Reinicialização da parede traseira:One-stop, reboque para a fita para a parte CFRP
No início do atual avanço dos compósitos de fibra de carbono em aplicações automotivas, o fabricante BMW Group (Munique, Alemanha) parecia se destacar. Trabalho inicial para acelerar a moldagem por transferência de resina (RTM) para a produção de seu M o teto do modelo esportivo levou ao estabelecimento de uma cadeia de suprimentos completa para peças de plástico reforçado com fibra de carbono (CFRP) em seu i3 e i8 veículos e, em seguida, para células de trabalho de fabricação e montagem totalmente novas para a carroceria multimaterial Carbon Core em branco (BIW) em sua Série 7 .
BMW se comprometeu com o i3 em 2009 com grande alarde, mas naquele mesmo ano, Audi AG (Ingolstadt, Alemanha) estabeleceu um centro técnico dedicado a plásticos reforçados com fibra. Em 2011, a Audi anunciou uma parceria com a Voith Composites (Garching, Alemanha) para desenvolver e produzir peças CFRP em alto volume. No ano seguinte, divulgou o desenvolvimento de um pilar B de aço reforçado com CFRP, feito por meio de moldagem por transferência de resina (RTM), e sua parceria com a SOGEFI (Guyancourt, França) para a comercialização de molas suspensas em bobina composta. Em 2012, a Audi também atuou como parceira fundadora do cluster de ponta MAI Carbon, que incluía BMW, Voith Composites, SGL Group (Wiesbaden, Alemanha) e outros.
Mais notavelmente, a própria narrativa da Audi sobre o desenvolvimento do CFRP começa com sua primeira geração R8 carro esporte, lançado em 2006. Apresentava tampas de compartimento para a capota conversível e lâminas laterais feitas por moldagem por transferência de resina (RTM). A empresa progrediu de exteriores estéticos e estruturas menores para o Sistema Modular de Carros Esportivos (MSS) no Audi R8 e-tron . Embora a estrutura principal desse supercarro elétrico fosse composta por vigas de alumínio extrudado unidas por fundidos de alumínio, todos os painéis e preenchimentos eram de CFRP, incluindo uma inserção de porta-malas com estruturas de colisão corrugadas que permitiam ao módulo traseiro absorver cinco vezes mais energia do que a estrutura de metal .
A espinha dorsal do MSS é sua parede posterior , que evoluiu de um conceito inicial em 2011 para o módulo que atualmente é produzido para o R8 não elétrico pela SGL Technologies (anteriormente BENTELER-SGL, Ort im Innkreis, Áustria; consulte “Tour pela fábrica:BENTELER SGL”). Mas a Audi já estava planejando sua próxima etapa:iterar a parede traseira para uso em seu A8 de maior volume sedan de luxo, com a Voith Composites como parceira de fabricação.
Voith Composites é uma subsidiária de 10 anos da multinacional Voith GmbH &Co. KGaA, fundada em 1867. A empresa controladora agora emprega 19.000 funcionários, tem receitas anuais de € 4,2 bilhões (US $ 5,2 bilhões) e fornece equipamentos de manufatura e tecnologias por meio quatro divisões:Voith Digital Solutions, Voith Hydro, Voith Paper e Voith Turbo. A Voith Composites evoluiu da produção de rolos CFRP usados na fabricação de papel para a fabricação de eixos cardans / cardans automotivos e industriais e laminados planos.
Em 2011, a Voith Composites começou a trabalhar em uma cadeia de processo CFRP altamente automatizada, com o objetivo de produzir o A8 parede traseira. Em seu núcleo estava o Voith Roving Applicator (VRA), que, em uma única linha, espalha a estopa de fibra de carbono de 35K de Zoltek (St. Louis, MO, EUA) em fita unidirecional (UD) ligada, que é então cortada e empilhada para formar um espaço em branco personalizado. O VRA foi reconhecido com o Prêmio JEC de Inovação em 2017. Ele também estabeleceu uma base robusta para as operações subsequentes de pré-moldagem e moldagem. Os principais prêmios da categoria de automóveis foram conquistados novamente para a Voith Composites e Audi no JEC World 2018 pela linha de produção digital 4.0 baseada em VRA, usada para fabricar o Audi A8 módulo de parede traseira. Trabalhando com o fornecedor de resina Dow Automotive (Auburn Hills, MI, EUA) e Zoltek, esses parceiros não apenas desenvolveram os materiais, processos e sistemas integrados de inspeção em linha necessários para fabricar peças CFRP de alto desempenho em taxas de alto volume, mas também criaram o produto completo conjunto de ferramentas essenciais de design / manufatura auxiliadas por computador (CAD / CAM) e de simulação que já estão sendo aplicadas para desenvolver peças futuras.
Evolução do design orientado para a eficiência
“Começamos a trabalhar com a Audi desde o início”, disse o Dr. Jaromir Ufer, chefe de desenvolvimento de negócios da Voith Composites. A primeira prioridade era desenvolver o novo A8 projeto da parede traseira, que direcionaria como a peça deve ser fabricada.
“Quando iniciamos a engenharia para esta produção, não podíamos encontrar produtos de prateleira [software] que tivessem tudo o que precisávamos”, explica Ufer. “Então, reunimos ferramentas de design como ABAQUS, mas construímos nossos próprios cartões de material e desenvolvemos nossos próprios métodos de simulação.” A Audi já havia identificado o peso reduzido do BIW e o aumento da rigidez torcional como objetivos principais para o R8 design da parede traseira (consulte “Parede do assento do Audi R8:um prelúdio para a produção”). Para o A8 módulo, um design integral foi desenvolvido para reduzir o MSS de múltiplos componentes montagem em um único painel CFRP em forma com um pequeno número de acessórios unidos e rebitados. Este projeto levou ao desenvolvimento de um laminado altamente anisotrópico com caminhos de carga localizados, o que permite que a peça acabada forneça 33% da rigidez torcional da célula de transmissão a 50% do peso em comparação com um conjunto de três a cinco peças de alumínio soldadas.
“A pré-forma composta para o Audi A8 o painel da parede traseira varia de uma base de 6 até 19 telas onde é adicionado reforço local - por exemplo, onde há recortes ou pontos de carga, como os acessórios de retenção do carrinho de criança ”, explica Ufer (Fig 2).
Aplicador móvel Voith
Ufer observa que o desenvolvimento deste projeto e o VRA ocorreram em conjunto. “Só por ter a liberdade de design que o VRA oferece foi o desempenho do novo A8 parede traseira possível. ” Também foi importante o fato de o fornecedor de fibra Zoltek ter se comprometido com o preço do programa por 7 anos.
O processo do VRA começa com uma gaiola de fibra de carbono PX 35 da Zoltek. Várias bobinas de reboque de 50K são alimentadas em cada linha VRA e espalhadas para produzir fitas de 50 mm de largura. Em seguida, é aplicado um aglutinante à base de epóxi que posteriormente reagirá com a resina de matriz epóxi de cura instantânea Dow VORAFORCE durante a moldagem por transferência de resina (RTM) da peça composta. Uma pequena quantidade de calor infravermelho (IV) é aplicada para derreter o aglutinante o suficiente para manter a fita unida por meio das etapas subsequentes de consolidação, corte e empilhamento (Etapa 1).
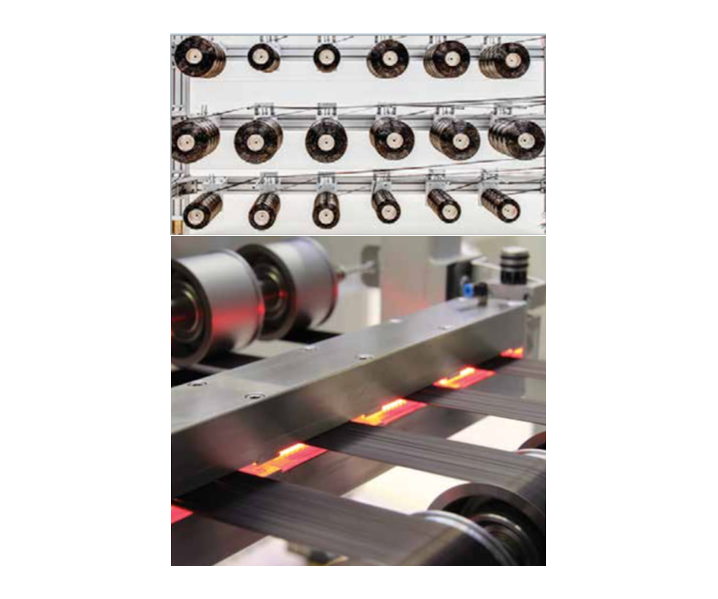
Etapa 1: A estopa de fibra de carbono Zoltek 50K é alimentada no Voith Roving Applicator (VRA), onde é primeiro espalhada, então revestida com aglutinante à base de epóxi e posteriormente aquecida por infravermelho para derreter parcialmente o aglutinante.
“Este é um processo contínuo totalmente automatizado”, afirma Ufer. “Se por algum motivo for necessário parar a linha, o equipamento reage automaticamente. Por exemplo, o aquecedor infravermelho é imediatamente desligado e retraído para evitar danos ao superaquecimento da fita. Existem centenas desses detalhes no equipamento e no controle digital possibilitando essa tecnologia ”.
Etapa 2: A fita de reboque é então consolidada à medida que avança através de vários rolos sob tensão.
Após a aplicação do aglutinante, a consolidação da fita é obtida à medida que ela passa por vários rolos sob tensão (Etapa 2). Ufer explica que isso também cria um buffer para a linha. “Temos uma unidade que interrompe o fluxo de tração contínua da fibra, proporcionando uma transição para o formato de pulso do mecanismo de corte e colocação da fita.” Este mecanismo baseado em gantry corta as fitas em comprimentos personalizados e as coloca em ângulos específicos de 0-360 ° em uma mesa rotativa (Etapa 3). Cada pilha personalizada, compreendendo 6 a 19 camadas de fita, varia em espessura de 1,5 a 3,7 mm, respectivamente.
Etapa 3: O VRA então corta a fita e coloca até quatro peças por vez em uma mesa rotativa, adaptando o comprimento da fita e o ângulo de orientação dentro da pilha de laminado (por exemplo, 45 ° / 90 ° / 30 °).
A Voith instalou quatro linhas VRA (veja a foto de abertura) e, embora cada uma aplique até quatro fitas de 50 mm de largura por vez, Ufer destaca que “as linhas têm uma abordagem modular, então eles podem aplicar 10 ou mais fitas por vez Tempo. Depende do tamanho da peça e da taxa de produção. ”
A automação inclui inspeção de qualidade. As varreduras das fitas e pré-formas são comparadas com um algoritmo de rejeição. “O escaneamento 100% da fita do VRA garante a distribuição correta da fibra para toda a linha de produção”, explica Ufer. “Também usamos termografia e sensores a laser para verificar as pré-formas em áreas designadas.” O VRA pode então reagir a qualquer problema que detectar. “Se uma fita não estiver correta”, ressalta ele, “o VRA cortará o comprimento deficiente e produzirá outra para substituí-lo”. Um código QR é colocado na pré-forma acabada para rastreabilidade. (Os códigos QR são preferidos às etiquetas de identificação por radiofrequência (RFID) porque supostamente suportam melhor o processo de injeção de resina.)
Formação, moldagem e montagem
A pilha 2D sai do VRA e é transportada para a seção de formação, moldagem e montagem da linha de produção. A primeira prensa na qual é colocada, fornecida pelo especialista em automação de compósitos FILL (Gurten, Áustria), usa calor e pressão para moldar a pilha de fitas 2D em uma pré-forma 3D (Etapa 4). Ufer explica que, porque a pré-forma varia em espessura e forma, a prensa pode adaptar a pressão aplicada à medida que forma regiões separadas da pré-forma presa na ferramenta de conformação. A ALPEX Technologies (Mils bei Hall, Áustria) fez os moldes RTM de aço combinado, com base em um projeto fornecido pela Voith Composites. “Desenvolvemos as ferramentas e o processo de prensagem virtualmente”, diz Ufer. “Embora nenhum loop de teste real tenha sido necessário, validamos e verificamos os modelos de simulação em outras formas e peças antes de usinar o A8 ferramentas de produção da parede traseira. Esta simulação do processo de moldagem correu direto para a produção real e ajudou a acelerar a otimização. ”
Etapa 4 :A pilha de fitas é enviada para uma prensa, onde é formada na forma final da peça 3D.
A prensa mantém por alguns segundos para reagir ao aglutinante em pó e definir o formato, resultando em uma pré-forma estável que pode resistir à lavagem da fibra durante a injeção de resina. “As partículas aglutinantes também funcionam para manter as fibras separadas para um melhor fluxo de resina durante o RTM”, observa Ufer. “Isso é útil porque não há costura na pré-forma para ajudar no fluxo da resina, então essas partículas de ligante atuam como canais de micro fluxo”.
A pré-forma moldada é a seguir transferida por robô para uma célula CNC da EiMa Maschinenbau GmbH (Frickenhausen, Alemanha), onde uma faca ultrassônica apara o contorno final externo. Em seguida, é colocado roboticamente em uma prensa RTM (Etapa 5) fornecida pela ENGEL (Schwertberg, Áustria). Todos os robôs da linha são fornecidos pela KUKA Robotics (Augsburg, Alemanha).
Etapa 5: A pré-forma moldada é colocada em uma prensa de 350 kN e moldada, usando ultra-RTM.
O processo RTM usado para moldar o A8 a parede traseira é a mesma desenvolvida no Audi Lightweight Center para o R8 anterior parede traseira, conhecida como ultra-RTM. Permite a moldagem de peças grandes com injeção rápida, mas com baixa pressão. Em comparação com os 140 bar típicos do HP-RTM, a pressão de injeção de resina no molde durante o ultra-RTM do Audi A8 parede traseira é <15 bar, ainda menos do que para o R8 . Como resultado, em vez de 2.500 kN de força de prensagem, apenas 350 kN são necessários. Portanto, uma impressora menor e mais barata pode ser usada para produzir peças de alta qualidade e alto volume de fibra.
A resina epóxi VORAFORCE 5300, um sistema de três componentes que inclui desmoldante, cura em 90-120 segundos a 120 ° C e tem uma viscosidade de processamento de 20 cps. Para o A8 parede traseira, uma injeção de resina de 1,3 kg é injetada na pré-forma, seguida por uma cura de 120 segundos.
A peça curada é desmoldada roboticamente e carregada em uma célula de fresamento CNC fechada para usinagem de recortes. Em seguida, a peça fresada é colocada em uma máquina de lavar automática para limpar a poeira residual de CFRP.
A parede posterior lavada é transferida para uma célula de montagem equipada com dois robôs. O primeiro robô coloca a peça moldada em uma máquina de rebitagem automatizada, que documenta a força aplicada durante a instalação do rebite. Isso faz parte da inteligência de fabricação incorporada ao processo geral e é adicionado ao registro de processamento digital de cada parte (ou seja, linha digital). A peça é então movida para a área de colagem e um segundo robô prepara as áreas para a colagem, usando uma limpeza automática com solvente. O mesmo robô aplica então o adesivo estrutural de poliuretano de dois componentes Dow BETAFORCE 9050M de cura rápida (Etapa 6), que é compatível com o epóxi de três partes. A seguir, a peça é colocada em um forno para um curto ciclo de cura do adesivo.
Etapa 6: O adesivo de poliuretano BETAFORCE é aplicado roboticamente para anexos colados e, em seguida, curado em um curto ciclo de forno.
Esta linha de produção mantém um tempo de ciclo de 5 minutos para a peça concluída e a demanda atual por peças pode ser atendida em um ou dois turnos de 8 horas. Um dispositivo de digitalização a laser 3D é usado periodicamente para verificar a forma 3D da peça e as medições. As peças acabadas são então preparadas para envio ao Audi A8 linha de montagem final em Neckersalm, Alemanha, a cerca de 3 horas de distância por estrada (Etapa 7).
Etapa 7: A peça acabada é então preparada para envio à linha de montagem final do Audi A8.
Colocação direta de fibra =flexibilidade futura
Com todo o investimento feito, é surpreendente saber que a Voith Composites não tinha certeza desse negócio, mas na verdade a empresa concluiu o desenvolvimento e participou de um processo de licitação para ganhar a produção. “Pudemos cumprir a meta de custo da peça definida pela Audi, bem como os requisitos de qualidade e desempenho da peça”, disse Ufer. Isso não foi pouca coisa, considerando que várias empresas disputavam o programa.
A Voith Composites patenteou várias partes de seu processo. “O VRA demonstrou a industrialização usando a colocação direta de fibra [DFP] de fitas, o que reduz o desperdício, bem como o material usado por meio de uma disposição altamente otimizada”, disse Ufer. Ele também usa os materiais mais econômicos - fibra de estopa pesada não tratada e aglutinante em pó. Seu processo de segunda geração substitui o aglutinante em pó com aplicação direta de resina, eliminando mais etapas do processo. No entanto, a empresa desenvolveu outros processos DFP, incluindo o Voith Longfiber Preformer e o Voith Prepreg Winding.
“Estamos estabelecendo novos padrões para peças de fibra de carbono para a produção em série automotiva de alto volume”, disse o diretor-gerente da Voith Composites, Dr. Lars Herbeck. “A fábrica inteligente que estabelecemos traz a produção automatizada de componentes CFRP a um novo nível de eficiência e flexibilidade, incluindo quase qualquer formato, bem como tamanhos de lote individuais.” Este é, de fato, para onde a indústria está se dirigindo.
Resina
- Por que o material PEEK está no topo de sua classe
- Plástico Reforçado com Fibra de Carbono (CFRP)
- K 2019:Materiais são importantes na Messe
- Arkema lança programa ‘Start-Up Connect’
- Polykemi investe em sua própria planta de composição nos EUA
- Polykemi terá produção de compostos em três continentes
- Fita termoplástica unidirecional de fibra de carbono à base de PPS
- Desafios do enrolamento de fita com laser de compósitos termoplásticos
- Fibra de carbono de reboque dividido aumenta o desempenho do SMC
- Módulo CFRP economiza peso no projeto do foguete