamos com a Notus Composites [Ras Al Khaimah, Emirados Árabes Unidos] para desenvolver um pré-impregnado de epóxi FR. Usamos principalmente fibra de vidro, mas também fibra de carbono em certas seções onde havia problemas de deflexão ”. Aprovado pela Defesa Civil de Dubai, Notus Composites EPFR-609 prepreg, em combinação com o filme de superfície NE11-FR, foi aprovado nos requisitos de incêndio NFPA 285, EN13051-1 e ASTM E1098 e E84 Classe A (consulte “Prepregs retardantes de fogo habilitados .. . ”E“ Triagem melhor e mais barata de materiais de construção de FRP ”).
Como as superfícies de metal externas em Dubai podem atingir temperaturas de 80 ° C (176 ° F) no verão, Affan explica, “curamos o pré-impregnado a 120 ° C para garantir T g suficiente (temperatura de transição vítrea) para resistir à deflexão da cabeça. Assim, os moldes foram usinados em espuma de poliuretano, que suportava aquela alta temperatura, que é mais cara. Tentamos três ou quatro espumas diferentes, mas apenas uma podia suportar a temperatura mais a pressão do vácuo e, ainda assim, era suficientemente suave para ser usinada em CNC de maneira fácil e rápida.
A usinagem CNC de cada molde levou de 12 a 72 horas e cada um dos 1.024 painéis compostos exigiu seu próprio molde . Todas as quatro máquinas CNC de 5 eixos CMS da Affan Innovative Structures (Zogno, Itália) - a maior medindo 33 metros de comprimento por 13 metros de altura por 2,5 metros de altura - eram necessárias para atender à exigente taxa de produção do museu. “Se uma [máquina] estava parada para manutenção, tínhamos as outras funcionando em paralelo”, explica Affan.
As camadas pré-impregnadas foram cortadas e equipadas usando um (Bulmer , Mehrstetten, Alemanha) cortador automatizado. “Não usamos núcleo nos painéis porque, ao contrário de hoje, não havia núcleos de espuma na época que pudessem atender aos requisitos de FR”, diz Affan. Mesmo com essa automação, a força de trabalho da empresa de 250 funcionários, um total que havia alcançado em 2015, também foi necessária para entregar a produção, em média quatro painéis por dia. Equipes de seis trabalhadores, cada um com um supervisor e um conjunto equilibrado de habilidades para serem eficientes, montaram os painéis. “Normalmente, teríamos duas ou três equipes trabalhando em um projeto”, observa Affan, “mas para cumprir esse cronograma de produção, tínhamos 20 equipes trabalhando a qualquer momento”.
Etapas de fabricação
-
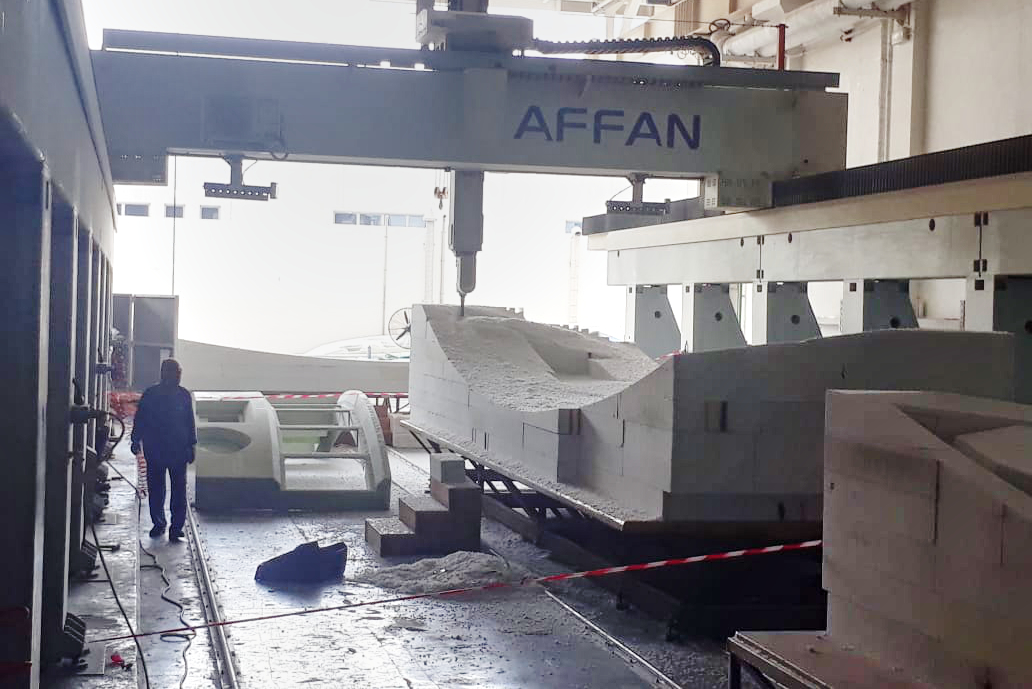
Etapa 1Espuma de poliuretano é fresada em moldes de precisão. Fonte para todas as imagens da etapa de fabricação | Affan Innovative Solutions
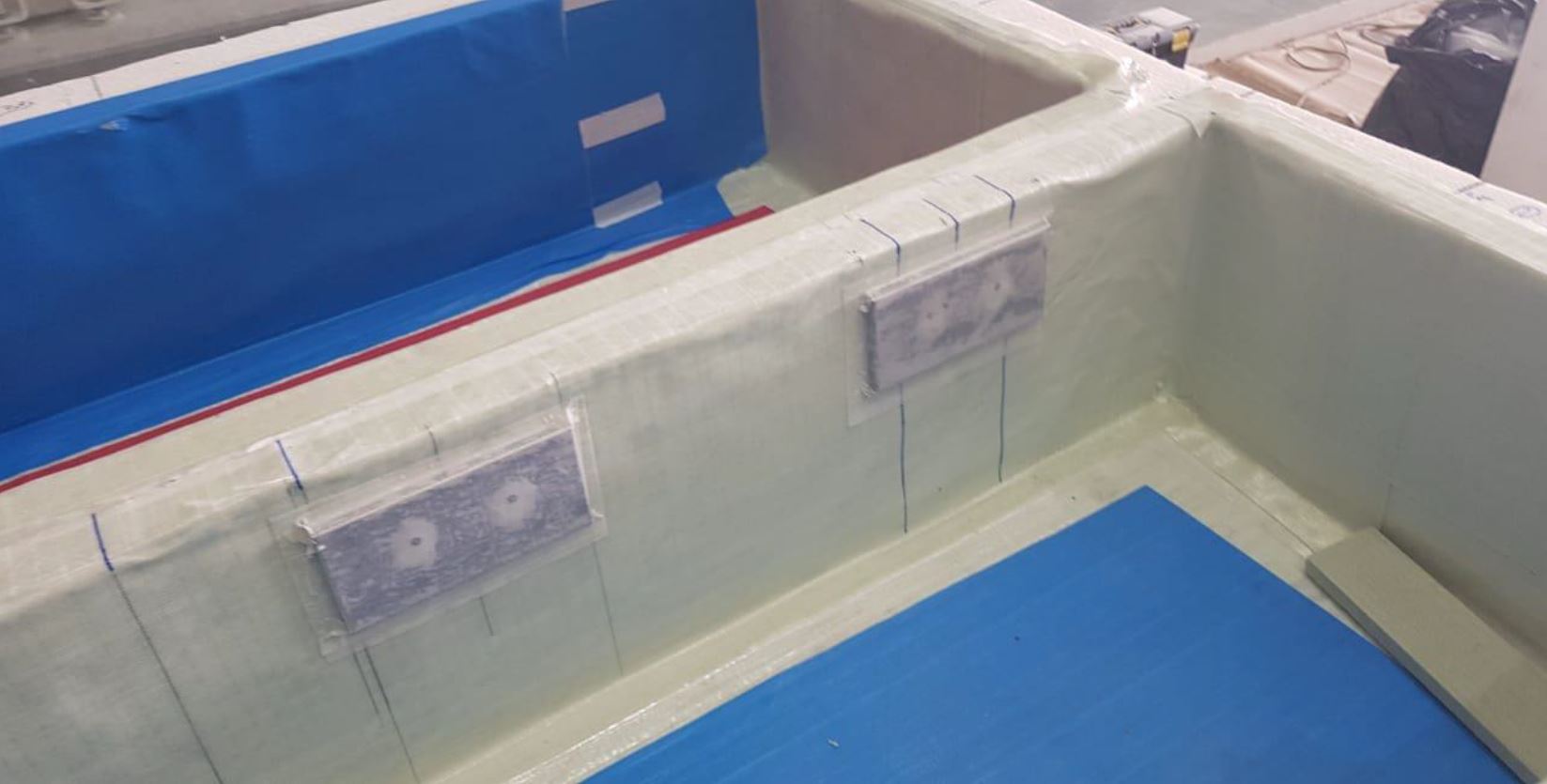
Etapa 2 A fibra de vidro / pré-impregnado de epóxi é colocada à mão nos moldes.
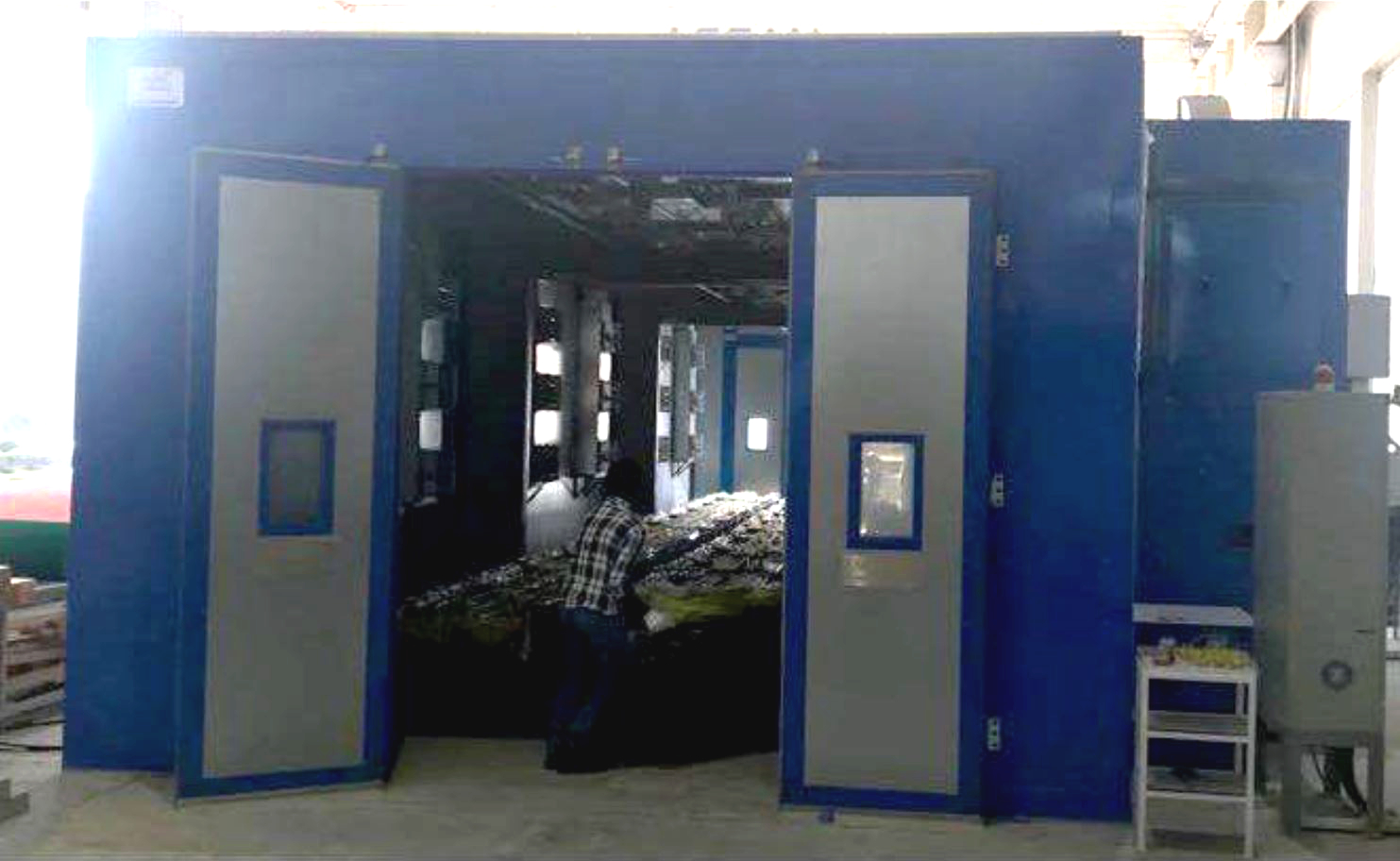
Passo 3 Layups pré-preparados são ensacados a vácuo e curados em um forno por 6 horas a 120 ° C.
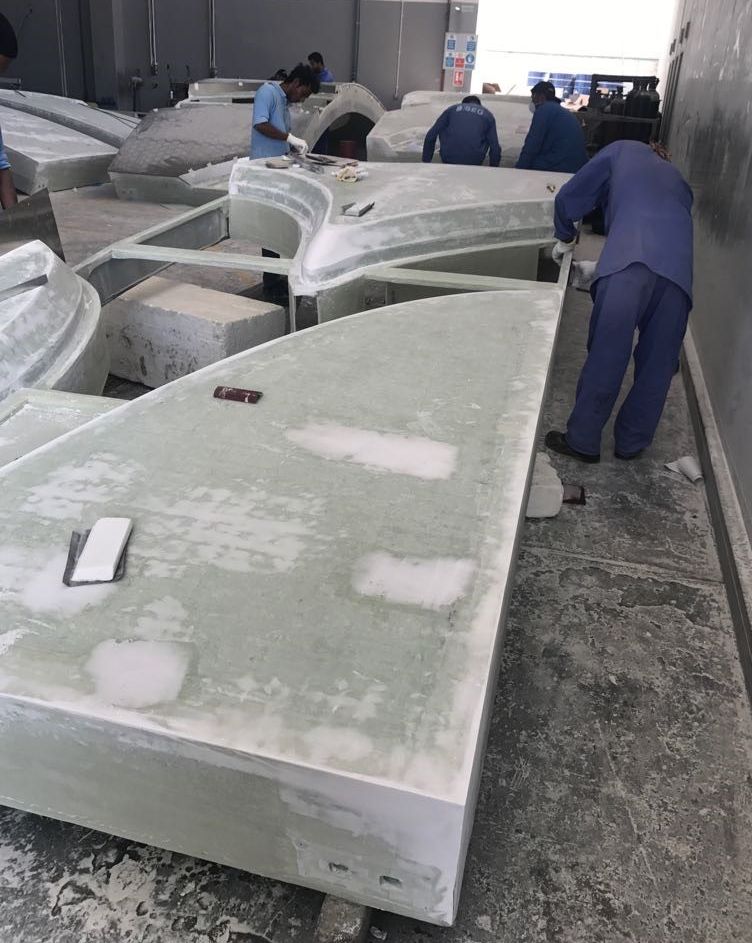
Etapa 4 Os painéis desmoldados são preparados para colagem com acabamento em aço inoxidável.
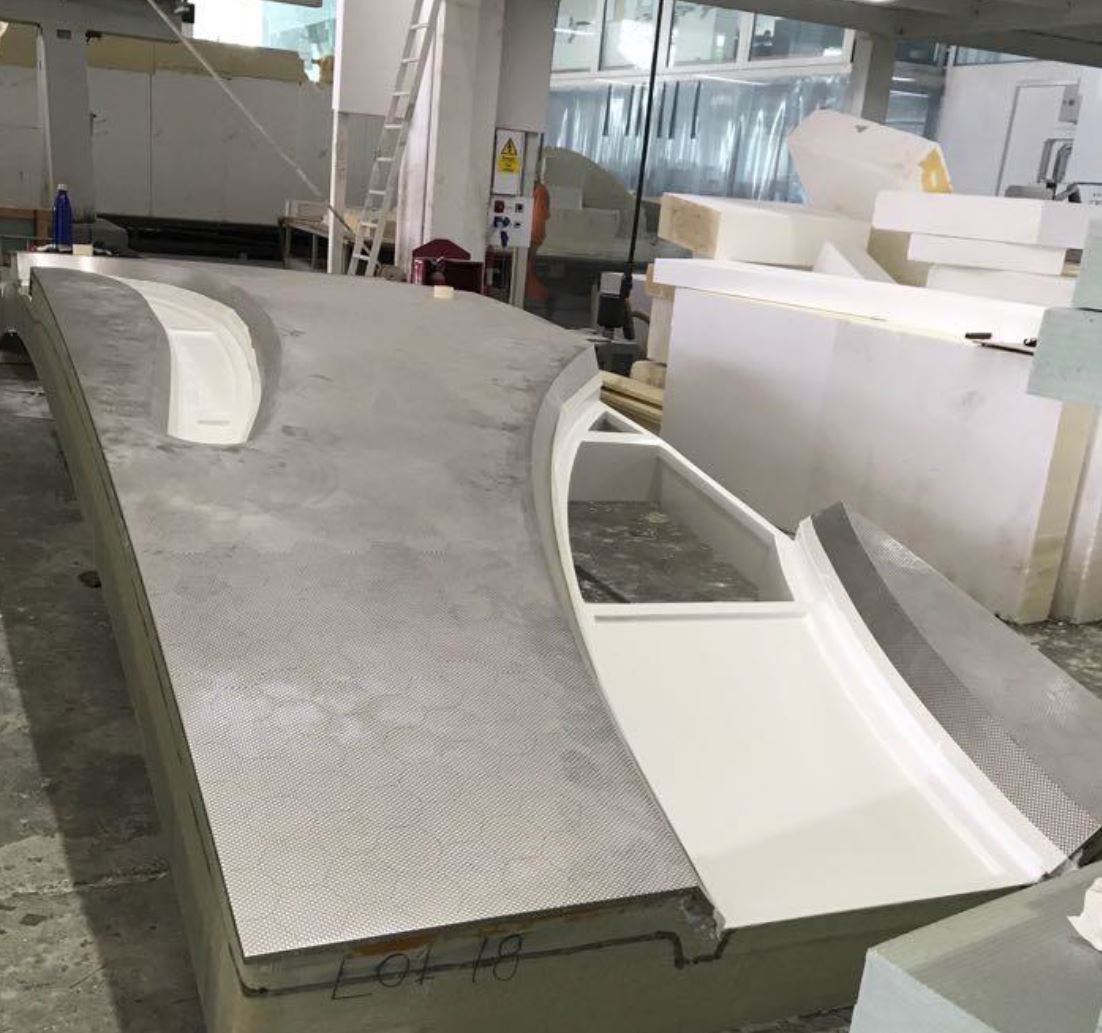
Etapa 5 Os hexágonos de aço inoxidável são ligados e fixados mecanicamente aos painéis de FRP.
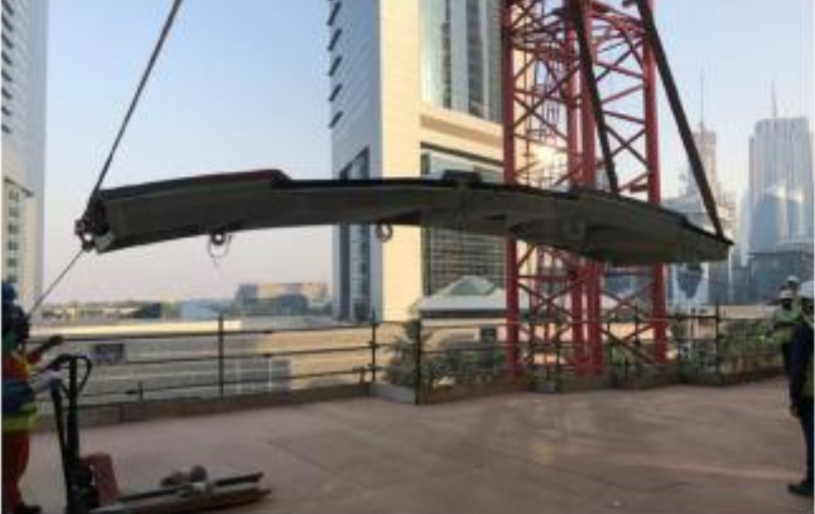
Etapa 6 Os painéis acabados são elevados para a instalação.
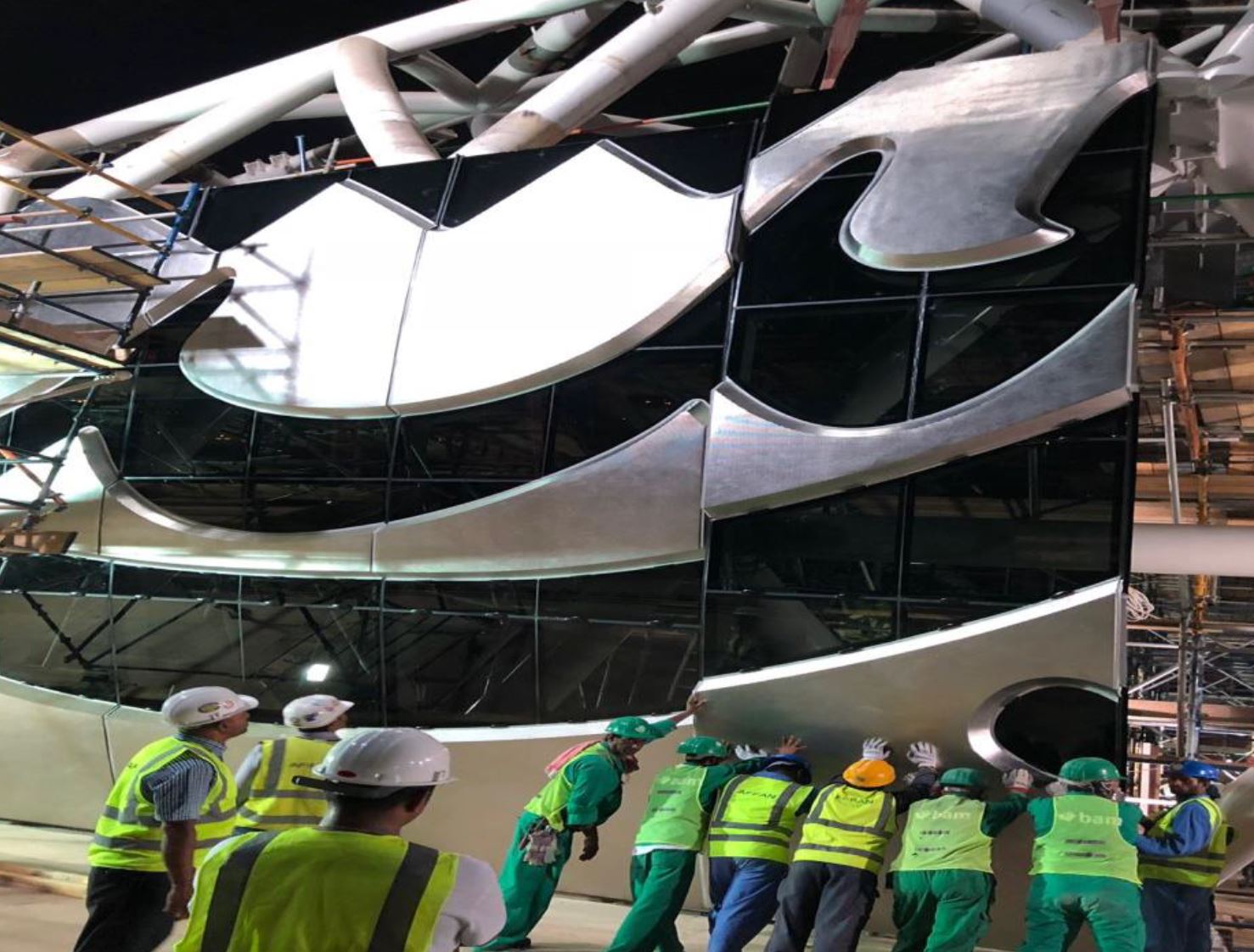
Etapa 7Cada painel é ajustado por meio de uma “junta universal” 3D exclusiva.
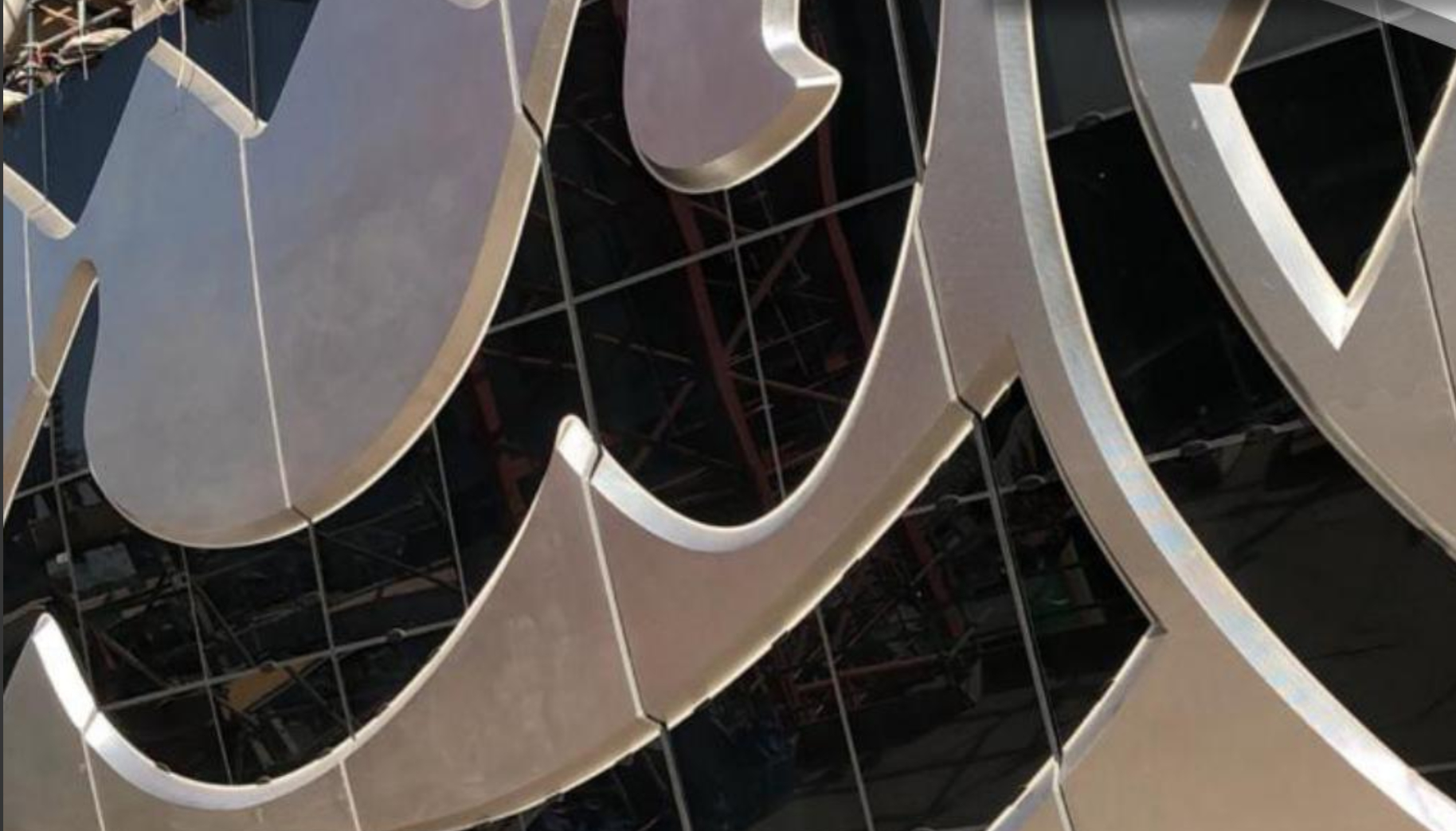
Etapa 8 Cada painel é ajustado por meio de uma “junta universal” 3D exclusiva para obter uma fachada externa alinhada suavemente.
Anterior Próximo
Layups eram colocados à mão, ensacados a vácuo e curados por 6 horas em fornos que mediam 20 metros de comprimento por 8 metros de largura por 3 metros de altura. “Cada máquina CNC tinha seu próprio forno”, diz Affan. “Não agrupamos muitos painéis por ciclo de cura. Em vez disso, quando cada painel estava pronto, nós imediatamente os curamos para manter o fluxo de produção o mais alto possível. Em seguida, desmoldamos os painéis e usamos um scanner 3D para garantir que o painel original corresponda ao arquivo CATIA. De acordo com nosso sistema de controle de qualidade total, tivemos que verificar os arquivos digitais em cada etapa do processo ”.
Os painéis acabados receberam o acabamento externo de aço inoxidável. “O aço inoxidável é colado com adesivo em cada painel e, em seguida, fixado com fixadores mecânicos, o que é uma arte por si só”, diz Affan. “O metal foi cortado em pequenos hexágonos para cobrir os painéis 3D. A grade hexagonal variava parte a parte dependendo da quantidade de curvatura. Embora tenhamos experiência e confiança na ligação, não poderia haver o risco de um único hexágono se desfazer durante a vida útil do edifício. Assim, cada hexágono teve que ser anexado - exigindo de 200 a 300 acessórios para um único painel. ” Os painéis acabados foram então enviados ao local para serem instalados.
Instalação sem problemas auxiliada pela NASA
A instalação foi concluída pela empresa de construção do edifício BAM International (Gouda, Holanda). “Fornecemos supervisores para a instalação apenas para ajudar no manuseio dos painéis”, observa Affan. “A forma como cada um é levantado é a chave. Os painéis foram projetados para serem fortes o suficiente para a posição específica de cada um no edifício. No entanto, eles devem ser içados de uma maneira específica, por meio de pelo menos dois pontos de içamento, assim como pendurar cassetes em métodos de construção mais tradicionais. ”
Havia um problema adicional que Affan era exclusivamente qualificado para resolver. “Para que cada painel assente na estrutura de aço e, ao mesmo tempo, forme uma superfície lisa, precisávamos da capacidade de ajustar o painel em profundidade, orientação e curvatura em 3D - em outras palavras, uma espécie de junta universal com três graus de liberdade . Em 1985, trabalhei como estudante na NASA na Califórnia em amortecimento de estruturas de estações espaciais. A chave era ser capaz de mover cada estrutura e ajustá-la quando o ônibus espacial atracasse, de modo que a vibração fosse amortecida rapidamente, um pouco como o cancelamento de ruído. Usei a mesma tecnologia para fixação e ajuste do painel durante a instalação. ”
Além disso, como os painéis também forneciam a vedação estanque do edifício, não poderia haver espaços entre eles. “Os painéis não podiam encostar diretamente ou podiam rachar”, disse Affan, explicando que, devido a uma alta carga viva de 1,5 toneladas no 6 th em balanço área de exposição no chão, a estrutura de aço realmente se move. “Mantivemos uma lacuna com espaçamento preciso entre os painéis e isso foi preenchido com uma gaxeta especial.” Esta junta, macia o suficiente para expandir, mas rígida o suficiente para suportar cargas, fornecia funcionalidade de vedação enquanto possibilitava a aparência estética do edifício.
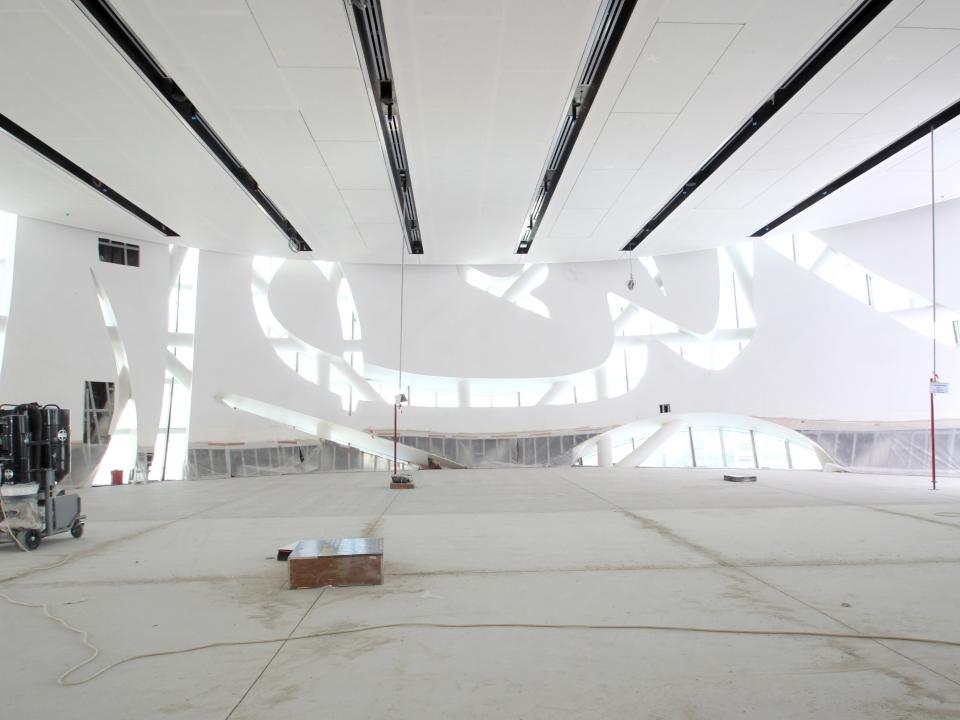
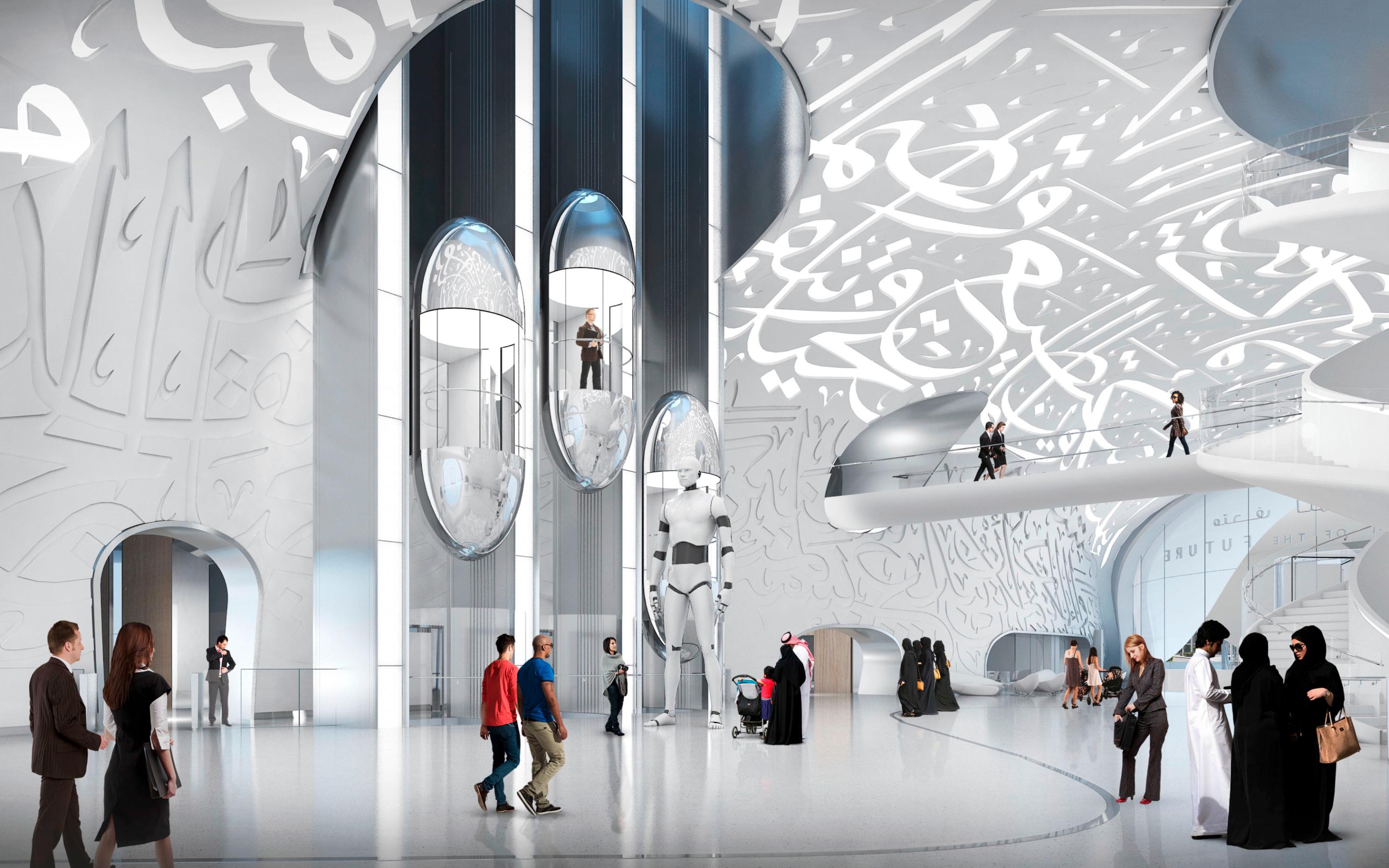
Essas soluções são uma vantagem, observa Affan. “Porque viemos de um background de estruturas, somos capazes de combinar muitos materiais. Isto é muito importante. Os compósitos são apenas um dos materiais que usamos. Este não foi apenas um projeto composto. ” Os resultados falam por si. “A instalação correu bem; não houve nenhum problema ”, diz Affan, que observa que não havia maneira de verificar se o painel caberia, exceto para garantir sua conformidade com o arquivo digital. “Ainda não tínhamos um painel que não se encaixasse ou tivesse o formato errado ou a palavra escrita incorretamente”, testemunhou Bauly, gerente de projeto de Buro Happold, em um artigo da BBC por Elizabeth Bains.
Futura construção modular
“Gerenciamos todo o processo juntos”, acrescenta Affan. “O trabalho em equipe dentro da própria empresa também foi fundamental; os grupos de design e layup precisavam coordenar-se uns com os outros. Nunca fizemos um trabalho tão grande como este e foi um desafio, mas gostamos de desafios. ”
Infelizmente, o COVID-19 tem cobrado seu preço. “Concluímos este trabalho pouco antes do bloqueio da pandemia”, diz ele. “Agora, estamos reduzidos a menos de 30 pessoas. É devastador. Mas isso afetou a todos, não apenas a nós. ” E, no entanto, Affan vê esperança para o futuro e para o papel que os compósitos desempenharão para alcançar a sustentabilidade e a inovação de que o mundo precisa na construção. “Principalmente em Dubai e no GCC (Conselho de Cooperação do Golfo), as pessoas querem experimentar novas ideias. Está demonstrando o futuro da arquitetura e construção. ”
Esse futuro, enfatiza, será para quem pode usar sistemas modulares de construção, “e o COVID-19 está na verdade acelerando isso. As empresas construirão módulos e os enviarão ao site. Isso se desenvolverá porque ele move as ineficiências para fora do local e para uma fábrica, aumentando o controle e a qualidade. No local, você deve coordenar todas as pessoas. É uma perda de tempo, esperando por outros subcontratados. Você também depende do clima e das paralisações do trabalho. A fabricação em uma fábrica elimina tudo isso. Por serem fortes, leves e duráveis o suficiente para transportar e instalar facilmente, os compostos permitem esse tipo de construção modular e você pode fazer qualquer formato que desejar. ”
Affan observa que a construção modular tem sido usada em navios de cruzeiro há anos, onde cada cabine é pré-fabricada, completa com aquecimento / ar condicionado, sistemas elétricos e de encanamento e, em seguida, montada na estrutura de aço do navio como blocos de LEGO. “Imagine quanto tempo você vai economizar quando cada módulo já estiver equipado. Estamos diante de um projeto de construção de um arranha-céu dessa forma com materiais compósitos ”, afirma. “Se você tem resinas FR, não precisa das peças que antes eram de metal.” Citando um hotel Marriott construído dessa forma e concluído no ano passado na cidade de Nova York, Affan acrescenta:“aquele edifício era de aço e madeira, mas podemos construí-lo em materiais compostos”.
Resina
- A segurança na nuvem é o futuro da cibersegurança
- O futuro do software de fatiamento
- Computação de borda:A arquitetura do futuro
- Visualizando o futuro da manutenção da planta
- O futuro dos data centers
- Construindo melhores cadeias de suprimentos para o futuro
- Automação inteligente de edifícios e o futuro do desenvolvimento imobiliário nas cidades
- Construindo o futuro da experiência do funcionário com automação inteligente
- Como a Tech Mahindra está construindo a fábrica do futuro
- O futuro da impressão 3D na fabricação